PAPER SPLITTING: HISTORY AND MODERN TECHNOLOGY
IRENE BR�CKLE, & JANA DAMBROGIO
3 3. PAPER SPLITTING IN MASS PRESERVATION
3.1 3.1 BEGINNINGS
It is no accident that paper splitting evolved into a mass preservation treatment after World War II when many European libraries and archives were faced with significantly increased preservation tasks brought about by wartime destruction and neglect. As early as the 1960s, the Czech conservator Josef Vyskocil considered paper splitting as a mass preservation measure that he applied, for example, in the treatment of fire-damaged papers (M�ller 1970; W�chter [1982] 1987a). The Czech conservator L. Sedlecky advanced the unusual idea of using a viscous polyamide solution as facing support (W�chter [1982] 1987a). Designed to simplify the splitting process, Sedlecky's treatment never became popular, but it is still referenced in the 1967 conservation treatment survey by German book conservator H. Eckhardt (Eckhardt 1967). Silk gauze, also known as chiffon, and jaconet, a fine cotton or linen fabric, were recommended by Vyskocil, Sedleczky, and Eckhardt as core materials for strengthening paper; Eckhardt also suggested nylon fabric. It was also discovered that paste used as a core adhesive could be made insoluble in water by the addition of alum or formaldehyde (Sievers 1966). However, since the 1960s, more stable alternative materials have become the standard.
3.2 3.2 PAPER SPLITTING AT THE THURINGIAN UNIVERSITY AND STATE LIBRARY, JENA
G�nter M�ller, chief conservator of the Thuringian University and State Library at Jena, Germany, began experimenting with manual paper splitting in the early 1960s (fig. 7). He is responsible for the preservation of rare printed books and manuscripts, among them a great number of historically important specimens damaged during World War II. In some books, M�ller even now still finds shrapnel fragments (M�ller 2000); many books also suffer from extensive mold and water damage. Many of the library's unique manuscripts exhibit severe losses in the ink lines caused by advanced iron gall ink corrosion; others carry notations in various types of inks, a further challenge for the conservator (M�ller 1991). Industrial pollution and sulfur emitted by the library's coal heating system, which was used between 1918 and 1988, contributed extensively to the deterioration of the library holdings. Many fragile materials requested by library users are first passed to M�ller's conservation laboratory before they can be forwarded to readers. Thousands of rare books have already been conserved by M�ller through paper splitting, and hundreds of thousands of brittle manuscripts are still waiting to be strengthened by this process (M�ller 1999b).
Fig. 7.
G�nter M�ller in his workshop in 1969 at the Thuringian University and State Library at Jena, posing with a manuscript leaf that is partly split. Courtesy of G�nter M�ller, Jena
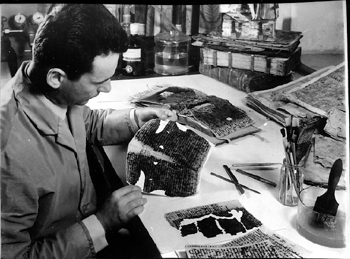 |
His pressing need for a mass treatment that would strengthen brittle paper led M�ller to many years of intensive investigation, which, until 1989, was curtailed by the lack of contact with the West. When M�ller began his work in the 1960s, two paper-strengthening methods were commonly practiced, silking and the more recent lamination of brittle paper with cellulose acetate film. Lamination, in particular, was considered a perfect solution for supporting brittle paper. However, the supplies and equipment needed for these treatments were difficult for him to obtain as they were available only from Western distributors (M�ller 1999b). After examining sample lamination treatments he had received from the American scientist William Barrow, M�ller felt he needed a mass treatment process that was less expensive, did not alter the appearance of the original, and involved only readily available materials. He explored leaf-casting developed by Yugoslavian conservators and soon was directed to articles by Sievers and Vyskocil, which described their trials with paper splitting (Sievers 1966; M�ller 1999b). Realizing the potential of this treatment, M�ller began experimenting with published procedures and, in his early articles, discussed their shortcomings (M�ller 1970). Over the course of 30 years he increased the refinement and efficiency of paper splitting, which until recently was still regarded as too labor-intensive to allow the timely treatment of vast library holdings (M�ller 1991).
Today, M�ller is able to split 400 sheets per day using his “Jenaer Papierspaltverfahren” (Jena Paper Splitting Procedure) that was patented in 1964 and again 1991 and since then has evolved still further. Books are disbound, and artifacts may be disinfected, surface-cleaned, washed, and leaf-cast in advance. Water-sensitive materials do not receive any aqueous treatment before splitting. M�ller has observed that the gelatin facing adhesive, applied to iron gall ink documents that constitute a major part of his work, consistently prevents the ink from bleeding during the splitting process. The preparatory work is followed by a paper-splitting cycle that usually takes 10 days. The night before splitting begins, a 40% (w/v) solution of pharmaceutical-grade gelatin (170 bloom strength) is prepared with the addition of glycerin (M�ller 1999b). This recipe is adjusted depending on the nature and condition of the artifacts. The first part of the procedure takes place in a small room that is conditioned to 70�F and 70% RH. The liquefied gelatin is warmed to 140�F and funneled onto rollers that are located in a heated gluing machine of the type employed in bookbinderies (part of the machine can be seen in figure 9, which illustrates a later stage of the process). The controlled room climate ensures that the facing support papers receive an even gelatin coating when they are passed through the gluing machine. A sheet of glued facing paper is laid on a table, and the dry or lightly dampened paper to be split is swiftly adhered to it before the gelatin solidifies. The paper relaxes and expands evenly before the laminate is pressed to establish a firm bond between the two papers.
Fig. 9.
The split paper halves receive a core adhesive application on the gluing machine. Courtesy of G�nter M�ller, Jena
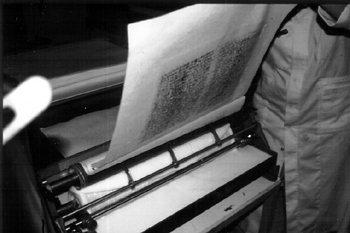 |
An absorbent paper, a so-called equalizer sheet as large as the facing support paper, is placed on top of the original already attached to the center of the facing paper. The equalizer sheet prevents a glue-to-glue bond between the margins of the two facing papers that would complicate the splitting process. It also allows the entire laminate to react uniformly to moisture and prevents uneven drying, cockling, and tearing of the original during splitting. No portion of the equalizer sheet remains permanently with the original.
Originals suffering paper losses receive a matching fill paper or leaf-cast pulp fill instead of the equalizer paper. Either of these fill materials functions in the same way as the equalizer sheet, except that portions of them remain permanently attached to the original where losses exist. Since the early 1990s, a leaf-caster has been available in the laboratory to fill losses in artifacts that can be subjected to aqueous treatment. If fills cannot be made by leaf-casting because a water-sensitive ink is present on the artifact, M�ller resorts to a special insert technique he developed over many years. It is perhaps best called a “double-splitting” method since it requires two splitting actions that follow each other in quick succession. First, the faced laminate is split; then an insert paper is placed between the split paper halves while the gelatin is still tacky; the split halves are then pressed a second time to adhere the filler paper to the facing papers in areas where the original suffered losses; the laminate is opened up again; this causes the filler paper to split where it adheres to the gelatin; excess insert paper is easily trimmed around the losses; finally, the two split halves are brushed with core adhesive and permanently united (M�ller 1970; H�ge 1981).
An artifact not suffering losses is sandwiched between the first facing paper and the equalizer sheet. It is then placed between plastic-covered cardboard pages of a large press book (such books are seen in figure 11, which illustrates a later stage of the process). The plastic covering is critical to the procedure because it prevents the moisture contained in the paper laminate from escaping. Several press books of the same dimensions are filled with faced originals. Each of the press books is placed in a press for five minutes to ensure good bonding between the papers, and then all books are stacked on top of each other to rest until the next treatment step. After pressing, the equalizer sheet is scored with a sharp knife along the perimeter of the original, and the portion that covered the original is lifted off. A second facing support paper is coated with gelatin and adhered to the open side of the original. This procedure creates a uniform laminate consisting throughout of three layers of paper (see fig. 3, upper right). All faced originals are returned to the press books and stacked for a few hours. Frank Mowery varies M�ller's procedure in that he first lays an equalizer sheet larger in size than the original on the table. He places the original paper on top and then adheres the first facing sheet to both papers (Mowery 1999).
Fig. 11.
After the core tissue has been attached as seen in figure 10, the split manuscript halves are reunited and the laminate is weighted for a short time between the plastic-covered pages of press books. (Two stacks of press books still filled with faced originals are seen in the foreground.) Faced originals are then transferred to cardboard stacks, where they rest for several hours. Courtesy of G�nter M�ller, Jena
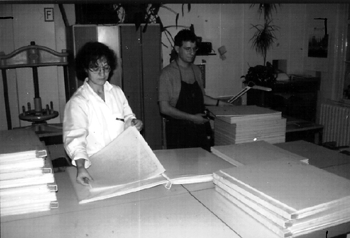 |
The success of every splitting process depends much on the consistency of the gelatin solution, which serves two important purposes. It attaches the facing paper to the original and supports it during splitting, and it also delivers moisture to the faced, dry, or lightly dampened original. It is important that the gelatin solution be viscous enough to remain on the surface of the original paper while the moisture it contains penetrates into the interior. A thick, dense paper can be sufficiently moistened only with a low-viscosity gelatin solution, but that same solution will penetrate and transparentize a thin, porous paper (Mowery 1999; M�ller 1999b; W�chter 1999b). Only if these parameters are observed will the paper moisten evenly and split in its center. To accomplish the splitting, the faced original is placed in a slit between two tables. The paper halves are pulled in opposite directions, beginning at a corner, until they are completely separated (fig. 8). Along one side, the facing papers are allowed to remain attached to each other, forming a hinge between the two split paper halves that serves as a registration guide when the halves are reunited after the insertion of the core tissue (M�ller 1999b).
Fig. 8.
Two staff members are splitting a manuscript folio that is positioned in a slit between two tables. Courtesy of G�nter M�ller, Jena
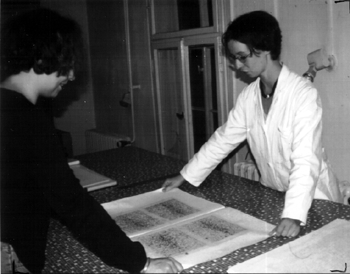 |
The viscosity of the core adhesive is adjusted depending on the paper thickness, a thin paper requiring a more viscous adhesive than a thick one (M�ller 1999b; W�chter 1999b). A cellulose ether adhesive mixture is prepared in M�ller's laboratory using a high-speed industrial blender. The standard core adhesive recipe published in 1989 included the following ingredients (M�ller 1989): 200 ml acrylic resin; 4,000 ml distilled water; 200 ml ethanol; 75 g carboxymethyl cellulose; 75 g methyl cellulose; 20 g calcium carbonate. The acrylic resin is emulsified in the blender before the rest of the ingredients are added. The adhesive is stirred for approximately 3 hours and then is rested for 12 hours to allow the cellulose ether to swell.
In past years, the core adhesive was applied to the two hinged split paper halves by brush. Today, the paper halves are coated by feeding them manually through the gluing machine (fig. 9). A thin abaca fiber paper (3.8g/m2), made by a German paper manufacturer from fibers imported from the Philippines, is placed on one of the coated halves (fig. 10). Good contact is ensured, and then the other split half is eased down on top (M�ller 1999b). Items reunited in this fashion are pressed between cardboards (fig. 11). The pressure is kept low to prevent the core adhesive from penetrating, and thereby transparentizing, the originals. After a few hours, all laminates are removed from the boards and placed on drying racks overnight. Finally, the facing papers are removed in water baths.
Fig. 10.
A staff member places the dry core tissue on the left side of the split manuscript that has just received the core adhesive as seen in figure 9. Courtesy of G�nter M�ller, Jena
 |
M�ller developed an efficient wet treatment system consisting of steel cassettes that hold 70 polyester fabric pockets, each of which can accommodate one paper laminate. The cassettes are lowered into washing tanks filled with deionized water (140�F), where they remain for 15 minutes. A small amount of a protein-digesting enzyme can be added to the washing solution. The facing papers release quickly during the short bath, and the cassettes are transferred to a final hot water bath (185�F) for 5 minutes (M�ller 1999b). The core adhesive remains unaffected, while the gelatin is reduced on the surface of the originals. Recently, however, M�ller has begun to eliminate the enzyme baths in the treatment of iron gall ink documents in order to leave a thin gelatin film on their surface as a form of resizing. After the final bath, the originals are removed from the pouches and separated from the reusable facing supports. It takes M�ller three to four weeks to disbind, treat, and rebind 5–10 damaged books; many more, however, are in treatment at any given time.
M�ller points out that at Jena and elsewhere, university and research libraries are faced with increasing requests by users who wish to see original materials that today are retrievable through electronic library catalogs and via the Internet. Paper splitting, he says, can secure and stabilize badly deteriorated paper, realign tears, and, combined with leaf-casting, fill losses and preserve original deckle edges and other paper features as well as various types of writing media. The procedure stabilizes paper mechanically and biochemically, and it stabilizes corroded ferrous inks (M�ller 1999b; M�ller 2000).
3.3 3.3 PAPER SPLITTING AT THE ZENTRUM F�R BUCHERHALTUNG AT LEIPZIG
Dr. Wolfgang W�chter's lifelong commitment to the development of efficient mass conservation treatments began in 1964 when the Restoration Department was first established at the Deutsche B�cherei in Leipzig, Germany. Dedicated to preserving materials in their original format, “the policy governing the workshop development has always been to translate research findings into the practice of preservation and restoration and to improve the cost-benefit ratio for these operations” (W�chter 1987b, 129). After Germany's reunification in 1989, the Deutsche B�cherei Leipzig, the Deutsche Bibliothek Frankfurt am Main, and the Deutsches Musikarchiv Berlin merged under the name Die Deutsche Bibliothek. The library's primary responsibility is the collection and bibliographic indexing of all German-language publications since 1913, including the work of German-speaking emigrants from 1933 to 1945. W�chter (1995) points out that, each year, 4.66% of an average library's holdings becomes unusable. W�chter was closely acquainted with M�ller's work in nearby Jena, where he had studied at the university. Having been introduced to paper splitting at Jena, W�chter began experimenting with the mechanization of the process in the 1960s. By the early 1990s, he had fully developed a machine that would streamline and economize paper splitting for mass preservation.
In 1992, the West German firm Becker Preservotec was contracted to further perfect W�chter's design. With the support of Becker Preservotec, the Conservation Department of the Deutsche B�cherei was privatized in 1997 and the Zentrum f�r Bucherhaltung (ZFB) was formed to serve clients in Germany and abroad. The first complete model of the paper-splitting machine has been operational since 1997. In 1999, the machine already had the capacity of splitting up to 5,000 paper sheets per day (W�chter 1999b). Rare materials including manuscripts are split by hand at the ZFB, while other materials such as newspapers are split by machine.
Preparatory treatments usually include disbinding, collation, washing, alkalization, and disinfecting of damaged papers. Formerly, papers also routinely underwent bleaching with oxidizing bleaches such as potassium permanganate. The treatment has been almost completely abandoned today because conservators have become aware of the importance of preserving the original tonality of historic paper and of the risk of weakening it during bleaching. Only a short bath in a 0.05% sodium borohydride solution is sometimes administered to lighten paper and stabilize the cellulose. When required, degraded papers may undergo leaf-casting on a machine developed by the Danish book conservator Per Laursen that W�chter plans to integrate with the splitting machine to streamline his mechanized paper-strengthening process. Pure alpha cellulose pulp purchased from paper manufacturers is used in leaf-casting (W�chter 1999b).
The mechanized process of paper splitting is continuous from the facing of the paper sheets to removal of the facings after completion of the splitting process. The machine is composed of three separate parts that are aligned in a formation comparable to a Fourdrinier machine (the first two parts of the machine are described in W�chter et al. 1996; the third, newest part is described in W�chter et al. 1997). In the first part of the machine, dry or lightly dampened original sheets with a maximum width of 48 cm are laid manually on a moving belt that is 50 cm wide and carries a continuous sheet of facing paper freshly coated with gelatin adhesive (fig. 12). Once attached to the facing paper, the sheets are transported a short distance to receive the second facing paper that is also coated with gelatin. A strip of filler paper (similar in function to M�ller's equalizer sheet) frames the originals, preventing a glue-to-glue bond along the very edges of the facing papers that would lead to uneven splitting. The facing adhesive is made of 7,000 ml water, 2,500 g food-grade gelatin (220–50 bloom strength), and 150 ml glycerin (W�chter 1997). For a thinner paper, a more viscous gelatin is used to prevent the penetration of the gelatin into the paper interior (W�chter 1999b). The two continuous facing paper sheets firmly adhere to the originals, while the sandwich passes between a set of rubber rollers adjusted to exert a certain amount of pressure (see fig. 12). The rollers operate under a dome that allows control of the ambient temperature and humidity. This environment ensures that the facing adhesive has time to set before the laminate travels a short distance to the second part of the machine. There, the facing papers are pulled in two opposite directions, causing the original sheets to be split into two even halves (fig. 13). Two opposite sets of rollers guide both halves to their point of reunification. The tension of the rollers is adjustable so that the split sheets traveling at a speed of about 1–2 m per minute can be kept properly aligned during machine operation. A staff member remains stationed at this part of the machine to monitor its operation. If the rolls of facing paper need to be changed or other adjustments made, newsprint is fed into the machine until placement of the originals can resume.
Fig. 12.
Paper sheets are being transferred to the first section of the paper-splitting machine at the Zentrum f�r Bucherhaltung (ZFB) in Leipzig, where they are adhered between the continuous facing supports.
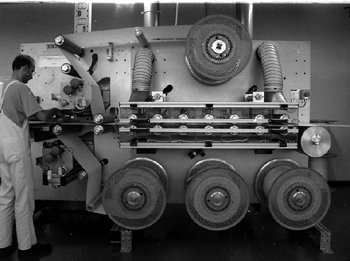 |
Fig. 13.
In the second part of the paper-splitting machine, the faced paper sheets are split as seen to the left (ZFB, Leipig). The split halves are reunited between the closely set rollers seen to the right.
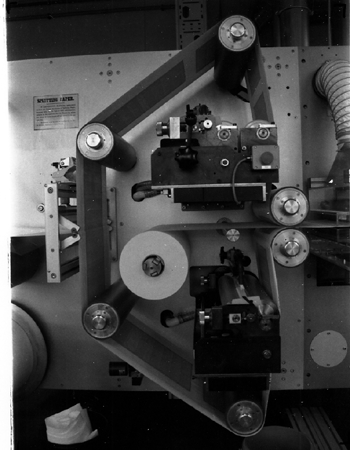 |
Shortly before they are reunited, the split halves are coated with a core adhesive. A core tissue delivered from a continuous roll is inserted between the two split halves at their point of reunification (fig. 14). The core adhesive consists mainly of methyl cellulose and carboxymethyl cellulose with the addition of less than 1% acrylic resin and sufficient calcium carbonate to leave a 3% alkaline reserve in the core of the treated paper. A recipe W�chter published in 1997 contained 4,000 ml distilled water; 200 ml acrylic resin (optional); 200 ml ethanol; 75 g carboxymethyl cellulose; 75 g methyl cellulose; 20 g calcium carbonate/magnesium carbonate; 30 g galactomannan (polysaccharide added optionally); 1 g Captan (fungicide added optionally [1,2,3,6 tetrahydro-N-trichloromethyl thiophtalimide]) (W�chter 1997, 111; W�chter 1999b).
Fig. 14.
The split halves receive a coating of core adhesive (it can be seen in the lower image as a white band between two rollers in a tray) (ZFB, Leipig). The core paper is fed from a roll and is received between the split halves at the moment of their reunification.
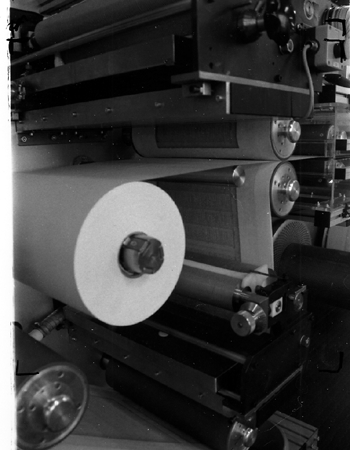 |
The core adhesive formulation is adjusted depending on the paper thickness and quality. The acrylic resin adhesive is added to reinforce particularly fragile materials. Galactomann, a polysaccharide gum from the guar plant and carob tree, has a chemical structure closely related to cellulose and many hydroxyl groups suitable for hydrogen bonds that ensure good bonding between the core tissue and the split original. Captan is the fungicide of choice at the ZFB because it is, according to W�chter, chemically stable and effective over long time periods without adverse side effects. The core tissue is an unsized cotton fiber paper (12 g/m2) that contains 5% calcium carbonate (W�chter 1999b).
This laminate passes through a set of rollers that allows the core adhesive to set, ensuring proper adhesion. The laminate is then transported to the third part of the machine for the final washing cycle, where it is guided in and out of a series of six narrow water tanks available (fig. 15). The tanks contain hot water that can be conditioned to various temperatures. Operators can change conditions for each tank separately and adjust the duration of each washing cycle by moving the rollers that guide the sheets inside the tanks up or down. Usually, only three washing cycles are needed to reduce the gelatin and release the originals from the reusable facing supports. In the first tank, a cellulase-free protease (Corolase 7089, a liquid bacteria protease from Bacillus subtilis) aids the release of the facing papers and the reduction of gelatin on the surface of the sheets. The enzyme operates best at a pH of 6.0–8.5 and a temperature of 131�F. In the second tank, the enzyme is deactivated at a temperature between 149�F and 158�F, and in the third tank, residual gelatin and deactivated enzymes are rinsed out. The paper sheets, now connected only by the continuous core tissue, are guided through a drying section. At the end, they are automatically cut into separate sheets using a laser sensor-operated blade. In 1999, the cost per folio was approximately $4 (W�chter 1999b).
Fig. 15.
In six washing tanks, the facing papers are removed and the residual gelatin dissolved (ZFB, Leipzig). Enzymes may be added to the first washing bath.
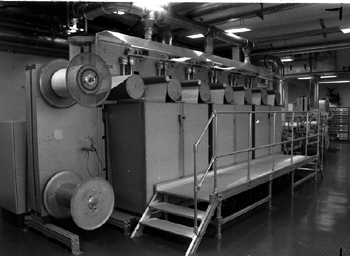 |
The possibilities of mechanized paper splitting were recently explored by the Cleveland Public Library, a current U.S. client of the ZFB. The library's Preservation Office wanted to restore the original format of three decorative 19th-century publisher's bindings and one early Ohio publication. The splitting and leaf-casting restored the flexibility of the pages and reestablished the spine fold that was previously cut to make preservation photocopies of the books. The text blocks were bound at the ZFB, incorporating the original bindings for all three volumes (fig. 16) (Olszewski 1999).
3.4 3.4 ARE THERE ANY MISHAPS IN PAPER SPLITTING?
Beset by seemingly imponderable variables, paper splitting holds more risks than benefits for the novice practitioner. Experimenting with splitting newsprint samples, the authors encountered some of the many pitfalls that await the inexperienced paper splitter. Some of them were also noted by paper conservator Monika Gast (1993), who candidly wrote about her early splitting attempts after attending a workshop conducted by G�nter M�ller.
Several common failures may occur during the splitting process: the facing support may not adhere if the viscosity of the gelatin is not calculated correctly; uneven splitting may occur if the gelatin is applied inconsistently or gels too quickly (this may happen when applying the gelatin by brush, and if the temperature and humidity in the work area are too cool and dry); the original paper may transparentize if the faced laminate is too strongly pressed, causing the gelatin facing adhesive to penetrate into the original paper; pressing too strongly may also cause the original paper to separate from the core tissue in the last stages of treatment when the gelatin penetrated into the paper interior is dissolved with the aid of enzymes; a weak or unevenly applied core adhesive may also cause internal separation of the paper layers after treatment. It is with good reason that experts who have split paper for many years warn that one must practice on at least 1,000 mock-ups before considering this treatment on an artifact.
Even in the hands of experienced practitioners, paper splitting is not completely without risks. Most of them are apparent and can be calculated in advance while one makes the decision to have an artifact split: the paper may lose some of its original texture (see fig. 30); although virtually all of the ca. 100 treated papers examined by the authors showed excellent alignment of the paper halves, small misalignments may occasionally occur (see fig. 20); small losses of the paper or media may occur (see fig. 26); small paper areas may not split if a damaged artifact was not properly aligned before splitting (see fig. 32).
Fig. 30.
Book pages with intaglio illustrations, raking light view. Bottom: detail of a washed page before splitting. Top: detail of a page after strengthening by splitting at the ZFB, Leipzig (the crease is original to the paper)
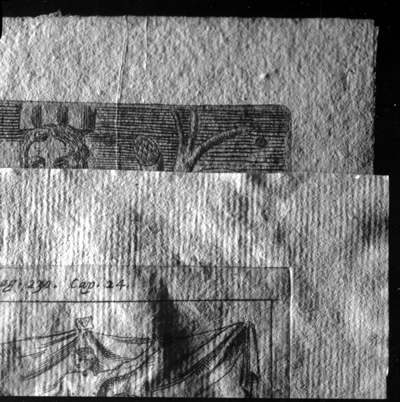 |
Fig. 20.
Newspaper page after strengthening by splitting at the ZFB, Leipzig, transmitted light view
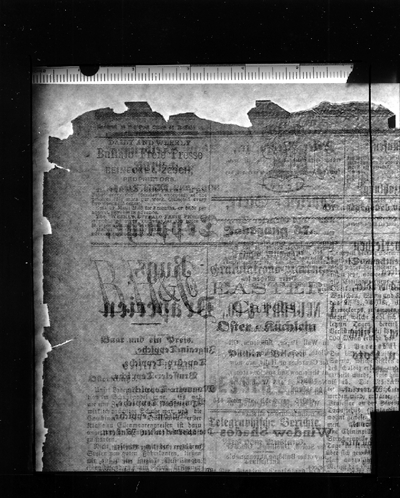 |
Fig. 26.
Detail, iron gall ink manuscript after strengthening by splitting at the Thuringian University and State Library. Ruler divisions are 1 mm. The ink did not bleed. A loss within the ink line (0.5 mm in diameter) reveals the white core tissue.
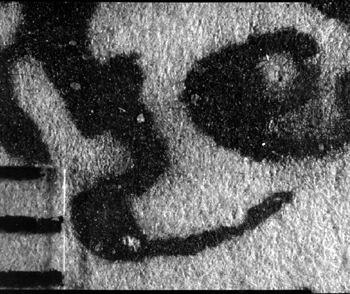 |
Fig. 32.
Detail, recto and verso of a book page, normal light view. An L-shaped tear that had already existed originally caused a triangular paper piece to be fixed in folded position during treatment. The elbow to the relief-printed figure (recto) now appears on the verso (left). The resulting hole in the page is filled with pulp applied during the leaf-casting treatment that preceded the splitting process at the ZFB, Leipzig.
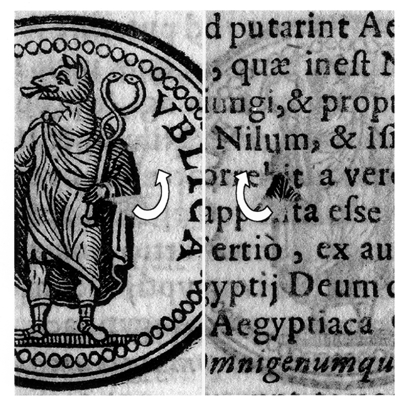 |
Current paper splitting by machine is a precise process that allows the efficient treatment of large quantities of materials. Rare and precious artifacts, however, are split by hand if it is decided that splitting is indeed the best method of preservation. The hand-splitting process allows greater control over individual artifacts because each one is treated separately.
|