PAPER SPLITTING: HISTORY AND MODERN TECHNOLOGY
IRENE BR�CKLE, & JANA DAMBROGIO
2 2. THE HISTORY OF PAPER SPLITTING
“Here we are talking about that which could be referred to as the ‘opera magna’ in the field of restoration … paper splitting … the division into two parts in the thickness of any piece of paper” (Morgana [1932] 1994, 83).
2.1 2.1 BEGINNINGS
Neither the inventor nor the invention date of paper splitting is known. Celebrated as a novelty, the treatment appeared seemingly quite suddenly in Europe during the first half of the 19th century. A certain W. Baldwin, an English restorer, is said to have split paper in 1848. The famous French restorer Alfred Bonnardot, who unfortunately did not witness Baldwin's process firsthand, believed it to be the earliest feat of paper splitting. It must have rapidly become public knowledge, however, when Baldwin succeeded in splitting English bank notes. So the process would not end up in the hands of dishonest individuals, the Bank of England generously offered him monetary compensation if he would divulge his method to bank officials instead of publicizing it (Bonnardot 1858, 332). According to Bonnardot, Baldwin was an employee at P. Colnaghi, a London print dealership that still exists today. There is, however, no confirmation of his tenure there because none of Colnaghi's business records predating 1870 survive (Colnaghi Art Gallery 1999). A possible reason for their disappearance is suggested by the English book conservator Bernard Middleton. Many company records, he says, “were destroyed by bombs in the Second World War, and others were deliberately discarded at that time because stored paper was a [fire] hazard” (Middleton 1999). Middleton believes that Baldwin was probably not self-employed because his name does not appear in the lists of 19th-century English bookbinders.
Apparently, Baldwin was not the only one to proudly offer this miracle treatment. A short notice in a mid-19th-century leaflet testifies to the increasing popularity that paper splitting enjoyed in England: “PAPER SPLITTING. W. Kennington, bookbinder, undertakes to show any person the process of splitting paper, however thin, for the sum of ten shillings, subject to the condition that the person to whom the secret is made known will not reveal it to any one else. Specimens may be seen on application to Mr. S. Gibbs, Stationer 5, Union Street” (Middleton 1999). Bonnardot also mentions a Parisian intaglio printer and restorer, A. Pierron, who placed several examples of split engravings at the Universal Exposition of 1855 (Bonnardot 1858).
The first detailed description of paper splitting was written by none other than Josef Meder, director of the Graphic Art Collection Albertina in Vienna from 1909 to 1923. As a print connoisseur and curator, he was interested in restoration matters and occasionally treated prints and drawings himself. In 1877 and probably around 1881, while he still was curator, he jotted down private notes on paper splitting (Helm 1979). Bonnardot's and Meder's accounts are important because they constitute the most detailed sources on paper splitting dating before the First World War. As late as the 1930s, Mario Morgana sought out Bonnardot, looking in vain for newer published information. This search inspired him to write this romantic recapitulation of the origin of paper splitting: “In 1848, a crafty restorer, a Londoner named Mr. Baldwin, succeeded in splitting prints. When the news reached Alfred Bonnardot, it must have disturbed his dreams because he had thought about a similar procedure that would have made possible certain special restorations that could not have been possible any other way” (Morgana [1932] 1994, 83). No doubt paper splitting was a process shrouded in mystery, even guarded with secrecy by those few who knew how to accomplish the task.
2.2 2.2 WHY WERE PAPERS SPLIT ORIGINALLY?
Paper splitting originated among art collectors and restorers who recognized it as a method designed to separate the recto and verso of double-sided prints, drawings, and manuscripts for their easier enjoyment (fig. 4). Although it may appear to the contemporary reader that this treatment was motivated by the potential monetary gain that results from making two artifacts out of one, 19th- and early-20th-century restorers and collectors seem to have been more concerned with optimizing the aesthetics of viewing artworks they owned. Bonnardot reported that a Paris collector, M. Hennin, owned a rare engraving showing a portrait of Henry IV that had large letters printed on its verso. These were apparent on the recto and “detrimental to the effect of the burin” (Bonnardot 1858, 332). The print was split in London by Baldwin and returned in two pieces “without even the least abrasion” (Bonnardot 1858, 332). Meder presumably split artworks on paper belonging to the Albertina (Schack and Fackelmann 1987, 7 n. 7). The German restorer Max Schweidler recommended splitting double-sided drawings for their easier viewing (Schweidler 1950).
Fig. 4.
Illustration in Mario Morgana's 1932 restoration manual showing a double-sided printed folio during splitting. Morgana [1932], 1994, 88
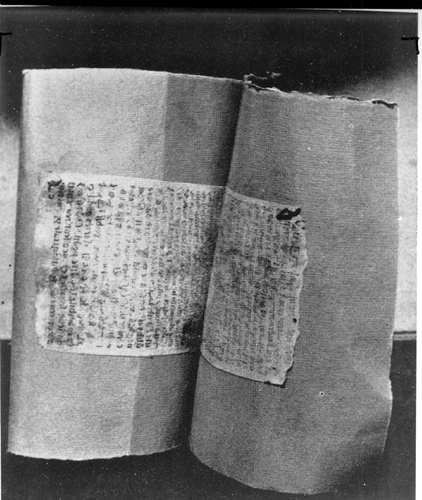 |
Meder also considered paper splitting for matters other than restoration. Somewhat cryptically, he commented on the splitting of certain printed images: “If they are illustrations on printing paper, these often very thin [split] sheets now can be adhered to white papers to be used as pictures, or they can be used as colored decal pictures” (Helm 1979, 213). This decorative use of split prints was not a mere aberration. Schweidler explained that prints could be split to be made into lampshades if their paper was not translucent enough to allow the light to pass without being split. We may assume that pictures used for lampshades were not considered valuable or important, and that the more serious business of paper splitting concerned the treatment of artwork. These excursions show, however, that an intimate connection still existed then between restoration and craft traditions. Indeed, paper splitting may well have originated with bookbinders, for they would have had a chance to observe in their practice that certain papers easily split (Sievers 1966). This realization could have easily led them to the development of a new treatment. Even the 1983 bookbinding manual of the German binder Fritz Wiese still mentions that the practitioner might occasionally be obliged to split “pictures” printed on both sides on request of a client (1983, 359). Schweidler was also aware of the surprise effect and publicity value of splitting bank notes (fig. 5) (Schweidler 1950).
Fig. 5.
Illustration in Max Schweidler's 1950 restoration manual demonstrating paper splitting using bank notes. One half of a bank note is seen after splitting. Schweidler 1950, 74.
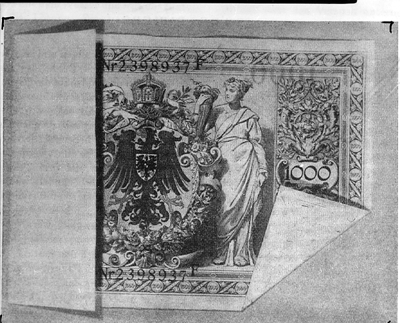 |
Schweidler further commented on splitting: “One will be forced to separate a paper if engravings or lithographs were printed on the reverse and should be lined. The application of paste would make the printing on the reverse show through to the front and would make it look unattractive” (Schweidler 1950, 75). However, “repair papers used purely for restoration should never be split because the side of the paper that receives the glue application will always acquire a certain density” (Schweidler 1950, 75). Schweidler is best known for a special mending technique that is often referred to as “invisible repair.” Rarely practiced today, it was much admired for its subtle finish. Papers used for these repairs were extensively thinned along their edges to match the chamfered losses of an artwork. Residues of a glue layer applied to such an insert paper during the splitting process would have made it difficult to shape the paper edges. Schweidler further wrote that papers that were to be split should be homogeneous in composition and free of lumps and metal inclusions. During splitting, these would become separated and leave small holes in the paper.
In the days of Schweidler, splitting double-sided artworks was still considered a necessary treatment and part of a reputable restoration practice. Even recently there have been signs of a residual interest—although little publicized and less easily accepted—in the separation of double-sided artworks. In the 1980s, two Austrian conservators split several privately owned double-sided drawings by 20th-century artists, including one by Oskar Kokoschka (1886–1980), lining each half with Japanese paper. The conservators argued that their procedure in this case was acceptable because they had adequately documented the original state of the drawings (Schack and Fackelmann 1987). Conservators today refuse to perform such treatments, considering them an unethical interference with the integrity of the artwork. This case is not mentioned here to generate obvious reactions but rather to show that we are part of a heterogeneous international community, evolving at different rates, and even recently following in good faith standards different from those by which we abide today.
2.3 2.3 SPLITTING PAPER BY HAND
Throughout the history of paper splitting, the fundamental principles and relatively rigid parameters of the treatment have remained unchanged. It is instructive to see, however, that some restorers and conservators were able to—and sometimes had to—develop their own treatment variations. As far as these are recorded, they allow us to appreciate the creativity and skill of our professional forebears.
In Essai sur l'art de restaurer: Les estampes et les livres (1858), Bonnardot said he regretted he had no firsthand knowledge of paper splitting. Having heard, however, of splitting treatments performed by the English restorer W. Baldwin and the French restorer and printmaker A. Pierron, he assured his readers that “the possibility of such a procedure is not an illusion” (Bonnardot 1858, 330). He consoled his eager audience: “I will share with the lovers of this art some observations that perhaps will enlighten them; because, from a reasonable hypothesis to the practical conclusions the step is sometimes very short” (Bonnardot 1858, 330). Bonnardot was able to intuit the basic principles that underlie the idea of paper splitting, and he even hypothesized about two different paper-splitting methods. He guided his audience step-by-step: “Let us begin with this consideration: when a force is applied to a solid body with the purpose of splitting it, it is always the part that is less strong, that is softer, or that is not stabilized, that will yield first. Now, in a piece of paper, one may consider the two outside surfaces … the firmest layers, and the intermediate layer, in its entirety, the weakest” (Bonnardot 1858, 134).
To save only the recto of a print, Bonnardot suggested adhering the print facedown to a marble slab and scraping off undesired paper layers on the verso. One should smooth away the roughened surface with a piece of sharkskin and then soak off the thinned paper sheet by immersing the marble in a water bath. If, however, it was desired to save both sides of a print, one side of the original should be adhered to a rigid, flat support using animal glue. Bonnardot was perceptive with regard to the quality of this adhesive: “It would have to be perfectly pure, without impurities, of homogeneous viscosity, and should not penetrate into the interior of the paper, but attach only to its surface” (Bonnardot 1858, 135). A varnish or resin could also be used as adhesive. The adhered paper should be allowed to dry. On the verso, one should then evenly apply another viscous layer of glue to adhere a piece of cloth or a smooth piece of parchment larger in dimensions than the original. After this support dried, one of its edges should be peeled off along its entire width, working slowly and with uniform force. Half of the paper would remain on the rigid support, the other half would attach to the cloth or parchment. Once the separation was accomplished, the split paper halves could be released from their respective supports in a hot water bath or alcohol, depending on the adhesive present.
Bonnardot's interest in technology was not unusual for his era, but it still may impress us today for being well ahead of contemporaneous developments in the restoration field. He suggested yet another method for paper splitting that was based on his knowledge of machines used in the leather and parchment industry to split sheepskins (Bonnardot 1858). A paper sheet would first be fully adhered on both sides between two thin wood panels. After drying, the edges of the panels would each be clamped to opposite sides of a vise with wide jaws and would be pulled apart along one entire edge just far enough to begin the splitting of the paper. The split, Bonnardot presumed, would occur in the center of the sheet not penetrated by the glue. Along the already split edge, the wood panels would be adhered between two revolving cylinders. Turning the cylinders, one could then pull the two panels apart to effect a separation in the center of the paper. If it is true that Bonnardot indeed never witnessed paper splitting, he is to be credited with an imaginative mind and an anticipation of even the most recent accomplishments in paper-splitting technology.
In his unpublished notes from 1877 and 1881, Josef Meder detailed a paper-splitting treatment designed to separate two-sided prints or drawings (Helm 1979). Judging by the procedural improvement recorded in the later text, we may assume Meder had considerable practical experience with paper splitting and monitored his results. In his 1877 notes, Meder recommended that one apply a thin coat of fine glue to two firm, smooth support paper sheets and allow them to dry. To remove the gelatin sizing of the paper to be split, it was immersed—depending on its thickness—for up to 12 hours in a 10% solution of hydrochloric acid, followed by 15 minutes in a lukewarm potassium hydroxide solution. Residual chemicals were then rinsed out in a succession of warm water baths. The paper was hung to evaporate excess water and then was placed between the two sheets of glue-coated support paper. It was lightly pressed to remove air bubbles and kept in a press for 12–24 hours. After being removed from the press, the support papers were trimmed to the dimensions of the original paper laminated between them. This step would prevent tears from occurring during splitting: “The surfaces of the paper to be split adhere to the glued paper, whereas the de-sized paper in the center will easily split into two planes, depending on the quality and make of its fiber matrix. One of the planes is usually thinner and carries the wire pattern and watermark, the other is usually a slightly dense fiber felt with an even, often amazingly beautiful texture” (Helm 1979, 221). To remove each paper half from its respective support, a piece of oil or wax paper was placed on the split side and the assembly was immersed in a warm water bath. After a few minutes, the support papers released and floated to the water surface. The split original could be removed from the bath with aid of the oil paper. A new piece of oil paper was placed on the front of the split original, and the assembly was immersed again. The washing was repeated until the glue was removed from the paper surface.
The recipes in the 1881 manuscript, however, allow us to infer that Meder may have been a bit apprehensive regarding the intense chemical treatments he had recommended in the 1877 manuscript for the removal of sizing from the paper to be split. Instead, he now suggested that the paper be soaked in warm water for several hours, then immersed for 1–2 hours, instead of 12 hours, in hydrochloric acid, and finally rinsed in hot water until completely free of acids. After this procedure, the paper was allowed to rest on a blotting paper. The recipe for the adhesive to be spread on the support papers called for 4 parts water, 1 part glue, 3 parts sugar, and 3/4 parts gum arabic. The addition of sugar and gum arabic improved the flexibility of the adhesive. Meder also recommended that the paper to be split be adhered to support papers that were first dampened to prevent curling and ensure even adhesion.
The English bookbinder Douglas Cockerell addressed the subject of paper splitting in his repair manual, Bookbinding and the Care of Books (1902). His scant description of the procedure differs from that of Meder in several points. Instead of preparing two support papers with animal glue, he preferred to brush the paper to be split on both sides with a thick starch paste. Then, a fine linen or cotton fabric (jaconet) was placed on each side of the pasted paper. The laminate was pressed briefly so that the fabric adhered well overall, and it was allowed to dry before the fabric sheets were pulled apart, each carrying half of the split paper.
Mario Morgana, in Restauro dei Libri Antichi (1932), was perhaps the first restorer to recommend splitting as a way of strengthening deteriorated paper, specifically tattered book frontispieces. Not satisfied with the results of manual splitting, he gave detailed specifications on an apparatus that, so he suggested, would make it easier to maintain the necessary force to pull the support sheets apart. First, two sheets of parchment were coated with animal glue and dried. The paper to be split was soaked in water to remove the sizing. Excess water was allowed to drain, and the sheet was placed between the gelatin-coated parchment sheets. The laminate was then passed over with a roller to ensure uniform adhesion before drying it under high pressure. After the faced paper had dried, it was inserted in Morgana's device (fig. 6). The splitting was initiated by hand. The bottom parchment sheet was clamped at head and tail between two bars (B/, B). A screw control (D) was used to increase the space between the larger block (A/) and smaller block (A) until the clamped laminate was stretched taut. One edge of the top parchment was threaded through a slit in a cylinder. While pressure was kept on the surface of the instrument, the cylinder was rotated around its own axis from B/ to B so that the parchment on top rolled up on the cylinder (see fig. 6). One-half of the paper was thus rolled up with the upper parchment sheet while the other remained on the lower, clamped parchment sheet (Morgana [1932] 1994).
Fig. 6.
Mario Morgana’s splitting apparatus. The diagram shows the mechanism of the apparatus depicted in the photograph. Morgana [1932] 1994, 91, 93
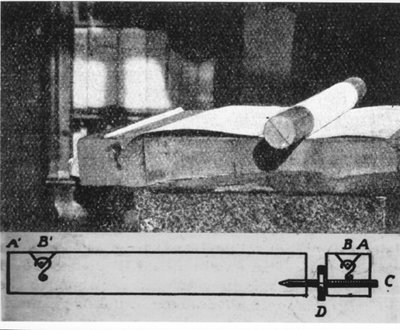 |
Also in the 1930s, another Italian, F. Leti, came up with the idea of using celluloid—then a new commercial product—as facing support (W�chter [1982] 1987a). The paper to be split was placed between two celluloid sheets, and all three were immersed in an acetone bath until the solvent had completely volatized. Apparently, this process fused the celluloid to the paper so it could be split. The split halves were again immersed in acetone to help release the celluloid. This procedure was suitable only for undamaged papers without losses that could be evenly attached to the celluloid.
To the German restorer Max Schweidler, paper splitting was not magic but just a “simple hand skill” (1950, 73). Schweidler was the first restorer to suggest dampening the artifact before facing it. He washed the facing papers and the artifact in cold water to allow the papers to expand and relax, drained them, and placed them on absorbent cardboards to remove further moisture. A pure, heated animal skin glue was applied to one side of the damp artifact (Schweidler 1950). A facing paper, slightly larger than the artifact, was placed on top. The second facing paper was attached in the same manner on the other side. Because all three papers were damp, wrinkles and bubbles could be easily brushed out. The laminate was weighted between absorbent boards under increasing pressure until it was dry. The overlapping facing paper margins were cut off along three sides of the original, and the splitting could begin at one of the exposed corners. The split halves were placed in a cold water bath to release them from their support papers. Once they were separated, the split papers were soaked in hot water to remove residual glue. Schweidler split damaged double-sided artworks permanently because he thought they required repairs that were best administered by lining. He also split undamaged double-sided artworks for the separate use of their split halves, but he did not mention whether he treated the newly exposed raw paper on the reverse by applying a surface size or by burnishing it.
Up to and even beyond Schweidler's time, glue and starch paste were the common adhesives used in paper splitting. Since the 1960s, however, some conservators have replaced the starch paste core adhesive with mixtures of methyl cellulose and polyvinyl acetate (PVA) dispersions (H�ge 1981). Polyvinyl acetates ensured good adhesion of the paper layers, while methyl cellulose was intended to ensure that treated papers could be separated again in the future, a claim that, conservators realized, was of more theoretical than practical concern (Schack and Fackelmann 1987). Fungicides and alkalizing agents have been added to these mixtures (H�ge 1981).
2.4 2.4 PAPER SPLITTING BY HAND IN THE UNITED STATES
Beginning in the 1940s, a few American conservators explored paper splitting for the treatment of individual artifacts. Willman Spawn, honorary curator at Bryn Mawr College, recently recounted his experiences with paper splitting during the 1950s. As the book conservator for the American Philosophical Society in Philadelphia, he was one of the first conservators known to the authors to employ this treatment in the United States (Spawn 1999). Spawn became interested in the process after he read Schweidler's manual and followed its instructions, the only exception being that he used rice starch paste instead of animal glue to adhere the facing papers. Like Schweidler, he split two-sided drawings into two separate works if desired by private clients, but he also used the treatment to strengthen severely damaged book endpapers in the society's collection. He felt that this technique offered an invisible repair that could strengthen the original paper internally. Because newsprint was the easiest type of paper to split, he often chose the Sunday funnies during the demonstrations he would provide when he lectured at various universities, conservation graduate programs, and libraries across the country (Spawn 1999).
Paper splitting was performed during the 1940s and 1950s at the Extra Bindery at the R. R. Donnelley & Sons Company in Chicago. The bindery specialized in fine and replica binding and conservation. In one of the bindery's pamphlets, paper splitting was promoted as a method of separating drawings or printed images without damaging either side of the paper, as a treatment to strengthen weakened paper, and as a method to reduce the thickness of blank paper that was to be used for repair (Lakeside Press n.d.). In one case, to fill losses in a printed broadside, pulp inserts were made and the missing text was replicated in an elaborate procedure that involved the production of a facsimile print of the broadside on a paper that matched the texture of the original sheet. The facsimile was split to reduce its thickness. Then, letters and individual words of the split facsimile were cut out and pasted on the pulp fills of the repaired broadside (Wiest and Crusius 1979).
In the present day, Frank Mowery, head of conservation at the Folger Shakespeare Library in Washington, D.C., practices manual paper splitting. He first attempted the treatment following W�chter's description in his book Buchrestaurierung, which was first published in 1982. In 1986, Mowery hosted W�chter during his first U.S. visit when he spoke about the splitting machine to the Washington Conservation Guild. Later, Mowery perfected his methods, learning from G�nter M�ller, chief conservator at the Thuringian University and State Library in Jena, Germany. Interested in determining accurately the critical moment when splitting of the faced original paper should best occur, Mowery has availed himself of a paper moisture meter (Sovereign Dual Probe Moisture Master). He allows the laminate to rest until the instrument indicates that only around 14% moisture is retained on its surface, and then splits it. The interior of the recently split original usually still measures 80–90% moisture content. Mowery split 19th-century papers from the Folger's collection that were weak and brittle due to previous restoration treatments, especially those that had been bleached without proper subsequent rinsing. He also split several incunabula and part of a 17th-century manuscript with severe iron gall ink corrosion. He favors paper splitting in such problem situations because it produces aesthetically pleasing results, provides good structural stability, and can be reversed. Working together with book conservator Bill Minter, Mowery has recently conceived of a paper-splitting device that is based on the Beloit sheet splitter, a machine used in the printing industry to sever paper into several layers for a determination of ink penetration. Adapting such a device for conservation would potentially eliminate the need for facing papers because the paper to be split would be frozen on both sides to metal surfaces (Mowery 1999).
|