CYCLODODECANE: TECHNICAL NOTE ON SOME USES IN PAPER AND OBJECTS CONSERVATION
IRENE BR�CKLE, JONATHAN THORNTON, KIMBERLY NICHOLS, & GERRI STRICKLER
3 CYCLODODECANE AS AN ISOLATING LAYER TO PREVENT STAINING OF POROUS MATERIALS DURING MOLDMAKING
Molding and casting of museum objects is carried out frequently and for a variety of reasons, among them to restore missing parts during restoration; to supply replicas of important objects to other institutions and researchers; to provide expendable reproductions for display and handling in interactive and “living history” exhibits; and to create authentic replicas for sale in museum shops. Conservators are often called upon to make the molds or to oversee and make material recommendations to mold makers. So-called silicone rubbers of the RTV-2 type (room-temperature vulcanizing polymers that cure after the mixing of two separate components) have been by far the most common mold-making materials for these purposes. They pick up very fine detail, cure to a strong flexible mass without shrinkage, release well from both the objects and the materials used to make positive casts, and have good permanence as finished molds. A drawback to their use, however, is the staining that can occur on porous surfaces due to the migration of uncured low-molecular-weight “silicone oils” before the rubber has cured, a problem noticed by many conservators and briefly noted in the literature (Larsen 1981). The researcher who addressed this problem most extensively reported that the least damage was caused by the use of barrier films and fast-curing rubbers but all caused some damage (Maish 1994). Since barrier films themselves posed removal problems and did not serve as effective barriers unless they were thick enough to obscure detail, not truly satisfactory solution to this problem then existed.
Cyclododecane suggested itself to the authors as a useful barrier to prevent the staining caused by uncured silicone rubber. If it truly did sublime completely, it would not need to be removed with solvents after the molding procedure. The likelihood of leaving behind residual barrier materials would be reduced, as would the chance of inadvertently “cleaning” the object, as sometimes happens due to the impregnation of surface deposits with the rubber and the subsequent removal of these deposits with the mold. Cyclododecane was tested as a barrier material on shards of modern terracotta flower pots and tiles of oolitic Indiana limestone. These examples were chosen as typical of the types of surfaces that would be most likely to stain during molding.
3.1 APPLICATION OF CYCLODODECANE
While cyclododecane can be deposited out of organic solvent solutions, our experience, as previously mentioned, indicated that this procedure resulted in the formation of large, needlelike crystals that would not form a consistent barrier film of sufficient homogeneity. While other authors reported success in solvent-borne application, our experiments indicated that a consistent compact layer could be achieved only by applying the melted cyclododecane. Molten cyclododecane applied by brush to a cool surface, however, caused it to cool so rapidly that it remained as a raised layer that would have obliterated surface features during molding. Terracotta and limestone heated to the melting point of cyclododecane allowed it to penetrate and fill the interstitial voids without apparent obscuring of surface detail. This method was employed in the test treatments.
For our molding tests, we chose a silicone rubber (Dow Corning 3110) that has been used extensively in conservation. In keeping with the recommendations of Jeffrey Maish (1994) for least staining, we chose the fast catalyst (no. 4, a tin catalyst). It became immediately apparent that cyclododecane alone would not function as a barrier to silicone oils. It is a nonpolar substance and is probably either penetrated or partially dissolved by the nonpolar silicone oils, and staining was as severe with the cyclododecane film as without it. While this development was initially discouraging, we next tried the addition of thin isolation films of polar materials on top of the cyclododecane. This procedure seemed to provide a promising solution to the problem. When used in this way, the cyclododecane would fill the interstitial voids and prevent penetration of the functional isolation film. This isolation film could thus be very thin and would be easy to remove prior to the subsequent sublimation of the cyclododecane.
3.2 TESTING OF BARRIER SYSTEMS
We chose four water-soluble polar isolation materials for further testing in combination with cyclododecane: gum arabic, polyvinyl alcohol, Aquazol (Poly (2-ethyl-2-oxazoline)) (Chiu and Fairchock 1986; Wolbers et al. 1998), and methylcellulose. These materials were chosen because they would not mix with either the cyclododecane or the silicone rubber and would be readily removable with water.
Previous experiments had indicated that none of these materials, when used on their own, provided adequate protection because they were not completely removable, did not prevent penetration of silicone oil, or both. Low-molecular-weight versions of the synthetic polymers were chosen because it was felt that they would provide the best barriers. Concentrations were chosen that would be fluid enough to be easily applied by brush and dry to a thin film that would not affect surface detail. These isolation films were applied on top of surfaces that had been previously impregnated with cyclododecane, and the mold rubber was cast onto the surfaces immediately. After removal of the mold, the isolation film was removed with water, and the cyclododecane was allowed to sublime in a warmed light box (38�C) that accelerated the sublimation process.
3.3 RESULTS
Results of our tests are summarized in table 2. The use of gum arabic and methylcellulose as isolating layers between the cyclododecane impregnation and the mold material gave visually acceptable results on both the terracotta and limestone samples and provided highly detailed molds of surface textures (figs. 7 and 8). As expected, the unprotected terracotta shard (no. 1) that had been in direct contact with silicone rubber showed a significant staining. The shard that had been impregnated with cyclododecane but had not received an isolating layer before molding (no. 2) was also significantly stained. An isolating film of Aquazol over the cyclododecane (no. 3) did not prevent the penetration of silicone oils into the terracotta, and it proved difficult to remove. When used in conjunction with cyclododecane, methylcellulose (no. 5) and gum arabic (no. 6) showed only barely detectable color shifts. Of these two substances, gum arabic performed slightly better than methylcellulose.
Fig. 7.
Terracotta shards after molding test treatments and sublimation of cyclododecane. 1: no barrier; 2: cyclododecane only; 3: cyclododecane and Aquazol; 4: cyclododecane and PVOH; 5: cyclododecane and methylcellulose; 6: cyclododecane and gum arabic.
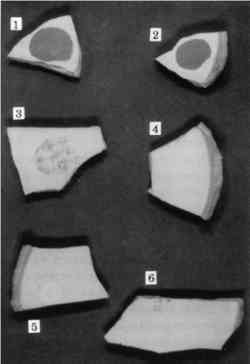 |
Fig. 8.
Limestone samples after molding test treatments and sublimation of cyclododecane. 1: no barrier; 2: cyclododecane and PVOH; 3: cyclododecane and methylcellulose; 4: cyclododecane and gum arabic
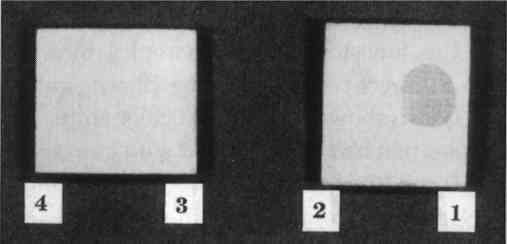 |
TABLE 2. SUMMARY OF RESULTS OF MOLDING TEST TREATMENTS
The limestone control samples that had been in direct contact with the silicone rubber (no. 1) also showed significant color shifts. The samples that had been isolated with gum arabic (no. 4) exhibited slightly darker speckles in the stone surface. Compared with gum arabic and polyvinyl alcohol (no. 2), methylcellulose (no. 3) performed slightly better as an isolating layer when used in conjunction with cyclododecane.
Overall, the results of this study are promising. Protecting the surfaces of porous substrates with a cyclododecane barrier film proved highly effective if an additional isolating layer of methylcellulose or gum arabic was used. Although even the most successful treatments caused very slight darkening of the substrates, this color change was virtually imperceptible and in the experience of one of the authors (Thornton) is an improvement over the results that can be obtained by other isolating strategies. Further, the authors believe that the slight darkening experienced by the successfully treated samples could be potentially eliminated if a second or third layer of the isolating film was applied or a single layer of a more concentrated solution were applied to form a denser isolating film. It is unlikely that either would interfere with the fidelity of the cast except where extremely fine detail is required, for example in the preparation of casts for electron microscopy. While there is hope for further refinement of method, initial results are very promising.
|