ADHESIVE QUALITIES OF CONSOLIDANTS FOR DETERIORATED WOOD
TOMOYASU SAKUNO, & ARNO P. SCHNIEWIND
2 EXPERIMENTAL
2.1 CONSOLIDANTS
THREE TYPES of synthetic resins generally considered suitable as consolidants for degraded wood were used. These were an acrylic (Acryloid B72), a polyvinyl butyral (Butvar B98), and a polyvinyl acetate (AYAT), their properties are shown in table 1. According to the resin-solvent combination, the consolidants were divided into two series, 1 and 2. In series 1, the solvents were of the polar type: acetone for B72 and ethanol for B98 and AYAT. In series 2, the nonpolar toluene was used for B72 and AYAT, while for B98 a 60:40 mixture (weight basis) of toluene and ethanol had to be used since the manufacturer did not list any suitable pure nonpolar solvent. In all cases, the concentration of the solution was held constant at 15% on a weight basis. At this concentration, solutions have sufficiently low viscosity to be suitable for consolidation treatments, since even at 20% concentrations complete penetration could be achieved in small specimens (Wang and Schniewind 1985). Preliminary experiments using solutions of 10, 15, and 20% concentrations did not reveal any significant differences in the resulting bond strength using a tensile shear test. Therefore the entire study was conducted using only 15% concentration. The viscosity of each solution was measured with a Brookfield viscometer.
TABLE 1 Properties of Consolidants
2.2 DEGRADED WOOD
The raw material was from foundation piles buried for about 70 years near the San Francisco waterfront. The properties of these piles are given in detail in a separate report (Schniewind, Gammon, and Bendtsen 1982). The remains of four of the piles, originally numbered 5, 9, 12, and 16, were selected for the present study. The length differed for each pile, ranging from 32 ft for pile 16 to 64 ft for pile 5. From each pile, three sections were selected: one from near the butt, one from the middle portion, and one from near the top (as referred to the tree; since piles are driven top first, the top is the end buried most deeply in the ground). Some representative sections are shown in figure 1.
Fig. 1.
Sections of deteriorated foundation piles
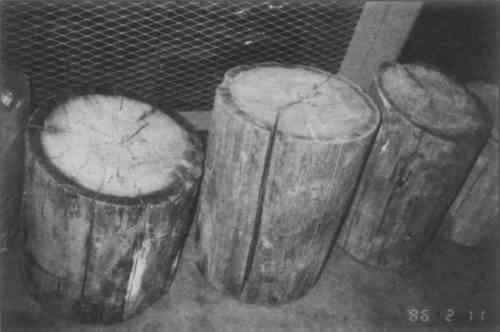 |
2.3 FABRICATION OF ADHESIVE SHEAR TEST SPECIMENS
Material to be used for bonding was, as much as possible, taken from the portion nearest the surface of each pile section and conditioned at 70�F and 65% relative humidity. It was desired to evaluate bond quality by shear tests in both a static and an impact mode of testing. To simplify the process, identical specimens were used for both types of test. The machining process for preparing specimen material is illustrated in figure 2. Note that the face to be bonded was always the face closest to the original surface of the piles, that is, the region with the most severe degree of deterioration. The resulting specimen blanks were planed smooth and cut into pairs of small blocks, one measuring 3/8 � 1 � 1 in and the other 3/4 � 1 � 1 3/4 in.
Fig. 2.
Preparation of test specimens. (dimensions in inches)
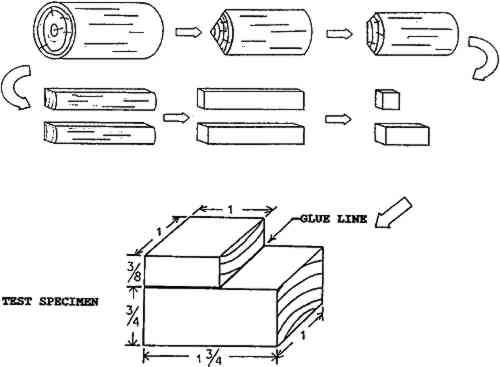 |
These blocks were then bonded together to form test specimens according to ASTM specification D950 (ASTM 1987), using each of the resins with their respective series 1 and series 2 solvents. The resin was applied to both surfaces at a spread of 0.233 kg/m2 of single glue line. The blocks were then tightly clamped and left overnight.
Following the same method, a polyvinyl acetate (PVA) emulsion adhesive, a common woodworking glue (Elmer's White Glue), was also used. This adhesive was used at full strength in order to obtain maximum bond strength for comparison.
Three test specimens (replications) were made for each combination of treatment, pile, and within-pile location. This procedure would have produced a total of 252 specimens each for both static and impact shear tests. However, the top section of pile 16 yielded only enough material for two instead of three replications for the resins with series 2 solvents, which reduced the total to 249 specimens each for static and for impact testing.
2.4 IMPACT AND STATIC SHEAR BLOCK STRENGTH TEST
After conditioning the test specimens for one week at 70�F and 65% relative humidity, impact and static shear strength tests were conducted. The impact shear strength test was conducted following the methods specified in ASTM D950, except that an Forest Products Laboratory toughness testing machine with a modified specimen holder as shown in figure 3 was used. The static shear strength test was made using the same test specimen configuration and a universal testing machine with a standard shear test tool. Testing speed was 0.024 in/min of the movable cross-head.
Fig. 3.
Specimen holder for impact shear tests
 |
|