PENETRATION AND PLACEMENT OF ALKALINE COMPOUNDS IN SOLUTION-DEACIDIFIED PAPER
George B. Kelly, & Stanley Fowler
3 RESULTS AND DISCUSSION
When sheets of paper are soaked in a deacidification bath, the time required for deacidification and the achievement of maximum alkaline reserve is controlled by a number of factors. These include the amount of acid present in the paper, the volume and concentration of the deacidification solution, the sizing on the paper, the porosity of the paper, the surface tension of the solution, the temperature and amount of agitation in the bath, and the number and spacing of the sheets being soaked. No doubt other factors could be stated, but these suffice to indicate the complexity of the process and the opportunities for variable results.
3.1 Rate of Penetration of Alkali in Paper During Immersion Deacidification
Where substantial amounts of acid are present in the paper or the deacidification solution is weak, the initial solution penetrating the paper may be nearly or completely exhausted of alkali. Little or no alkali remains in the liquid contained in the sheet to deposit an alkaline reserve on drying. To achieve the maximum alkaline reserve, time must be allowed for fresh alkaline salt to diffuse into the sheet. This can take a surprisingly long time, particularly with low porosity or thick papers, due to the interference by the capillary network on the diffusion of the fresh solution.
The effect of solution concentration on the time to reach maximum alkaline reserve in the papers from the old book is shown in Figure 1. With solution A (8.5 g/l) the paper was neutralized almost immediately and reached maximum alkaline reserve in about 40 minutes. With solution B (2.13 g/l) neutralization required about 20 minutes and maximum alkaline reserve required about 80 minutes, and, of course, the maximum alkaline reserve was much lower than with solution A due to the lower concentration of the solution. When a wetting agent (methanol) was included in the 2.13 g/l solution (solution C), the times for neutralization and for achieving maximum alkaline reserve were substantially reduced due to the assistance of the wetting agent in penetrating the paper. This illustrates the rather wide variation in time which can be required to achieve the maximum pickup of deacidifier permitted by the concentration of the solution.
In this demonstration, the sizing of the paper and its high acidity combined with the variation in solution concentration to produce widely different results. The addition of the methanol gave a substantial improvement by compensating for the inability of the weaker solution to penetrate the sizing readily.
Under even less favorable combinations of circumstances, such as a less porous or much thicker paper, or restriction of the diffusion of liquid by crowding the papers together in the bath, the time required could be even greater than the maximum time observed here. Therefore, no definite rule for soaking time can be given except to be patient and allow as much time as one can—with the safety of the document in mind—to be certain that the desired alkaline reserve has been achieved. The times shown in Figure 1 will give some measure to judge what might be required.
3.2 Migration During Drying
In considering possible causes for the grainy surface effect in deacidified sheets, it appeared that migration of salts during drying might be a likely candidate. After paper has been soaked to impregnate it with alkali, the alkali should be evenly distributed in the paper. However, as the paper dries, solvent moves to the surface where evaporation is taking place and tends to carry the soluble alkali with it. Thus, the paper may end up containing a higher concentration of alkaline salt near the surfaces than in the interior. Other solids also move with solvents in the paper, as is well known from the appearance of rings or tide marks in spotted or partially wetted papers, particularly old papers.
The distribution of alkali between the drying surface and the interior layers was demonstrated by the simple technique of preparing a stack of very thin tissue papers which were impregnated singly and consolidated while wet into a composite paper by rolling to compress the stack and expel excess solution. The composite dried as a unit but could be separated after drying into the original sheets for individual analysis, and by this means the distribution of the alkali was determined. The results of such a technique for several concentrations of deacidifying solutions are shown in Figure 2. The surface layer (no. 1) contained over three times as much alkali as the least alkaline center layer. As these composites were supported during drying on a glass plate, because of their extremely low wet strength, the concentrations in the bottom layers were not particularly significant. With a drying surface on both sides, the curves would be expected to have a symmetrical U shape, with a similar concentration of alkali at both surfaces.
Fig. 2.
Effect of drying on distribution of alkaline reserve
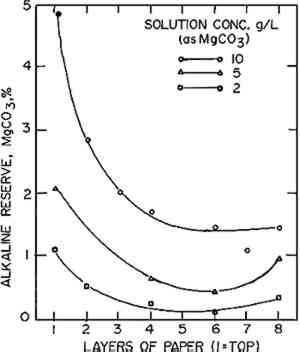 |
The higher concentration of salt at the surface was consistent with the premise that migration could contribute to grainy surfaces. Apparently, under certain conditions migration is either increased or something triggers the growth of unusually large crystals. Either of these could lead to a grainy surface.
If the higher concentration of salt at the surface could be reduced, the formation of grainy surfaces would be much less likely. Therefore, we attempted to flatten the migration curves by variations in the drying technique. Oven drying at 105�C produced a similar curve, with a slightly higher surface-to-interior alkali ratio of about 4.0 and, hence, was no help. It was thought that if the treated paper were heated in a high humidity atmosphere, the carbon dioxide could be driven off, precipitating MgCO3, without changing the moisture content of the paper enough to encourage migration. Neither of the two conditions tried (99% r.h. at 60� C for 1 hour, or live steam at 100� C for 1 hour) was effective in reducing the surface-to-interior ratio below 3.0. In fact, the ratios were much worse, at about 10. Obviously, this was the wrong approach.
Even freeze drying did not completely overcome the tendency to migrate. A composite impregnated with 10 g/l solution and immediately frozen and dried at −40� C in a Vertis freeze dryer under vacuum still showed a tendency to migrate, as shown in Figure 3. There was an improvement in the surface-to-interior alkali ratio, which was reduced to about 1.5:1 instead of 3:1. This was very surprising as we had anticipated that rapid freezing would fix the alkali in place and prevent migration. However, when water freezes it tends to crystallize in pure crystals, excluding impurities so that they concentrate in the unfrozen liquid. Thus, the freezing of the composite on the metal plate, where it would freeze from the bottom up, could have acted to force some of the alkali toward the surface. Even the very rapid freezing (about 2 minutes) was not able to completely overcome this tendency.
Fig. 3.
Effect of freeze drying on distribution of alkaline reserve
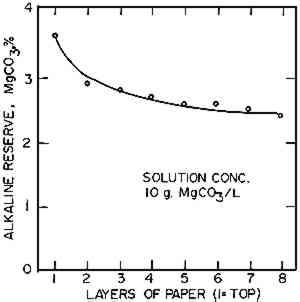 |
It was concluded, at least with magnesium bicarbonate, that there was no convenient way to fix the alkali in a form which would not migrate during the drying of the sheet. However, the tendency could be materially reduced by freeze drying.
3.3 Modifying the Location of Alkali Within the Paper
While we were unable to fix bicarbonate in place after impregnation by soaking, we were able to precipitate an alkali (calcium carbonate) in the center of the composite sheet by a variation of the previously published double decomposition technique.6 In this variation, calcium chloride and ammonium carbonate solutions were introduced simultaneously from opposite sides of the sheet and calcium carbonate precipitated. The excess reactants were then removed by washing. The distribution of alkali in the composite is shown in Figure 4. Here the bulk of the alkali is in the interior of the sheet, with very little at either surface.
Fig. 4.
Distribution of alkaline reserve with controlled double decomposition treatment
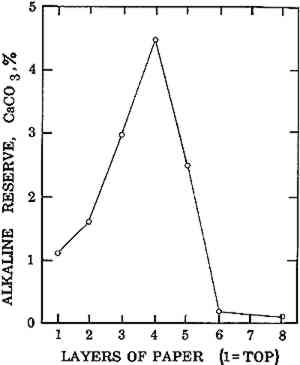 |
These two techniques demonstrate the ability to place the bulk of the alkali either in the center of the sheet or near the surface. However, a uniform distribution does not appear to be feasible at this time. Of the two possible placements, the surface deposition obtained by the usual soaking and drying appears to offer the best protection against atmospheric pollutants, as well as being the simplest operation. However, it may lead to occasional grainy surfaces.
The grainy surface can be removed in either of two ways: 1) The sheet can simply be returned to the deacidification bath where the deposit will be redissolved slowly. The sheet can then be dried between blotting papers which will absorb the excess of migrating alkali and leave the surface free from the grainy deposit. 2) Alternatively, the surface deposit can be washed off with water and the sheet redried. Of course, either of these two methods reduces the amount of alkaline reserve left in the paper, but one frequently has to choose between undesirable alternatives.
The fact that the grainy surface appears only irregularly even in concentrated deacidification baths is still puzzling, and we are continuing our study to determine what triggers its appearance.
3.4 Effect of Solvent on Non-Aqueous Deacidifiers
Non-aqueous deacidification agents are used widely for treating water-sensitive documents, and even for non-sensitive documents where the solution's fast drying saves time. In the use of these agents, we have noted that application from one side alone does not always alkalize the far surface, particularly if the specimen is thick, moist, or highly humid.
When non-aqueous deacidifiers like magnesium methoxide or methylmagnesium carbonate are used, the solvent can materially affect the penetration of the alkalizing agent. Figures 5 and 6 show the capillary rise of the solvent and alkaline solute in filter paper strips after a 15 minute immersion of one edge in the deacidifying solution. When the solvent is pure methanol, the deacidifying agent remains substantially with the solvent front in advancing up the strip. However, when the solvent is diluted with Freon TF, as is commonly the case in deacidification work, separation can occur. The solvent front advances up the paper normally but the alkalies, magnesium methoxide and methylmagnesium carbonate, are substantially retarded, leaving a significant gap between the solvent front and the alkali front in the strip. Magnesium methoxide appears to be somewhat less mobile than methylmagnesium carbonate in these tests.
Fig. 5.
Capillary penetration of alkaline salt with a good solvent
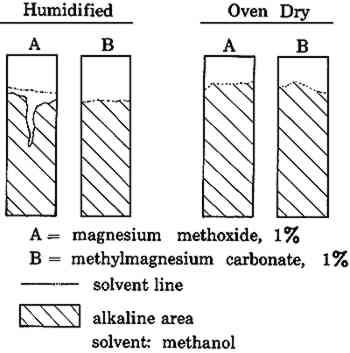 |
Fig. 6.
Capillary penetration of alkaline salt with a poor solvent
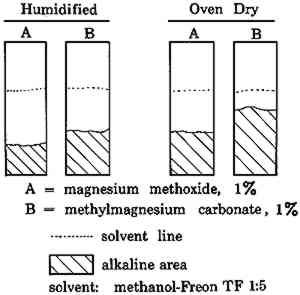 |
Even when solution penetration is limited to the small distances involved in document treatments, a significant separation of the alkali and solvent fronts can occur. The same separation was demonstrated with blotting paper 0.026″ thick. Brush application of a 1% methanol-Freon solution of methylmagnesium carbonate to one face of the blotter until the other face was thoroughly damp raised the pH of the application side to 9.1, while the pH of the opposite side remained at 6.7. Splitting the blotting paper indicated that no alkali penetrated further than 0.020″, and most did not penetrate further than 0.015″. With pure methanol solvent, complete penetration of the blotter was obtained.
In methanol, the two deacidification agents are highly associated with the solvent molecules, and move readily with the solvent front. However, both deacidifying agents are insoluble in Freon TF by itself. As methanol is diluted with Freon TF, the solvent mixture becomes less able to hold the deacidification agent in solution. With the poorer solvent, the forces to pull the solute along with the solvent front are much weaker, and the adsorbtive forces of the cellulose molecules retard the motion of the alkali while permitting the solvent to advance.
Possibly the solvents themselves are partially separated by the passage through the filter paper, because an intermediate solvent front located between the alkali front and the main solvent front became visible as the strip began to dry. Since the Freon TF is the more volatile of the two solvents, it evaporates more readily. The second front, therefore, appears to be the beginning of a higher concentration of methanol than is present in the main solvent front.
Not all of the retarding forces are physical in nature; chemical depletion can occur as well. Moisture in humidified papers reacts with the organic magnesium compound and precipitates it, causing depletion of the solution.
In cases where the inks in a document are not affected by methanol, the lagging behind of the alkali can be avoided or minimized by using pure methanol as the solvent and by oven drying the paper7 before treatment. In other instances, the lagging behind of the alkali front can be used to advantage in treating art works that have alkali-sensitive colors. In such cases, the application of the deacidification solution in methanol-Freon solvent mixtures to the back of the art work can substantially deacidify the bulk of the substrate without penetrating the front surface where the alkali could change colors. The deacidified back and center of the paper will be stabilized and may serve to hold together a deteriorating and unprotected surface, and thus maintain the art work for a longer period than would otherwise be possible.
|