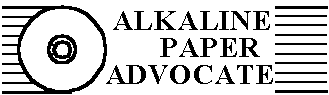
Volume 5, Number 1
Mar 1992
News
Other Things You Can do with Waste Paper
- Engineers from the Sullivan Machinery Co. near Sydney,
Australia, have found a way to make biodegradable coffins from waste
newspapers. They look very much like traditional wood ones, and
sell for E500 each. [This news, appropriately enough, appeared in a
packaging journal, Monitor (Packag.), no. 1,
1991.1
- The Wall Street Journal for September 27-28, 1991, reports a
patented new process to make woodlike blocks out of waste paper and
water. No adhesive is needed, though additives can be used, such as
color, fire retardants and insect proofing. The blocks can be
sliced or sanded. The process was developed at Gustavus Adophus
College, St. Peter, MN.
- The U.S. Department of Agriculture Forest Products Laboratory
has investigated recovery of fibers from towns and industries and
the alternative uses they might be put to: production of composite
materials, composting with paper mill sludges to make potting soil,
and energy generation (from waste wood and refuse), among other
uses. (From "Alternative Uses of Recovered Fibers," by T.E. Hamilton
et al, paper presented at "Focus '95+: Landmark Paper Recycling
Symposium," March 1991, Atlanta. TAPPI Press, 1991, $80.)
Recent Developments in the Industry
- Seven wood-containing machines have been converted to alkaline
and five more are in the process of converting, according to Jerry
Pflieger of OMYA, a supplier of calcium carbonate. Peter Duncan,
president of OMYA.says that about 60%-65% of Europe's
wood-containing capacity has been converted. More information on
this, and on the various advantages of alkaline papermaking, are in
a paper by Charles E. Swann in the American Papermaker for February
1992: "More Mills Switch to Alkaline to Improve Quality and Cut
Costs."
- It is now possible to make printing and writing papers that are
made up of two or three layers of fibers. They are called
"stratified," "multi-ply" or multilayer grades, and have been used
for packaging, linerboard and tissue in the past. The idea is to
put the best layers on the outside, so that a cheaper fiber (e.g.,
CTMP) can be used on the inside. All three layers can now be made
at the same time with a special headbox.
At the time this procedure was published in Tappi Journal, only one
mill was known to be using this process for printing and writing
papers ("Stratification of Paper Grades," by John H. Harwood, May
1990, p. 115-122). That mill was located in Norway.
- A reusable coated paper that can be erased with heat has been
invented by a small German company, ETIP GmbH, which has its U.S.
offices in Freeland, Washington. The paper is fed into a $75
machine and comes out clean, ready for reuse. There are some kinds
of inks that cannot be erased, however. The paper will probably
cost 404t a sheet, and each sheet can be reused about 50 times
before it wears out, company officials claim. The first products
based on this technology are expected out this year. (More
information in the San Francisco Chronicle for August 17,1991.)
- Conditions under which ozone bleaching works best are discussed
in the November Pulp & Paper, in an article by
Howard Deal, "Environmental Pressure Causes Change in Bleaching
Technologies, Chemicals." If the ozone is not properly controlled,
it can destroy the cellulose, but at a pH between 1.0 and 4.0
(achieved by acetic acid), good control is possible. Temperatures
between 80' and 140'F are used for a short time, less than 10
minutes.
- A two-part survey of the use of ozone in bleaching pulps is in
the January and February issues of Tappi Journal.
- Ozone has been used in paper conservation to bleach documents,
using a special piece of equipment that was marketed a few years ago
in England, but its use is not generally condoned, because of its
destructive potential.
Non-Wood Fibers
- An organization called Ecologically Sound Papers, based in the
UK, is arranging to have a hemp-based paper produced. They chose
hemp because it produces long fibers, is an annual plant grown
throughout Europe, has a low lignin content (4%) and a low nutrient
draw-up from the soil. The paper will be manufactured by William
Sommerville & Son. (From Pap. Eur., v. 3, no. 7,
Oct. 1991, p. 8)
- Barriers to use of kenaf fiber in papermaking were described by
panelists at the 1991 TAPPI Pulping Conference in November. The
report, on p. 260-261 in the February Tappi Journal,
helps explain why kenaf is taking so long to be adopted as a fiber
source for papermaking. For one thing, it is an annual crop, so it
has to be stored for most of the year before use, and the problem is
to prevent deterioration in storage. (It is bulky, so it has to be
stored outside.) Farmers do not want to grow kenaf because it is not
as profitable as other crops. The new investment in handling and
processing facilities is too large to displace wood, and the costs
of production can be even higher than for wood. Wheat straw was
suggested as an alternative, because it is readily available as an
agricultural by-product, and it makes good newsprint.
On the other hand, according to one participant, time is on the side
of kenaf because ways of growing and using it will become more
efficient, while wood pulp will continue to grow more
expensive.
Nonwood pulp stocks available on the market are listed in
Lockwood-Post's Directory: cotton linter, bagasse, bamboo, esparto,
flax, jute, rag, rope and straw. Some of them are imported from
other countries. But no kenaf.
![[Contents]](/byorg/abbey/ap/img/contbtn.gif)
![[Search]](/byorg/abbey/ap/img/srchbtn.gif)
![[Abbey]](/byorg/abbey/ap/img/abbbtn.gif)