THE USE OF CYCLODODECANE AS A TEMPORARY BARRIER FOR WATER-SENSITIVE INK ON ARCHAEOLOGICAL CERAMICS DURING DESALINATION
VANESSA MUROS, & JOHN HIRX
2 WORKING PROPERTIES OF CYCLODODECANE
Prior to beginning any of the tests on modern samples, the working properties of CDD were examined. Several published studies (Br�ckle et al. 1999; Hangleiter 1999; Stein et al. 2000) discuss the structure of formed films of CDD using different application methods and how the application methods affect the material's properties and behavior. Many of the published examinations and tests that examined CDD's working properties were repeated for this study (appendix 1), some with slight modifications, to ensure that the same results would be obtained using a different substrate or additional application methods. The results of these studies were used to determine the protocol for the bench tests on modern terracotta samples and to focus the testing on those application methods expected to produce the best protective barriers for the water-sensitive ink.
2.1 APPLICATION METHODS
Cyclododecane (C12H24) is a cyclic hydrocarbon that appears as a waxy solid. It has a melting temperature of 58–61�C (J�egers and J�egers 1999), and with low heat can be applied to surfaces as a melt. It is soluble in a range of nonpolar solvents, allowing it to be applied in solution. It can also be purchased as an aerosol spray (Hangleiter 1999).1 The application method used can affect the structure of the CDD films produced, which in turn affects the behavior of the film. It is important for conservators to be aware of the characteristics of CDD films in order to determine which application method will produce the most suitable film for the desired treatment and end result.
Previously published examinations (Br�ckle et al. 1999; Stein et al. 2000) have found that melting CDD on a glass slide produced a dense, compact layer of small acicular crystals. Solvent applications produced films with an open network of these crystals. The faster the solvent evaporated, the smaller and more tightly packed the crystalline structure formed. Added to the authors' examinations (fig. 2) was the aerosol spray film, which was made up of very small, slightly rounded crystals with spaces in between (appendix 1.1). From these evaluations it seems that the most effective, and least permeable, barrier would be made by those application methods that produce denser films with smaller crystals tightly packed together, such as the melt film or CDD in fast-evaporating solvent solutions. The spaces visible in some CDD solution-based films or the aerosol spray film may potentially allow water to permeate the CDD barrier and damage water-sensitive ink.
2.2 PENETRATION INTO POROUS SUBSTRATES
Tests have found that the application method can affect how deep CDD can penetrate into the substrate to which it is applied. Stein et al. (2000) learned that when comparing stone samples coated with cyclododecane as a melt and in solution, the solution tended to travel farther into the samples than the melt did. Warming samples prior to coating with molten CDD can help increase the depth of penetration
Fig. 2.
Crystalline structure of cyclododecane applied in various forms: (A) in petroleum ether, (B) in mineral spirits, (C) in dichloromethane, (D) in toluene, (E) as a melt, (F) as a spray (magnification 40x). Note how the slower-evaporating solvents, such as mineral spirits and toluene, formed long needlelike crystals with spaces in between each of them. Faster-evaporating solvents formed smaller crystals, in a tighter, less porous, crystal network. The melt appears to be made up of small crystals formed closely together creating a compact, dense film. The spray film seems to be comprised of small, globular crystals rather than acicular ones like the other films.
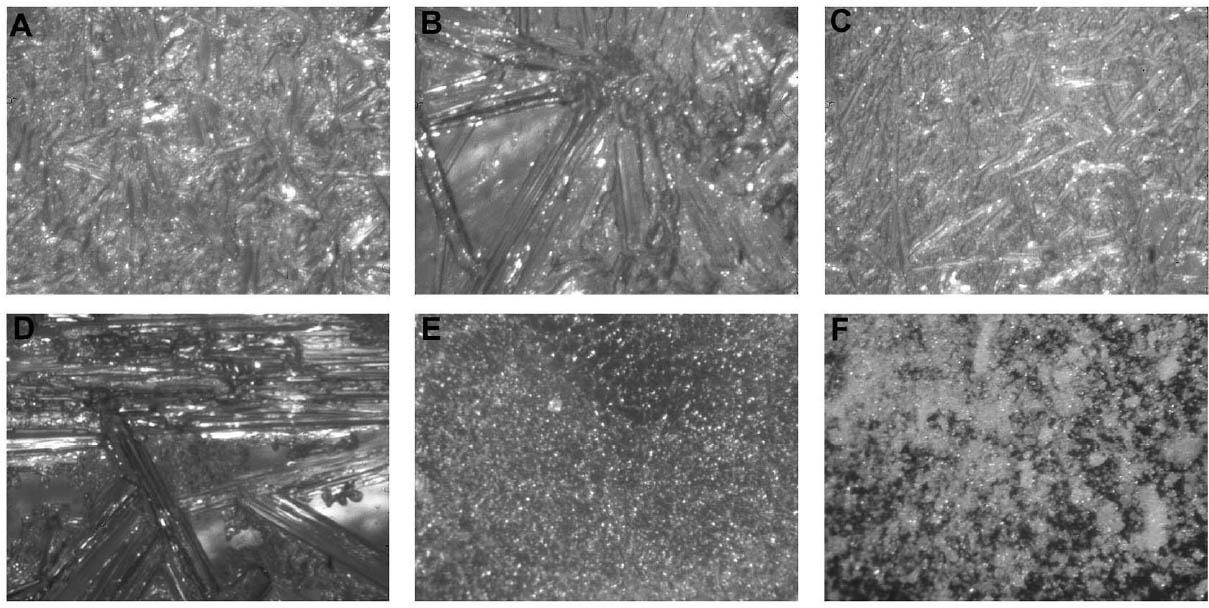 |
(Riedl and Hilbert 1998). Similar tests, after Stein et al. (2000), were conducted using terracotta samples to determine if a different substrate affected how far CDD penetrated. Unglazed terracotta samples, about 7 mm thick, were used for the tests. A 3 x 2 cm area on the surface of each sample was coated with CDD, as a melt using a heated spatula, in petroleum ether and the aerosol spray. To measure the depth to which CDD had penetrated into the sample, a “wettability test” was used (Kumar and Ginell 1997). After coating, the samples were cut in half, and the cross section was “wet” with a watersoluble dye. Colorhue Instant Set silk dyes were used as the indicator. Since cyclododecane is hydrophobic, the treated areas would not absorb the dye. The undyed section indicated the presence of cyclododecane and was then measured.
The results obtained were similar to those previously published (table 1). The aerosol spray, added to the authors' tests, appeared only to sit on the surface, and the depth of penetration could not be measured.
For the purposes of this study, the CDD would need to travel far enough into the sample to completely coat or encapsulate the inscription so that no damage could occur even from the action of water underneath, or behind, the inscribed area. Since the aerosol spray film appeared to sit on the surface, it was thought that this application method would not produce an adequate barrier because it would not coat the inscription sufficiently. CDD as a melt or in a solvent solution could be used since both seemed to penetrate deep enough into the samples to completely coat any ink on the surface.
2.3 SUBLIMATION RATE
The sublimation rate of CDD has been found to be greatly affected by the method of application used, in addition to factors such as the surrounding air temperature, humidity, and ventilation (Hiby 1997). In tests where limestone and sandstone samples were coated with cyclododecane, the coating formed from the melt took two to three times longer to sublime than those applied in solvent form (Stein et al. 2000).
Table .
Depth of Penetration of Cyclododecane (CDD), Applied in Various Forms, into Terracotta Samples
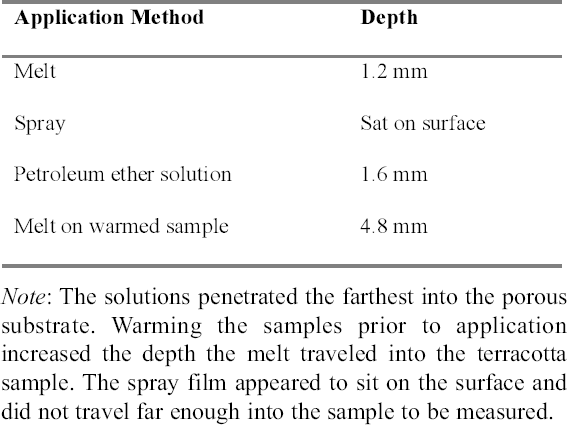 |
Examining the pore structure of plaster samples coated with CDD using a cryo-scanning electron microscope (SEM), Riedl and Hilbert (1998) found that a film of CDD from solution took five months to completely sublime, while the melt can take approximately nine months to completely sublime.
Sublimation tests similar to those conducted by Stein et al. (2000) were repeated applying CDD on glass slides and terracotta samples (appendix 1.2). The sublimation rate of the aerosol spray film was included in these tests. The authors' results were similar to those of the investigations discussed above (table 2). The aerosol spray film was the first to sublime, possibly due to its superficial penetration exposing it more to the air, and to its less dense film formation. The solutions were the next to sublime, where CDD in petroleum ether took longer to sublime than the mineral spirits solution. This is perhaps due to the differences in the formation of the solid films. The film produced by the melt took the longest to sublime because it forms as a very dense film of small, tightly packed crystals. In treatments that may occur over long periods of time, it is important to understand the sublimation rate of the application method chosen to ensure that the CDD film is not compromised.
2.4 RESIDUES
Though cyclododecane sublimes over time, recent analyses have found that some residues can remain within the coated material (Caspi and Kaplan 2001). Using various analytical techniques, residues of materials chemically related or similar to cyclododecane have been found within ceramics and on the surfaces of glass slides. The residues appear to come from impurities in CDD as a result of the manufacturing process. Caspi and Kaplan also found that the
Table .
Rate of Sublimation of Cyclododecane, Applied in Various Forms, from Glass Slides and from Terracotta Samples
 |
residues varied based on the manufacturer and the batch of CDD used. The conclusion drawn from these analyses was that the residues were present in such minute quantities and were chemically similar enough to CDD that they would not harm the object.
Tests were conducted by the authors to determine whether the batch of CDD used for these tests contained residues. Glass slides were coated with CDD as a melt, in various solutions and from the aerosol spray, based on the methodology of previous residue tests (Caspi and Kaplan 2001; Maish and Risser 2002). All slides exhibited white tidemarks after the sublimation of all the CDD films. Glass slides coated with only solvents also produced these tidemarks, likely due to impurities in the solvents. Therefore, the tidemarks seen on the slides are the result of impurities in the CDD and/or solvents, depending on the application method. Tidemarks like those seen on the slides were not visible on the surfaces of the terracotta samples coated for earlier examinations, but it is assumed residues are present within the samples. Testing and treatment using CDD will continue based on the conclusions of Caspi and Kaplan (2001). Future investigations and analysis, however, should be encouraged to further determine the effects of these residues, if any, on objects coated with cyclododecane.
|