THE CONSERVATION OF AMERICAN WAR MEMORIALS MADE OF ZINC
CAROL A. GRISSOM, & RONALD S. HARVEY
2 FABRICATION
The principal advantage of using zinc for monuments was that this dull, gray metal could inexpensively be made to imitate bronze or stone. Application of paint or other surface treatments, however, made zinc an “invisible” metal. Today zinc remains almost unknown to the general public and even to conservation professionals. Zinc statues are frequently misidentified as lead or cast iron since all three are “white” metals. In fact, lead can be readily differentiated because it is easily scratched, and iron can be distinguished because it is magnetic.
Cast iron was zinc's chief competitor for low-cost statuary in America. At first, zinc fountain statues like Antonio Canova's (1757–1822) Hebe, first produced in marble in 1796, probably copied cast-iron statues made slightly earlier by companies like the Philadelphia firm of Robert Wood & Company (Hinckley 1853). Use of zinc for fountain statues quickly superseded cast iron, however, because zinc was so easily cast and joined with ordinary lead-tin solder. Before the development of welding at the end of the 19th century, cast-iron statues had to be laboriously made by bolting pieces together; alternatively, they could be cast whole, which required complex molding or pattern making. Cast iron remained in use for statuary only when its advantages of weight and strength were important. For instance, Jockey, Chinaman, and Darkey hitching posts were made exclusively of cast iron. Identical statues cast in zinc had more limited uses as trade signs for stables and teahouses, as well as for the New York City premises of the statue's purveyor, J. W. Fiske (Fried 1970). Cast-iron animal statues also may have continued to outnumber their zinc counterparts because their ruggedness made them more suitable for display on lawns.
American zinc statues were fabricated using three techniques. The most common was to assemble small sand-cast pieces with lead-tin solder. Surfaces of soldiers fabricated in this way were almost invariably painted to simulate bronze. A second type of statue was described by its producers as made of so-called white bronze, a material distinct from real (copper alloy) bronze. White bronze was produced only by the Monumental Bronze Company in Bridgeport, Connecticut, or affiliates with similar names and mostly used for tombstones and cemetery statues. White-bronze statues were carefully made so that joins were unobtrusive, and surfaces were sandblasted to achieve matte finishes that had the “appearance of a superior sort of stone” (Schuyler 1878, 7). A third technique, stamping statues in sheet zinc, was used mostly for architectural statues. These could be purchased for even less than cast statues. Only one sheet-zinc soldier has been located, however, probably because identical soldiers made from sheet copper could be purchased for only a little more money. Supporting armatures are always found inside sheet-zinc statues, while they are rarely used inside those made of cast zinc.
2.1 PAINTED CAST-ZINC STATUES
Contemporaneous publications describing fabrication of painted cast-zinc statues in America are almost nonexistent. The archives and recollections of the last president of a company that sold them have proven to be invaluable resources (Fiske 2000; Israel 2000). Another source of information on production has been evidence found on the statues themselves.
The earliest known zinc soldiers were made for the City of New York Civil War Monument (1869) in Brooklyn's Green-Wood Cemetery: an Infantryman (fig. 1), Cavalryman, Artilleryman, and Engineer. Contemporaneous photographs and remnants of copper plating provide solid evidence that the statues originally imitated bronze (Richman 1998). Moreover, the statues are replicas of four bronze statues on an earlier City of New York Civil War Monument (1866) at Calvary Cemetery in Queens. While no further copies of three statues are known, the Infantryman was a popular figure standing at parade rest, wearing a greatcoat, and steadying his rifle with the fingers of his left hand dangling over the end of the barrel. The statue was reproduced at least once in zinc (for White Plains, New York) and four times in bronze (for Wilmington, North Carolina; Ossining, New York; and Clinton, and Lawrence, Massachusetts). It also seems to have been the model for two slightly different versions sold through trade catalogs in later decades (see below). M. J. Power (1836–1902) cast the bronze statues for the City of New York Monument in Calvary Cemetery, and later bronze copies of the Infantryman bear his foundry mark. The founder for the zinc statues at Green-Wood Cemetery is undocumented, but Seelig is the most likely candidate. During the 1850s the immigrant sculptor had established a zinc foundry in Williamsburg, just across the East River from New York City, and verbal tradition among his descendants supports attribution of the soldiers to his foundry (Sammel 2002). The sculptor is unknown, but the statues bear considerable resemblance to the work of Buberl. Moreover, Buberl is known to have worked with Power and modeled several zinc statues cast by Seelig, including a colossal Robert Fulton (1872) for the Fulton Ferry landing in Brooklyn, now in the Museum of the City of New York.
Recent bronze replication afforded an opportunity for close examination of the Green-Wood Cemetery statues at Modern Art Foundry in Queens, New York. During deinstallation at the cemetery, the
Fig. 1.
Infantry, City of New York Civil War Monument (1869), copper-plated cast zinc, Green-Wood Cemetery, Brooklyn, N.Y. Photograph by Carol A. Grissom
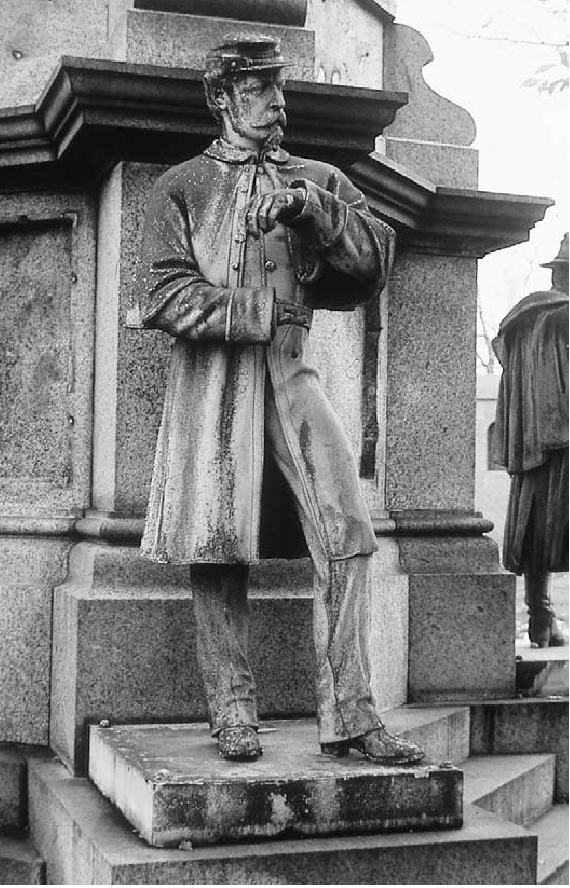 |
Infantryman came apart at the waist, revealing a Roman join. Several inches of the lower edge of the upper body fit like a sleeve over the upper edge of the lower half, fixed with pins at intervals around the waist. Disassembly also showed a pair of wrought-iron bars extending from the waist to below each heel. The location of joins revealed how patterns were made for casting. Each leg, for instance, has seams at the center front and back, indicating that patterns were made by bisecting each leg of the model, which was probably made of plaster. Each half of the leg model would then have been rammed in sand and removed to create a void for “flat casting,” as it is known in modern foundry parlance (Spring 2001). In contrast, legs of the identical bronze statues at Calvary Cemetery were cast as integral units. Fabrication of the Green-Wood statues differs in several respects from later zinc statues. Pattern pieces were larger and thicker than for the later soldiers, and Roman joins and armatures have not been found subsequently. Copperplating on the Green-Wood Cemetery statues, revealed only after surfaces had been cleaned at the foundry, is also unique for zinc Civil War soldiers. It supports the hypothesis that Seelig was the fabricator since he is known to have had experience with making electrotypes (Stiles 1884). While European statues were often copperplated after about 1850, the only other American zinc statues known to be plated are 20th-century religious statues sold by the Daprato Statuary Company, referred to as “orbronze” (Daprato 1921). The earliest known group is a Crucifixion erected in 1916 in Brookville, Indiana, and the earliest known Daprato catalog showing orbronze statues is dated 1921.
In subsequent decades, slightly different versions of the Green-Wood Cemetery's Infantryman were sold through catalogs by J. W. Fiske and the J. L. Mott Iron Works, known in about 10 copies each. Principally purveyors of utilitarian ironwork, the two New York City companies had sidelines in fountains with cast-iron basins that incorporated zinc statues, and they marketed individual zinc statues as well. Both companies seem to have obtained statues from a zinc foundry, which cast their models, sold them statues “off the shelf,” or both. J. W. Fiske used M. J. Seelig & Co. for casting statues by 1892 (Seelig 1892; Fiske 2000), and in 1927 Seelig scrapped Fiske's patterns for the Civil War Soldier on the company's behalf (Seelig 1927). No documentation has been found regarding Mott's source for zinc statues, but nearly all statues in a Mott catalog of 1873 are listed in a contemporaneous Seelig catalog (1876), supporting the Seelig foundry as the source during those years.
J. W. Fiske's soldier (fig. 2) was almost certainly modeled before the Mott statue, since the 1875 dedication of a copy in Saratoga, New York, is well documented. The name of the statue's modeler—Allicot—has been found in Fiske family papers (Fiske 1941) and can be plausibly identified with Henry J. Ellicott (1848–1901) since the statue resembles other works by the sculptor, e.g., the First Pennsylvania Cavalry Monument (1890) at Gettysburg. The figure
Fig. 2.
J. W. Fiske's Grand Army of the Republic Fountain (1893), imitation bronze paint on cast zinc, Pottstown, Pa. Photograph by Carol A. Grissom
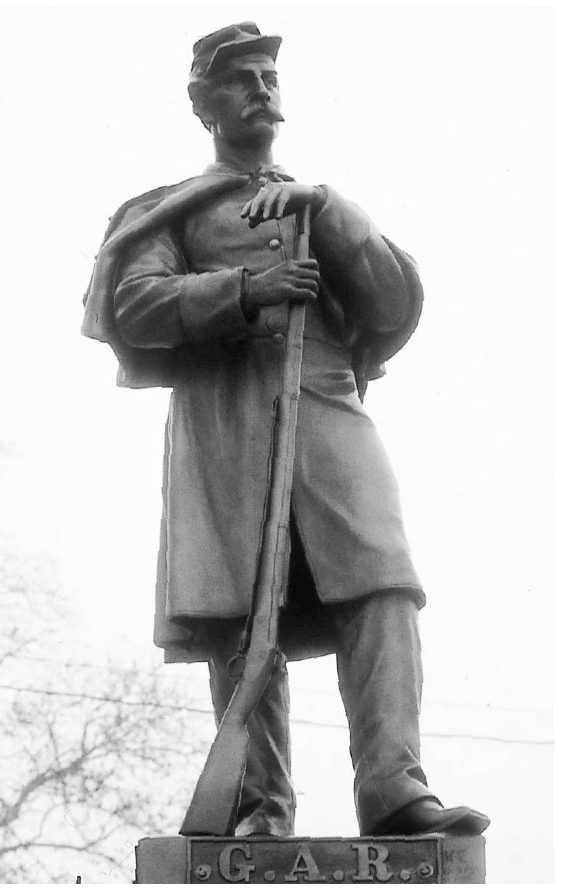 |
differs in small ways from the earlier Green-Wood Cemetery Infantryman. The cape of the Fiske soldier's greatcoat, for instance, is thrown over the proper right shoulder, and the figure no longer sports a goatee. J. W. Fiske threatened penalties for use of its statue patterns by others (Seelig 1892), probably forcing the J. L. Mott Iron Works to obtain another statue in response to heightened demand for Civil War memorials about 25 years after the conflict (fig. 3). The first documented dedication of a Mott soldier occurred in 1888, and it has not been found in company catalogs until 1890. The Mott statue is a more exact but awkward copy of the Green-Wood Cemetery Infantryman. In many other instances, Fiske and Mott sold identical statues of the same subject, probably obtained from Seelig's inventory. Copies of
Fig. 3.
J. L. Mott Iron Works–type Civil War soldier on cast zinc. Photographs by Carol A. Grissom: a. Grand Army of the Republic Civil War Monument (1888), showing remnants of dark-colored paint, Woodlawn Cemetery, Bronx, N.Y.; b. Union Sentry (ca. 1895), polychromy, West Lafayette, Ind.; c. Civil War Private (1891), glossy commercial bronze paint, Lebanon, N.H.
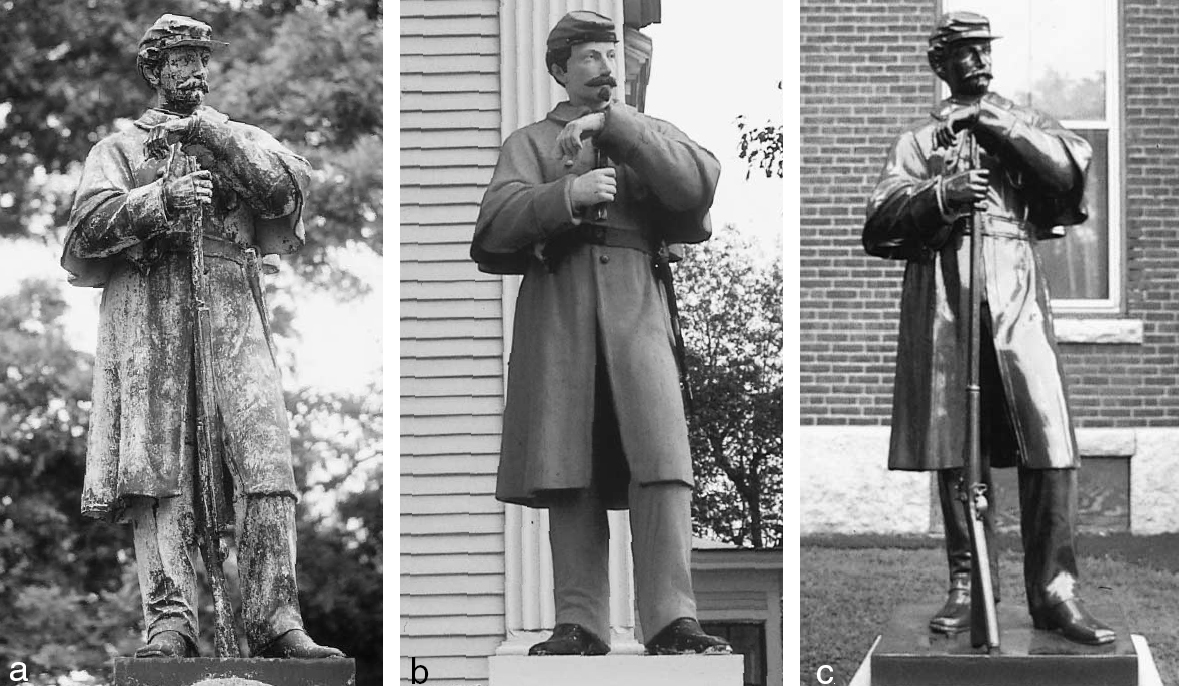 |
a popular Indian Chief that bear Fiske and Mott foundry plaques, for example, display identical seams and measurements. The Indian Chief seems to have been first cast by Seelig (1876) as a cigar-store Indian for another company that sold merchandise for tobacco shops. Wm. Demuth & Co. had entered it “according to Act of Congress in the year 1872… in the office of the Librarian of Congress” (Fried 1970, 54).
J. W. Fiske's statues were mainly cast in sand using zinc patterns, which could be used an almost unlimited number of times (Wilkinson 1871). Cast-iron piece molds were also made for slush-casting portions of Fiske's statues, such as a small head, although there is no evidence of this form of manufacture in the case of Fiske's soldier (Fiske 2000). The patternmaker placed seams where it was convenient for molding and casting instead of where they would be unobtrusive, since statues were to be painted. From the 1930s until zinc statues were no longer sold by the company in the 1950s, cast pieces arrived from the foundry at Fiske's Manhattan offices packed in burlap bags inside wooden barrels (Fiske 2000). There, facilitated by marks that had been struck across joins on interior surfaces of the patterns, they were soldered together by workmen in the subbasement. Mott's statues are similar to those of Fiske in terms of fabrication, and soldiers sold by both companies were customized with genuine gilt-brass army buttons soldered to the zinc. Presumably obtained by the foundry from those available in New York City, buttons on a J. W. Fiske statue in Pottstown (fig. 4) are those of New York state militia rather than the local Pennsylvania regiment (Albert 1976).
Both Mott and Fiske soldiers were available “painted one coat” (probably a primer) or, for a slightly higher price, “bronzed” (Mott 1890, 1901, 1911; Fiske ca. 1908–15). According to 19th-century documents, Fiske sent a workman to “bronze” a fountain on-site in the New York area (Fiske 1893), and analyses have shown that this treatment consisted of the successive application of white lead paint, reddish brown paint, and copper flakes in a clear medium, topped by varnish (Grissom 1994). Microscopic examination of original bronze paint from the Pottstown soldier revealed three layers, with the middle layer containing copper flakes dusted on still-wet lacquer (Lins 1996). From at least the 1930s through the 1950s, statues were painted in Fiske's
Fig. 4.
Detail of fig. 2, showing gilt-brass buttons before recent repainting Courtesy of Dennis Montagna
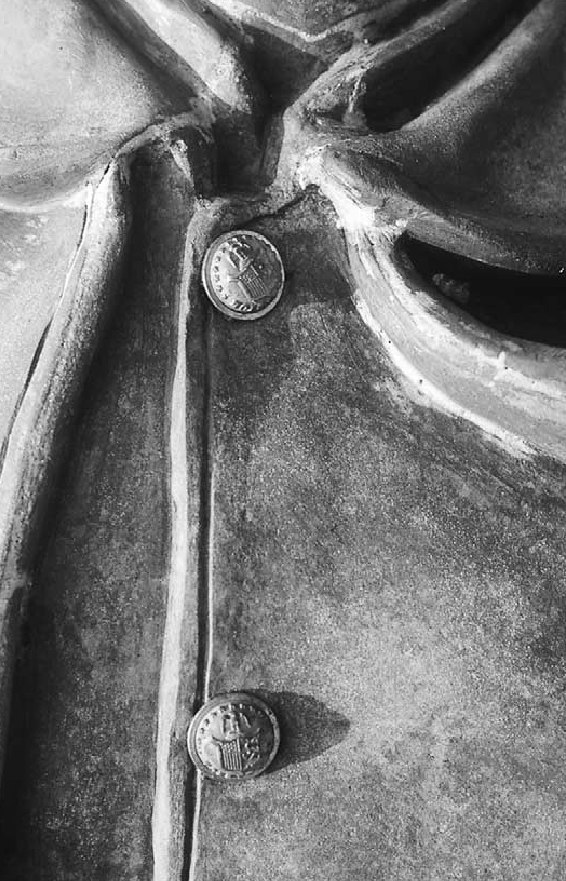 |
basement prior to shipping them to customers, although by then the practice of “bronzing” had ceased in favor of the application of stippled green-and-black paint (Fiske 2000). A few soldiers are now painted naturalistically, such as those at the Old Soldiers Home in West Lafayette, Indiana (see fig. 3b), but no records have been found that indicate this paint was an original treatment. Most painted soldiers were placed on stone pedestals, but at least five originally stood atop cast-iron fountains. Catalogs document that fountain bases were also available bronzed, and cross sections of paint from the Pottstown statue's base showed that the earliest layers were comparable to those of the bronzed statue. A light-colored sand paint imitating stone was applied to the base afterward, however, and this treatment has been repeated to the present day. A Spirit of the American Doughboy in Winchester, Massachusetts, was reportedly electroplated with copper when erected (Bronnet 1997), although this claim has not been confirmed.
2.2 WHITE-BRONZE MONUMENTS
White-bronze monuments and statues were sold only by the Monumental Bronze Company; its predecessor, Schuyler, Parsons, Landon, & Co.; and affiliates: the Detroit White Bronze Company; the Philadelphia White Bronze Company; the American Bronze Company in Chicago; the Western White Bronze Company in Des Moines, Iowa; and the St. Thomas White Bronze Company in St. Thomas, Ontario (Rotundo 1989). White bronze was promoted as the latest scientific achievement, and articles about it appeared in contemporary scientific journals (Scientific American 1885; Saw 1910). Considerable documentation of the companies' unique fabrication processes is also provided in advertising (Schuyler 1878; Monumental Bronze 1882; American Bronze ca. 1891; Western White Bronze 1893). The following is taken from the American Bronze Company (ca. 1891, 9) catalog:
The designs are first modeled in clay and reproduced in plaster of Paris, from which a wax cast is taken, this cast being necessary in order to procure a perfect metal pattern, from which the monument is moulded and cast in the ordinary way. The fusing and joining together of the different parts by pouring molten metal of the same material as the castings, at a high degree of heat, along the joints, makes them practically one solid piece.
Joining zinc with zinc is unusual, not otherwise done in the United States or Europe. Molten zinc does not adhere well to cast zinc, and the deposits of molten metal had to be quite thick in order for pieces to be successfully joined. Sometimes the strategy seems to have been to key pieces in place mechanically. During treatment at Modern Art Foundry, for instance, a Confederate soldier from Suffolk, Virginia, was found to have 20 cm of solid metal inside the lower legs, apparently for attaching it to the base. The underside of the base revealed that a cast-zinc bar had been placed at the center of each hollow foot and lower leg. Molten zinc was then poured around it four or five times, filling remaining space and locking the leg in place. Analyses have shown that the Monumental Bronze Company and its affiliates used zinc of high purity (Grissom 1994), and white-bronze monuments are consistently well made. Areas where a rare casting flaw occurred were apparently drilled out. Zinc was poured into the gap from the back, resulting in a spot distinguishable by slightly different coloration on an aged exterior surface. Edges of white-bronze castings were placed in the least obtrusive locations and carefully finished, permitting surfaces to remain unpainted with minimally visible seams. The recently patented technique of sandblasting was used to achieve matte, stonelike surfaces (Tilghman 1870). No coatings were applied, and subsequent surface corrosion was considered desirable, contributing further to the imitation of stone. White-bronze statues have no armatures, and the self-base of soldiers is usually hollow, thereby fitting like a sleeve over the top section of a white-bronze base. Nonetheless, vertical zinc stiffeners have been found spanning the inside of the self-base of a white-bronze statue of a settler on the Settlers' Monument (1889) in Newark, New Jersey.
By far the most popular white-bronze statue was referred to in the Monumental Bronze Company's catalog as an American Soldier, depicted standing at parade rest but now with both hands around the barrel of his rifle (fig. 5). More than 60 Union and 2 Confederate white-bronze copies of the American Soldier were erected between 1877 and 1913. The statue is an awkward version of bronze soldiers available shortly after the end of the Civil War, including those by Martin Milmore (1844–1881) in New England towns, Randolph Roger's (1825–1892) Infantryman for the Michigan Soldiers' and Sailors Monument in Detroit (1867), and J. Q. A. Ward's (1830–1910) Seventh Regiment Memorial (1869) placed in New York's newly created Central Park. Somewhat less popular was a white-bronze statue of a Colorbearer holding onto the staff of a large upright flag with his left hand, a drawn sword in the other hand. It is known in 11 copies dedicated from 1886 to 1908 (figs. 6, 7). Since white bronze appears bluish
Fig. 5.
The Monumental Bronze Company's Civil War Monument (1887), showing the soldier's pronounced backward lean, white bronze, Monroe, Maine. Photograph by Ronald S. Harvey
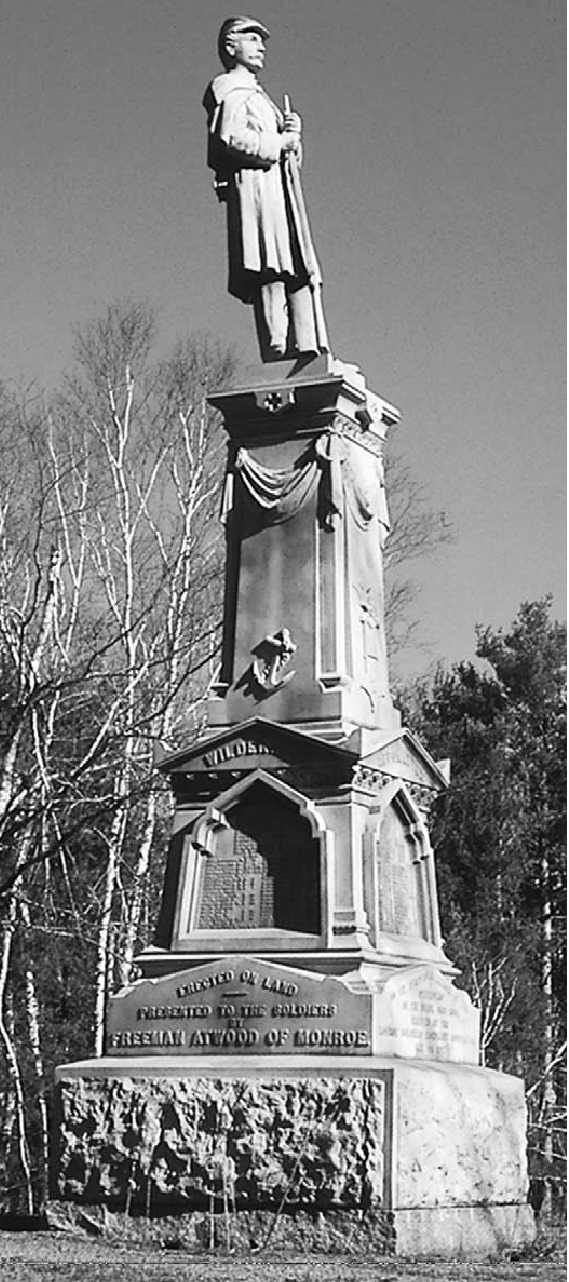 |
gray in color, it could be taken to represent the blue or gray uniform of either side in the conflict. At least 20 white-bronze copies of a Confederate Soldier wearing a broad-brimmed hat and bearing a bulky bedroll
Fig. 6.
The Monumental Bronze Company's Biddeford Civil War Monument (1887), white bronze, Biddeford, Maine. Photograph by Carol A. Grissom
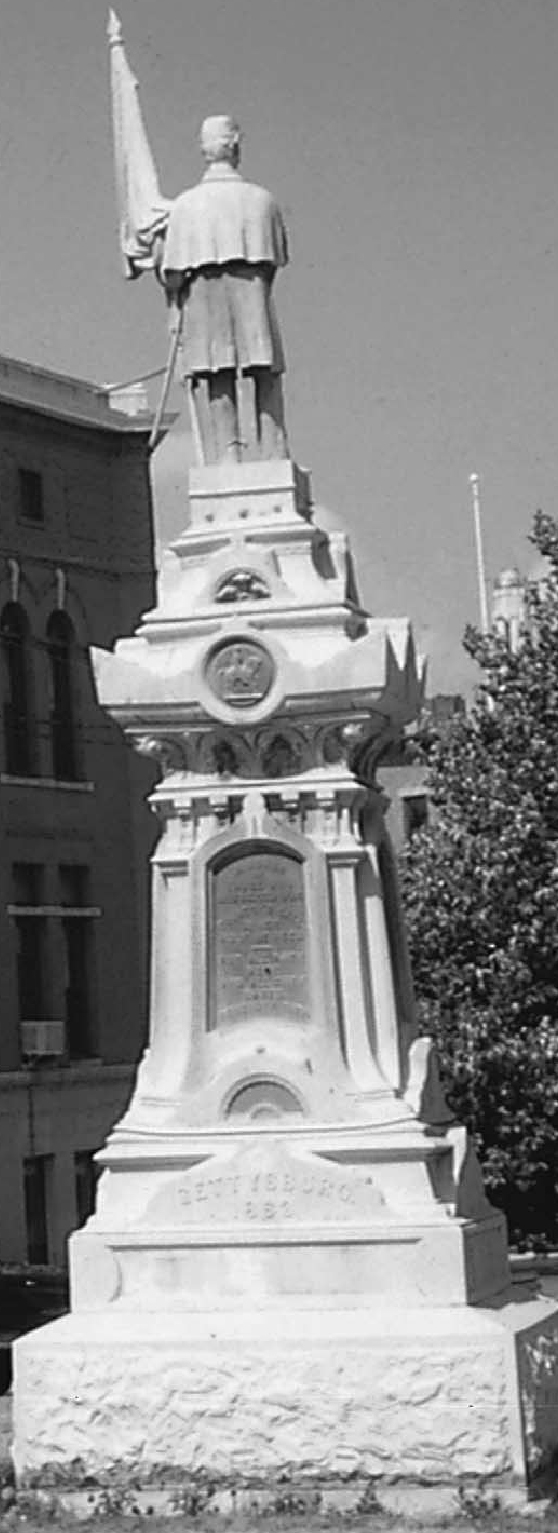 |
slung diagonally across his body were erected from 1889 to 1914. Statues representing other military personnel, including sailors, were made for multi-figured white-bronze monuments, such as those in the two Portsmouths (New Hampshire and Virginia). Some statues bear considerable resemblance to each other, and portions of models may have been reused, a relatively easy process since statues were cast in pieces. Artillery in the Virginia monument, for instance, appears almost identical to the monument's Infantryman, except that a ramrod has been substituted for a rifle and the bedroll is omitted. Custom-made statues include an appealing Drummer Boy in Brooklyn's Green-Wood Cemetery.
One of the most unusual aspects of white-bronze Civil War statues is that more than half were displayed atop imitation-stone bases also made of white bronze (see figs. 5, 6). In some cases this combination resulted in monuments more than 12 meters in height. The use of zinc for such large structures is unique. Nothing this ambitious was attempted in Europe, although zinc was used more extensively in Central Europe for both statuary and architecture. These white-bronze bases consist of three to six sections, each square in plan, including columns, Corinthian capitals, and sections customized with inscriptions or low-relief illustrations. The lowest section almost invariably was modeled in imitation of rough-hewn rock, sometimes with a foundry inscription in raised letters on the back face. Each section was made by fusing the corners of its four sides with thick deposits of zinc. Sections were kept separate for easy transport and assembly on-site.
Typically, white-bronze monuments were placed without attachment on simple footings. Sometimes these consisted of as little as a single course of stone placed on the ground. Starting from the bottom, as sections were added, each was bolted to the adjacent section on the inside center of each face. The final step was to place the statue on top. It was usually attached on center through the self-base, using brass bolts covered by decorative white-bronze heads.
Original supports are minimal inside all large white-bronze monuments that have been examined (fig. 8). Several vertical cast-zinc stiffener plates were attached at the foundry inside each face of the lowest
Fig. 7.
Detail of fig. 6, showing the leveled statue and Pliacre fill just below its self-base. Photograph by Carol A. Grissom
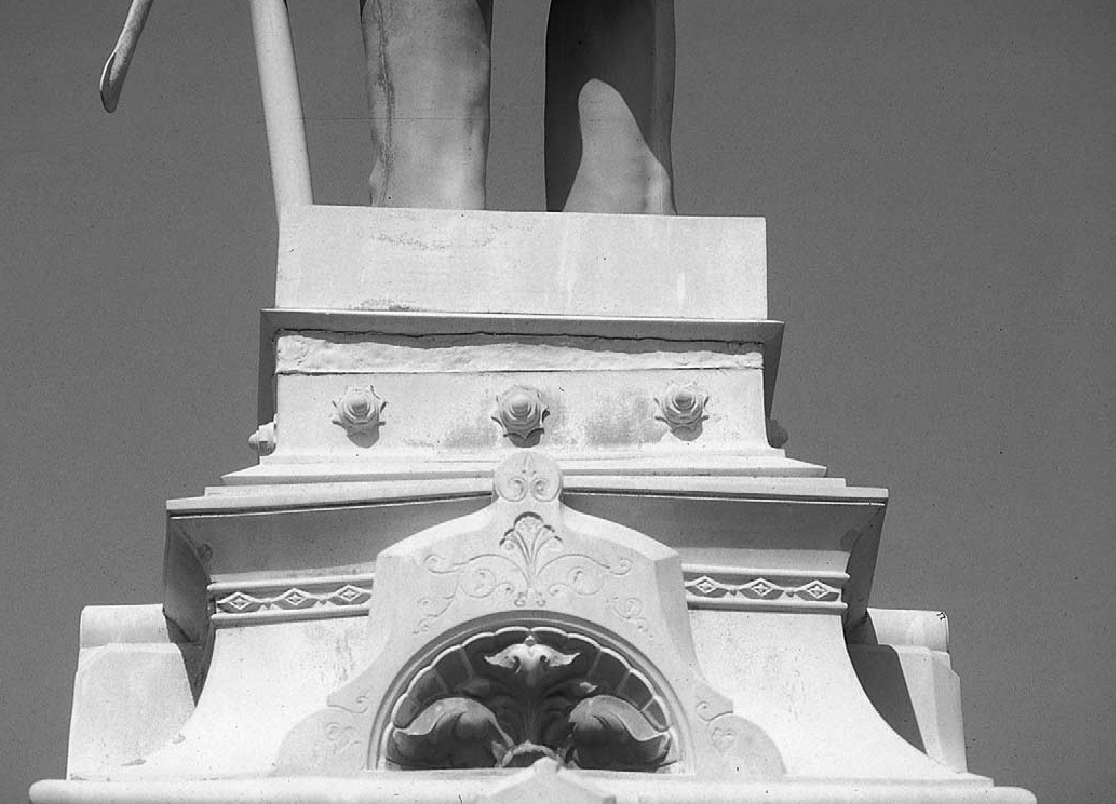 |
section. Galvanized-iron columns were shimmed to fit on-site, inside each corner of the section above.
2.3 SHEET-ZINC SOLDIERS
Stamped sheet-zinc statues are readily distinguished from cast statues by their thinness, light weight, smooth surfaces, and susceptibility to denting. Identical models were available stamped in zinc, copper, brass, or bronze sheet through trade catalogs that featured architectural metalwork. The earliest known model of a sheet-metal soldier, a Soldier on Guard, appeared in a Bakewell & Mullins catalog in 1887. By 1897, eight soldiers are found in a catalog of the Friedley & Voshardt Company. Many models are almost exact copies of earlier cast-zinc statues, including the Green-Wood Cemetery–type Infantryman and white-bronze statues of the American Soldier and Colorbearer. While extant sheet-copper or sheet-bronze soldiers are relatively common, only one sheet-zinc soldier has been located, a W. H. Mullins Company (1913)Confederate Infrantryman at Parade Rest on the Confederate Monument (1891) in Georgetown, South Carolina. Two sheet-zinc statues in Paducah, Kentucky, are known as The Blue and The Gray but were actually sold by the Friedley & Voshardt Company as School Boys. By 1896, statues stamped from copper-alloy sheets cost little more than zinc (Mullins 1896), and in 1913, when the W. H. Mullins Company issued a beautifully bound catalog of sheet-metal soldiers for the 50th anniversary of the Gettysburg battle, only sheet-copper and bronze statues are illustrated.
At the most active architectural sheet-metal company, W. H. Mullins, dies for stamping were made from plaster models. The lower die was made of cast zinc, and the upper die of lead. Sheet metal was heated, then placed between the dies and smashed into shape with a drop hammer (Lemonte 1947). The stamped pieces were then riveted or soldered
Fig. 8.
Interior of lower sections of the Monumental Bronze Company's Settlers' Monument (1889) during disassembly, showing the original corner posts and buckled vertical stiffeners, white bronze, Newark, N.J. Photograph by Carol A. Grissom
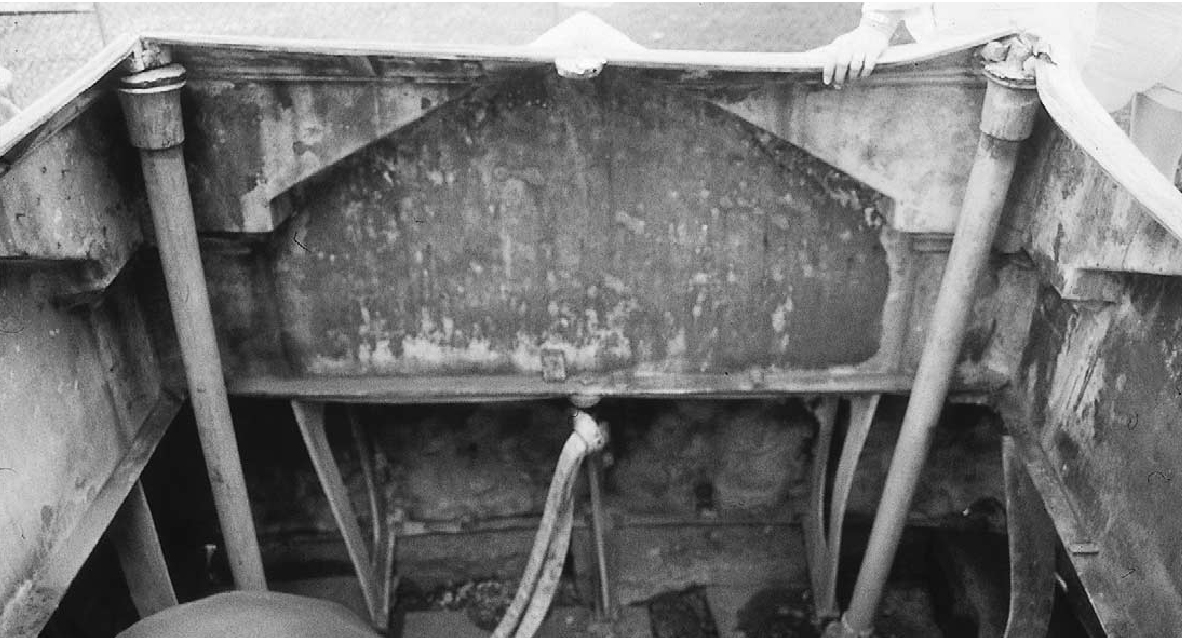 |
together. In contrast to most cast-zinc soldiers, sheet-zinc statues invariably have armatures. Cast-iron tubes and sheet-zinc cylinders have been found inside other sheet-zinc statues made by Mullins, extending from their bases to just inside the heads. A Bakewell & Mullins catalog (1884) notes use of wrought-iron armatures, but these have been confirmed only inside sheet-copper statues. Sheet-zinc soldiers are presumed to have been painted, but no documentation of original finishes has been found. The Georgetown soldier is unpainted, but that may be accounted for by its unusual placement on a white-bronze base, probably after the original white-bronze statue was damaged. Sheet-copper and sheet-bronze statues were patinated with an “oxidized or antique bronze finish” (Mullins 1896, 10). Other sheet-zinc statues, like a popular Justice displayed on courthouse roofs, were usually painted white in imitation of stone or, in a few cases, gilded.
|