CONSTRUCTION HISTORY IN ARCHITECTURAL CONSERVATION: THE EXPOSED AGGREGATE, REINFORCED CONCRETE OF MERIDIAN HILL PARK
LORI AUMENT
3 JOHN J. EARLEY
John J. Earley 1881–1945) began his career at the age of 17 as an apprentice in his father's stone-carving studio in Washington, D.C. Earley and his associate, Basil Taylor, assumed control of the Earley Studio in 1906 after the death of Earley's father. Previously, the studio had produced primarily ornamental stone sculpture (Cron 1977). Earley and Taylor changed the focus of the studio to plaster and stucco work. Through interest in Portland cement stucco during the years 1911–14, the studio became involved in concrete work. Its first major commission for concrete work was at Meridian Hill Park, a project that propelled the Earley Studio into the development of remarkable finishes and high-quality concrete. After the pioneering work at Meridian Hill Park, the Earley Studio continued to improve on its work, which eventually became the standard for artistic treatment of architectural concrete. Landmark projects include the Fountain of Time sculpture in Chicago (1922), the Shrine of the Sacred Heart in Washington, D.C. (1923), and the Bah�'� Temple in Wilmette, Illinois (1934). Contemporaries acknowledged Earley's contributions to the concrete industry. They credited him with elevating the status of the material and the industry (Earley 1924). It is in the evolution of concrete finishing, which coincided with a general acceptance of concrete as an architectural material, where Earley's work is paramount. His work was often cited in the literature of the day both in the United States and abroad (Howe 1921; Hart and Wilson 1927; Bauer 1928; Childe 1943). After his death in 1945, Earley was remembered for his tireless work in perfecting the artistic qualities of concrete through experimentation, innovation, and fine craftsmanship (John J. Earley Obituary 1946).
John J. Earley thought of himself first and foremost as a craftsman and artist. His self-proclaimed title was “Architectural Sculptor.” Although Earley went on to serve as president of the American Concrete Institute, he maintained that his concrete work developed from an artistic and not a scientific study. He wrote: “I am a craftsman and all that I could ever do was to record sensible experiences and the conclusions drawn from them and to describe the work which resulted from those conclusions” (Earley 1938, 589). He championed the work of the craftsman who perfects a technique through pragmatic trial and error rather than scientific testing. Earley's role as a craftsman explains why he approached concrete as an artistic medium rather than an engineering material.
At the time of Earley's work in concrete, the architectural community was debating the most appropriate and aesthetically pleasing expression for this relatively new material. In the search for a way to transform concrete from a construction material to one capable of complex architectural expression, the focus was on the proper form and finish of the material. Most agreed that concrete should not imitate other building materials but should be formed and finished to reveal its inherent qualities as a poured and molded material. Concrete offered the possibility of escaping the masonry vocabulary of stone laid on stone. Contemporary concrete work was constructed with perforated, monolithic walls, such as Frank Lloyd Wright's Unity Temple in Oak Park, Illinois (1904–6); formed with repetitive cast-concrete elements, as in Irving Gill's prefabricated concrete slab houses in Los Angeles, California (1910–13); and poured in organic forms, as seen in the undulating facade of the now demolished Blenheim Hotel in Atlantic City, New Jersey (1906), designed by William Price. However, concrete needed an appealing finish to be considered a true architectural material capable of performing under various aesthetic demands. In an effort to make concrete more aesthetically pleasing, many architects and contractors experimented with treating its surface. The treatments included tooling, painting and stuccoing the surface, coloring the cement, exposing the aggregate, and molding the concrete with a textured surface. Earley took part in this experimentation and achieved some of the most outstanding and enduring concrete finishes of the period.
The process of exposing aggregate in concrete appealed to Earley's desire to give concrete an artistic finish that was characteristic of the material. To expose the aggregate, the concrete is removed from the mold while it is still green, meaning not fully cured. The surface of the concrete is then scrubbed to remove the exterior film of wet cement and to expose the aggregate beneath. This process gave an appealing finish while revealing elements inherent to concrete as a conglomerate material such that “any section through it would have the character desired for the surface” (Earley 1934, 251–52). Earley wrote that “it was this decision to employ finishes characteristic of the nature of reinforced concrete that gave the interest to succeeding studies” (Earley 1918, 128).
To achieve artistic results in exposed aggregate concrete, Earley adopted techniques from the arts of mosaic and painting. He showed sophistication in placing and juxtaposing small tesserae in his concrete mosaic work. The art of mosaic was easily adaptable to exposed aggregate concrete, Earley felt, as both have a surface “made up of a myriad of tiny, irregular stone chips averaging about 1/4 in. in maximum dimension, and closely grouped. Interstices are slightly tilted in various directions, resulting in a richly textured surface which, however, is held firmly in plane by the flat surface of the mold” (Earley 1940, 103). As in mosaic work, the exposed aggregate of concrete imparts not only color but also texture and radiance to the surface of the concrete. The aggregate's “small size and jagged shape results in their catching and refracting light from all directions, giving the surface a subdued ‘sparkle’ which is highly distinctive” (Earley 1940, 102). The Shrine of the Sacred Heart (1923) exemplifies Earley's concrete mosaic work, though the influence of the art of mosaic can be seen throughout his work.
From the beginning of its development, Earley compared the exposed aggregate finish to the play of colors in pointillism. Earley incorporated the optical science of pointillism, where pure spots of color resolve to a uniform hue at a given distance, into exposed aggregate concrete: “By considering the particles of aggregate as spots of color in juxtaposition, all the knowledge and much of the technique of the impressionist, or the pointillist school of painting, was immediately applicable to concrete” (Earley 1925, 19). The optical science of pointillism guided the careful selection and combination of aggregate in Earley's concrete work in order to produce various visual sensations from different distances: “We have designed surfaces to fill the most exacting requirements and to meet the greatest differences in scale, surfaces which lose their texture and resolve to uniform hue at twenty-five feet, surfaces which hold their texture at five hundred feet” (Earley 1925, 21).
While Earley was looking to established arts to improve the aesthetic quality of concrete, he recognized the merit of concrete as an artistic medium in itself. It was extremely durable, economic, and flexible and permitted rapid execution of forms. Earley saw concrete as a modern artistic material that could solve modern building-design problems. He wrote: “It is deceiving to see the material [architectural concrete] as a form of structural concrete elevated to the level of an artistic medium when on the contrary it is an artistic medium extended to more general use” (Earley 1938, 591). He likened his use of concrete to Luca della Robbia's development of terracotta during the Renaissance (Earley 1926b). In both instances, he felt, technology had developed new materials that were both functional and ultimately artistic, to express the architectural ornamentation of its own era.
3.1 INITIAL EXPERIMENTATION IN CONCRETE, 1915–1916
Earley approached the problem of constructing the concrete at Meridian Hill Park in the spirit of experimentation. In 1915, the Earley Studio was awarded the contract for the work at Meridian Hill Park, in part because of its reputation for cement stucco work. At that time, the Earley Studio was involved in a study at the Bureau of Standards on reducing map cracking in Portland cement stucco applied over metal lath.2 Earley worked with J. C. Pearson, the bureau's cement chemist, to reduce the appearance of map cracking (Bureau of Standards 1926). These experiments were contemporaneous with the concrete work at Meridian Hill Park and led to a collaboration that directly influenced the construction techniques used in the exposed aggregate concrete there.
3.2 PRELIMINARY MOCK-UPS
The contract for Meridian Hill Park stipulated that a full-scale mock-up of a wall unit, complete in all details except for reinforcement, be approved by the Commission of Fine Arts before work could begin. The wall unit consisted of a rusticated post attached to a wall panel with a base, an inner panel with a surrounding border, and a coping with a drip edge. The form of the wall shown in the construction drawings and historical photographs of the mock-ups is almost identical to that seen in the park today. Earley made three mock-ups in total for inspection. The commission refused the first mock-up of smooth cast concrete because of its uninteresting surface. Horace Peaslee later commented that “in the first stage of the construction … the intent was to obtain interest in the surface by expedients of form alone, paneling the wall sections and rusticating the posts. An effort was made to rib the rustication in the manner of the heavy cutting of certain Italian garden work. The balusters, urns, etc., were of cast cement, smooth, cold, and uninteresting” (Peaslee 1930a, 31). While the form replicated Italian masonry, the concrete of the first mock-up failed to capture the correct color and texture.
The second mock-up was essentially the same in form but an attempt was made to use textured finishes to make the wall more interesting. The surface was enlivened by texturing the surface of the concrete and by applying cement stucco to the concrete backup. The Portland cement stucco testing at the Bureau of Standards, in which the Earley Studio took part, had included test panels of cement stucco on monolithic concrete that yielded promising results (Bureau of Standards 1926). Of the second mock-up, Earley wrote:
An effort was made to relieve the monotony of appearance by finishing various details in different texture. The piers were built of rusticated blocks the surface of which was grooved vertically with straight, symmetrical, V-shaped grooves about 3/8 in. on centers and 1/4 in. deep. The coping and border of the wall panels were sand floated. The panels themselves were pebble dash in which the pebbles were as nearly as possible one size, having passed a 1/4 in. screen and having been retained on a 1/8-in. screen. (Earley 1918, 128)
Fig. 6.
Second mock-up made for Meridian Hill Park, 1915. Courtesy of the National Park Service, Museum Resource Center
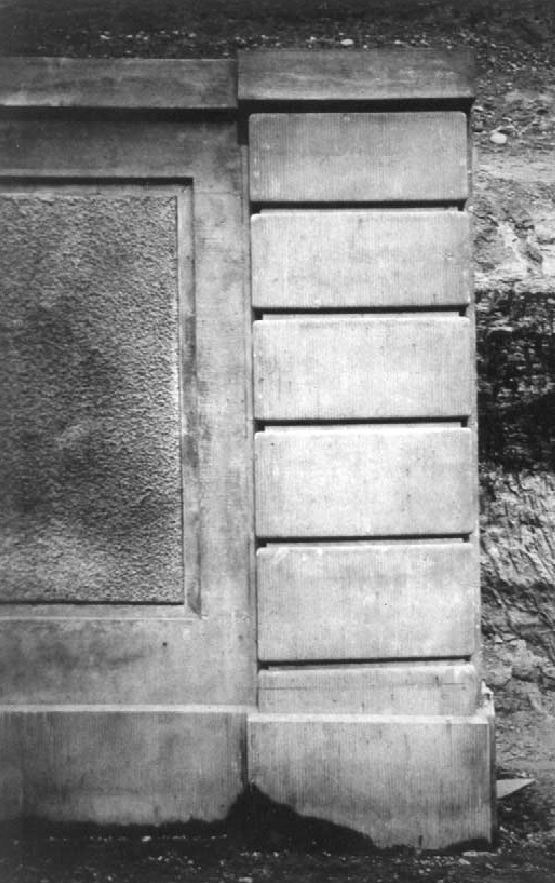 |
The experiment with this technique can be seen in historical photos of the mock-up made along 16th Street (fig. 6).
While the textured finishes did break up the monotony of the surface, Earley himself criticized the second mock-up for its poor color and particularly for its failure to express the character of concrete. He wrote that “the color was unsatisfactory. It was the cold gray cement color that has always been so objectionable. Every particle of sand was coated with cement and had no color value of its own” (Earley 1918, 127). The second mock-up was also objectionable because of its inability to reveal the physical characteristics of concrete. In a caption to a detailed photograph of this mock-up, Earley noted that the “textures are conventional and not characteristic of concrete” (Earley 1918, 129). This mock-up was “a plastered wall, nothing more. The construction might just as well have been of brick, terra cotta, or metal lath on channel studs so far as the appearance revealed. The wall was without scale. It did not give the appearance of strength and size equal to its task as a retaining wall” (Earley 1918, 127). The second mock-up offended Earley's aesthetic sensibilities because it was both unattractive and uncharacteristic of the material.
A third mock-up, in the same form but with an exposed aggregate finish, was presented for a final review. It is unclear how exposed aggregate concrete came to be used at Meridian Hill Park. It is known that the Commission of Fine Arts desired that the walls should closely resemble the Mediterranean tuff-and-pebble mosaics found in Italian villa gardens. Cass Gilbert, a member of the Commission of Fine Arts, is credited with sparking Earley's imagination to create a similar texture in concrete (Avery 1944). The process of exposing aggregate was practiced on earlier concrete work, most notably Frank Lloyd Wright's Unity Temple (1906), but it is unclear how knowledge of the technique came to Earley or to the commission.
Earley described the effect the exposed aggregate had on the surface of the concrete at Meridian Hill Park:
A change took place in the color. The surface, which had been wholly of a cement gray, was broken in frequent spots by clean pebbles in their natural color which varied from white, to yellow, to light brown. … These spots relieved the gray of the cement to such an extent that they imparted to the whole structure a cream color which was a great improvement and a decided step forward. (Earley 1918, 128)
In contrast to the earlier mock-ups, this wall harnessed the qualities of the material by emphasizing the texture and color of the aggregate. In contrast to the earlier experiments, Earley wrote: “The wall was no longer a plastered one, but was reinforced concrete and nothing else, and it seemed big and strong enough to suit all the demands that would be made upon it” (Earley 1918, 128). The third, exposed aggregate mock-up was approved for construction in 1915, which began at the north end of the west wall.
3.3 CONSTRUCTION OF WEST WALL UNITS, 1915–1916
The concrete for the 1915–16 wall units was a 1:2:4 mix, with 1 part cement to 2 parts sand and 4 parts aggregate. The cement was a white Portland cement made by the Atlas Company, which was the type preferred by Earley throughout his career (Cron 1977). The sand used in the mix was a river sand finer than 1/4 in. and was known as concrete or torpedo sand, composed of uncrushed, rounded quartz grains. The aggregate was specified as Potomac River gravel and ranged from 1 1/4 in. to 1/4 in. with the greatest proportion between 3/4 and 1/4 in. in diameter; Potomac River gravel is composed of highly colored, naturally weathered, rounded quartz. The exact grading of the aggregate for the two mixes used in the wall units is not known, but it was probably graded in a conventional manner combining aggregate graded through descending sizes. Water was added to the mix so that “its consistency was soft, so soft that it would flow readily” (Earley 1918, 130). The forms of the wall units were made of plaster waterproofed with shellac. The plaster forms fit inside standard wooden forms that supported the weight of the concrete. The walls and posts were reinforced with 1/2 and 3/4 in. twisted steel rods embedded 4 in. in the form (Meridian Hill Park Specification 1915).
The west wall units, each comprised of one wall panel and post, were cast as an integral form in one pour using two concrete mixes. The range in texture of the exposed aggregate in the west walls indicates the use of two types of mixes in each wall unit, one with coarse aggregate and one with medium aggregate. The rusticated posts, coping, and base all have a coarse exposed aggregate finish, while the inner panel has a medium exposed aggregate finish. The inner border has a smooth finish that has been tooth-chiseled. Pouring of these wall units required dividers, probably of sheet metal, that separated the different concrete mixes and were raised as the pour progressed (Mann 1981). Sharp raised ridges at mix boundaries remain as evidence of the use of such dividers during construction.
After 24 to 48 hours, the forms were pulled while the surface of the concrete was still green. The surfaces of the inner panel, the face of the coping, and the rusticated posts were scrubbed with a steel brush to expose the aggregate, care being taken to create an even exposure. The exposed aggregate surfaces were washed with muriatic acid to remove any excess cement film, and the walls were then hosed with water (Peaslee 1930a). The border around the panel was tooth-chiseled. Fine, crisp details such as the drip edge under the coping and the recessed groove on the panel were achieved by detachable wooden strips. These strips were loosely attached to the interior of the plaster mold and were grooved on the back to allow for expansion. After the pour, the wooden strips remained in the concrete form, protecting the fine details. The strips were released as the wood dried and shrank. The walls were carefully monitored while they dried and were wetted if they appeared to be drying too rapidly. The top of the wall coping and the top of the base received a troweled surface (Earley 1918).
Construction of the west wall progressed as every other post and panel unit was poured in place. This method allowed for the ends to be coated with five-ply felt and tar to form an expansion joint. This process ensured that when the wall units were poured to fill the gaps between the previously poured units, the adjacent wall panels had sufficient strength to withstand the work performed on the new panel (Earley 1918).
|