A CASE STUDY IN THE USE OF CYCLODODECANE AND LATEX RUBBER IN THE MOLDING OF MARBLE
JEFFREY P. MAISH, & ERIK RISSER
3 APPLICATION OF CYCLODODECANE
Trials conducted with cyclododecane posed two principal technical challenges: the controlled application of a uniform layer on a large area, and the control of its property of forming a crystalline structure during solvent loss or cooling. The application of CDD in solid form can be a slow process, producing a thick and inconsistent layer with unwanted crystalline features. Considering the ultimate goal of studying tool markings, these effects were deemed a hindrance. Solvent application of CDD was investigated as an alternate method of application and means of crystallization control, but it was observed to have an additional adverse film-disrupting effect on the latex rubber, most probably due to the solvent.
3.1 SURFACE APPLICATION PRACTICALITIES OF CYCLODODECANE
To maximize the CDD concentration without obscuring surface details, the authors initially applied molten CDD to a test surface with the further aid of a heat gun. This method, although perhaps suitable for small areas, was also proved unsuitable for providing a uniform surface free of artifacts that would be captured in subsequent molding.
Further trials were conducted with CDD in two recommended solvents: odorless mineral spirits and naphtha (Hangleiter 2000).1 Solubility tests indicated that high concentrations could be achieved with both, but the authors obtained higher concentrations in naphtha (95% w/v in naphtha vs. 65% w/v in odorless mineral spirits). Concentrations as high as 140% in hexanes have been reported (Stein et al. 2000). The main limitation to these higher concentrations appeared to be the more rapid crystal formation that could obscure original surface detail. Application of a slightly warmed and less-concentrated solution overcame this limitation, providing a more controllable application method that slightly penetrated the stone surface while yielding a more uniform layer. Rapid cooling (Hangleiter 2000) has reportedly been used to reduce crystal size, but in this instance, it is speculated that the surface morphology of the stone inhibited the crystal formation to a degree.
A weight-loss trial with 80% CDD in naphtha (fig. 4) shows a high initial rate of mass loss that would presumably correspond to solvent evaporation (naphtha) with a subsequent slower loss rate reflecting the CDD sublimation, perhaps in combination with some remaining solvent. The graph implies that CDD could be deposited on the surface and latex applied following an initial solvent loss.
3.2 DEVELOPING A TIMING WINDOW: THE SOLVENT-LATEX INTERACTION
The solvents in the CDD mixes appeared to cause an uneven drying and buckling of the latex rubber. Because of this observed deleterious solvent effect, further trials were conducted using a porous limestone sample to pinpoint the timing between the more rapid evaporation time of the solvent from the surface (with CDD remaining deposited) and application of latex. Limestone was chosen simply for its rough surface morphology and greater tendency to visually show staining problems.
Fig. 4.
Weight loss over time caused by the evaporation and sublimation of 80% cyclododecane in naphtha (w/v). Initial weight loss over six hours is most probably attributable to solvent loss (naphtha), while the subsequent slower rate of weight loss is governed increasingly by cyclododecane sublimation.
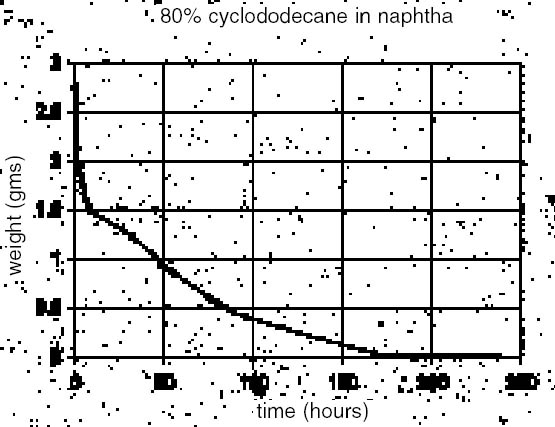 |
CDD (20% in odorless mineral spirits) was applied to the entire test surface, and latex was brushed on in regular strips at five-minute intervals up to 25 minutes during the CDD–solvent-drying process (fig. 5). The odorless mineral spirits solvent was observed to have considerable adverse effect on the latex before 10 minutes of solvent evaporation time. By 25 minutes, the CDD had developed a quite prominent and visible crystalline pattern. The ideal window was therefore judged to begin in the vicinity of 20 minutes after the application of the CDD, when excess solvent had evaporated but cyclodode-cane still remained as an undifferentiated barrier. At this point, latex rubber could be brushed on, and, once dry, the rubber served not only to mold the first layer of detail on the surface but also as a barrier to succeeding applications of materials. In effect, the CDD formed a barrier to this first coating of latex rubber.
Fig. 5.
Solvent-CDD effect on latex rubber. Note that the deformation effect on the latex rubber film is less pronounced after 20 minutes but severe in the 5–10-minute range.
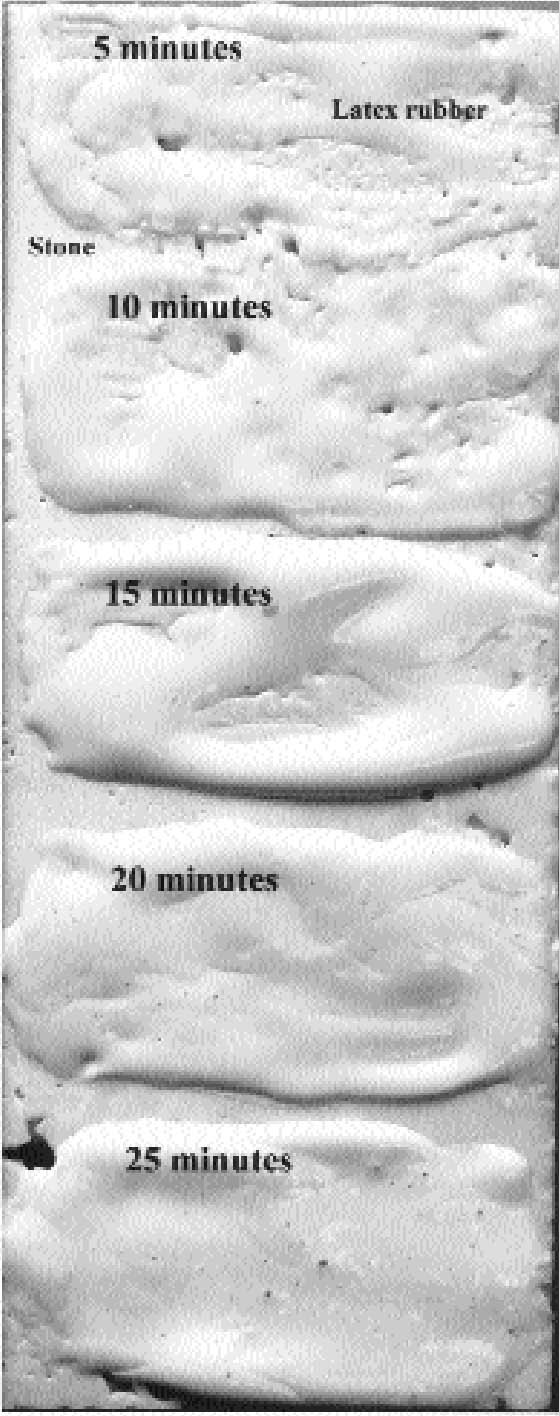 |
3.3 CRYSTAL FORMATION AND BARRIER PROPERTIES
To better understand CDD crystalline growth, incremental 20% w/v (20%, 40%, 60%, 80%) solutions of CDD in naphtha and odorless mineral spirits were prepared. Solutions were warmed to 30�C, and a single, thin brush stroke was applied to standard microscope slides to aid in visualization and interpretation. To better understand the sublimation processes, digital time-lapse photomicrography (using a Kodak MDS 100 camera) was used to observe the surfaces over a four-hour period. Similar results were observed for both solvents, with higher concentrations of CDD in solvent producing smaller crystals but forming crystals more rapidly. Naphtha appeared to produce slightly smaller crystals than odorless mineral spirits. Higher concentrations (i.e., with a greater relative amount of CDD) also produced fewer visible holes toward the end of the sublimation period (a period of hours), and the barrier layer took longer to sublime. After four hours on the glass slide, all but the 80% solution in odorless mineral spirits appeared to have sublimed completely, although faint tide lines were visible on some slides.
3.4 RESIDUES
Following the previously mentioned weight trial using 80% CDD in naphtha (w/v), a final stage was reached where 0.02% of the starting solution weight remained unsublimed for almost a week before the weight finally returned to zero. Preliminary reports (Stein et al. 2000; Caspi and Kaplan 2001) have suggested that some residue is left by CDD, and this was confirmed in this trial. Even though the balance measured to an accuracy of 0.0001 gram and eventually returned to 0 weight, a faint “tidal” film could still be observed on the watch glass. At this point the nature of the film is undetermined, but it is likely from the CDD as no residue was noted for the evaporation of naphtha alone. In either case, the amount was undetectable by fairly precise weighing alone and would require further analytical study.
3.5 MOLDING EFFECT ON UNBOUND PIGMENT
The final parameter of the CDD test was to gauge its effectiveness in protecting a loosely bound material during molding. Latex rubber alone was determined to have no visible effect on unprotected marble, and CDD was therefore to be applied only in areas containing unbound pigment. A comparison was made to gauge the protective effects of 20%, 40%, 60% and 80% CDD solutions in odorless mineral spirits and naphtha on an unbound pigment layer (fig. 6). To maximize the deposition of dry pigment, a porous travertine marble sample was brushed with terra rossa dry pigment and distributed by wiping over the stone's surface. The warmed CDD solutions of varying concentrations were gently brushed onto the surface in two sets of four rectangles, and after 20 minutes' solvent evaporation time, high solids latex rubber was applied over all test rectangles and allowed to dry. The latex was then peeled back, revealing the underlying test patches.
The 20% CDD solutions in both odorless mineral spirits and naphtha provided virtually no protective effect to the pigment. At 80% concentration in naphtha, however, it is estimated that roughly 10% of loosely bound pigment was picked up, whereas, unexpectedly, half of the pigment was picked up in the adjoining 80% cyclododecane in odorless mineral spirits square. The solution in naphtha appeared to perform substantially better than the solution in odorless mineral spirits in inhibiting pigment removal. This finding suggests that solvent choice may play a critical role in protecting unbound pigment. In tests on glass slides, CDD in naphtha crystallized more rapidly than in odorless mineral spirits, and perhaps this CDD-naphtha combination produces a better protective layer. The solvent itself (odorless mineral spirits) may also have had a more mobilizing effect on unbound pigment.
In light of all the trials, and to maximize the concentration of CDD, a 90% solution (w/v) in naphtha was selected as a barrier to be used in conjunction with latex rubber. Additionally, when warmed slightly on a hot plate to 30–40�C, this solution flowed quite evenly.
Fig. 6.
Consolidation effect on dry unbound pigment of 20%, 40%, 60%, 80% cyclododecane (w/v) in odorless mineral spirits (left) and naphtha (right). Note the consistently greater amount of pigment present in the latex rubber peeled from the odorless mineral spirits side and the final result at bottom between 80% CDD in odorless mineral spirits and naphtha. A relatively small amount of removed pigment can be noted on the latex peeled from the area brushed with 80% CDD in naphtha.
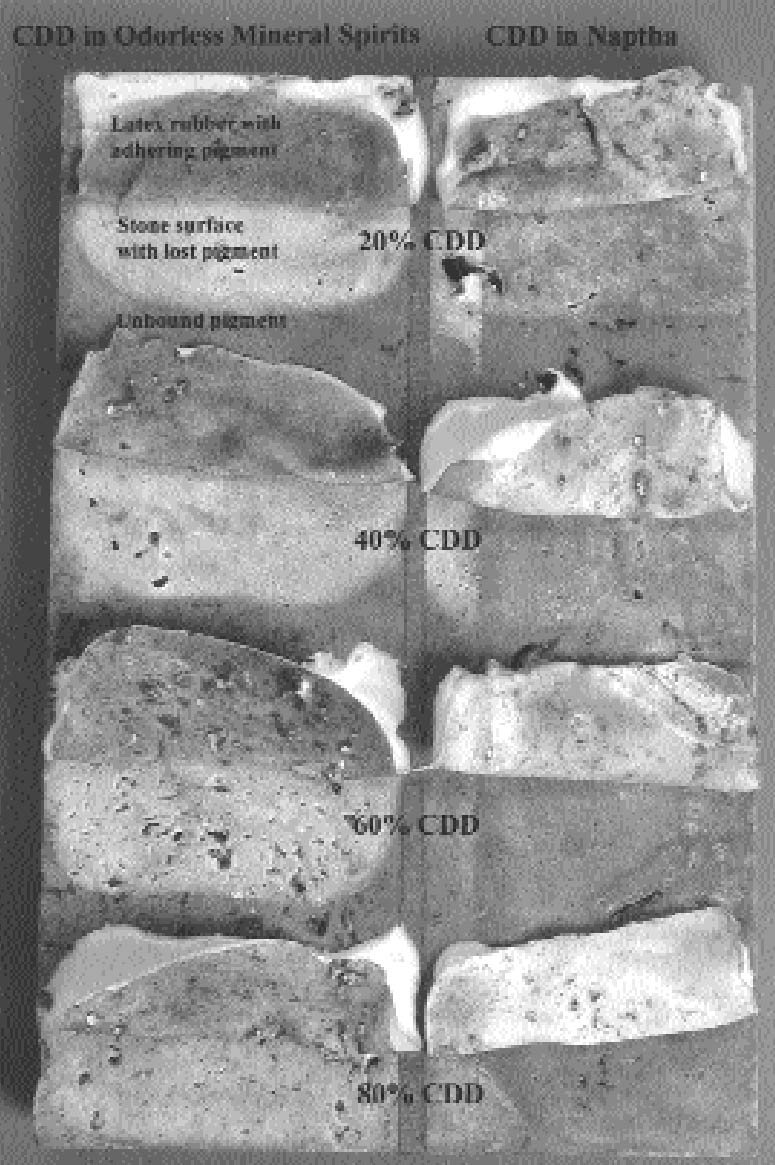 |
|