A CASE STUDY IN THE USE OF CYCLODODECANE AND LATEX RUBBER IN THE MOLDING OF MARBLE
JEFFREY P. MAISH, & ERIK RISSER
2 MATCHING BARRIER TO MOLD MATERIAL
2.1 RUBBER
In mold making, conservators have long been aware of the possibility of transferring mold-associated materials to the surfaces of art objects. The use of a protective barrier in itself presents challenges in that this material must be subsequently removed and in instances may interfere with the molding itself. A variety of molding materials are available, but each has characteristic problems. Polyurethane rubbers can achieve good detail but bond tenaciously to unprepared substrates. Polysulphide rubbers are less expensive, but they produce substantial oily stains. Water-based alginates can render good detail in small molds but lack the strength for larger-scale molds. Silicone rubbers applied without barriers are known to transfer a silicone oil that in general must be removed by poulticing (Maish 1994).
Considering the near life size of the marble bust, room temperature vulcanization rubber (RTV 2) was initially considered, but it would require the application of some type of protective barrier to the marble. Trials with different rubber types revealed that a high-solids latex left a test marble surface without a barrier unaltered and, in this particular case, had good releasing properties. Under low-power magnification the latex rubber provided visual detail approximating that of a silicone rubber RTV 2 (fig. 2). In one published case, sufficient detail was achieved for making detailed replicas for scientific research (Baird 1965).
Fig. 2.
Examples of level of detail produced by rubber latex: a, slightly elevated paint markings on laboratory glassware; b, cutting marks on modern marble sample captured, side by side, by latex (left) and silicone (right) (note some marble grain detail captured by both latex and silicone); c, 1 cm grid scratched in marble with a scalpel
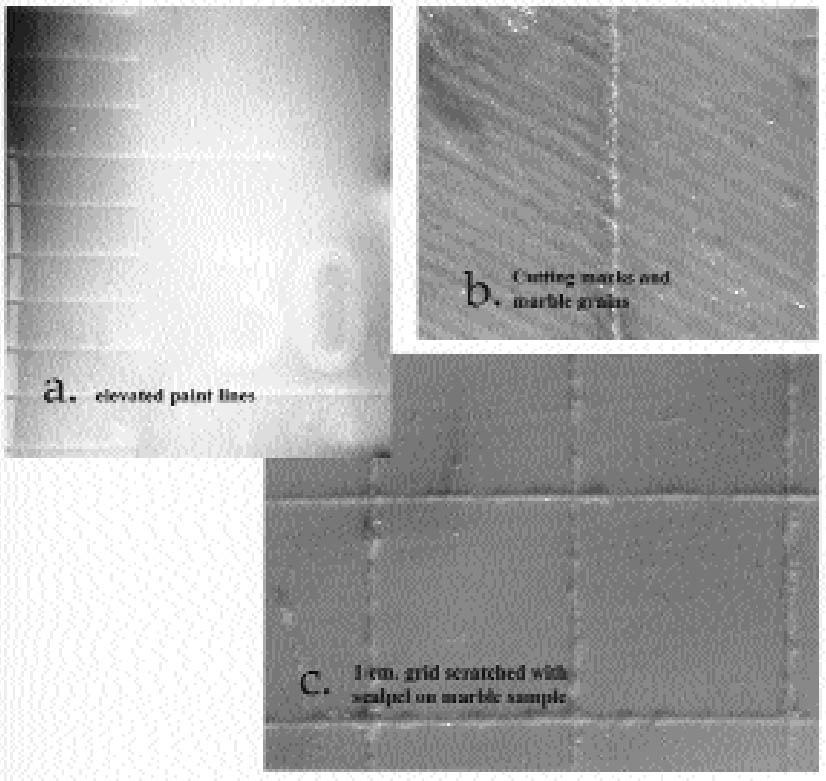 |
The disadvantages of latex rubber include extreme shrinkage due to loss of water upon drying and short mold life. Small-scale tests suggested that latex renders a high level of detail and that most if not all shrinkage in the rubber occurs orthogonally, or perpendicular to the surface being molded. Since shrinkage is not occurring parallel to the surface, dimensions are rendered fairly faithfully. However, because latex requires air-drying, only thin coats can be applied at a time. Ammonia is often present in latex rubbers and can have deleterious effects on some materials, especially metal alloys, as it can leach components and artificially enrich a surface. Latex rubber molds have a relatively short life and would be of use only if a set of casts were produced shortly after mold production. Natural rubbers, in general, have a high proportion of double bonds, making them especially susceptible to oxidation, with disproportionate effects to physical properties (Mills and White 1987)(fig. 3). In this study, however, use of a water-based rubber was considered an advantage when used in conjunction with a nonpolar barrier. Tests with a high-solids (74%), no-ammonia latex (Latex 74, A-R Products) were encouraging.
Latex rubber air-dries in fairly thin layers, and, traditionally, multiple layers of the material are applied and partly reinforced with gauze until sufficient mold thickness is achieved. This procedure may increase production time, and to expedite this thickening process, several trials were conducted to gauge whether an RTV rubber could be used to support or back a thinner layer of latex rubber. The ability of an RTV rubber to set in a thicker layer would, we hoped, shorten work time, help create a uniform rubber thickness, and provide a better fit to a resin mother mold. Tests were conducted to gauge whether latex could be bonded to either a silicone or nonsilcone type RTV rubber, and a urethane (Ever-green 30A) was selected to take advantage of its bonding properties and slight adhesion to latex.
Fig. 3.
Molecule of cis isomer of rubber (Buttle et al. 1974)
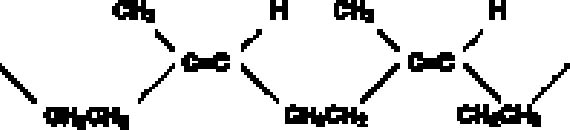 |
2.2 THE BARRIER
Some success has been reported with silicone rubber used in conjunction with certain barrier types. Pulga (1997) reports on a peelable barrier, while Br�ckle et al. (1999) applied a volatile/subliming cyclododecane (CDD) barrier to isolate a second waterborne barrier. The aim in the latter case was to reduce the penetration of the water-based material into the substrate and to facilitate subsequent barrier removal. CDD alone is soluble, to a degree, in silicone oils, offering little if any protection from penetrating oils during silicone rubber molding. Further testing of silicone rubber (RTV 2) at different set times on unbound pigment mock-ups also showed significant pigment loss with molding.
Because of its intrinsic and promising sublimation properties, further trials were conducted to develop a methodology using CDD for molding the marble bust (see Stein et al. 2000 for properties). Cyclododecane, a waxy nonpolar material (C12H24), could conceivably work well in conjunction with a polar molding compound that would include water-based materials such as rubber latex.
|