THE HISTORY, TECHNOLOGY, AND CONSERVATION OF ARCHITECTURAL PAPIER M�CH�
JONATHAN THORNTON
ABSTRACT—The use of paper or paper fiber in the production of three-dimensional objects seems to have closely followed the spread of papermaking itself. Brief notice of this ancient history is followed by description of papier m�ch� as an architectural material from the 17th to the early 19th century, focusing on the mid-18th century, when it appears to have been used most extensively. The practice of the London craftspeople who produced sculptural detail in this medium for domestic use and export are examined as illuminated by the technical examination of paper m�ch� in the Miles Brewton House of Charleston, South Carolina, dating from the 1760s. Discussion of the Brewton house material includes the complete rococo-style ceilling in the parlor, the reconstruction of gilded molding based on fragments from the drawing room found in a rat's nest during restoration, and a bas-relief of Apollo and a gilded border in the stair hall that was damaged but largely complete. Restoration of original decorative schemes required the replication of more than 150 ft of gilded and burnished cotton rag paper molding based on the conserved rat's nest fragments and the replication of gilded and ungilded moldings from the stair hall both to infill losses in extant molding and to replace missing molding for which physical and documentary evidence existed. The research required to duplicate this forgotten art is described as well as the modeling, carving, and mold-making techniques eventually used in accomplishing this extensive retoration project. Conservation methods used on existing 18th-century material are also detailed, focusing on lightweight materials chosen to support and reconstruct the Apollo relief.
1 INTRODUCTION
“Frames for pictures and divers fine pieces of embossed work with other curious moveables, may, as trial has informed us be made of it [paper] … either painted or overlaid with foliated silver or gold, as the artist pleases,” wrote Robert Boyle in the 17th century (Boyle 1966, 111:485–86). He was not the first to think of paper fiber as a material appropriate for the production of three-dimensional objects, and he was certainly not the last. It is no surprise to any craftsperson familiar with the material that objects were made from paper pulp in China virtually as early as sheet paper and subsequently by the other cultures to which papermaking spread (Osborne 1975).
Most people think of “papier m�ch�,” as molded paper came to be called, as 19th century tea trays, desk furnishings, and small furniture—what Boyle may have anticipated by the term “curious moveables” (Dickinson 1925; Devoe 1971; van der Reyden and Williams 1986). More surprising is the vogue that papier m�ch� enjoyed as an architectural material starting in the middle of the 18th century. The novel material was intended as a replacement for the laboriously modeled plaster and carved wood that had been used to create elaborate interiors during this and earlier periods. Papier m�ch� was often used as sculptural relief for ceilings and walls in imitation of plasterwork and was generally painted white. It was also used as decorative border or fillet in imitation of carved and gilded wood to border the “surbase” (chair rail) doors, windows, chimney pieces, cornices, or anywhere else it might look attractive. This border might be burnished with water gilding or finished with the cheaper oil gilding. The makers were explicit in selling its advantages to the public. In 1754 Augustin Berville advertised in Dublin that he made a “Pasteboard Stucoe” with which he could “finish in three or four Days, with as much Boldness, Relief and Beauty, as that of any other Stuccoe, the fullest and richest Design or Ornament for a Cieling … without sullying or hurting the Furniture or lumbering the Room” and that his ornament was “by much the cheapest, and not subject to split or crack, or fall from the Cieling, and may be taken down at Pleasure and removed and fixed up in any other place” (quoted in Longfield 1948, 57).
2 HISTORY AND DEFINITION
The term “papier m�ch�” may well have originated in England and was used with various creative spellings from then on to describe three-dimensional objects composed of paper fiber, whether layered up in sheet form or cast as a beaten pulp (Oxford English Dictionary 1971). The modern term “cast paper” as used for the latter technique was not recognized as a distinct method but only as a variant encompassed by the same term. Since the craft was carried on away from paper mills, recycled sheet paper was the raw material in any case, whether repulped or layered with an adhesive.
The origin of the commerical production of papier m�ch� is unresolved and perhaps unresolvable. It is interesting to not that a French writer stated in 1788 that “the English cast in cardboard (“carton”) the ceiling ornaments that we make in plaster: they are more durable; break off with difficulty or if they do break off the danger is nil and the repair cheap” (Bielefeld 1850). The trade seems to have developed in London during the 1740s and was carried on by craftspeople or probable Huguenot extraction such as Peter Babel and Ren� Duffour, whose advertisements survive. One unsubstantiated account states that William Wilton, father of the noted English sculptor Joseph Wilton, established a papier m�ch� factory and employed “people from France.” This account seems credible in view of the facts that Wilton was a decorative plasterer active by 1722 and a manufacturer of apparent means who could send his son to study in France and Italy. Perhaps it was Wilton's laborers who subsequently set up their own businesses and gave the trade a French name and association that was to continue.
By midcentury, the manufacture of architectural papier m�ch� was well developed and its use becoming commonplace (Cornforth 1992). Papier m�ch� was an ideal material for export abroad, and extensive documentary evidence attests to the concurrent popularity of this stylish material in the American colonies. Such notables as George Washington and Benjamin Franklin ordered it for their houses. While most it was either bought through the commerical representatives or “factors” of the wealthy or from middlemen dealers in the colonies, limited evidence indicates domestic manufacture. A Mr. “Minshall, Carver and Gilder,” stated in 1769 that he “makes Paper Ornaments for Ceilings and Stair Cases, in the present Mode” in New York (quoted in Gottesman 1938). Nicholas Bernard, “Carver,” also advertised his “Paper Machine for ceilings” in the same city and year. Although Bernard may have been a dealer only, his trade suggests otherwise.
Despite the popularity of this material, relatively little of it either survives or has been correctly identified. A complete ornamental ceiling survives in Philipse Manor in Yonkers, New York, dating from the 1750s or 1760s (Waite 1972), and papier m�ch� fillet survives in the Governor Wentworth House in Portsmouth, New Hampshire (Nylander 1986). By far the largest concentration of extant and restored papier m�ch� is present in the Miles Brewton House in Charleston, South Carolina. The papier m�ch� in the Brewton house may have been imported from England by the contemporaneous Charleston dealers Charnock and King (South Carolina Gazeteer and Country Journal 1765) or John Blott (South Carolina Gazette 1765). The remainder of this paper will concern the examination, conservation, and restoration of this material.
3 WORK CARRIED OUT IN THE MILES BREWTON HOUSE
The Miles Brewton House is perhaps the most photographed and written-about house in Charleston and is frequently cited as an outstanding example of Georgian architecture in the United States. Built by the wealthy merchant, Miles Brewton, in the 1760s, it has never been sold out of the builder's family. I began work on the papier m�ch� in this house in 1990 with the restoration architects Joe Oppermann and Charles Philips and the owners, Peter and Patricia Manigault. The papier m�ch� will be discussed according to the room and location in which it either survived or was restored according to the best evidence.
3.1 THE FIRST-FLOOR PARLOR
The parlor ceiling was essentially intact. Described as plaster for many years, it was identified correctly as papier m�ch� by Frank Welsh, a professional paint analyst in Bryn Mawr, Pennsylvania, during his examination of the house.
This ceiling decorated with a low-relief ornamental scheme featuring the foliate C and S scrolls of the fully developed rococo style was originally painted white. While these ornaments were coated with many layers of paint, very fine and sharp detail did not appear to the characteristic of this decoration, and full stripping of the paint was not carried out.
3.2 THE SECOND-FLOOR DRAWING OR “BALL” ROOM
In 1773, after dining with Brewton, the Boston Brahmin Josiah Quincy described the drawing room as having “rich blue paper with gilt moshee borders” (quoted in Andrews 1978, 33). More than 200 years later a worker involved in restoration of the house removed the remains of a rat's nest from behind a column on the hall side of the door to the drawing room. Numerous small shreds of gilded material were removed from the nest and carefully saved on the supposition that they are the only remains of the border described by Quincy (fig. 1).
Fig. 1.
Fragments of the drawing room border as recovered from a rat's nest.
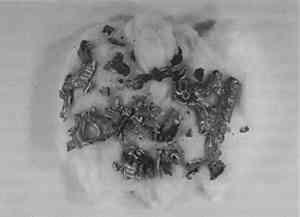 |
None of the drawing room border shreds were larger than an inch, and most were considerably smaller. Optical microscopy showed them to be composed of short-fibered linen and cotton rag pulp as is typical of the period. The paper appeared to have been built up in layers in negative or intaglio molds, with the paper that extended beyond the design finally folded over the back to create a hollow structure. The molded paper was probably waterproofed and hardened with linseed oil as indicated by its fluorescence under ultraviolet illumination. The dried strips were then coated with layers of calcium carbonate gesso and a thin coating of a plum-colored bole as preparation for traditional water gilding and as is consistent with English gilding of the period. Obvious original faults or gaps in the gilding are present, indicating that the material was not gilded to the ultimate degree of finish, probably owing to cost considerations. Small areas of bole were allowed to show, having the effect of deepening the perceived color from a normal viewing distance.
The shreds were laid out in an organized way to analyze the design and make joins. Some fragments must have been fairly large when stored by the rat, because several pieces joined to each other. The joined pieces were sufficient to make a full repeat of the pattern (fig. 2).
Fig. 2.
The drawing room border in the process of reconstruction.
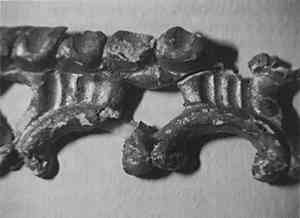 |
The fragments were cleaned mechanically to remove large encrustations. Pieces were joined with a 50% (w/v) B72 resin solution in acetone. Where pieces were very fragile, they were consolidated before joining them with a 20% (w/v) solution of B72 in toluene. Joins were reinforced on the back with small pieces of Japanese paper adhered with Rhoplex A.C. 33. A few areas were bridged with paper and Rhoplex to fill missing parts, then a fill built up on top of the paper with Polyfix. Surfaces were cleaned with ethanol after repair was complete. A box was constructed of basswood, birch plywood, and glass to safely house the larger repaired border section and several additional pieces that did not make contiguous joins. This archival storage box made it possible to minimize restoration.
3.3 STAIR HALL CEILING
Papier m�ch� decoration on the cove ceiling of the stair hall had been painted many times and evidently altered by restoration. The decoration consists of a central sculptural figure medallion and a decorative border that forms a rectangle around the flat central portion of the ceiling and is doubled back-to-back down the corners of the cove.
3.3.1 Examination and Treatment of the Borders
Initial examination of the border indicated that roughly 60% of the original material was intact under layers of paint. The paint could be picked off mechanically in some areas, showing burnished gold underneath. Some sections of border had been replaced with crudely modeled plaster fills, while other areas of original border were sagging and poorly attached. The border had been attached originally with brass brads, which had been supplemented at a later date with iron tacks. Paint was removed from the original border using heat guns and dental probes. The border was left in place owing to its fragility; excessive damage would have resulted had removal been attempted. In addition, it was felt that the original placement of the border fragments and the attachment hardware were worth preserving. Several loose sections representing a complete repeat were removed, however, to serve as models for replication of infill material and to be conserved more fully. These sections were taken to the Art Conservation Department in Buffalo and conserved in the same way as the drawing room fragments. The border was reproduced as described below. The reproduction was antiqued by abrasion and pigment toning to match the extant border.
Loose areas of the cleaned original border were adhered to the ceiling plaster using hot-glue-gun adhesive consisting of polymide resin. The reproduction material was cut out to infill all of the areas of loss and adhered in place with a combination of no. 4 stainless steel sheet metal screws and glue-gun adhesive. Original material was stripped of paint residues using a methylene chloride-type stripper rinsed with ethanol. Small losses, nail heads, and new screw heads were either inpainted with acrylic emulsion gold paint or with the blue background color of the ceiling.
3.3.2 Examination and Treatment of the Figure
The central sculptural figure was found to be extensively plastered over with gypsum plaster and heavily damaged. Examination and treatment were necessarily combined due to this plaster that revealed the original figure only as it was removed. Plaster was mechanically excavated using serrated plasterworking tools, small chisels, dental probes, and vibro-tools.
Before treatment the figure appeared as a female figure with crudely modeled breasts and oversize head seated in cloud shapes (fig. 3). Removal of the plaster revealed that the entire upper torso was missing and that the original face was present but crushed into the head cavity (fig. 4). The revealed original was far superior to the restoration in senstivity of modeling. Remains of original modeling around the missing torso area indicated that the original was probably a draped figure. The figure was restored as a draped male figure of Apollo facing left with a lyre cradled in the left arm and an unknown attribute held in the right (fig. 5). The figure is seated in cloud shapes (nimbi) with rays of light emanating from behind the head and nimbi.
Fig. 3.
The stair hall figure in situ as excavation of plaster overfill has begun.
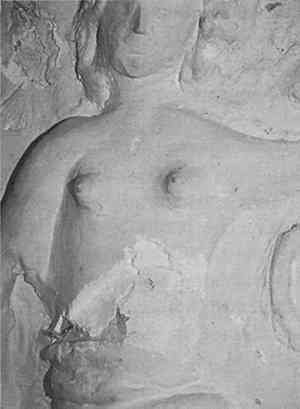 |
Fig. 4.
The Apollo figure in its actual state after excavation of plaster and removal from the ceilling.
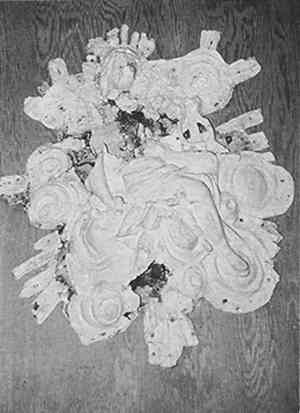 |
Fig. 5.
The conserved and restored Apollo figure back in place.
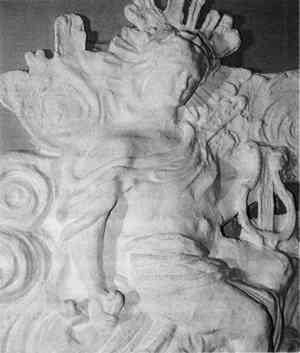 |
Numerous nails, wires, and screws were removed from the figure during the excavation of the plaster. The figure was finally fully detached and placed on a table for repair and restoration. Repairs to the original were made with 50% (w/v) B72 in acetone and reinforced with Japanese paper saturated with Rhoplex A.C. 33. Large areas of loss were bridged and reshaped with animal glue-sized gauze that was then modeled over with spackling compound bulked with lighweight glass microballoons, which was allowed to dry and further shaped and smoothed by burnishing. The missing torso area was restored by modeling sculpey, a polymer-type modeling material directly in the chest cavity. Layers of Japanese paper and Rhoplex were built up on top of the modeling material to fill up to the edges of the void. This paper shell was removed and strengthened further with glue-sized gauze applied to the back. The modeling material was then removed from the chest, and a structural support made with balsa wood and glue-gun adhesive (polyamide) was built into the chest cavity. The reconstructed torso was adhered to the balsa framework and to the edges of the original with glue-gun adhesive and Rhoplex and paper. Screw and hardware holes, cracks, and minor damages were filled with microballoon spackle.
After the figure became secure enough to be turned over, a degraded corrugated cardboard backing from an earlier restoration could be removed. A new backing board was cut from 4-ply acid-free mat board and adhered to the original with spots of glue-gun adhesive. Further fills were carried out with glue-sized gauze, which was wrapped around the back of the mat board where possible. Final filling and remodeling of missing nimbus edges and sun rays were done with microballoon spackle on top of the mat board. An isolating layer of Soluvar varnish and titanium white was spray-applied to the entire figure before painting. The figure was painted with a low gloss white oil paint. Areas of mat board around the perimeter that had been left for reattachment were punched and screwed through into the ceiling with no. 8 stainless steel panhead sheet metal screws. The screw heads were smoothed over with spackle and painted to match the blue background color of the ceiling.
3.4 REPLICATION OF GILDED BORDER
At the request of the owners, I replicated 170 ft of gilded border for the drawing room and 30 ft of border for the stair hall ceiling, using materials and techniques as close to the originals as possible, with modifications dictated by modern understanding of material permanence.
The paper pulp chosen for the project was pure cotton “half stuff,” or partially beaten pulp. This pulp was chosen for its long-term durability and historic authenticity, as it is, like the original, a pure, high-quality pulp with no wood content. However, pure cotton pulps were not used before the 19th century, and its use will make the reproduction material distinguishable from 18th-century border.
A section of the patterns containing a full repeat was modeled free hand in nonhardening clay (plasticene) (fig 6). Because of the fragility of the original, it was not possible to make a mold or impression, but careful measurements were made to ensure fidelity. The models also needed to be made slightly larger than the originals to account for shrinkage. The short sections so produced were multiplied by taking a plaster mold from them, making plasticene impressions from the mold, stringing them together, and refining the pattern further in the resulting long section. These final patterns were shellacked, and silicone rubber master molds were made from them. The silicone rubber molds were used to produce wax patterns from which several plaster working molds were made using Hydrostone plaster reinforced internally with loose-weave jute fabric. The plaster molds were bedded to plywood boards using microballoon-bulked epoxy resin to produce very strong molds capable of withstanding the pressure necessary to press the paper. Although some molds were impregnated on the mold surface with shellac and wax, polyurethane varnish proved to give the best results in terms of mold longevity. The finished molds were sprayed with Parafilm mold release agent prior to pressing in the pulp.
Fig. 6.
Modeling the stair hall ceilling border prior to mold making.
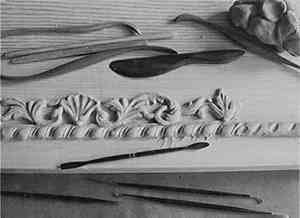 |
The pulp was prepared by beating the cotton “half stuff” in a hollander beater during a fairly brief beating cycle of one-half hour. A small percentage (less than 1%) of methyl cellulose was added to produce a somewhat harder paper capable of reproducing detail. The wet pulp was heaped onto the mold surface by hand, with care taken to distribute it as evenly as possible. A polypropylene screen was laid on top, and a large part of the water was removed by blotting with sponges and cloth diapers (fig. 7). Although initial production was carried out using specially shaped wooden tools to press the pulp into low spots, a system of silicone rubber countermolds was later devised that speeded up production and gave better results. An initial countermold was made with a gap between it and the mold surface roughly corresponding to the thickness of fully wet pulp. This mold was pressed into the design with maximum hand pressure in conjunction with blotting. After the pulp had dried and contracted, a second pressing was done using a countermold with less clearance between it and the mold. Finally, hand modeling tools made to fit specific shapes were used in extreme low spots to be sure that the paper was in conformity to mold surfaces and free of voids. Thin spots and gaps were filled during this process by tearing small patches of wet pulp from the margins and transferring these to areas needing filling. The molds were then left to dry.
Fig. 7.
Removing the excess water from a pulp filled mold by sponging through a screen.
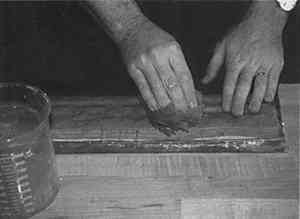 |
When the paper in the molds was virtually dry–usually after 10–12 hours—the strips were carefully removed and stapled to boards along the margins to prevent distortion while final drying took place (fig. 8). The somewhat fuzzy and imperfect surfaces of the border were burnished at this stage with a variety of shaped and polished steel burnishers. Burnishing was undertaken to compact the paper surface and heighten detail.
Fig. 8.
Removing a still damp border strip from a mold.
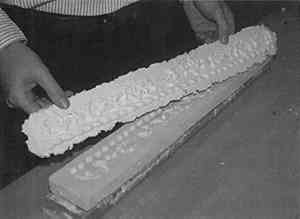 |
After complete drying, the border sections were impregnated with a soaking spray coat of Soluvar varnish and allowed to dry again. The varnishing helped to “set” the shape and dimension of the borders before application of the aqueous gesso and bole. Documentary evidence indicates that this step was accomplished in the 19th century by soaking the paper in linseed oil and allowing it to dry before further coating (DeVoe 1971). The border strips were then cut from the boards using a razor-sharp French-type leather skiving knife and trimmed further with scalpels (fig. 9). Some areas of the background were left in place to accept screws when attaching the border to the ceilings.
Fig. 9.
Cutting the border strip free of the drying board.
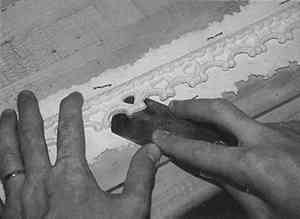 |
Preparation for water gilding was carried out using traditional materials and recipes. The strips were spray coated with four coats of gesso made from gilders' whiting in a 4.5% (w/v) rabbit skin glue solution. I have had best results spraying gesso through the cheapest available air brush (Badger model 250) because it operates with a simple atomizer and there are no internal parts to clog. After drying, the gesso was smoothed and polished with barely damp rags. A final spray coat of red colored bole or gilder's clay was spray-applied and subsequently polished. The strips were gilded with 23 carat gold leaf and the highlights were burnished with agate burnishers according to traditional practice. The steps in the preparation of the border are shown in figure 10.
Fig. 10.
Steps in the replication of a papier m�ch� border
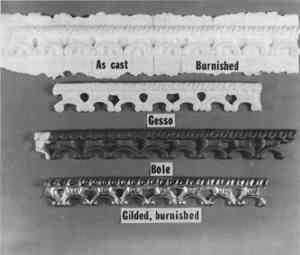 |
The border strips were finally spray-lacquered with Agateen lacquer on both the front and back to further waterproof them and protect the gold surface from damage by handling during installation. Details of the finished borders are shown in figures 11–12.
Fig. 11.
The ceiling moldings in the drawing room bordered with gilded papier m�ch� border
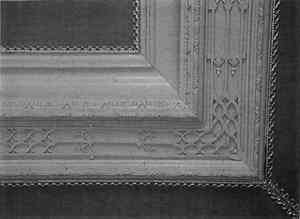 |
Fig. 12.
Detail of the gilded border strip back-to-back down the corner of the ceiling cove
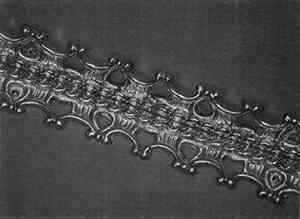 |
4 REPLICATION OF OTHER STAIR-HALL ORNAMENT
During restoration of woodwork in the stair hall, a third border pattern came to light in the form of small pieces of plaster fallen behind the wainscoting. The decision was made to replicate this border in plaster and use it to border the woodwork in the stair hall (fig. 13). Reconstruction of this design showed it to be identical to a surviving papier m�ch� border in the Wentworth House, indicating that the plaster pieces were a subsequent restoration of an original paper border.
Fig. 13.
Papier m�ch� patterns present in the Miles Brewton House (shown in plaster). (1) drawing room ceiling, (2) stair hall ceiling, (3) central hall walls bordering all woodwork.
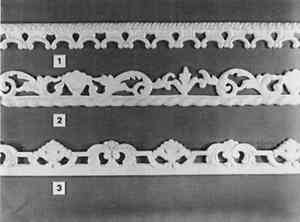 |
The rectilinear design of this border made it more expedient to carve the prototype model in wood. This pattern was molded and multiplied to create long master patterns and molds as described for the other borders. The final borders were cast in Hydrostone reinforced with cotton string and saturated with Soluvar varnish.
An early 20th-century scale drawing of the exterior wall in the stair hall showed an extensive rococo-style scheme of decoration above the windows. This decoration was entirely missing. One small piece of papier-m�ch� in a gadroon motif had been found in a bureau in the house. This fragment was in scale with a border shown in the drawing and probably came from this decoration.
For reasons of economy, this decorative scheme was reproduced in wood, plaster, and composition. Elements of the design were selected from the composition molds of George Jackson and Sons in London and from my own collection. Where no molds could be found that were appropriate in design and scale, the motifs were modeled and cast in plaster. All elements of the design were glued and nailed to Baltic birch plywood backings into larger units that could be screwed to the wood paneling of the stair hall. This decoration was painted white in conformity to the surface found on the papier m�ch� fragment.
5 CONCLUSIONS
Of the materials commonly used for interior relief decoration during the 18th century—carved wood, plaster, and papier m�ch�—papier m�ch� offered several advantages to both manufacturer and customer. The ornaments could be produced at a central plant and, except for mold making and gilding, by relatively unskilled workers. Available patterns were easily disseminated by catalogs, and the lightweight ornaments could be shipped anywhere and mounted by local craftsmen. This ease of installation clearly gave the larger relief schemes imitating plasterwork a ready market where skilled plasterers were few or nonexistent. It is also clear that the gilded or white papier m�ch� borders would have undersold the carved wood equivalent although “liable to harbor vermin” (Prime 1969, 224) as a contemporaneous Charleston wood carver stated.
Indeed, surviving papier m�ch� has become extremely brittle due to the depradations of insects, the degradation of the glue and linseed oil components, and their deleterious effects on the paper substrate. Reproducing this material allowed me to appreciate its properties when new: it is tough, flexible, capable of fine detail, and, due to its absorptive nature, somewhat easier to gild and burnish than gessoed wood. To hold a strip of border that looks like polished gold yet weighs next to nothing tricks the senses. These qualities of novelty and contradiction must also have appealed to elite educated dilettantes of the 18th century.
The restored Miles Brewton House is a unique example of the extensive use of a versatile material, popular in its own time, which has since been virtually forgotten. It is my hope that this extensive restoration will help papier m�ch� take its proper place in the history of 18th-century materials and techniques.
REFERENCES
Andrews, W.1978. Architecture, ambition, and Americans: A social history of American architecture, rev. ed.New York: Free Press.
Bielefeld, C.1850. Omaments … manufactured in the improved papier m�che�. London: The author.
Boyle, R.1966. The works, ed.T.Birch. 1671. Reprint. Hildesheim, Germany: Georg Olms Verglagsbuchhandlung. 1966.
Cornforth, J.1992. Putting up with Georgian D1Y. Country Life186(15):54–56.
Dickinson, G.1925. English papier m�ch�: Its origin, development, and decline. London: Courier Press.
Devoe, S. S.1971. English papier m�ch� of the Georgian and Victorian periods. Middletown, Conn: Wesleyan University Press.
Gottesman, R. S.1938. The arts and crafts in New York, 1716–76. New York: New-York Historical Society.
Longfield, A. K.1948. The manufacture of “raised stucco” or “papier m�ch�” papers in Ireland c. 1750–70. Royal Society of Antiquaries of Ireland88 (July):55–62.
Nylander, R., E.Redmond, and J.Sander, 1986. Wallpaper in New England. Boston: Society for the Preservation of New England Antiquities.
Osborne, H., ed.1975. The oxford companion to the decorative arts. Oxford: Clarendon Press. 603–8.
Oxford English Dictionary. 1971. Oxford: Oxford University Press. 1928, 439.
Prime, A. C.1969. The arts and crafts in Philadelphia, Maryland and South Carolina 1721–1785. New York: Da Capo Press. 224.
South Carolina Gazette. 1765. Charleston, April 20, 4-1. Winston-Salem, N.C.: Museum of Early Southern Decorative Arts research files.
South Carolina Gazeteer and Country Journal. 1765. Charleston, December 24. 1-1 Winston-Salem, N.C.: Museum of Early Southern Decorative Arts research files.
van derReyden, D., and D. C.Williams. 1986. The technology and conservation treatment of a nineteenth-century English “papier-m�ch�” chair. AIC preprints, 14th Annual Meeting, American Institute for conservation, Washington, D.C.125–42.
Waite, J. G.1972. The stabilization of an eighteenth century plaster (sic) ceiling at Philipse Manor. New York: New York State Historical Trust.
SOURCES OF MATERIALSAcryloid B-72 (a copolymer of ethyl methacrylate and methy acrylate)Rohm and Haas, Philadelphia, Pa. Rhoplex A.C. 33 (acrylic polymer emulsion)Rohm and Haas, Philadelphia, Pa. Polyfix (vinyl polymer and calcium carbonate filling material)LePages Ltd., Bramalea, Ontario Master Mechanic All Purpose Hot Melt Glue (polyamide glue-gun adhesive)True-Value Hardware, Chicago, III. One Time spackling compound (vinyl emulsion and glass microballoons)Red Devil Inc., Union, N.J. Sculpey (polyvinyl chloride modeling material)Polyform Products Inc., Schiller Park, III. Soluvar Picture VarnishBinney and Smith, Easton, Pa. Silastic, E., R.T.V. (silicone polymer molding material)Dow corning, Midland, Mich. Hydrostone (high-strength gypsum plaster)U.S. Gypsum, Chicago, III. Parafilm (microcrystalline wax-type release agent)Sculpture Supplies, Ltd., New York, N.Y. Methocel A4M (methyl cellulose)Dow Chemical Co., Wilmington, Del. Agateen (cellulose nitrate- type lacquer)Agate Lacquer Co., Long Island City, N.Y.
AUTHOR INFORMATION
JONATHAN THORNTON received his B.A. in art history and studio art from Antioch College in 1974 and an M.A. and certificate of advanced study in art conservation from the State University of New York (Cooperstown Graduate Program) in 1980. Since that time he has been teaching object conservation in the same graduate program, first at Cooperstown and subsequently in Buffalo, where he is now associate professor. His current research interests include the materials techniques and history of sculptural decoration. Address: Art Conservation Department, State University College of New York at Buffalo, 1300 Elmwood Ave., Buffalo, N.Y. 14222.
Section Index |