ABRASIVENESS OF CERTAIN BACKING FABRICS FOR SUPPORTING HISTORIC TEXTILES
LoERNA PALMER SIMPSON
ABSTRACT—Decisions to mount a historic textile to a backing fabric are often made in the conservation, display, or storage of historic textile items. A method for studying the abrasive nature of textile backing fabric surfaces was developed and investigated in this experimental research project. A test procedure was developed by adapting the crockmeter, a textile testing instrument. A test piece of flannel fabric was mounted on the crockmeter and rubbed against the backing fabric, and then the number of loosened fibers transferred to the backing fabric was counted. Four unbleached cotton fabrics—muslin, duck, warp sateen, and sailcloth—were identified as fabrics used by textile conservators and selected for initial study. Of the four fabrics, the muslin caused the fewest fibers to be removed. Differences in abrasiveness related to weight and weave of the four fabrics were analyzed. Although this methodology was accelerated from actual museum conditions, it allows comparision and rating of backing fabrics by providing a test for measuring fiber loss due to abrasive action of fabric surfaces. Further work on additional backing fabrics is planned.
1 INTRODUCTION
IN THE conservation, display, or storage of historic textile items, decisions are often made to mount the historic textile object to another fabric surface. This other fabric may function simply as a backing material for mounting, or it may support a fragile item, sometimes even bridging an open area where original yarns and structure may have been lost.
The mount design and the backing fabric itself need certain characteristics in order to function well. These characteristics include:
- adequate support for the historic textile;
- a visually satisfying surface appearance compatible with the historic item;
- necessary strength over time for the weight of the historic textile fastened to it; and
- a surface that does not introduce any hazards to the historic item.
Hazards that should be avoided include the presence of objectionable chemicals and finishes, such as starches, sizings, bleaches, spinning oils, and other impurities from fabric manufacturing processes, as well as accumulated surface dirt.
An additional hazard to be avoided is the placing of any abrasive, rough surface next to the historic textile. Sometimes a small degree of friction is helpful in holding the two textile items together so that they do not slide apart easily. However, too rough a surface in a backing fabric may also cut away at adjacent delicate fibers and fabric surfaces. This condition may result particularly if the item is displayed or stored in a vertical manner with gravitational force exerting pull on one surface against the other. In other circumstances, changes in environment such as humidity fluctuations may cause movement of the historic textile against its backing fabric. Even general handling of the item such as lifting and repositioning may cause movement of the two fabric surfaces against each other.
This experimental research project was designed to investigate the abrasive nature of certain textile backing fabric surfaces and to develop and refine a test procedure for measuring this abrasiveness. A review of literature revealed that no such textile test method existed. One related study was found in which surgical fabrics were tested for generation of lint (Buras and Harris 1983), but no previous studies on abrasiveness of backing fabrics used in conservation were discovered.
2 GENERAL CHARACTERISTICS OF A TESTING METHOD
SEVERAL IMPORTANT characteristics of a textile test method are described by Cohen (1982). A textile test should be both valid and reliable, measuring what is being studied and providing consistent, repeatable results. The test should be simple to perform and use equipment that is easy to operate and not too expensive. The testing procedure should be completed within a relatively short time. Generally, the test procedure will be accelerated compared to the actual action it is duplicating. Correlation should exist between the test procedure and the actual problem or end use being evaluated. The method should also provide a range of results that are measurable.
3 EXPERIMENTAL PROCEDURE
3.1 EQUIPMENT AND PROCEDURE
THE MODE of abrasiveness selected for study was the rubbing of fabric against fabric, while the measurement value selected was the number of loosened fiber particles transferred during rubbing. The crockmeter, a commonly used textile testing instrument, was adapted for this purpose. Buras and Harris (1983) had similarly adapted the crockmeter to produce linting of surgical fabrics. They had measured the weight of the transferred fibers on a sensitive analytical balance and made photomicrographs of representative transferred fibers with a scanning electron microscope. This researcher felt that such expensive equipment would limit the development of a simple, inexpensive test method that a conservator might use in a conservation laboratory. Therefore, it was decided to develop a simpler test procedure by counting the number of fibers transferred to the backing fabric specimens, using a readily available linen tester/pick glass. The crockmeter was selected as a modestly priced, readily available, and simple-to-use textile testing instrument.
The crockmeter's primary purpose is to evaluate colorfastness to crocking, i.e., the rubbing off of dyes from a fabric surface onto another surface. In the colorfastness to crocking test, AATCC Test Method 8 (AATCC 1988), the dyed or printed fabric is mounted on a lower platform, and rubbed 10 cycles with a white fabric mounted on a peg in the upper rubbing arm. The degree of color that rubs off onto the white fabric is then rated against a color transference scale. For this abrasiveness test the crockmeter peg was covered in a brightly colored, napped 100% cotton fabric obtained from Springs Industry, and the backing fabric specimen was placed on the lower platform (fig. 1). The rubbing action of the peg (10 cycles back and forth) allowed fibers from the upper colored flannel fabric surface (simulating the historic textile) to be transferred onto the white backing fabric mounted on the lower platform. The standard design of the crockmeter incorporated the following features: with a complete turn of the crank, a flat 5/8 in diameter peg moved back and forth in a straight line along a 4.125 � 0.125 in track on the specimen surface with a downward force of 900 g (32 oz) on the peg.
Fig. 1.
Crockmeter with peg in upper arm and backing fabric specimen placed on lower platform
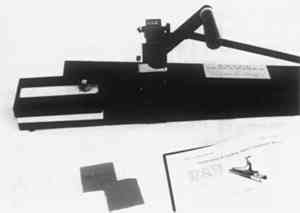 |
Although this method of fiber transfer was more accelerated than actual museum conditions would be, it was selected as an appropriate, fast test by which the abrasive action of the lower fabric surface might be studied. A 5 power linen tester with a 1 in square area was positioned over a centered template for viewing the transferred fibers, and a pick needle was used to assist in counting while scanning the representative 1 sq in of fabric (fig. 2). Preliminary testing had determined that a centered area of this size was appropriate for counting transferred fibers.
Fig. 2.
Linen tester positioned over template for counting transferred fibers
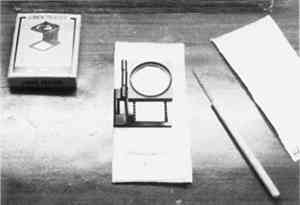 |
3.2 BACKING FABRICS
Four backing fabrics from Testfabrics, Inc.—representative of backing fabrics used by textile conservators—were selected for initial investigation. The unbleached 100% cotton fabrics (table 1) included muslin, duck, sailcloth, and warp sateen. Fabrics with similar fiber content but different fabric weights and fabric constructions were deliberately selected in order to determine if the test method would show a measurable range of values.
TABLE 1 Backing Fabrics Selected for Study
The backing fabrics were pretreated by laundering, then specimens were cut and conditioned under standard testing conditions of 70�F and 65% RH before being evaluated by the abrasiveness test method. A description of these procedures follows.
3.3 PRETREATMENT OF BACKING FABRICS
Pretreatment of the backing fabrics was performed, based upon recommendations in the ASTM draft 53.702, “Standard Practice for Pretreatment of Backing Fabrics Used in Textile Conservation” (ASTM 1988). The fabrics were washed, rinsed, and dried three times, using a phosphate detergent that did not contain bleaches, enzymes, carbonate builder, or fluorescent whitening agents (AHAM Standard Detergent or AATCC Standard Detergent 124-W.O.B). This special detergent was selected in order to avoid adding substances to the fabric that might not be thoroughly rinsed out and might later damage and weaken fiber structures by reactions such as oxidation. The wash-rinse-dry cycles were completed in order to remove residual amounts of sizing and impurities remaining in the backing fabrics as well as to reduce relaxation shrinkage that might occur. Tortora (1987, 389) states that “the wetting of a fabric causes the tension that has been applied during the manufacture of the fabric to be relaxed, so that fabrics generally shrink after the first and up to the fifth laundering.”
3.4 SIZE AND NUMBER OF FABRIC SPECIMENS
Twenty specimens, 2 �–by–6 in, were cut from each backing fabric, with 10 specimens for the face evaluation and 10 for the back evaluation. These fabric specimens were cut with the longer dimension (6 in) in the warpwise direction rather than on the true bias as had been done in a preliminary abrasiveness study reported by this author (Simpson 1988). This change was based on recommendations by conservators that testing in the warp direction rather than the bias would more closely simulate the mounting position of historic textiles on a backing fabric, where the warp is usually positioned vertically. The prewashed backing fabrics were conditioned at least 24 hours at standard textile testing conditions of 70�F and 65% RH before being tested.
Both the face and back sides of the backing fabrics were tested. The muslin, duck, and sailcloth did not visually appear to be different from top to bottom side, so a face and a back side were designated arbitrarily. However, the nature of the warp sateen weave provided a warp float face side and distinctly different back side.
3.5 STATISTICAL ANALYSIS
The first research question to answer was whether differences existed between the arbitrary face and back sides for each of the four backing fabrics. The t-test for independence was calculated, with significance set at .05 (SAS 1985). When differences did not exist, data from the two sides were pooled for further analysis.
The one-way analysis of variance by ranks (SAS 1985) was used to measure the effect of fabric type on the number of fibers removed; if significant, the effects of fabric weight and fabric construction on number of fibers removed were also determined. Where significance was shown, the Ryan-Einot-Gabriel-Welsch multiple range test (REGWQ) (SAS 1985) was used to determine which fabrics differed significantly from the others. Significance levels were set at .05 for both tests.
4 RESULTS AND DISCUSSION
4.1 DIFFERENCES IN FACE AND BACK SIDES OF FABRICS
THERE WERE no significant differences in the number of fibers removed by the abrasive test for the face and back sides for the muslin, duck, and sailcloth fabrics, so the two sides were pooled for further statistical analyses. As anticipated, there were differences in the face and back sides for the warp sateen fabric. Therefore, the face side of the sateen fabric, which had the warp satin floats, was included individually in the analysis. The back side of the warp sateen fabric was eliminated from further analysis, since it was felt that this fabric would be chosen specifically to utilize the warp satin face.
4.2 EFFECT OF FABRIC
Significant differences were evident for the four fabrics tested (fig. 3). The muslin fabric removed fewer fibers (36.6 fibers) than did the duck, warp sateen, and sailcloth fabrics (58.0, 59.2, and 59.4 fibers, respectively). The latter three fabrics were not significantly different from each other when analyzed by the REGWQ multiple range test.
Fig. 3.
Fiber count (abrasiveness) by fabric type: muslin, duck, warp sateen, sailcloth. (Note: Group means with the same letter are not significantly different at the .05 level of confidence.)
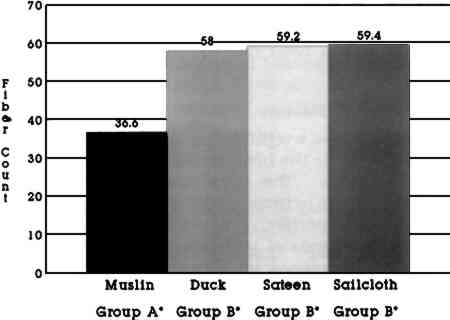 |
Because differences were noted for the muslin fabric when compared with the duck, warp sateen, and sailcloth fabrics, further analyses of the fabric construction characteristics were completed. Fabric weave and weight differences were investigated.
4.3 EFFECT OF WEAVE CATEGORY AND YARN INTERLACEMENT
There was one plain-weave construction, the muslin fabric. In the warp sateen fabric, each warp yarn floated over 4 filling yarns in a warp satin-weave structure. Both the duck and sailcloth fabrics were a modified basket weave, with paired warp yarns interlacing over and under each filling yarn. As shown in figure 4, the plain-weave fabric removed the fewest fibers when tested for abrasiveness (36.6 fibers), while the modified basket-weave fabric group removed significantly more fibers (58.7 fibers), as did the satin-weave fabric structure (59.2 fibers). The modified basket-weave and satin-weave categories were not significantly different from each other but were different from the plain weave. It was originally theorized that the satin weave, having the fewest interlacements of warp with filling yarns, would have the lowest abrasiveness rating, while the plain weave with the maximum number of interlacements would have the highest rating. Instead, the opposite was true. For these four fabrics, other factors appeared to be more influential on abrasiveness than the degree of yarn interlacement in the weave structure. It is speculated that yarn size and yarn twist may be contributing factors.
Fig. 4.
Fiber count (abrasiveness) by fabric construction: plain, modified basket, and satin weaves (Note: Group means with the same letter are not significantly different at the .05 level of confidence.)
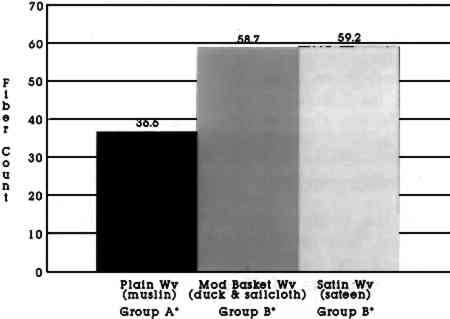 |
4.4 EFFECT OF FABRIC WEIGHT
The lightest weight fabric was 3 oz/sq yd (muslin), while the heaviest fabric was 9 oz/sq yd (sailcloth). The duck and warp sateen fabrics fell in between, at 7 oz/sq yd and 8 oz/sq yd, respectively. When analyzed by the one-way analysis of variance, there were significant differences in abrasiveness between the lightest-weight fabric and the other three heavier fabrics. However, the three fabrics weighing 7, 8, and 9 oz/sq yd were not significantly different from each other (fig. 5). The 7 oz/sq yd fabric was more than twice the weight of the lightweight fabric and did remove significantly more fibers in the abrasiveness test. However, the 9 oz fabric weighed three times that of the light-weight fabric (at 3 oz/sq yd) yet did not remove any more fibers than did the 7 and 8 oz/sq yd fabrics.
Fig. 5.
Fiber count (abrasiveness) by weight of fabric: 3, 7, 8, and 9 oz/sq yd. (Note: Group means with the same letter are not significantly different at the .05 level of confidence.)
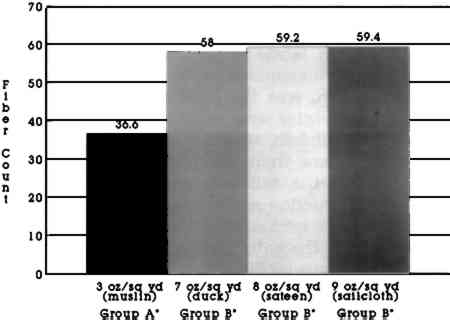 |
5 CONCLUSIONS
Of the cotton unbleached backing fabrics studied, only for the warp sateen fabric were the face and back sides found to remove differing numbers of fibers, while for muslin, duck, and sailcloth the top and bottom sides of the fabrics were equally abrasive. Muslin was the lowest in abrasiveness as determined by the modified crockmeter test, while the other three backing fabrics removed more fibers. When fabric weight and weave construction were examined, the lightest weight fabric, muslin, was the least abrasive, while the heavier fabrics were more abrasive. However, the sailcloth was no more severe in removing fibers than the duck and sateen, even though the sailcloth was the heaviest. Weave construction and degree of yarn interlacement were evaluated. Unlike the original expectations, the satin weave, which had the fewest interlacements, was in the more abrasive grouping, while the plain weave with the most interlacements was in the less abrasive category. Thus, of the four fabrics tested, the lightweight muslin was the least abrasive in nature. The other three fabrics—duck, warp sateen, and sailcloth—appeared more abrasive, although they differed among themselves when weight and fabric construction/yarn interlacement were analyzed.
Testing of additional backing fabrics is planned in order to answer questions raised by this initial study. These questions include: What is the action of different fibers such as linen, silk, and synthetics, which are longer and smoother than the cotton fiber? What are the effects of the amount of yarn twist or various yarn sizes on the abrasive nature of the fabric?
It is acknowledged that the relationship of this abrasion test to actual textile mounting conditions has not been demonstrated. However, actual mount displays and conditions were observed, and similar conditions were selected when working out the testing procedure, e.g., the movement of one fabric surface against another. When the general requirements of a testing procedure are understood, then the real actions of movement and abrasion that may take place slowly over days, weeks, or months must necessarily be quickened. This abrasive test is fast and simple to perform, uses equipment that is not prohibitive in price, and provides a range of measureable values.
Although accelerated from actual museum conditions, this methodology appears to provide a procedure for measuring fiber loss due to abrasive action of fabric surfaces. It also allows comparison and rating of the backing fabrics tested and should help in providing a better understanding of certain important factors at work in such situations. Certainly, the abrasive action is only one of many factors to be considered when appropriate backing is selected. However, conservators who are concerned about fiber loss with fragile historic textiles may find this information useful in selecting less abrasive backing fabrics.
SOURCES OF MATERIALS USEDAATCC crockmeter, handpowered or electricAtlas Electric Devices Co., 4114 N. Ravenswood Ave., Chicago, Ill. 60613 Linen testerConservation Materials Ltd., 1165 Marietta Way, Sparks, Nev. 89431 Red 100% cotton flannel, “Furry”Springs Industry, Ft. Mill, S.C. 29715 Backing fabricsTestfabrics, Inc., P.O. Drawer O, Middlesex, N.J. 08846 Detergent without optical brightner, bleach, or, fabric softener is AHAM (Association of Home, Appliance Manufacturers) Standard Detergent, available in 2-, 5-, and 20-lb cansTextile Innovators Corp., CYBER Center, 1600 Pennsylvania Ave., York, Pa 17404, or 124-W.O.B. in 20-lb bucketsAATCC, P.O. Box 12215, Research Triangle Park, N.C. 27709 Hand-drawn template, 2 �–by–6 in, with centered, 1 in opening, is cut from manila or poster board
REFERENCES
AATCC. 1988. AATCC test method 8-1985, Colorfastness to crocking: AATCC crockmeter method. In AATCC Technical Manual 1988, 58:24–25. Research Triangle Park, N.C.: American Association of Textile Chemists and Colorists.
ASTM. 1988. Draft 53.702, Standard practice for pretreatment of backing fabrics used in textile conservation. Unpublished document. Philadelphia, Pa.: American Society for Testing and Materials.
Buras, E. M., Jr., and R. H.Harris, Jr.1983. Generation of lint from fabrics. Textile Chemists and Colorists15 (January): 17–19.
Cohen, A. C.1982. Beyond basic textiles. New York: Fairchild Publications.
SAS. 1985. SAS user's guide: Statistics, 5th ed.Cary, N.C.: SAS Institute, Inc.
Simpson, L. P.1988. Investigating the abrasive characteristics of textile fabric surfaces supporting historic textiles. Textile Specialty Group Abstracts, AIC preprints, 16th Annual Meeting. American Institute for Conservation, Washington, D.C.296.
Tortora, P. G.1987. Understanding textiles. New York: Macmillan Publishing Co.
AUTHOR INFORMATION
LOERNA PALMER SIMPSON is assistant professor of textiles in the Department of Apparel, Interiors, Housing, and Merchandising, Oregon State University. She received her Ph.D. from Texas Woman's University and her master's degree from Kansas State University. She is active in several professional organizations, including AIC, American Society for Testing and Materials (ASTM), and American Association of Textile Chemists and Colorists (AATCC). Address: Department of Apparel, Interiors, Housing, and Merchandising, Oregon State University, Corvallis, Oreg. 97331.
Section Index |