CELLULOID OBJECTS: THEIR CHEMISTRY AND PRESERVATION
JULIE A. REILLY
ABSTRACT—Cellulose nitrate plastic was the first synthetic commercial material. Cellulose nitrate was used to produce a great number of objects now in museum collections. This paper discusses the manufacture, deterioration, and preservation of celluloid objects.
1 A HISTORY OF CELLULOSE NITRATE PLASTICS
1.1 INTRODUCTION
MANY INSTITUTIONS find that their collections include objects made from early plastics, but little information is available to inform collections management and conservation decisions with regard to these objects. Although there is a fair amount of information available concerning cellulose nitrate conservation materials and film products, there is relatively little published material concerning objects made from cellulose nitrate. In an effort to address this problem, the following information has been compiled concerning the history, composition, manufacture, and deterioration of celluloid objects.
1.2 HISTORICAL SIGNIFICANCE
The impetus for the synthesis, refinement, and manufacture of celluloid was a great rise in the demand for ivory, tortoise shell, and horn objects while the supply of these materials was fixed and the cost high. The search for an imitation of ivory and other natural materials was prompted by fears that the wildlife populations of the world were being rapidly decimated (Friedel 1977, 69).
Celluloid was manufactured commercially in England as early as 1866, when the Parkesine Co. was established by A. Parkes (Kaufman 1963, 119). The company was liquidated in 1868, but the manufacture of celluloid has continued to the present. In the United States, celluloid manufacture began in 1870 with the formation by J.W. Hyatt of the Albany Dental Plate Co. (later the Celluloid Manufacturing Co., which became part of the Celanese Corp.) (Kaufman 1963, 38). The use of the word “celluloid” to describe these plastics was patented by J. W. Hyatt. Most celluloid objects were made between 1846 and 1950. (See table 1 for a history of celluloid invention and usage.)
TABLE 1 Chronology of Cellulose Nitrate-Related Events
Celluloid was first marketed as an imitation ivory used to make small personal objects. Eventually celluloid was used to make an astounding variety of objects (see table 2). However, as Robert Friedel writes: “For the first twenty years that celluloid was on the market, the identification of the material as an imitation substance was paramount in its uses and public description of them (Friedel 1977, 175).”
TABLE 2 Uses of Celluloid
Friedel writes that by the turn of the century celluloid was no longer stereotyped as an imitative material but was valued for its unique qualities in photographic and cinematographic applications:
The large scale adoption of celluloid in photography revolutionized that medium, made another medium, cinematography, technically feasible for the first time, and gave celluloid its most significant breakthrough from imitation. The widespread use of celluloid in photography, and in other areas, drew attention to the material's faults as well as to its uses. This was most clearly demonstrated by the concern over the substance's flammability. Hence came a search for substitutes for celluloid. [Another] … important but unexpected role played by celluloid was as a model of a plastic material—both of what such a material could be and of what it should not be. One of the greatest achievements of celluloid was to provide, by both its virtues and its shortcomings, many of the central themes to be taken up by the seekers of new materials in the 20th century. Celluloid became one of the most important measures by which plastic materials were judged…. As the new plastics … began to emerge …, celluloid began to diminish in importance but not before it had demonstrated the possibilities of an entire class of new substances (Friedel 1977, 205–206).
By the 1950s celluloid was commercially manufactured only to make lacquers and coatings, adhesives, and some textile fibers. Small batches of celluloid are custom made today for replacement parts for musical instruments and other historic objects (Lundberg 1983). Celluloid has many brand names (table 3). Most are obsolete but are often used indiscriminately by those who deal with historic plastics.
TABLE 3 Brand Names of Cellulose Nitrate Products
Much early work was done by chemists and inventors on the characteristics and chemistry of celluloid. Although celluloid led researchers into the realm of polymer science, due to its rapid decline and substitution by new polymers, it has never been studied extensively with the theoretical and instrumental tools available to scientists today. Thus we have a spotty and incomplete understanding of celluloid and its chemical nature.
2 SYNTHESIS AND MANUFACTURE
2.1 GENERAL
CELLULOSE NITRATE is created when the cellulose molecule is chemically modified by strong nitric acid, sulfuric acid, and water (fig. 1). The compound thus formed has been used to produce a wide variety of materials, including explosives, adhesives and cements, film bases, collodion, lacquers and coatings, and solid plastics (table 4). The primary differences among these various materials can be related to the degree of nitration of the cellulose nitrate molecule used in their manufacture. The level of nitration of a cellulose nitrate molecule is usually given as the percentage of nitrogen atoms per glucose residue in the molecule. Other differences are due to the cellulose nitrate/plasticizer ratio and the presence of varying amounts of solvent in the formulation.
Fig. 1.
Cellulose nitrate, cellulose, and camphor molecules
 |
TABLE 4 Cellulose Nitrate-Based Products
The synthesis and manufacture of celluloid plays a pivotal role in its long-term stability; in many cases, the production history of an object will determine its survival. The following discussion of the synthesis and manufacture of celluloid highlights those factors that directly or indirectly affect the long-term condition of objects in museum collections.
2.2 RAW MATERIALS
The raw materials required to synthesize celluloid include cellulose fibers, nitric acid, sulfuric acid, water, alcohol, camphor, colorants, and fillers (fig. 2). The cellulose fibers, acids, water, and alcohol are used to make cellulose nitrate, which is mixed with the camphor, colorants, and fillers to make celluloid.
Fig. 2.
Flow chart of celluloid manufacture
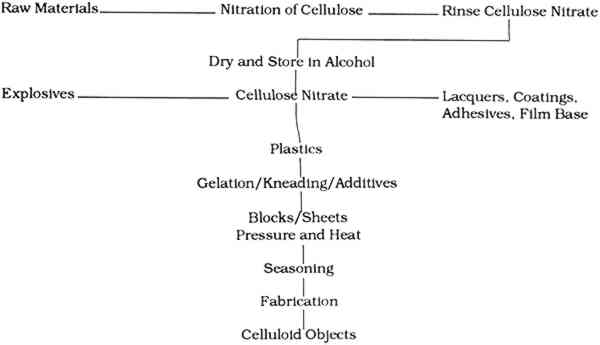 |
2.2.1 Cellulose
The starting material, cellulose, can be obtained from a variety of sources, including cotton, ramie, flax, jute, and wood pulp (fig. 1). The main commercial source of cellulose for cellulose nitrate synthesis in the United States was cotton mill waste, including cloth scraps from clothing production and waste fibers from spinning plants. These wastes were processed by degreasing with carbon tetrachloride or benzene, scouring, bleaching, and washing to yield fairly clean short cotton fibers (Worden 1911, 1:38–39). Cotton mill waste was the most common source, but considering the economic or commercial nature of cellulose nitrate production, it is conceivable that any type and quality of cellulose may have been used to make cellulose nitrate.
The inherent qualities of the original cellulose are partially retained by the finished celluloid. For this reason, one potential source of deterioration in celluloid comes from the instability of the cellulose molecule and the chemicals used to process the cellulose.
2.2.2 Acids, water, and alcohol
The nitric and sulfuric acids used were generally of high purity, although in more recent processes much of the acid mixture used is “waste acid” reclaimed from other processes (Worden 1911, 1:83–84). The water and alcohol used were generally of high quality, although lower purities of these liquids were also often used for economic reasons. Impurities in any of the above liquids may introduce centers of deterioration in finished celluloid.
2.2.3 Camphor
After the cellulose nitrate is synthesized, it is mixed with camphor, a resin from the evergreen cinnamomum camphora that grows in Asia and Florida (fig. 1). The trunks, roots, and branches are steam distilled to yield the resin, which can be pressed and fractionated into several components, all consisting of variations of the general camphor molecule (C10H16O) (Brady and Clauser 1977, 126–28). The primary structure is 1,7,7-trimethylbicyclo(2,2,1)hepta-2-one (Selwitz 1988, 43). Camphor is a white crystalline substance that belongs to the terpenoid family. It is bicyclic and the natural form is dextrorotary. The specific gravity of camphor is 0.986 to 0.996. It sublimes (evaporates from the solid) at room temperature, melts at 176�C (350�F) and boils at 209�C (408�F) (Encyclopedia Americana 1983, 303). Camphor was first synthesized in 1859 but was not commonly made for industrial uses until after World War I (Kirk and Othmer 1982, 745–49).
Synthetic camphor is produced by converting α-pinene from turpentine to camphene to isobornyl acetate to isoborneol to camphor. Synthetic camphor is chemically identical to natural camphor but is optically inactive (racemic) (Brady and Clauser 1977, 126–28; Kirk and Othmer 1982, 709–62).
Several types of camphor substitutes have similar characteristics but different chemical structures. They include Borneo camphor (borneol) and bornyl chloride. Neither of these compounds was widely used but may have been mixed with camphor (Brady and Clauser 1977, 126–28). Other camphor substitutes developed by industry include Lindol (Celanese Corp.), which is tricresyl phosphate ortritolyl phosphate; triphenyl phosphate; dehydranone (Union Carbide); and cyclohexyl levulinate. None of these products offered better characteristics than camphor (for less cost). None was used to replace camphor entirely, although small amounts were often added to the celluloid mixture. Worden lists the characteristics that make camphor the best “latent solvent” for cellulose nitrate:
- It is an excellent gelatinizing agent of quick and deep penetration, and is an energetic solvent….
- It is readily soluble in ethyl alcohol … [methyl alcohol and acetone]….
- It has a high melting (175�F) and boiling (204�F) point, and gives, therefore, a solid celluloid,
- Its characteristic odor is usually considered as not unpleasant, and it has no cumulative or deleterious effects on the makers and handlers of the celluloid. Furthermore, the volatility is so low as to make loss from evaporation during storage negligible.
- It is uncommonly resistant towards chemical agents [nitric acid, acids, alkalis] and does not liberate anything on liquefying which would tend to decompose celluloid….
- It reduces the explosibility, but not the inflammability, of cellulose nitrate when mixed with it.
- It does not possess a high power of crystallization, and hence does not separate out of celluloid upon heating and subsequent [sic] cooling or upon long storage.
- Light has no effect upon it … (Worden 1911, 1:249).
Worden writes that other “latent solvents” do not readily “gelatinize” cellulose nitrate, crystallize out, darken on exposure to light, soften, or produce other unwanted characteristics in cellulose nitrate plastics.
2.2.4 Additives
Colorants added to celluloid include dyes, pigments, and lakes. Other fillers and additives include alcohol-soluble “antacids” for translucent celluloid. Opaque celluloid was “stabilized” by certain fillers such as zinc oxide and zinc carbonate and did not generally require an “antacid” (Worden 1911, 2:595). Stabilizers for translucent celluloid included aryl phenyl ureas, lactates (sodium, potassium, calcium, strontium, magnesium), and many other substances (Worden 1911, 2:597–99). The combination, quality, and quantity of the numerous additives to celluloid affect its stability.
As the above discussion suggests, the raw materials used to create celluloid play an important role in the stability or instability of the finished celluloid.
2.3 Cellulose Nitrate Synthesis
As noted earlier, the first step in making celluloid is the synthesis of cellulose nitrate fibers (fig. 2). This synthesis is achieved by exposing cleaned cellulose fibers to an aqueous solution of nitric acid. Many of the two secondary hydroxyl groups and the one primary hydroxyl group on the glucose units of cellulose become esterified. The basic reaction is as follows:
Fig. .
 |
As the arrows indicate, this reaction is reversible in the presence of nitric acid and water. The nitrate groups oxidize the cellulose residues and produce nitrous oxides that catalyze further reactions. This reversibility of the nitration reaction indicates a source of potential deterioration.
Early in the experimentation with this reaction, it was discovered that the presence of another acid in the nitration vat would produce more uniformly nitrated cellulose nitrate and help reduce the cost of reagents for the reaction. Water, acid salt mixes, other organic liquids, and several acids were added to reaction vats by researchers in an attempt to find the optimum cellulose nitrate. Most of these experiments were unsuccessful. Sulfuric and phosphoric acids were acceptable, but phosphoric acid proved to be too corrosive to the reaction vats at nitration temperatures and was only used for small batches of explosive-grade cellulose nitrate. Sulfuric acid proved to be the best additive. It slowed the nitration reaction, lending the manufacturers a degree of control (Miles 1955, 61–101). It produced more uniformly nitrated batches of cellulose nitrate and thus improved the quality of the cellulose nitrate produced.
Once it had been established that a sulfuric/nitric acid mixture was best, much research was dedicated to deriving the optimum concentrations of each reagent in the mix. The optimum mixture for the nitration mix ranges as follows:
It was thought that the contributing acid (sulfuric) aids in the nitration reaction by swelling the fibers so that the nitrate groups could penetrate the fibers more easily and evenly. Nitrate ester formation is favored over sulfate ester formation so that comparatively few sulfate groups are left bound to the cellulose nitrate.
The nitration of cellulose nitrate appears, on paper, to be a fairly simple reaction. However, no clear comprehensive mechanism has been found to describe it. Analysis of carefully controlled and nitrated cellulose indicates that the reaction is not as simple as was believed. The percentage of nitrogen in the resultant cellulose nitrate indicates that the reaction is not stoichiometric. The irregular nitration was thought to be a result of inhomogeneities in the original cellulose fibers (Clark 1981, 247).
It was believed that the amorphous and crystalline regions of the cellulose fibers reacted differentially to the nitration mix. The comparatively large sulfate molecules were believed to enter the amorphous regions, creating pathways for the smaller nitrate groups. The sulfate groups were supposedly too large to enter the crystalline regions, where the nitrate groups had to fend for themselves. This model would indicate that NO3 and SO4 concentrations or percentages would vary randomly throughout a fiber and might explain nonstoicheometric nitration.
A study by D. T. Clark (1981, 247–49) indicates that the physical structure of cellulose may not be responsible for the irregular nitration of the molecule. Clark's work shows that the degree of substitution of nitrogen—a measure of the percent nitrogen—in cellulose nitrate is 2.8 molecules of nitrogen per cellulose residue. This is not stoichiometric, as noted by earlier chemists.
Clark summarizes early concepts on cellulose nitrate by indicating that irregular nitration was thought to be due to inhomogeneities in the structure of cellulose or inhomogeneities in the nitrating mix. To find more concrete proof for the reason for the irregular nitration of cellulose, Clark used electron spectroscopy for chemical analysis (ESCA) to look at the chemical compositions of various regions of cellulose nitrate fibers. Clark varied the depth of the particle beam to obtain the chemical composition at different depths in a cellulose nitrate fiber. He found that the degree of substitution of nitrogen for the whole fibers he examined was the same as the degree of substitution of nitrogen on the fiber surfaces. He found that in mixed acid nitrations, sulfate esters were formed only on the fiber surface, not in the inner regions of the fibers or even in “amorphous” inner regions. He also found that the sulfate—nitrate—denitration equilibrium was reached rapidly during the nitration reaction. The similarity of the surface degree of substitution to the bulk degree of substitution, the lack of sulfate esters in the fiber interior, and the rapid and constant sulfate—nitrate—denitration equilibrium do not fit well with the previously proposed explanations for the composition of cellulose nitrate. Clark's work indicates that a great deal of research and examination are necessary before we will have a complete understanding of the properties and chemistry of cellulose nitrate.
The inhomogeneities of cellulose nitrate fibers and the presence of sulfate esters and groups in cellulose nitrate fibers create sources of potential deterioration in the final product. Sulfate esters can hydrolyze to sulfuric acid.
2.4 RINSING, DRYING, KNEADING
After the cellulose nitrate fibers were nitrated to the desired percent nitrogen, the acids were drained away and the mass of cellulose nitrate was “quenched” or rinsed with water. This step, introduced commercially in 1865, was considered to stabilize the cellulose nitrate by removing the bulk of the free acids from the mass. Different rinsing procedures abounded, but most involved washing the cellulose nitrate in water at elevated temperatures and/or pressures (Worden 1911, 2:595–96). It was believed that much of the instability of cellulose nitrate was due to free sulfuric and nitric acids trapped in the amorphous regions of the cellulose fibers when the mass of cellulose nitrate was rinsed in water. These trapped free acids could provide a source of deterioration in celluloid.
After rinsing, the cellulose nitrate was dried, usually with heat or alcohol, until the water content was less than 2% (Worden 1911, 2:599–605). At this point the cellulose nitrate was kneaded in a machine much like a commercial bread kneader (Worden 1911, 2:606–609). During the kneading, a 50% solution of camphor in alcohol was added to the cellulose nitrate (Miles 1955, 207). The camphor-alcohol solution changes the order or macro-structure of the cellulose nitrate fibers. The molecules are forced apart and eventually lose any regular relationship with other molecules. This reaction is much like the denaturation of proteins by hot water. After the camphor-alcohol is mixed with cellulose nitrate fibers the resultant celluloid plastic has no fibrous orientation of molecules and is called a gel, or as Miles (1955, 206) describes it, after gelation there is “no trace of solid structure” in the celluloid. The reaction is not well understood, but it is known that a homogenous gel will form with one molecule of camphor for each glucose unit (Petitpas and Mathieu 1946, 525). The molecules are not chemically “bound” to each other; this allows for the sublimation and migration of camphor out of and through celluloid.
Kneading produces a doughy mass, to which any colorants, fillers, or other ingredients needed in the final celluloid are added. These additives all affect the stability of celluloid. Certain fillers such as TiO2 (Worden 1911, 2:624) are known to reduce the effects of photodegradation of plastics, while others seem to increase the rate of deterioration (Sirkis 1982). The additives kneaded into the celluloid in this step introduce sources of potential deterioration.
2.5 SEASONING, CRYSTALLITE FORMATION
When the mixing was complete the mass of celluloid was pressed into blocks of various sizes (Miles 1955, 207). The pressure used to prepare the blocks, and pressure applied later during fabrication, forced the cellulose nitrate molecules together. In areas, the intermolecular camphor molecules were compressed and “squeezed out,” leaving cellulose nitrate molecules again in intimate contact with each other. At sites where this occurs crystallites are formed. These local sites of crystal formation form the centers of crystallization in aging celluloid. The blocks were “aged” in drying sheds for varying amounts of time. This “seasoning” step was required because the celluloid went through dimensional changes as a result of the evaporation of alcohol and other volatile constituents (Miles 1955, 207). Therefore, to avoid warping, splitting, and shrinking of the finished pieces it was necessary to allow the blocks to season for up to several weeks prior to fabrication. Seasoning times varied greatly from batch to batch and from manufacturer to manufacturer (Worden 1911, 2:611–17). Many objects probably were fabricated before their parent blocks had “aged” sufficiently. Objects made from inadequately seasoned celluloid will have stresses, strains, and dimensional problems creating another source of potential deterioration.
2.6 FABRICATION
The fabrication of celluloid objects was a complex process. Celluloid was machined like wood (sawed, drilled, carved, and planed) and was formed with heat and pressure and blow molded. The technique of blow molding was developed for use with celluloid. (The first blow molded objects were small celluloid dolls later known as Kewpie Dolls [DuBois 1972, 44–45].)
Elaborate procedures were implemented to create detailed and highly accurate imitations that are deceptively difficult to differentiate from the natural materials. For example, the intricate pattern of lines characteristic of ivory and called the lines of Retzius were imitated fairly accurately. Thin sheets of celluloid were prepared in two colors, one opaque and the other more transparent. The opaque ivory-colored sheets were layered between more transparent sheets of the same color. A block was created out of these alternating layers with heat and pressure. This block was then sliced and the thin slices pressed into another block. The second block, when fabricated, created an accurate imitation of ivory (Worden 1911, 2:683–87). Even at a magnification of 12x structures of celluloid ivory may be indistinguishable from those of real ivory.
Another similar example is the imitation of horn. Cones of celluloid were cut from blocks of varying opacity and color. These cones were stacked and pressed into a block (Worden 1911, 2:687–89). When the solid block was machined in a certain manner, accurate striations and laminae were visible. At 12x magnification, imitation horn may be indistinguishable from horn. The details of an object's fabrication can cause deterioration problems. Combs were often made by laminating two layers of celluloid together. The layers were often different colors and opacities and hence different compositions of celluloid. The expansion and/or contraction of the different layers may cause the warping or splitting off of a layer. Auxiliary materials added in the fabrication of objects such as metal fittings and decorative elements create complex interactions during decomposition.
2.7 SOURCES OF INHERENT DETERIORATION
In summary, the synthesis and fabrication of celluloid objects introduces many potential problems for celluloid as it ages. These inherent problems include:
- regular deterioration of cellulose molecules; chemical deterioration produced when processing cellulose; range in quality of cellulose used
- range in quality of acids, alcohols, and water used
- impure camphor, other compounds mixed with camphor
- combination of quality and quantity of additives
- reversibility of nitration reaction and corrosive power of deterioration products
- inhomogeneities of cellulose nitrate fibers
- presence of sulfate esters
- trapped “free” acids
- freedom of movement of camphor
- crystallite formation—pressure
- seasoning
- fabrication technique
3 DEGRADATION
3.1 INTRODUCTION
ONCE A celluloid object has been fabricated, it becomes subject to the chemical, physical, and biological forces of its environment. The visual appearance of deteriorated celluloid varies. Celluloid that has been protected from undesirable environmental conditions will deteriorate according to the mechanisms inherent in its own structure. The cellulose nitrate molecules continue to crystallize around the loci created by the pressures used in manufacture. Camphor molecules are squeezed out, often to the surface where they will sublime at room temperature. This sequence of events leaves celluloid very brittle, cracked, shrunken, warped, collapsed, crumbling, discolored, and crystallized. Celluloid that has been exposed to undesirable environmental conditions is apt to be even more discolored, warped, swollen, softened, mushy, and coated with droplets or a film of nitrate salts and their acids.
When celluloid objects are fabricated with other materials such as metals, glass, textiles, and paper the problems of degradation are compounded. The deterioration products of celluloid are often corrosive (nitric acid) and react readily with other materials in proximity.
As mentioned, celluloid's inherent degradation or aging process involves the recrystallization of cellulose nitrate molecules and the expulsion and sublimation of camphor. Environmental conditions generally alter this process by enhancing degradation of the cellulose nitrate molecules. Degradation through thermal, chemical, photochemical, and physical means generally leads to lower viscosities and softer rather than more brittle celluloid. Conservators must find the balance between these two processes if celluloid objects are to be preserved.
3.2 FORCES OF DEGRADATION
Celluloid deteriorates as a result of four degradation processes: thermal, chemical, photochemical, and physical.
3.2.1 Thermal Degradation
Thermal degradation of celluloid involves the breaking off of nitrate groups in the cellulose nitrate molecule. As a result, nitrous gases are evolved. The following reaction equation shows the probable mechanism whereby the weak -O-NO2 bonds are broken, leaving NO2 gas, aldehydes, and alcohols.
Fig. .
 |
Selwitz indicates that nitrogen-oxygen bond cleavage takes place at temperatures above 100�C and when the molecule is exposed to visible and long-wave ultraviolet light (Selwitz 1988, 25).
3.2.2 Chemical Degradation
Chemical degradation can result from acid or alkaline hydrolysis. Acid hydrolysis involves the fission of glucosidic links in the cellulose nitrate molecule. With cellulose nitrate, this reaction is very slow and results in the reduction of the average molecular chain length of the cellulose nitrate molecule (Miles 1955, 268). Acids may be present as a result of synthesis, manufacture, or environmental conditions.
Chemical breakdown of the cellulose nitrate molecule by alkalis is more rapid than that by acids—often called denitration—the following reactions show the results of alkaline degradation (after Miles 1955, 286).
Fig. .
 |
Alkalis may also be present from synthesis, manufacture, and environment.
Alkaline hydrolysis produces a wide variety of low molecular weight oxidized compounds. Inorganic nitrates, ammonia, cyanides, carbon dioxide, oxalic acid, maleic acid, glycolic acid, and malonic acid have all been recorded as deterioration products (Miles 1955, 278). Basic pigments added to cellulose nitrate lacquers were found to increase the rate of deterioration through nitrate loss in accelerated aging (Hercules 1955, 44–48). Acids may have been added to mixtures to neutralize alkaline pigments such as bone black, oil black, and nigrosine (Hercules 1955, 44–48).
Aside from acid and alkaline hydrolysis, some metallic oxides are known to cause irreversible gelation of cellulose nitrate in solution (Chao 1934, 99–102). Lacquers, glues, and badly deteriorated celluloid can be irreversibly gelled by oxides of lead, calcium, arsenic, tin, iron, copper, and zinc (in order of decreasing effect). Many lacquers contain tartaric, citric, or maleic acid as a gel inhibitor. Early tubes for cellulose nitrate adhesives were made of lead, which gelled the adhesive so that it would not set. This discovery led to the knowledge that certain metallic oxides could gel cellulose nitrate (Miles 1955, 291–92).
Selwitz points out that due to its structure the cellulose nitrate molecule is highly polar. This “extraordinarily high nonionic polarity” is also a contributing factor to the high instability of celluloid plastics (Selwitz 1988, 2).
3.2.3 Photochemical Deterioration
Photochemical deterioration is relatively severe in celluloid due to the ability of the molecule to absorb strongly in certain wavelength ranges. The far ultraviolet is readily absorbed by celluloid. The maximum and complete absorbance occurs at around 2536 cm−1 (Miles 1955, 287). Different wavelengths of light have been found to deteriorate celluloid by reducing the viscosity and/or chain length of the molecules (Miles 1955, 291). The results of strong absorption can be seen as yellowing, embrittlement, and softening. One interesting breakdown mechanism apparently involves the disintegration of the nitrated glucoside ring structure by exposure to far-ultraviolet radiation (Selwitz 1988, 25).
3.2.4 Physical Degradation
Physical degradation of celluloid can be caused by thermal, chemical, and photochemical deterioration, loss of volatile constituents like camphor, and external physical stresses from fabrication or housings. Many objects appear to collapse on themselves as a result of the entrapment of harmful deterioration products in their interiors. The trapped gases accelerate deterioration in the immediate area and essentially consume the inside of the objects (Sirkis 1982).
The thermal, chemical, photochemical, and physical breakdown of celluloid constitutes a set of highly interrelated decomposition reactions and mechanisms. Light, alkalis, acids, and certain metallic oxides can be very detrimental. The primary environmental contributor to celluloid degradation, however, appears to be moisture. Water is required for most of the aforementioned reactions. Water also has the potential to create physical stresses due to the isotropic nature of celluloid and its capacity for water absorption. Worden discusses a close relationship between nitrate content and absorption of water by cellulose nitrate (Worden 1911, 2:974). As the nitrate content drops (i.e., in degradation) cellulose nitrate can absorb more moisture from the atmosphere, increasing the rate of many water-dependent reactions (also see Miles 1955, 158–59) (Hercules, 1955, 36). This characteristic indicates that celluloid plastics may be more sensitive to moisture than are other more highly nitrated cellulose nitrate materials.
4 CELLULOID IN THE COLLECTION
4.1 IDENTIFICATION
THE FIRST step in dealing with celluloid objects in a museum setting is identification. This is rarely possible by visual or tactile means; chemical or analytic identification is necessary. This section deals with the identifying properties and characteristics of celluloid.
4.1.1 General Characteristics
Celluloid is a rigid thermoplastic made by compression or blow molding, casting, or machining. It softens in moderate heat. When gently rubbed with a soft cloth, celluloid will give off the odor of camphor. It burns rapidly and continually with a yellow flame when ignited. It may explode or give off the odor of camphor while burning (Saunders 1966, 18).
Celluloid contains nitrogen that can be detected by a variety of techniques (Saunders 1966, 21). The presence of nitrogen can be an indicator of celluloid, but it can also indicate other nitrogen-containing polymers. However, the presence of nitrogen can be used to distinguish celluloid from other cellulosic derivatives.
4.1.2 Optical Characteristics
Cellulose has an optically biaxial and positive unit cell and is highly birefringent. When nitrated the fibers become less birefringent and the optical activity changes from biaxial positive to uniaxial to biaxial negative with increasing nitrogen content. The refractive index of cellulose nitrate is lower than that of cellulose and drops even lower with increasing nitrogen content. The range is from 1.49 to 1.51 (Miles 1955, 210–11). Isolation of cellulose nitrate from celluloid for optical identification is problematic in that when cellulose nitrate is gelled by camphor it loses its original structure and, hence, many of its original optical characteristics.
As noted earlier, under low magnification celluloid can be indistinguishable from natural materials.
4.1.3 Solubility
Celluloid is soluble in two types of solvents. The first type includes acetone, other ketones, and alkyl acetates. These solvents do not cause any change in the crystalline structure of the cellulose nitrate molecule. The second type of solvent—methyl nitrate, alkyl nitrate, and water—does change the crystalline structure of cellulose nitrate molecules (Petitpas and Mathieu 1946, 525).
The solubility of celluloid is complex in that it is a two-component system—camphor and gelled cellulose nitrate (table 5). Some solvents, such as ethanol, primarily affect the camphor portion while others affect both portions (acetone) and some affect only the cellulose nitrate (water). The solubilities of celluloid can differentiate it from natural materials. For example, celluloid is soluble in acetone while ivory is not. The method used by the author to differentiate celluloid from ivory involves taking a very small scraping from the object with a small scalpel blade under low magnification. The sample, visible under microscope, is left on the edge of the scalpel blade and a single drop of acetone is placed on the sample. Ivory flecks do not dissolve and are swirled around in the currents of the acetone drop. These flecks appear to sparkle as they reflect light. Celluloid dissolves instantly, leaving an apparently pure drop of acetone.
TABLE 5 Solubility of Celluloid
4.1.4 Stains
Celluloid can also be identified by several stain reactions. These reactions can be affected by the presence of certain common chemicals, so it is best to use as many different identification techniques as possible (table 6).
TABLE 6 Stain Reactions for Identification
4.1.5 Infrared Spectroscopy
One definitive test for celluloid and cellulose nitrate is its characteristic infrared spectrum. Samples prepared in KBr pellets or as a thin film will provide a clear-cut set of peaks. Figure 3 shows a generalized spectra of aged celluloid and camphor. Table 7 lists the wavenumbers of cellulose nitrate.
Fig. 3A.
Infrared spectrum of aged celluloid
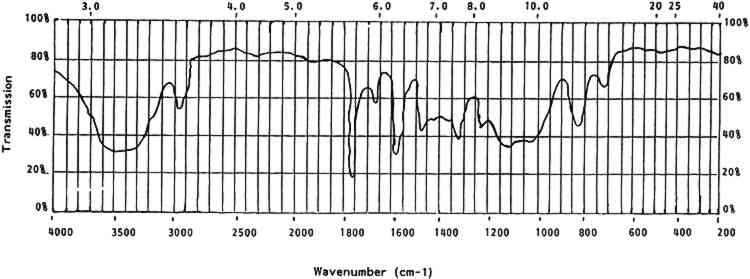 |
Fig. 3B.
Infrared spectrum of camphor
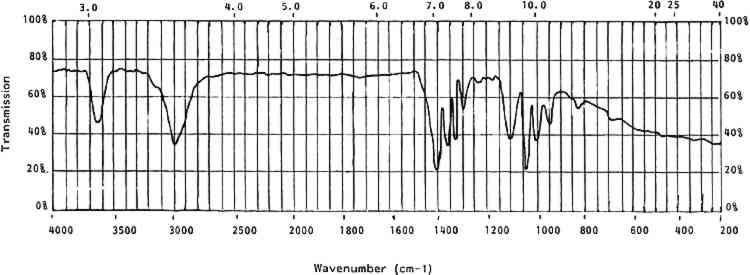 |
TABLE 7 Cellulose Nitrate Infrared Spectrum
All solubility, stain, and infrared tests given here have been tested by the author unless otherwise noted. Techniques that require unusual equipment, great exactitude, or a significant amount of time have not been included.
4.2 ISOLATION AND DOCUMENTATION
Once an object has been identified as celluloid, it should be isolated from other materials so that its deleterious breakdown products will not harm other objects. After isolation, a condition report is essential. This documentation will sometimes be the only source of information to use in monitoring the condition of the objects over time. It is interesting to note that celluloid is often an unsuspected part of a collection until its effects on neighboring objects or materials are noticed. Certain measures that may slow inherent or environmental deterioration can be implemented only after celluloid objects are segregated.
4.3 CLEANING AND TREATMENT
After examining the objects and recording their condition, note any film or droplets on their surfaces. These are generally acidic deterioration products and should be removed, as they will accelerate degradation of the celluloid. Little experimentation has been conducted to date on cleaning methods for celluloid. The deterioration products are usually readily soluble in water. However, water should be used sparingly as deteriorated celluloid can be water-soluble. Cleaning with a barely dampened swab can be effective but can also be abrasive. If water is used it should be removed immediately with a dry swab.
Many celluloid objects have adhesive residues on them from pressure-sensitive tapes and glues. These adhesives have often combined chemically with the celluloid and can only be removed mechanically. Mechanical cleaning is very dangerous on celluloid because the object surface is often softer than the adhesive accretion. It is advisable to remove foreign accretions from celluloid, as they may accelerate local degradation, but only if extreme care and skill can be applied. After any deterioration products or accretions have been removed, the object should be rehoused. Repairing, mending, consolidating, or any cosmetic treatments should be avoided until more is known about the reaction of celluloid to conservation materials and supplies. As stated earlier, alkaline materials can cause irreversible chemical and structural damage to celluloid. As a result, any experimentation using alkaline-neutralizing steps must be cautiously pursued and investigated with every available analytic tool. After documentation and cleaning, celluloid should be housed carefully.
4.4 STORAGE, EXHIBIT ENVIRONMENT
The instability of celluloid is both inherent and environmental. If the environment of a celluloid object, in storage or on exhibit, is adequately controlled, deterioration may be slowed but never entirely halted. The chemical and physical characteristics of celluloid deterioration indicate that an ideal environment for celluloid objects would include:
- low relative humidity to slow degradation due to denitration and hydrolysis, slow acid formation, and reduce dimensional changes
- low temperature to slow the rate of deterioration, crystallization, and denitration
- continual air exchange to help carry away gaseous autocatalytic deterioration products
- no other cellulosic materials in proximity. Tissues, boxes, etc., will deteriorate rapidly, in proximity to celluloid, add to the risk of a fire, and complicate ongoing degradation
- acid-resistant cases and cabinets to protect against rusting
- devices that exclude or at least filter ultraviolet and other radiation such as Plexiglas UF 3
- nonmetallic object containers (boxes, trays) made of glass, ceramic, or acid-resistant plastic. Metallic containers corrode and may lead to gelation of the celluloid.
- protection from contact with the metallic oxides and salts of lead, calcium, arsenic, tin, iron, copper, and zinc. For example, if deteriorated celluloid becomes dissolved in moisture absorbed from the atmosphere or in liquid deterioration products, the metallic oxides of calcium in calcium-buffered materials can irreversibly gel the softened or dissolved celluloid.
- an acid-absorbing material in the storage or exhibit space to react with the acids formed during deterioration (CaCO3 is one possibility if it is not in contact with the celluloid)
- separate storage to prevent damage to other materials by the degradation products of the celluloid
5 CONCLUSION
THERE IS very little concrete and practical information available on the treatment and storage of celluloid. Research into its compatibility with other resins and compounds would allow more specific treatment recommendations, and experimentation with storage materials and containers would allow more specific housing suggestions. An examination of environmental control techniques for cases and storage units may provide ideas for maximum protection of celluloid objects from inherent and environmental degradation.
Celluloid is a material from which new information and techniques will grow. As the myriad synthetic polymers around us age and gain historical and even ethnographic (if not archaeological) value, conservators will be increasingly faced with a new class of materials that require treatment and care. If conservators are to be prepared to face the treatment, housing, and exhibition needs of plastics, they must begin research and experimentation now. For many celluloid objects it is already too late.
ACKNOWLEDGEMENTS
THE AUTHOR would like to acknowledge the professional commitment and concern of the Conservation and Physical Sciences staff at the National Museum of American History, Smithsonian Institution, whose funding and continued support made it possible for the preparation of this paper. Personal thanks are due to Scott Odell, Martin Burke, and Patricia Mercado for their involvement in this project.
APPENDIX
1 APPENDIX
Miscellaneous Properties of Celluloid
REFERENCES
Brady, G. S., and H. R.Clauser. 1977. Materials handbook, 11th ed.New York: McGraw-Hill.
Chao, H.1934. The reduction of the viscosity of nitro-cellulose solutions by ammonia. Ph.D. diss., Ohio State University, no. 4236.
Clark, D. T.1981. The modification, degradation, & synthesis of polymer surfaces studied by ESCA. American Chemical Society Series162:247–91.
DuBois, J. H.1972. Plastics history U.S.A.Boston: Cahners Publication Co., Inc.
Encyclopedia Americana. International edition. Danbury, Cann: Grolier1982.
Encyclopedia of chemical technology, 3d ed.1982. New York: John Wiley and Sons. 22:709–62.
Friedel, R.1977. Men, materials, and ideas: A history of celluloid. Ph.D. diss., Johns Hopkins University.
Hercules Powder Co. 1955. Nitrocellulose. Wilmington, Del: Hercules Powder Co.
Kaufman, M.1963. The first century of plastics. London, England: Crown Press.
Lundberg, R.1983. Personal communication.
Miles, F. D.1955. Cellulose nitrate. London: Oliver and Boyd.
Petitpas, T. and Mathieu, M.1946. The reactions occurring in the gelatinization of the nitrocelluloses. Transactions of the Faraday Society42B(17):525.
Saunders, K. J.1966. The identification of plastics and rubbers. New York: Barnes and Noble.
Saunders, K.J., 1973. Organic polymer chemistry. London, England: Chapman and Hall.
Selwitz, C. M.1988. Cellulose nitrate in conservation. Marina del Rey, Calif.: J. Paul Getty Trust.
Sirkis, L.1982. The history, deterioration and conservation of cellulose nitrate and other early plastic objects. Masters Thesis. Institute of Archaeology, University of London.
Worden. 1911. Nitrocellulose industry. Vols. 1 and 2. New York: Van Nostrand.
FURTHER READING
Anderson, B. W.1971. Gem testing, 8th ed.London: Butterworths. 324.
Bernadou, J. B.1901. Smokeless powder, nitrocellulose and theory of the cellulose molecule. New York: J. Wiley and Sons.
Bikales, N. M., and L.Segal. 1971. Cellulose and cellulose derivatives. Part 5. New York: Wiley Interscience.
Blaker, R., R.Badger, and R.Noyes. 1947. Molecular properties of nitrocellulose II: Studies of molecular heterogeny. Journal of Physical and Colloidal Chemistry51(2): 574–79.
Celanese Celluloid Corp.1942. Cellulose plastics in war and industry. Celanese Celluloid Corp. Publication. New York
Darwualia, E. H., S. M.Moonim, and J. C.Arthur. 1971. Photooxidation of chemically modified celluloses and free radical formation. Textile Research Journal42:592–95.
DeCroes, G. C., and J. W.Tamblyn. 1952. Protection of cellulose esters against breakdown by heat and light. Modern Plastics29:127–89.
DeCroes, G. C., and J. W.Tamblyn. 1953. Stabilization of cellulose esters. National Bureau of Standards, circ. no. 525. 171–90.
Desai, R. L., and J. A.Shields. 1969. A new surface effect in photodegradation of cellulose. Journal of Colloid and Interface Science31(4):585.
DuBois, J. H.1942. Plastics. Chicago: American Technological Society Publication. 63–84.
Gordon, R. W.1957. Dielectric relocation of cellulose nitrate and cellulose. Ph.D. diss., McGill University.
Haslam, J., H. A.Willis, and D.C.M.Squirrel. 1981. Identification and analysis of plastics, 2d ed.London: John Wiley and Sons.
Hercules Powder Co. 1939. Nitrocellulose. Wilmington, Del.: Hercules Powder Co.
Husbands, V., J.Cloonan, and G.Keen. 1968. The examination of toys for celluloid, Journal of the Association of Public Analysts6(3):85–88.
ICCROM. 1963. Synthetic materials used in the conservation of cultural property. Rome: International Center for the Study of the Preservation and Restoration of Cultural Property. 29.
Ito, K.1971. Mechanics of upper and lower yield points of amorphous polymer solids. Transaction of the Society of Rheology15(3):389–413.
Jilk, L.1938. The effect of light on cellulose nitrate I. Ph.D. diss., University of Minnesota.
Johnson, M.1976. Nitrocellulose as a conservation hazard. AIC preprints, 4th Annual Meeting, American Institute for Conservation, Washington, D.C.66–75.
Jortner, J.1959. Photochemistry of cellulose acetate. Journal of Polymer Science37:199–214.
Kagarise, R. E., and Weinberger, L. A.Infrared spectra of plastics and resins. NRL Report 4369.
Kelly, R. R.1969. Wood types 1828–1900. New York: Van Nostrand.
Kenyon, W. O.1935. A study of alkaline decomposition of cellulose nitrate. Ph.D. diss., University of Rochester.
Kline, G. M.1962. High polymers, Vol 12. Analytical chemistry of polymers, part III. New York: Interscience.
Koob, S. P.1982. The instability of cellulose nitrate adhesives. The Conservator (6):31–34.
Lewin, J. B.1968. In Film-forming compounds, part 3, vol. 1, ed.R.Myers and J.Long. New York: Marcel Dekker, Inc., 108–51.
Masselon, Roberts, and Cillard. 1912. Celluloid: Its manufacture, applications, and substitutes. Trans. H. H.Hodgson. London: Charles Griffin and Co. Ltd.
Mustafa, A., and A. F.Dawoud. 1966. Stabilization of starch and cellulose nitrates. Explosivstoffe14(11): 241–47.
Neff, S. B., and R. J.Haughwout. 1969. Cellulosics. Plastics World27(8).
Patrick, R. L.1969. Adhesion and adhesives. Vol. 2: Materials. New York: Marcel Dekker, Inc.471–75.
Roff, W. J., J. R.Scott, and J.Pacitti. 1971. Fibres, films, plastics, and rubbers. London: Butterworths. 159–63.
Rosenberger, H. M., and C. J.Shoemaker. 1959. Infrared determination of nitrocellulose in mixtures of cellulose resins. Analytical Chemistry (31):1315.
Rothstein, E. C.1968. Evaluating UV absorbers: Clear coatings. Paint and Varnish Products58(2): 39–43.
Sarker, N., and G. D.Rose. 1971. Comments on the degradation of aqueous solutions of methycellulose. Journal of Paint Technology43(558):69–72.
Sax, N. I.1979. Dangerous properties of industrial materials, 5th ed.New York: Van Nostrand Reinhold. 475.
Schick, P. E.1943. A study of the mechanics of film formation in the spray-coating of paper with nitrocellulose lacquers. Ph.D. diss., Institute of Paper Chemistry, Appleton, Wisc.
Scrutton, R. F.1969. Vibration and fractures in machining plastics. Society of Plastic, England, Annual Technical Conference Journal25(7):52–54.
Simonds, H. R.1939. Industrial plastics. New York: Pitman Publication Corp. 1–53.
Simonds, H. R., and C.Ellis. 1943. Handbook of plastics. New York: Van Nostrand. 160–73, 173–76, 231.
Tichenor, R. L.1946. The photochemical decomposition of cellulose acetate-butyrate. Journal of Polymer Science1:217.
Urbanski, T.1968. Some remarks to pulping and stabilization of nitrocellulose. Explosivstoffe16(9):217.
Winding, C. C., and R. L.Hasche. 1974. Plastics. New York: McGraw-Hill. 97–105.
Winslow, F. H., and W. L.Hawkins. 1967. Some weathering characteristics of plastics. Modern Plastics44(8):141–42.
AUTHOR INFORMATION
JULIE A. REILLY received a B.A. in anthropology from Towson State University and an M.A. in anthropology from the George Washington University where she studied applied sciences and instrumental analysis and completed a series of graduate conservation courses. She completed internships and worked as a contract conservator at the National Museum of American History, Smithsonian Institution. She worked as archaeological conservator for the National Park Service and as objects conservator for the Colonial Willamsburg Foundation. She is currently working as objects conservator for the H. F. duPont Winterthur Museum and as adjunct professor in the University of Delaware/Winterthur Art Conservation Program. Address: Conservation Division, Winterthur Museum, Winterthur, Delaware 19735.
Section Index |