A FRESH FACE FOR SAMUEL GOMPERS: METHYL CELLULOSE POULTICE CLEANING
Lisa A. Goldberg
2 CASE STUDY
2.1 Condition
A MARBLE BUST OF SAMUEL GOMPERS was brought from the National Portrait Gallery to the Conservation Analytical Laboratory in 1986 for cleaning.4 Carved by Moses Dykars in 1924, the bust exhibited highly polished, roughly cut and acid etched surfaces (Figure 1). The bust had been stationed in the National Portrait Gallery near the entrance to the cafeteria, at a height which encouraged visitor handling. The head appeared to be covered with a thick layer of grime and grease which gave the sculpture a yellowed appearance. Prominent areas on the face and lapels were covered with a thicker layer of grime which ranged from grey to dark brown in color.
Fig. 1.
Portrait bust of Samuel Gompers, before treatment.
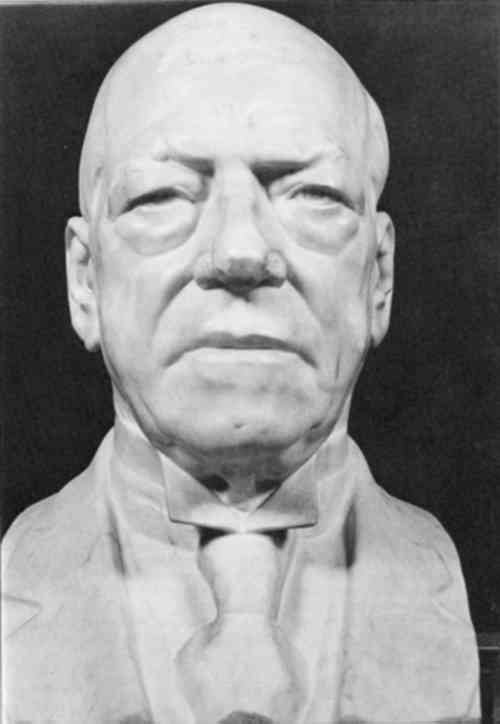 |
In initial cleaning tests, the surface grime was easily removed with saliva dampened swabs, followed by separate swab applications of acetone, ethanol, benzine and tricloroethylene. However, test cleaning of a larger area on the proper left side of the head resulted in a partially cleaned surface with a mottled appearance.
2.2 Experimental
Poultice cleaning was chosen in an attempt to achieve an evenly clean surface. Initial tests with attapulgite and fumed silica packs in water, stoddard solvent and a mixture of acetone, alcohol and water yielded unsatisfactory results because they did not completely remove the surface grime and both left residual powder on the surface.
Methyl cellulose was tested as a medium because it is a non-ionic, inert material which forms a thick gel that can easily be peeled away when dry.5 The initial test poultice of 7% methyl cellulose, 6,000 centipoise viscosity, (Archivart� brand) with 0.3% ammonium hydroxide removed surface dirt as well as small granules of the marble substrate from two pin head sized areas (0.1-0.3 mm) on the proper left shoulder of the bust when the film was peeled away. This area had not appeared abraded before treatment, but surface crystals may have been poorly adhered to the substrate. Alternatively, the poultice may have adhered too strongly to the marble surface, causing damage as it dried. Examinations of segments of the film by scanning electron microscope at 845X magnification revealed several clusters of rhombohedral crystals as well as a negative impressions of other crystals on the marble surface (Figure 2). Examination of one crystal with energy dispersive x-rays yielded high percentages of calcium and silica, supporting its identity as calcite. A portion of the film examined under polarized light at 250X magnification revealed similar, birefringent clusters of crystals embedded in the poultice film.
Fig. 2.
Scanning Electron Micrograph of the Archivart� Methyl Cellulose Poultice, at 845X magnification.
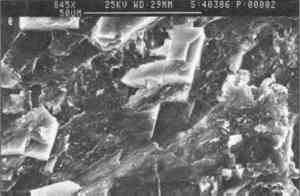 |
In an attempt to prevent the film from pulling crystals from the object, the methyl cellulose was modified by adding various bulking agents to reduce shrinkage in drying. Attapulgite, talc and hydrophilic fumed silica were all mixed into test poultice solutions in 1% concentration by weight. When the resultant films were examined at 250X magnification under polarized light, all three revealed clusters of small, birefringent crystals. Fumed silica proved to be the most successful additive because the gel remained translucent and the dry film left no residue on the marble surface.
Plasticizers were then added to the various solutions in an attempt to reduce the adhesive characteristics of the film as it dried. Glycerol and propylene glycol were effective in reducing the number of birefringent crystals evident at 250X magnification in the test poultice films which were allowed to dry before removal from the marble surface. In low percentages, these plasticizers seemed to remain in the methyl cellulose layer, leaving no observable residue on the surface.6 X-ray fluorescence results showed that propylene glycol was a more appropriate plasticizer because less was needed to produce a film with the desired characteristics.7
Dow Chemical Company suggested that a plasticized mixture of a methyl cellulose of lower molecular weight, as represented by a lower centipoise number would produce a more flexible, less adherent film in drying.8 Test films of methyl cellulose 400 (Dow Chemical Methocel A4C�, Premium grade), mixed with propylene glycol and fumed silica were effective in cleaning the surface without removing birefringent crystals when peeled away from both smoothly polished and roughly cut surfaces.
2.3 Treatment
The entire object was cleaned by applying a poultice of 7% Methocel A4C� in deionized water (weight/volume), with additions of 0.3% ammonium hydroxide and variable quantities of propylene glycol and fumed silica. The ammonium hydroxide was added to buffer the aqueous solution up to a pH of approximately 9 to prevent leaching calcium from the stone and to help in dirt removal.9
The poultice medium was mixed in accordance with directions which were provided by the supplier, Dow Chemical Company.10 The methyl cellulose powder (7% by weight) was dispersed in a pre-measured mixture of water and ammonium hydroxide (by volume) which was continually warmed and magnetically stirred on a hot plate to an approximate temperature of 70–80�C.11 After all of the methyl cellulose had flocculated into tiny particles, the cloudy solution was cooled in a refrigerator for approximately one hour. At this lower temperature, the dispersed particles of methyl cellulose dissolved and swelled into a clear, smooth gel. The solutions were mixed in quantities of 300 to 400 ml per jar and approximately four to six jars were needed to coat the sculpture entirely. Occasionally, lumpy solutions resulted from not enough heat, quick addition of the powder or lack of stirring in the cooling phase. Slightly yellowed solutions may have resulted from too much heat or use of a wooden tongue depressor in stirring the mixture. The propylene glycol and fumed silica were added to the mixture immediately before the poultice application. Each jar of methyl cellulose was emptied into a large container and enough propylene glycol was added to give the mixture an elastic consistancy. Although the amount of propylene glycol was not pre-measured, percentages ranged from 3.2% to 5.5%, depending on the desired elasticity. The fumed silica was added in a similar manner, until the mixture appeared stiff enough for application; quantities ranged in percentage from 0.25% to 2%. The variation in amounts of additives neccessary to change the consistency of the solution may be temperature dependent.12 As the solvated polymer reaches its thermal gelation temperature it becomes a stiffer, less elastic paste. Less viscous solutions, which required less fumed silica, may simply have been a result of a cooler gel application.
The white, somewhat elastic mixtures were then applied over the entire stone surface and were allowed to dry at ambient room temperature and 42–44% relative humidity (Figure 3). Three applications of approximately 1/4″ to 1″ wet-thickness were applied over the course of a week. The thickness was variable because the gel tended to sag, leaving prominent surfaces with a thinner film than deeply cut areas. The thickness of the gel was adjusted by redistributing the poultice material while wet. Each poultice required approximately 48 hours to dry to a flexible film. After each poultice had dried, it was sprayed with a mist of deionized water to swell the film and facilitate its removal. The film was then gently and easily peeled back from the surface in large sections (see Figure 4). After the first treatment, the stone appeared cleaner, but areas which were heavily soiled were still quite grey, especially the nose, lapel edges and mouth. The second poultice revealed a cleaner surface with slightly brownish areas on the right side of the head and shoulders. The third application diminished the intensity of these discolorations (see Figure 4).
Fig. 3.
Portrait Bust of Samuel Gompers, Covered with the modified metyl cellulose poultice, during treatment.
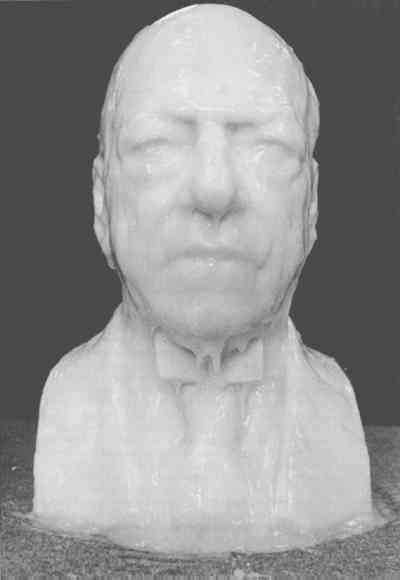 |
Fig. 4.
Three dry poultice films, (treatment remnants).
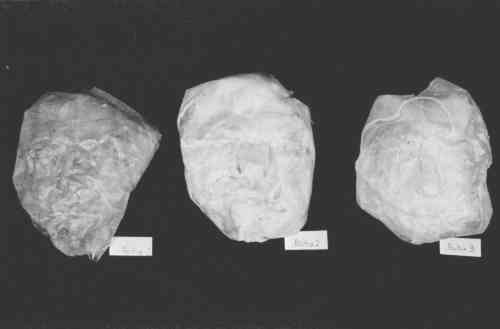 |
The source of the brownish stains is unclear. In the initial cleaning tests, the top of the head appeared to have a brownish tinge. After poultice cleaning, small deposits of a waxy material were noted in the corners of the eyes and ears and these were removed with petroleum benzine. Solvent packs were applied to small sections of brownish areas on the head in hopes that this staining might be a remnant of an older coating material; but these poultices had no effect on the intensity or hue of the discoloration. Other possible sources for this discoloration include natural variation in the marble, iron inclusions or microbial activity.13
|