TREATMENT OF A SILVER DRAGON FOR THE REMOVAL OF SILVER CYANIDE AND CHALCONATRONITE
Donna K. Strahan
ABSTRACT—Analysis of the corrosion products on a silver dragon suspected to have been treated with cyanide revealed both silver cyanide and chalconatronite. It appears that both of these corrosion products can be formed on silver objects cleaned or replated using a cyanide solution. These corrosion products darken with exposure to light; therefore, they may be mistaken for silver sulfide. In order to determine how to remove the highly poisonous cyanide corrosion product, numerous tests were run. Using a carefully timed procedure the silver cyanide was removed with an aqueous solution of 20% sodium thiosulfate. The chalconatronite was removed mechanically.
1 INTRODUCTION
CORROSION FOUND ON a silver Japanese dragon was brought to the attention of the conservators at the Walters Art Gallery because of its unusual bright blue corrosion deposits. Upon examination, a gray corrosion product which turned black with time was also found in association with the blue corrosion. Samples of both corrosion products were analysed. The blue product was identified by X-ray diffraction as chalconatronite (Na2Cu(CO3)2.3H2O). The black material was identified by X-ray diffraction as silver cyanide (AgCN),1 and the author has previously reported its occurrence in a preliminary article.2 A spot test for silver cyanide is found in Feigl but has not been tried by the author (see Appendix). This paper will discuss the rarity and formation of chalconatronite on a silver object and the tests and methods used to remove the silver cyanide corrosion.
2 DESCRIPTION AND EXAMINATION OF THE SILVER DRAGON
THE MEIJI PERIOD (late 19th century) dragon was made of silver with the remains of gilding on its claws and tongue. X-radiography of the dragon showed it was cast in five separate sections and was soldered together to form its serpent-like shape. Composition of the surface metal was determined by x-ray fluorescence to be 6% copper and 94% silver, a composition similar to sterling silver.3 A coating over the object's surface was identified by infrared spectrophotometric analysis to be an acrylic resin.
The blue and the gray corrosion products were found scattered over the body with the main conglomerations at the intersection of the spikes on the back and along the legs. Both corrosion products occurred in close proximity, and there was less blue corrosion than gray corrosion. The blue corrosion was generally fluffy; however, in some areas it was compact and appeared visibly crystalline.
Both corrosion products proved to be light sensitive. The blue corrosion color faded after two months exposure to the laboratory environment. After roughly a month in the laboratory, the gray corrosion had converted to a charcoal black color.
3 COMMERCIAL SILVER CYANIDE CLEANING
A CURATOR RECALLED that the dragon had been sent to a commercial silver company for cleaning during the early 1960's. The silver company to which the dragon was sent is no longer in existence, and their method of cleaning silver is not known. Since the mid-19th century, immersion in a cyanide bath has been a common method for removing silver tarnish, as well as for plating silver. The existence of cyanide corrosion on the surface of the dragon leads to the belief that it was cleaned by the above method. A probable scenario is that the cyanide solution entered the hollow sections of the body through minute gaps in joints or flaws in the casting. Some of the solution may have remained on the surface of the interior due to poor rinsing and then slowly migrated to the exterior surface, attacking the silver and forming cyanide salts. The interior has probably been corroded in a similar manner, but there is currently no means to confirm this without damaging the object.
There are numerous old recipes for cleaning silver which call for the use of a potassium or sodium cyanide solution. For example, Dick's recipe4 calls for 1 gallon of water, 4 ounces of potassium cyanide, 1 pound of hyposulphite of soda (sodium thiosulfate), 8 ounces of muriate of ammonium (ammonium chloride) and 4 ounces of liquid ammonia (ammonium hydroxide). In 1892 Hiorns discussed removing silver sulphide with a five percent solution of potassium cyanide.5 Modern formulations differ very little from earlier baths. They include potassium cyanide, sodium cyanide and sodium carbonate.6
Cleaning in a modern commercial silver shop is often begun by degreasing the object in a potash or lye solution and rinsing it in water. If copper corrosion is present on a silver alloy, commercial shops often remove it with sulphuric acid or hydrochloric acid before dipping the object into a cyanide solution. It is dipped into a ten percent cyanide solution, followed by a water rinse. Cyanide salts deposited from immersion in the bath are removed with a scratch brush, a fine brass wire brush described as soft as human hair. The object is then polished with a lye compound and rouge.7
Fig. 1.
Japanese silver dragon.
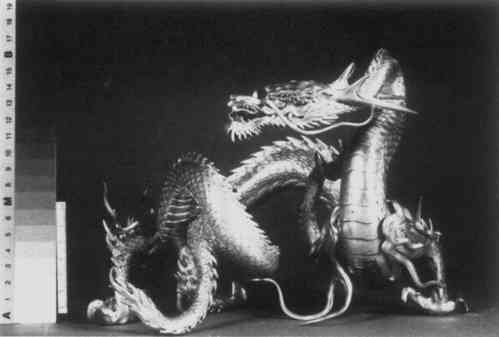 |
4 HAZARDS OF CYANIDE CLEANING
USING SILVER OBJECTS cleaned or replated in a cyanide bath can be a hazard because of the presence of cyanide salts trapped in a spout, handle, grill, a soldered join or the intricate pattern of a design. Hollow handles which have been slush cast may be thin in some areas and contain tiny holes which could allow the handles to fill up with cyanide solution during the electroplating or cleaning process. In addition, intentional vent holes in two-piece soldered silver alloy sections are potential areas for the entrapment of silver cyanide. Trapped residues could seep out slowly over time.
Cyanide reacts with the silver, producing silver cyanide (AgCN), an extremely poisonous grayish-white odorless powder which darkens when exposed to light. Although it is not readily absorbed through the skin, it is deadly by inhalation or ingestion. Acids readily react with it to break down the complexed metal salt, producing highly poisonous hydrogen cyanide gas which has the characteristic odor of bitter almonds. Cyanide is one of the fastest acting of all known poisons and both the TLV (Threshold Limit Value) and the OSHA PEL (Permissible Exposure Limit) are 5 mg/m3 over an eight hour time period.8 Acids may be present in silver cleaning solutions, such as silver dips and others, or in foods.
5 CHALCONATRONITE
BLUE CHALCONATRONITE, a hydrated sodium copper carbonate, has previously been reported by Gettens and Frondel9 and by Horie and Vint.10 Its initial discovery by Gettens and Frondel on an Egyptian bronze led to the conjecture that its presence was due to the dry alkaline burial condition of the object. Gettens and Frondel gave detailed crystallographic properties and x-ray powder diffraction patterns. Horie and Vint then reported that chalconatronite was also produced on corroded bronzes which had been treated with sodium sesquicarbonate. The recent analytical results of the silver dragon indicate chalconatronite is more common than anticipated and may be caused by other treatments.
While the occurrence of cyanide salts on the dragon could be explained by the cyanide bath, the explanation of the occurrence of chalconatronite and its close proximity to the silver cyanide is less clear. There are several possible explanations. The sodium present in the chalconatronite may have come from the cyanide cleaning solution as an added component or from a degraded bath while the object was immersed. Normally sodium and potassium cyanide are continually added to cleaning or plating solutions to keep them saturated with these substances. If they are not replenished, the cyanide slowly oxidizes to a cyanate which hydrolyzes to a carbonate and ammonia is evolved.11 This could produce carbonate ions and ammonia in the bath available to attack the copper component of the silver alloy, although the small amount of ammonia evolved from hydrolysis of the cyanide solution is not likely to have contributed to the corrosion products. Another source for the sodium aside from the sodium cyanide solution may have been an alkaline rinse used after the cyanide bath, such as NaOH or Na2CO3. The carbonate in the chalconatronite may have developed from the absorption of carbon dioxide from the atmosphere by the highly alkaline solution. It is also possible that the carbonate developed from the deterioration of the cyanide solution, or, further, it may have come from an alkaline rinse.
The copper in the chalconatronite may have come either from a contaminated bath or from the alloy itself. If the copper was derived from the alloy, then this would explain why the two corrosions occurred together rather than scattered separately over the object's surface. The areas which had been corroded by the cyanide were more porous or pitted in comparison to the rest of the metal. Dr. F. Christopher Tahk has suggested that due to the oxidation potentials of both copper and silver, the cyanide would readily attack both metals simultaneously, probably faster than the carbonate. The observed separation of the corrosion products may then have occurred through the usual segregation processes of repeated recrystallization with relative humidity fluctuations.12
Tests were run to determine whether sodium carbonate would react with the small percentage of copper present in sterling silver. A solution of 14% sodium carbonate was placed on a sterling silver blank in a humid atmosphere and removed after twenty-four hours. Blue crystals were produced and confirmed as chalconatronite by x-ray diffraction analysis.13 Considering chalconatronite can be formed on sterling silver over a long period of time, it is unlikely that it would form during a brief rinse such as the dragon may have undergone. However, it may have had time to form from the solution which was left behind on the interior after the treatment was completed. Although it would be interesting to observe cyanide attack a sterling silver blank, tests were not conducted because of the inherent dangers of handling the test solutions.
In summary, chalconatronite seems to be most likely formed by cyanide trapped within the dragon's body slowly seeping out and reacting with the silver alloy. All of the constituents necessary to form both corrosion products were present, and through recrystallization both cyanide and carbonate compounds products could be found adjacent to one another.
Fig. 2.
Black silver cyanide corrosion is visible on the tail and surrounding the manufacturer's plates between the dragon's front legs.
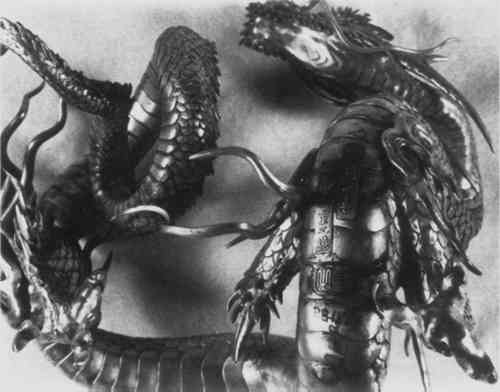 |
6 TREATMENT OF THE SILVER DRAGON
THE PURPOSE OF THE TREATMENT was to remove both the silver cyanide and the chalconatronite corrosion products. The two corrosion products were removed in separate stages. The treatment was begun by removing the old coating with organic solvents. Some of the silver cyanide was removed at this time but some of it remained undisturbed. Tests were therefore run to find a chemical means of removing the corrosion without damaging the silver.
Fig. 3.
Chalconatronite (large fluffy blue product) and silver cyanide (smaller black spotty product) present on a tail spine (16X).
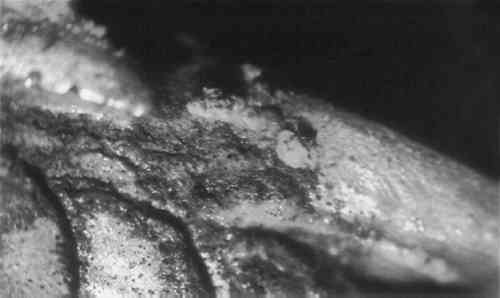 |
Fig. 4.
Laboratory grown chalconatronite on a sterling silver blank (30X).
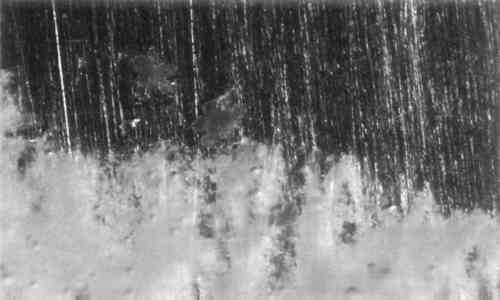 |
Silver cyanide is readily soluble in ammonium hydroxide (NH4OH), sodium thiosulfate (Na2S2O3), potassium ferricyanide (K3Fe(CN)6) and other alkaline cyanide solutions.14 All of these reagents are capable of harming the sterling silver alloy. Copper is attacked by ammonium hydroxide, and silver by sodium thiosulfate and the alkaline cyanide solutions. Tests were carried out to determine which product would be effective yet damage the alloy the least by varying the concentration and time of contact.
A sterling silver blank (7.5% copper) was prepared for metallographic analysis and etched with a mixture of 5 ml concentrated ammonium hydroxide, 10 ml hydrogen peroxide (3%) and 10 ml distilled water, to determine its structure before the test solutions were applied. In this manner the structure of the blank was known and any dissolution by the test solutions could be monitored. The blank was repeatedly polished down roughly half a millimeter and swabbed with test solutions for a specific period of time to discover what reactions, if any, had occurred. High concentrations of all these reagents harmed the alloy. Those solutions which had caused minimal damage were chosen to test the solubility of silver cyanide (see Table). Due to the limited amount of silver cyanide available for testing on the dragon, the accuracy of the tests can not be assured, but from the test results the least damaging and fastest acting solution was selected: aqueous 20% sodium thiosulfate.
Table Tests for the Removal of Silver Cyanide
Originally, the masking of uncorroded silver areas on the dragon with a resin was planned to prevent the possibility of etching. However, in the limited time available for the treatment no satisfactory coating material was found. Extreme care was taken to keep the cleaning reagent away from the uncorroded surface. The dragon was treated locally, not allowing the sodium thiosulfate solution to remain on the surface for more than 30 to 45 seconds. No etching of the surrounding uncorroded metal surface was visible under low magnification, and all of the silver cyanide was removed. It is noteworthy that the underlying metal was found to have been etched during the corrosion process.
The sodium thiosulfate solution did not appear to affect the chalconatronite. Where this corrosion product was disfiguring and accessible, it was removed mechanically. Slight pitting in the surface became visible when the corrosion was removed.
After thorough rinsing with distilled water and drying, the object was coated with 10% Acryloid B-72 solution, dissolved in 50% methyl ethyl ketone, 40% toluene, 10% diacetone alcohol. The coating was sequentially brushed and sprayed on the object.
Fig. 5.
Japanese silver dragon after treatment.
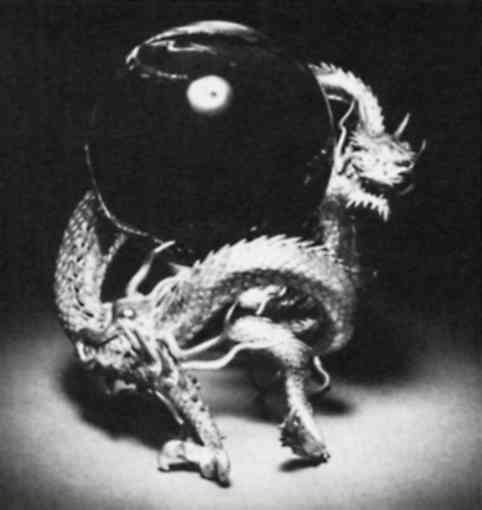 |
7 CONCLUSION
BOTH SILVER CYANIDE and chalconatronite may be more common on museum objects than previously thought. They may not be readily apparent since their colors alter upon exposure to light so that they may be confused with more common less toxic products. For example, the darkening of silver cyanide can look like silver sulfide corrosion. It is imperative to remove silver cyanide because of its poisonous nature. No method is known to the author for removing silver cyanide corrosion without liberating hydrogen cyanide gas and/or causing at least microscopic etching to sterling silver. An aqueous 20% solution of sodium thiosulfate was chosen as a method which did not create hydrogen cyanide gas. Etching was kept at a minimum by careful timing and observation of the procedure which had been worked out beforehand on expendable blanks. All treatments to remove silver cyanide should be carried out in a fume hood. Any by-products should be disposed of properly after determining the current appropriate disposal method.15
ACKNOWLEDGEMENTS
THE AUTHOR WISHES TO THANK Ms. Terry D. Weisser for her support and advice while this treatment was carried out at the Walters Art Gallery. This work was partially carried out while on a National Museum Act grant and the author wishes to thank NMA for the opportunity. Much appreciation goes to the reviewers Mr. Andrew Linns, Philadelphia Museum of Art, Dr. F. Christopher Tahk, Art Conservation Department, Cooperstown, and Ms. Terry D. Weisser, Walters Art Gallery for their time and thoughts. In addition, thanks are expressed to the editors of the paper; Carol Grissom, Susan West, Ann Boulton, and Mary Garbin from the Conservation Analytical Lab, Smithsonian Institution.
APPENDIX
1 APPENDIX
1.1 SPOT TEST FOR SILVER CYANIDE THROUGH CONVERSION INTO SILVER CHROMATE16
“The conversion of silver cyanide into silver chromate provides a sensitive and specific test for AgCN because other water-insoluble, acid-resistant silver salts such as AgCl, AgBr, AgI, AgSCN, AgIO3, etc. do not react.
Procedure: A small amount of the finely divided sample is placed on a piece of filter paper or in a depression of a spot plate and spotted with a drop or two of the reagent. The formation of a red-brown color (silver chromate) indicates the presence of silver cyanide.
Reagent: MercuryII nitrate (or acetate)-potassium chromate solution. Several ml of a 5% aqueous solution of mercuric nitrate or acetate are made acidic with dilute acetic acid and 2 g of sodium acetate are added, followed by several drops of a potassium chromate solution. Should a slight precipitate appear, it can be removed by filtering or centrifuging. The clear yellow reagent is stable.
The conversion of AgCN to AgCrO4 by means of the reagent also occurs in solutions containing complex [Ag(CN)2]− ions.
Fig. .
 |
An excess of alkali cyanide causes no interference because CN−ions are removed by the formation of mercuric cyanide
Fig. .
 |
The above procedure can be used for the detection of silver cyanide in ammoniacal solution. However, preliminary evaporation to dryness is an essential first step.”
NOTES
1. X-ray diffraction analyses were performed by Paul Jett of the Technical Laboratory of the Freer Gallery of Art and also by Martha Goodway of the Conservation Analytical Laboratory, Smithsonian Institution.
2. Strahan, p. 63.
3. X-ray fluorescence and infrared spectrophotometric analyses were performed by the Martin Marietta Corporation of Baltimore, Maryland.
4. Dick, p. 297.
5. Hiorns, p. 85.
6. Kirk-Othmer, p.64.
7. Personal communication with Don Heller, Conservation Department, Winterthur Museum, Winterthur, Delaware.
8. Committee on Hazardous Substances in the Laboratory, p. 147.
9. Gettens and Frondel, p. 64.
10. Horie and Vint, p. 185.
11. Untracht, p. 686.
12. Correspondence with Dr. F. Christopher Tahk, Director, Art Conservation Department, State University College at Buffalo, Cooperstown, New York.
13. X-ray diffraction analysis was performed by the author with the guidance of Joan Mishara of the Conservation Analytical Laboratory, Smithsonian Institution.
14. Curtman, p. 377.
15. Committee on Hazardous Substances in the Laboratory, p. 46.
16. This appendix is taken verbatim from Feigl, pp. 352–353.
BIBLIOGRAPHY
Baekeland, Frederick. Imperial Japan: The Art of the Meiji Era (1868–1912), Cornell University, New York, 1980.
Committee on Hazardous Substances in the Laboratory. Prudent Practices for Handling Hazardous Chemicals in Laboratories, National Academy Press, Washington, D.C., 1981.
Curtman, Louis J.Qualitative Chemical Analysis, The Macmillan Company, New York, 1938.
Dick, William B.Dick's Encyclopedia of Practical Receipts and Processes or How They Did it in the 1870's, Funk & Wagnalls, New York.
Feigl, Fritz and Anger, Vinzenz. Spot Tests in Inorganic Analysis, Elsevier Publishing Company, New York, 1972.
Gettens, Rutherford J., and Frondel, Clifford. Chalcontronite: An Alteration Product on Some Ancient Egyptian Bronzes. Studies in Conservation, 2,21955, pp. 64–74.
Hiorns, Arthur H.Metal-Colouring and Bronzing, Macmillan and Co., New York, 1892.
Horie, C. V., Vint, J. A.Chalconatronite: A By-Product of Conservation? Studies in Conservation, 27, 1982, pp. 185–186.
Hughes, Richard and Rowe, Michael. The Colouring, Bronzing and Patination of Metals, Crafts Council, London, 1982.
Kirk, Raymond E. and Othmer, Donald F.Encyclopedia of Chemical Technology, 8, John Wiley and Sons, New York, 1979.
Oguchi, Hachiro. Experimental Studies on Japanese Traditional Coloring Copper. Bulletin of the Faculty of Fine Arts Tokyo University of Arts, 8, Tokyo, 1972.
Oguchi, Hachiro. Japanese Shakudo: Its History, Properties and Production from Gold-Containing Alloys. Gold Bulletin, 16, 4, 1983, pp. 125–132.
Roberts-Austen, W. Chandler. Cantor Lectures: Alloys. Journal of the Society of Arts, November 20, 1893, PP. 1022–1030.
Savage, E. and Smith, C. S.The Techniques of the Japanese Tsuba Maker. Ars Orientalis11, 1979, pp. 291–328
Strahan, Donna K.A Cautionary Note on the Presence of Silver Cyanide on Museum Objects. Journal of the American Institute for Conservation23, 1983, pp. 63–64.
Untracht, Oppi. Jewelry Concepts and Technology, Doubleday and Co., New York, 1982.
Section Index |