CONSOLIDATION OF DETERIORATED WOOD WITH SOLUBLE RESINS
Y. Wang, & A.P. Schniewind
6 RESULTS AND DISCUSSION
THE TESTS OF SPECIMENS SUBJECTED to normal air drying will be discussed first, followed by a discussion of the effect of very slow drying. For the sake of convenience, every individual treatment is given a code as shown in Table 1. The first two numbers denote the resins, the first one or two characters following the resin code indicate the solvent, and the last character designates the concentration level. Slow drying (for 12.5% concentration only) is distinguished from normal air-drying by addition of the letter S to the code (not shown in Table 1).
Table I Coding of Treatments
6.1 Strength, Stiffness and Retention
Values of modulus of rupture (MOR) and modulus of elasticity (MOE) of treated and untreated bacterially degraded wood are shown in Table 2. There seems to be no clearly evident pattern among the strength values for treated and untreated specimens. However, the modulus of elasticity and modulus of rupture appeared to be strongly related to original wood density. Linear regression analysis (analysis of the relationship between two variables) showed them to be closely correlated, with coefficients of determination, r2, of 0.796 and 0.722 for strength and stiffness, respectively (r2 can vary from 0 to 1; an r2 of 0.8 means that 80% of the variation in one variable is explained by variation in the other variable). Therefore, the effect of density had to be eliminated in order to establish the true treatment effects (Snedecor and Cochran, 1980). Accordingly, an analysis of covariance was made taking original wood density as the covariate (an analysis of covariance examines the effect of known factors, such as treatments, on one variable—here strength or stiffness—while adjusting for the effects of another variable—here density). Adjusted values of MOR and MOE are listed in Table 3.
Table II MOR and MOE as tested, original wood density, weight retention and viscosity of resin solutions
Table III MOR and MOE Values Adjusted for Density
Table 3 shows that generally, within a resin and solvent combination, MOR and MOE increase in the order of increasing concentration, but there are exceptions where ethanol is the solvent. Among the treatments, 98ET.H, i.e., 20% Butvar B98 dissolved in ethanol/toluene, has the highest adjusted values of both MOE and MOR.
The weight retention of consolidant is proportional to concentration as shown in Table 2. Assuming the specimen has been completely saturated with resin solution, it is possible to calculate an estimated maximum resin retention from the original wood density (which determines void space) and the resin concentration. Estimated maximum retention values are shown in Table 4. Since the relationship between concentration and weight retention is similar for all treatment groups, only one polymer and solvent combination was examined. From Table 4, it is observed that the estimated maximum retention was less than the actual retention for each concentration. Volume increases were considered as a possible reason, but there was every reason to believe that the sample material was more like that of Barclay (1981) where expansion was too small to have a significant effect on retention, than the severely degraded material treated by Payton (1984) where linear expansion of the order of 5% had been observed. A more likely explanation is that concentration increased during treatment (which would also tend to increase actual retention), although every effort was made to keep this effect to a minimum.
Table IV Comparison Between Estimated Maximum Retention and Actual Retention
According to Siau (1971), volume retention of fluid in wood is related to pressure differential and the reciprocal of viscosity each to the power of 0.5 on a theoretical (cf. Equ. 1) or of 0.42 on an empirical basis for undegraded wood. However, in this study, viscosity did not appear to play a role in volume retention. Viscosity values of the resin solutions are listed in Table 2, and at the highest concentration, viscosity increased considerably. The 20% solution of Butvar B90 in ethanol, for example, was almost unworkable, but the specimens still appeared to reach complete saturation. This is probably due to the small size of the specimens, the fact that the wood is sapwood, the use of vacuum rather than external pressure, and possibly increased permeability of deteriorated wood. For instance, Ellwood and Ecklund (1959) observed that the sapwood of pine logs deteriorated by bacteria had greatly increased permeability in extreme cases because of destruction of the ray tissue. Also, solvents such as ethanol may be able to remove extractives from pit membranes and thus increase the permeability of specimens. Equ. 1 is therefore not applicable to the specimens of this study because it requires volumetric retention to be less than maximum.
6.2 Rule of Mixtures in Consolidation
Siau et al. (1968) proposed a geometrical model to predict improvements in strength and stiffness of wood-plastic composites by using the rule of mixtures. It is also possible to apply the rule of mixtures to wood-consolidant composites by assuming the consolidant is deposited in the cell lumens. Thus, the amount of structural material will increase without an increase in total volume.
The rule of mixtures for wood and consolidant can be expressed by the following equation which is a modified version of an equation given by Siau (Wang, 1984):
Fig. .
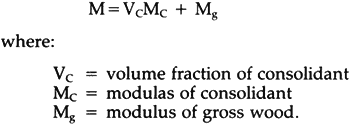 |
where:
Vc = volume fraction of consolidant Mc= modulas of consolidant Mg= modulus of gross wood.
Mechanical properties of Butvar B98 and Butvar B90 are listed in Table 5. The lower bounds of MOE of Butvar B98 and B90 were chosen to predict the stiffness of wood-consolidant composites. The average values of the lower and higher bounds of tensile strength of Butvar B98 and Butvar B90 were selected for the modulus of rupture; they are 6,100 psi and 6,200 psi, respectively. The predicted values of modulus of elasticity and modulus of rupture were then obtained from Equ. 2 and are listed in Table 6.
Table V Some Physical Properties of the Consolidants
Table VI Comparison Between Estimated and Adjusted MOR and MOE Values
Since no published information on the mechanical properties of Acryloid B72 was available, efforts were made to obtain the mechanical properties from cast film of Acryloid B72. The film as cast from solution was very soft and flexible, in contrast to the rigid pellets of Acryloid B72 as supplied. Films cast from either a toluene or an acetone solution lost about 3% in weight and became noticeably stiffer after heating in a vacuum oven at 45�C for twenty hours, and film heated at 100�C for two hours became hard and brittle. Thus, it may be concluded that solvent trapped in Acryloid B72 film acts as plasticizer. The same phenomenon is expected to take place in the wood-consolidant composite. This can be expected to limit the effectiveness of Acryloid B72 as a consolidant,∗ and no predicted values can therefore be shown for it in Table 6.
∗Additional experiments are planned to investigate the effect of longer drying times (1 year or more).
Table 6 indicates that all values of estimated MOR and MOE ascend with increasing concentration, without exception. However, it is noted that most ratios of estimated modulus to actual modulus are smaller than 1.00. This means that the predicted values tend to be too low, and that the rule of mixtures may not be sufficiently accurate for wood-plastic composites in bending. Plasticization of the resin by solvent retention cannot be a factor, as this would tend to have the opposite effect on reducing actual as compared to estimated values.
It is also noted that the few ratios of estimated to actual modulus greater than 1.00 are mostly for low concentration treatments. The ratios generally decrease with increasing concentration levels, as shown at the bottom of Table 6. There appears to be no ready explanation for this observation.
6.3 Interpretetation of Statistical Analyses
Analyses of covariance of all treatment data with normal air drying, taking original wood density as covariate, showed that treatment and pile∗ as main effects and their interaction are all significant at the 5% level for both MOE and MOR.
∗Since each pile originates from a different tree, and wood properties can be expected to vary from tree to tree, pile was included as a factor in the analysis.
The fact that pile was found to have a significant effect shows that there are factors other than density. Probably the difference is due to differing degrees of deterioration, since losses in strength are not always well correlated with weight loss and hence density.
Although treatment has a significant effect, this does not mean that each individual treatment is significantly different from the control group. Comparisons between individual treatments and the control group are listed in Table 7. There were more treatments that had a significant effect on MOR than on MOE. Although improvements in strength and stiffness depend on the mechanical properties of the consolidants used, strength would be more sensitive than stiffness to such improvements. This is because strength is controlled by local flaws or weak spots which are amenable to repair by the consolidant, while stiffness depends more on the quality of the entire specimen volume.
Table VII Probability Values for the Hypothesis: Control Mean = Treatment Mean, for Each Treatment Using Means Adjusted for Density
With respect to strength, all treatments with Butvar resulted in significant increases at medium and high concentrations, and in some cases even at low concentration. Acryloid B72, on the other hand, is significant for only one treatment (72A.H.). This is probably due to the plastization already discussed. The highest value of MOR is for treatment 98ET.H.
In order to examine the effect of concentration, drying rate, type of solvent, and molecular weight of Butvar, a set of four separate analyses of covariance was made. Two of these were 4-way analyses for Butvar, with molecular weight, solvent, pile, and either concentration or drying rate as the main effects, while the other two were 3-way analyses for Acryloid, with solvent, pile, and either concentration or drying rate as main effects.
Pile was a significant factor in each analysis conforming to the larger analysis of covariance already discussed. Concentration was a significant factor for both Butvar and Acryloid, as might be expected since there are substantial increases in retention when the concentration is increased (Table 2), with accompanying increases in bending strength in almost all cases (Table 3).
Detailed comparisons of the data in Table 3 show that both MOR and MOE are generally larger for B98 than B90-treated specimens. This difference was found to be statistically significant in the analysis where drying rate was one of the variables, but was not significant when concentration was the variable. Thus there is some evidence that B98 is more effective, probably owing to its lower molecular weight, allowing it to penetrate into smaller spaces, but the evidence is not very strong.
Examining the effect of type of solvent, the data in Table 3 show that generally the use of polar solvent (ethanol for Butvar and acetone for Acryloid) results in larger MOR and MOE values than the use of non-polar solvents (ethanol/toluene mixture for Butvar and toluene for Acryloid), although the highest strength values for a single treatment included a non-polar solvent. On the average, the polar solvent gave higher strength values in every case; but this difference was sometimes significant and sometimes not, so that here also the evidence is not very strong.
A comparison of MOR and MOE values for normal air drying and very slow drying is shown in Table 8. Since the data in this table are also adjusted data, but cover a different population of specimens, they cannot be compared with data for otherwise identical treatments in Table 3. With some exceptions, the values for slow drying are lower than those for normal air drying. In part this appears to be due to generally lower retention in the specimens dried slowly. The statistical analysis showed that the faster drying rate resulted in significantly higher values of both MOR and MOE for Butvar, while there were no statistically significant effects of drying rate in the case of Acryloid.
Table VIII Weight Retention, Retention, MOR and MOE for Two Drying Rates
Differences in drying rate might lead to two different phenomena. If there is a liquid flow, fast drying might lead to migration of solution to the surface resulting in enhanced retention of resin in the surface layers. Payton (1984) believed this to be an important factor. On the other hand, if there is no liquid flow, slow drying might lead to migration of resin into the specimen interior by diffusion. This would take place if partial evaporation from the surface layers leads to an increase in resin concentration, setting up a concentration gradient and subsequent diffusion of resin into the interior. All specimens were blotted after treatment, and in no case was there noticeable gloss on the surface after drying, which can taken as evidence that there was no significant migration of resin to the surface. On the other hand, the lower strength values associated with slow drying could be explained by an inward migration of resin, since it is less effective in the interior than at the surface in improving bending strength. In any case, the data indicate that in terms of improving strength properties, very slow drying has no advantages and may be detrimental.
6.4 Factors Affecting Retention
All specimens in this study seemed to have reached complete saturation during vacuum impregnation even at high concentration and its accompanying high solution viscosity. Thus, higher concentration solutions will deposit more resin and therefore impart more strength. However, for practical applications in which large objects or woods with low permeability are to be consolidated, full penetration is not easily obtained. In those cases, absorption could be increased by either increasing the pressure differential by application of positive pressure after the vacuum treatment (which would require more elaborate equipment), or by reducing the viscosity of the treating solution. The latter can be achieved either by reducing concentration, which is to some extent counterproductive since it reduces the retention in those parts that have been penetrated even though the total retention may be higher, or by choosing solvents which impart lower viscosity to the solution. Viscosity could also be lowered by heating, possibly at the expense of undesirable side effects. The choice of solvent or of concentration thus becomes one that cannot be made on absolute terms, but must be tailored to the particular requirements and conditions of the object to be treated.
|