LEAF CASTING ON THE SUCTION TABLE
Robert Futernick
5 ALTERATION OF THE VACUUM TABLE DESIGN
RECENTLY we constructed a small portable vacuum table that especially lends itself to leaf casting and pulp filling procedures. It is made entirely of clear plastic, so that when it is placed on a light table, light is transmitted up through the top of the suction box. Permeability of a small part of the upper surface was achieved by drilling many tiny holes in the Plexiglas. Marjorie Cohn suggested at the Milwaukee meeting that a fritted glass plate might be set in the top surface to allow transmission of light without the need for drilling. A full size transparent suction table would be most desirable. Recently, T. K. McKlintoc proposed the use of etched syntered polyethylene as a surface. This translucent porous material, supported by plastic lighting difuser, would result in a device that could serve both leaf casting and conventional suction table needs alike. An illustration of a possible design is shown below (figure 6).
Fig. 6.
A light-transmitting suction table for pulp casting or treatment of a small area.
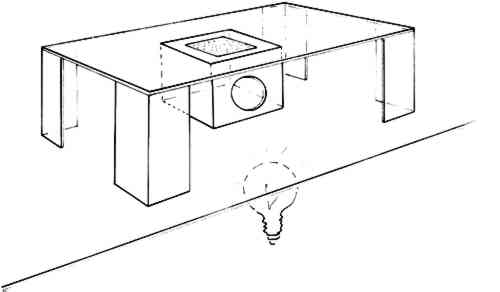 |
5.1 Working features of a transmitting suction table
- A light suction table is extremely versatile. It can serve for leaf casting as just described, conventional pulp filling, and for very precise and selective addition and deposition of pulp.
- For conventional pulp filling, suction is applied but temporarily blocked by placement of a sheet of thin plastic film over the opening of the table. When proper pulp density and distribution is achieved, the “table cloth” (plastic film) is yanked and the liquid quickly falls, leaving the fibers in place.
- For certain shaped holes or art that cannot tolerate much wetting, a transmitting table is extremely useful. A dirty edge or a small loss, tear or paper thinning is set on Reemay over the suction area with the vacuum on. Pulp, suspended in very dilute concentration, is dripped onto the damaged area with a wide-tipped medicine dropper. Air flow takes the pulp to the open area and causes adhesion to the edge of the top or to the previously dripped application. It is possible to build up multiple layers until the desired result is achieved without much lateral wetting. It is necessary to send distinct droplets. Attempting pulp application from close range will result in fiber clumping.
|