THE EFFECT OF AN ALKALINE RINSE ON THE AGING OF CELLULOSIC TEXTILES, PARTS I AND II
Ira Block
2 PART II: STRENGTH RETENTION AND COLOR CHANGE
2.1 INTRODUCTION
IN PART I, it was reported that a treatment in dilute calcium hydroxide solution could increase the resistance of cellulosic textiles to degradation by heating at 150�C, an accelerated aging test that should predict the results of natural aging. It was found that the logarithm of the percent strength retained (Y) could be related to the logarithm of the baking time (T) by an equation of the form: Y = A + n�T. The slopes of the lines for specimens which remained untreated or were subject to treatment for each of the respective fibers were essentially the same, and it was concluded that the treatment is effective irrespective of the source of the cellulose. In addition, it appeared that the chemistry of the degradation process was independent of the source of the cellulose.
This part presents the results of a more detailed study of the effect of a Ca(OH)2 rinse on the strength retention and color change of new cellulosic fabrics subjected to accelerated aging.
2.2 EXPERIMENTAL
2.2.1 Color Measurement
The color change of the test samples was monitored by measuring the color of fabric samples with a Hunterlab Model D25D2 Color/Difference Meter. A glossy black support was used to insure that the background color for all measurements was the same. The details of reagent application, aging and tear testing were provided in Part I.
2.3 RESULTS
2.3.1 Strength Retention
The results of this study of the strength retention of artificially aged cotton and spun rayon fabric are shown in Figs. 2 and 3, respectively. If first-order kinetics apply, the rate of decrease in strength retention should be proportional to the strength retained, and a plot of the log(strength retained) vs time would be linear. In both cases, it is seen that such an assumption is valid for less than forty hours baking time at 150�C
Fig. 2.
Strength Retained vs. Baking Time at 150�C for Cotton Cloth.
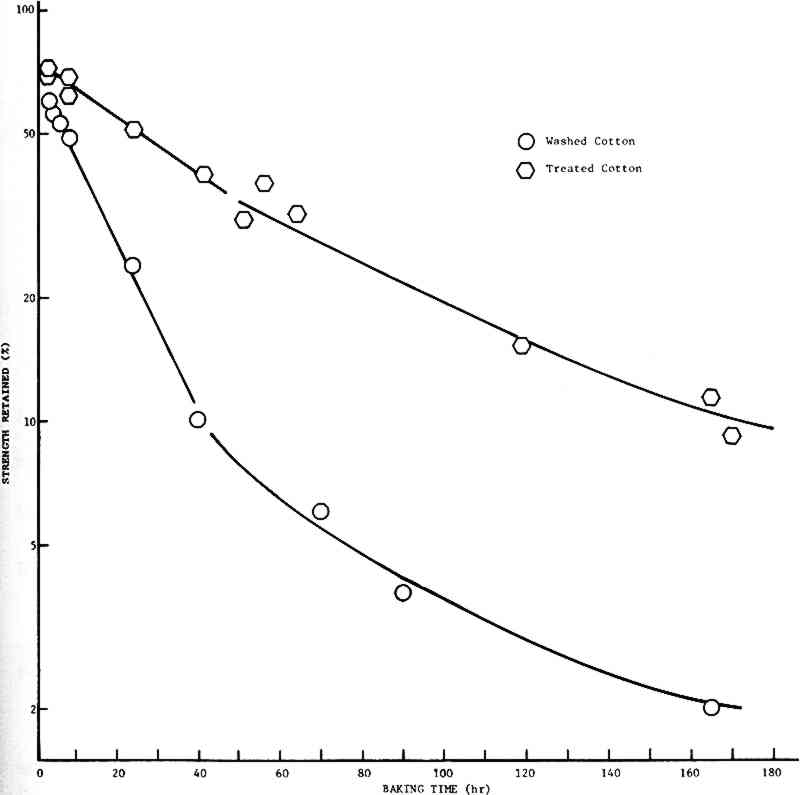 |
Fig. 3.
Strength Retained vs. Baking Time at 150�C for Rayon Cloth.
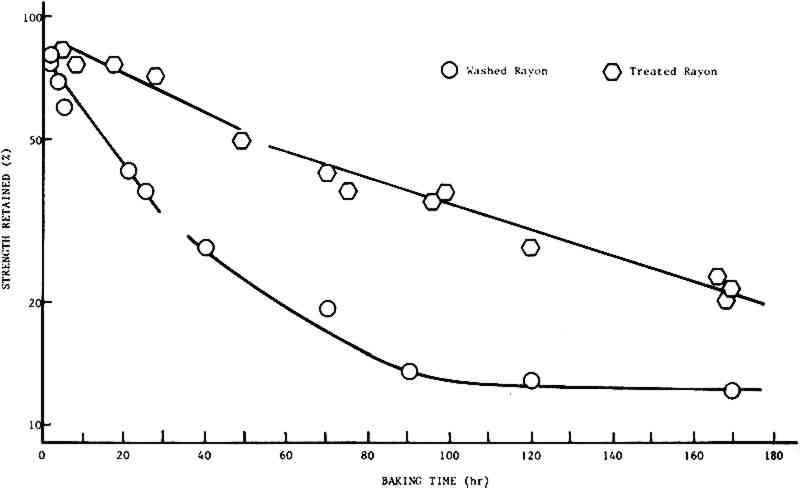 |
Beyond forty hours the curves for the untreated material exhibit definite concavity. The treated material, however, continues to follow first-order (or psuedo first-order) kinetics to about 120 hr. The rate of strength loss for the treated materials, as measured by the initial slopes of the lines, are found to be about one-half that of the untreated materials. For cotton, the untreated fabric degrades at a rate of about 1.8%/hr, while the treated cloth degrades at a rate of only 0.9%/hr. The untreated rayon cloth loses strength at the rate of about 1.7%/hr, while the treated cloth degrades at only about 0.7%/hr. In addition, the decay rates are essentially the same for both cotton and rayon.
It should be noted that, since the parameter being measured is a physical property that is only indirectly related to the chemistry of the cellulose polymer making up the fibers, the more curves depart from linearity, the less meaningful comparisons between them become. Thus, comparisons of the rates of decay of treated and untreated cloths for times greater than forty hours should be limited to the observation that the treated fabrics degrade at a lesser rate than the untreated fabrics. However, it is of interest to note that the decay rates for both the treated cotton and treated rayon cloths are almost identical (about 0.2%/hr). This is in keeping with the observation in Part I that the rates of decay appear to be independent of the source of the cellulose.
Finally, it may be seen that there is a very rapid strength loss occurring in the first hour or so of baking. This phenomenon is not unexpected, since the fabrics contain some moisture when placed in the oven, and it has been demonstrated in Part I (and see refs. 25, 27, 29, 36–38, 40) that moisture accelerates the rate of degradation.
2.3.2 Color Change
The assumption that the change in color of the fabrics would be affected only by some chemical species in the cellulose and oxygen allows us to write:
Fig. .
 |
where E is the color, [O] the concentration of oxygen at the surface of the fabric, and [C] the concentration of the cellulose moiety that causes the color change.
If [C] remains constant, then (because [O] is constant), we may write
Fig. .
 |
where Et is the color at time ‘t’, and Eo is the original color. The change in color should be linear with time. It was found, however, that the rate of color change did not remain linear with time, but decreased as the fabric became darker. This phenomenon comes about because the color meter cannot detect small differences between large color changes. In order to avoid this problem, we may define the following parameter:
Fig. .
 |
where Ef = the color at infinitely long baking times, Et = the color at time ‘t’, and Eo = the original color. Ef was determined by measuring the color of samples baked for over 400 hr. The value of F is ‘1’ if there is no color change, and ‘0’ when the maximum has been reached. Thus, a plot of (1 – F) vs time should be linear.
Figure 4 shows the plots of (1 – F) vs time for treated and untreated cotton and rayon. Of major interest is the fact that there is no apparent difference in the rate of color change for treated and untreated cloth. That the yellowing and darkening of cellulosic material is not affected by an alkaline treatment indicates that the species which cause the change in color are not acids. This result is in agreement with those of Albeck, et al41 who concluded that “the yellowing tendency of [oxidized] cottons is found to depend solely on the aldehyde groups content, the ketone and carboxyl groups having no appreciable influence.”
Fig. 4.
Normalized Color Change vs. Baking Time at 150�C for Cotton and Rayon Cloths.
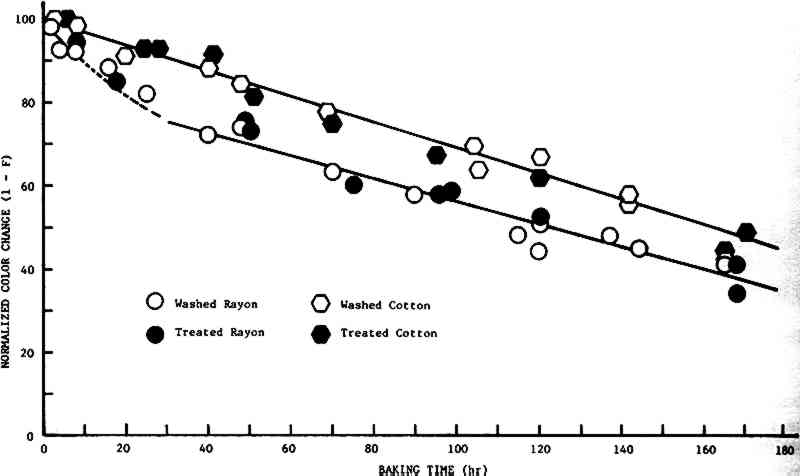 |
Furthermore, we see that the initial rate of discoloration of the rayon is greater than that of cotton, while at times greater than 40 hr it is the same (about 0.3 units/hr). This effect may be due to the higher surface area of the finer rayon fibers compared to the cotton. Increased surface area would permit a more rapid diffusion of moisture from the fiber, which might enhance the rate of reaction at the air/fiber interface if, as is likely, moisture influences the reaction rate. It should be noted that the result could also be ascribed to the fact that the cotton has a dense cuticle layer which the rayon lacks, so that these phenomena may be due to a combination of surface area and cuticle.
2.4 CONCLUSIONS
FROM THE RESULTS of this work to date, it may be concluded that rinsing new cellulosic textiles in a dilute calcium hydroxide solution enhances resistance to strength loss caused by thermal degradation by about a factor of 2, but has little or no effect on the darkening of the fibers, and that these results are independent of the source of the cellulose. In addition, the darkening of cellulosic textiles appears to proceed through the formation of aldehydes rather than acids.
ACKNOWLEDGEMENTS
THE AUTHOR WISHES to thank Mrs. Lucia Tang for her helpful suggestions, and the Conservation Analytical Laboratory of the Smithsonian Institution and the University of Maryland for their support, both financial and moral, of this work.
|