ERADICATION OF INSECTS FROM WOOL TEXTILES
Barbara M. Reagan
ABSTRACT—A variety of chemical and nonchemical methods is available for controlling fabric pests. Part I in this series presents an overview of the various methods available for insect control on wool textiles. Part II presents the results of a study on the feasibility of using microwaves as a nonchemical means of insect control.
1 Part I chemical, Environmental, And Irradiation Methods
1.1 INTRODUCTION
Museum personnel, private collectors, and university faculty responsible for maintaining textile collections frequently are required to make decisions or are asked questions pertaining to insect control on wool textiles. Decision making in this area becomes increasingly difficult with the enactment or revisions of state and federal laws and with new developments in chemical pesticides and alternative methods of eradication. It is the intent of this paper to present an overview of chemical and nonchemical methods of pest control applicable to museum and home use. The discussion of chemical insecticides is not limited to those EPA-approved for museums, institutions, or public buildings because many questions concerning fabric pest control come from private collectors. Furthermore, some of the less toxic insecticides approved for home use may eventually be approved for use in museums and other public buildings.
The commercial products listed as insecticides are those now approved for general or restricted use by the Environmental Protection Agency (EPA). The status of specific insecticides should always be checked because lists of EPA-approved products quickly become obsolete. In addition, many states have specific pesticide registration requirements, which often limit the geographic availability of commercial products. One may contact state agricultural extension specialists for information on state laws and requirements regulating the use of pesticides.
In addition to common methods of controlling insect growth on wool textiles, several unusual and alternative chemical, biological, and nonchemical methods of pest control are discussed below. These may serve as an inspiration for future research. Even though this paper focuses on elimination methods for controlling fabric pests, preventive measures (i.e., good housekeeping practices and periodic inspection of wool, feathers, furs, etc.) can reduce the risk of introducing insect populations into dwellings and storage areas or providing conditions that favor insect development.1
1.2 INSECT DAMAGE ON TEXTILES
Insect damage to wool-containing textiles in the United States is estimated at $200 million annually.2 According to the National Pest Control Association,3 fabric pests are making a comeback because most residual insecticides formerly used in their control (i.e., dieldrin and DDT) have been banned. Fabric pests attack wool and other protein-containing items such as feathers, skins, hair, and insect and animal collections. Insect damage can appreciably reduce the value of garments, carpets, upholstered furniture, and priceless heirlooms. Museum personnel, conservators, and owners of private or public collections often are confronted with the problem of controlling pests in textile storage areas or in individual items such as recent acquisitions that show signs of possible infestation.
The majority of insect damage to wool is attributed to the common or webbing clothes moth and the black carpet beetle; other insects and species of clothes moths and carpet beetles, however, also may cause considerable damage.4 Fabric pests commonly encountered in the United States include:5
- Webbing clothes moth, Tineola bisselliella Hum.
- Casemaking clothes moth, Tinea pellionella L.
- Carpet moth or tapestry moth, Trichophage tapetzella L.
- Plaster bag-worm, Tineola walshinghami Haworth
- Black carpet beetle, Attagenus megatoma F.
- Common carpet beetle, Anthrenus scrophulariae L
- Varied carpet beetle, Anthrenus verbasci L.
- Odd beetle, Thylodrias contractus Mot Schulsky
- Cabinet beetle, Trogoderma spp.
- Hide beetle, Dermestes spp.
In an excellent publication on pest control in museums, Kingsolver6 presents an informative and well-illustrated guide to these and other insect pests found in museums. By referring to this guide, one can greatly expedite the identification of common fabric pests—the first step in any eradication procedure.
Factors to consider when selecting a suitable method to control fabric pests include:
- the type of pest and its life cycle;
- the type and form of the item to be treated and its location;
- the potency of the treatment and the desired residual effect;
- toxicity and hazards to the environment;
- availability and cost;
- detrimental effects to the textile, including its fiber properties, dyes, and finishes;
- application equipment and personnel required, such as a licensed pest control operator (PCO) for “restricted use” pesticides; and
- federal and state laws governing the use of the chemical pesticides.7, 8, 9 The relative safety of a selected insecticide always should be ascertained before it is used.
The type of insect and its developmental stage should be considered when selecting an appropriate insecticide or investigating new or alternative eradication methods. Adult insects and young larvae, for example, are often more susceptible to insecticides than are eggs, mature larvae, and pupae. Similarly, clothes moths are more susceptible than carpet beetles to cedar vapors, temperature extremes, and certain insecticides.10, 11 Many insecticides that rapidly kill clothes moth larvae have little or no effect on carpet beetles.12 Higher concentrations of chemicals are usually required to protect wool textiles from black carpet beetles than from clothes moths.13 Furthermore, certain insect species reportedly build up tolerances to insecticides used to control fabric pests.
1.3 CHEMICAL METHODS OF CONTROLLING INSECTS
Pesticides are chemicals that kill or control pests. They are classified according to their function. Insecticides, for example, are chemicals used to kill insects, whereas herbicides are used to kill weeds.14 Pesticides are sold in a variety of usable forms, depending on the active ingredients and intended use. Some of the common forms of available insecticides for controlling fabric pests include fumigants, repellents, sprays, dusts, aerosols, fogging concentrates, impregnates (mothproofing agents), and attractants.15 These terms often reflect the mechanism by which the insect is controlled. Additionally, fabric pests can be controlled with chemicals that modify the chemical makeup of wool, function as antimetabolites, or control insect behavior; or they may be controlled biologically. In the following discussion, the various insecticides used to control clothes moths, carpet beetles, and other insects that attack textiles are discussed in terms of the control method.
Ware16 and Parker17 outline the various physical forms of pesticides available commercially. Sprays, for example, are available as emulsible concentrates, wettable powders, water-soluble powders, oil solutions, soluble pellets, or sprayable suspensions. It is beyond the scope of this article to discuss each form.
Most insecticides for fabric pest control are contact sprays which contain the active insecticide plus inactive aromatic hydrocarbons and petroleum-derivate solvents. Pesticide users should be aware of the insecticides as well as other additives in the formulation. A recent technical report from the Carpet Manufacturers Association18 stated that commercial insecticide products containing malathion, diazinon, or dichlorvos can cause color change and fading of some dyestuffs. Of particular interest to museum personnel are the results of the Survey of Pest Control Procedures (copies of which were sent to 300 museums).19 Several insecticides (e.g. p-dichlorobenzene, pyrethrins, and dichlorvos) which can cause specimen discoloration and deterioration were reported. In some instances, however, I question whether the degrading effects were due to the insecticide or to the solvents and additives in the commercial formulation. Thus, when evaluating the potential risk of insecticides on textiles, one should consider both the active insecticidal chemicals and the inactive dispersants, solvents, and other additives.
The use of pesticide chemicals in the United States is regulated by state and federal laws. The history of pesticide legislation has been reviewed by Dewey20 and Russell.21 Today the Federal Insecticide, Fungicide, and Rodenticide Act (FIFRA) as amended in 1972, 1975, and 1978, and as administered by the Environmental Protection Agency (EPA), is used to control the use of pesticides so as to protect the applicator, consumer of treated products, and environment.
All pesticide products must be registered with the EPA, must be classified for “general use” or “restricted use,” and must conform to specific federal labeling requirements. Pesticides registered for “restricted use” are those that may so adversely affect the environment that they can be applied only by a certified pest control operator. If a pesticide has been registered for “restricted use,” that should be clearly stated on the label.22
Even though a pesticide may be registered for “general use,” as is the case with “restricted use” pesticides, it may be used only at specific sites designated on the label and approved by the EPA. Thus, many pesticides suitable for home use cannot be used in museums, institutions, or public buildings. According to Stanley and McCann,23 very few insecticides are registered and recommended for use in museums (two are naphthalene and Dowfume 75—in fumigation chambers only).
Pesticide product labels also are required to contain “signal words” in bold print. These are extremely important because they represent the category of toxicity:24
1.3.1 Toxicity
Most insecticides are toxic to humans and should be used with great caution to avoid long-term health related problems. Insecticides usually are more toxic than other types of pesticides, such as herbicides and fungicides. Among the various chemical classes of insecticides, the organophosphates, carbamates, and organochlorines are the most toxic. The pesticide formulation also influences its toxicity; for example, liquid pesticides usually are more toxic than are granular forms because they are formulated in higher concentrations.
The relative toxicity of pesticide chemicals are described in terms of various hazard indicators, such as skin and eye effects, as well as in terms of Acute Dermal LD50, Acute Oral LD50, and Inhalation LC50 values, which are the lethal dosages (LD) or lethal concentrations (LC) necessary to kill 50% of the test subjects (for example, rats or rabbits for measuring toxicity to mammals).25, 26 In general, low LD50 values indicate high mammalian toxicity, whereas high LD50 values reflect negligible toxicity.
Pesticide applicators and users also should be aware of permissible safe concentrations of pesticide chemicals in the air to which humans can be exposed. These safe concentration limits, expressed as Threshold Limit Value (TLV), represent the concentration of the pesticide believed to be harmless to workers when they are continuously exposed for an 8-hour working day, 5 days a week. TLVs for specific pesticides also are reported for short-terms exposure (i.e., maximum allowable concentration for 15 minutes).27
1.3.2 Fumigants
Fumigants are usually highly toxic gases and liquids that are restricted to use only by certified applicators or by persons under their direct supervision.28 It's expensive to use fumigation techniques because special equipment is required, such as fumigation chambers, and users must be specially trained.
In general, chemicals used for fumigation are small, volatile molecules, many of which contain one or more halogens (Cl, Br, or F). Common fumigants that may be used to kill insects on textiles are listed in Table I.
TABLE I Insecticidal Fumigants
Fumigants usually kill all stages of the insect, but they do not protect against reinfestation. However, fumigating buildings and warehouses to eradicate populations of clothes moths, carpet beetles, and other fabric pests is rather uncommon, except when infestation is severe. In addition, favorable conditions usually are required for fumigation to be effective against certain insects such as carpet beetles.29
Care must be exercised in using fumigants because of their extreme toxicity and because of fire or explosive hazards, as indicated in Table I. Fumigants also may be damaging to textiles and cause metal surfaces to corrode.
1.3.3 Repellents
Insect repellents are used to discourage insect attack, but many also effectively kill certain stages of specific insects. Some repellents, however, have no lethal effects on insects.
Two of the most common repellents used to control clothes moths and carpet beetles are naphthalene and p-dichlorobenzene, which, if used in high concentrations (i.e., 1 lb/100 cu ft), release vapors that may effectively kill clothes moth eggs and young larvae; however, they have little or no effect on eggs introduced into an area after they have been laid.30, 31 Naphthalene and p-dichlorobenzene also are classified as fumigants, so I have listed them in Table I.
1.3.4 Contact Sprays
Chemicals used as contact sprays and mothproofing agents kill by contact or by being ingested. They vary in effectiveness, mode of action, toxicity, residual properties, and form and method of application.32 The main chemical classes of insecticides used in contact sprays are: 1) organochlorines, 2) organophosphates, 3) botanicals, 4) pyrethroids, 5) dicarboximides, 6) thiocyanates, and 7) carbamates. The active insecticide (within each class) used for fabric pest control are given in Table II; also given are a few examples of commercial products containing the specific insecticide to illustrate the availability of the chemical in commercial formulations.
TABLE II Fogging Agents, Contact Sprays, and Mothproofing Agents EPA-approved for Fabric Pest Control
In general, the organophosphates, organochlorines, pyrethroids, and carbamates are residual-type insecticides with long-lasting effects.33 Throughout history, however, some of the most widely used insecticides have been obtained from the flowers, leaves, and roots of plants (the botanicals). Because many of them are less toxic than other chemical classes, they have been well suited for home use. The botanicals are usually fast acting, but they have little or no residual effect. Synergists such as piperonyl butoxide are frequently added to increase the toxicity of the botanical insecticides.
The toxicity values for the active ingredients in the contact sprays, fogging agents, and mothproofing agents are given in Table III. Usually lesser amounts of the more toxic insecticides, such as the organochlorines, are required for insect control. The merits of using larger quantities of the less toxic insecticides for a desired level of protection can be debated. Whether the contact sprays and mothproofing agents can be absorbed through the skin when individuals come into contact with the treated textile or item is questionable.34
TABLE III Toxicity Values for Insecticides Used to Control Fabric Pests.
1.3.5 Mothproofing Agents
Mothproofing agents have a greater residual effect than do most contact sprays, repellents, and fumigants. A few commercially available mothproofing sprays are sold for home use; however, many of the more durable formulations are applied industrially to wool textiles during processing or during dry cleaning. Mothproofing chemicals do not repell insects, but rather function as a stomach poison after the insect has ingested a small portion of the treated material.35
Some of the earliest mothproofing agents were compounds containing fluorine such as ammonium fluosilicate and zinc fluosilicate.36 These substances were dried into the wool textile. The products most commonly used as mothproofing agents in the United States are Mitin FF and Edolan U, which usually are applied to wool from acidified dyebaths at the boil for the greatest effectiveness.37 They bond to wool ionically by means of the sulphonic acid groups on the insecticide, similar to acid dyes. DDT and dieldrin, also organochlorines, were among the most permanent mothproofers available, but they can no longer be used legally because of EPA restrictions.38
Several commercially available mothproofing agents for home use contain methoxychlor, dichlorvos, or one or more of the pyrethroids (i.e., permethrin, resmethrin, and tetramethrin), as shown in Table II. As indicated by recent studies, permethrin has potential as a possible mothproofing compound for industrial application during dyeing.39, 40 Synthetic pyrethroids are similar to naturally occurring pyrethrins; they exhibit low mammalian toxicity and are biodegradable. Permethrin shows great promise as a mothproofing agent because it is photo-stable and is among the most insecticidally active pyrethroids available.41
The effectiveness of residual insecticides and mothproofing agents may be reduced by washing, dry cleaning, and exposure to light. Even so, wool textiles should be periodically cleaned, if possible, because contamination from perspiration, urine, food stains, air-borne organisms, and soil from handling can encourage insect growth. Clean wool lacks those substances, which commonly contain B vitamins, essential for insect development.42 Whenever possible, textiles should be cleaned before treating; otherwise, in addition to providing nutrients for insect growth, the dust and dirt may absorb some of the mothproofing solutions.
Certified pest control operators and professional exterminators also may apply contact sprays and mothproofing chemicals, usually by spraying the surfaces of the material to be protected (i.e., carpets, rugs, and upholstered furniture). (They commonly refrain from treating clothing items, however.) The mothproofing agents applied by these professionals are usually sprays prepared from oil or water solutions. Water-based solutions are suitable for rooms with poor ventilation and items having rubber or adhesive backings that may be damaged by oil-based sprays. Water-based solutions, on the other hand, may cause shrinkage, color loss, and staining on certain textile items.43
1.3.6 Antimetabolites
Antimetabolites are similar to known metabolites (i.e., vitamins, hormones, amino acids), but are not metabolized in the same way, so they disrupt the metabolic cycle and cause insects to starve. Other types of antimetabolites, like sulphonamides, may be used on wool textiles to inhibit the development of microorganisms, which supply important nutrients for insect growth.44
1.3.7 Chemicals that Control Insect Behavior
An alternative method for controlling insects on textiles and a possible area for future research is the use of chemicals that control insect behavior by impeding their ability to locate food, mate, or find suitable egg-laying sites. Another method with possibilities is the use of chemical attractants to lead insects into traps containing poisons or sterilants. Unlike insecticides, many of the chemicals used to control insect behavior are neither toxic nor polluting.45
1.4 BIOLOGICAL CONTROL
Certain types of microbial pathogens such as fungi, bacteria, and viruses can be devastating to insect populations. When they are used deliberately to control insects, the method is referred to as biological control. Microbial pathogens usually have a restricted host range and are harmless to higher animals and man. They have been used to a limited extent to control insects other than those that commonly attack wool textiles. Some of the advantages and disadvantages of biological control are discussed in Wool Science Review,46 but again, little research has been done on using this method to control insect growth on textiles.
1.5 CHEMICAL MODIFICATION OF WOOL
Another approach to reducing or eliminating insect attack on wool is by chemically modifying the wool protein, keratin. Methods explored include: 1) chemically modifying the cystine linkage or keratin's side chains, which would inhibit enzyme attack and protein digestion by the insect; and 2) chemically bonding toxic groups to the polymer chains.47 Although promising, none of these methods have achieved industrial significance.
1.6 LAUNDERING AND DRY CLEANING SOLUTIONS
Two of the simplest methods to kill the various stages of clothes moths and carpet beetles are washing the wool items in a strong solution of neutral soap or dry cleaning in a suitable solvent.48 Of course, neither method prevents reinfestation, although the cleaned article may be less attractive or nutritive and thus will inhibit insect growth. However, the cleaning solution may damage delicate or fragile historic textiles.
1.7 NONCHEMICAL METHODS OF INSECT CONTROL
1.7.1 Temperature
Clothes moths and carpet beetles can be killed by extremes in temperature. Success depends on the exposure temperature and its duration. Rawle49 reported that all stages of the webbing clothes moths were killed by heating the infested area or item to 41� for 4 hours. The exposure can be shortened if higher temperatures are used. Exposure times are reduced to 11 minutes for clothes moths and 30 minutes for carpet beetles when the temperature is raised to 49�C. Textile pests also can be killed by immersing the infested item in hot water at 60�C.
Cold storage of woolens and furs is based on the premise that insect larvae are inactive at temperatures below 10�C. Before wool items and furs are placed in cold storage, they usually are disinfested in a suitable fumigation chamber.50 Kew51 reported that exposure at − 18�C for 48 hours effectively kills pupae, larvae, and adult cigarette beetles. Other researchers have shown that freezing is an effective means of killing both clothes moths and carpet beetles.52
1.7.2 Irradiation Disinfestation
The insect-killing power of electromagnetic radiation as an alternative to chemical methods has been investigated as a way to control pests in a variety of commodities, such as cereal products, wheat, flour, feed bags, and wood, to reduce insect damage during storage and transportation.53, 54, 55, 56 One of the first attempts to use electromagnetic radiation for insect control occurred more than 50 years ago when X-rays were used to kill beetles in packaged cigarettes.57 In several excellent review papers, Nelson58, 59 discusses the use, past accomplishments, current studies, advantages, and future possibilities for insect control with electromagnetic, sonic, and ultrasonic energy.
The use of gamma radiation, microwaves, and radiowaves for insect control has received considerable attention because of their advantages over chemical insecticides. Irradiation disinfestation is usually much faster than conventional chemical methods of insect control, it leaves no harmful residues, and it is easily adapted to continuous-process treatments. In addition, insects are not likely to develop a resistance to electromagnetic radiation treatments.60, 61
Reagan, Chio-Cheng, and Streit62 demonstrated that 2450 MHz microwave radiation will disinfest wool textiles without significantly changing the color of various acid dyes and natural dyes commonly used on wool or without causing a significant loss in fabric strength.
Most of the research on microwave insect control has been directed toward insects other than fabric pests. Because insecticides may have a detrimental effect on the dyes, finishes, and fibers in historic textiles, more research is needed on nonchemical methods of controlling insects on textiles. As stated by Edwards, Bell, and King:63
The discovery of efficacious nonchemical methods of pest control that are economically feasible for the average museum would be the best of all possible answers.
1.8 SUMMARY
Commonly used chemical and nonchemical methods of controlling fabric pests on wool textiles as well as alternative methods that merit consideration and possible research have been presented. Careful attention must be given to the method(s) used in museums for disinfestation, especially when treating textiles that are in a fragile or damaged state. Preventive insect control procedures must be effective without damaging the textile. Research is continuing at Kansas State University to evaluate the effects of chemical insecticides on the physical and chemical properties of wool and the colorfastness of natural and synthetic dyes.
ACKNOWLEDGEMENTS
I thank Annie Cheng and Kari Arnold, Research Assistants, Department of Clothing, Textiles and Interior Design; and Marian Massoth, Extension Assistant, Pesticide Impact Assessment, for their assistance in collecting data on pesticide formulations. The technical assistance of Mr. Martin Dannatt, CPO, Schendel Pest Control, Manhattan, Kansas, also is appreciated.
REFERENCES
Encyclopedia of Structural Pest Control, Vol. 3: General Pests. National Pest Control Association, Vienna, Va.
Metcalf, R.L.; Luckman, W.W.Introduction to Pest Control Management. New York: John Wiley & Sons, 1975.
Ref. 1.
McPhee, J.R.The Mothproofing of Wool. England: Merrow Publishing Co. Ltd., 1971.
Ref. 1.
Kingsolver, J. “Illustrated Guide to Common Insect Pests in Museums.” Pest Control in Museums: A Status Report (1980). ed.S.R.Edwards, B.M.Bell, and M.E.King, Lawrence, Kansas: Association of Systematics Collection, 1981.
Applying Pesticides Correctly: A Guide for Commercial Applicators. Environmental Protection Agency, Office of Pesticide Programs, Washington, D.C.
Edwards, S.R.; Bell, B.M.; King, M.E., ed.Pest Control in Museums: A Status Report (1980). Lawrence, Kansas: Association of Systematics Collection, 1981.
Spivak, S.M.; Worth, J.; Wood, F.E. “Assessing the Effects of Pesticide Chemicals on Historic Textiles,” Preservation of Paper and Textiles of Historic and Artistic Value II. Advances in Chemistry Series 193, ed.J.C.Williams, Washington, D.C.: American Chemical Society, 1981.
Rawle, S.G. “The Effects of High Temperature on the Common Clothes Moth, Tineola Bisselliella (Humm).” Bulletin of Entomological Research. 42 (1961): 29–40.
Laudani, H. “Technology of Grain Irradiation.” USDA Agricultural Research Service, Marketing Quality Research Division, 1967, pp 1–8.
“The Present Situation in Mothproofing Wool, Part 1.” Wool Science Review. No. 2 (1965): 1–17.
Dodd, G.D.: Carter, S.W.: Patchett, C.J. “The Use of Permethrin in New Insect Proofing Agents for Wool.” Journal of the Society of Dyers and Colourists97 (1981): 125–127.
Berg, G.L., ed.Farm Chemicals Handbook 1982. Willoughby, Ohio: Meister Publishing Company, 1982.
Ware, G.W.The Pesticide Book. San Francisco: W.H. Freeman and Company, 1978.
Ibid.
Parker, T.A. “Pesticide Terminology.” Pest Control in Museums: A Status Report (1980). ed.S.R.Edwards, B.M.Bell, and M.E.King, Lawrence, Kansas: Association of Systematics Collection, 1981.
“Carpet Spot Complaints.” Carpet Manufacturers Association of the West, West Covina, Ca. February 12, 1982.
Ref. 8.
Dewey, J.E. “Pesticide Application Laws, Regulations, and Training Programs Designed for Promoting Greater Worker Safety.” Pesticide Management and Insect Resistance. ed.D.L.Watson and A.W.A.Brown, New York: Academic Press, 1977.
Russell, I.L. “Federal Statutes and Regulations Governing the Use of Pesticides,” Pest Control in Museums: A Status Report (1980). ed.S.R.Edwards, B.M.Bell, and M.E.King, Lawrence, Kansas: Association of Systematics Collection, 1981.
Encyclopedia of Structural Pest Control, Vol. 6. National Pest Control Association, Vienna, Va.
Ref. 15.
Stanley, E.; McCann, M. “Technical Reports on Pesticides Used in Museums.” Pest Control in Museums: A Status Report (1980). ed.S.R.Edwards, B.M.Bell, and M.E.King, Lawrence, Kansas: Association of Systematics Collection, 1981.
Pecsok, R.L.; Chapman, K.; Ponder, W.H., ed.Chemical Technology Handbook. Washington, D.C.: American Chemical Society, 1975.
Herrick, R. “The Historical Perspective,” Dangerous Properties of Industrial Materials. ed.N.I.Sax, New York: Van Nostrand Reinhold Company, 4th edition, 1975.
Ref. 24.
Ref. 15 and 20.
Ref. 22.
Laudani, H.; Clark, P.H.; Williams, H.L.; Dale, W.E. “Insect Control on Feathers.” Soap and Chemical Specialties. 31 (1975): 199, 201, 203, 204, 225 and 227.
“Paradichlorobenzene.” Bulletin 30C, PPG Industries, Pittsburgh, Pa.
Moncrieff, R.W.Mothproofing. London: Leonard Hill Ltd., 1950.
Private communication, March 1981: Gates, D., Cooperative Extension Service, Kansas State University, Manhattan, Kansas 66506.
Pence, R.J. “Fabric Pest Control.” Soap and Chemical Specialties. 35 (1969): 65–68, 105, 106.
Ref. 1 and 4.
Hall, A.J.Textile Finishing. London: Heywood Books, 3rd edition, 1966.
“Care Needed in Industrial Mothproofing.” CSIRO Textile News. No. 7 (1979): 1, 5.
Ref. 15.
Byrne, K.M.; Shaw, T. “Mothproofing of Wool with Permethrin: Industrial, Environmental and Toxicological Aspects.” Journal of the Society of Dyers and Colourists. 97 (1981) 404–410.
Mayfield, R.J.; O'Loughlin, G.J. “Industrial Mothproofing of Wool with Permethrin.” Report No. G42, CSIRO Division of Textile Industry, Australia, 1980.
Ref. 1, 39 and 40.
Ref. 34.
Ref. 1.
Ref. 34.
“The Present Situation in Mothproofing of Wool, Part 2.” Wool Science Review. No. 28 (1965): 33–48.
Ibid.
Ibid.
Back, E.A.Clothes Moths. USDA Leaflet No. 145.
Ref. 10.
Shepard, H.H.Clothes Moths and Carpet Beetles. University of Minn. Agricultural Extension Service, USDA Extension Folder 89.
Ref. 8.
Ref. 48.
Hurlock, E.T.; Llewelling, B.E.; Stables, L.M. “Microwaves Can Kill Insect Pests.” Food Manufacturer. 8 (1979): 37, 39.
Nelson, S.O.: Stetson, L.E. “Comparative Effectiveness of 39- and 2450 MHz Electrical Fields for Control of Rice Weevils in Wheat.” Journal of Economic Entomology. 67 (1974): 592–595.
Nelson, S.O. “Insect Control Studies With Microwaves and Other Radiofrequency Energy.” Bulletin of Entomological Society of America. 19 (1973): 157–163.
Bletchly, J.D. “VHF Radiowaves for Wood-Boring Insect Control.” International Pest Control. 7 (1965): 15–20.
Laudani, H. “Technology of Grain Irradiation.” USDA Agricultural Research Service, Market Quality Research Division, 1967, pp. 1–8.
Nelson, S.O. “Electromagnetic and Sonic Energy for Insect Control.” Transactions of the American Society of Agricultural Engineers. 9 (1966): 398–405.
Nelson, S.O. “Radiation Processing in Agriculture.” Transactions of the American Society of Agricultural Engineers. 5 (1962): 20–25, 30.
Tilton, E.W.; Brown, J.H.; Cogburn, R.R. “Irradiation Disinfestation of Cornmeal.” Journal of Economic Entomology. 71 (1978): 701–703.
Ref. 53.
Reagan, B.M.; Chiao-Cheng, J.H.; Streit, N.J.
“Effects of Microwave Radiation on the Webbing Clothes Moth, Tineola Bisselliella (Humm.) and Textiles.” Journal of Food Protection. 43 (1980): 658–663.
Ref. 8.
Martin, H.; Worthing, C.R., ed.Pesticide Manual. 4th Ed.England: British Crop Protection Council, 1974.
Kenaga, E.E.; End, C.S.Commercial Experimental Organic Insecticides (1974 Revisions). College Park, Maryland: Entomological Society of America, October 1974.
1 Part II Eradication By Microwave Irradiation: An Experimental Method
1.1 INTRODUCTION
Clothes moths, carpet beetles, and other fabric pests usually are eradicated and controlled by insecticidal chemicals that are often toxic, polluting, and cause deterioration and discoloration in textiles. A recent publication on pest control practices in museums stated that additional research is needed to develop safe and effective nonchemical methods of controlling insect growth.1 Extreme variations in temperature have been used to a limited extent to disinfest textiles. For example, subjecting textiles to temperatures below freezing (i.e., − 18�C for 4 hours or 0�C for several days) can be effective in killing fabric pests.2
An alternative, nonchemical method of disinfesting textiles is microwave irradiation. Applying microwaves to textiles is not new. Microwave heating has been used to a limited extent in the textile industry for drying, dyeing, and finishing textiles.3–11 Microwave disinfestation also is not new. Since World War I, the feasibility and cost-effectiveness of killing insects with electromagnetic radiation have been explored.12 Gamma, microwave, and radiowave frequencies have been used in the agricultural and food processing industries to control insect growth in wheat, flour, stored grain, and cereal products and to eradicate wood-boring insects in timber.13–16
Advantages of microwave and radiowave disinfestation include speed, efficiency, and the absence of toxic, hazardous or polluting residues.17, 18 Also, insects are not likely to develop a resistance to radiation as they often do to chemical insecticides. In Australia, for example, clothes moths had developed a tolerance to dieldrin, a widely used mothproofing agent that is no longer available in the United States.19, 20
The microwave absorbing potentials of the insect and of the host or infested material determines the effectiveness of the treatment. The efficacy of microwave disinfestation depends on the physical, chemical, and dielectrical properties of the material and insect and the output and frequency of the radiation.21 Host materials containing no polar groups and little or no moisture generally do not absorb microwaves.
Microwave absorption produces heat by increasing the vibrational activity of the molecules. The lethal effect in insects is attributed to the heat generated in the host material and in the insect's body, but certain nonthermal effects have been reported.22 Microwave exposure also can result in abnormal development, prolonged pupation, and shorter adult life in insects, as reported for mealworms irradiated with microwaves.23
Because the radiation-absorbing qualities of the host material and of the insect may differ, one may heat faster than the other.24, 25 The type, particle size, compactness, and moisture content of the host material as well as the type, developmental stage, and species of the insect influence the effectiveness of microwaves.26 Nelson27 reported that microwave disinfestation was more effective in killing rice weevils in wheat as the moisture content of the wheat was increased. In several studies, it was necessary to heat the host material to a temperature that was lethal to the insect to obtain 100% kill.28
The chief purpose of radiation-disinfestation treatments is to kill insects economically and effectively without harming the host material.29 Previous research by Reagan, Chiao-Cheng, and Streit30 showed that 2450 MHz microwave radiation can be used to disinfest wool textiles. Four minutes of microwave exposure was effective in killing (100%) the egg, larval, and adult stages of the webbing clothes moth on small wool samples (4.5 � 4.5 cm) with no significant color change in 93 acid and natural dyes commonly used on wool fabrics. Research was continued to determine if longer exposure times were needed to disinfest larger wool samples (i.e., 2.2 m) and is reported here.
In assessing the potential of using microwave radiation for disinfesting wool textiles, I also evaluated the effects of microwave radiation on selected physical and chemical properties of new and old wool fabrics. Specific tests performed on the new wool included breaking strength, elongation, shrinkage, moisture regain, color change (yellowing), and alkali solubility. Breaking strength, elongation, and alkali solubility tests were performed on the old wool. Because of the limited sample size, shrinkage and moisture regain tests were not conducted on the old wool samples after microwave irradiation. Color change was not evaluated on the old wool because the samples had been dyed. Scanning electron micrographs were taken of fiber specimens from both new and old wool samples before and after they were irradiated with microwaves to determine if any surface changes might have occurred in the fibers after treatment.
1.2 EXPERIMENTAL PROCEDURES
1.2.1 Materials
1.2.1.1 Insects
Webbing clothes moths, Tineola bisselliella (Humm.), obtained from the Stored-Products Insects Research and Development Laboratory, Savannah, Ga., were reared according to the procedures in AATCC Test Method 24-1977, Resistance of Textiles to Insects.31 Insect cultures were prepared by placing newly emerging moths from the stock cultures into 2-quart Mason jars containing Moth Test Cloth (Testfabrics, Inc.) fortified with brewer's yeast. After 3 days, the moths were removed and transferred to other jars for further egg laying.
The Moth Test Cloth containing the newly deposited eggs was removed from the jars and gently brushed with a soft-bristled brush to dislodge the eggs as shown in Figure 1 The eggs were passed through a No. 40 U. S. standard sieve to separate them from larger, extraneous matter, and then 10 each were placed in small bags consisting of a 5 � 5 cm swatch of transparent cellulose film and Moth Test Cloth, sewn together on three sides 0.5 cm from the edge. After the eggs were placed in the fabric/film bag, its open end was closed with transparent tape.
Fig. 1.
Removing newly deposited eggs from moth test cloth with soft-bristled brush.
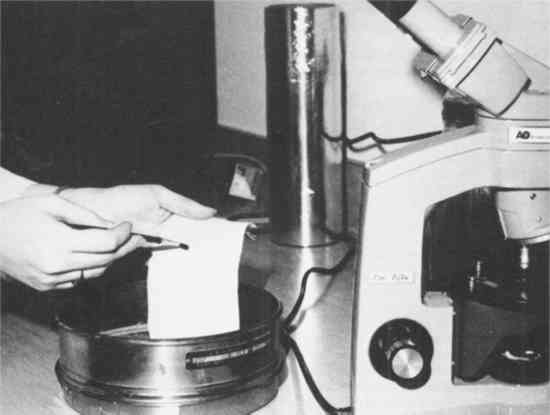 |
The larvae and adult moths, 10 each, also were placed in individual fabric/film bags. Experiments were carried out on larvae approximately 40–43 days old as measured from the date of egg deposition. Newly emerging moths were collected in a glass vial fitted with a rubber-stoppered, suctioning device (see Figure 2). Before the moths were transferred to the fabric/film bags, they were temporarily immobilized by placing the vial in a beaker of ice water. The fabric/film bags, containing the moths were set aside approximately one hour before microwave exposure.
Fig. 2.
Transferring adult webbing clothes moths from Mason jars with a rubber-stoppered suctioning device.
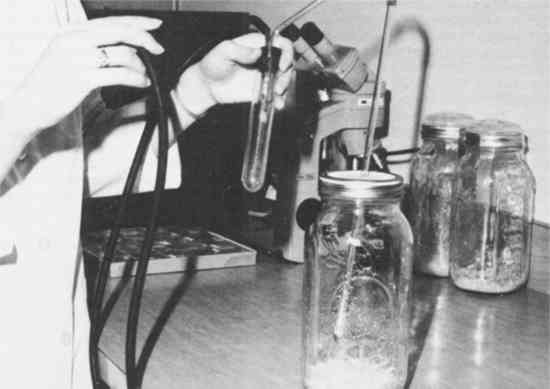 |
1.2.1.2 Wool Fabrics
A worsted, 100% wool gabardine (Style #522, Testfabrics, Inc.) with a fabric count of 29 � 19 per cm and fabric weight of 407 g/m2 was used in the experiments for determining the lowest level of microwave raidation lethal to the egg, larval, and adult stages of the webbing clothes moth. It also was used in assessing the effects of microwave radiation on the physical and chemical properties of new wool.
In addition, two 100% wool fabrics dating from c. 1916 were irradiated with microwaves and evaluated for changes in alkali solubility and tensile properties to determine if aged fabrics were more susceptible than new wool to damage by microwaves. Both of these fabrics were taken from swatch cards used for advertising purposes. The sample designated Fabric A was a 2/2 worsted wool gabardine with a fabric count of 22 � 14 per cm. Fabric B was a plain weave, wool flannel with a fabric count of 22 � 13 per cm. Both old wools had a fabric weight of 203 g/m2. Prior to microwave irradiation and performing the various physical and chemical tests, all fabrics were conditioned in a standard atmosphere for testing (70 � 2�F and 65 � 2% relative humidity) for 24 hours.
1.2.2 Method
1.2.2.1 Insect Exposure to Microwave Radiation
The egg, larval, and adult stages of the webbing clothes moth were exposed within a 2.2 m sample of wool gabardine that weighed 832.4 g to determine the time required to disinfest the amount of cloth used in an “average” wool garment. The wool gabardine samples were conditioned for 24 hours and then folded so that the final dimensions of each were 22.5 � 30.0 cm.
The fabric/film bags containing the insects were placed singly between the folds in the wool gabardine with an equal amount of fabric above and below. The top layers of the fabric were arched slightly so that the weight of the fabric would not crush the insects (see Figure 3). The wool gabardine and fabric/film bags containing the insects were irradiated for 0.5, 1.0, 2.0, 2.5, 3.0, 4.0 or 5.0 minutes in a Sharp Carousel, Model R-6770, microwave oven (2450 MHz) operating at full power, then removed immediately. The 2.2 m wool samples were reconditioned for 24 hours before each successive exposure. Three replicates of the fabric/film bags containing the eggs, larvae, or adult moths were irradiated at each of specified exposure times.
Fig. 3.
fabric/film bag containing 10 insects is placed inside 2.2 m of wool gabardine.
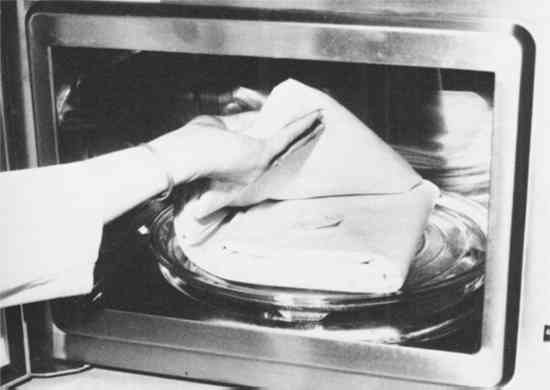 |
Mortality counts on the eggs were made 30–40 days after microwave exposure. The larvae and adult moths were examined approximately one hour after being irradiated. A larva showing no response to the touch of a pin was considered dead.
1.2.2.2 Fabric Temperature
The temperature of the 2.2 m wool gabardine samples during microwave exposure was monitored with temperature-sensitive strips (Tempilabels�, Omega Engineering, Inc.) to determine the evenness of microwave heating within the fabrics and to evaluate the effects of microwave irradiation on the properties of wool. The Tempilabels� contain a series of dots corresponding to different temperatures. The center of the dots will darken if the temperature associated with a specific dot has been reached.
A series of Tempilabels� were placed at the following locations within the 2.2 m wool gabardine samples: top-edge, top-center, middle-edge, middle-center, bottom-edge, and bottom-center (see Figure 4). Temperatures were recorded after 1, 6, and 10 repeated 3-minute exposures and after 10 minutes of continuous exposure. The 3-minute period of exposure represented the time necessary to kill the egg, larval, and adult stages of the webbing clothes moth. Temperatures after 10 minutes of continuous exposure were recorded to assess the effects of prolonged microwave irradiation on wool.
Fig. 4.
Locations of Tempilabels� used to monitor temperature of wool gabardine (2.2 m sample) during microwave irradiation: top, middle, and bottom edges and centers.
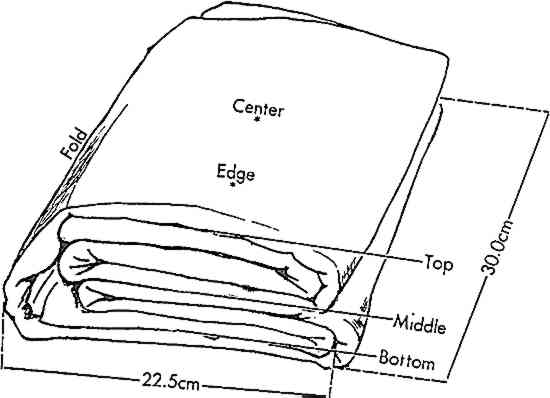 |
Additional tests performed on the 2.2 m samples used for determing fabric temperatures included shrinkage, color change, moisture regain, alkali solubility, and tensile properties. These samples were not used in the previous experiments in which the lethal dosage of microwave radiation was ascertained. After each 3-minute exposure, 25 � 25 cm samples were cut from the middle section of the larger 2.2 m wool samples, replaced by unexposed samples to maintain a constant sample weight, and conditioned for further testing. Two replicates were tested at each microwave exposure level.
1.2.2.3 Fabric Shrinkage
To determine whether or not microwave irradiation caused fabric shrinkage, five sets of 25.4 � 25.4 cm reference squares were randomly marked on each of the 2.2 m samples of wool gabardine. After irradiating the samples with microwaves for 1, 6, or 10 3-minute periods or for 10 minutes, they were reconditioned and the reference markings were measured at the corners and midpoint of each square, in both the warp and weft directions. The average original (unexposed control) and final (after exposure) distances between the reference markings were used to calculate shrinkage (%) in the lengthwise and widthwise fabric directions.
Fig. .
 |
where:
A = original distance between reference marks, and B= final distance between reference marks.
1.2.2.4 Color Change
The color of the undyed wool gabardine before and after microwave irradiation was evaluated visually and instrumentally with a Hunterlab D25M-4 tristimulus colorimeter. A Tektronix 31 programmable calculator, which interfaced with the optical processor on the colorimeter, converted CIE tristimulus values (X, Y, and Z) into CIE 1976 L∗a∗b∗ uniform color solid coordinates, and calculated total color difference, ΔE. Six readings were averaged for each sample (top-edge, top-center, middle-edge, middle-center, bottom-edge, and bottom-center positions), within each treatment (1, 6, and 10 3-minute exposures and one 10-minute exposure) and replication.
1.2.2.5 Moisture Regain
Proceedures in ASTM D 629–77, Quantitative Analysis of Textiles,32 were used for determining the amount of moisture in the wool gabardine before and after microwave exposure. Three specimens, each measuring 7.6 � 7.6 cm, were cut from the control and microwave irradiated samples (25.4 � 25.4 cm squares removed from the 2.2 m samples). All specimens were conditioned for 24 hours, weighed, heated in a Precision Scientific Company, Model 17 laboratory oven at 110 � 2�C for one hour, and then placed in a desiccator for 4 days to ensure that all residual moisture had been removed. The dried specimens were then reweighed, and moisture regain was calculated by using the following equation:
Fig. .
 |
where:
A = air-dry weight of specimen, g, and B= oven/desiccator-dry weight of specimen, g.
1.2.2.6 Tensile Properties
Changes in tensile properties are one of the most widely used methods for investigating the effects of thermal treatments on fiber properties. In this study, breaking strength and elongation tests were conducted on warp yarns taken from the 25.4 � 25.4 cm samples of wool gabardine after microwave irradiation (1, 6, and 10 3-minute exposures and one 10-minute exposure). The unexposed controls also were tested. Breaking strength and elongation tests were performed on yarns taken from the filling direction in the old fabrics. Because of the limited fabric, the old wools were tested only before and after 10 minutes of microwave irradiation. The old wool fabric samples were placed between the center folds of a 2.2 m sample of wool gabardine during exposure to maintain the same mass of fabric used in testing the new wool.
Procedures in ASTM D 2256, Standard Test Method for Breaking Load (Strength) and Elongation of Yarn by the Single-Strand Method,33 were followed by using a Scott CRE tensile testing machine, a 3-inch gage length, and a 20 � 3 second time to break. The results reported are an average of five yarn specimens for each replication (2) and microwave exposure time.
1.2.2.7 Alkali Solubility of Wool
The method described by Earland and Raven34 was used to determine the amount of wool soluble in a 0.100 N solution of sodium hydroxide. Fabric samples weighing approximately 1 g were cut from the control and microwave-irradiated wool (25.4 � 25.4 cm sample removed from the larger 2.2 m sample), conditioned, and then unraveled. The unraveled yarns were cut into 1 cm lengths, placed in 250 ml beakers, oven-dried at 110 � 2�C for one hour, and then placed in a desiccator overnight.
Specimens weighing approximately 0.5 g were removed from each beaker and weighed to the nearest 0.001 g. The weighed specimens were transferred to a 250 ml of 0.100 N sodium hydroxide at 65 � 0.5�C. The flasks were stoppered and placed in a Tamson, Model TCV 40, constant temperature bath set at 65 � 0.5�C and shaken gently every 10 minutes for 60 minutes. The contents of the flasks were then transferred to separate, preweighed sintered glass crucibles. The flasks were washed thoroughly in distilled water and emptied into the crucible. The collected material was washed six times with distilled water (55 ml each), once with acetic acid (30 ml of a 0.5% solution), and then given six aditional rinses with distilled water (55 ml each), by using gentle suction to drain the solution after each rinse. Next, the treated specimens were dried in an oven (110 � 2�C) for 3 hours, placed in a desiccator overnight, and then weighed to the nearest 0.001 g. The alkali solubility of the specimen was calculated as follows:
Fig. .
 |
where:
W1 = mass of oven-dry specimen before NaOH treatment, and W2= mass of oven-dry specimen after NaOH treatment.
1.2.2.8 Scanning Electron Microscopy (SEM)
The surface characteristics of fibers taken from the new and old wool fabrics before and after 10 minutes of microwave exposure were examined by an ETECH Scanning Electron Microscope. Specimens irradiated for 3 minutes were not evaluated because previous tests indicated that the changes in these specimens were minimal. Fiber specimens randomly selected from the unexposed and exposed samples were prepared for SEM analysis by mounting them on specimen holders with a conductive paste and coating with a thin layer of carbon and gold-palladium (60–40).
1.2.2.9 Statistical Analysis
Data obtained from the shrinkage, color difference, moisture regain, breaking strength, elongation, and alkali solubility tests were analyzed statistically by using a general linear model and analysis of variance procedure. The Duncan's Multiple Range Test was performed on the data if F was significant in the previous two tests. The level of confidence used in all statistical tests was 0.05.
1.3 RESULTS
1.3.1 Insect Mortality
Mortality percentages for the egg, larval, and adult stages of the webbing clothes moth after 0.5, 1.0, 1.5, 2.0, 2.5, 3.0, 4.0, and 5.0 minutes of microwave irradiation are presented in Table I. Three replicates of 10 insects each were tested at each exposure time and developmental stage of the insect.
TABLE I Mortality of Egg, Larval, and Adult Stages of the Webbing Clothes Moth Exposed to 2450 MHz Microwave Radiation for Different Exposure Times.
In general, mortality percentages associated with the egg, larva, and adult webbing clothes moth progressively increased as microwave exposure time increased. Compared with the larval and adult stages, a higher percentage of eggs was killed by low levels of microwave exposure (0.5, 1.0, and 1.5 minutes), but longer exposure times were needed for 100% mortality in the egg stage. Also, a percentage of egg mortality would occur normally without irradiation; Rawle35 reported the average mortality of unexposed eggs to be approximately 25%, but considerably fewer of our unexposed controls died.
The times required to obtain 100% mortality in the egg, larva, and adult clothes moth were 3.0, 2.0, and 2.0 minutes, respectively. Hence, 3.0 minutes of microwave exposure was sufficient to kill all three stages of the insect in a 2.2 m sample of wool gabardine.
The moth or adult stage of the insect was the least resistant to microwave radiation. As noted in Part I, susceptibility of insects to chemical and nonchemical methods of control is frequently influenced by the stage of the insect.
The egg, larva, and adult clothes moth were killed more quickly when exposed between a 2.2 sample of wool gabardine than when exposed in the Bradley No. 3 polystyrene boxes as reported in our earlier study.36 Wool normally has a high moisture content; in this case, the additional steam generated by the moisture in the larger (2.2 m) wool samples greatly facilitated disinfestation.
1.3.2 Temperature of Irradiated Wool
The average temperatures attained in the 2.2 m wool samples at the six designated locations during microwave exposure, as measured with the heat-sensitive Tempilabels�, are presented in Table II. The initial 3-minute period of microwave exposure resulted in temperature ranges of 62� to 76�C for the six positions monitored within the samples. Repeated 3-minute periods of microwave exposure produced similar temperature ranges. The continuous 10-minute exposure resulted in significant higher temperature ranges of 103� to 149�C. Domestic microwave ovens often produce uneven heat, so variations in temperature within the 2.2 m wool samples were not unexpected.
TABLE II Temperature of Wool Gabardine (2.2 m sample) Exposed to 2450 MHz Microwave Radiation.
The temperatures of the top-center (TC) and top-edge (TE) positions in the wool samples exposed continuously for 10 minutes were considerably lower than those recorded at other locations. In the samples exposed to microwaves for 3 minutes, both initially and after 10 repeated exposures, the highest temperatures were recorded at the middle-edge (ME) positions. Slightly lower temperatures were attained in the middle-center (MC) positions where the insects were placed during testing. Thus, the exposure conditions recommended for microwave disinfestation are 3 minutes of continuous exposure with a minimum internal sample temperature of 69�C.
In selecting a method of insect control for historic as well as contemporary textiles, a major concern is the effects of the treatment on the item. If wool is heated in dry air above 100�C for an extended time, it loses its moisture, the fiber may become harsh, and yellowing and decomposition may occur, resulting in the evolution of hydrogen sulfide and ammonia.37
In an excellent paper on the thermal behavior of textiles (1,436 references), Slater38 reviews conduction, convection, and radiation heating methods, including electromagnetic energy sources, in terms of efficiency, advantages, disadvantages, and industrial applicability. Cloth temperatures below 105�C are considered safe for most textiles. In this study, 3 minutes of microwave exposure resulted in fabric temperatures that were 20–40� below the safe temperature; however, 10 minutes of exposure, far exceeding that needed to disinfest the 2.2 wool samples, produced fabric temperatures above 150�C. Thus, prolonged periods of microwave irradiation should be avoided to reduce the danger of fiber degradation.
1.3.3 Effects of Microwave Radiation on Selected Physical and Chemical Properties of Wool
In selecting a method of insect control for textiles, a major concern is the effects of the treatment on the physical and chemical properties of the fabric. Tests used in this study to assess the safety and viability of microwave irradiation as a nonchemical method of insect control on wool were shrinkage, color change, moisture regain, alkali solubility, tensile properties, and visual fiber characteristics as viewed by scanning electron microscopy. Wool gabardine samples (2.2 m) were irradiated with microwaves for 3 minutes (time required to produce 100% kill) and 10 minutes. The 3-minute treatments were repeated 10 times so that the effects of successive exposures could be evaluated. Samples were evaluated after 10 minutes of exposure to determine if accidental or prolonged microwave heating was detrimental to wool. Because of the limited sample size, the only tests performed on the historic (c. 1916) wool fabrics were yarn breaking strength and elongation, alkali solubility of wool, and SEM analysis. The effects of microwave exposure on acid dyes and natural dyes commonly used on wool were evaluated in a previous study.39
1.3.3.1 Fabric Shrinkage
The average lengthwise and widthwise shrinkage (%) values for the 2.2 m wool samples are given in Table III. One 3-minute exposure resulted in 0.33% and 0.05% shrinkage in the lengthwise and widthwise fabric directions, respectively. No significant increase in shrinkage occurred after 6 or 10 repeated 3-minute exposures. The small amount of shrinkage that occurred in these samples could have been relaxation shrinkage, because the wool gabardine was not steamed, pressed, or washed prior to irradiation.
TABLE III Shrinkage of Wool Gabardine (2.2 m sample) Exposed to 2450 MHz Microwave Radiation.
Compared with the samples exposed repeatedly to microwaves for 3 minutes, the 2.2 m wool samples exposed continuously for 10 minutes exhibited significantly more shrinkage in both the lengthwise and widthwise fabric directions. Thus, prolonged periods of microwave exposure may result in excessive fabric shrinkage and should be avoided.
1.3.3.2 Color Change
The average total color difference for the wool fabrics exposed 1, 6, and 10 times to microwave radiation for 3 minutes ranged from 0.16 to 0.87 ΔE units. For the samples irradiated continuously for 10 minutes, the color difference values were slightly higher, ranging from 0.49 to 1.06 ΔE units (see Table IV). When evaluated visually, however, there was no perceivable color change or yellowing in any of the test specimens irradiated 3 minutes. A slight yellowing was observed in the specimens irradiated continuously for 10 minutes. All color difference values were less than that which corresponded to a step 4–5 (slightly stained) rating on the AATCC Gray Scale for Staining (4–5 rating = 2.3 � 0.3 ΔE (CIELAB) units). Color difference values for the AATCC Gray Scales cannot be used to judge precisely the amount of color change in a test specimen, however.
TABLE IV Total Color Difference (ΔE) for Wool Gabardine (2.2 m samples) Exposed to 2450 MHz Microwave Radiation.
Even though color change could not be perceived visually in the samples that were irradiated continuously for 10 minutes, the highest ΔE values were obtained in those areas of the 2.2 m samples that exhibited the highest temperatures. Thus, prolonged or excessive microwave heating may cause discoloration in wool.
1.3.3.3 Moisture Regain
The wool gabardine samples irradiated with microwaves for 3 minutes and 10 minutes had slightly lower moisture regain values after exposure, but the differences were not statistically significant (see Table V). In this study, moisture regain was evaluated because water absorption in wool is related to the number of polypeptide and amino groups in the fiber. Chemical decomposition may alter the absorption properties of wool if the functional groups are appreciably changed. In addition, the brittleness of a fiber increases as moisture regain decreases. Results of this study showed that microwave irradiation did not cause a significant change in the absorption properties of wool.
TABLE V Moisture Regain Values for Wool Gabardine (2.2 m samples) Exposed to Microwave Radiation.
1.3.3.4 Tensile Strength
No significant change occurred in the breaking strength and elongation of the warp yarns taken from the new wool gabardine irradiated repeatedly for 3 minutes, with intermittent cooling and conditioning, or continuously for 10 minutes. The old wool fabrics dating 1916 also exhibited no significant change in strength and elongation after 10 minutes of continuous microwave exposure (see Table VI). These results agreed with those previously reported.40
TABLE VI Breaking Strength and Elongation of Yarns from Wool Gabardine and Old Wool (c. 1916) Exposed to 2450 MHz Microwave Radiation.
1.3.3.5 Alkali Solubility of Wool
The solubility (%) of wool in a 0.100 N sodium hydroxide solution is a sensitive and convenient quantitative test for assessing the extent to which wool has been damaged during processing (i.e., bleaching, chlorination, light exposure, etc.).41 When the peptide, disulfide, or hydrogen bonds in keratin are ruptured, the solubility of wool usually increases. Zahn and W�rz42 reported the alkali solubility values for wool samples heated and also treated with a variety of chemical agents.
Alkali solubility data for the new wool and old wool fabrics before and after microwave irradiation are given in Table VII. The solubility of the untreated wool gabardine sample was 17.01%. The one 3-minute exposure to microwaves resulted in a 5% decrease in alkali solubility, but repeated 3-minute exposures and the continuous 10-minute exposure increased the percentage of wool soluble in the sodium hydroxide solution. These increases ranged from 8 to 16%. Results from the Duncan's Multiple Range Test showed that all levels of microwave exposure produced significant changes in the percentage solubility of the wool gabardine; there was, however, no significant difference between the mean solubilities for the samples exposed continuously for 10 minutes or repeatedly to six 3-minute exposures. The greatest increase in alkali solubility occurred in the samples that were irradiated with microwaves for 10 3-minute treatments.
TABLE VII Alkali Solubility Values for Wool Gabardine and Old Wool (c. 1916) Exposed to 2450 MHz Microwave Radiation.
The alkali solubility data corresponded with the breaking strength data in that decreases in solubility resulted in increases in breaking strength and vice versa. For example, the wool gabardine samples exposed to microwave radiation for one 3-minute period exhibited a 3.3% increase in breaking strength and a 5% decrease in solubility; whereas the sample irradiated 10 times exhibited a 7% decrease in strength and a 16% increase in solubility, which were the highest mean values obtained in each test.
Old wool Fabric A exhibited only a 2% increase in alkali solubility after 10 minutes of microwave irradiation, whereas old wool Fabric B exhibited a 3% decrease in solubility. Thus, less change occurred in the solubility of the old wool specimens after irradiation, compared with that of the new wool. This may be attributed to the dyes and finishes on the fabric or the previous history of the old wool samples.
1.3.3.6 Scanning Electron Microscopy
Representative specimens from the new wool gabardine and old wool fabrics (c. 1916) before and after 10 minutes of continuous microwave irradiation are shown in Figures 5–7. As mentioned previously, the old wool fabrics were taken from swatch cards used in advertising and thus had not been subjected to repeated wearings or launderings through consumer use. The scale structure and surface characteristics of the old wool fibers were similar to the fibers taken from the new wool gabardine.
Fig. 5.
Scanning electron micrographs of fibers from new wool gabardine, (left) unexposed and (right) exposed to microwaves for ten minutes (1200X).
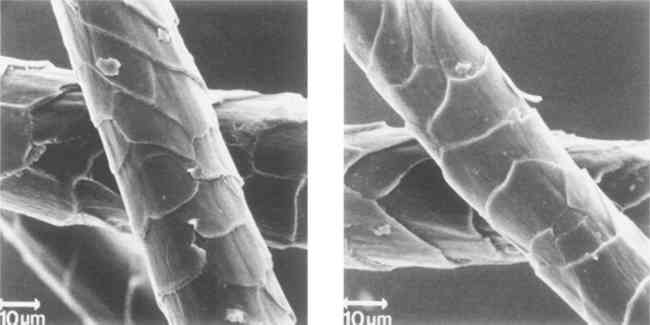 |
Fig. 6.
Scanning electron micrographs of fibers from old wool Fabric A (gabardine, c. 1916), (left) unexposed and (right) exposed to microwaves for 10 minutes (1200X).
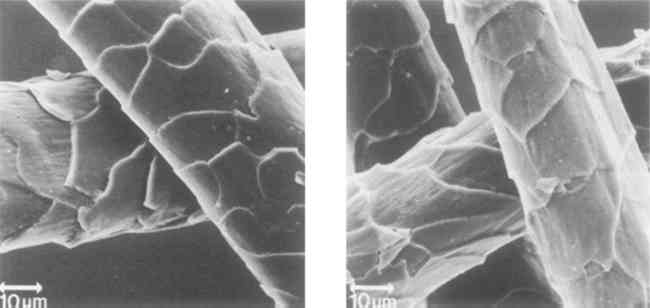 |
Fig. 7.
Scanning electron micrographs of fibers from old wool Fabric B (flannel, c.1916), (left) unexposed and (right) exposed to microwaves for 10 minutes (1200X).
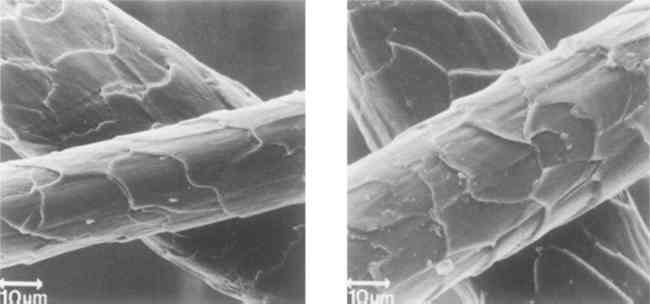 |
Fiber specimens from the new and old wool fabrics were examined after 10 minutes of microwave heating to determine if prolonged periods of irradiation resulted in surface defects or damage. If changes were observed in the fiber after 10 minutes of exposure, additional analyses would have been conducted on fibers irradiated for 3 minutes; however, no changes were observed in the surface characteristics of the new and old wool fibers after 10 minutes of exposure, as shown in Figures 5–7, right-side images. The fiber surfaces had well-defined, undamaged scales; and no cracks, splits, or other defects were apparent.
1.4 CONCLUSIONS
If prudently administered, microwave heating can provide a safe and effective, nonchemical method of disinfesting wool textiles. In this study, 3 minutes of microwave exposure was sufficient to obtain a 100% mortality in the egg, larval, and adult stages of the webbing clothes moth in a 2.2 m sample of wool gabardine with minimal effects on the chemical and physical properties of wool.
Prolonged periods of microwave heating should be avoided, however, as wool may suffer degradation at temperatures above 100�C. Ten minutes of microwave irradiation, which represented prolonged heating in this study, produced internal fabric temperatures of 149�C and caused an increase in alkali solubility, shrinkage and color change when compared with the unexposed samples or those irradiated for 3 minutes.
Before using any chemical or nonchemical method of eradication on textiles, especially those that have historical significance, the past history and condition of the item must be carefully assessed. Microwave disinfestation may be suitable for wool textiles that are in good condition, as demonstrated in this study; however, most chemical and nonchemical methods of insect control, including freezing or conventional heating, may accelerate deterioration in already-damaged textiles. Of course, metal objects should be removed from the textile item before microwave irradiation to avoid damaging the textile or microwave oven due to sparking. In addition, textiles containing metallic yarns should not be exposed to microwaves.
REFERENCES
Edwards, S.R.; Bell, B.M.; King, M.E., ed.Pest Control in Museums: A Status Report (1980). Lawrence, Kansas: Association of Systematics Collection, 1981.
Ibid.
Pepperman, Jr., A.B.; Vail, S.L. “Microwave Drying of FR Cotton Fabrics.” Textile Chemist and Colorist. 9:7 (1977): 17–21.
Lyons, D.W.; Hatcher, J.D.; Sunderland, J.E. “Drying of a Porous Medium with Internal Heat Generation.” Int. Journal of Heat and Mass Transfer. 15 (1972): 897–905.
Evans, D.G.; Skelly, J.K. “Application of Microwave Heating in Dye Fixation.” Journal of the Society of Dyers and Colourists. 88:12 (1972): 429–433.
Delaney, M.J.; Seltzer, I. “Microwave Heating for Fixation of Pad-dyeings on Wool.” Journal of the Society of Dyers and Colourists. 88:2 (1972): 55–59.
Pepperman, Jr., A.B.; Vail, S.L.; Lyons, D.W. “Application of Microwave Drying to Flame-Retardant Finishing of Cotton Textiles.” 16th Annual Chemistry and Processing Conference. March 17–19, 1976, pp. 114–120.
Needles, H.L.; Tai, A.; Berns, R.S.; Alger, K.W. “Microwave-induced Dyeing and Finishing Processes on Textile Substrates.” 1977 National Technical Conference: Book of Papers. Research Triangle Park, N.C.: American Association of Textile Chemists and Colorists, pp. 201–207.
Pendergrass, J.E.; Hatcher, J.D.; Lyons, D.W. “Deposition of Finishes and Dyes in Materials Dried Using Microwave Heating.” Journal of Microwave Power. 7:3 (1972): 207–213.
Pepperman, Jr., A.B.; Vail, S.L.; Lyons, W.L. “The Use of Microwave Drying in the Application of Flame Retardants for Cotton Fabrics.” Journal of Coated Fabrics. 6 (1976): 95–104.
Metaxas, A.C.; Catlow, N.; and Evans, D.G. “Microwave Assisted Dye Fixation.” Journal of Microwave Power. 13:4 (1978): 341–350.
Kirkpatrick, R.L.; Roberts, J.R. “Insect Control in Wheat by Use of Microwave Energy.” Journal of Economic Entomology. 64 (1971): 950 and 951.
Hurlock, E.T.; Llewelling, B.E.; Stables, L.M.; “Microwaves Can Kill Insect Pests.” Food Manufacturer. 8 (1979): 37:39.
Nelson, S.O.; Stetson, L.E. “Comparative Effectiveness of 39- and 2450 MHz Electrical Fields for Control of Rice Weavils in Wheat.” Journal of Economic Entomology. 67 (1974): 592–595.
Bletchly, J.D. “VHF Radiowaves for Wood-Boring Insect Control.” International Pest Control. 7 (1965): 15–20.
Laudani, H. “Technology of Grain Irradiation.” USDA Agricultural Research Service, Market Quality Division, 1967, pp. 1–8.
Nelson, S.O. “Electromagnetic and Sonic Energy for Insect Control.” Transactions of the American Society of Agricultural Engineers. 9 (1966): 389–405.
Thomas, A.M. “Pest Control by High Frequency Electrical Fields–Critical Resume.” Technical Report W/T23, British Electric and Allied Industries, England, 1952.
Lang, J.H.; Bry, R.E. “Preliminary Investigations of Tetramethrin as a Protectant of Woolen Cloth Against Damage by Black Carpet Beetle Larvae (Cleoptera: Dermestidae).” Journal of the Georgia Entomological Society. 7:4 (1972): 260–264.
Mayfield, R.J.; Russel, I.M. “Resistance of Dieldrin of the Case Bearing and Webbing Moth Species in Australia.” Textile Institute and Industry. 15 (1977): 419–420.
Nelson, S.O.; Whitney, W.K. “Radio Frequency Electrical Fields for Stored Grain Insect Control.” Transactions of the American Society of Agricultural Engineers. 3 (1960): 133–137, 144.
Waters, F.L. “Microwave Radiation for Control of Tribolium Confusum in Wheat and Flour.” Journal of Stored Products Research. 12:1 (1976): 19–25.
Carpenter, R.L.; Livstone, E.M. “Evidence for Nonthermal Effects of Microwave Radiation: Abnormal Development of Irradiated Insect Pupae.” IEEE Transactions of Microwave Theory and Techniques. 19 (1971): 173–177.
Nelson, S.O. “Insect Control Studies with Microwaves and Other Radiofrequency Energy.” Bulletin of the Entomological Society of America. 19 (1973): 157–163.
Yeomans, A.H. “Radiant Energy and Insects.” Yearbook of Agriculture. 1952, pp. 411–421.
Ref. 17 and 21.
Ref. 24.
Ref. 15.
Ref. 25.
Reagan, B.M.; Chiao-Cheng, J.H.; Streit, N.J. “Effects of Microwave Radiation on the Webbing Clothes Moth. Tineola bisselliella (Hum.) and Textiles.” Journal of Food Protection. 43 (1980): 658–663.
1980 AATCC Technical Manual. Research Triangle Park, N.C.: American Association of Textile Chemists and Colorists.
1980 ASTM Book of Standards. Parts 32 and 33, Philadelphia, Pa.: American Society for Testing and materials.
Ibid.
Earland, C.; Raven, D.J.Experiments in Textile and Fibre Chemistry. London: Butterworth & Co. Ltd., 1971.
Rawle, S.G. “The Effects of High Temperature on the Common Clothes Moth.” Bulletin of Entomological Research. 42 (1951): 29–40.
Ref. 30.
Earland, C.Wool: Its Chemistry and Physics. 2nd Ed.London: Chapman & Hall Ltd, 1963.
Slater, K. “The Thermal Behavior of Textiles.” Textile Progress. 8:3 (1976): 1–121.
Ref. 30.
Ibid.
Ref. 37.
Zahn, H.; W�rz, A. “Solubility in Acid as a Means of Determining Changes in Wool.” Journal of the Textile Institute. 45 (1954): 88–92.
Section Index |