NOTES ON A PRESSURIZED SYSTEM FOR PRODUCING MAGNESIUM BICARBONATE SOLUTIONS
Randall Couch
6 CARBON DIOXIDE
MAGNESIUM BICARBONATE is formed from magnesium hydroxide and carbon dioxide according to the reaction Mg(OH)2+2CO2 → Mg(HCO3)2. If this reaction occurs under pressure, the concentration of dissolved carbon dioxide is increased, and Le Chatelier's principle requires that the concentration of product must also increase to restore equilibrium. This is the advantage of pressurized systems for producing deacidification solutions.
The surface area of contact between reactants is also important, since the reaction cannot take place except where they meet. The surface area of powder can be maximized by straining and dispersing it in the blender as we have done. The surface area of CO2 is maximized by bubbling, and in this respect our system is not very efficient. There are two reasons for this.
The first cause is inherent in the closed design of the system. When CO2 gas enters the mixing chamber, it bubbles up through the liquid to form an atmosphere which quickly (in a matter of minutes) reaches a pressure equilibrium with the gas source. In our system this happens when the chamber pressure reaches roughly 32 p.s.i. The result is that bubbling comes to a halt—gas can only enter as fast as it is consumed in 1) saturating the water and 2) the bicarbonate reaction itself. After the gas stops bubbling up through the liquid, the site of the reaction is soon limited primarily to the surface of the water, which is agitated only moderately by the stirrer.
There is a partial solution to this problem. The chamber is equipped with a screw-type bleeder valve, which can be adjusted to vent the CO2 atmosphere at a steady rate This prevents the formation of pressure equilibrium. The more gas vented, the more bubbling—but under those circumstanes the pressure is lowered. The optimum balance of pressure against volume of bubbled gas would be a useful specification for the design of an ideal pressurized system. We simply vented the minimum amount of gas necessary to achieve continuous bubbling, so that chamber pressure seldom falls below 30 p.s.i. Venting yielded no appreciable improvement in clarity or rate, however.
The second factor affecting CO2 dispersion is bubble size. Gas enters our mixing chamber through a straight pipe with an inside diameter of ⅜ inch. If the same volume of gas were forced through the numerous 10—15 micro-meter openings of a diffuser, an increase in CO2 surface area of several orders of magnitude would result. Additionally, the small bubbles would take longer to rise to the surface, thus prolonging the time of contact between liquid and gas bubbles.
A diffuser offered an obvious opportunity to gain efficiency in the system. However, it would require expensive alterations to the mixer, since adding a diffuser would prevent the same tube from being used to pump out the finished solution. Before having another tube welded and sealed into the mixer, a test was devised to determine what sort of benefits would result from better dispersion of CO2.
Two quantities of deacidification solution were produced: one in the traditional manner with deionized water, and a second in which the water was saturated with CO29 at the start. Both quantities were subjected to bubbling and pressure as described above. Samples were drawn every 20 minutes and titrated using the Taylor test. Figure 2 summarizes the results.
Fig. 2.
Rates of solution of magnesium hydroxide at 23�C and 31 p.s.i. pressure. Note: 150 g solid added to 8 gallons of a) deionized water and b) water saturated with CO2 (Canada Dry salt-free seltzer). CO2 bubbled continuously as described in text. Both samples remained cloudy after two hours.
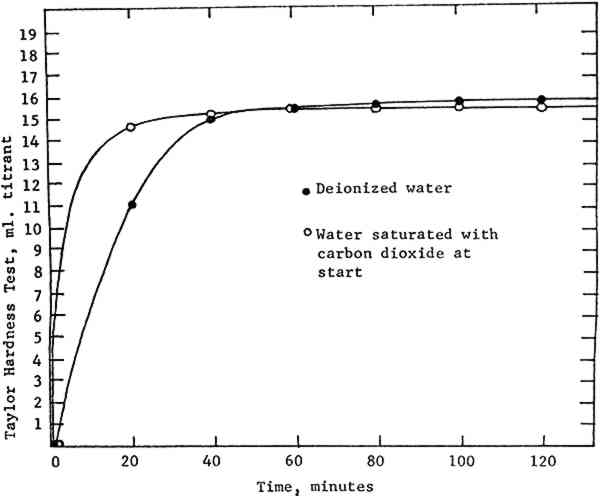 |
As anticipated, the initial reaction rate was significantly faster using carbonated water. However, the “plateau of solubility” or maximum obtainable concentration was roughly the same in both trials. Carbonated water produced a bicarbonate solution of slightly greater clarity than did deionized water, but in both cases some turbidity remained after two hours of bubbling.
Improved CO2 dispersion, then, could shorten the necessary bubbling time, but by itself could not accomplish the task of generating a clear solution of sufficient strength. Modification of our present equipment to accommodate a diffuser was thus judged to be not worthwhile, though such a device should be considered in the design of new systems.
|