THE CONSERVATION OF GEORGE WASHINGTON'S REVOLUTIONARY WAR CAMPAIGN MARQUEES
Fonda Ghiardi Thomsen, & Louise Cooley
5 TREATMENT
5.1 Washing
The same procedure was used for washing both fabrics. Because of the immense size of the pieces, washing was done in a twelve by sixteen foot by six inch, polyethylene-lined plywood tank on the front lawn of the laboratory, as shown in Figure 2. The fabric was sewn between two, twelve by eighteen foot sheets of polypropylene screening5 for handling. Deionized water, on tap from the laboratory, was used for the entire procedure. The water temperature remained around 24� centigrade since it was coming from a large holding tank. The washing consisted of an initial soaking, a wash in 0.1 percent Orvus neutral anionic detergent,6 then consecutive rinse baths as needed. One liter water samples were taken at the start and completion of each soak cycle to monitor pH and anionic detergent levels, as shown in Figure 3. A neutral anionic detergent was chosen for washing both fabrics because it would enhance wetting yet could be monitored to determine the exact amount of rinsing necessary. In that area of West Virginia, contamination from air pollutants is minimal. Weather reports were watched closely. A twenty-four hour guard was employed, and the tank was covered with black polyethylene during prolonged soaking outside.
Fig. 2.
Historic fabric in the washing tank
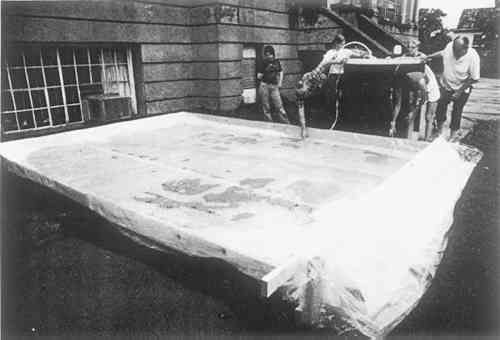 |
Fig. 3.
pH values and anionic detergent levels of the water during treatment. pH tests were done with Beckman Zeromatic SS-3 meter using a silver-silverchloride glass electrode. Anionic detergent level tests were done with a visocolor kit for anionic detergents distributed by Gallard-Schlesinger Chemical Manufacturing Corp., Carle Place, NY.
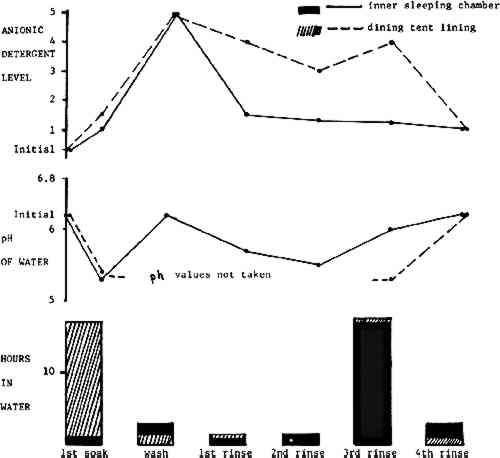 |
5.2 Drying
Two criteria governed the drying of these unwieldy pieces of fabric: (1) elimination of the weight of the water, and (2) drying of the fabric as rapidly as possible. There was no area within the building large enough to dry the fabrics completely opened out. Therefore, on a clear day, after the final rinse, each was laid out on six mil black polyethylene sheeting, on the sloping portion of the lawn to provide rapid drainage. This procedure gave the staff the opportunity to straighten warps, wefts, and seams, and remove as much additional water as possible with a neutral blotting paper, as shown in Figure 4. The fabric was refolded onto the washing screen, carried into the building and suspended on the screen from the ceiling of one of the laboratories, as shown in Figure 5. Dehumidifiers were used to reduce the relative humidity to fifty-five percent. Two large fans were run to circulate the air. The inner sleeping chamber was outside during drying about one and one-half hours. Complete drying inside was accomplished within six hours. The thinner dining tent lining was outside about forty-five minutes. Drying was completed inside within two hours. It is considered that the benefits derived from this outdoor drying far outweighed any theoretical damage which might have accrued by this somewhat unorthodox method of drying.
Fig. 4.
Inner sleeping chamber folded out on the sloping lawn for the first stage of drying
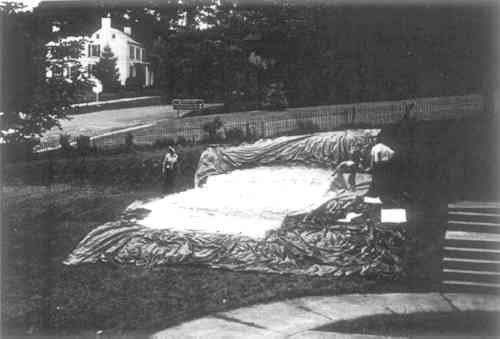 |
Fig. 5.
Historic fabric on the screen suspended from the laboratory ceiling for final stage of drying
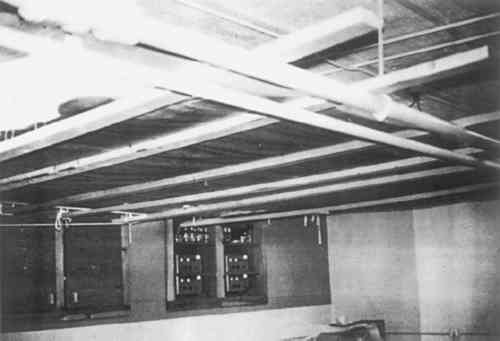 |
5.3 Backing
The fabrics were in a weakened condition. It was mandatory that they both be supported on the underside before rehanging on exhibit.
5.3.1 Inner Sleeping Chamber
A one hundred percent linen fabric7 of approximately the same weight as the original, but with a plain weave, was purchased. Even though the original fabric was a twill, a twill backing would have permitted diagonal stressing to occur to the original fabric. A plain weave was selected to give uniform support in both the horizontal and vertical directions. One hundred percent cotton thread was used for the stitching. The backing fabric was washed and ironed at a commercial laundry, under the supervision of the conservators, to preshrink and remove size.
5.3.2 Dining Marquee Lining
A two hundred count/square inch, one hundred percent cotton,8 plain woven sheeting, one hundred twenty inches wide, in the greige (unbleached), was obtained for the backing. Even though the original fabric was a lightweight wool, a stronger fabric was needed to support such a large area. The cotton provided the strength yet was lightweight enough to match the body of the original fabric. After washing to remove size, the cotton was dyed commercially9 to a mustard green color compatible with the present appearance of the original fabric.
Three, thirty-foot lengths of linen were sewn together along their selvage edges to form the backing for the sleeping tent. Four, twenty-foot lengths of cotton were sewn widthwise for the dining tent backing. A framework, similar to tapestry repair frames used by the Mobilier Nationale at Gobelins in Paris, was constructed to permit the backing to be smoothly attached to each tent. The frame consisted of two, twenty-six foot long, parallel, friction-braked, aluminum rollers10 for holding the stretched backing, and a third roller of cardboard for supporting the historic fabric, as shown in Figure 6. With the backing tensioned between the two rollers, the historic fabric was unrolled a little at a time, laid across the stretched backing, and fixed into place by sewing, as shown in Figure 7. Four women were trained and supervised in this work by Mrs. Cooley. Heavy duty, one hundred percent cotton thread was used for stitching. All holes were sewn to the backing around their inner perimeters with a span stitch. The entire surface of the historic fabric was sewn into place by rows of one inch tent stitches, about three to four inches apart, across the width. Patches were left intact except where they interfered with the natural lay of the fabric.
Fig. 6.
Framework used for backing the historic fabrics
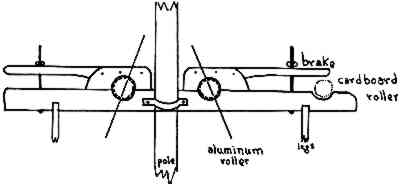 |
Fig. 7.
Historic fabric being sewn to backing
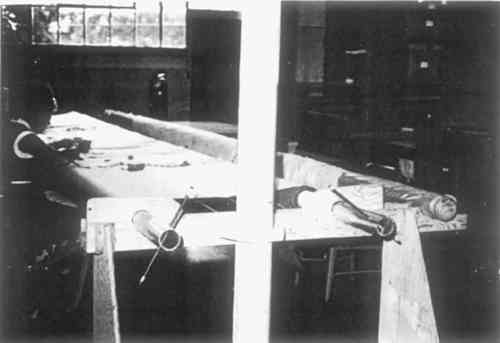 |
|