AN EVALUATION OF FOUR BARRIER-COATING AND EPOXY COMBINATIONS IN THE STRUCTURAL REPAIR OF WOODEN OBJECTS
LISA ELLIS, & ARLEN HEGINBOTHAM
ABSTRACT—Barrier coatings are widely used in conservation to add a measure of reversibility to an otherwise irreversible adhesive bond. Barrier materials are applied as thin films to mating surfaces prior to application of a primary (irreversible) adhesive. Subsequently, if reversal is required, the barrier layer can be softened or dissolved, releasing the bonded joint. This investigation was undertaken to determine the suitability of two synthetic resins for use as barrier layers in the bonding of wood with epoxy. The two materials in question, Paraloid B-72 and Paraloid B-67, were chosen because of their potential to be practically reversible in low-polarity solvents. The two polymers were compared, as barrier materials, to two proven barrier coatings, hide glue and Butvar B-98, by measuring their strength in shear according to ASTM D905-98. Investigations were also undertaken to determine the amount of time necessary for barrier layers to dry prior to application of epoxy. Finally the practical reversibility of the barrier coatings was empirically evaluated. Paraloid B-72 was found to be a suitable barrier material in all respects, while Paraloid B-67 failed both strength and reversibility tests.
TITRE—Une �valuation de quatre mat�riaux employ�s comme couche isolante lors des r�parations structurelles d'objets en bois � l'aide de colle �poxyde. R�SUM�—Les couches isolantes sont tr�s souvent utilis�es en restauration pour aider � la r�versibilit� d'un lien adh�sif autrement irr�versible. Le mat�riau s�lectionn� est appliqu� en un mince film sur les surfaces � coller avant l'application de l'adh�sif (irr�versible). �ventuellement, s'il y a besoin de d�faire ce lien adh�sif, la couche isolante pourra �tre ramollie ou dissoute de fa�on � d�tacher les pi�ces. Cette recherche a �t� entreprise dans le but d'�valuer l'efficacit� de deux r�sines synth�tiques lorsqu'elles sont employ�es comme couche isolante lors de la r�paration d'objets en bois avec de la colle �poxyde. Les r�sines Paraloid B-72 et Paraloid B-67 ont �t� s�lectionn�es car elles demeurent solubles dans des solvants peu polaires. Les deux r�sines ont �t� compar�es � deux autres mat�riaux ayant d�j� fait leur preuve comme couches isolantes, soit la colle de peau et le Butvar B-98, en mesurant leur r�sistance au cisaillement selon le standard ASTM D905-98. Des recherches ont �galement �t� men�es pour d�terminer le temps de s�chage requis avant l'application de la colle �poxyde. Finalement, la r�versibilit� a �t� �valu�e de fa�on empirique. Les r�sultats d�montrent que le Paraloid B-72 peut servir ad�quatement comme couche isolante, tandis que le Paraloid B-67 donne des r�sultats non-satisfaisants au niveau de la r�sistance du lien et de sa r�versibilit�.
TITULO—Evaluaci�n de cuatro recubrimientos de barrera y combinaciones de epoxi en la reparaci�n estructural de objetos de madera. RESUMEN—Los recubrimientos de barrera son ampliamente usados en conservaci�n para agregar una medida de reversibilidad a lo que de otro modo ser�a una uni�n adhesiva irreversible. Los materiales de barrera son aplicados en forma de pel�culas delgadas a las superficies que se van a unir, previo a la aplicaci�n de un adhesivo primario (irreversible). Si posteriormente se requiere que esta uni�n sea reversible, la capa de barrera puede ser ablandada o disuelta, liberando la uni�n as� adherida. Esta investigaci�n fue efectuada para determinar si dos tipos de resinas sint�ticas son apropiadas como capas de barrera en la uni�n de madera con adhesivo ep�xi. Los dos materiales en cuesti�n, Paraloid B-72 y Paraloid B-67, fueron escogidos por tener el potencial de ser reversibles en la practica, en solventes de baja polaridad. Los dos pol�meros fueron comparados, como materiales barrera, con dos recubrimientos de barrera ya probados: cola animal y Butvar B-98, midiendo su fuerza de rotura, de acuerdo a la norma ASTM D905-98. Se efectuaron, adem�s, investigaciones para determinar el tiempo de secado que necesitan las capas de barrera previo a la aplicaci�n del adhesivo epoxi. Finalmente, fue evaluada emp�ricamente la reversibilidad pr�ctica de las capas de barrera. Se encontr� que el Paraloid B-72 es un material de barrera apropiado en todos los aspectos, mientras que el Paraloid B-67 fall� en las pruebas de fuerza y de reversibilidad.
T�TULO—Uma avalia��o de quatro revestimentos de prote��o e combina��es de ep�xi no reparo estrutural de objetos de madeira. RESUMO—Revestimentos de prote��o s�o amplamente usados em conserva��o para aumentar o grau de reversibilidade de uma ader�ncia, de outro modo, irrevers�vel. Materiais de prote��o s�o aplicados como finas pel�culas para unir superf�cies antes da aplica��o de um adesivo principal (irrevers�vel). Posteriormente, se a revers�o for necess�ria, a camada de prote��o pode ser amolecida ou dissolvida, liberando a jun��o. Esta pesquisa foi realizada a fim de determinar a conveni�ncia do uso de duas resinas sint�ticas como camadas de prote��o na ader�ncia de madeira com ep�xi. Os dois materiais em quest�o, Paraloid B-72 e Paraloid B-67, foram escolhidos por seu potencial de reversibilidade em solventes de baixa polaridade. Os dois pol�meros, enquanto materiais de prote��o, foram comparados a dois revestimentos de prote��o testados, cola animal e Butvar B-98, atrav�s da medi��o de sua for�a de ades�o, de acordo com ASTM D905-98. Tamb�m foram feitas pesquisas para determinar o tempo necess�rio para as camadas de prote��o secarem antes da aplica��o de ep�xi. Finalmente, a reversibilidade pr�tica dos revestimentos de prote��o foi empiricamente avaliada. Paraloid B-72 revelou-se um material de prote��o apropriado em todos os aspectos, enquanto Paraloid B-67 falhou em ambos os testes de resist�ncia e reversibilidade.
1 INTRODUCTION
In the conservation of wooden artifacts, it is often necessary to repair broken wooden elements that serve a structural or load-bearing function. Such repairs must have high strength, yet be reversible in the future. Where the break in question is recent and the mating surfaces are clean and undisrupted, animal hide glue is widely believed to be a suitable adhesive, though, in practice, reversal of intact hide glue bonds can be problematic. In cases where the mating surfaces are dirty or damaged, or a gap-filling adhesive is needed, animal hide glue may have greatly reduced strength, and an alternative adhesive may be required. Bulked epoxy resins have found wide use in such instances, and some have the advantage that after setting they can be carved, sawn, sanded, and finished, allowing them to be used simultaneously as both adhesive and fill material. These qualities, along with their high strength, can recommend the use of bulked epoxies over laboratory-prepared acrylic adhesives such as Paraloid B-72 bulked with glass microspheres or fumed silica. One commercially available bulked epoxy, widely used by furniture conservators, is Araldite 1253, a carvable paste epoxy, bulked with titanium dioxide, amorphous silica, iron oxide, and phenolic resin (Ciba 2001). The primary disadvantage of using epoxies in conservation is that, once cured, the bonds formed can be extremely difficult to reverse due to the insolubility of the cross-linked polymer in solvents.
Barrier coatings add a measure of reversibility to adhesive bonds that might otherwise be impossible to release. They are applied as thin films to mating surfaces prior to the application of the difficult-to-reverse primary adhesive. In the conservation of wooden artifacts, animal hide glue has been used as a barrier material for epoxy joins due to its high strength, its ease of use, and its familiarity among furniture conservators. Hide glue, however, has certain disadvantages when used as a barrier material. First and foremost, it is not always reversible in a safe and practical manner. Reversal depends on moisture and/or heat, both of which can cause damage to wood and associated finish materials. Some promising work has been reported using microwave radiation to reverse hide glue bonds (Neher 1996). However, the equipment necessary is quite expensive, and the technique has not gained wide acceptance. In addition, hide glue is known to weaken when exposed to extremes of humidity (Buck 1990) and may degrade over long periods of time.
Recognizing the difficulty in reversing repairs made using hide glue as a barrier, and seeking an appropriate alternative, Anderson and Podmaniczky (1990) tested the suitability of Butvar B-98 (polyvinyl butyral) as a barrier layer for epoxy joins in wood. Butvar B-98 is often referred to simply as a polyvinyl butyral, but it is actually a copolymer of polyvinyl butyral, polyvinyl alcohol, and polyvinyl acetate in a ratio of approximately 40:10:1 (Horie 1987, 101– 2; Monsanto 1994). This polymer was recently shown experimentally by Spirydowicz et al. (2001) to be a suitably stable material for the consolidation of dry archaeological wood. Reporting on the results of their testing, Anderson and Podmaniczky (1990) noted that while barrier coatings should help make epoxy repairs more easily reversible, they must also maintain the overall strength of the bond. The results of their work demonstrated that Butvar B-98 dissolved in ethanol is a suitably strong barrier material when used in conjunction with the bulked epoxy Araldite 1253.
Butvar B-98, while a good alternative to hide glue as a barrier material, nevertheless has significant limitations with regard to its reversibility; it is soluble in polar solvents such as alcohols and in certain mixtures of polar and nonpolar solvents (Monsanto 1994; Spirydowicz et al. 2001). Unfortunately, many varnishes and paints used traditionally to coat wooden artifacts are also sensitive to this range of solvents, making it difficult or impossible to dissolve a Butvar B-98 barrier layer without damaging an adjacent surface coating. This is particularly true because extended exposure may be necessary to allow the solvent (present as either a liquid or vapor) to penetrate deep into the repair and dissolve the barrier. Even after Anderson and Podmaniczky's important study, therefore, a need remained for a well-tested barrier coating of high strength that could be reversed in low-polarity solvents.
In this study, the authors chose Paraloid B-72 and Paraloid B-67 for comparison with the other proven barrier adhesives because they have advantageous dissolution properties, they are readily available, and they are well known and widely used by conservators. Paraloid B-72, a copolymer of ethyl methacrylate and methylacrylate, formerly known as Acryloid B-72, is a Feller Class A material and is not known to become insoluble or degrade over time (Horie 1987, 106). Its inclusion in this study seemed obvious: it is a mainstay in the conservator's studio, and its strength, when used in combination with epoxies in the bonding of stone, has recently been clearly established and published by Podany et al. (2001). In addition, it is soluble in a wide range of solvents, ranging from low-polarity solvents such as xylenes to highpolarity solvents such as acetone. In the context of wooden artifacts conservation, this property confers the significant advantage that a barrier layer of Paraloid B-72 could be applied in acetone—a solvent that is fast-drying and low in toxicity, while remaining reversible in xylenes, a solvent that will not dissolve or damage most associated historic furniture finishes or paints.
Paraloid B-67, polyisobutyl methacrylate, formerly known as Acryloid B-67, is also considered a Feller Class A material even though it is known to cross-link over time (Horie 1987, 108). It was considered in this study because it is reversible in lowaromatic hydrocarbons that present less of a health hazard than the fully aromatic solvents necessary to reverse Paraloid B-72.
The authors conducted comparative shearstrength testing using Araldite 1253 bulked epoxy with all four of the mentioned barrier coatings (hide glue, Butvar B-98, Paraloid B-72, and Paraloid B-67). Results were compared with the measured strength of Araldite 1253 used without a barrier coating. It was hoped that if Paraloid B-72 or Paraloid B-67 proved to be of comparable strength to the other two proven barrier materials, the results of this work would provide conservators with more options in choosing a barrier coating when factors such as the solubility of an original finish need to be considered. To confirm that the adhesive bonds using barrier layers were in fact reversible, the authors also conducted empirical reversibility testing.
2 METHODOLOGY
This study was organized into four components. First, a barrier application protocol was established, and the amount of time required for barrier layers to dry was determined experimentally. Second, the shear strength of adhesive bond made with Araldite 1253 epoxy and each of the barrier materials, as well as that of the Araldite 1253 alone, was determined quantitatively according to ASTM D905-98 (ASTM 2001c). Third, the patterns of failure in the test samples were analyzed. Both strength testing and failure analysis were conducted according to ASTM standard D905-98. Fourth, the practical reversibility of the barrier materials was tested empirically.
2.1 BARRIER APPLICATION PROTOCOL
The following solutions of barrier materials were chosen for testing:
- 10% (w/v) solution of Butvar B-98 in ethanol
- 17% (w/v) solution of Paraloid B-72 in acetone
- 17% (w/v) solution of Paraloid B-67 in Shell Mineral Spirits 135
- Titebond Liquid Hide Glue direct from manufacturer's container
The solutions were formulated as such for two reasons: they needed to be concentrated enough to leave a significant amount of material on the surface of the wood, but they also had to be applied in a continuous, even coat with a brush. Anderson and Podmaniczky used a 20% (w/v) solution of Butvar B-98 in ethanol in their study. In our experience, however, this mixture proved too viscous to brush on conveniently, and a concentration of 10% in ethanol was used instead. The 17% solution of Paraloid B-72 (w/v) in acetone was chosen because it had been used successfully in the 2001 study by Podany et al. and was found to be easy to apply. The 17% solution of Paraloid B-67 in Shell Mineral Spirits 135 was chosen to be comparable to the Paraloid B-72 solution. The Titebond hide glue was chosen because it is widely available in a reasonably standardized formulation and was found to be of a strength comparable to typical hot animal hide glues in moderate humidity environments (Buck 1990). While some contest the comparability of hot and liquid hide glues (Podmaniczky 2003), it was assumed that for the purposes of this study the liquid hide glue could be considered generally representative of the highly variable class of collagen-based glues. The viscosity of the liquid hide glue was found to be suitable directly from the manufacturer's bottle.
The barrier coatings were applied as consistently as possible to samples of hard maple similar to those called for in the ASTM shear-strength testing method. For each kind of coating, a new brush was dipped into the jar containing the solution; the bristles were then brushed against the rim of the jar; and the brush was flipped over and excess solution brushed away. The sample was then brushed once along its length and again across the grain. The coatings applied this way appeared to completely saturate the surface of the wood, leaving no bare or dry areas.
After the first application had dried, the barrier coatings were examined. While the hide glue layer appeared coherent and glossy over the entire surface, the three synthetic resin layers did not; therefore, a second coat of each synthetic resin was applied over the first. Upon drying, all three of these samples appeared to have a reasonably thin yet coherent and glossy film over the test surface. We therefore decided that in preparing the sample blocks for shear-strength testing, the hide glue barrier layer would be applied in a single layer, while the three synthetic resins would be applied in two layers.
2.2 SOLVENT EVAPORATION FROM THE BARRIER COATINGS
We next tried to determine the length of time required for the barrier layers to dry, prior to the application of the epoxy adhesive. It is generally accepted that there should be little to no solvent remaining in the coating, as retained solvent can act as a plasticizer within the resin and thus weaken the barrier film (Podany et al. 2001, 27).
2.2.1 TESTING METHOD
A simple test was designed to establish when the solvent had evaporated from barrier layers. Small wafers of hard maple (the wood called for in the ASTM shear-strength testing method) were painted with the barrier coatings and then weighed periodically until there was no more significant weight change. The maple was cut into 20 samples measuring approximately 5 x 7.5 x 0.4 cm. Five pieces of wood were set aside to be used as controls to track the changes in weight of the substrate caused by fluctuations in the ambient relative humidity. The 15 remaining samples were divided into three groups. Each group was coated with two coats of the synthetic resin barrier solutions, the second coat following the first by three days. Hide glue was not tested for solvent evaporation time because of anticipated complications due to its continual weight change with fluctuations in ambient relative humidity. Changes in weight for all 20 samples were recorded in the same order, using an Ohaus Precision Standard scale, which is accurate up to 1 mg (0.001 g). Since the weight of solvent added in each coat was typically about 0.3 g, the scale was effectively accurate to approximately 0.3% for measuring solvent loss. The five wafers of each group were weighed individually, and their weights were then averaged. Initially, weight measurements were taken every half hour. The interval between measurements increased with time until, five days after the second application of barriers, measurements were taken twice a day. We felt that once the weight stopped changing measurably, it could be concluded that the barrier adhesives were essentially free of solvent.
To better understand the dynamics of solvent evaporation from wood substrates, the same test was carried out using two different substrates, Douglas fir wood and 4 mil Mylar polyester film (essentially nonabsorbent). These results were compared to those recorded for hard maple.
2.2.2 Results of Solvent Evaporation Tests
The solvent evaporation testing on maple showed that all three nonaqueous barrier-coating materials would be essentially solvent free within five days of the application of the second coat. As expected, acetone and ethanol, the faster-evaporating solvents, yielded dry films more quickly than the slower-evaporating Shell Mineral Spirits 135. Table 1 shows the times required for the 98% and 100% evaporation of solvent from the second coat of barrier solution. Based on this result, sample blocks of maple that had been coated with the barrier layers and allowed to dry for three days, then recoated and allowed to dry for five days, were considered suitable for strength testing according to ASTM standards.
Two interesting phenomena were observed during evaporation testing. First, it became clear that the nature of the substrate played a large role in the evaporation rate of solvent from the resin layer. Figures 1 and 2 illustrate the extremely different evaporation rates for three different substrates when initially coated with resin solutions. Figure 1 shows the progress of drying for the first coat of 17% (w/v) Paraloid B-72 in acetone when applied to Mylar, maple, and Douglas fir test panels. On the Mylar substrate, which is essentially nonabsorbent, over 99% of the solvent applied had evaporated within one minute. In contrast, on the test wafers of maple, a dense and even-grained wood, it took approximately 21 hours for 98% of the solvent to evaporate. With the fir substrate, which is lighter than maple and has distinct hard and soft zones in each annual ring, it took approximately 29 hours for 98% of the solvent in the first coat to evaporate. Figure 2 shows the progress of drying for 17% (w/v) Paraloid B-67 in Shell Mineral Spirits 135 (a much slower-evaporating solvent than acetone) on the same three substrates. On the Mylar substrate, 98% of the solvent applied had evaporated after only 1 hour and 40 minutes. On the test wafers of maple, it took approximately 60 hours for 98% of the solvent to evaporate, and with the fir substrate, it took over 91 hours for 98% of the
Table .
Time Required for Solvent Evaporation from Second Coat of Barrier Material on Hard Maple Substrate
 |
solvent to evaporate. It is interesting to note that in the drying curves for Paraloid B-67 on maple and fir substrates, the fir samples initially dried more quickly than the maple samples but were overtaken by the maple after about a day. The cause of this phenomenon is unknown, but it suggests that the mechanisms of solvent evaporation from wooden substrates are complex and may depend on a wide range of variables, such as the anatomical characteristics of the wood, interactions with bound water in the wood, the condition of the wood surface, the affinity of the particular solvent for both the resin and the wood, the volatility of the solvent, and the film thickness.
The second phenomenon noted during evaporation testing was that, on wooden substrates, the first and second coats of resin solutions dried at different rates. With the fast-evaporating solvents, acetone and ethanol, the second coat of barrier material clearly dried more quickly than the first. Presumably this is because the first layer of resin seals the wood, so that when the second coat is applied, the solvent is not absorbed into the wood to the same degree. Figure 3 shows the percent of solvent evaporated vs. length of time for the first and second coats of 17% (w/v) Paraloid B-72 in acetone applied to maple substrate. While the first coat did not reach 98% evaporation until 21 hours after application, the second coat was 98% dry after only 2.5 hours. In contrast to the results with fast-evaporating solvents, the second coat of barrier in slow-evaporating mineral spirits dried more slowly than the first. Figure 4 shows the percent of solvent evaporated vs. length of time for the first and second coats of 17% (w/v) Paraloid B-67 in Shell Mineral Spirits 135 applied to maple substrate. While the drying rates are much more similar than with Paraloid B-72 in acetone, it is clear from the graph that the first coat evaporated more quickly than the first. This result presumably indicates that some of the solvent in the second coat penetrated the first coat and was absorbed into the wood. The increased overall thickness of resin after the second coat may then have contributed to an overall slower drying of the coating layer.
The degree to which barrier layers on wood should be allowed to dry before final assembly with
Fig. 1.
Evaporation of solvent from 17% (w/v) Paraloid B-72 in acetone applied to three different substrates
 |
Fig. 2.
Evaporation of solvent from 17% (w/v) Paraloid B-67 in Shell Mineral Spirits 135 applied to three different substrates
 |
Fig. 3.
Comparison of solvent evaporation rates from the first and second coats of 17% (w/v) Paraloid B-72 in acetone when applied to hard maple
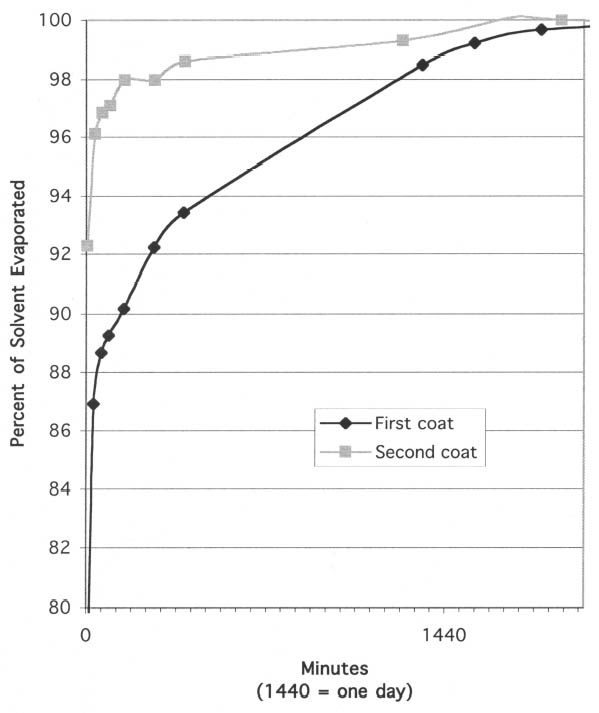 |
Fig. 4.
Comparison of solvent evaporation from the first and second coats of 17% (w/v) Paraloid B-67 in Shell Mineral Spirits 135 when applied to hard maple
 |
epoxy is difficult to judge with certainty. Both for convenience and because contamination of the surface by airborne pollutants could result in a weakened bond, it is better to close joints soon after the surfaces are prepared. However, premature bonding when using barrier coatings could result in a joint that is initially weak due to placticizing effects of retained solvent. It might also result in bonds that are weakened even after the eventual drying of the solvent (the retained solvent could impair the bonding of the epoxy to the resin, or the shrinkage of the resin film during drying could cause internal stresses within the joint). Based on our results, it should also be considered that when applied to wood, a significant portion of the solvent may be retained, not in the resin layer but in the wood itself. In this case, any remaining solvent would not be likely to contribute to plasticizing or weakening the barrier layer. In any event, more testing is clearly warranted to determine the relationship between solvent retention and the strength of barrier coatings on wood substrates.
2.3 STRENGTH TESTING
Unfortunately, there is no ASTM standard for determining the strength of combinations of barrier coatings and adhesives. Where possible, this study used the testing methodology as specified by ASTM D905-98, “Standard Test Method for Strength Properties of Adhesive Bonds in Shear by Compression Loading,” and modifications were made where necessary. Modifications were in some cases based on those made by Podany et al. in their 2001 study and by Anderson and Podmaniczky in 1990.
2.3.1 Determination of Specific Gravity
ASTM D905-98 specifies the use of hard maple for shear-strength testing of adhesives. It further stipulates that the maple used fall within a certain range of specific gravity. To measure the specific gravity of the maple obtained for this test, two small pieces of the wood were oven-dried, according to the specifications of ASTM D143-94 (2001b), “Standard Test Methods for Small Clear Specimens of Lumber.” The two samples were weighed and then placed in an oven at 103�C until their weight loss ceased changing. The moisture content of the wood was then determined by dividing the samples' loss in mass by the oven-dry mass. These results were used to calculate the specific gravity of the blocks as shown in Appendix X1 of ASTM D905-98 (ASTM 2001c, 25). The specific gravity of the hard maple stock fell in an acceptable range.
2.3.2 Sample Preparation
The size of the samples specified by ASTM D905-98 was too large for the Getty Conservation Institute's Instron tensile-testing machine, which is limited by a 10 kilonewton (kN) load cell. Based on the ultimate strength of trial samples of different sizes prepared for this purpose, it was calculated that the machine would be able to run samples of approximately one-quarter of the specified size. The final configuration of the test blocks (fig. 5) results in a bond area of 1 sq. in.
The 3/4 in. x 9 1/4 in. hard maple stock was cut into 1 1/4 in. strips across the grain on a table saw. Surfaces to be glued were prepared by sanding lightly with 320 grit abrasive paper. The wooden strips were divided into five groups, four of which were coated on one face with each of the respective barrier materials in the manner described in section 2.1. The fifth group was not coated with any barrier material and served as a control. After drying, pairs of strips from each group were bonded together using Araldite 1253 in the manner described below. The two components of the epoxy were measured before mixing by weight according to the product data sheet, provided by manufacturer Vantico (Vantico Inc. 2002), which specifies the optimal resin: hardener weight ratio at 100:82.
One of the strips, already coated with the barrier, was covered with the epoxy paste and laid, faceup, in a jig built for this experiment. The second strip was placed into the jig above the first, overhanging by approximately a quarter of an inch. The upper strip was pushed down in the jig so that the adhesive layer measured 0.030 in. or 30 mils thick. This adhesive-layer thickness was chosen to approximate a typical gap-filling bond as might be required in wooden artifacts conservation. The samples were removed from the jig and left to cure for eight days. Excess epoxy was removed from the edges of the strips, first using a shoulder plane.
Fig. 5.
Dimensions of hard maple samples prepared for shear-strength testing
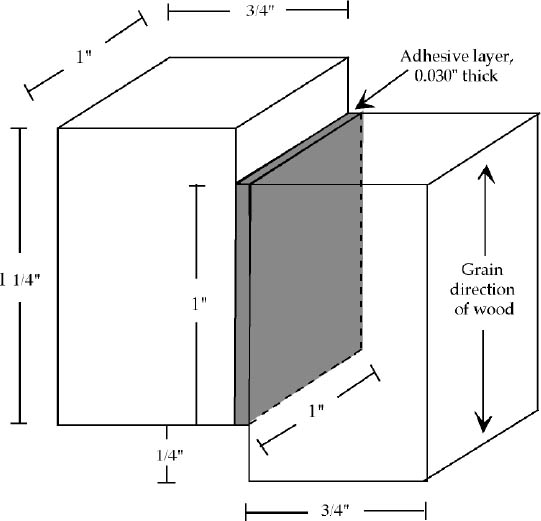 |
Some suggest that the bond between glue and epoxy may be strengthened if the epoxy is applied before the glue is completely dry or if the surface of the dried glue is scuffed prior to application of the epoxy (Podmaniczky 2003). The sample blocks prepared with a hide glue barrier layer for this study, however, were assembled after the glue had thoroughly dried, without any surface preparation.
Once the samples had been cleaned of excess adhesive, the bonded wooden strips were then cut into smaller pieces, approximately 1 in. wide, on a table saw. Ten small test blocks were prepared and labeled for each barrier material. The bond area of each sample block was then calculated by measuring the width and length of the bonded area. These data were recorded for use in determining the final load at failure for each test block.
2.3.3 Shear-Strength Measurement
The samples were tested in batches according to sample type by the same operator during a four-hour run. The samples were held in sealed polyethylene bags until just before testing. Ten samples per sample type were run. Both parts of each sample were labeled in pencil according to adhesive type and numbered in sequence for post-testing analysis of the break edge.
A Model 4201 Instron with a 10 kN load cell, belonging to the Getty Conservation Institute, was used to test the samples (fig. 6). Instron Series IX Automated Materials Tester software, version 8.06.00, was used to run the tests and to partially analyze the data. Before each sample was run, the operator entered the width and thickness of each sample. The Instron's moving crosshead was configured to push down on one of the two bonded sample blocks while the other was held in a fixed position, creating a shear stress on the adhesive bond (fig. 7). The crosshead was set to move down at a constant rate of 5 mm per minute, the ASTM standard specified speed, until the sample failed.
For each sample, the Instron Series IX Automated Materials Tester software then calculated the maximum load, displacement of the crosshead at maximum load, and stress at maximum load, as well as the mean and standard deviation of the samples grouped together. The software also produced graphs showing these results.
The quantitative results of the Instron testing were then subjected, by group, to the “Q” test for outliers at the 90% confidence level. This test is part of ASTM E178-94 (2001a). The test considers the number of samples and the distribution of the results. Any individual result deemed incompatible with the spread of the others is excluded within a determined confidence level.
2.3.4 Results of Shear-Strength Testing
Table 2 and figure 8 show the results of the Instron shear-strength testing. Araldite 1253 epoxy bonds prepared with Butvar B-98 and Paraloid B-72 barrier layers proved to be as strong as or stronger than bonds prepared with no barrier. Bonds prepared with liquid hide glue barrier layers were weaker on
Fig. 6.
The Instron Model 4201 with 10 kN load cell at the Getty Conservation Institute
 |
Fig. 7.
Detail of the Instron's crosshead with a sample in place
 |
average, but nearly as strong as bonds with no barrier, while bonds prepared with Paraloid B-67 barrier layers were much weaker than any other type. These results indicate that Butvar B-98, Paraloid B-72, and liquid hide glue barrier layers yield high-strength epoxy bonds and can be considered suitable barrier materials for use with wood and epoxy adhesive. Conversely, the use of Paraloid B-67 was shown to result in consistently weak bonds and to be clearly unsuitable for use as a barrier material. The failure of Paraloid B-67 to produce a sufficiently strong bond was disappointing, since it could have provided a barrier method reversible in solvents of low polarity—safe for objects, and, with low toxicity, safe for conservators. This failure may be directly related to the low polarity of the Paraloid B-67 polymer. It may be that epoxy resin, which is a highly polar material (Down 2001), is unable to bond satisfactorily to such a low-polarity material. This hypothesis is supported by the fact that 100% of failure occurred between the Paraloid B-67 and epoxy layers (see below, sec. 2.4). If this outcome is in fact the case, then the search for a strong barrier material soluble in low or nonaromatic solvents may be inherently unlikely to succeed.
2.4 FAILURE ANALYSIS: ESTIMATED PERCENTAGE WOOD FAILURE
ASTM D905-98 specifies that an estimated percentage wood failure be calculated. In a simple adhesive-testing scenario, this calculation serves to distinguish between areas in which the adhesive has failed and areas where the substrate has failed. This study, however, presented a more complex situation than anticipated by ASTM standards because of the use of the barrier coatings. The control samples prepared with simple epoxy bonds were analyzed according to the ASTM standard. For samples prepared with barrier adhesives, failure was divided into the following four groups:
- wood failure, wherein wood was removed from one of the faces of the wooden sample
- barrier coating–wood failure, meaning that the barrier coating was pulled from the wooden face, sometimes, but not always, taking tiny wood fibers along with it
- barrier coating–epoxy failure, where the join failed in the interface between the two
- epoxy failure, where the epoxy adhesive was pulled apart, and remains were found on both faces of the sample.
For all samples, the percentage failure of each type per sample was defined using a gridded, transparent plastic ruler (fig. 9). The grid, which divides square inches into 254 units, was placed on top of each bond surface after failure and examined under a stereomicroscope. The number of square units in which each type of failure occurred were counted, and the percentage of failure for each type was calculated.
In the event that an epoxy bond on a wooden artifact is stressed to the point of failure, it is preferable that the adhesive break away cleanly from the substrate without causing additional damage to the wood. The results of the failure analysis, shown in table 3, indicate that all four barrier materials tested offer some protection to the underlying wood by reducing wood failure when the bond is broken. Wood failure, which was 6.8% for wood bonded directly with epoxy, was reduced to nil or virtually nil when any of the four barriers was used. Butvar B-98 and liquid hide glue samples tended to fail at the interface between the epoxy and the barrier layer, while Paraloid B-72 tended to fail at the interface between the wood and the barrier. Paraloid B-67, which failed the overall strength testing, always failed at the interface between the epoxy and the barrier, indicating that the cause of failure was poor adhesion between the Paraloid B-67 and the epoxy.
Table .
Results of Shear-Strength Testing Using Epoxy Adhesive Alone and with Four Different Barrier Layers
 |
Fig. 8.
Results of Instron shear-strength testing of epoxy bonds with different barrier materials. The graph shows the mean strength of the 10 samples tested and indicating the range of one standard deviation.
 |
2.5 REVERSIBILITY OF BARRIER COATINGS IN SOLVENT VAPORS
To test the reversibility of the barrier coatings, spare sample blocks of maple, coated with the barriers, were bonded to one another using Araldite 1253. The three barrier materials reversible in organic solvents (Paraloid B-72, Paraloid B-67, and Butvar B-98) were tested for reversibility in solvent vapor chambers with no direct application of liquid solvent. After the epoxy had cured, brass screws were inserted into the upper and lower pieces of wood. Four large steel washers were suspended from the bottom screws. The total weight of the four washers was approximately 88 grams. The samples were suspended by the upper screws on bamboo skewers lying on the rim of glass beakers, which were enclosed in sealed, clear polyethylene bags (fig. 10). Approximately 2 ml of the appropriate solvent was placed in the bottom of the beakers. Xylenes were used for the sample bonded with Paraloid B-72, ethanol for the Butvar B-98 sample, and Shell Mineral Spirits 135 for the Paraloid B-67 sample.
The Butvar B-98 sample fell apart on its own in three to four days. The Paraloid B-72 sample came apart with gentle pressure after five days in the solvent-rich environment. The Paraloid B-67 coating did not fall apart, even with gentle pressure, after five days, at which point the test was suspended. These results suggest that Butvar B-98 and Paraloid B-72 barrier layers are practically reversible in ethanol and xylenes respectively, even without direct application of liquid solvent. The disadvantages of using ethanol for reversal on objects with painted or varnished surfaces have been discussed above (see sec. 1). While xylenes should be safe to use with many painted or varnished surfaces, they will not be safe with all. Furthermore, the health hazards associated with xylenes makes them a less than ideal choice for barrier reversal. The failure of the Paraloid B-67 barrier layer to be reversed by the vapor of mineral spirits (in which it had previously been dissolved) is somewhat mysterious, though it may be related to the low vapor pressure of the solvent. Had it not been for the failure of Paraloid B-67 to perform adequately in strength testing (see sec. 2.3.4), further testing of more volatile and/or more polar solvents might have been warranted.
Fig. 9.
The gridded, transparent ruler used for failure analysis
 |
Fig. 10.
Empirical reversibility testing using improvised vapor chambers
 |
2.6 MICROWAVE REVERSIBILITY OF HIDE GLUE
The possible utility of microwave technology for reversing hide glue joints has not gone unnoticed, especially by furniture conservators (Neher 1996; Anderson and Podmaniczky 1990). Theoretically, microwave radiation can be used to excite the hide glue's water molecules, heating and weakening the glue line to the point that it either falls apart or comes apart with gentle pressure. In practice, consumer microwave ovens can be used to deliver the microwaves if an object is small enough; otherwise there are hand-held devices (available at considerable expense), such as the WorkRite Wood Welder, that generate radio frequencies for use in industrial applications.
A simple experiment was undertaken to
Table .
Failure Analysis
 |
separate sample blocks that had been bonded with epoxy using Titebond Liquid Hide Glue as a barrier coating. The samples were heated in a microwave oven; some had water injected into the bond line with a very fine syringe. All samples came apart easily after 20–30 seconds. Intentional overexposure in the microwave oven resulted in scorching of the wood blocks, demonstrating that this method of reversal has some potential dangers. Microwave reversal is not suitable for joints in close proximity to metal fasteners or ornaments. While the reversal of hide glue barrier layers with microwave radiation cannot be universally recommended, further study is called for in this area.
3 CONCLUSION
This study demonstrates that Paraloid B-72 is a suitable material for use as a reversible barrier layer for epoxy joins in wood. It offers strength comparable to epoxy used alone as well as to the other proven and widely used barrier materials, Butvar B-98 and hide glue. Like these other barrier materials, Paraloid B-72 appears to offer some protection to underlying wood in the event that the epoxy bond is broken. Additionally, Paraloid B-72 was shown in practice to be a reversible barrier material in xylenes vapor. This quality factor offers advantages over Butvar B-98 and hide glue when making repairs near finished, painted, or otherwise solvent-sensitive surfaces. This study also demonstrates that Paraloid B-67 is not a suitable material for use as a reversible barrier layer for epoxy joins in wood. Paraloid B-67 failed both strength and reversibility tests.
ACKNOWLEDGEMENTS
The authors would like to especially thank the J. Paul Getty Museum's Brian Considine, Jane Bassett, Julie Wolfe, George Johnson, and Mark Mitton of Decorative Arts and Sculpture Conservation for their unstinting support and great help throughout the project; Jerry Podany of Antiquities Conservation for sharing his knowledge and experience with barrier coatings; Stefan Simon of the Getty Conservation Institute for permission to use the institute's equipment, and the institute's Urs Mueller for providing cheerful advice, Instron training, and setup; and Jane Down of the Canadian Conservation Institute for her insight and guidance.
SOURCES OF MATERIALSParaloid B-67, polyisobutyl methacrylateConservation Support Systems Santa Barbara, Calif. 93101 Butvar B-98, polyvinyl butyral resinConservation Support Systems Santa Barbara, Calif. 93101 Ciba Araldite AV 1253, Vantico Inc.Conservation Support Systems Santa Barbara, Calif. 93101 Paraloid B-72, copolymer of ethyl methacrylate and methylacrylateConservation Support Systems Santa Barbara, Calif. 93101 Shell Mineral Spirits 135, slow evaporating, 15% aromatic contentConservation Support Systems Santa Barbara, Calif. 93101 Titebond Liquid Hide GlueFranklin International Columbus, Ohio 43207
REFERENCES
ASTM. 2001a. Standard practice for dealing with outlying observations, E178-94. In Annual book of ASTM standards. Philadelphia: American Society for Testing and Materials.
ASTM. 2001b. Standard test methods for small clear specimens of lumber, D143-94 (reapproved 2000). In Annual book of ASTM standards. Philadelphia: American Society for Testing and Materials.
ASTM. 2001c. Standard test method for strength properties of adhesive bonds in shear by compressive loading, D905-98. In Annual book of ASTM standards. Philadelphia: American Society for Testing and Materials.
Anderson, M. J., and M. S.Podmaniczky. 1990. Preserving the artifact: minimally intrusive conservation treatment at the Winterthur Museum. Papers from the Wooden Artifacts Group, ed. M. J.Anderson. Wooden Artifacts Specialty Group of the American Institute for Conservation of Historic & Artistic Works.
Buck, S. L.1990. A study of the properties of commercial hide glue and traditional hot hide glue in response to changes in relative humidity and temperature. Papers from the Wooden Artifacts Group, ed. M. J.Anderson. Wooden Artifacts Specialty Group of the American Institute for Conservation of Historic and Artistic Works.
Ciba Specialty Chemicals Corp., North America. 2001. Araldite 1253 packaging materials. East Lansing, Mich.
Down, J. L.2001. Review of CCI research on epoxy resin adhesives for glass conservation. Reviews in Conservation2:39–46.
Horie, C. V.1987. Materials for conservation. London: Butterworths.
Monsanto Co.1994. Butvar polyvinyl butyral resin: Properties and uses, pub. 2008084B. St. Louis, Mo.
Neher, A.1996. Radio frequency heating and the reversibility of animal glue in furniture joinery. UKIC Conservation News59:35–37.
Podany, J., K. M.Garland, W. R.Freeman, and J.Rogers. 2001. Paraloid B-72 as a structural adhesive and as a barrier within structural adhesive bonds: Evaluations of strength and reversibility. Journal of the American Institute for Conservation40:15–33.
Podmaniczky, M. S.2003. Personal communication. Furniture conservation department, Winterthur Museum, Winterthur, Delaware.
Spirydowicz, K., E.Simpson, R. A.Blanchette, A.Schniewind, M. K.Toutloff, and A.Murray. 2001. Alvar and Butvar: The use of polyvinyl acetal resins for the treatment of the wooden artifacts from Gordion, Turkey. Journal of the American Institute for Conservation40:43–57.
Vantico Inc.2002. Product data, Araldite AV-1253/HV-1253. Available from Advanced Materials Division, Huntsman Polyurethanes, Everberg, Belgium.
FURTHER READING
Blackshaw, S. M., and S. E.Ward. 1983. Simple tests for assessing materials for use in conservation. In The Proceedings of the Symposium Resins in Conservation, ed. J. O.Tate, N. H.Tennent, and J. H.Townsend. Edinburgh: Scottish Society for Conservation and Restoration. 2.1–2.15.
Bradley, S.1984. Strength testing of adhesives and consolidants for conservation purposes. In Adhesives and Consolidants, ed. N. S.Brommelle et al. London: International Institute for Conservation of Historic and Artistic Works. 22–24.
Down, J. L., J.MacDonald, J.Tetreault, and R. S.Williams. 1996. Adhesive testing at the Canadian Conservation Institute, past and future. Studies in Conservation41:19–44.
Koob, Stephen P.1986. The use of Paraloid B-72 as an adhesive: Its application for archaeological ceramics and other materials. Studies in Conservation31:7–14.
AUTHOR INFORMATION
LISA ELLIS is currently the Sherman Fairchild Fellow at the Museum of Fine Arts, Boston. The work described in this paper was conducted while she was a graduate intern in the Decorative Arts and Sculpture Conservation department at the J. Paul Getty Museum. She has graduate degrees in art history from the University of Toronto and art conservation from Queen's University, Kingston, Ontario, Canada. She has held internships at the Society for the Preservation of New England Antiquities, The Art Gallery of Ontario, Parks Canada, the Institute of Nautical Archaeology's Bodrum Laboratory in Turkey, and the Agora Excavations in Athens. Address: Museum of Fine Arts, Boston, Objects Conservation, 465 Huntington Ave., Boston, Mass. 02115; lellis@mfa.org
ARLEN HEGINBOTHAM is assistant conservator of decorative arts and sculpture at the J. Paul Getty Museum in Los Angeles, California. Since taking an interest in art conservation in 1990, he has worked in several private furniture conservation studios, including most recently Robert Mussey Associates in Boston, Massachusetts. He has also held internships and technician positions at the Yale Peabody Museum of Natural History, the Isabella Stuart Gardner Museum, and the Philadelphia Museum of Art. He received his B.A. in East Asian studies from Stanford University in 1989 and his M.A. in art conservation from Buffalo State College in 1999. Address: Decorative Arts and Sculpture Conservation Department, J. Paul Getty Museum, 1200 Getty Center Dr., Suite 1000, Los Angeles, Calif. 90049-1687; ahegin-botham@getty.edu
Section Index |