CONSERVATION OF A LYRE FROM UR: A TREATMENT REVIEW
VIRGINIA GREENE
ABSTRACT—In 1976, the University of Pennsylvania Museum Conservation Laboratory took apart the gold, silver, and lapis bull head from a Sumerian lyre. The head, excavated in the 1920s, had been previously restored. The head was taken apart and the component parts cleaned, revealing details of the original construction that had never been recorded. The head and beard were reassembled using more modern materials and a complex armature to support the weight of the lapis beard. After 16 years on exhibit, the head was reexamined for a traveling exhibit, and the methods and materials used in the 1970s were evaluated.
TITRE—La restauration d'une lyre provenant d'Ur: un traitement en revue. R�SUM�—En 1976, le laboratoire de restauration du mus�e de l'universit� de Pennsylvanie (University of Pennsylvania Museum) a d�mont� la t�te de taureau d'une lyre sum�rienne, faite d'or, d'argent et de lapis-lazuli, qui avait d�j� �t� restaur�e depuis sa d�couverte lors de fouilles dans les ann�es 20. La t�te fut d�mont�e et ses composantes nettoy�es, r�v�lant ainsi des particularit�s de la construction originale qui n'avaient pas �t� not�es auparavant. La t�te du taureau fut remont�e � l'aide de mat�riaux modernes et d'une armature complexe pour supporter le poids de la barbiche en lapis-lazuli. Apr�s 16 ann�es d'exposition, la t�te fut examin�e en vue d'une exposition itin�rante, et les m�thodes ainsi que les mat�riaux employ�s dans les ann�es 70 furent �valu�s.
TITULO—Conservaci�n de una lira de Ur: revisi�n de un tratamiento. RESUMEN—En 1976, el Laboratorio de Conservaci�n de la Universidad de Pensilvania desmont� una cabeza de toro de una lira sumeria fabricada en oro, plata, y lapisl�zuli. La cabeza, excavada en la d�cada de 1920, hab�a sido restaurada con anterioridad. En 1976 se desarm� la cabeza y se limpiaron sus partes componentes lo que revel� detalles de la construcci�n original que no hab�an sido antes registrados. La cabeza y la barba se volvieron a unir con materiales m�s modernos y a trav�s de una armadura compleja para soportar el peso de la barba de lapisl�zuli. Tras 16 a�os de exhibici�n, la cabeza fue reexaminada previo a una exhibici�n itinerante y los m�todos y materiales usados en la d�cada de 1970 fueron revisados.
TITULO—Conserva��o de uma lira de Ur: an�lise de tratamento. RESUMO—Em 1976, o Laborat�rio de Conserva��o do Museu da Universidade da Pensilv�nia desmontou o ouro, a prata e a cabe�a de touro em l�pis-laz�li de uma lira sumeriana. A cabe�a, escavada nos anos 20, havia sido previamente restaurada. A cabe�a foi separada e as partes que a compunham foram limpas, revelando detalhes da constru��o original que nunca haviam sido registrados. A cabe�a e a barba foram remontadas usando materiais mais modernos e uma complexa estrutura para suportar o peso da barba em l�pis-laz�li. Ap�s 16 anos em exibi��o, a cabe�a foi reexaminada para uma exposi��o itinerante e os m�todos e materiais usados nos anos 70 foram avaliados.
1 BACKGROUND
The site of Ur is located near the Euphrates River in southern Mesopotamia (present-day Iraq). Inhabited from the 4th to the 1st millennium B.C., Ur was one of the southernmost large cities of Mesopotamia, an important administrative and commercial center with substantial facilities for water transport.
Ur was excavated from 1922 to 1934 by a joint expedition of the British Museum and the University of Pennsylvania Museum, directed by C. L. Woolley under a permit granted by the Iraq Antiquities Service. Among the most important areas excavated by Woolley was the Royal Cemetery. The 16 burials he identified as royal tombs all have a chamber of stone or mud-brick set at the bottom of a pit that was approached by a ramp. The pits were filled with the bodies of servants who were sacrificed at the time of the primary burial. The tombs were lavishly provided with tools, weapons, vessels of various kinds, personal ornaments, and musical instruments. The levels in which the royal tombs are located have been dated by carbon 14 to 2600–2500 B.C. (Moorey 1977, 24).
Although many of the objects allocated to the University of Pennsylvania Museum were sent to Philadelphia in “as excavated” condition, several major pieces, including a lyre with a bull head of gold, silver, and lapis lazuli and a frontal plaque of shell set in bitumen, had been restored (figs. 1a, b, see page 246). The bull head, crushed and severely distorted when uncovered (de Schauensee 2001, pl. 30), had been reshaped and provided with an entirely new soundbox, the original having survived only as an impression in the ground. Unfortunately, the dimensions of the restored soundbox did not match the measurements given in the excavation report (Woolley 1934, 70), and the box had been decorated with reproduction inlay modeled after the genuine inlay from another lyre.
When it became possible to have a new soundbox constructed, the head was removed from the old soundbox and brought to the Conservation Laboratory for examination and treatment. Initially there was no thought of taking the head apart; the intent was to clean the surface and make minor repairs.1
2 DESCRIPTION OF THE HEAD
To provide a reference point for the description of the treatment, the materials and original construction of the head are presented first. It must be kept in mind that most of this information was not known at the time the treatment began and was revealed only as the work proceeded. All conclusions relating to the proposed original construction were reviewed and approved by the curatorial staff.
2.1 THE HEAD, EARS, AND HORNS
The front and sides of the head are formed of a single piece of gold sheet, with openings for the eyes, hair, and beard, as well as small holes for pegs that held the ears in place. A second rectangular piece of gold sheet forms the back of the neck, overlapping the front section under the horns (fig. 2a). Two small holes, about 1 mm diameter and 7 mm apart, are visible near the proper right edge of the strip, and there are traces of two similar holes on the left edge. There are matching pairs of holes on the edges of the gold sheet forming the head. No evidence of a support system was found inside the head, which was most likely manufactured by hammering the gold sheet around a solid wood core (palm and poplar wood, among others, were available locally).
Both ears and horns also had wood cores. Each ear was formed of a single piece of gold sheet, with a seam running from the tip of the ear down the upper edge and along the back of the ear near one side. The upper part of the seam was hammered; the lower part, along the back of the ear, was secured with four gold tacks (fig. 2b, see page 246). The tacks remain on the proper right ear; on the left ear only the holes can be seen. Small holes in the gold sheet of the head indicate that the ears were secured to the head with pegs, probably made of wood.
Each horn was also covered with a single piece of gold sheet, with a narrow seam running the length of the horn. The seam was hammered, but no tacks were used to secure the gold to the original core. The horns had short tips made of lapis lazuli, with a narrow, tapering tenon with a crosswise hole (fig. 3a). The tenon on the proper right tip was broken through the hole; the other was undamaged. There is no direct evidence of the method originally used to attach the tip to the horn core, as no wire or other construction technique was found. One possibility is illustrated in figure 3b. A hole would have been carved or drilled in the end of the core to receive the tenon. A pin—possibly organic, as no traces of metal corrosion products were found—was inserted through the wood and the hole in the tenon, securing the tip in place. The gold sheet was then wrapped around the horn core and hammered into place.
The eyeballs were made of shell and lapis lazuli. The latter formed the iris and lids, and the shell formed the white of the eye. The three parts fit closely together when assembled (fig. 4a, see page 247). The tip of the iris element, which faces the rear of the eyeball, has a biconical hole. On the proper left eye, a fragment of mineralized copper alloy wire was found in the hole and another short length of wire on the back of the eyeball assembly. A small amount of black grainy material was visible around the wire,
Fig. 1a.
The bull head as previously restored. The gold, lapis, and shell of the head are original; the “inlay” is plaster. Lapis-bearded lyre from the Royal Cemetery at Ur, ca. 2600-2500 B.C., gold, silver, lapis lazuli, and shell, height of head 35.6 cm. University of Pennsylvania Museum CBS 17694, field U10556.
 |
Fig. 1b.
The frontal plaque of shell set in bitumen
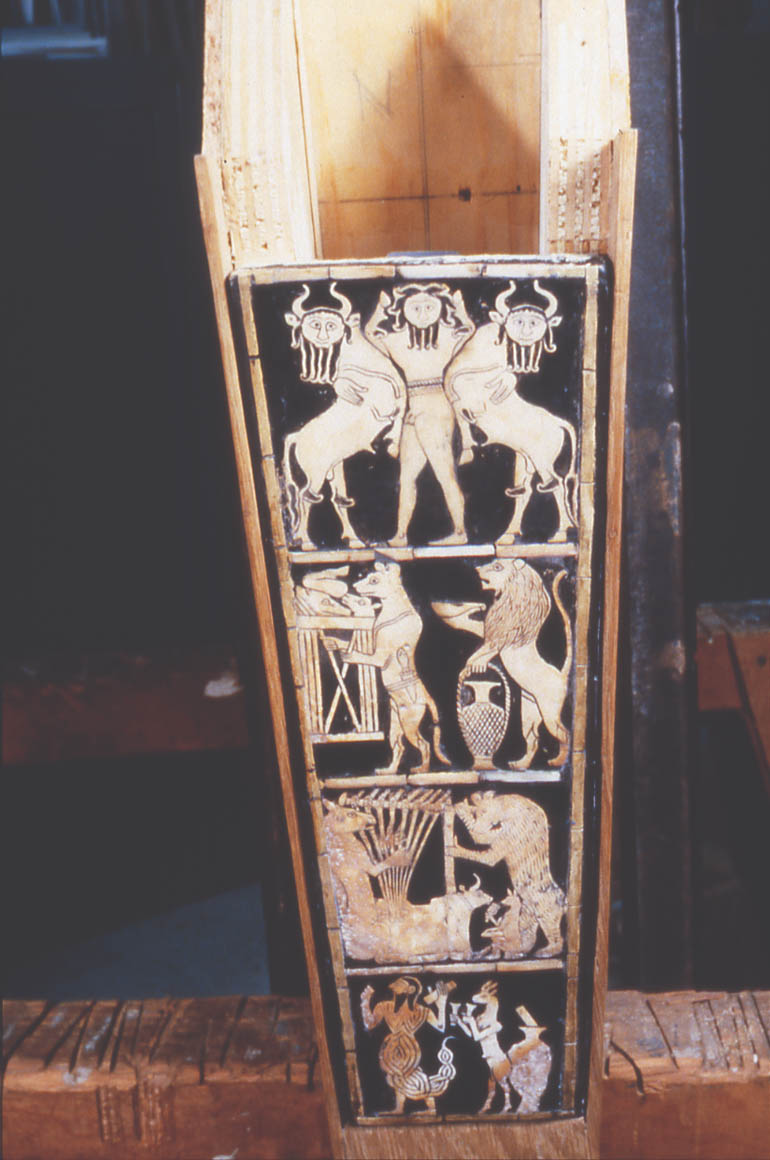 |
Fig. 2a.
The side of the head, beneath the proper right horn and ear, showing the cracks and tears in the gold sheet, the small holes in the neck strip, and the overlapping plaster.
 |
Fig. 2b.
The proper right ear, with the gold tacks visible along the seam. The heavy facing has been partially peeled back from the gold sheet.
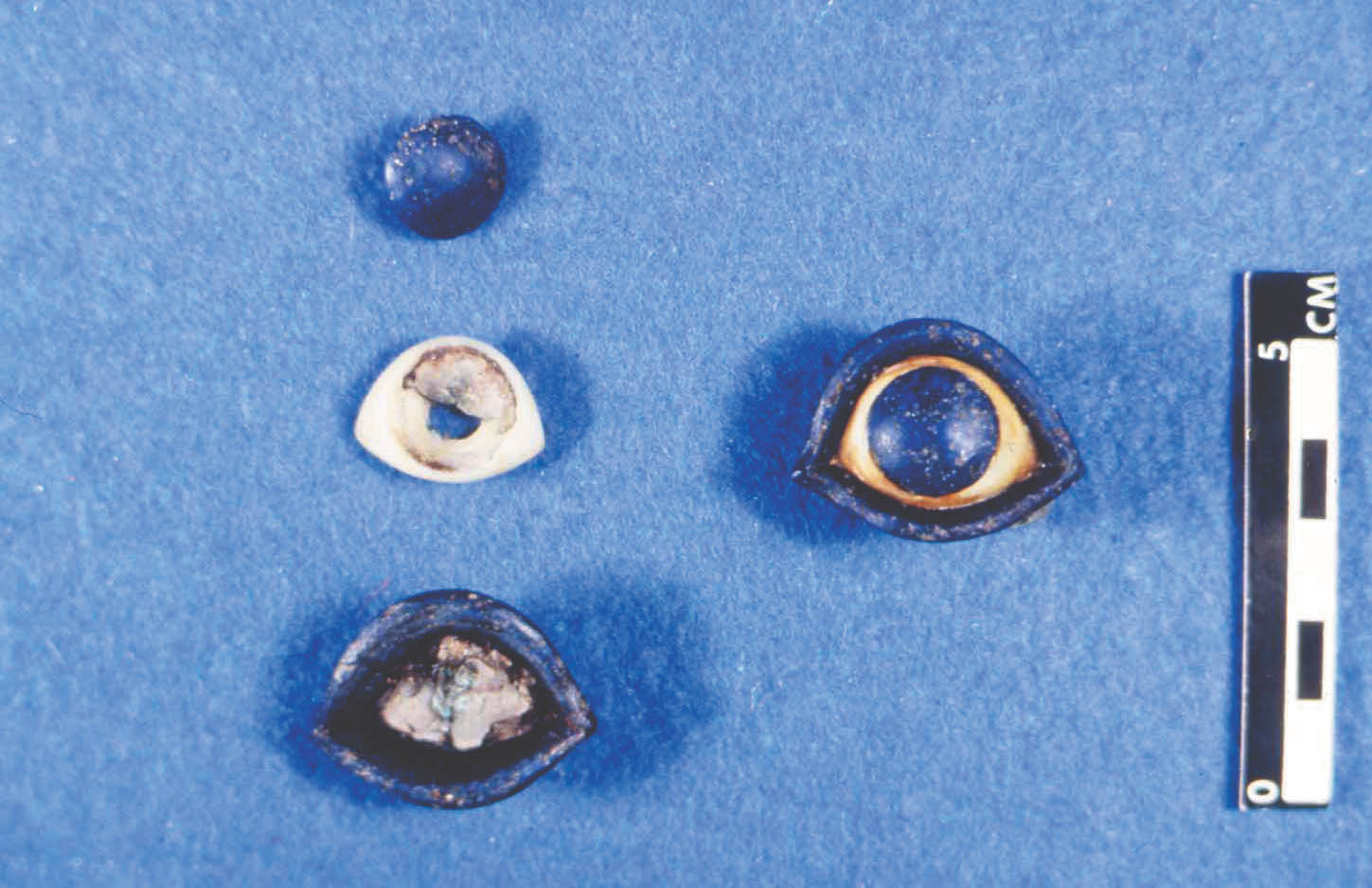 |
Fig. 3a.
The lapis horn tips. Note the tenons with crosswise holes. The missing tip has been restored.
 |
Fig. 3b.
One possible method of attaching the lapis tip to the horn core
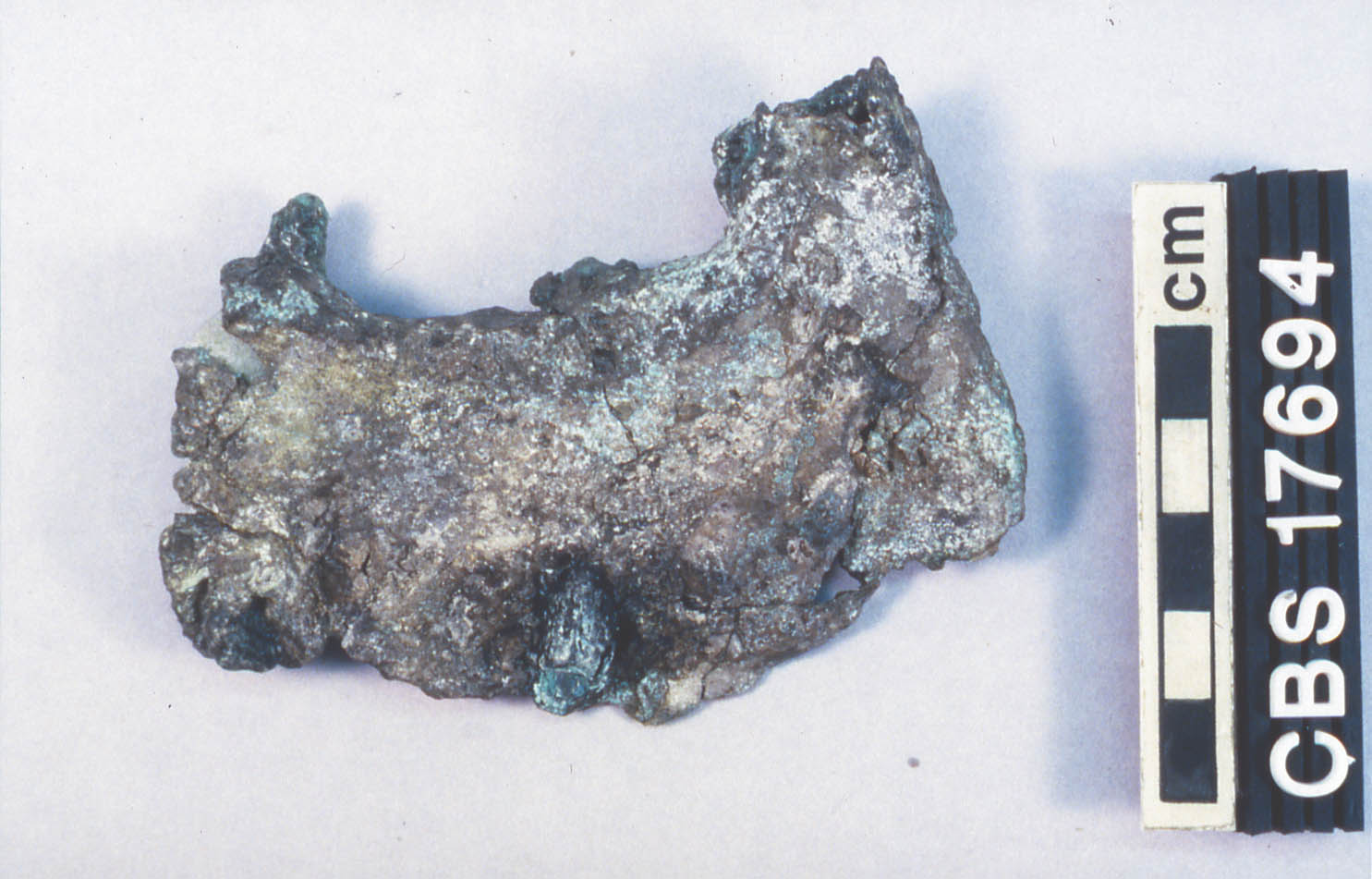 |
Fig. 4a.
The eyeball assemblies, removed from the head. The proper right eye has been taken apart. Some of the hard gray restoration material is visible.
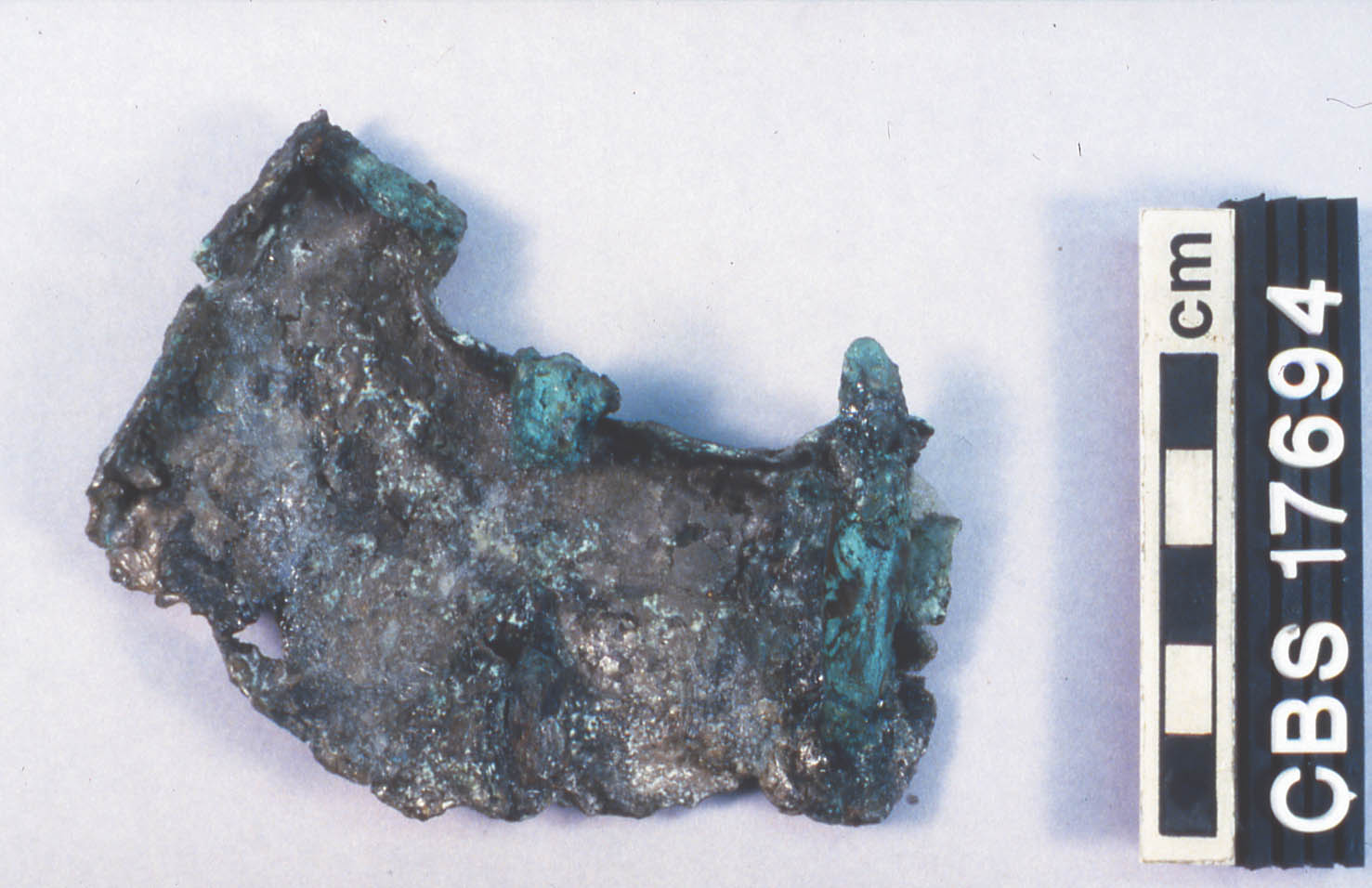 |
presumably the remains of the original bitumen adhesive. Bitumen, a naturally occurring petroleum product, dark brown or black in color and viscous in consistency, was widely used in the ancient world as an adhesive (Forbes 1964).
Figure 4b shows one possible method of assembling the eyeball without adhesive, using wire and a wooden peg. The nested pieces would be held securely by the wire tied around the peg, and the entire eyeball could then be handled as a unit as it was inserted into a hollow in the head core, using bitumen adhesive. As the shell and lapis elements were almost certainly made by a specialized craftsman, this assembly would keep the eyeballs together before they were attached to the head.
The hair was composed of small lapis tesserae (73 complete, 3 fragmentary), carved to represent individual curls of hair. They were set in six horizontal rows, attached directly to the head core by bitumen.
Fig. 4b.
One possible method of assembling the eyeball without adhesive
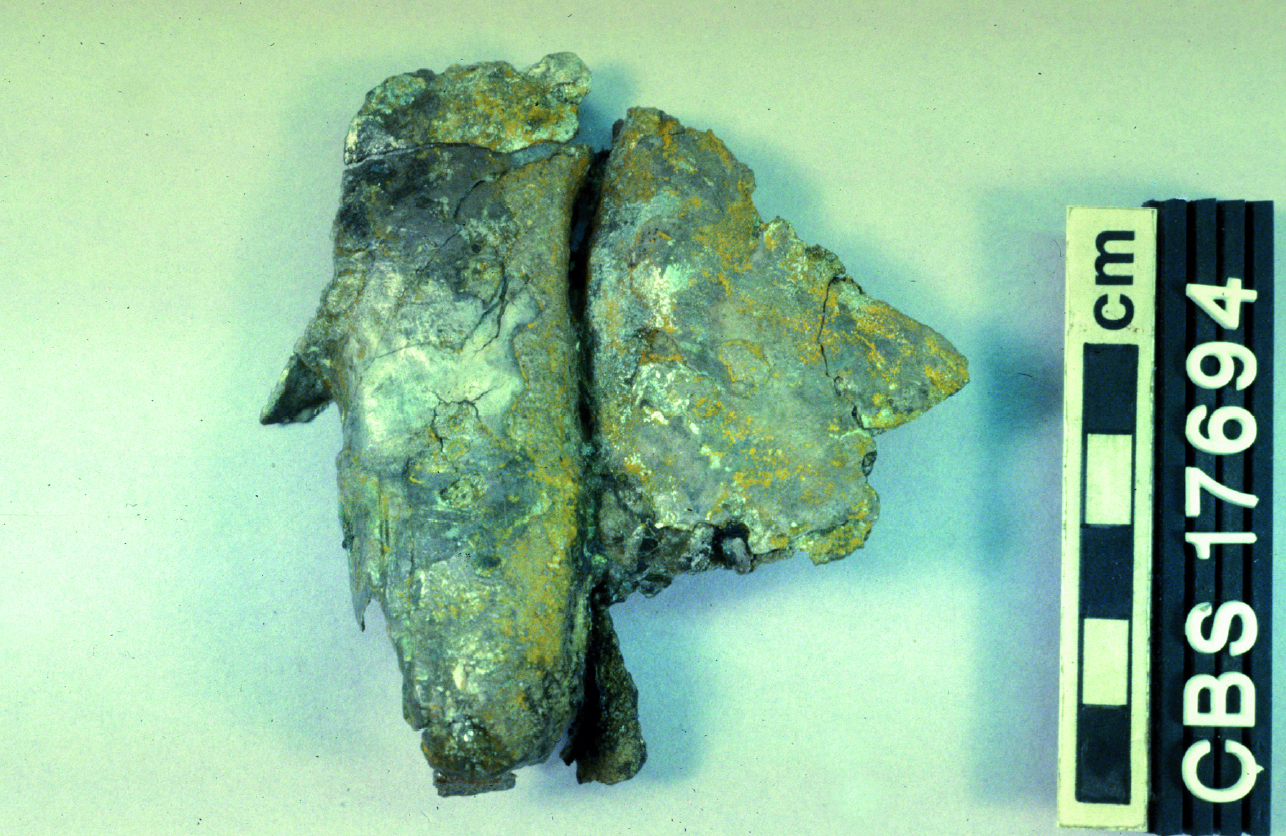 |
2.2 THE BEARD
The front of the beard is made of 58 lapis tesserae, arranged to form a wavy beard with six long locks in the center and three shorter curls on each side. Two additional side curls were placed on top of the main part of the beard, alongside the nose of the bull (see fig. 1a, page 246).
Each tile has a biconical hole on the reverse, many of which still held the mineralized remains of copper alloy wire (figs. 5a, b; see 5b on page 247). The presence of these holes had never been recorded and was entirely unsuspected before the bull head was treated, although large shell “inlay” pieces with similar holes (some of which also have remains of wire) are known from Ur (de Schauensee 2001, pls. 33a, b, 34).
Three large fragments of the original silver beard backing were found during the treatment:
Fragment 1. A large flat area, broken into several fragments, without original (finished) edges
Fragment 2. A fragment from the upper proper right corner of the central section of the beard, including finished edges on the top and sides, and parts of three copper alloy pins or nails that appear to have been used to attach the beard to the head (figs. 6a, b, see page 248). Two of the pins were clearly driven in from the back of the beard. The original length of these pins is uncertain;the surviving sections of two are ca. 5 cm long. The third pin, of which only 2 cm remains, was inserted from the side of the beard into the head core.
Fragment 3. A section from the proper left side, including a finished edge. This fragment (figs. 7a, b, see page 249) consists of parts of two separate pieces of silver sheet and demonstrates that the beard was not backed as a single unit but in sections. Four small silver tacks, ca. 6–8 mm long, can be seen along the juncture of the two sections, three on one side and one on the other. The heads of two of the tacks are visible and show clearly that the tacks were inserted from the outside of each section, piercing the silver sheet and securing it to the beard core.
Fig. 5a.
The back of the beard tiles, showing the biconical holes and fragments of mineralized wire
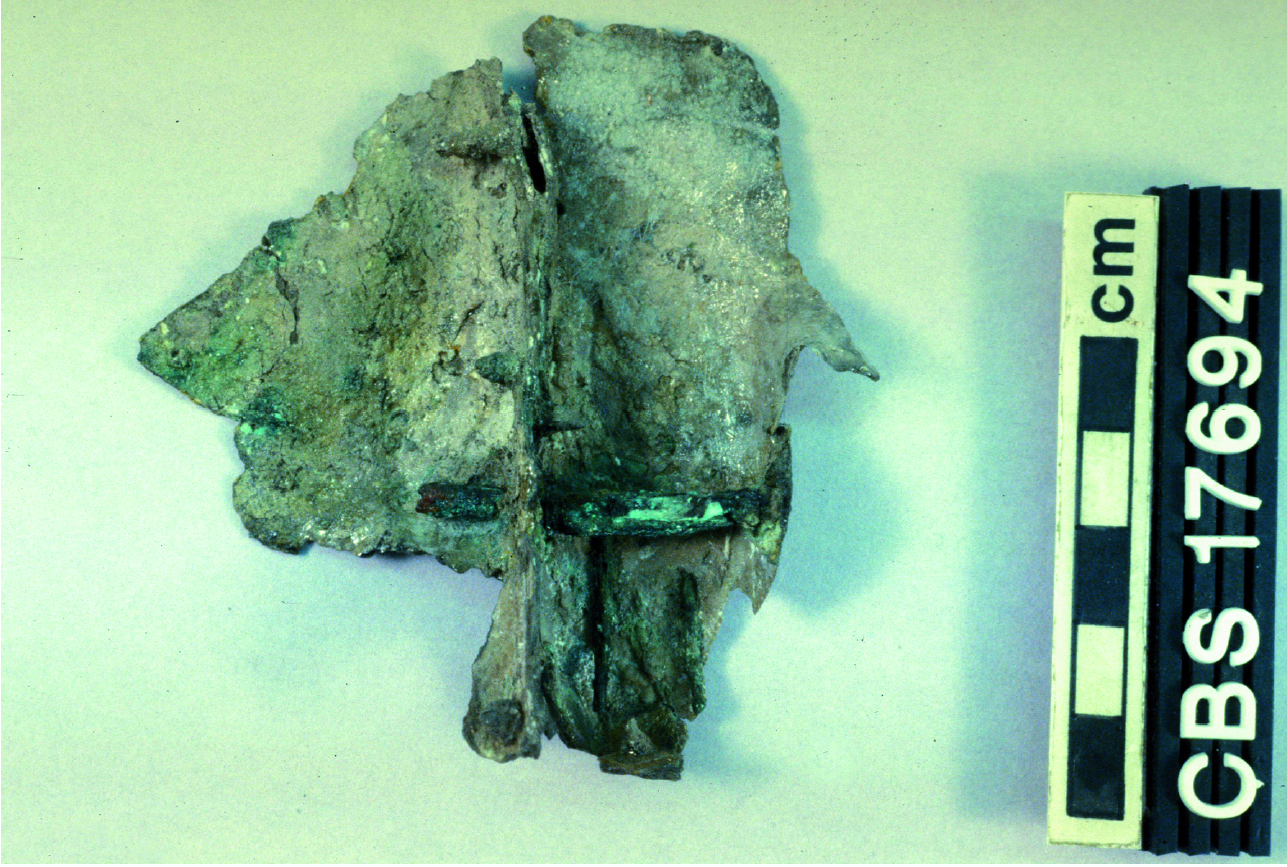 |
Fig. 5b.
Detail of the beard back
 |
Fig. 6a.
Exterior of fragment 2 of the silver sheet. Parts of two nails are visible at center and left, clearly penetrating the silver from the exterior.
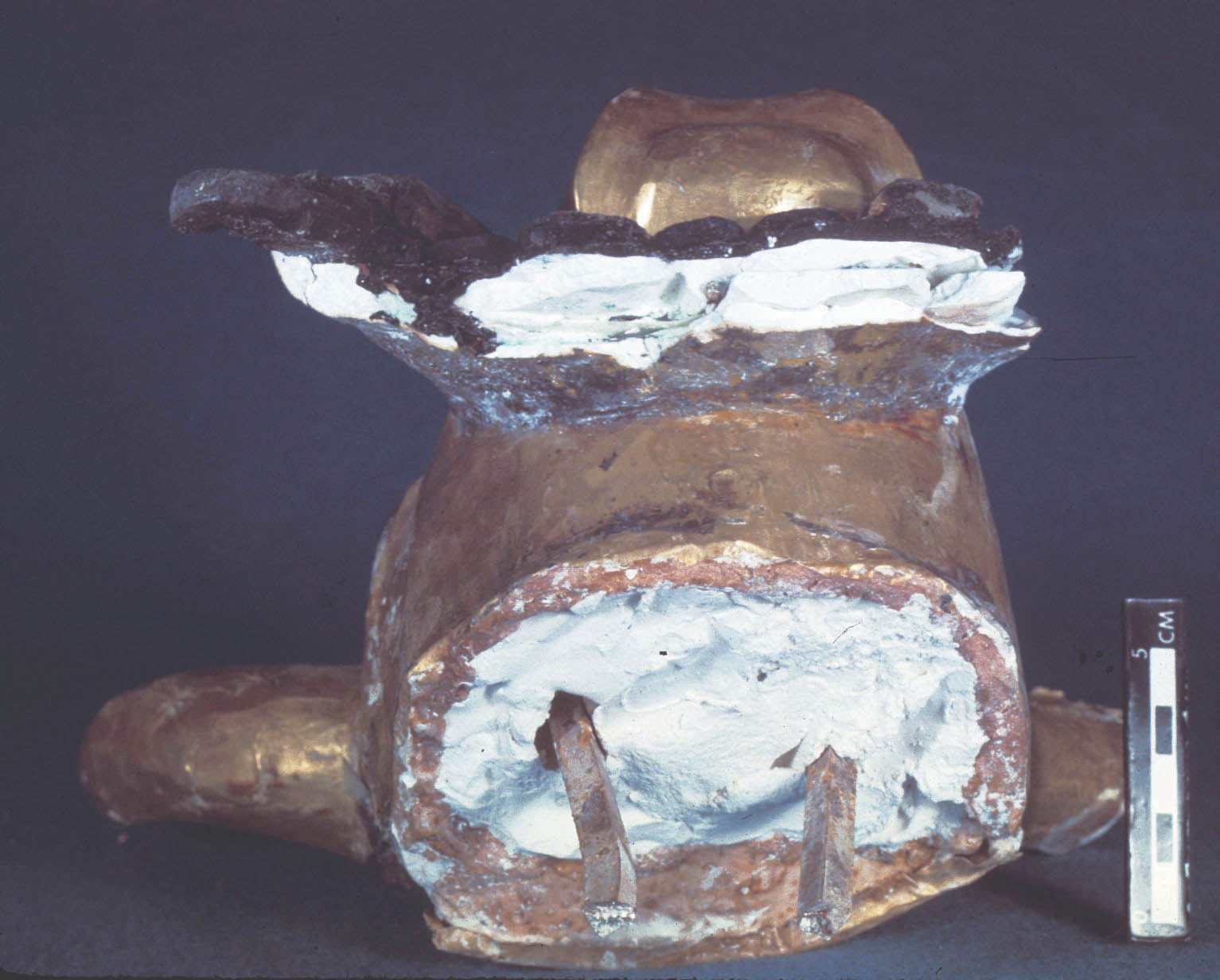 |
Fig. 6b.
Interior of fragment 2. Two copper alloy nails can be seen at the center and right; the third runs horizontally along the upper left corner.
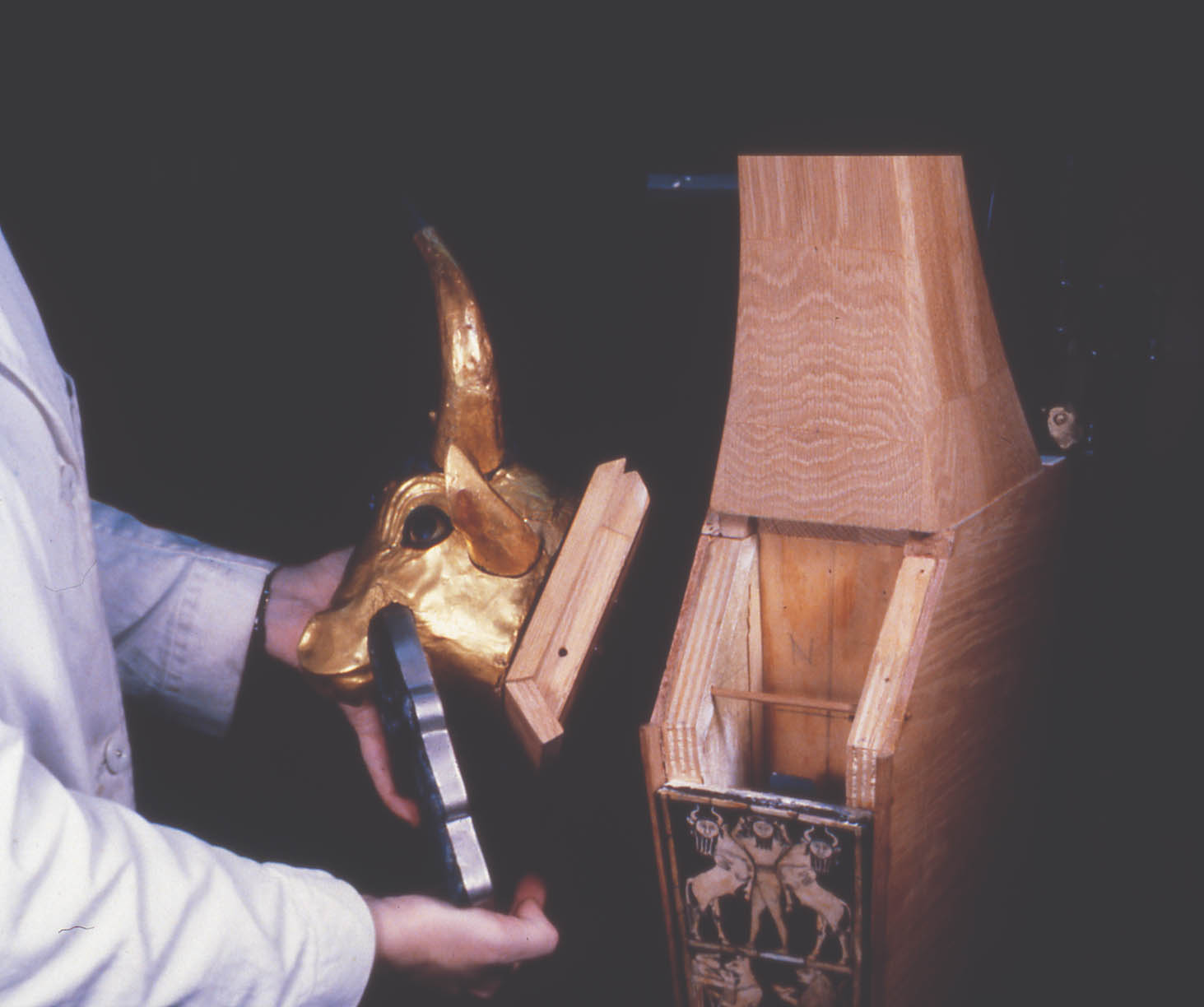 |
Fig. 7a.
Exterior of fragment 3 of the beard backing, from the proper left side. Two separate pieces of silver sheet are wrapped around the backs of two of the beard sections.
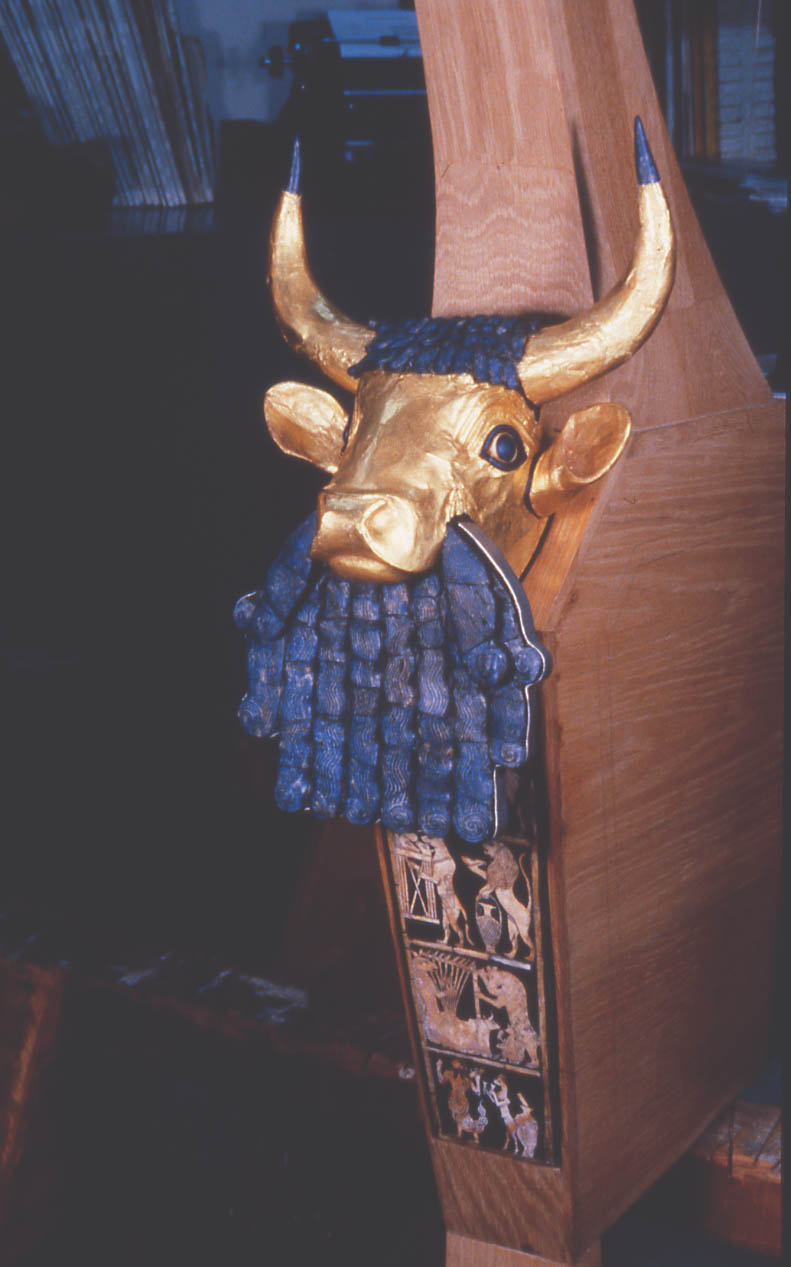 |
Fig. 7b.
Interior of fragment 3. In the lower part of the photograph is one of the copper alloy nails used to fasten the two beard sections together.
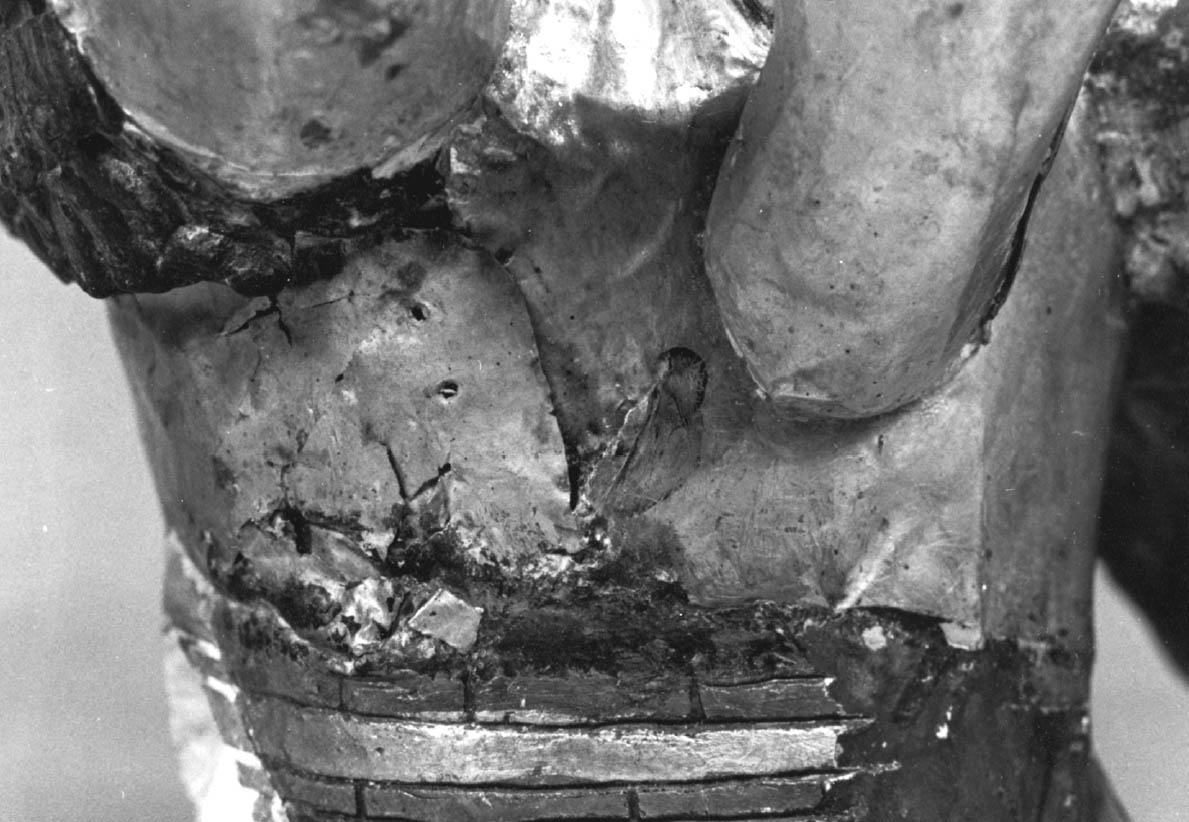 |
Also present is part of a long copper alloy pin or nail that was used to join two of the beard sections. The original length of the pin is unknown; the existing fragment is 3.7 cm long, and copper stains on the silver suggest that it was at least 2–3 mm longer. The head of the pin is missing, but deformation of the silver sheet makes it obvious that the pin was inserted from the outside of one section, completely through that section, and into the adjacent unit. Between the pin and the silver sheet was a tiny fragment of completely mineralized wood, the only trace of the original beard support. The fragment was too small and too heavily mineralized for identification.
On the inner surface of fragment 3 were two lengths of mineralized copper alloy wire (15 and 22 mm long), a small lump of bitumen, and a very small amount of a light brown powdery material that was not identified but may also be residue from a deteriorated wood backing. The wire may be the remains of wire from the beard tiles, which fell onto the silver sheet after the disintegration of the wood beard support.
After the head had been dismantled and cleaned, additional fragments of the original silver beard backing, which had been cataloged under a different accession number, were discovered in storage (fig. 8). These included the proper right-side section of the beard, corresponding to part of fragment 2, and 19 smaller pieces. One was L-shaped, with a short length of copper alloy pin inserted through the side near a silver tack; three other fragments also had silver tacks. One flat fragment had the remains of a piece of copper alloy wire adhering to it. In addition, there were 11 loose silver tacks, a length of copper alloy pin, and the head from another similar pin.
The location of the fragments of silver sheet in relation to the beard tiles is illustrated in figures 9a and b. As found in the first restoration (fig. 9a), the silver does not correspond to the outline of the beard. In the proposed original layout, illustrated in figure 9b, the outlines correspond, and the beard can now be seen as a discrete unit. The beard was fabricated in three sections, each with a wood support onto which the lapis tiles were mounted with bitumen. As with the eyeball assembly and hair tiles, the beard tiles were made by a craftsman who specialized in stone. The wires on the reverse of the tiles suggest that after manufacture the lapis tesserae were arranged in their proper configuration and attached to a thin layer of organic material (fabric or leather). Attaching the assembled tiles to a thin backing would ensure that they could be transported and mounted easily when the head was assembled. The wire ends would also act to secure the tesserae in the adhesive. Silver sheet was then placed over the back of each section of the beard and hammered around the sides to cover the wood support, with small silver tacks used to hold the sheet in place.
The three sections were then aligned and joined with long copper alloy pins, driven through the side sections into the wood support of the central section (fig. 10). Two pins were used on the proper right side; only one is preserved on the left side, but there is room for a second. The assembled beard was then attached to the head core with additional copper alloy pins: at least two were driven in from the back of the beard upward into the head, and at least one additional pin was inserted on each side. The beard was attached to the head directly over the gap in the gold sheet, which was probably cut for reasons of economy or, possibly, to allow a more secure attachment of the beard to the head core. The two remaining lapis curls were then adhered to the upper surface of the beard with bitumen.
The system used to attach the head to the original soundbox is unknown. It is unlikely, given the weight of the head and beard, that it was mounted entirely with adhesive, but wooden dowels could have been used to provide additional support.
2.3 THE FRONTAL PLAQUE
The plaque (see fig. 1b, page 246) is composed of small shell elements set into a bed of bitumen. It may have been assembled in advance on a rigid support, which was then secured to the front of the soundbox.
3 INITIAL RESEARCH
Faced with an object that had been restored many decades ago, the first problem was to discover—if possible—exactly what had been done during excavation and in the course of the first restoration.
Fig. 8.
Fragments of the silver beard backing, interior view, ready for mounting. University of Pennsylvania Museum CBS17684 and CBS 17694
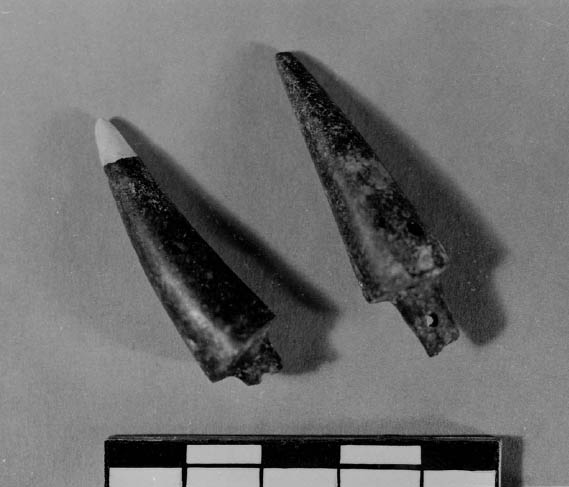 |
The condition of the head when excavated, and some of the restoration procedures, are described by Woolley (1934) in his published report. The bull head had been crushed, and both horns and ears had been displaced from their original positions (de Schauensee 2001, pl. 30). The lapis tiles forming the hair had fallen into the head. The lapis tiles from the beard had shifted and were partly overlapped. The silver sheet backing of the beard was bent and broken. Paraffin wax was poured over all the parts of the head, reinforced with muslin wrapping, and the pieces removed from the ground. After separating the various elements of the bull head, the gold was annealed and reshaped with finger pressure.
According to Woolley (1934, 70), the gold was filled “with plastic wood, plaster, &c.,” and the horns and ears were reattached in the appropriate positions. The silver backing for the beard was “reduced and straightened, and the lapis tesserae, which had been kept in their original order, were replaced” (Woolley 1934, 70). The lapis hair tiles were also reattached to the head; some of these had been preserved in their original positions, and the remainder were placed to fill the gaps.
Fig. 9a.
Position of the silver sheet in relation to the beard tiles, as found in the first restoration
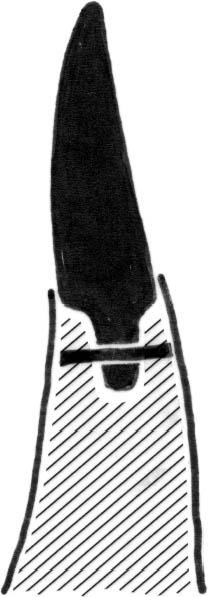 |
Fig. 9b.
Proposed correct relationship between the silver sheet fragments and the beard tiles
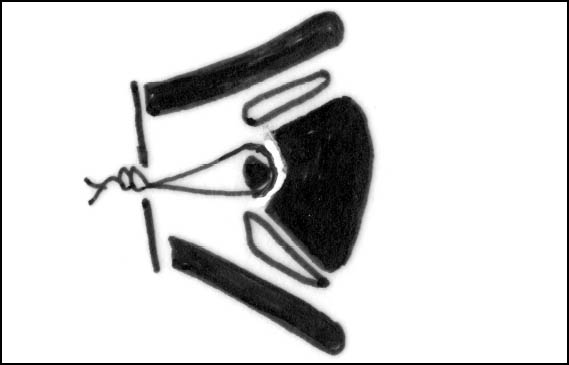 |
Fig. 10.
Section through head and beard, showing proposed original construction. The beard tiles are attached to a layer of fabric that was adhered to the support with bitumen. After the beard assembly was completed, the beard was nailed onto the head core over the gap in the gold sheet.
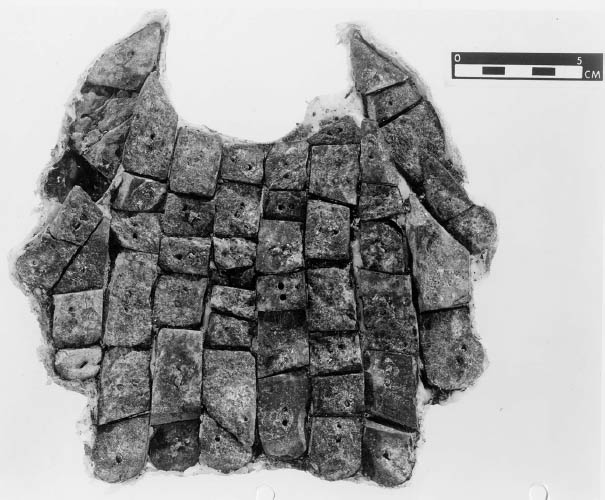 |
Fig. 11.
Proper left horn. The plaster core can be seen beneath the torn gold sheet.
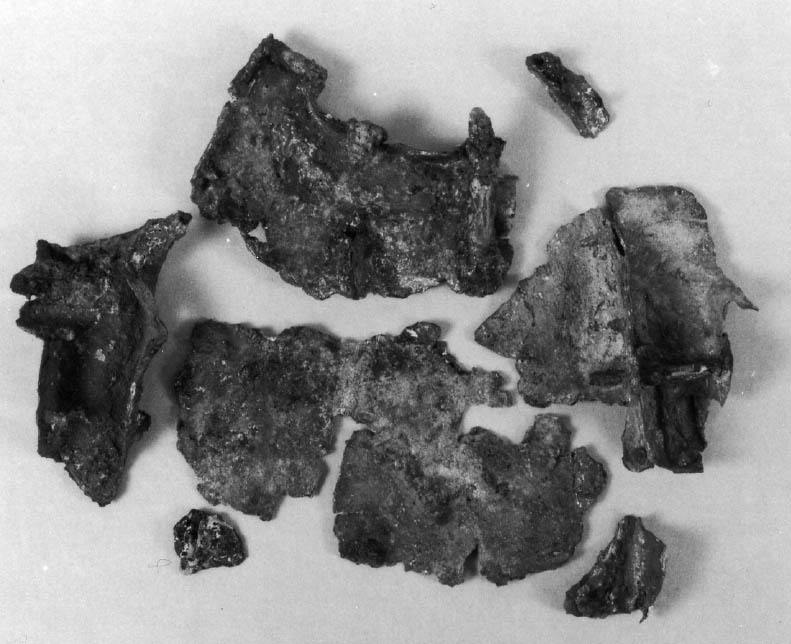 |
Fig. 12.
The head with the plaster neck removed, showing the ends of the iron armature and the broken surface of the beard with multiple layers of plaster and wax
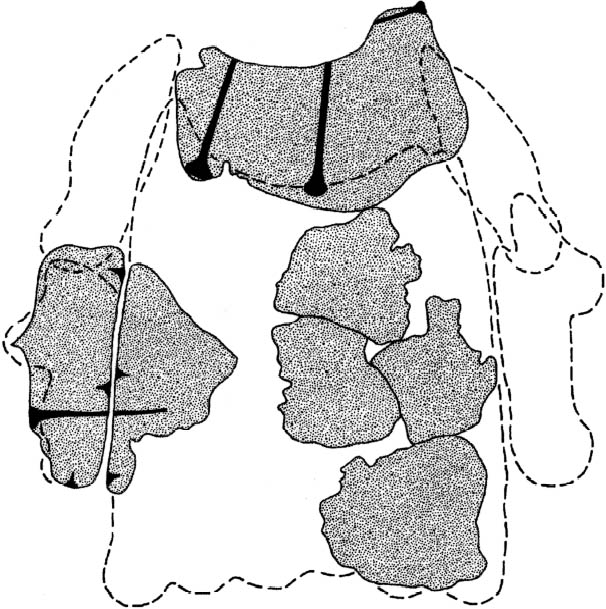 |
The plaque was lifted in the same manner as the head: paraffin wax was poured over the shell pieces, also picking up the powdery remains of the original bitumen adhesive. In the laboratory (location not specified) excess wax was removed, and the plaque was flattened (Woolley 1934, 70).
This brief and unsatisfactory account and two published photographs of the soundbox impression in situ and the head before restoration (Woolley 1934, pls. 106a, b, reprinted in de Schauensee 2001, pls. 26, 30) are the only records of the condition of the head when excavated and of the first restoration procedures. It is not even certain when the restoration was done, or where, or by whom.2
4 CONDITION OF THE HEAD BEFORE TREATMENT
The head, horns, and ears were filled with plaster. There were many small cracks and tears in the gold sheet of the head and some distortion of the torn edges (see fig. 2a). The plaster neck with the reproduction inlay overlapped the edge of the gold sheet. Many small creases were visible around the nose, probably produced when the gold sheet was reshaped after excavation. The lapis and shell eyes were covered with a film of wax and dirt, but there were no visible losses or damage.
The ears were secured in place with wooden pegs and a clear adhesive. The adhesive, which had the appearance of cellulose nitrate, had deteriorated, and the pegs were loose. The gold sheet of both horns had numerous cracks and tears, with some distortion of the edges (fig. 11, see page 250), which was particularly severe on the proper left horn. The plaster core of this horn had been broken and then repaired with what appeared to be cellulose nitrate adhesive. Below the repair the gold had almost entirely separated from the plaster. About 5 mm was missing from the end of the proper right tip.
The hair and beard tiles were set into a matrix of dark brown wax and also covered with a film of wax and dirt. A yellow wax had been applied around the beard at the point where it was inserted into the head. The edges and back of the beard were covered with metallic silver paint over a layer of ocher yellow paint. The original silver backing was not visible. The edges of the beard were chipped in several places, exposing a modern plaster support, and there was considerable separation of the lapis tiles and wax from the underlying plaster.
A small sample of the dark brown wax was examined under the microscope. Under 20x it appeared as a translucent, slightly yellow wax with dark brown grains of varying sizes. These grains are almost certainly the remains of the original bitumen adhesive, preserved by Woolley when he poured paraffin wax over the beard.
On the basis of the available information, it was assumed that the dark brown wax dated from the time of excavation and that all other visible restoration materials, including plaster, adhesives, and wood pegs, had been added at the time of the first restoration. The head was taken to the Hospital of the University of Pennsylvania for radiographic examination. This examination revealed a large, U-shaped armature inside the head, presumed to be part of the first restoration, but no other evidence of a support system, ancient or modern (de Schauensee 2001, pls. 31a, b).
The curatorial staff then approved the removal of the plaster neck from the head. This procedure exposed the ends of the iron armature. Some rusting of the iron had occurred, and removal of the armature was clearly advisable. The curators also wanted to be able to easily remove the head and plaque from the new soundbox for study, and this step would be difficult to achieve without removal of the old plaster and armature. The damage to the gold sheet needed to be repaired and the areas with cracks and splits given more adequate support. In addition, in spite of the care taken in handling, the beard broke off close to the head when the plaster neck was removed (fig. 12, see page 250). It was then clear that the beard was composed of not one but several layers of plaster, interleaved with wax and fabric. There were many areas of cleavage between the layers, as well as cracks and crevices in the plaster itself, which would make it difficult as well as undesirable to simply reattach the beard. Traces of the original silver beard backing could be seen inside the head, and both conservation and curatorial staff felt that all the original silver should, if possible, be exposed, cleaned, and photographed.
The decision was therefore made to take the head completely apart, clean and photograph all component parts, and reassemble it with a new support system that would allow the head and plaque to be easily removed from the soundbox.
5 CONSERVATION OF THE HEAD
The conservation treatment was divided into several stages. The horns and ears were removed from the head, and the separate pieces were faced. The section of beard that had become detached was dismantled first, followed by the section of beard still inside the head. The plaster was then removed from the head, horns, and ears.
5.1 EARS AND HORNS
The ears, being loose, were simply lifted off the wooden pegs. The adhesive holding the horns was removed with acetone, which was also used to separate the lapis horn tips from the plaster.
5.2 FACING
The ears, horns, and head (with the lapis hair tiles still attached) were faced with a layer of cellulose tissue and microcrystalline wax. Over this was put a layer of cheesecloth and wax, as it was not certain at that time to what extent the gold sheet would be able to hold its shape without a core. This heavy double facing later proved unnecessary, but it did enable the conservators to handle the head with confidence during the early stages of the treatment.
5.3 EXCAVATING THE BEARD
Starting with the section of the beard that had been detached from the head, the lapis tiles were faced with several layers of cellulose tissue and microcrystalline wax before work was begun on the back surface. The layers of silver and yellow paint proved resistant to solvents, but most of the paint was eventually removed with dimethylformamide and methylene chloride. Because of the poor condition of the silver, no attempt was made to remove every trace of paint. The silver sheet was very soft and friable, with a laminated structure and crumbling edges. As the silver was exposed, it was consolidated with polyvinyl acetate (PVA-AYAF) in toluene, and a temporary facing of tissue and microcrystalline wax was applied to the surface. Unfortunately, the PVA solution used as a consolidant for the silver did not set properly on some of the fragments, possibly owing to the presence of a previous consolidant. The PVA was removed with acetone, and after some experimentation, these fragments were successfully consolidated with Rhoplex AC-33 acrylic emulsion. (Paraloid B-72 [ethyl methacrylate copolymer, formerly Acryloid B-72], the first alternative tried, did not appear to be as successful as the emulsions, and the Rhoplex was superior to Jade 403.) A layer of fine muslin had been used as a separator between the silver sheet and the plaster that formed the primary support for the restored beard. Silver and muslin together were removed by inserting a spatula between the muslin and the plaster.
The work on the beard uncovered no conclusive evidence that the silver sheet had ever been treated. On the contrary, both the condition of the silver itself and the presence of fragments of copper alloy wires and pins (see sec. 2.2) strongly suggested that the backing was merely cleaned of superficial dirt before being incorporated into the restoration. The same was true of additional fragments of the silver sheet that had not been part of the restored head.
Attached to the interior face of the silver sheet were a number of small lumps of copper corrosion products. On the basis of appearance and experience (no analysis was done), these were described as predominantly carbonates, with some cuprite. Large areas of the silver sheet and the muslin were also stained green. After photography, a permanent support of fine fiberglass chopped-strand mat and Paraloid B-72 in toluene was put on the inner surface of the silver, and the temporary wax-and-tissue facing was removed from the outer surface. The support was put on the inner surface, covering details of interest, because it was assumed at the time that the fragments of the original silver sheet would be replaced on the newly restored beard.
After removal of the silver, work continued from the back of the beard. The plaster support below the muslin was composed of several thin layers (which showed distinct cleavage in many areas) and a thick layer reinforced with three modern wooden dowels (ca. 0.5 cm diameter, 6.5 cm long). The layers of plaster and wax were removed by softening the plaster with cotton packs soaked in hot water and then removing both plaster and wax with a scalpel. Beneath the plaster was the wax bed holding the lapis tiles. A sample of the wax was saved for future analysis, and the remainder was removed mechanically, with toluene as needed. The tiles were then placed on a tracing of the beard to preserve their original position and faced as a unit using tissue and microcrystalline wax.
Work was now started on the portion of the beard still attached to the head. Once the back surface was partially cleaned of paint, it was possible to see that the silver sheet extended into the plaster core of the head through an opening in the gold sheet. This open space, through which the beard had been inserted into the head during the first restoration, was too small to permit safe excavation of the plaster. This part of the beard was therefore dismantled from the front. Incorporated in the wax and plaster layers were three additional modern wood dowels that extended into the plaster core of the head. These were approximately the same size as the ones previously found in the lower part of the beard. It was now obvious that the beard had broken at the weak point between the two sets of dowels and that no fulllength reinforcement had been used in the restoration. By fortunate chance, the break fell between two sections of silver sheet, so that no original material was damaged.
Beneath the wax and plaster layers was the muslin separator, which peeled off when dampened with water, exposing a substantial area of silver sheet along with the remains of several corroded copper alloy pins or nails (see sec. 2.2). As the surface of the silver was cleaned, it was consolidated with Paraloid B-72 in toluene (which in this case was entirely successful) and then given a temporary facing of tissue and microcrystalline wax. The silver sheet, however, was still held firmly in place by the plaster inside the head.
5.4 EYE ASSEMBLY
Before removing the plaster from the head, the eyes (see. fig. 4a, page 247) were removed from the head by flowing toluene around the outer edges and removing the softened wax mechanically. The eyeball assembly was held together with what appeared to be paraffin wax, presumably left in place after the eyes were excavated. This wax was easily dissolved with ligroine (petroleum ether, boiling point 90–100�C), and the sections were separated and cleaned with the same solvent. The backs of the eyes were not protected when the head was restored, and plaster had flowed around the fragments of wire on the proper left eyeball, causing additional corrosion and making it very difficult to clean the fragile and completely mineralized wire.
The back of the proper right eyeball showed traces of copper corrosion embedded in a hard gray material that was insoluble in water, ethanol, acetone, toluene, and ligroine, as well as 50:50 acetone: ethanol. Additional traces of this gray substance were found between the elements of the eyeball assembly, together with paraffin wax. This substance is almost certainly a modern restoration material. It was never identified, but a sample was kept.
All the shell and lapis elements were cleaned in ligroine, leaving the gray material in place. Both eyeballs were reassembled using Jade 403 PVA emulsion adhesive. The plug of gray material was replaced in the back of the right eyeball, but the coiled wire from the left eye was kept separate for later examination. The details of the eyeball construction (like those of the horn tips) had not previously been recorded.
5.5 REMOVAL OF OLD PLASTER CORES
The horns and ears were soaked in warm water for several hours, and the softened plaster was removed mechanically. Metal tools were used initially, but once the plaster had been excavated to 5 mm of the interior surface, only wooden tools were employed. The gold sheet had not been lined, and in several places the plaster adhered tenaciously to the metal, but it was eventually detached after longer periods of soaking. The tiny gold tacks in the proper right ear were now visible: all four were intact and 5–6 mm long (see fig. 2b, page 246).
The plaster inside the head was first softened with packs of cotton wool soaked in hot water. The exposed silver sheet was protected with polyethylene sheet. As the cavity grew, small amounts of water were poured in and left for several hours at a time. When the excavation had progressed to within 1 cm of the interior surface, the remaining portions of the silver sheet could be removed. With the silver out, the head could safely be immersed in water, and after an overnight soaking the rest of the plaster was removed without difficulty.
Unfortunately, no separator had been applied to the outer surface of the silver sheet before the beard was inserted into the head. The plaster thus flowed into every crack and crevice in the silver and could not be completely removed.
Three separate batches of plaster had been used to fill the head. An initial batch of hard white plaster was poured into the nose. The restored beard was then inserted through the opening in the gold sheet and held in position with wax. A second pouring of similar plaster secured the beard in place and filled most of the head. A third batch of softer pale pink plaster filled the rest of the head cavity and held the iron armature in position.
It was impossible to tell whether the head had been entirely filled with white plaster and then excavated for the armature or whether the space for the armature was left from the start. In any case, the difference in materials would support the theory that the construction of the soundbox and the attachment of the head to the soundbox were done by a different person, and/or at a different time, than the restoration of the head itself.
With the interior surface of the gold head exposed, two sets of small holes could be seen on the edge of the gold sheet under the horns, matching the pairs of holes on the neck strip. There were no original tacks present, and the two sets of holes were not properly aligned. It was also then evident that the gold sheet extended only a few millimeters under the bottom row of lapis hair tiles, which were embedded in the same type of wax as the beard tiles. When this wax was removed, the backs of the hair tiles proved to be plain, unlike those of the beard, and so must have been held in position on the core entirely with bitumen adhesive.
6 NEW RESTORATION OF THE HEAD AND BEARD
6.1 BACKING THE BEARD TILES
The lapis tiles were backed using fiberglass chopped-strand mat and Paraloid B-72. The conservators were very reluctant to cover the holes and the remains of the wire, but the curatorial staff felt that with the details recorded, it was preferable to restore the beard to its original appearance insofar as it was possible to do so. It was decided, however, not to replace the fragments of silver sheet on the beard. Owing to their distorted and fragile condition, it would have been very difficult to mount them safely and maintain the original appearance of the beard. A Plexiglas mount was therefore constructed for the three larger fragments of the original silver backing. After examination of the additional fragments found in storage, five of these fragments were added to the original mount. The clear mount enables both sides of the silver to be seen, and it is possible to remove the fragments from the mount for closer examination (de Schauensee 2001, pl. 50).
After the backing had been applied to the beard tiles, the curatorial staff decided that the beard should have a straight bottom, not a concave one as in the original restoration. The backing was removed, and with the permission and assistance of the curatorial staff a number of tiles were repositioned to give a better fit and appearance. When the new layout was approved, the tesserae were backed with lightweight fiberglass cloth and Paraloid B-72 in toluene. The cloth was chosen partly as a result of the difficulties encountered in removing the chopped-strand mat to reposition the tiles. It was considerably easier to handle, would not disintegrate if any of the tiles had to be repositioned again, and would be easier to remove completely if repositioning ever became necessary. The beard and the two side sections, originally three separate pieces, were backed as a single unit for ease in handling;only the two outermost side curls were backed separately.
6.2 ARMATURE AND HEAD CORE
To provide adequate support for the beard as well as the gold sheet of the head, it was necessary to fill the head with a solid material. This material had to be rigid and reversible, have good long-term aging properties, and be strong enough to support the beard assembly. The first three conditions also applied to the new filling for the horns and ears. The new backing for the beard would have to be strong, lightweight, removable, and approximately as thick as the original (as measured by the depth of the original silver backing). To support the damaged areas and to protect the gold sheet if the core ever had to be removed, the head, ears, and horns would have to be lined before the filling was added. The design of the new soundbox and the mechanism used to attach the head also had to allow for the easy removal of both the head and the plaque.
6.3 LINING—AND ALIGNING—THE GOLD SHEET
The most suitable material for the lining seemed to be fiberglass, either chopped-strand mat or woven cloth, with Paraloid B-72. As this part of the project was carried out before the removal of the beard backing (see sec. 6.1), chopped-strand mat was chosen. After the lining was in place, the wax and tissue facings were removed from the ears and horns to check the alignment of the torn edges. The alignment was poor enough to justify complete removal and reapplication of the lining. During this messy process it became clear that the heavy facing on the gold sheet had been unnecessary. If handled with care, it would be possible to line and fill not only the ears and horns but the head as well without using any facing for support. Lightweight fiberglass cloth designed for model building was chosen for the new lining. The cloth was flexible, fit into tight corners, was easy to handle, and could be removed without shredding.
Removal of the opaque facings from the head made it clear that the head was considerably distorted. With the approval of the curatorial staff, an attempt was made to reduce the asymmetry using gentle finger pressure and a stream of warm air, and this procedure was successful.
Without the facing it was also clear that the gold strip for the neck was not in its correct position. The strip was realigned by matching the two sets of pinholes (de Schauensee 2001, pl. 45). The strip was first placed overlapping the head, as in the first restoration. Later, however, it was decided to replace it under the edges of the head section. This arrangement would account for the placement of the pinholes at the extreme edge of the proper left side and the fact that this edge appears undamaged. If the edge of the neck strip had not been visible when the holes were made, then the pins could easily have been placed too close to the edge.
Before the horns and ears were relined, all torn edges of the gold sheet were aligned and secured on the exterior with pressure-sensitive tape (3M Magic Tape); holes and gaps were also covered with tape. The clear tape enabled all the edges to remain visible during the process of filling, which proved very helpful, and the tape could be easily removed without damage to the gold. The head, horns, and ears were then lined with strips of fiberglass cloth using Paraloid B-72 in toluene.
The head was lined with strips of fiberglass cloth and Paraloid B-72, with an extra layer of cloth added to the neck strip. The lapis hair tiles were lined as a unit and secured into position on the head using additional strips of fiberglass cloth on the interior.
After the head was completely filled and reassembled, Liquitex acrylic modeling paste was used on the loss areas of the head, ears, and horns to cover the texture of the fiberglass cloth lining. These fills were then inpainted with Liquitex acrylic paint, using a nonmetallic ocher color approved by the curatorial staff.
6.4 FILLER FOR THE HEAD, EARS, AND HORNS
While the conservation of the head was still in progress, testing was started on possible materials for the new core. The first material to be examined was epoxy resin filled with styrene foam pellets, which had been successfully used by Mexican conservators as a backing for wall paintings.3 This mixture was light, rigid, and easy to work with. Initial reversibility trials by the author indicated that if enough foam pellets were used, they could easily be dissolved with acetone and the epoxy matrix removed mechanically. However, a second set of tests demonstrated that it would be very difficult to remove the epoxy from small confined spaces, where there would be few pellets and a concentration of resin.
After unsuccessful experiments with a number of synthetic resins, tests were made using polyethylene glycol (PEG) wax grades 4000 and 6000 filled with the styrene pellets. This procedure proved entirely successful. PEG waxes are soluble in water, ensuring that the core would be reversible without disturbing the lining. PEG 6000, which is harder at room temperature, was chosen to ensure that the core would remain hard even through a Philadelphia summer in a gallery without climate control. The greatest difficulty with the wax-pellet mixture was the tendency of the pellets to float to the surface. This tendency was controlled by thickening the wax with aerogel silica (Cab-O-Sil). This procedure prevented the pellets from floating, but the mixture would no longer pour and had to be forced into position.
6.5 DESIGN AND CONSTRUCTION OF THE ARMATURE
The wax-based fill was clearly not as strong as the epoxy version. It was, however, lightweight, stable, and easily reversible. The strength of the epoxy was unnecessary for the horns and ears, and if the fill for the head did not have to bear the weight of the beard, then great strength was no longer a consideration. W. Thomas Chase, of the Freer Gallery of Art, suggested that the head be “floated” around an armature that would be attached directly to the soundbox and support the full weight of the beard. With his assistance, a Plexiglas armature was designed (fig. 13). The use of this design eliminated any need for a mount that would be in direct contact with the gold sheet. Owing to the size and shape of the beard, and of the openings into the head, it was necessary to make the armature in two pieces that would be bolted together after the beard support was inserted into the head.
Fig. 13.
Plexiglas armature used to support the beard
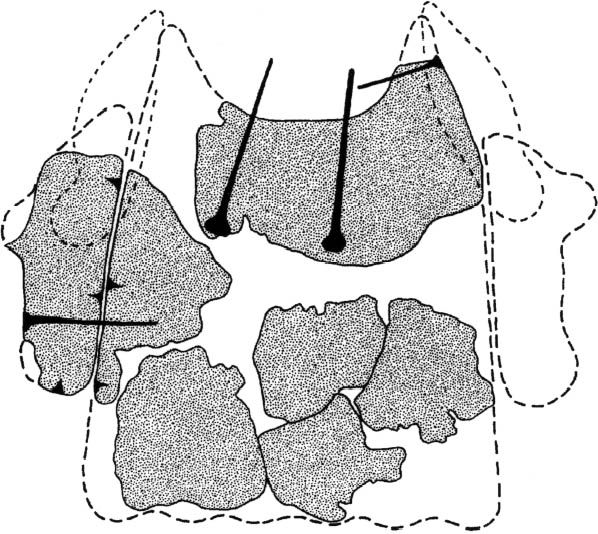 |
The part of the mount holding the beard was made of 1/4 in. (6.25 mm [nominal 6 mm]) Plexiglas sheet and the section in the neck of 1/8 in. (3.125 mm [nominal 3 mm]), with an extra piece of 1/4” in. stock added for strength and to allow the bolt heads to be countersunk. The position of the armature inside the head is shown in figure 14.
6.6 ADDING THE WAX FILL
To keep the eyeballs isolated from the wax, which would otherwise penetrate every crevice and make future removal very difficult, a small cup made of fiberglass cloth impregnated with Paraloid B-72 was fastened over the back of each eyeball assembly. Paraloid B-72 was used to hold the eyeballs in position in the head.
The ears and horns were filled individually, with Plexiglas pegs inserted at the bottom. The head was then filled in sections. Before the wax fill of the head was completely set, the ears and horns were put onto the head to ensure that the dowel hole would be at the correct angle (fig. 15a). They were then removed until the final assembly. The armature was also added as the head was filled, positioned so that it projected slightly from the neck edge (fig. 15b; see also fig. 13). This arrangement would enable the head to be mounted firmly against the soundbox without putting pressure on the edges of the gold sheet.
When the filling was complete and the facing removed from the hair tiles, it was obvious that the tiles were not in the correct position. The tiles were removed from the fiberglass cloth backing, two additional layers of fiberglass were added to give a better contour, and the tiles were set back into place individually using Paraloid B-72. The pattern of the first restoration was followed, as there is no other evidence of the original position of the tiles. Several fragmentary tiles were put at the back of the neck. The spaces between the tesserae were then filled with pigmented wax (PEG 4000 grade with powder pigment) to represent the original bitumen adhesive.
Fig. 14.
Section drawing showing position of armature inside the head, with the restored beard
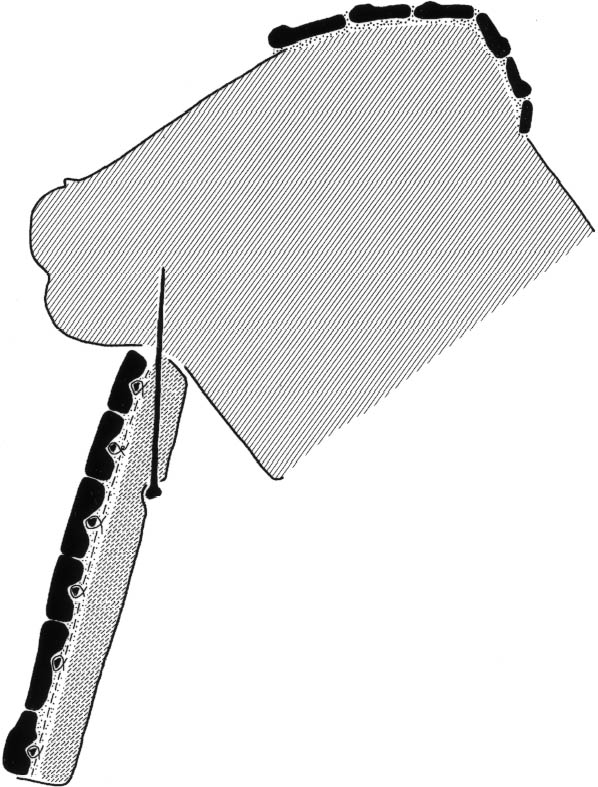 |
6.7 COMPLETION OF THE BEARD
The irregular back of the beard was leveled with a fill of Jade 403 and styrene pellets (the latter sifted to give a batch of uniform small size). The adhesive was selected because it was reputed to remain soluble in water (and so could be removed without disrupting the fiberglass backing) and gave better adhesion to the Plexiglas mount than PEG wax.
Fig. 15a.
Filling the head. The horns are in position for the next layer of fill.
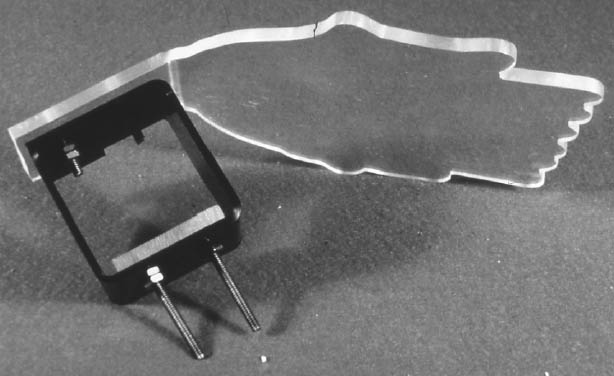 |
Fig. 15b.
Filling the head. The first batch of wax is in place, the armature has been inserted, and the two pieces fastened together.
 |
Fig. 16.
Mounting the head on the new soundbox. The hole for the locking pin can be seen on the side of the wood block supporting the head.
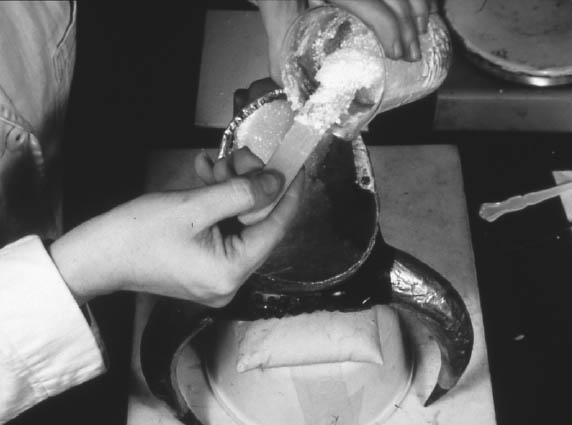 |
Fig. 17.
The completed lyre, ready for installation in the gallery. The dark line of the spacer can be seen between the head and the soundbox.
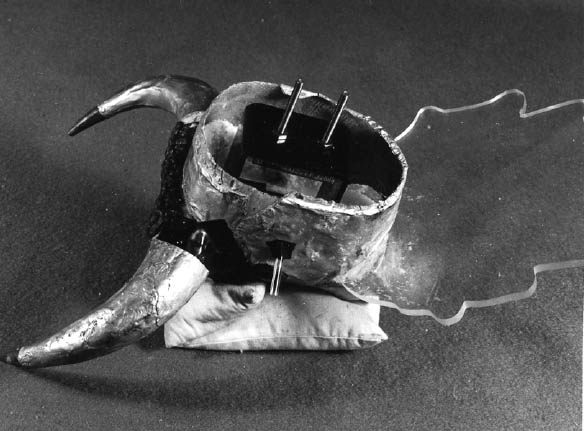 |
After the decision was made not to remount the fragments of the original silver sheet, metal foil was considered as an alternative, but this proved difficult to manipulate and unsatisfactory in appearance. After consultation with the curatorial staff, it was decided that no real attempt would be made to re-create the metallic quality of the original backing. Instead, the back of the beard was covered with two layers of 4-ply archival mat board and the sides with two layers of archival blotting paper (which conformed easily to the curves without creasing); both were adhered to the Plexiglas with Jade 403. Gaps between the back and sides were filled with Liquitex acrylic gesso, the edge was sanded slightly to reduce the sharp angle, and the backing was painted gray. The curatorial staff approved of this solution, which offered a reasonable approximation of the original effect at normal viewing distance but could easily be identified as a restoration. After the beard restoration was complete, the side curls were attached to the front of the beard using Paraloid B-72.
6.8 ADDING THE HORNS AND EARS
The missing section of lapis horn tip was modeled using Sculpey polymer (PVC) clay (see fig. 3a) and attached with Paraloid B-72. The same adhesive was used to join the tips to the horns. At the request of the curatorial staff, the horn tips were reversed from the first restoration so that they were recurved. Most of the excavated bull heads from Ur have slightly recurved horns, and it is certainly possible that the horns could have been attached backward during the first restoration.
Finally, the horns and ears were put into position with Paraloid B-72. Pigmented wax was added around the lower edges of the beard curls, the base of the horns and ears, and at the corners of the beard where it meets the head. The wax concealed the ragged edges and probably approximates the original appearance of the bitumen adhesive.
7 PLAQUE
The shell inlays of the front plaque were set into a dark brown wax, presumably the paraffin wax used to lift the object mixed with the remains of the original bitumen adhesive (see fig. 1b, page 246). One piece of the shell border was missing (from the observer's upper right); it was unclear whether this was a recent loss. The plaque had been backed with a layer of a hard, gray, plasterlike material in good condition.
Old adhesive from the back of the plaque and fake inlay on the sides were removed with a scalpel. The surface of the shell was cleaned with ethanol. The missing piece of shell was restored with acrylic modeling paste and inpainted with acrylic paints.
8 MOUNTING THE HEAD AND PLAQUE ON THE SOUNDBOX
Mervin Martin, in consultation with the conservation staff, designed a mounting system for the head and plaque that would allow for easy removal in the future. The plaque is mounted by sliding it into a groove on the front of the soundbox (see fig. 1b, page 246). The head armature is bolted to a piece of wood that fits into a groove in the front of the soundbox and is held firmly in place with a crosswise dowel (fig. 16, see pge 251).
A soft polyethylene foam spacer was placed between the head and the wood base, bringing the lower edge of the neck out to the level of the armature. The edge of the foam was painted dark brown to look like the bitumen adhesive that had probably been used as part of the original mounting system (fig. 17, see page 251). The lyre was reinstalled in the Mesopotamian Gallery of the University of Pennsylvania Museum in 1980.
9 THE TREATMENT REVISITED
In 1996, after 16 years on exhibit, the bull head was examined in preparation for a traveling exhibit, Treasures from the Royal Tombs of Ur. The head and plaque had been removed a number of times for study or travel, without difficulty and without damage to themselves, the mechanism, or the soundbox. A detailed examination by conservator Lynn A. Grant revealed no sign of deterioration either in the head core or in the beard support. The Plexiglas armature remained securely in place, in spite of the complex design and the lack of climate control in the gallery. The restored beard backing was painted a darker gray to satisfy the preferences of the exhibit curator, but no other work was needed to prepare the lyre for exhibit. When the objects are eventually reinstalled at the University Museum, a new mount will be constructed for the pieces of the original silver backing, which are also in excellent condition. The treatment, in fact, appeared to have been completely successful.
However, many aspects of the work are now somewhat embarrassing. The materials used reflect the practices of the 1970s and would be considerably different if the treatment had been carried out more recently. A contemporary treatment would reflect current safety practices, a wider ranger of available materials, and greater experience on the part of the conservators, including experience in keeping treatment records.
Most notably, toluene would not be used either as the solvent for the Paraloid B-72 or to clean the lapis tesserae. At that time, the laboratory purchased Paraloid B-72 not as dry pellets but in a toluene solution, which was then diluted further with toluene. At present, the resin is prepared from pellets and normally used in acetone or ethanol solution. The choice of ligroine (and, in one place, ethanol) for the wax removal reflects early efforts to reduce the use of xylene and toluene, though this reason was never made clear in the treatment report. Dimethylformamide (DMF) and methylene chloride were at the time, and remain today, solvents of last resort. Even in the 1970s they were used in a fume hood, with appropriate personal protection.
At that time, PVA-AYAF was normally used in the laboratory as a consolidant for pottery and other porous materials, as well as an adhesive, although Paraloid B-72 was generally employed for backings. This practice accounts for the initial choice of PVA-AYAF as the consolidant for the silver. By the mid-1980s PVA solutions had been almost entirely replaced by acrylics, and B-72 would have been the first material tried as a consolidant—which still might not have avoided the problem of incompatibility with a previous consolidant. An acrylic would also now be the adhesive of choice for the eyeball assemblies.
Emulsion adhesives would be used only a last resort, as they are now known to cross-link over time. At the time of the treatment, both Jade 403 and Rhoplex AC-33 were in common use, and Jade 403 was still thought to remain soluble in water.
The styrene foam pellets used in the wax fill were easily available from a local distributor (they were used at the time to fill bean-bag chairs), and the staff was not given a great deal of time to explore alternatives. The conservators were aware that the pellets were not a conservation-grade material and might not age well, although it was hoped that the fact they were in the dark would extend their life. The use of a material that could be easily dissolved (in acetone) would contribute to the potential ease of removal of the core, but the wax itself dissolves in warm water. If the treatment were carried out today, a different material would certainly be chosen. Shredded Ethafoam, which has recently become available, would be a possibility, along with glass and resin microballoons. The use of a hard water-soluble wax as the primary fill material still looks like a good choice.
There is, however, a notable discrepancy between the care taken to protect the back of the eye assembly and backing the beard tiles directly over the holes and wires. If this treatment were being done today, more effort would be put into finding a way to mount the beard tiles without completely coating the backs of the tiles with adhesive. In retrospect, it is also clear that the fragments of silver sheet should not have been backed until later in the treatment process; the author is less likely now to make assumptions in advance about the course of a complex treatment.
If done even 15 years ago, the photographic documentation would have been done primarily using black-and-white film, with color only as a supplement, instead of having been done largely with color slides. If the treatment were carried out today, digital photographs would also be taken. Moreover, more attention would be paid to specifying the exact materials used in the treatment and the reasons for their selection. The laboratory reports have detailed discussions of the properties needed for a particular material and procedure but often neglect to identify (or to identify adequately) the specific product that was finally selected. An example of this omission is the choice of facing materials, where the discussion is extended but the specific type of tissue and the wax chosen were not identified. From the author's recollection of what the laboratory was using at the time, the tissue was an uncoated long-fibered cellulose tissue similar to lens tissue, intended principally for mounting paper-based material. No further information on the microcrystalline wax could be located, except that it was made by Sunoco.
Still satisfactory in retrospect are the decision to use a heavy facing until the strength of the gold sheet was known, the use of a fiberglass–Paraloid B-72 lining for the gold, the care taken in the selection and testing of the fill for the head, the decision to mount the silver backing separately from the head, the ingenious design of the armature and mounting systems, and, above all, the meticulous and patient excavation of the beard backing.
Some of the work certainly reflects the unexpected expansion of the scope of the project and the fact that the conservation staff was under considerable pressure to finish the work as quickly as possible and without spending any money beyond that available in the normal laboratory supplies budget. Additional time for planning and research would have improved both materials and procedures. With additional years of experience, the staff might well have been able to successfully resist the pressure for speed and possibly have been able to secure additional funding, given the importance of the piece.
The Conservation Laboratory now has the experience to plan adequately for major projects, but access to analytical services is not much improved. Radiography can still be arranged through the generosity of the University of Pennsylvania Medical Center, but for almost all analytical work, it is necessary to have outside funding, as the laboratory budget will not support the expense even when facilities are available.
However, in spite of everything that would now be done differently, the treatment still looks like a success. After 21 years of exhibit, including one loan and a traveling exhibit with 10 venues, the head and beard appear to be as stable as they were immediately after the work was completed, and this is a satisfactory result by any standards.
ACKNOWLEDGEMENTS
The author would like to extend her thanks to the many people who participated in this project, especially the following (titles and affiliations are those of 1973 except as noted): Diane E. Davies (now Diane Davies Burke), assistant conservator, University of Pennsylvania Museum (currently at the Saint Louis Museum of Art), who was entirely responsible for the excavation of the interior of the beard and provided constant support in the running of the laboratory; in the Near East Section of the University of Pennsylvania Museum, Dr. Robert H. Dyson Jr., curator, now retired, Dr. Christopher Hamlin, assistant curator, Maude de Schauensee, assistant to Dr. Dyson, and Dr. Richard Zettler, currently associate curator; Victoria Jenssen, assistant conservator, University of Pennsylvania Museum; Shelley Reisman (now Shelley Reisman Payne), intern from the Winterthur/ University of Delaware Conservation Program (currently in private practice in Nashville), who assisted in dismantling the lyre and also made the arrangements for the radiography of the head; W. Thomas Chase, head of the Conservation Laboratory at the Freer Gallery of Art, Washington, D.C. (now retired), who cheerfully interrupted his own work to make imaginative and useful suggestions about the construction of the new armature; J. E. Curtis of the Department of Western Asiatic Antiquities of the British Museum and other members of the staff who searched diligently for information on Woolley's role in the first restoration; James House Jr., Mervin Martin, and Edward MacLean, who produced a soundbox both attractive to the eye and accurate as to details; and a second thank you to Mervin Martin, for the design and construction of the mounting mechanism for the head and plaque; Lynn A. Grant, conservator at the University of Pennsylvania Museum, who examined the lyre in preparation for the traveling exhibit and confirmed that the treatment had been surprisingly successful.
NOTES
1. The Near East Section of the museum had long wished to have a new soundbox constructed, and this was finally made possible by donations from the museum volunteer guides (1976) and the Kevorkian Fund (1977). James House Jr., a retired woodworker who had been an instructor in sculpture in the Fine Arts Department of the University of Pennsylvania, was hired to build the new soundbox. Owing to House's illness, the work was eventually completed by Mervin Martin, assisted by Edward MacLean. The head with its plaster neck and the shell plaque were removed from the old soundbox by House, assisted by conservators Virginia Greene, Diane Davies, and Victoria Jenssen and Winterthur/University of Delaware Conservation Program intern Shelley Reisman.
2. The conservation staff consulted the published excavation report (Woolley 1934) and requested copies of Woolley's original field notes and any treatment records from the British Museum. J. E. Curtis of the Department of Western Asiatic Antiquities of the British Museum kindly sent copies of the relevant pages from Woolley's field notes; these contained less information than the published report. A search of the photographic records of the excavation did not turn up additional pictures of the lyre or any records relating to the restoration of the head or plaque. The soundbox is known to have been fabricated at the University of Pennsylvania Museum (de Schauensee 2001, 51).Woolley's report includes a picture of the restored head (Woolley 1934, pl. 107). The work on the head may have been carried out either in the field or in London, possibly by Woolley himself or under his supervision. It is more likely that it was done in London at a time when Woolley was in the field. It also seems likely, from the absence of information in his field notes, that Woolley wrote much of his report from memory and/or based on information from others that may have been a treatment proposal rather than a report of the actual treatment. It is unlikely that the gold was annealed, and there is no description of the “reduction” process supposedly carried out on the silver sheet or evidence of any treatment of the silver beyond superficial cleaning. The hard gray material found behind one eyeball may be the “plastic wood” mentioned by Woolley, although the product with that trade name sold in the United States is light brown, not as fine-grained, and considerably less dense.
3. The author heard a paper (and observed a demonstration) on this technique at the 1975 American Institute for Conservation Annual Meeting in Mexico City. There are no abstracts or preprints available for this meeting, but a published report was later located (Montero 1974).
REFERENCES
de Schauensee, M.2001. Two lyres from Ur.Philadelphia: University of Pennsylvania Museum.
Forbes, R. J.1964. Studies in ancient technology,vol. 1. Leiden: E.J. Brill.
Montero, S. A.1974. Un nuevo soporte para pinturas murales. Boletin INAH (Instituto Nacional de Arqueologia e Historia) 10: 27–34, English abstract in Art and Archaeology Technical Abstracts 15(1978) no. 151479, BCIN (Bibliographic Database of the Conservation Information Network) no. 52515.
Moorey, P. R. S.1977. What do we know about the people buried in the Royal Cemetery? Expedition20:24–40.
Woolley, C. L.1934. The Royal Cemetery. Vol. 2of Ur excavations. Joint Expedition of the British Museum and of the Museum of the University of Pennsylvania to Mesopotamia.London: Oxford University Press for the Trustees of the Two Museums.
AUTHOR INFORMATION
VIRGINIA GREENE has an M. A. in anthropology from the University of Pennsylvania and a diploma in the conservation of archaeological and ethnographic materials (with distinction) from the Institute of Archaeology, University of London. She has been head of the Conservation Laboratory at the University of Pennsylvania Museum, Philadelphia, since 1972. Remaining a generalist out of both choice and necessity, she treats a wide variety of archaeological and ethnographic objects and is involved in the planning and oversight of storage renovation and other construction projects at the University Museum. Address: Conservation Laboratory, University of Pennsylvania Museum, 33d and Spruce Sts., Philadelphia, Pa. 19104
Section Index |