THE ANCIENT EGYPTIAN COLLECTION AT THE MUSEUM OF FINE ARTS, BOSTON. PART 2, A REVIEW OF FORMER TREATMENTS AT THE MFA AND THEIR CONSEQUENCES
SUSANNE G�NSICKE, PAMELA HATCHFIELD, ABIGAIL HYKIN, MARIE SVOBODA, & C. MEI-AN TSU
6 STONE
6.1 CLEANING
It is clear that stone artifacts were cleaned early in the history of the museum, but specific cleaning methods prior to the 1970s are undocumented. During the 1970s, stains were typically removed from limestone and sandstone with a warm solution of Calgon, followed by a mixture of equal parts of methylene chloride and ethylene glycol. Poultices of attapulgite clay mixed with organic solvents were also used for stain removal. Dilute hydrochloric acid is documented for the removal of calcareous encrustations from sandstone.
Granite statuary may have been polished with a mixture of water, Calgon, and a silica-based polishing compound, although it is unclear if this technique was specifically used on Egyptian granite. Vermarco, a marble cleaning solution, also may have been used on the collection.
Dry-cleaning techniques, such as eraser crumbs and chemical sponges, as well the use of alcohol, acetone, and emulsions of nonpolar solvents with limited water, became preferred methods of removing dirt and grime in the 1980s.
Fig. 13.
Pottery coffin (fig. 11), after treatment. Courtesy of Nina Vinogradskaya, 1998
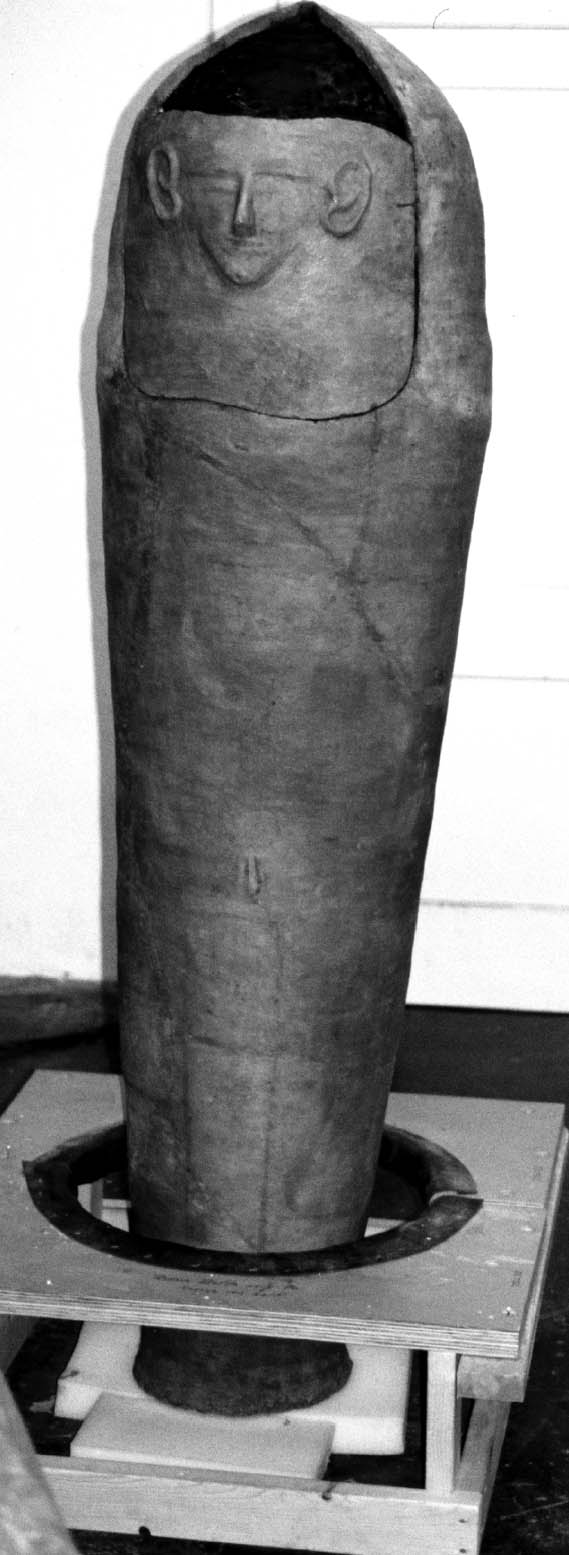 |
6.2 DESALINATION
There is no clear evidence that porous stone artifacts were desalinated in the field or in the museum in the early 20th century. However, desalination of stone of limestone and sandstone was probably occasionally undertaken, as it was advocated in the literature (Petrie 1904; Lucas 1932).
Sandstone and limestone sculptures were desalinated by aqueous immersion in the 1970s, although details, such as length of immersion and quantity of water, were not recorded. Desalination was terminated when chlorides were no longer detected using a silver nitrate spot test. On some occasions, treatment records indicate that desalination was ended prematurely due to pigment loss and/or structural damage to limestone. Poultices of cotton pulp and water were also used for salt extraction from limestone and sandstone. Apparently in a response to problems that arose from soaking, stone artifacts were tested for the presence of water-sensitive mineral inclusions prior to desalination in the early 1980s. Currently, desalination by water immersion is not performed on stone artifacts, and attempts to reduce soluble salt activity are made through management of the environment.
Although water immersion of stone artifacts had the significant benefit of reducing soluble salts, one of the primary factors of stone decay, the process could significantly jeopardize the structural integrity of the stone as well as disrupt pigmented surface decoration. Immersion of the Nefermaat and Atet limestone relief fragments (MFA Eg. Inv. 40; Petrie 1892) in the 1970s caused swelling of clay deposits, internal cleavage, and, possibly, overall softening of the stone. In 1985, a planning grant from the National Endowment for the Arts funded investigations into the mineral composition of the stone as well as potential consolidation with silanes, acrylic resins, or a mixture of the two. Due to both the magnitude of the project and the lack of a totally satisfactory treatment procedure, treatment was postponed. Currently, treatment of this important relief is being reconsidered. Due to advancements in the engineering of structural supports, the internal structural problems will be addressed through a detachable mounting system that surrounds and supports the fragments individually. Delamination and flaking of the surface will be consolidated with Paraloid B-72. Most important, exhibition and storage in a controlled environment are considered critical for the long-term well-being of the reliefs.
6.3 CONSOLIDATION
Review of museum records clearly demonstrates that the primary challenge of stone conservation over the last century has been the treatment and subsequent re-treatment of unstable stone surfaces. Powdering, flaking, and sugaring surfaces occur on limestone and sandstone artifacts due to the presence of soluble salts and/or poor cementation of particles. Additional internal structural problems may arise from cracking along bedding planes, swelling of clay deposits within the stone matrix, and intergranular cleavage, the latter a condition most commonly observed in granite. Attempts to stabilize these conditions through impregnation with various adhesives have had mixed success. In most cases they appear to have been beneficial, if not mandatory, for short-term preservation, but in many other cases consolidation has proven to be detrimental for long-term stability.
Wax, shellac, and natural resins have been identified as early consolidants of limestone and sandstone artifacts. Possibly some of these treatments were carried out in the field. Cellulose nitrate was used as a consolidant in Giza, and it was used at the museum into the 1970s, particularly to consolidate pigmented limestone and sandstone surfaces prior to desalination.
PVAC resin was the favored stone consolidant in the 1970s. A dilute solution, usually in toluene, was routinely used on sandstone and limestone, both as consolidant for actively spalling surfaces and as a precautionary measure for stable pieces that did not yet show signs of salt efflorescence. Nubian granite statues and stelae that showed delamination and networked cracking were stabilized with thicker concentrations of PVAC, which acted as both a consolidant and a gap filler. Elmer's Glue-All was also used as a stone consolidant. Sometime in the history of the museum, flour-based wallpaper paste was also used to consolidate flaking limestone and sandstone artifacts. Finally, soluble nylon has also been encountered on spalling limestone reliefs.
During the 1980s and 1990s, many new materials were investigated as possible stone consolidants. Vacuum impregnation of poorly cemented sandstone with Paraloid B-72 was implemented in the late 1970s and early 1980s. Methyl methacrylate monomer, polymerized in situ with ultraviolet radiation, was used to consolidate sandstone in the early 1980s. In the later 1980s, in response to the lack of information on the consolidation of polychromed stone sculpture, a study was undertaken (Mangum 1986) on the consolidation of a pigmented Meroitic sandstone triad (MFA 21.11808). Methyl triethoxy silane was chosen as a consolidant for the poorly cemented sandstone sculpture, following consolidation of the pigmented surface with gelatin. In 1992, after extensive consideration and testing, ethyl silicate was successfully used to consolidate a monumental Nubian sandstone coffin bench and chapel wall (MFA 23.868, 24.1793), which in part had been previously consolidated with methyl methacrylate monomer.
Consolidation with materials favored earlier, such as shellac, natural resins, and wax, has caused notable darkening of surfaces, a condition that often warrants their later removal. Wax has the additional drawback of attracting dirt and grime, and if applied thickly forms an impermeable layer, which causes further structural decay with the onset of soluble salt activity.
Over time, cellulose nitrate typically takes on a dark gray appearance and, if applied heavily, forms a thick, glossy layer that has a tendency to delaminate as the result of shrinkage and/or soluble salt efflorescence. Although cellulose nitrate remains soluble in many polar organic solvents, its removal is complicated by the presence of original pigment, which can be disrupted by dissolution of the resin and mechanical action. Similar problems have been observed on objects treated with wallpaper paste.
The bust of Prince Ankhhaf (MFA 27.442; Bolshakov 1991), a lifelike portrait composed of painted gypsum applied over carved limestone, illustrates the ongoing struggles with cellulose nitrate in relation to soluble salt activity. Correspondence among Reisner, Smith, and Dunham in 1927, two years after the bust was excavated, reveals that Lucas had consolidated the bust with celluloid in Egypt (fig. 14). By April 1927 the bust had been almost completely overpainted (fig. 15), presumably prior to Lucas's consolidation. The bust came to Boston in the summer of 1927, and shortly after its arrival was placed in a case with deliquescent salts as an effort to curb soluble salt activity. In a letter to J. L. Smith from September of that year, Dunham noted that the “celluloid coat has been lifted in small patches and bubbles, together with the surface layers of the paint” (fig. 16; Dunham 1927). He attributed this condition to “extreme changes in humidity and temperature” that occurred before the bust was placed in the desiccated environment. He noted that the surface appeared shiny and called “the celluloid coating a mistake.” It is possible that the condition of the Ankhhaf bust prompted Lucas to warn,“An excess of celluloid (i.e. too strong a solution or too many coats of a dilute solution) on certain painted objects, especially tempera paintings on clay plaster, may cause the paint to crack and to become raised up in small saucer shaped fragments over the whole surface” (Lucas 1932, 42–43).
Fig. 14.
Bust of Prince Ankhhaf, condition after excavation. Giga, Mastaba tomb G 7510, 4th Dynasty, 2555–2532 B.C., painted plaster, limestone, height 50.48 cm. MFA 27.442. Courtesy of Harvard University–MFA Expedition, 1925, neg. B5609
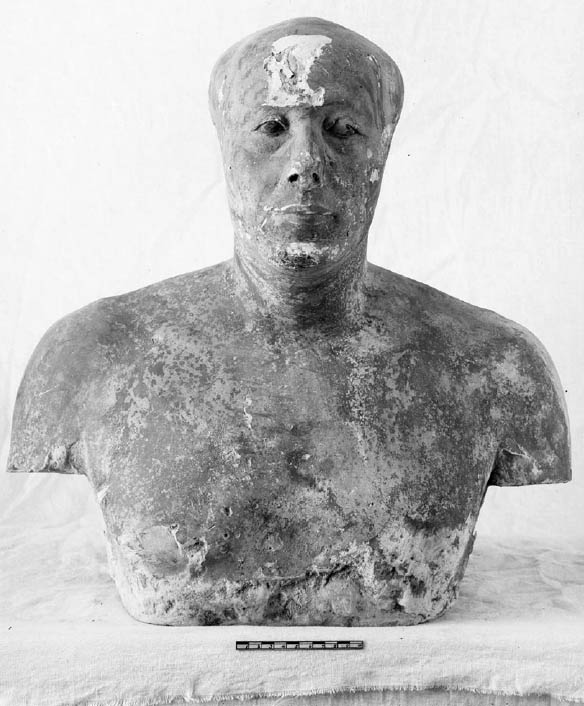 |
By the summer of 1938, the celluloid coating had begun to peel. Young reduced the coating, apparently without disruption of the underlying pigment, and designed the first documented microclimate in the museum. A pump, installed in the bottom of the display case (fig. 17), circulated internal air over a tray of calcium chloride. The humidity was lowered from 60 to 30% RH, where it remained for some time. The bust has required minor consolidation since that time but has remained remarkably stable under current gallery conditions.
Over the past 30-plus years, PVAC coatings have remained easily reversible and have not significantly discolored. Exudation of the resin under elevated temperatures has been observed on heavily consolidated pieces, such as a Nubian granite stele (MFA 23.736). This object had been consolidated with 18.9 liters of PVAC in the 1970s due to severe internal cracking.
Fig. 15.
Bust of Prince Ankhhaf (fig. 14), overpainted. Courtesy of Harvard University–MFA Expedition, 1927, neg. A4651
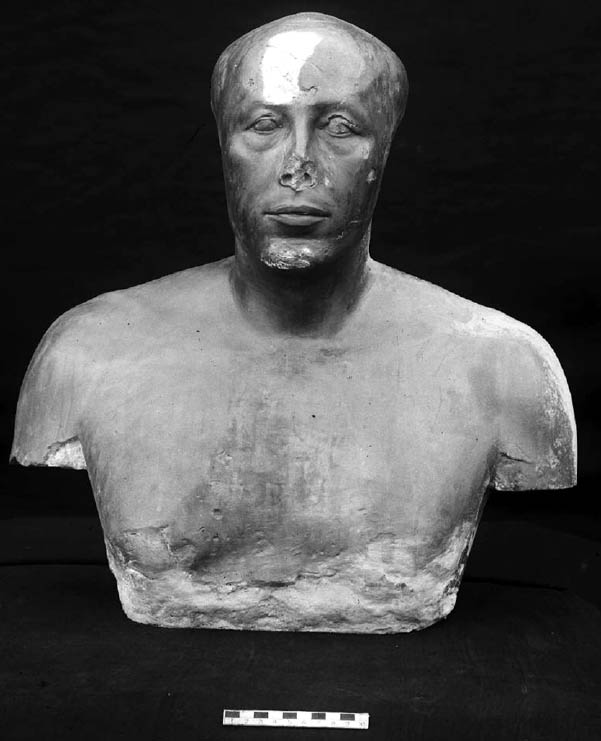 |
Some other efforts to consolidate Egyptian stone have been problematic. Approximately 10 years after a set of sandstone relief blocks (MFA 24.1793) were consolidated with methyl methacrylate polymerized in situ, small beads of the consolidant (unpolymerized monomer) were visible along the sides of the blocks, and white residues, possibly tidelines of resin, were noted in many areas. External surfaces were reportedly stable, while internal areas were still sugary and in need of stabilization. Reconsolidation with ethyl silicate 10 years later was not apparently adversely affected by the presence of monomer remaining from the earlier treatment.
6.4 RECONSTRUCTION
Museum practices for mending stone artifacts appear to have paralleled those used in the field. Mucilage, animal glue, and plaster were most likely used as adhesives until the introduction of polyester and PVAC resins. It is interesting to note that the use of shellac and cellulose nitrate to mend joins has been found on a surprisingly low number of Egyptian stone artifacts in the museum's collection.
Fig. 16.
Detail of bust of Prince Ankhhaf (figs. 14, 15), showing curling celluloid and overpaint. Courtesy of � Museum of Fine Arts, Boston, fall 1927
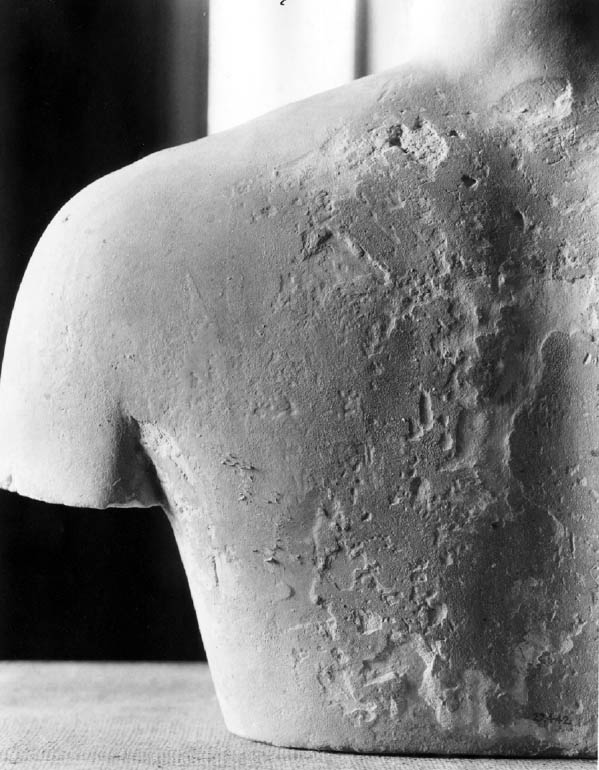 |
PVAC resin came into use as an adhesive in the 1970s. At this time epoxy and polyester resins were reserved for structural joins of large stone pieces, many of which were pinned with brass dowels. Treatment records also document the use of Dekadhese and Hydro-Stone mixed with Elmer's Glue-All for structural mends. In the 1980s, Paraloid B-72 and Paraloid B-48N began to replace PVAC for mending small artifacts. The practice of priming of edges with Paraloid B-72 prior to the application of polyester or epoxy resins was also adopted during this time. By the early 1990s, the employment of stainless steel pins and structural epoxies for joining or mounting large stone sculpture became standard practice.
Fig. 17.
Bust of Prince Ankhhaf (figs. 14–16), installed in gallery with environmental controls. Courtesy of � Museum of Fine Arts, Boston, 1939, neg. A7417
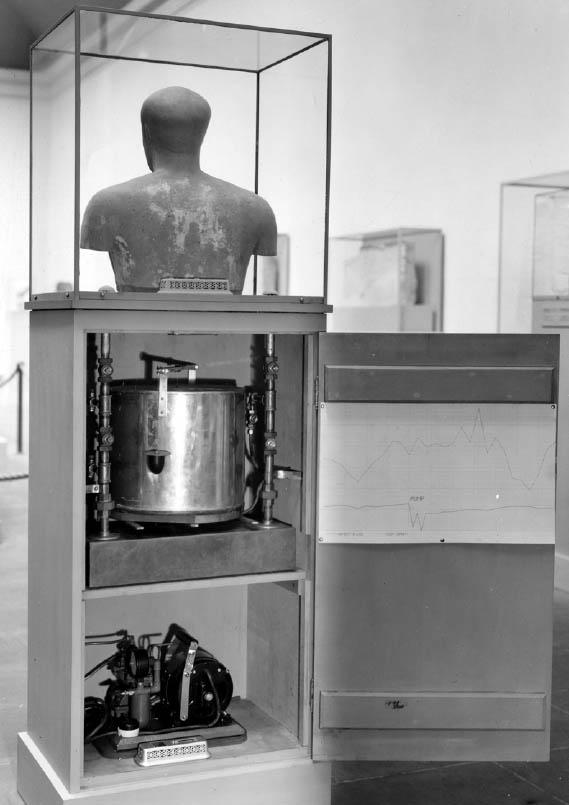 |
Artifacts mended with mucilage, animal glues, and barium sulfate cement have usually required retreatment. Mucilage and animal glue tended to shrink and become brittle. The barium sulfate cement's aging characteristics vary. In many instances, it has retained its strength and cohesion, but in others it has weakened and begun crumbling. Due to its resistance to water, acid, and organic solvents, this cement is extremely difficult to soften, leaving mechanical removal the most practical treatment option for reversal.
Plaster and Hydro-stone are the most commonly encountered fill materials. Wax was used to restore translucent calcite (Egyptian alabaster) vessels and statuary, probably in the first quarter of the century. Additionally, PVAC mixed with kaolinite as well as with plaster has been identified on some artifacts.
In the mid-1990s, a thermoplastic mixture composed of PVAC, ethylene acrylic acid copolymers, and antioxidants (G�nsicke and Hirx 1997) was used as a fill material for translucent stones such as calcite and marble. However, due to its low glass transition temperature, slumping of large fills has occurred, and its use is now reserved for small, shallow fills. Currently, bulked Paraloid B-72 fills and detachable epoxy fills are common choices for stone artifacts.
6.5 COATING
At some point in the history of the MFA, several of the stone masterpieces sculpted from graywacke were coated, possibly in preparation for mold-making in 1942 (see below). The large-scale pair statue of King Menkaure (Mycerinus) and a Queen (MFA 11.1738; Reisner 1931) and the smaller triad of King Menkaure (Mycerinus), Hathor, and the Hare Nome (MFA 09.200) both have a thin coating of an acetone-soluble resin that may be PVAC.
In the case of the triad, the coating is discontinuous due to wear and handling and has developed a cloudy, whitish appearance in some areas. Surface cleaning can be done only with water due to the sensitivity of the resin. Removal of the coating can be accomplished with acetone but is complicated by the presence of original pigments, which in part have been consolidated by the resin. Additionally, the saturated appearance of the sculpture, which is favored by many, would drastically change as a result of reduction of the coating. Due to these considerations and the overall stability of the sculpture, no re-treatment has been carried out.
6.6 MOUNTING AND INSTALLATION
Up until the mid-1960s, wall reliefs were installed by stacking individual blocks on top of each other, typically held together with mortar or plaster and supported by a wooden frame and bricks. Stone reliefs and other architectural elements were also set into walls with bricks, mortar, plaster, and/or Portland cement, often without a moisture barrier. In several cases, the backs of large reliefs were removed in order to reduce weight and simplify installation. In 1915, at least two pieces (MFA 89.557, 90.235) were installed after “useless granite” was sawed from their backs (Whitehill 1970, 283).
In response to rigorous exhibition schedules and a need for more portable mounting systems, new approaches to the installation of large-scale stone artifacts were developed in the 1980s. Freestanding, self-supporting steel and aluminum frames that support blocks individually are now used instead of immobile installations. The reconstruction of the Koptos Gateway (MFA 24.1632–33;Thomas 1995), a monumental Ptolemaic gateway comprising 25 sandstone blocks, marked the first large-scale mount to be designed in consultation with a structural engineer. The project, initiated in the early 1990s in preparation for a three-venue traveling exhibit, required a portable mount that could support more than 907 kilograms of stone in an earthquake zone. Since this time, collaboration with structural engineers on the design of portable earthquake mounts has become standard practice in the treatment of large-scale sculpture.
6.7 REPLICAS
In the spring of 1942, due to a growing threat of attacks on Boston by German U-boats, significant pieces in the collection, such as the bust of Ankhhaf and the pair statue of King Menkaure (Mycerinus) and a Queen, were taken off-site and replaced with plaster replicas produced by the Conservation Department (MFA 1944). The composition of plaster and the painting techniques were documented, but the mold-making materials and release agents were not. It is suspected, however, that the mold-making process was the impetus for coating both the pair statue of King Menkaure and a Queen and the triad of King Menkaure, Hathor, and the Hare Nome.
The sale of replicas in the museum shop became popular during the 1970s and 1980s. Treatment notes by Nichols indicate that Egyptian limestone objects were brushed with petroleum jelly prior to application of the silicone rubber mold material. The petrolatum, applied primarily to prevent staining from silicone oil, was then reduced with hexane. In the 1980s, Paraloid B-72 replaced petroleum jelly as an isolating layer. Mold-making efforts have affected later treatments, as remnants of silicone rubber trapped within fine crevices have been documented.
|