ANALYSIS OF GYPSUM-CONTAINING LIME MORTARS: POSSIBLE ERRORS DUE TO THE USE OF DIFFERENT DRYING CONDITIONS
A. ELENA CHAROLA, & SILVIA A. CENTENO
3 RESULTS AND DISCUSSION
3.1 GYPSUM
The results, expressed as millimoles of water per mole of gypsum (mM water/M gypsum) for the drying of pure gypsum powder under different conditions and the subsequent moisture absorption for those samples dried at ~0% RH and at 105�C upon 20-day conditioning at 75% RH, are presented in table 1.
The results clearly show that under normal laboratory conditions, gypsum dehydrates partially, i.e.,
Table .
Moisture Loss Expressed as mM Water/M Gypsum
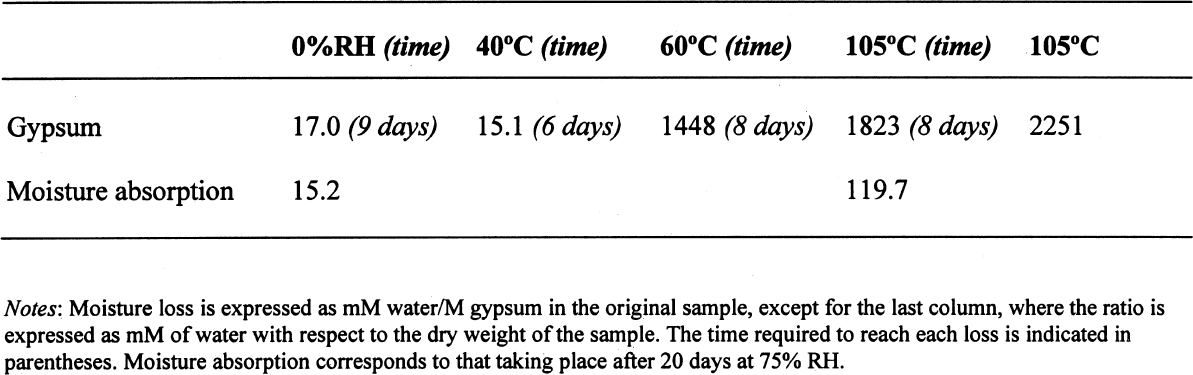 |
converting to the metastable hemihydrate CaSO4.1/2H2O at 60�C, and dehydrates most probably into the thermodynamically stable phase anhydrite CaSO4 when heated to 105�C. The reaction can be written as:
The sequence of these dehydration reactions has been previously observed and described (Macdonald 1953; Palache et al. 1966; Deer et al. 1975; Ullmanns 1976). Gypsum only lost sorbed moisture when kept at ~0% RH, and this amount was recovered when conditioned at 75%RH. The sample dried at 105�C apparently did not reabsorb any hydration water.
3.2 GYPSUM-CONTAINING MIXTURES
The results of the gypsum mixtures with powdered calcite or silica, as well as of the control samples, are presented in table 2.
The first interesting observation is that the samples dried at 105�C lost practically the same amount of moisture as those at 60�C, or even less. These results could be explained by the fact that these samples were dried together with the abovementioned gypsum sample, and thus the high amount of moisture lost by this material in addition to that lost by the mixtures prevented further desorption or dehydration from these last samples during the week-long drying. It appears that although the oven does have a ventilation opening and equilibration of absolute humidity with the environment may take place when the door is opened, this condition is not sufficient to eliminate the released moisture when there are many samples present (in our experiment, five samples were in the oven simultaneously). The ease of moisture absorption or desorption depends on the nature of the sample, and since it has been shown that the joint presence of a hydrating salt and a nonhydrating material enhances moisture absorption (Charola and Weber 1992), it appears that it may also presumably hinder dehydration of the hydrated salt.
At ~0% RH, calcite powder loses the same amount of moisture as at 60�C, whereas the silica powder shows that it requires some heating to lose the sorbed moisture.
The weight loss and gain of the samples (previously dried at 60�C) redried for 11 days at 105�C and re-exposed to laboratory conditions for four days, the time it took for samples to re-equalize with ambient conditions, are presented in table 3.
Since these samples had been previously dried at 60�C, the amount of moisture lost corresponds to the difference in moisture loss between these two drying temperatures. Gypsum nearly recovered all the moisture lost during the 11-day drying, corresponding to
Table .
Moisture Loss Expressed as mM Water/M Material in the Original Sample
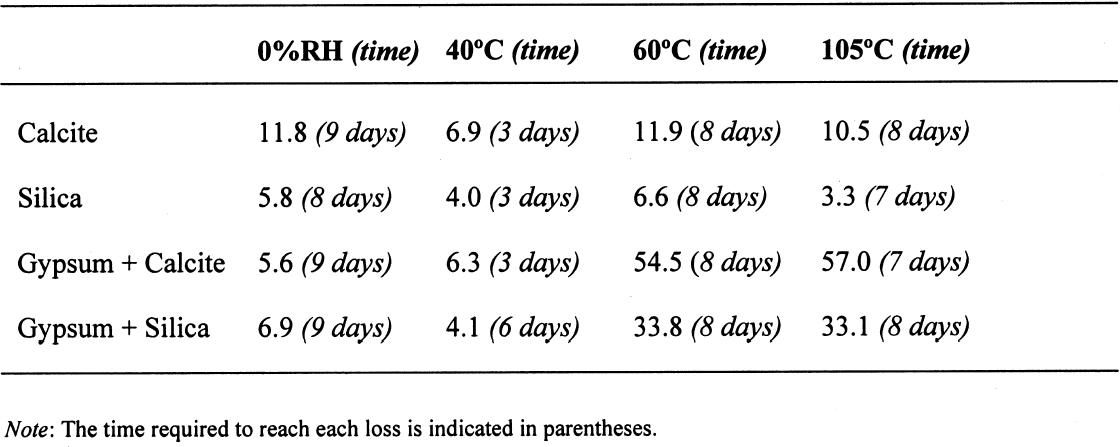 |
Table .
Amount of Moisture, Expressed as mM Water/M Material, Lost during 11 Days of Drying at 105�C and Gained upon Re-exposure to Laboratory Conditions during Four Days, by Pure Gypsum or Mixed with Calcite or Silica
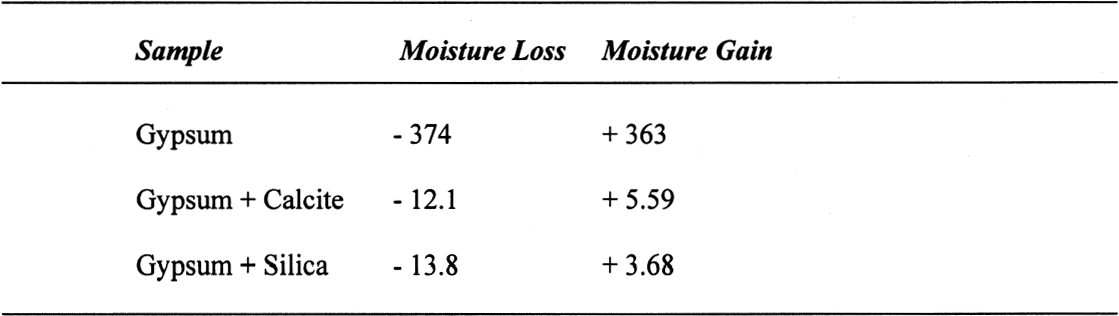 |
the loss of the 0.5 molecule of the hemihydrate (the value is not exactly 500 because the weights are not standardized against the dry weight—see table 1) and suggesting, by the ease of rehydration, that the anhydrite obtained was the metastable form, called soluble anhydrite or γ-CaSO4, which rehydrates readily to hemihydrate (Deer et al. 1975). However, it contrasts significantly with the previously obtained data of the sample set at 75% RH (table I). In this case, it would appear that the stable anhydrite form, or β-CaSO4, is formed, since it does not rehydrate that easily. Conditions influencing this dehydration are probably the varying amounts of moisture present in the oven during drying.
3.3 GYPSUM-AND SALT-CONTAINING MIXTURES
The samples containing soluble salts, preconditioned at 75% RH and then dried in a desiccator at ~0% RH, arrived at their minimum weight in two days. This result can be explained by the loss of absorption power of the desiccant agent, even though there was no visual color change in the cobalt salt used as indicator. Cobalt salts will change color from blue (dehydrated state) to pink (hydrated state) when the relative humidity is over 30%.
The corresponding samples dried in the oven, at 40�C and 105�C, took about seven to eight days to reach this point. The moisture loss, expressed as the ratio of millimoles of water to the total number of moles of material in the original sample, is presented in table 4.
As indicated previously, the samples in the desiccator did not lose all their moisture, although the moisture loss follows the overall trend.
The moisture loss for the control sample is equivalent to that lost “theoretically,” as calculated
Table .
Moisture Loss Expressed as mM Water/M Material in the Original Sample
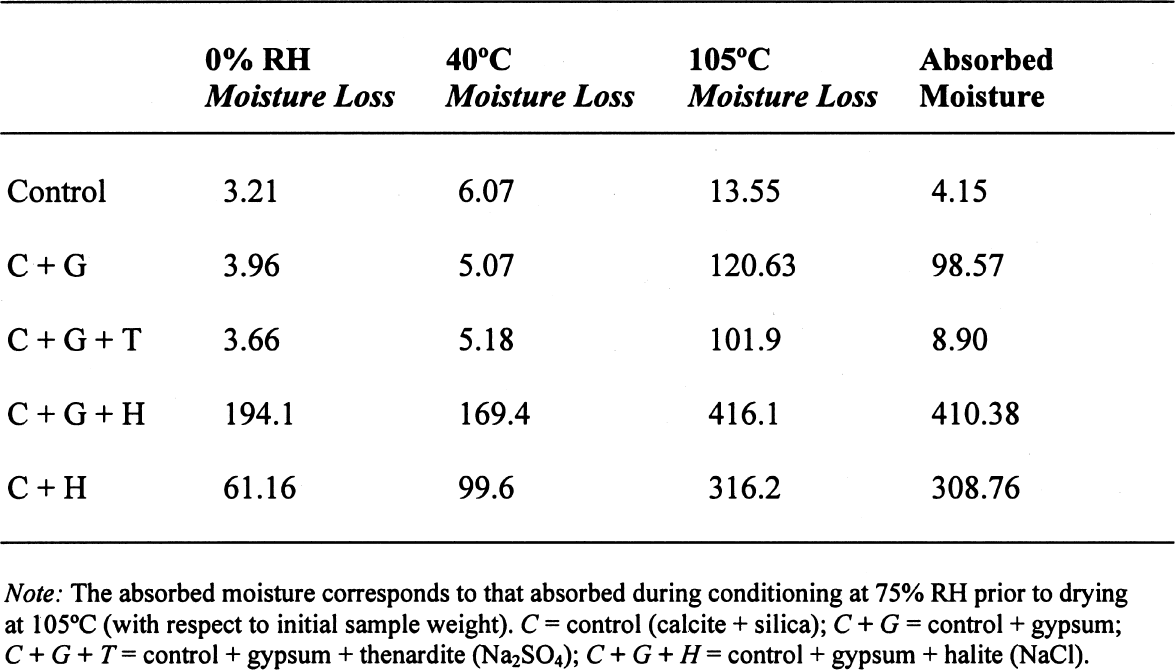 |
from the moisture loss of the individual calcite and silica samples reported in table 2 (see next section for an example of the calculation)—that is, approximately 8.88 mM/M sample, plus the moisture absorbed during conditioning at 75% RH.
A similar behavior is observed for the sample containing gypsum, the difference between the lost and absorbed moisture reaching some 22 mM water/M sample, fairly close to the measured 17 mM water/M gypsum as reported in table 1. This finding clearly shows that gypsum does not dehydrate completely at 105�C when mixed with another material and if a relatively high amount of water vapor is present in the oven, as discussed for the previous samples.
For samples containing NaCl, the hygroscopicity of sodium chloride (NaCl) at 75% RH is clearly evident, and the amount of moisture lost corresponds practically entirely to the moisture sorbed by this salt.
Finally, the presence of sodium sulfate in the mixture reduces by nearly tenfold the amount of moisture absorbed, though the amount lost by heating is similar to the sample without this salt. This unexpected behavior requires further research that is outside the scope of the present article.
3.4 ANALYSIS OF ERRORS
From the data in tables 1 and 2, the amount of sorbed moisture for the different powders can be calculated. For example, silica powder lost approximately 7 mM of sorbed water per mole of silica, while gypsum lost some 17 mM of water per mole of gypsum. The sample, weighing 3.09719 g, was constituted of 0.15486 g of gypsum and 2.94233 g of silica, corresponding to 0.8994 and 48.9898 mM, respectively. The theoretical loss of sorbed moisture would correspond to 0.35973 mM, the sum of 0.01529 mM of water from the gypsum and 0.34293 mM of water from the silica. This sum corresponds to a calculated weight loss of 6.46 mg. In the case of calcite, 12 mM of water per mole of calcite were used for the calculations. The results obtained for these calculations, as well as the actual measurements obtained, are presented in table 5.
The difference obtained between the calculated
Table .
Comparison of Measured and Calculated Weight Losses
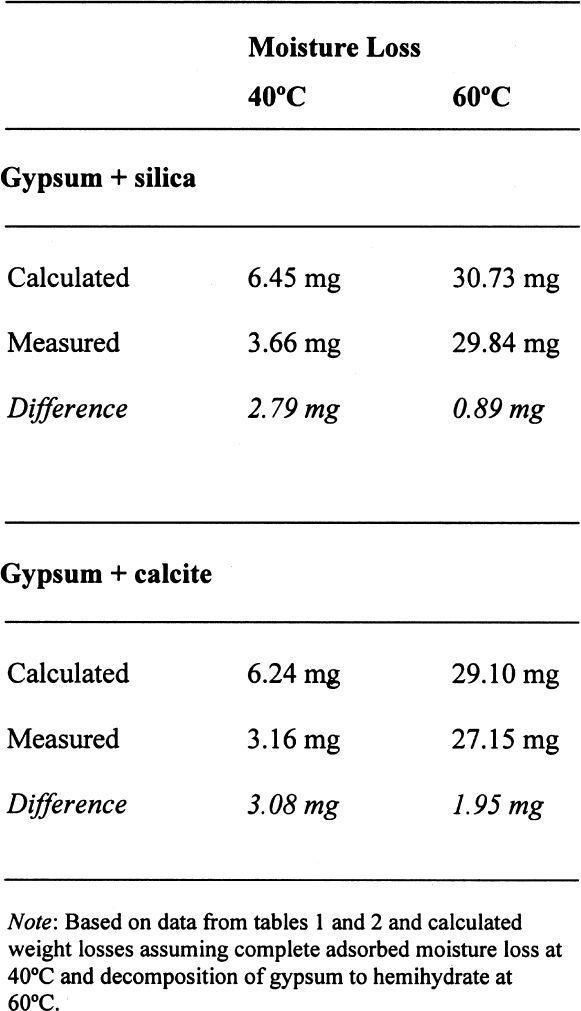 |
and the measured amount differs by around 3 mg for samples dried at 40�C, indicating that the sample has not dried completely. Considering that the total weight of the sample is around 3 g, this difference represents a relative error of approximately 0.1%.
On the other hand, for samples dried at 60�C, if the decomposition of the gypsum is taken into account, the relative error decreases to around 0.05%, taking an average difference of 1.5 mg. However, if the decomposition of the gypsum is not taken into account, i.e., only assuming loss of adsorbed water as calculated for 40�C, the differences obtained would be –23.39 mg for the silica mixture and –20.91 mg for the calcite mixture, corresponding to an overestimation of the moisture content and increasing the relative error tenfold (~0.7%).
A similar analysis can be done for some of the samples reported in table 4. If the weight loss is calculated from the initial weight of the sample, i.e., prior to conditioning, the data presented in table 6 are obtained.
While the control samples behave as expected, those that contain gypsum do not follow a predictable path. The gypsum present, dried at 105�C, loses some hydration water, and from the data obtained, it would appear that approximately one-half of the gypsum present dehydrates to the hemihydrate. This introduces a relative error of 0.3%, whether it is assumed that the gypsum does or does not dehydrate to hemihydrate. Under the same conditions, the control sample shows a relative error of 0.01%.
How critical these errors are depends on the accuracy with which the mortar analyses are carried out. Comparing the methods mentioned in the introduction, table 7 can be constructed.
All methods mentioned use precisions that result in relative errors below the one observed, resulting either from insufficient drying or from gypsum decomposition.
|