OVERLAY WITH A DIFFERENCE: STRONG SUPPORT-THREAD EDGE FINISH FOR TETEX TR
REN�E DANCAUSE
ABSTRACT—Overlays are commonly used for securing the entire surface or parts of a textile artifact in poor condition. They are usually sheer textile supports placed on the face of a textile and are often combined with underlays. The overlay technique is more successful if applied to a surface having no three-dimensional elements. However, some flags such as guidons have battle honors—thick, disproportionately heavy crests that protrude from the flat plane of the ground fabric, usually of silk. One such military flag in a weak, light-damaged state was given a unique overlay support.What follows is a description of a practical technique for fashioning strong finished edges by hot-melt-cutting Tetex TR fabric with a preinserted support thread. Conservators in disciplines such as ethnographic and objects conservation may find the instructions for making this Tetex TR overlay useful for treating composite artifacts with textile components.Polyester Tetex TR has excellent physical properties, but if used without an appropriate finishing technique, the edges fray dramatically, and its usefulness in conservation is limited. The resulting custom-made overlay successfully accommodates the complex shape of the guidon battle honor crests while lying flat in contact with the ground silk, providing it with support. The focus of this article is the construction of a custom-made overlay that fulfills these unique requirements.
TITRE—Une variante � la technique du renfort frontal: une m�thode de finition des bords de Tetex TR. R�SUM�—Un renfort frontal est souvent utilis� pour stabiliser une oeuvre textile enti�re ou une partie d'une oeuvre en pi�tre �tat. Il s'agit g�n�ralement d'un textile transparent que l'on fixe sur le c�t� recto de l'oeuvre, souvent en combinaison avec un renfort dorsal (un doublage). Le renfort frontal donne de meilleurs r�sultats si l'oeuvre textile n'a aucun �l�ment tridimensionnel qui surjaillit de la surface. Cependant certains drapeaux, tels les guidons, ont des insignes de batailles qui jaillissent de la surface et qui sont �pais et tr�s lourds comparativement au tissu de fond, g�n�ralement en soie.Cet article d�crit comment un drapeau de ce genre, rendu fragile � cause de la photod�gradation, a �t� trait� au moyen de la technique du renfort frontal, laquelle a �t� adapt�e pour tenir compte du probl�me des insignes. On d�crit cette variante de la technique qui a �t� la cl� du succ�s du traitement, c'est-�-dire la mise au point d'une m�thode solide de finition des bords d'un morceau de Tetex TR. Celleci consiste � couper � chaud et � thermosouder les bords � l'aide d'un fil de renfort qu'on avait ins�r� au pr�alable � l'endroit requis. Cette technique peut �tre utile non seulement aux restaurateurs de textiles, mais aussi aux restaurateurs d'objets ou d'objets ethnographiques, lesquels sont souvent confront�s � des oeuvres composites faites en partie de textile.Le Tetex TR est un tissu en polyester qui poss�de d'excellentes propri�t�s physiques, mais dont les bords sont difficiles � finir, ayant tendance � s'effilocher facilement, ce qui limite l'utilit� de ce tissu en restauration. Comme le d�montre l'exemple qui en est donn�, la nouvelle m�thode d�crite dans cet article satisfait � ces deux exigences particuli�res: le renfort tient compte de la forme complexe des insignes du guidon tout en restant en contact intime avec la soie de fond, r�ussissant ainsi � bien la soutenir.
TITULO—Recubrir con una diferencia: C�mo usar hilo para crear una terminaci�n de orilla firme en Tetex TR. RESUMEN—Los recubrimientos son m�todos com�nmente utilizados para asegurar la superficie completa, o partes de un artefacto textil que este en condiciones precarias. Usualmente son soportes textiles transparentes que se ubican sobre la cara de un textil y son a menudo combinados con refuerzos por debajo. Esta t�cnica de recubrimiento es m�s exitosa si es aplicada a una superficie que no tenga elementos tridimensionales. Sin embargo, algunas banderas como los guiones tienen “honores de batalla,” que son emblemas gruesos, pesados que sobresalen en forma desproporcionada de la superficie plana de la tela de fondo, generalmente de seda. Una bandera en estado muy d�bil—producto de da�o por luz—fue tratada con un recubrimiento especial.Lo que sigue es la descripci�n de una t�cnica pr�ctica para lograr orillas firmemente terminadas por medio de cortado-fundido al calor de la tela Tetex TR con un hilo de soporte preinsertado. Los conservadores en especialidades tales como conservaci�n de objetos etnogr�ficos y artefactos pueden hallar de mucha utilidad las instrucciones para hacer este recubrimiento de Tetex TR que se puede utilizar para tratar artefactos compuestos que tengan componentes textiles.El poli�ster Tetex TR (llamado antiguamente Stabiltex) tiene excelentes propiedades f�sicas, pero si no se usa la t�cnica apropiada los bordes se desflecan en forma dram�tica y su utilidad en conservaci�n es limitada. El recubrimiento—hecho a medida—se acomoda exitosamente a la compleja forma de los escudos de honores de batalla del gui�n mientras descansa plano en contacto con la seda del fondo, otorg�ndole soporte. Este articulo describe en forma puntual la construcci�n de un recubrimiento hecho a medida que cumple con estas funciones espec�ficas.
1 INTRODUCTION
This investigation into hot-melt-cutting of polyester Tetex TR (formerly called Stabiltex), and consequently other sheer and heavier polyester fabrics, stems directly from the innovative work done by Fonda G. Thomsen (1988) on this topic. Thomsen used an electric wax pen to simultaneously cut and hot-melt-seal the raw edges of Stabiltex for applications such as seams and overlays. Along with other developments, her experimental work led her to conclude that overlays could be custom made for embroideries where the decorative stitching is left exposed, while protecting the ground fabric with the overlay. In a later article, Ann French (French and Gentle 1993) described how an overlay was constructed to support a section of a highly embroidered 17th-century textile having three-dimensional raised elements. She realized the usefulness of Thomsen's technique and successfully “heat-cut” the corresponding raised elements from the Stabiltex overlay. Thus the overlay lay flat on the textile, improving the overall appearance and supporting the weakened area of the artifact.
A second case history by Nicola Gentle (French and Gentle 1993) in the above article described the fabrication of an overlay to cover damaged silk damask from the counterpane of a state bed. The sheer fabric was first stitched in place, and after precautions were taken, the excess Stabiltex around the edges was hot-melt-cut away, in situ. The cut edges were then tucked under an ornamental braid. A variation of these techniques was used to prepare an overlay for a silk flag with applied crests in fine condition protruding from the extremely fragile light-damaged ground fabric.
2 BACKGROUND
The flag in question is the First Guidon of the Royal Canadian Dragoons (RCD), the first cavalry unit in the Canadian army, housed at Canadian Forces Base (CFB) Petawawa, Ontario1 (fig. 1). A guidon, from the French word guydhomme or “guideman,” is a small military flag used as a guide to the troops (Smith 1975; Sierksma 1980). The guidon was presented to the regiment in 1901 by the duke of Cornwall and York (later King George V) and was used in ceremonies and parades for years until the regiment was given its second guidon in 1919. The guidon embodies the sacrifices made in the service of Canada and is regarded as being unique and irreplaceable. The First Guidon was recently conserved in the Textile Laboratory of the Canadian Conservation Institute and will be exhibited periodically by the RCD at CFB Petawawa, Ontario.
3 DESCRIPTION
The guidon measures 77 cm (30 in.) by 113 cm (44� in.) and is swallow-tailed (split-fly) (fig. 2). It is made of a single layer of lightweight, tightly woven warpor weft-faced plain weave (rib) silk fabric. No selvage is present, and thus the identification of the rib as warp or weft is undetermined. The silk is now a dull greenish yellow color on the front. It has a central device, a circular appliqu� bearing the royal cipher of King Edward VII encircled by the regiment's full title, all couched in metallic threads on a fuchsia silk ground. An ornate colorful crown embroidered directly on the ground using silk threads surmounts the central device. Fleurs-de-lis embroidered in the same way appear one each to the right and left of the crown. The applied crests or “battle honors” are similar in shape to a scroll or ribbon (fig. 3) and refer to military campaigns. They are located directly underneath each fleur-de-lis and are constructed of heavy metallic embroidery threads. A silk-thread embroidered maple leaf appears on both the lower left and lower right sides. All of these motifs appear on the reverse of the flag as well. The book Old Colours Never Die: A Record of Colours and Military Flags in Canada (Dunbar and Harper 1992) features a before-treatment photograph of the First Guidon.
Fig. 1.
The First Guidon after treatment with its overlay in place. Accession number RCD 43/M233
 |
4 CONDITION
As previously mentioned, the guidon ground is in a weak physical state overall because of exposure to light. The resultant texture of the guidon silk is powdery. Originally a dark navy blue silk, as evidenced by the color of the reverse, it is now a pale green color on the front. Other colored features such as the front of the sleeve and the double-sided embroidery have also faded.
The incompatibility of the weakened lightweight silk ground and the disproportionately heavy applied ornamentation, such as the metal fringe, the tassels, the grommet, and the double-sided appliqu�s worked in heavy metallic threads, have caused vertical splits of the ground silk in some adjacent areas (fig. 4). In figure 4, the two black vertical lines immediately adjacent to the honor are deep creases of the ground. Small splits in the surrounding area appear dark because faded silk on the front powdered away, resulting in exposure of navy ribs. The silk ground was previously repaired in numerous areas by hand, using a darning technique with coarse navy silk threads, also evident in the photograph. These extensive repairs disrupt the aesthetic integrity of the whole. The threads used have also faded over time but are darker than the ground. In some areas, these repairs have failed, and further splits have formed adjacent to the original splits.
The guidon has tide lines visible on front and reverse surrounding the battle honors, casting a slight shadow underneath the crests. A gray cast is visible in areas where the metallic elements of the tassels and cord rubbed against the surface of the silk.
Fig. 2.
The First Guidon of the Royal Canadian Dragoons, before treatment
 |
5 CONSIDERATIONS
The full conservation treatment details are beyond the scope of this article, and only decisions relating to the purpose for and construction of the overlay will be discussed. Polyester Tetex TR was chosen as the overlay material for this artifact because it is durable, strong, and sheer, and of the colors available, the one chosen is ideal. It is also possible to hot-melt-cut the fabric to overcome raveling of straight or shaped raw edges. Typically, most textile conservators choose to use natural yarns and fabrics in conservation treatments, especially when treating items such as silk flags. In conservation today, inert synthetic materials, though less commonly considered, are used in the treatment of objects, especially if they have unique properties that, when applied, do not compromise the original. Thus, the merits of using a fabric such as Tetex TR in various applications are recognized for use by textile conservators and by conservators in other areas of the field who treat composite artifacts.
Fig. 3.
One of two battle honors (thick crests) that protrude from the flat plane of the flag, also showing tide lines
 |
Fig. 4.
Detail of the same battle honor as in figure 3 showing splitting resulting from weakened silk, and incompatibility of materials—for example, heavy metallic thread composing the battle honors applied to fine silk ground fabric. Previous repairs are also shown.
 |
Overlays are widely used in the conservation treatment of parts of or entire surfaces of textile artifacts that are in poor condition (Dancause 1996). Often a sheer fabric is used for the overlay, enabling one to view the extant textile underneath. However, the properties of such an overlay affect the color, pattern, and texture of the original. It is important that the overlay blend aesthetically and perhaps even compensate for loss of the remaining textile. The overlay serves to prevent further loss of the textile and, to an extent, unify uneven coloring of the original if it is stained. An illustration of this property is the previous repairs to the guidon. Where they were causing further damage, they were removed. The appearance of the flag was improved, but the ground under the repair threads had not faded to the extent of the rest of the flag. The overlay would assist to visually blend these areas to the other parts of the flag. Lastly, it is important that the overlay be light-weight, conform comfortably to the object, and be secured with a minimum of stitching or other attachment to the strongest areas of the artifact.
Specifically, in order for the overlay to lay in flat contact with the surface of this artifact, three areas of the overlay had to be hot-melt-cut away to accommodate the three-dimensional nature of the appliqu� and design motifs. These three areas correspond to the exact shapes of the two battle honors and the tassel grommet. In these cutout areas, the Tetex TR was required to have reinforced hot-melt-cut edges able to withstand manipulation, enabling minimal stitching to attach the overlay to the artifact in select strong areas. The method of hot-melt-cutting had to accommodate both complex curves and square edges of the shaped design motifs. To fulfill the considerations listed above, a technique was sought that enabled the hot-melt-cut edges of the Tetex TR to be stronger than simply by hot-melt-cutting alone. A support thread, therefore, was added to the Tetex TR before hot-melt-cutting. The support thread is not melted away; rather, it stays in situ, partially fusing with the Tetex TR, thus strengthening the cut and finished edge of the fabric.
Paradoxically, Tetex TR is sheer but uncommonly strong and resistant to degradation, yet its cut and unfinished edges are weak and vulnerable to fraying. The hot-melt-cutting process alone enables the fabric to resist raveling to an extent. However, because the interstices of Tetex TR are large compared to the width of the yarns, the melded junctures are fine and remain fragile. Objects such as the guidon—having disproportionately heavy motifs adjacent to light-weight degraded silk—that require handling such as mounting or stitching require an overlay with edges adequately resistant to fraying. A support-thread edge finish on a Tetex TR overlay is more equal in strength and resistance to Tetex TR itself.
When the overlay with the support-thread edge finish on Tetex TR is stitched in place, a small, discrete, invisible stitch is taken. A deeper stitch would be needed to prevent breakage of the finish if the edge were hot-melt-cut alone. For some applications, the strength of the cut edge is less of an issue, such as when the melded edge can be tucked under another textile element. In such cases, stitches can be taken farther away from the melded edge, leaving the edge finish undisturbed. This technique was not possible for the guidon overlay.
6 REQUIRED MATERIALS AND TOOLS
The use of the materials and tools listed here will be discussed in detail in the following section: Mylar; marker; masking tape; polyester Tetex TR; polyester thread; curved or straight sewing needles; Teflon-coated fiberglass; hot spatula with pointed head; gripping tweezers; knife or scalpel.
7 STEP-BY-STEP INSTRUCTIONS
7.1 PREPARING THE MYLAR TRACING
Mylar is laid on the artifact, and the image or design motif to be transferred is traced using a marker (fig. 5). This process differs from that of Thomsen, who laid a thin sheet of glass on the object, placed the Tetex TR over the glass, and hot-melt-cut the fabric with the aid of a ruler. Similarly, French used sheet glass that was raised so as not to weight the textile and traced the image onto the glass. The guidon has three-dimensional elements protruding from the surface up to 5 mm (1/4 in.) in areas. In this case, because of the size of the flag, the use of glass was considered too hazardous, so Mylar was used to do the tracing instead.
The Mylar tracing is a pattern used in transferring the motifs to the Tetex TR, and it can also be retained as a documentary record of the object after the completed treatment. Registration marks such as the outer edges of the artifact are also traced, and the tracing is labeled as to its orientation in case it is accidentally turned to the wrong side. The Mylar tracing is taped to a table surface with masking tape along the four edges.
It should be noted that in the case of the guidon, only the design motifs protruding from the surface of the flag (the appliqu�s and grommet and not the embroidered motifs) were to be accommodated by the overlay. The other embroidered motifs were not obscured by the Tetex TR overlay and so were left covered by the sheer fabric, because it was judged too difficult to hot-melt-cut more than the required motifs from the Tetex TR, and, visually, the covered motifs were aesthetically acceptable despite Tetex TR's slight opacity. The fewer the openings in the overlay, the more it is able to provide overall support to the flag. Supplementary stitching of the overlay to the ground was possible in the stronger areas of the silk flag protected by the embroidery.
Fig. 5.
Tracing of one of the battle honors, one-half scale.
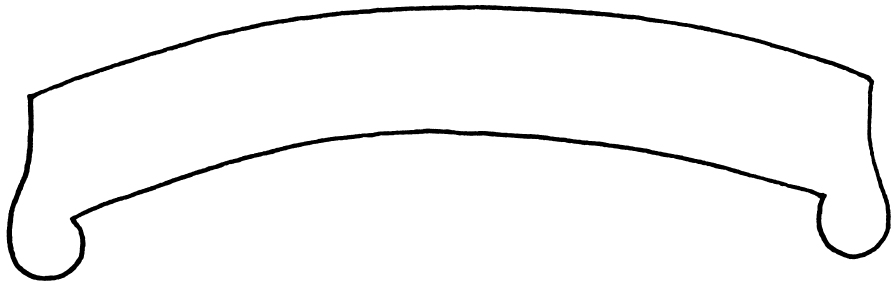 |
Polyester Tetex TR was chosen, in this particular case, as the overlay material. However, other polyester fabrics ranging from sheers to denser, more opaque fabrics work equally well using this edge-finishing technique. The purpose of the overlay, whether it is to cover and support the ground or, conversely, individual motifs, and the requirements of the artifact dictate which polyester is chosen. After several polyester fabrics were experimented with, the following three were considered as possibilities: an open-weave polyester: 16 threads/cm warp and weft (40 threads/in.);Tetex TR: 25 threads/cm warp and weft (62 threads/in.); and a denser fabric: 51 threads/cm warp (128 threads/in.) and 42 threads/cm weft (104 threads/in.). The open-weave fabric and melded edge were considered too weak, and the denser fabric visually obscured the flag despite its strong edge finish. Of these, polyester Tetex TR was the only fabric available in the right color. Ideally, the fabric chosen should have no dents or fold lines.
7.2 PRESTITCHING TETEX TR TO REINFORCE HOT-MELT-CUT EDGES
A generous piece of polyester Tetex TR fabric is cut, and the four outside edges of the fabric are bound with masking tape. The taped edges aid in manipulation of the Tetex TR during the “fittings” described below. Labeling the masking tape edges with a marker indicates the orientation of the overlay. The taped fabric edges are retained throughout, enabling one to add and remove additional masking tape to hold the Tetex TR to the table, necessary for each fitting, thus facilitating working with the fabric. Preparing the Tetex TR in this way ensures better results for the difficult-to-manage fabric by assisting in the alignment of the grain line in the next step.
The Tetex TR is taped down taut, on grain, to the table over the Mylar tracing, in preparation for stitching of the support thread (fig. 6). It is secured taut to the table because otherwise the Tetex TR shifts while working and it is impossible to acquire the precise placement of the design elements to be transferred to the Tetex TR by stitching. The corner of a table is used to aid in aligning the Tetex TR warp and weft threads. The placement of the Tetex TR is marked on the table with a pencil for future reference, as hot-melt-cutting of more than one design motif will be done. One design element to be cut out of the Tetex TR is stitched first, following the Mylar tracings using a small running stitch (two or three Tetex TR threads at a time). The sewing is done slightly beside the tracing lines toward the part of the design motif to be cut out of the Tetex TR. This allowance compensates for the tautness introduced to the Tetex TR when taped to the table. Also, a small degree of shrinkage occurs during the hot-melt-cutting process when the Tetex TR “melts back,” which ultimately incorporates ease, making the void slightly larger. Some experimentation is necessary to gauge the amount of this allowance.
Fig. 6.
The polyester Tetex TR overlay fabric taped tautly to a table surface over the Mylar tracing in preparation for stitching the second battle honor outline. As shown, the first battle honor has already been hot-melt-cut.
 |
Widely available G�termann 100% polyester two-ply sewing thread in a color matching the Tetex TR was chosen as the support thread. Trials with other threads may have equally good results. The G�termann thread is coarse in comparison with the Tetex TR yarns and makes a border or outline on the overlay. In the end, the overlay's reinforced cut edges fit snugly around the protruding crests, and consequently the support threads were not visible.
Stitching is carried out using curved needles because of the tautness of the Tetex TR on the table, but individual preference may dictate the use of straight needles. Pulling the stitching thread in tension with the Tetex TR, especially on straight lines, will improve the appearance of the finished hot-melt-cut edge. For overlays having more than one tracing to be cut out, as in the case of the First Guidon, only the outlines of one design motif at a time are stitched and hot-melt-cut. Before proceeding with the stitching and the hot-melt-cutting of the second motif, a fitting is conducted on the artifact.
7.3 A FITTING CONSISTS OF SEVERAL STEPS
The overlay fabric is removed from the Mylar after stitching, the motif is hot-melt-cut and left to cool (details of the hot-melt-cutting process follow), and then the overlay is placed on the object for the first fitting. The Mylar is placed over the overlay that sits on the object, and a tracing of the second design motif is done. The Mylar is removed and taped to the table again, the overlay is also removed and taped in position over the Mylar, and the second design motif is stitched and the process repeated. This fitting process for large overlays automatically compensates for the tautness introduced to the Tetex TR and for the slight shrinkage introduced by hot-melt-cutting mentioned earlier. It is difficult to give an empirical measurement of this adjustment because each person's idea of tautness is different and is hard to measure. It is for this reason that each design motif is traced, hot-melt-cut, and fitted from start to finish, one at a time, rather than all at once.
7.4 WORK SAFELY
Before the actual hot-melt-cutting begins, the hot spatula and other materials are set up either in a fume hood or under an exhaust trunk so the polyester fumes are not inhaled. When working with a hot spatula, label it as being “in use” or “hot,” and inform others not to disturb you with startling noises. If these warnings are not heeded, a burned conservator or sadly deformed overlay from a dropped spatula could be the result. I have found success in working in a slow, undisturbed, controlled manner, allowing enough time to complete each step.
8 WORKING WITH THE HEATED SPATULA
When ready to begin hot-melt-cutting the first stitched motif, tape the overlay down to a sheet of Teflon-coated fiberglass that itself is secured to the table surface. The Tetex TR has less of a tendency to shift and bubble if it is taped. Alternatively, the hot-melt-cutting can be done with the Tetex TR unrestrained, depending on individual preference and experience (fig. 7). If using the Teflon, transferring the image tracings to it before the hot-melt-cutting may be helpful.
Polyester melts at 238–90�C (460–554�F) (Hudson et al. 1993). The heated spatula must reach these temperatures and have a narrow, needlelike head capable of making a fine cut in the polyester fabric when heated. Our laboratory has a changeable-head spatula purchased in the 1970s, which has two useful heads for hot-melt-cutting: one resembles a fine needle and is 5 mm (1/4 in.) long; the other is coarser and 7 mm (1/2 in.) long. It appears as though one of these heads was retrofitted in-house. Authors French and Gentle (1993) describe using a pyrograph, a wood-or leather-burning tool with various heads.
“Meld,” a word combining melt and weld, will be used to refer to the hot-melt-cutting process whereby not only is the Tetex TR melted as it is cut but the polyester conforms to the supplementary support thread that itself is intended to stay intact (fig. 8). In order to meld, the needle head is held perpendicular to the table, gliding the head in contact with the Teflon-coated fiberglass. Whether or not the Tetex TR edges are restrained while melding, in both cases the author found that the use of gripping tweezers or needle holders held in the free hand greatly facilitates grasping the freshly hot-melt-cut area and holding it in its required shape until it cools, to maintain curved or multiangular features of design motifs. Also, sometimes it helps to hold the Tetex TR taut, slightly up off the table, with tweezers in one hand while hot-melt-cutting with the other. The side of the pointed spatula head is passed in contact with the support thread, retaining the thread (the Tetex TR melts neatly around the larger thread) to strengthen the melded edge, and it is used as a guide to cut away the unwanted part of the Tetex TR, one small section at a time (fig. 9). Any lingering with the head of the heated spatula will melt the support thread. Melding is stopped every few seconds to enable the area to cool while holding it in the desired shape with tweezers. Cooling is very brief. In between melding sessions, melted polyester is scraped from the needle head with a knife.
Fig. 7.
The hot-melt-cutting setup with Teflon-coated fiberglass under the battle honors, the tools needed, a light and extraction unit (clear dome)
 |
Fig. 8.
A close-up of the support thread held in place by the hot-melt-cut Tetex TR
 |
Fig. 9.
The resulting void in the overlay accommodates the battle honors and illustrates also that the support thread is retained.
 |
9 ACHIEVING THE DESIRED RESULTS
The results obtained can be improved by the following helpful hints. Practice makes perfect when melding edges with a heated spatula, and working with the right tools makes for a less frustrating experience. Less expensive, similar-weave polyesters can be used for experimentation. Practice first with simple cutout shapes, then progress to more complex shapes (fig. 10) with more than one design motif cut from sample overlays, to get an idea of how to judge the adjustments to make for each potential fitting.
As mentioned, it is critical to keep the heated spatula head free of melted polyester by scraping off the residues every few seconds while working. Otherwise, the polyester burns and turns dark, and some residues may themselves meld to the finished edge, causing an undesirable darkening and uneven appearance. It is virtually impossible to melt these away when doing touch-ups. A clean needle head also ensures that a smooth, gliding hand movement is possible during melding.
Sometimes while melding, a bead or fine strings of melted polyester form and remain attached to the melded edge. These are easily located by feeling the cooled edges or by examination under a stereo microscope. It is advisable to go around a second time with the heated spatula to smooth out these areas, which are potentially abrasive to the artifact.
Last but not least, once the hot-melt-cutting of the overlay is complete, the masking tape binding is cut away. If the tape is pulled off, the weave of the Tetex TR becomes permanently distorted.
Fig. 10.
Test sample of a complex shape cut from Tetex TR using the technique, showing the level of detail that can be attained
 |
10 CONCLUSIONS
A unique feature of the treatment of the First Guidon was the fabrication of a specialized overlay. The overlay fulfills a complex set of criteria. It needed to be a colored, sheer, strong fabric. It was also required to complement the disparate elements composing the artifact by providing support to the weak ground while having openings with edges resistant enough to be secured to extremely heavy but strong protruding crests.
While it was not possible to discuss other aspects of the treatment in detail, a complementary underlay was also devised to adequately support the flag with corresponding openings for the battle honors on the reverse. The underlay is made of a different fabric, and the edges of the cutouts were finished with hand stitches.
The overlay and underlay are secured with stitching around the perimeter of the cutouts to heavy metallic threads composing the battle honors, which are in excellent condition. Supplementary stitches were placed in select embroidered areas of the flag where the silk ground was protected from light damage, as well as around the outer edge of the flag. The flag assembly is mounted on a padded, fabric-covered solid support with recesses for the two battle honors.
11 DISCUSSION
Tetex TR is very difficult to handle, yet its other physical properties make it widely advantageous for use in many conservation disciplines. Any simple working technique with good results that may not be possible by stitching alone is useful because, for conservators working on a wide variety of objects, more options become available for conservation treatments. Introducing an element of control while working with Tetex TR, such as taping the edges down taut, means the fabric is less demanding in terms of handling and the work is less time consuming.
As demonstrated, possibilities are limitless for accommodating three-dimensional elements and complex-shaped design motifs in a Tetex TR overlay, including shaping overlays to match differences in color or pattern of ground fabrics (fig. 11). Conversely, complex shapes corresponding to motifs can be cut for use as overlays of individual elements by melding away the negative areas of the Tetex TR. A polyester thread, stitched and fused in place, will strengthen its cut and melted edges.
This technique is useful in circumstances where the only option for stitching the overlay in place is to tack the finished edges to a few strong design elements. The edges must be able to withstand reasonable manipulation and must hold stitches without failing. Another scenario where this technique may be advantageous is when the cut Tetex TR edge cannot be hidden under another textile element, so is left exposed, and cannot be secured in place farther from the edge. In this case, stitching the reinforced edges is possible without risking damage to the edge finish, and the stitches used are shorter and less visible. It is hoped that the provision of detailed instructions for this practical technique will overcome the difficulties of working with Tetex TR and so give wider appeal for its use to conservators in other disciplines.
Fig. 11.
After-treatment detail of battle honor shown in figure 4, with overlay loosely stitched in place
 |
ACKNOWLEDGEMENTS
The author is fortunate to work with two knowledgeable, experienced Textile Laboratory colleagues, Jan Vuori and Janet Wagner, and wishes to thank them for generously providing encouragement and support. Thanks also to CCI photographer Carl Bigras for photographing the melding process.
NOTES
1. The information in this paragraph was kindly provided by the owners of the First Guidon, the Royal Canadian Dragoons, CFB Petawawa, Ontario.
REFERENCES
Dancause, R.1996. On holy ground: Methods for the repair of areas of loss on historic military uniforms. Textile Conservation Newsletter30 (Spring): 12–14.
Dunbar, F. J., and J. H.Harper.1992. Old colours never die: A record of colours and military flags in Canada. Toronto: F. J. Dunbar. Plate follows 152.
French, A., and N.Gentle. 1993. The use of a pyrograph to heat-cut Stabiltex. Conservation News50:17–18.
Hudson, P. B., A. C.Clapp, and D.Kness. 1993. Joseph's introductory textile science. New York: Harcourt Brace College.
Sierksma, K.1980. Flag glossary and description rules. In Symposium Conservation of Flags. Amsterdam, Netherlands: International Association of Arms and Military History and the Committee for Conservation of Textiles in Museums. 19.
Smith, W.1975. Flags through the ages and across the world. New York: McGraw-Hill.
Thomsen, F. G.1988. Hot melt cutting of Stabiltex. Journal of the American Institute for Conservation27(1):32–37.
SOURCES OF MATERIALSCurved needles and gripping tweezers, needle holders, forcepsFine Science Tools Inc. 202-277 Mountain Highway North Vancouver, BC V7J 3P2 Canada (800) 665-5355; fax: (800) 665-4544
Fine Science Tools (USA) Inc. 373-G Vintage Park Drive Foster City, Calif. 94404-1139 (800) 521-2109; fax: (800) 523-2109 Suture needles are available in 5 sizes in packages of 12. Heated spatulaConservation Lighting and Equipment Design 69-71 Haydons Rd. Wimbledon, London SW19 1HQ United Kingdom 0181-540-5772; fax: 0181-543-4055 MylarConservation supply houses Teflon-coated fiberglass/ArmalonChemfab Corp. 13 Water St. P.O. Box 476 North Bennington, Vt. 05257 (800) CHEMFAB; fax: (802) 477-1135
Joseph Robb & Co. 5600 Philip Turcotte St. Montreal, QC H4C 1V7 Canada (514) 937-9151
Silchem Inc. 1361 Huntingwood Drive, Unit 4 Scarborough, Ont. M1S 3J1 Canada (416) 297-8111; fax: (416) 297-9579 Polyester Tetex TR (formerly called Stabiltex)Tetko Inc. “Specialty Sales” 111 Calu met St. Depew, N.Y. 14043 (716) 683-4050; fax: (716) 683-4053
SEFAR Mesh & Technology, Sefar Inc. Moosstrasse 2, P.O. Box CH-8803 Ruschlikon, Switzerland 411-724-6511; fax: 411-724-1525 or TALAS, 568 Broadway New York, N.Y. 10012 (212) 219-0770; fax: (212) 219-0735
AUTHOR INFORMATION
REN�E DANCAUSE graduated with distinction from the University of Alberta with a B.Sc. in home economics. Her background is in clothing and textiles, with a specialty in the conservation of historic textiles. Dancause worked as a volunteer and as a contractor in several museums in Alberta, Ontario, and Qu�bec before being awarded a textile fellowship in the Canadian Conservation Institute (CCI) Textile Laboratory in 1994. She has worked as a textile conservator at CCI since 1995. Address: Canadian Conservation Institute, 1030 Innes Rd., Ottawa, Ontario, Canada K1A 0M5
Section Index |