REGALREZ IN FURNITURE CONSERVATION
HANS PIENA
3 RESULTS
3.1 THE OLD FINISH
Because the tackiness of the finish on the bed could have been caused by the substrate and not by Regalrez 1094, the same finish was applied onto glass (see table 3, no. 1) This produced a tacky finish as well, leading to the conclusion that, whether or not the old finish on the bed had contributed to some of the tack, the Regalrez 1094 varnish itself becomes tacky when handled.
3.2 THE SOLVENTS
To see if particular types of solvents would cause the tackiness, new solutions of Regalrez 1094 with six different solvents were made (see table 2). Nhexane was chosen for its high relative evaporation rate. Xylene was chosen to see if an aromatic would make any difference. Shellsol D40 and TD were recommended for use with Regalrez by the National Gallery of Art (1996), Washington, D.C. The white spirit is a proprietary product commonly used by furniture conservators in the Netherlands. Shellsol D70 was chosen for its low relative evaporation rate.
The evaporation of hydrocarbon solvents from a film of a hydrocarbon resin can be slow because of the affinity between the two. However, under the same conditions, the solvent with the highest relative evaporation rate can be expected to produce a dry film sooner than the other solvents (Carlson and Schniewind 1989). Unfortunately, with the entire range of solvents discussed here, Regalrez 1094 produced a film that was tacky upon touching after three months of drying (see table 3, nos. 1-6), thus leading to the conclusion that the relative evaporation rate of the solvent does not significantly influence the tackiness.
To quantify the amount of solvent retained in a film of Regalrez, solutions of the four highest grades (40% w/w) with Shellsol TD were brushed onto thin metal sheets, which were weighed before and after application. In addition, the samples were weighed once every day for a period of 14 days. The relative humidity ranged from 50% to 60%, the temperature from 18�C to 22�C. The amount of Shellsol TD in Regalrez 1094 dropped to 7.8% after five days, depending on the grade of Regalrez used (fig. 1). The other three grades contained approximately 16% at that moment. The remaining solvent evaporated very slowly. Regalrez 1094 still contained 7.2% of the original amount of solvent after 14 days and was tacky when handled. The higher grades 1126, 1128, and 1139 were not tacky even though they still contained about 16% solvent. The final thickness of the film was 10-20μm.
3.3 THE COMPONENTS
To see which component caused the tackiness— Regalrez 1094, Kraton G1650, and/or Tinuvin 292—a series of mixtures was made, each containing 10% of one of the three ingredients (table 3, nos. 7-9). In addition, films made of melted Regalrez without any solvent were tested (table 3, nos. 13-16).
Table .
Mixtures Used in the Tests
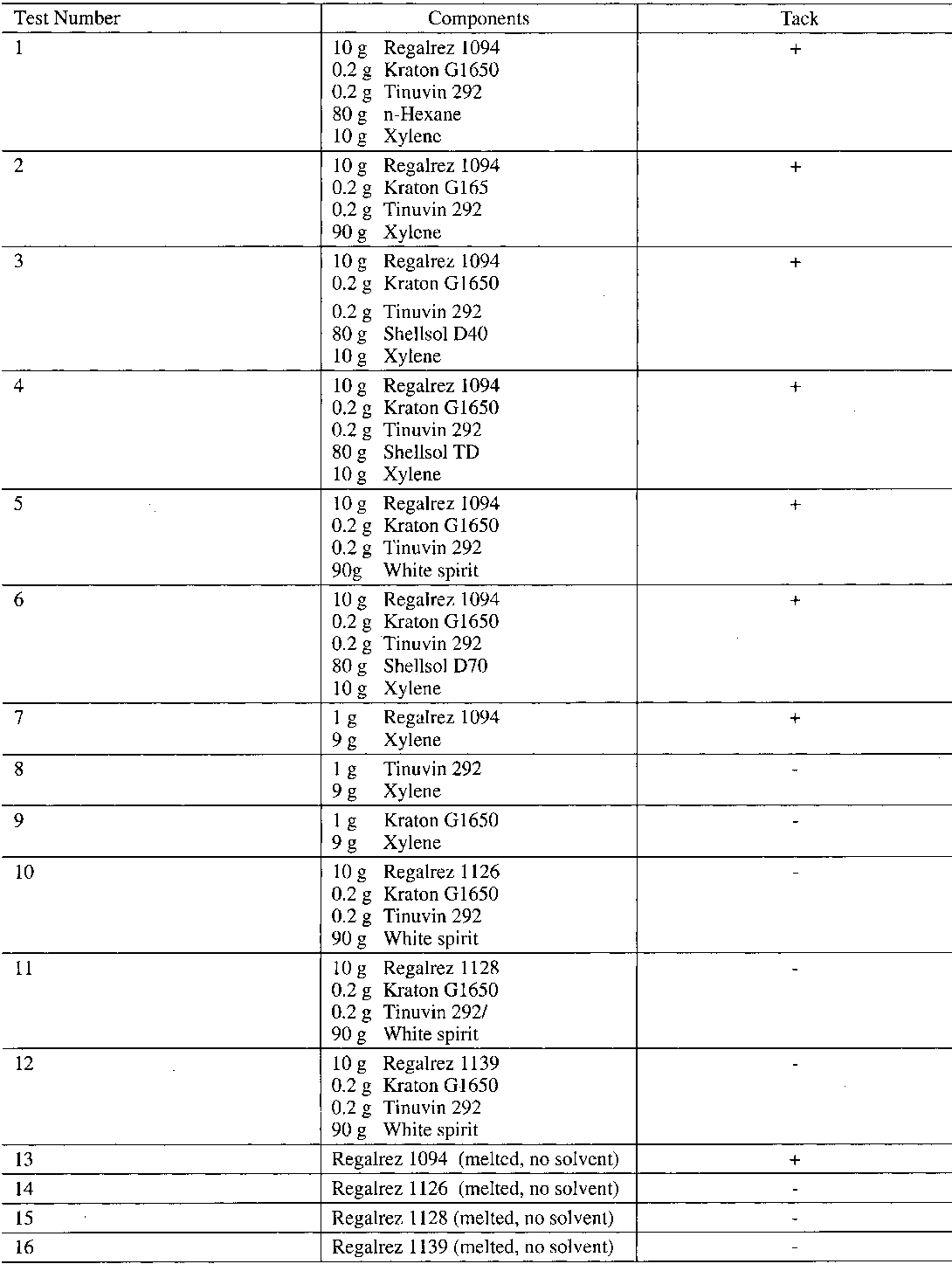 |
Only the films that contained Regalrez 1094, both with or without solvent, produced a tacky finish.
Fig. 1.
Percentage of solvent retained in films of Regalrez (40% w/w) in Shellsol TD. The bottom line represents Regalrez 1094; the top three lines represent Regalrez 1126, 1128, and 1139.
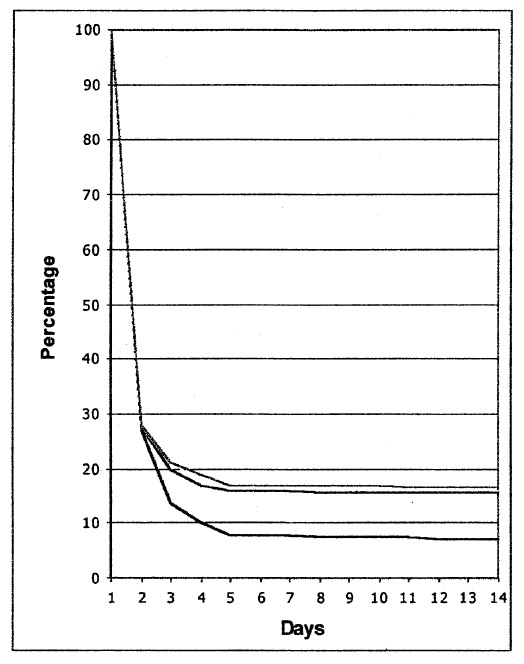 |
Whitten (1995a, 127) writes that dissolving Kraton G1650 in solvents with little or no aromatics content will make more viscous solutions. On the other hand, it is difficult to dissolve Kraton G1650 in a pure isoparaffin like Shellsol TD. Without using any heat, Kraton G1650 tends to swell to a transparent gel that does not mix well with the other components. Only xylene and white spirit with 23% aromatic content easily dissolved Kraton G1650. At least 10% of xylene had to be added to the other solvents to do the same.
Kraton G1650 is a triblock copolymer made up of a poly-ethylene-butylene block at the center and polystyrene blocks at each end. It has a solubility parameter range of 7.7– 9.4 (Shell Chemical Co. 1995, 34-36). As table 2 shows, the solubility parameters of the aliphatic solvents used are too low to fall within this range. Solvents at the lower end of this range dissolve the elastomer blocks at the center but not the polystyrene blocks at each end. This result can produce a mixture of high viscosity or merely swelling, in which case Kraton G1650 forms into a gel. If one does not want to use any aromatics, however, Kraton G rubbers can be dissolved in aliphatic hydrocarbon solvents if there are approximately 50% of naphthenics in the solvent. Of the aliphatic solvents used, only Shellsol D40 and D70 have 45% of naphthenics, and they dissolved Kraton G1650 reasonably well. Furthermore, the addition of resins can lower the viscosity of mixtures with solvents at the lower end of the range (Shell Chemical Co. 1995, 36-37). Although not extensively tested, Kraton G1650 dissolves best in Shellsol D40 and D70 if it is added after the Regalrez is dissolved.
|