OBSERVATIONS ON CYCLODODECANE AS A TEMPORARY CONSOLIDANT FOR STONE
REN�E STEIN, JOCELYN KIMMEL, MICHELE MARINCOLA, & FRIEDERIKE KLEMM
2 2. PHYSICAL AND WORKING PROPERTIES
Cyclododecane (C12H24) is a translucent, waxy hydrocarbon solid, with a melting range between 58� and 61�C. The 12-carbon molecule is cyclic and unbranched. With continued exposure to air, the solid will completely disappear through sublimation, in a manner similar to camphor. Cyclododecane is readily soluble in nonpolar and aromatic solvents and is poorly soluble in polar solvents. It is insoluble in water and therefore exhibits strong hydrophobicity.
Cyclododecane is commercially manufactured as a sealing wax. Br�ckle et al. (1999) reported that it is used as an additive in fragrances and synthetic waxes. Cyclododecane also serves as an auxiliary binder in the injection molding of ceramics and metal powders, improving casting accuracy and efficiency by promoting the removal of binders through sublimation (Hanamura and Katuyoshi 1988; Okamoto 1990). The Material Safety Data Sheet lists low toxicity and gives no restrictions on handling. Cyclododecane is not reported by the supplier, Kremer Pigments, to contain either additives or impurities.
Cyclododecane can be heated and applied as a melt, using a brush or heated spatula. Sticks of cyclododecane can be molded to fit into a hot-glue gun or other applicator with a warming chamber. McGowan (1999) described the use of a tool with a heated chamber and Teflon roller. Alternatively, cyclododecane may be dissolved in nonpolar or aromatic solvents and introduced by spray, brush, or injection. The concentration of saturated solutions varies with individual solvents; thus the amount of consolidant delivered by a given volume of saturated solution will vary with solvent choice. Saturated solvent solutions exhibit very low viscosity, and their mobility promotes ease of application by brush, squeeze bottle, sprayer, or syringe, although fast-evaporating solvents may quickly result in clogged needles or nozzles.
In order to observe coatings formed by various cyclododecane delivery systems, glass slides were brushed with cyclododecane applied as a melt and as saturated solutions in xylenes, Shellsol OMS, and hexanes. Shellsol OMS, formerly called Sol 71 and Odorless Mineral Spirits, is produced by Shell Chemicals and is described in the manufacturer's literature as a mixture of predominantly branched-chain, saturated hydrocarbons (C3-C12) with less than 0.1% aromatics. These three solvents were selected for evaluation because they provide a range of solubility parameters and evaporation rates. Saturated solutions of cyclododecane were prepared by continually adding known quantities of the consolidant to a known quantity of solvent until no further dissolution occurred and small amounts of solid cyclododecane remained visible in the solution. A saturated solution in Shellsol OMS was found to be approximately 80% wt/wt, while a saturated solution in xylenes was approximately 120% wt/wt and in hexanes was 140% wt/wt. Glass slides were then painted with each saturated solution and with melted cyclododecane. Upon evaporation of the solvents and upon cooling of the melted consolidant, crystal-like structures of cyclododecane formed on the slides. As a wax, cyclododecane is not a fully crystalline solid. The size and pattern of cyclododecane crystal-like structures differ with delivery method (fig. 1). A closely interwoven network of relatively large acicular crystal-like structures formed from the melted cyclododecane. The size and pattern of the coatings formed by the three solvent systems vary with the solvent's evaporation rate. Slides brushed with the Shellsol OMS solution showed, comparatively, a more open network, while those brushed with the faster-evaporating solutions produced tighter networks of smaller crystal-like structures. The consolidant delivery method may, therefore, be modified depending on the type of coating or penetration (discussed below) necessitated by treatment circumstances.
Fig. 1.
The size and pattern of cyclododecane crystals vary with delivery method.
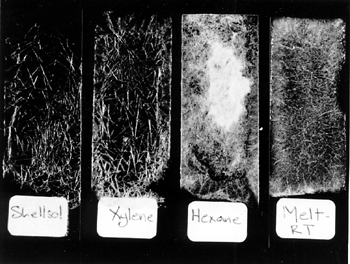 |
While the glass slides provided a suitable nonporous substrate for assessing superficial coatings of cyclododecane, different methods are necessary for examining the behavior of the consolidant within porous structures. Nicole Riedl and Georg Hilbert (1998) used cryo-scanning electron microscopy (cryo-SEM) analysis to examine porous plaster samples treated with cyclododecane. For this research, melted cyclododecane was applied to plaster samples that had been heated under an infrared lamp for one hour, and a saturated solution of cyclododecane in petroleum ether was brushed on unheated plaster samples. Riedl and Hilbert found that no crystalline structures formed within the substrate pores; instead, a smooth homogeneous film was observed coating the plaster particles of samples treated with both melted and solvent deliveries. These results suggest that there is no probable risk of damage due to pressure exerted on pore walls by crystal growth. The effect on the plaster as the subliming cyclododecane leaves the pores is not yet fully understood.
Sublimation can be hastened by increased ventilation or by increased temperature, supplied by a hot-air gun, hair dryer, oven, or heat lamp. Conversely, sublimation can be delayed by sealing the object in a closed environment. Delayed sublimation is demonstrated by the following comparison of two sets of glass slides that were coated with the various consolidant solutions described above. One set of treated slides was exposed to room conditions (approximately 22�C and 50% RH), and the second set was placed into plastic Petri dishes with loose-fitting covers. The Petri dishes were stacked and sealed in a zip-close polyethylene bag. This enclosure, although not airtight, was selected because it replicates the sort of covering that could be used during practical treatment. Within four days, the cyclododecane had sublimed from the unwrapped set of glass slides. The denser coating layers that resulted from the melt and hexanes deliveries required more time to sublime than the more open network of crystals produced from the slower-evaporating solvent solutions. The area of the cyclododecane coatings was observed to diminish gradually from the edges. No traces or residues were visible on the slides following sublimation. After two months in the box and bag enclosure, crystals of cyclododecane were still present on the second set of glass slides. Sublimation did occur to some extent because the packaging was not airtight (fig. 2).
Fig. 2.
Coated slides after two months within an enclosure, demonstrating delayed sublimation of cyclododecane
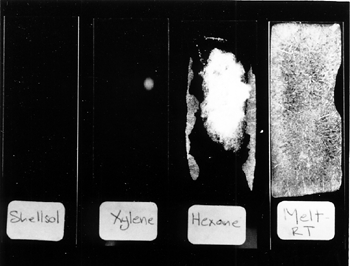 |
|