THE TREATMENT OF AN ODILON REDON CHINE COLL� LITHOGRAPH, L'ART CELESTE
CAROLYN MURPHY
ABSTRACT—This article describes the treatment of an Odilon Redon chine coll� lithograph, L'Art Celeste. The paper sheets, already partially detached, were separated in a stain removal treatment. During treatment the sheets changed in size and shape so significantly that realignment of the image, which extended onto the plate paper, became a problem. A conventional approach to reattachment proved unsuitable because the two papers were unusually dimensionally unstable and reactive to moisture. By using a combination of flattening techniques, a method was devised to selectively expand and contract the two paper sheets involved in order to regain alignment of the image components. Then a “dry” adhesion procedure, using Klucel G in ethanol, was developed to adhere the sheets together, preserving the alignment already achieved. These methods may also have application in the treatment of other moisture-sensitive paper objects.
TITRE—Le traitement de L'Art c�leste, une lithographie sur chine coll� d'Odilon Redon. R�SUM�-Cet article d�crit le traitement de L'Art c�leste, une lithographie sur chine coll� d'Odilon Redon. Les deux feuilles de papier, d�j� partiellement d�tach�es l'une de l'autre avant l'intervention, furent s�par�es pendant le traitement pour �liminer les taches. Les changements de forme et de dimension des feuilles furent si importants que le r�alignement de l'image, qui se trouvait aussi pr�sente sur le papier-support, devint un probl�me. Une approche conventionnelle de r�attachement des deux feuilles s'av�ra �tre inutile dans ce cas � cause de leurs inhabituelles instabilit� physique et sensibilit� � l'humidit�. Tout en utilisant une combinaison de techniques de remise � plat, on a mis au point une m�thode qui permit de contracter ou de dilater localement les feuilles afin de r�aligner les �l�ments de l'image. Pour pr�server l'alignement qui avait �t� accompli, on d�veloppa une m�thode de collage “� sec”, avec du Klucel G dilu� dans de l'�thanol, pour recoller les deux feuilles ensemble. Les m�thodes de travail d�crites peuvent aussi s'appliquer au traitement d'autres objets en papier qui sont sensibles � l'humidit�.
TITULO—El tratamiento de una litograf�a chine coll� de Odilon Redon, L'Art Celeste. RESUMEN—Este art�culo describe el tratamiento de una litograf�a chine coll� de Odilon Redon, L'Art Celeste. Las hojas de papel que ya se encontraban parcialmente delaminadas, fueron separadas durante un tratamiento de remoci�n de manchas. Durante el mismo las hojas cambiaron su tama�o en forma tan notable, que la realineaci�n de la imagen, que se extend�a hacia la plancha de papel, se transform� en un problema. Una forma convencional de encarar la uni�n de las dos hojas result� ser inadecuada ya que ambos papeles eran inusualmente inestables dimensionalmente y muy reactivos a la humedad. Usando una combinaci�n de t�cnicas de aplanado, se dise�� un m�todo para expandir y contraer selectivamente las dos hojas de papel involucradas para alinear los componentes de la imagen. Luego se desarroll� un procedimiento de adhesi�n en seco utilizando Klucel G en etanol para adherir las hojas preservando la alineaci�n lograda previamente. Estos m�todos podr�an tener aplicaci�n en el tratamiento de otros objetos de papel sensibles a la humedad.
1 INTRODUCTION
Paper expands when it is moistened and contracts when it is dry. Because of its absorbency, or hygroscopic nature, paper is dimensionally unstable when exposed to varying degrees of moisture. Depending on the length of fibres, their orientation, the degree of hydration, or the thickness and density of the sheet, paper may expand and contract drastically or little, unevenly or uniformly, when its moisture content changes.
These characteristics, so eloquently described by Keyes (1978, 5), are especially significant when considering the treatment of chine coll� prints. A chine coll� print consists of two sheets of paper: one thin image-bearing paper called the chine, and one thicker support paper, the plate paper. The sheets are adhered to each other when damp, during the printing process. The difference in the nature of the two sheets (thickness, density, fiber content, surface texture, moisture sensitivity, etc.) and the interplay of these differences create artistic qualities that cannot be achieved by any other printing technique. Equally, if the sheets become separated over time, or in the course of conservation treatment, these differences can work against the successful reunion of the chine coll� parts. The challenge for the conservator, when faced with objects that have unusual or competing characteristics, is to find ways to look beyond conventional approaches, to find solutions that work.
This paper discusses the treatment of a chine coll� lithograph by Odilon Redon, L'Art Celeste (1894), from the collections of the Fine Arts Museums of San Francisco.
2 BACKGROUND
2.1 ARTIST
Odilon Redon (1840–1916), a French symbolist artist working in the late 19th century, created, in addition to drawings and paintings, more than 200 chine coll� lithographs in the course of his artistic career. His use of lithography and chine coll� was part of a broader interest in these techniques, which had become popular in the late 19th century. Ignace Fantin- Latour suggested that Redon try lithography in the late 1870s, although Redon had in fact learned the technique in the 1860s from Rodolphe Bresdin. Gott (1990) speculates that it was also, probably, Fantin-Latour who introduced Redon to the professional printing workshop of Lemercier and Cie. Redon subsequently issued all of his lithographs with Lemercier until the late 1870s. Then, from 1887 to 1894 Redon printed all his lithographs with Becquet. However, during 1894 he began to experiment with a range of printers. It was in this period L'Art Celeste was printed by Furstein. After 1894, apart from a few lithographs editioned elsewhere, Auguste Clot and Blanchard printed all of Redon's lithographs (Gott 1990).
2.2 CHINE COLL�
Chine coll� is a technique used in printmaking. It was first developed in the late 18th century (Jenkins 1990) and is still in use today. According to Jenkins (1990, 46) the process was developed for copper plate line engravings, which required a paper that was “strong enough to take the huge pressure from the wooden roller presses while damp, yet soft enough to take an impression from the delicate shallow lines of the engraved plate.” It was found that by printing the image onto a thin chine attached (during the printing process) to a thick plate paper, prints of unusual delicacy could be created.
The term chine coll� means “adhered paper.” Chine refers to the Chinese paper that was used historically as the image-bearing paper, and coll� means “paste” or “gum,” indicating that the Chinese paper was adhered to a heavier support paper. In the late 19th century increasing trade with Asia resulted in the availability of a range of thin Chinese papers, sometimes called China papers, which were ideal for use in the chine coll� process. This increase in the availability of suitable papers helped to foster the new popularity of the technique. Because of the imperial and trade links between Britain and India, this Chinese product of the East became known in Britain, rather confusingly, as India paper, and the chine coll� prints as India proof prints. Jenkins (1990) has compiled a list of many alternative names, all of which refer to the chine coll� printmaking technique. For the sake of consistency, in this paper the image-bearing paper is referred to as “chine” and the secondary support paper as “plate paper.”
In making chine coll� prints, a layer of size or thin starch adhesive is usually brushed onto the reverse of the chine. This adhesive is allowed to dry and is then reactivated when the paper is dampened prior to printing. This method was in use in the late 19th century (Gott 1990) and may have been the method used to create L'Art Celeste. Other methods of adhering the two sheets include sprinkling starch powder over the reverse of the dampened chine directly prior to printing, or relying on the pressure of the printing process to allow the dampened papers to fuse together. This latter method usually requires that the reverse of the chine be brushed to create a fluffy surface that will more easily adhere to the plate paper (Jenkins 1990). The chine is always the image-bearing paper, though Jenkins (1990, 52) notes: “It is quite common to find the printed image extending beyond the edges of the India paper, either intentionally or unintentionally…. The juxtaposition of the two sheets, the change in tone, the contrast of texture, are therefore a vital and integral part of the composition and should never be disturbed.”
2.3 TREATMENT OF CHINE COLL�
The treatment of chine coll� prints is usually considered problematic. The very nature of the chine coll� is such that through trying to treat problems such as staining and discoloration, another problem might easily be created—separation of the parts of the print (Petukhova 1987). In treating chine coll� prints, all attempts must be made to avoid treatments that might result in the separation of the two sheets forming the chine coll�. For this reason, careful planning and a cautious approach to treatment procedures, to avoid any risks to the attachment of the chine and plate paper, are always advised.
However, there are times when the parts of a chine coll� become separated (Petukhova 1987; Szczepanowska and Schuettinger 1997) or, as in the case of this Redon print, may already be separated. In such cases, treatment procedures are needed that will result in the successful reunion of the chine and plate paper (McAusland and Stevens 1979; Petukhova 1987; Burns and Potje 1990; Szczepanowska and Schuettinger 1997).
2.4 OBJECT DESCRIPTION
L'Art Celeste, a chine coll� lithograph, is a proof before letters, annotated in pencil at the bottom right corner “epreuv 1 Mai. L'Art Celeste” (proof, 1 May. The Celestial Art). It was subsequently printed in an edition of 50. Gott (1990, 43) notes that many of Redon's proofs were preserved “through Redon's habit of making gifts of working and trial proofs to friends and collectors.” The image is printed on a thin, smooth chine (317 � 258 mm) with grain horizontal across the sheet. The grain of the thick wove plate paper (450 � 318 mm) runs vertically down the sheet. Based on a visual study of the 16 chine coll� lithographs by Redon, including L'Art Celeste, in the collections of the Fine Arts Museums of San Francisco, the papers used in L'Art Celeste seem typical of the papers Redon used to create chine coll�. The general appearance of the chines is similar, with the color best described as a gray-yellow, as mentioned by Gott (1990, 27). The plate papers in this group, including L'Art Celeste, are thick and slightly textured wove sheets varying in color from cream to white.
Fibrous impurities, often found in late-19th-century China papers, can be seen in L'Art Celeste and in most of the other Redon chine coll� prints examined. Such impurities were conventionally removed by the printer prior to printing. However, it is possible that Redon “may have preferred to leave the paper in its natural imperfect state for aesthetic reasons” (Gott 1990, 27).
The relationship between the chine and plate paper forming a chine coll� is critical to the aesthetic appreciation of the artwork, as has been noted previously. In L'Art Celeste the image extends beyond the edges of the chine onto the margins of the plate paper on all four sides, a significant amount compared to other Redon lithographs examined. The surface appearance of the chine can be altered by the texture of the plate paper beneath showing through the chine. This effect is quite obvious in L'Art Celeste and is integral to the appearance of the image. The texture of the plate paper, the quality of the chine, and the extent to which the chine is inked all influence this property.
3 TREATMENT
Before the author received the print for treatment, it had already received partial conservation treatment. Records indicated that the object was badly foxed and in need of wet treatment to remove, or at least reduce, the staining in the paper. In addition, the two sheets of paper forming the chine coll� print had become partially separated from each other so that approximately half the chine had lifted completely away from the plate paper. The parts of the moisture-sensitive chine that were delaminated from the plate paper had, over time, expanded and contracted in response to changes in relative humidity so that the chine was no longer planar and could not be successfully readhered to the plate paper in situ. A decision was made to complete the separation of the sheets so that wet treatment and stain removal could more easily be undertaken, and to facilitate full reattachment. The sheets came away from each other easily in a water bath and were successfully washed and light-bleached to remove the staining that disfigured them. After rinsing and partial air-drying, the sheets were pressed between blotters under a sheet of glass. Numerous later attempts at registering the papers for reattachment were unsuccessful, as the papers had expanded and contracted quite differently from one another during treatment. The ink lines on the chine no longer aligned with the corresponding ink lines on the plate paper. In figure 1, the image components that extend onto the plate paper are clearly visible. The overall effect of these dimensional changes was that the chine was now too wide by approximately 2 mm (fig. 2), and too short by approximately 2 mm. A pause in the treatment to consider the possibilities stretched to several years. It was at this later date that the author first encountered the object and treatment was resumed.
Fig. 1.
Odilon Redon, L'Art Celeste, 1894, chine coll� lithograph, 450 � 318 mm. Fine Arts Museums of San Francisco, San Francisco. The two sheets of the chine coll� during treatment, showing where the image extended onto the plate paper
 |
Fig. 2.
Detail of chine coll� during treatment, showing the inaccurate alignment of the image components on each sheet.
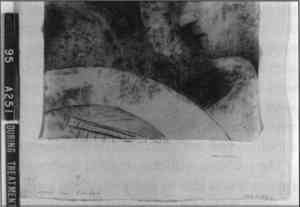 |
The history of difficulties associated with the reattachment of the print indicated that any procedure involving the use of water would be problematic due to the extreme moisture sensitivity of the chine and plate paper. Despite these difficulties it seemed appropriate to at least attempt readhesion with wheat starch paste, a historically appropriate, and conventionally acceptable, conservation adhesive. This first attempt at readhering the parts of the chine coll� print was based on methods described in the conservation literature (McAusland and Stevens 1979; Petukhova 1987; Burns and Potje 1990; Szczepanowska and Schuettinger 1997). It was hoped that the differences in the hygroscopisity of the two sheets could be used to advantage, through differential humidification, so that image alignment could be achieved while the sheets were damp. Once aligned, the sheets would be immediately adhered together with wheat starch paste. The chine was to be humidified enough so that it would cling to polyester film. In this way it could be fairly easily manipulated to allow registration of the sheets. The plate paper would then be humidified gradually until it registered with the humidified chine. Once alignment of the image was achieved, wheat starch paste would be applied to the humidified chine through a fine-meshed screen to achieve a thin, even film of adhesive. The mesh barrier would also prevent any potential pulling or stretching of the chine caused by the action of a paste brush over the paper surface. Positioning of the chine would then be achieved with the aid of the polyester film carrier.
To experiment with and perfect this alignment procedure, mock-up objects were prepared, also with mismatching grain direction. Papers identical to those used to create the chine coll� were not available to the author for experimental purposes. Instead papers were chosen that, as far as possible, matched the object papers' properties: thickness, density, surface texture, grain direction, hygroscopicity, etc. This choice was made qualitatively and was based on an empirical understanding of the properties of the object. Alignment of the two sheets was marked around all four edges with pencil lines perpendicular to the edge of the chine and extending onto the plate paper. The sheets were washed and air-dried a number of times until the pencil marks were out of alignment. The sheets were then differentially humidified, by lightly spraying with water, until alignment was achieved. Adhesive was then applied, and the readhesion process was successfully undertaken.
Having achieved reattachment of the mock-up, it was time to attempt reattachment of the Redon print. Since the object papers were not the same as those used in the mock-up, variation in the papers' response to the process was expected. Accordingly the process was altered, as seemed appropriate during treatment, through variation in the degree of humidification and in the use of stretching techniques such as brushing out the wet paper sheets with a Japanese smoothing brush. All attempts were unsuccessful in achieving accurate alignment of the image. Accordingly, the second step in the process, the application of the adhesive, was not attempted on the artwork.
The problem with this original treatment approach was that so many variables were working at the same time that it was impossible to control the process adequately. Different paper thickness, grain direction, and absorbency contributed to the difficulties. Trying to readhere the parts of the chine coll� in one continuous procedure no longer seemed feasible considering the complexity of the object. Instead, it was decided to break the treatment up into smaller, more manageable steps. Alignment of the image was dealt with separately from the reattachment process.
3.1 COMBINATION OF DRYING METHODS USED TO ACHIEVE IMAGE ALIGNMENT
The fibers in a sheet of paper are usually more or less aligned in one direction (the grain direction), due to the nature of the papermaking process. The hygroscopic nature of paper fibers is such that, when wetted, the paper sheet will expand to a greater degree in the cross-grain direction. This effect is magnified in thin dense sheets, such as the chine in a chine coll�, where there is no interfiber space to accommodate this swelling. In some cases a five- to tenfold difference, in expansion of the paper sheet (width to length), can be observed. Accordingly, a dry sheet of paper that is wetted will expand to the extent that it is able, depending on the degree of humidification. In drying, however, the expansion or contraction of a sheet of paper depends on the degree of initial humidification as well as on the method of pressing and the amount of pressure applied.
The difference in the nature of the two sheets forming the Redon chine coll� (thickness, density, fiber content, grain direction, surface texture, moisture sensitivity, etc.) made realignment of the image components problematic. Alignment when the object was wet had already proved too difficult to achieve. Because of the greater degree of control that could be achieved in drying, humidification and flattening techniques were used in attempting to manipulate the size and shape of the two sheets of paper. First, the plate paper was humidified and pressed between blotters until dry. This preliminary flattening was conducted so that the discrepancy in size between the two sheets could be more easily assessed. Although there was a slight dimensional change in the plate paper, the image components were still significantly out of alignment at all four edges.
Next, friction drying was attempted. Both papers were placed between Goretex and damp blotters until judged sufficiently humidified. Each paper was brushed out between sheets of dampened Japanese paper (thin mino)1 and was then pressed between blotters in a screw press to flatten. After friction drying of both papers, the hoped-for alteration in the shape and size of the two sheets had been, at least partially, achieved. Each sheet had expanded considerably more across its grain than with its grain, a result that meant that the registration of the width of the image was now accurate. However, the chine had lengthened to such an extent (approximately 5 mm) that it was now too long by about 2 mm and, though flatter, was still slightly distorted at the bottom edge.
The next step in the process was to try to alter the length of one sheet while maintaining its width. The author decided to attempt a reduction of the length of the chine, rather than induce an increase in the length of the plate paper, since the chine was more responsive to moisture. It was hypothesized that by humidifying and pressing, with minimal pressure, it might be possible to induce contraction of the sheet across its grain (the length) without significantly affecting its width. The chine was sprayed with water so that it was only very slightly damp and was then pressed between blotters under two sheets of glass. No alteration in size was noted. The process was repeated, making the object slightly more humid and using only one sheet of glass for weight. It was found that the height of the chine decreased by approximately 1 mm, while its width did not change. This process was repeated two more times without any alteration in method until the object size was sufficiently altered to allow exact alignment of the image components. There was still a slight distortion at the bottom edge of the chine. This made positioning of the chine to achieve alignment awkward, but not impossible.
In summary, the image components were brought back into alignment by utilizing the hygroscopic nature of the paper and the opposing grain directions of the two sheets. The chine was especially susceptible to the effects of moisture and could be fairly accurately manipulated, in increments, through a judicious humidification and flattening procedure. Figure 3 illustrates this process.
Fig. 3.
Steps in the process of achieving alignment of the two sheets.
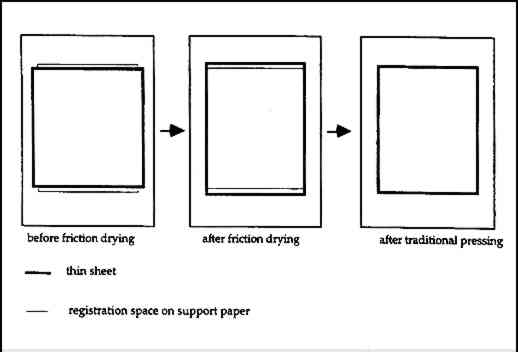 |
3.2 READHESION OF THE CHINE COLL�
An attachment process was now required that would not alter the relative size and shape of the two sheets of paper and would allow careful manipulation of the chine during the attachment process, so that the slight distortion at the lower edge of the sheet could be worked out. The difficulties encountered during the previous reattachment attempt indicated that any dampening of the sheets would probably result in loss of image alignment. Accordingly, a nonaqueous readhesion procedure was sought. An attachment method using Klucel G (hydroxy propyl cellulose) in ethanol was devised, tested on a mock-up, and then successfully implemented to readhere the object.
The reverse of the chine was coated with 5% w/v Klucel G in ethanol. The adhesive was applied with a squeegee through a finemeshed screen to achieve a thin, even layer. The adhesive was placed in the middle of the screen and squeegeed to the edges of the chine to prevent any adhesive getting under the edges and onto the front of the chine. The paper was peeled off the screen. At the corners, where the object was held to lift it away from the screen, the adhesive layer was disrupted. A brush was used to reapply adhesive to these areas. The adhesive layer was dried with a hair dryer set on low heat.
The dry plate paper was then placed on the vacuum suction table on a sheet of blotter. Under suction, the dry chine was positioned on the plate paper. Exact alignment could be fairly easily achieved on the suction table, since the adhesive was not activated until after the image was aligned. When the two sheets were in position, the adhesive, on the reverse of the chine, was reactivated by lightly spraying the face of the object with ethanol.
Gradually more ethanol was sprayed over the object until the chine was about half-wet. At this stage the chine began to expand, forming small bubbles as the chine lifted up from the plate paper. It was left under suction, and as it dried out the bubbles went down, aided by gentle burnishing with a septum elevator tool through polyester web. The sheets were observed to be still in alignment. Strips of polyester film were then placed around the edges of the object so that approximately 1 mm of the edge of the chine was covered by the polyester film. It was hoped that this step would sufficiently increase the suction pressure to maintain contact between the two sheets. The object was again lightly sprayed with ethanol and observed. Spraying was gradually increased until the chine was fully wetted with ethanol. Lifting of the chine did not occur during this slightly altered procedure. The object was then left under suction for about 3 minutes, until the object was partially dry. The author was concerned about moving the object before it was quite dry and possibly disrupting the adhesion of the sheets (and the alignment), so the polyester film strips were removed and polyester web, blotter, and a rubber mat were placed over the object, which was still under suction. After a few minutes the object was taken off the vacuum suction table and was placed between polyester web and blotter and transferred to a screw press.
After a few hours the object was checked and found to be dry to touch and fully adhered. The image components were in alignment at all four edges (fig. 4). It was left in the screw press another 3 days and was then transferred to new blotters and placed under one sheet of glass. The following week the object was checked. The sheets were fully adhered, but the object had a concave bowing. This bowing could probably have been rectified through carefully humidifying and flattening the object; however, the author was concerned about any undue introduction of moisture that might upset the newly achieved union between the two sheets. Instead, a more cautious approach was chosen to rectify the problem. The object was left under glass between fresh blotters. Gradually over some months, with periodic changing of blotters, the concavity decreased until the object was flat.
Fig. 4.
Redon, L'Art Celeste, after treatment
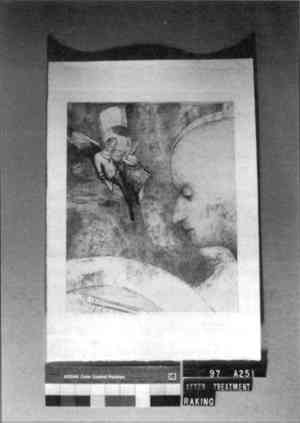 |
4 CONCLUSIONS
A conventional approach proved unsuitable for the treatment of this chine coll� print. The hygroscopic character of the papers restricted the treatment procedures that could be utilized and dictated a two-phased approach to achieve treatment objectives. With a combination of humidification and flattening techniques, the different moisture sensitivity of the chine and plate paper was used to advantage to achieve the appropriate alteration of the size and shape of the two sheets in gradual increments. However, in adhering the two sheets together, their moisture sensitivity and concurrent dimensional instability had to be circumvented. A simple, dry method for readhering the separated parts of the chine coll� print was developed. This method utilizes a solvent-soluble cellulose ether adhesive, applied to the reverse of the chine, which is reactivated while the object is held in registration by vacuum pressure on the suction table. These treatment methods, successfully used to readhere the chine and plate paper of a chine coll� print, may also have application in the treatment of other moisture-sensitive paper objects.
Nowhere are paper's properties of expansion and contraction more evident than in the treatment of chine coll�. Therefore, an understanding of the treatment of these objects broadens one's knowledge of papers in general. An empirical understanding of the properties of the object combined with a careful, considered approach to the planning of treatment procedures were the keys to the success of this treatment. By viewing setbacks in the treatment process as opportunities to gain a greater understanding of the properties of the object, the author was able to continually reassess and reshape the treatment process. This approach resulted, ultimately, in the successful realignment and reattachment of the chine and plate paper forming Redon's L'Art Celeste.
ACKNOWLEDGEMENTS
This project was completed while the author was a Getty Fellow at the Fine Arts Museums of San Francisco. The author gratefully acknowledges the Getty Grant Program, Santa Monica, California, the University of Canberra, and support from the National Film and Sound Archive and other Australian cultural institutions. The author also gratefully acknowledges the advice and assistance of the paper conservators at the Fine Arts Museums of San Francisco: Pauline Mohr, Janice Mae Schopfer, and particularly Debra Evans and Bob Futernick, whose help with the editing of this paper was invaluable.
NOTES
1. Friction drying was undertaken with the grain of the friction-drying papers across the grain of the object papers. The author thought that this procedure might encourage alteration in the size and shape of the paper sheets. Subsequent testing suggests that crossing the grain of the friction-drying papers to the grain of the object paper makes no difference to the stretching effect of the friction-drying process. In fact, for the mock-ups prepared, the alteration in the size of the sheets caused by friction-drying was exactly the same when the friction-drying papers were across, or with, the grain of the object. In both cases the sheet size increased by 1–2 mm with the grain, and 4–5 mm across the grain. Only one type of paper was tested. Tests were not undertaken to determine the effect of having one friction drying paper across the grain, and one with the grain, of the object paper.
REFERENCES
Burns, T., and K.Potje. 1990. Paper conservation catalog. 4, Support problems. Washington, D. C.: AIC-BPG.
Gott, T.1990. The enchanted stone: The graphic worlds of Odilon Redon. Melbourne: National Gallery of Victoria.
Jenkins, P.1990. India proof prints. Paper Conservator14:46–57.
Keyes, M. K.1978. The unique qualities of paper as an artifact in conservation treatment. Paper Conservator3:4–8.
McAusland, J., and P.Stevens. 1979. Techniques of lining for the support of fragile works of art on paper. Paper Conservator4:33–44.
Petukhova, T.1987. Treatment of chine-coll� prints. The Book and Paper Group annual. 6. Washington, D.C.: AIC-BPG. 106–10.
Szczepanowska, H., and B.Schuettinger. 1997. 45 chine coll� miniature engravings of portraits of presidents and other U.S. government officials, 1880. Conference handbook, Institute of Paper Conservation 4th International Conference, London. London: IPC. E14–E15.
SOURCES OF SUPPLIESKlucel G (hydroxy propyl cellulose)Hercules Incorporated, 500 Hercules Rd., Research Center, Building 8145, Wilmington, DE 19808
AUTHOR INFORMATION
CAROLYN MURPHY graduated from the conservation program at the University of Canberra, Australia, in 1995. She worked in private practice for one year before undertaking a Getty Fellowship at the Fine Arts Museums of San Francisco in 1996–97. Currently she is the conservator (works on paper) at the Queensland Art Gallery, Brisbane, Australia. Address: Queensland Art Gallery, P.O. Box 3686, South Brisbane, Queensland 4101, Australia
Section Index |