OBSOLETE FILL MATERIALS FOUND ON CERAMICS
STEPHEN KOOB
4 CATALOG
The examples in this article are predominantly from the author's archives and the collections of the Freer Gallery of Art, supplemented by examples from numerous publications on ceramics restoration. The references are all in English, or from English translations; most of the “how-to” manuals are from American workshops. The catalog is arranged in roughly chronological order (see table 1). It is difficult to know how early some of the techniques and materials were developed and at what point they ceased to be used. General comments on identification and appearance are included but should be considered only as guidelines. The ceramics conservator can quickly develop an ability to recognize certain types of ceramics restorations, but should also be aware that this is a field where innovation and resourcefulness abounded. Of all the identification techniques available, solvent solubility is one of the most useful. It must be kept in mind, however, that a ceramic may have had more than one campaign of restoration.
TABLE 1. PROPOSED CHRONOLOGY OF FILL MATERIAL USE
UV fluorescence is noted for the relevant material and is given under long-wave examination. Short-wave examinations revealed no different specific appearances, only a duller, lighter fluorescence. The solvents offered for solubilities are the most common and are not a comprehensive list.
Bitumen—Bitumen was used more than 6,500 years ago to repair ceramics (Williams 1988) and probably as late as the 19th century A.D. The term encompasses various naturally occurring mixtures of hydrocarbons, of indeterminate compositions, boiled down to a tarlike material. The sources can vary from oil residues (tar or asphalt pits) to pine or other tree resins. In the ancient Near East the prime source was the Dead Sea (Lucas 1989). Dark brown-black and shiny in appearance, bitumen becomes extremely brittle with age, breaking with sharp conchoidal fractures. Although it was not very attractive, the liberal application of excess adhesive served the dual purpose of joining and filling and can therefore be considered as the first fill material. Thickened pine resins were commonly used to repair South American and Southwest Native American pottery. Birch bark tar was used to repair a Roman jar in Britain (Charters et al. 1993) and also probably produced a waterproof seal.
UV fluorescence: Bitumen fluoresces orange.
Solubility: Petroleum distillates, alcohol.
Animal hide or skin glues—Probably in use as early as the pine resins, and extremely popular throughout the 19th century, animal protein glues remained in use into the early 20th century. These glues originated from mammal or fish sources that are rich in collagen, such as skins, internal membranes, bones, and hooves. They are also the adhesive base for numerous “glue putties,” which are used as a combination of adhesive and fill material (fig. 4).
Fig. 4.
Animal glue fills around substituted fragments, Syrian jar, Freer Gallery of Art, F 11.5
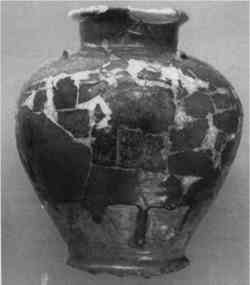 |
Originally a clear yellow-brown, animal glues age to a darker color. They are often used in excess on ceramics, so that the excess itself fills the losses along a break line. To stiffen the glue and to reduce its considerable shrinkage on drying, the glue is often bulked with fillers and pigments. When set and dry, the fill material is quite strong, but it can be carved or sanded as necessary. Fish glue with chalk, brick dust, or fire-clay dust was also recommended for filling small gaps between joined fragments (Rathgen 1905).
The materials used to bulk animal glues included whiting (calcium carbonate), zinc oxide, lead white (basic lead carbonate), and clay (St.-Gaudens and Jackson 1953). These were also recommended as a base with animal glue to make gesso or fine surface finishing over a coarser body fill (fig. 5). Animal glue bulked out with earthenware clay is one of the most convincing imitations of terracotta ware. When used for fills, this mixture can be virtually undetectable visually or by examination with UV light. Only when this mixture is subjected to wetting or soaking is the secret revealed.
Fig. 5.
Animal glue–whiting gesso layer over clay replacement fragments
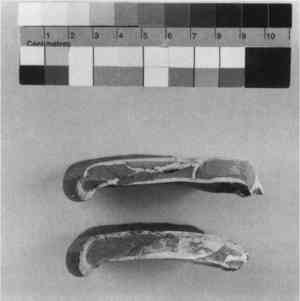 |
Small amounts of linseed oil and turpentine (Rathgen 1905) were added to provide glue putties with better workability, prolonged setting times, and durability. They are no longer used because of their poor stability and tendency to migrate out of the putty and stain the ceramic.
The major disadvantages to this fill material (with or without additives) include the shrinkage of the glue, embrittlement over time, and extreme water sensitivity. These properties generally result in the filler cracking and eventually breaking up (see fig. 6).
Fig. 6.
Deteriorating fill made of animal glue and whiting
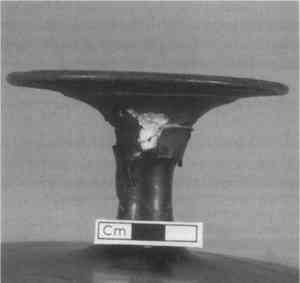 |
UV fluorescence: Animal glues naturally fluoresce a hazy or light white, sometimes a pale yellow. When bulked out with clay or nonfluorescent pigments, they do not fluoresce. Fresh linseed oil has a negligible fluorescence but, when aged and yellow, fluoresces slightly yellow (de la Rie 1986).
Solubility: Water, preferably warm.
Urushi (lacquer)—This is true lacquer, originating from the resin sap of the Asian tree Rhus vernicifera. It has a long tradition of restoration use, primarily in Japan. It was used as early as 2500 B.C. for the repair of cracked earthenware, and its use continues into the 20th century (Nakasato 1988).
Urushi has a clear yellow-brown appearance as a resin. In use, it was often mixed with pigments, and on ceramic repairs urushi was often coated with powdered gold (later burnished), or maki-e (pictorial) designs (fig. 7). No attempt was made to blend the fill in with the ceramic; in fact, the contrast presented by the original and the repair was esteemed.
Fig. 7.
Urushi repair with maki-e on a 16th-century Japanese bowl, Freer Gallery of Art, F 00.53
 |
Urushi requires a very high humidity and a long time (24 hours) to set. It is irreversible and extremely toxic to work with. While aesthetically challenging for Western tastes, when coated with gold it is protected from oxidation and light and thus very stable. Other lacquer types found in China and Burma are less stable and have not been found as repairs. True urushi would allow the ceramic to be reused, a feature important in Japanese culture.
By the late 20th century, with the advent of synthetic resin adhesives, urushi almost disappeared from use as a ceramic fill material. However, it still has some traditional use, and is recently making a comeback (see section 6, Conclusions).
UV fluorescence: None.
Solubility: Virtually insoluble. Can be softened by 50/50 acetone/ethanol or pyridine.
Clamps, Rivets, Solder, Bolts, Metal Pins, and Ferrules—Metal and metalworking techniques have been used since antiquity, both to join broken fragments and to fill the holes created by the drilling required for their attachment. Various types of metalwork, such as nails, screws, bolts and dowels, or pins were used to anchor fills to the ceramic, particularly when additional structural support was considered necessary (St.-Gaudens and Jackson 1953; Parsons and Curl 1963). These were usually inserted into a drilled hole and cemented in using a plaster or mortar rather than pressure-fit.
Metal armatures (see figs. 8 and 9) were in common use by the early 19th century. These included “wire supports, made to fit the individual piece in a neat and inconspicuous way” (quoted in Burns 1941, 161–62). They were usually made of copper or brass and often were anchored to holes drilled on the interior surfaces or break edges. Solder was probably first used as a joining agent and a fill material in the late 19th century. Pewter and tin solder were recommended for filling losses on the edge of china or porcelain after first grinding grooves or dovetails into the ceramic body to anchor the metal fill (Klein 1962; Yates 1953). Pewter pellets could simply be melted into position using a heavy-duty soldering iron without the use of any flux, but flux was necessary when two different metals were soldered together (Klein 1962). For large losses, the soldered dovetails served a dual purpose—as a fill and as an anchor for copper screening. The metal screening was tinned (coated with pure hot tin) to prevent corrosion of the copper (Klein 1962). Putties or synthetic glaze mixtures were then applied over the soldered fills or screening to imitate the ceramic surface.
Fig. 8.
Clay, mixed with animal glue, formed around a metal armature
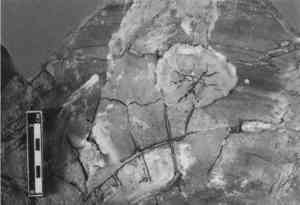 |
Fig. 9.
Metal armature, fabricated and anchored to the ceramic body to support fill material
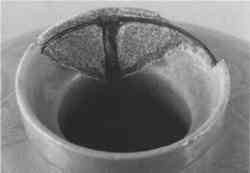 |
In general, metal dowels, pins, and armatures are not necessary for most ceramics restoration. They necessitate damage to the original and often result in additional weakness when done improperly.
Solubility: None. Mechanical removal required.
Substituted or “Alien” Fragments—From at least the 6th century B.C., and well into the 20th century, fragments or entire sections from another vessel were chosen to replace missing pieces and to fill losses (Khazanova 1978; Elston 1990a). In antiquity, substituted fragments on Greek vases were attached by mechanical means (clamps or staples) (Elston 1990a). On more recent repairs, attempts were made to fit in a fragment that was a good match, one with similar surface color or decoration (figs. 10–12), while in other cases the fragment only served as a support or fill and was disguised with surface fill or paint. The inserted fragments and those surrounding the loss were often cut or filed down, causing irretrievable damage to both original ceramic and fill. Whole sections of ceramics were “replaced” in this manner (Koob 1988), including handles, bases, rims, or losses to the body (fig. 13).
Fig. 10.
Section of Greek vase filled with substituted fragments. Note the attempt to line up the drapery designs (the lower fragment is from another vase).
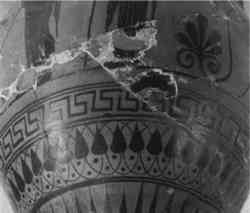 |
Fig. 11.
Section from fig. 10 removed. The white putty is an animal glue/whiting gesso
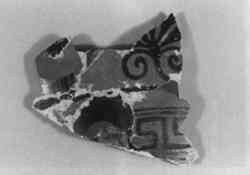 |
Fig. 12.
Section of fig. 11 as seen from the back. The assorted fragments are from numerous vessels, of different periods.
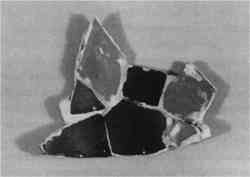 |
Fig. 13.
Major substitution ot restore a Greek vase. In addition to the fragments inserted into the body, the base and rim are also from entirely different vassels.
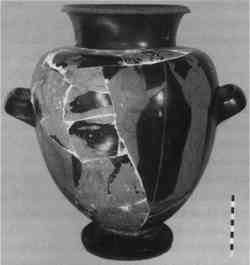 |
This practice was well-documented as noted in a 1769 advertisement for artificial replacements for teapots (Lanmon 1969). It was especially popular in the restoration of Far Eastern ceramics (Buys and Oakley 1993), and probably preceded the use of putties or cast fills. The ready availability of fragments from other vessels (lying around in the ceramics restoration workshop) was perhaps one of the reasons, but the practice was “justified” because a complete vessel resulted. Moreover, the restoration could not easily be identified as a fake, since simple examination or probing with a sharp tool would reveal “original” ceramic underneath the retouched surface.
These types of fills generally are not discovered until all the retouching and overpaint on the restored area is removed, or a very careful x-radiograph is examined, and still they may be undetected if the fragments were chosen from a vessel with nearly identical thickness and radio-opacity. X-ray fluorescence and x-radiography are useful nondestructive analytical techniques should the restorer have used two very different (but visually identical) ceramics, e.g., a lead glaze spout on an alkaline glazed body. Examinations to this extent were certainly not encouraged when a restored ceramic was offered for sale, and many composite restorations have gone unnoticed and undetected.
Solubility: Insoluble. Removal depends on method of attachment to original.
Natural Waxes—Natural waxes such as beeswax have been in use at least since Roman times (Braude 1943) and were certainly in use well into the 20th century (Yates 1953). Carnauba wax was often added to beeswax to form harder and more durable fills. It has been found as fills on Greek vases that were restored in the late 19th and early 20th centuries. Waxes were generally pigmented to match the ceramic or glaze color (fig 14).
Fig. 14.
Natural wax fills, colored green, on a Syrian bowl (with substituted rim fragments), Freer Gallery of Art, F 09.125
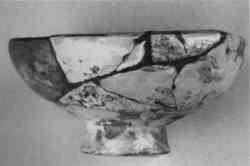 |
When pigmented and mixed with a resin such as gum elemi (for better adhesion), these wax fill mixtures made a very good imitation of a glazed surface. However, their poor aging properties and tendency to pick up dirt and grime or discolor have generally eliminated their use. Waxes were also recommended for strengthening and sealing fills (Lucas 1924). Appearances under ultraviolet light vary considerably, depending on mixtures.
UV fluorescence: Beeswax fluoresces yellow or, when old and oxidized, orange. Carnauba wax does not fluoresce but reflects a pale gray-blue.
Solubility: Petroleum distillates, such as ligroine, naphtha, and toluene. When severely aged, 1,1,1 -trichloroethane.
Paints and Sruface Coatings—These were an integral part of loss compensation and often substituted for fills or compensated for inadequate fill appearances. They were used with much the same chronology as waxes, and certainly included thinned wax or natural resins as binders. Paints were used to hide (and fill) in losses along break lines and to fill and cover minor scratches and other surface imperfections such as spalls or firing defects.
The most common paints and coatings were shellac (fig. 15) or gum based, with finely ground pigments as the colorants. Heavily pigmented paints using natural earth colors were very popular because they were hard to detect under UV light. By 1980, wax, shellac, and gum binders for paints had virtually disappeared from use, replaced by more stable media.
Fig. 15.
Sheellac-based paints, used to fill in surface losses on a Greek vase
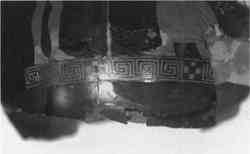 |
Natural waxes were also used alone to coat fills in an attempt to more closely imitate a ceramic surface sheen or glaze. The success with which waxes are able to produce a translucent or glazelike appearance still make them popular today, but most uses of natural waxes have been eliminated and replaced by more stable synthetic waxes (G�nsicke and Hirx 1997).
UV fluorescence: Varied, depending on the binding medium.
Solubility: Varied, depending on the binding medium.
Clay—Clay may have been used from antiquity to the 20th century to cover repairs or surface damage. It is commonly found completely covering the interior of vessels to hide repairs and was applied because it generally does not fluoresce on its own.
Unfired clay is not very stable, particularly in high humidity. Animal glue and shellac were common additives in the 19th century, as they allowed the clay to be molded or shaped, and they imparted significant strength and durability after drying and setting. Even so, it was generally necessary to build the clay “putty” up on a metal framework anchored into the original ceramic fragments (see fig. 8).
UV fluorescence: None.
Solubility: Water (unless mixed with shellac).
Lime Plaster, Cement—These materials were in common use from perhaps the 5th millennium B.C., but it is not known when they began to be used on ceramics for repairs. They were very popular from the late 18th century until the late 20th century. Lime plaster was often used to “anchor” pins and dowels and as a fill material. It requires a long time to set (12–24 hours), during which time the ceramic cannot be moved. Cement has been used to reinforce and “fill up” large storage vessels, particularly those on display in colonnades or outdoor exhibits of archaeological museums.
These materials are extremely detrimental to the ceramic because of the migration of salts and the stress created by the weight. They are almost impossible to remove without considerable damage.
Solubility: Lime plaster can be removed by wetting with water, followed by careful mechanical removal. Alternatively, careful application of a weak acid solution (e.g., 3–5% nitric acid) will break down the mortar or cement, but it is not recommended for ceramics with carbonate fillers or inclusions. Application must be followed by thorough rinsing.
Shellac—In common use as an adhesive and coating varnish from the late 16th century, well into the 20th century, this natural resin (secreted by an insect) was and is available in numerous grades, the most common being “orange flake.” Resin was dissolved in warm alcohol and boiled down to a thick syrup for use as an adhesive or a base for pigmented paint and putty (fig. 15).
Shellac became a favorite adhesive for complex pottery assemblies because of its thermoplasticity. This quality allowed a restorer to heat up a misaligned join and move the fragments into correct alignment. Unfortunately, the heating was generally done using an open flame (alcohol lamp or Bunsen burner), and the resin often burned, causing both irreparable damage to the ceramic and the insolubility of the resin. The disadvantages also include its very dark brown appearance, brittleness, structural failure, and difficulty in removal (Koob 1979; 1984).
Shellac was also bulked out like the animal glues for use as a fill material (fig. 16). Shellac and mastic (pine resin from Pistacia lentiscus) were mixed together to form a putty for repairing china (Braude 1943).
Fig. 16.
Shellac putty used to fill gaps between replacement fragments
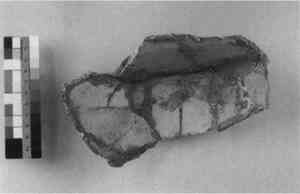 |
The problem of embrittlement is serious, as most shellac and animal glue restorations from the mid- to late-19th century have now reached the end of their physical stability. Stress caused by handling, shock, and abrupt changes in temperature or humidity can cause collapse and additional damage. With the advent of modern synthetic thermoplastic resins, shellac adhesive and shellac putties have almost completely disappeared from use on ceramics.
UV fluorescence: Although pure shellac is known for its distinctive bright orange or mustard yellow fluorescence under ultraviolet light, when bulked out with clay or fillers it is usually a dull orange.
Solubility: 50/50 acetone/ethanol, warm ethanol, pyridine (Koob 1979).
Glassy Fluxes—These were low-melting ceramic glazes or fluxes used to “fuse” broken fragments or substituted fragments together, in use from the 16th (possibly earlier) to 20th century. The application of fluxes or glazes was extremely risky because of the danger of breaking the original ceramic or ceramic fragments during the refiring procedure, as well as of damaging the original surface decoration, such as glazes and colored slips (Lanmon 1969; Marshall 1996).
If done carefully, the flux melted at a temperature lower than the original ceramic and not only joined the broken fragments together but filled any losses along the break line. Low-melting glazes were also used to fill small losses, such as chips missing from the rim. The ceramic could be reused.
Visually, there is always a color difference along the break edge. Pooling or surface buildup of the new glaze or flux was also common and necessitated grinding away of the excess, followed by polishing. The ceramic appeared whole under ultraviolet light.
Solubility: Totally insoluble; irreversible.
Wood—As early as 1760, elaborately turned wooden bases for goblets, or handles for teapots, were made to replace losses and “affixed” (Lanmon 1969). Wooden pins or dowels were also used to connect replacement fragments or fills to the original ceramic body. Sawdust was mixed with animal glue or other resin, for both small and large fills (Buys and Oakley 1993).
Wood fills have also been encountered in the form of blocks or chunks joined together by adhesive and puttied over (figs. 17, 18). After the initial discovery, the fills were examined by x-radiography to identify the construction technique (fig. 19).
Fig. 17.
Rim restorations removed from an earthenware bowl
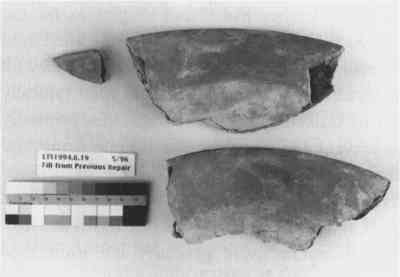 |
Fig. 18.
Detail of fig. 17 showing wood grain
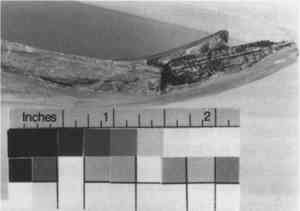 |
Fig. 19.
Radiograph of two rim restorations showing sections of wood
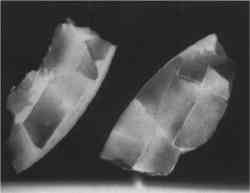 |
Manufactured Ceramic Fragments—From the 18th century (or earlier) to the 20th century, fired clay fragments were specifically manufactured to fill a loss. A suitable clay was chosen (e.g., earthenware for earthenware, white china clay for china) and the loss was filled with the wet clay, already formed to the appropriate thickness. The clay was probably rolled out as a slab, allowed to become “leather hard,” and shaped to fill the loss. As the clay dried, it would shrink and could be easily removed from the loss area. The clay fill was carefully allowed to dry and then typically cut or broken into smaller fragments, primarily to prevent additional distortion upon firing, and also to imitate the size and shape of original fragments. The fragments were then fired and used, as above, to fill in losses (see figs. 5 and 16). The fragments were generally left unfinished and were simply glued or puttied into place, then covered over with a finishing ground, gesso, plaster, and overpaint (see fig. 5).
These restorations are often difficult to discern in a simple examination or under ultraviolet light, as they are fired clay and their appearance is frequently very close to the original. Closer inspection reveals the absence of finishing marks (no wheel or turntable lines, no surface treatment such as slips or engobes), and a uniform thickness that is different from the ceramic into which it has been inserted. The edges are usually cut sharply or trimmed to accommodate the application of a thick adhesive or putty.
The earliest documented restoration incorporating this technique was 1837, but it is likely this technique was used much earlier. During the dismantling of a previous restoration, a fragment of the vessel was found to have been signed on the underside (interior) in ink with initials and the phrase “in Roma l'anno 1837” (see fig. 2). The fragment must have been signed during the restoration, as the vessel has too small a mouth and neck to get one's hand in.
The main disadvantage to this practice was the fact that the ceramic replacement part was subject to shrinkage, cracking, or distortion and after being joined to the original, still required touch-up and inpainting.
Solubility: Insoluble. Removal depends on method of attachment to original.
Manufactured Ceramic Replacement Fragments with Fired Decoration—This restoration concept, in use from the early 19th century to the mid-20th century, is similar to the fabricated body fragments described above but taken further, to produce a close or identical copy of the original (fig. 20). The initial manufacturing steps were the same as above, with the addition of surface decoration, done with slips or glazes. The fragments were again fired as fragments to minimize shrinkage, distortion, and changes in surface color. Multiple firings may have been required, for the clay and the glaze(s).
Fig. 20.
Manufactured replacement fragments with fired decoration, made of polychromed glazed ceramic, in the style of the original (fragment on the left is original; fragments on the right are modern replacements), Arthur M. Sackler Gallery, S 1987.85
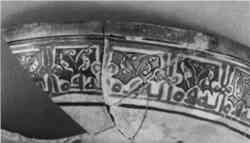 |
Without doubt, this method required enormous skill, knowledge of the original, and patience, especially in the reproduction of polychrome glazes. Manufactured fragments were adhered in place along with the original fragments. Minor flaws and gaps were filled and retouched. The results were often surprisingly good and this technique was certainly done with deceit in mind. The repair can be easily distinguished from the original once overpaint and adhesive are removed, however, because of the following flaws:
- A different clay composition was used.
- The fills or replacement pieces were fired as fragments, resulting in shrinkage, cracking, distortion, and melting of the glaze (if applied) over the edges.
- Glazes rarely have similar colors, compositions, or physical properties (i.e., crackle), when compared closely to the original.
- Glazes often have flaws characteristic of being fired as fragments, such as pooling or “beading up” along break edges. Sometimes these flaws have been filed or sanded off.
This technique has been found on numerous types of ceramics, including Greek vases (Snow 1986), European 18th-century ceramics (Buys and Oakley 1993), and Islamic pottery (see fig. 20).
Solubility: Insoluble. Removal depends on method of attachment to original.
Sodium Silicate—Sodium silicate was recommended for use from the early 19th century to the mid-20th century. Also known as “water-glass,” this material was produced by melting purified silica sand with soda ash or sodium sulfate, then dissolving the resulting glass mixture in water (Skeist 1977). It was readily available as a ground powder or in solution of various specific gravities. Recommendations for use included mixing it into a paste with whiting, pigments, ground glass, or flint (St.-Gaudens and Jackson 1953; Hiscox 1948).
This compound is basically a water-soluble glass produced by mixing excess alkali with silica. It behaves similarly to a severely crizzled glass in that repeated exposure to high humidity will rapidly leach out the soluble alkali and degrade the glass. Limitations also include the fact that the sodium silicate paste and ceramic original need to be heated for application.
Solubility: Limited solubility. Once set, the paste behaves like a weak, unstable glass.
Paper, Papier-m�ch�, Other Cellulosic Materials—In use from the mid-19th century to early 20th century, shredded paper was boiled with glue, whiting, linseed oil, and turpentine to make a “stone cement” for filling large gaps on ceramics (Rathgen 1905). Newspaper, envelopes, and other paper materials were used as crude molding or backing material and have often been found left on the inside of a vessel attached to putties or cast fills. The date of the newspaper or stamped envelope often provides information as to the date of the restoration. Cotton bandages were recommended for use as reinforcements on the inside of the ceramic “when a heavy pot is reconstructed from a great many pieces” (Plenderleith 1934, 25–26). The bandages were soaked in shellac, glue and plaster, or wax mixtures (fig. 21).
Fig. 21.
Gauze soaked in animal glue, used as backing for a fill
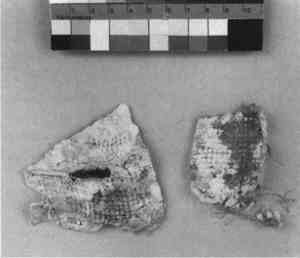 |
Solubility: Dependent on binding material.
Gutta-percha—A natural rubber latex, gutta-percha was used from the late 19th to the early 20th century both as a bonding and fill material (Braude 1943; Yates 1953). This material is extremely viscous and difficult to work with, is dark in color (but can also be bleached), and ages poorly, with significant shrinkage and embrittlement. Rubber “varnish” was also suggested as a binding agent for a colored fill (Andr� 1976). The aging properties of this material are known to be poor (Horie 1987).
UV fluorescence: None.
Solubility: Chlorinated hydrocarbons, especially chloroform. When aged and brittle, it becomes totally insoluble. Very hot water (70–80�C) will soften the rubber enough for it to be peeled away without damaging the ceramic.
Cellulose Nitrate—This extremely popular synthetic resin has been in conservation use since the late 19th century (Horie 1987). When bulked with sawdust, it was popularly known as “Plastic Wood” (St.-Gaudens and Jackson 1953). The color of the fill depended on the color of the sawdust used and any added pigment.
This resin was also recommended as a strengthening agent (or consolidant) for fills (Lucas 1924). Problems and limitations included considerable shrinkage and poor stability. The resin yellows appreciably, becomes extremely brittle, and can eventually crack and disintegrate. Since the advent of polyvinyl acetate and acrylic adhesives, the manufacturing production of this resin has dropped off dramatically, as has its popularity.
UV fluorescence: Pale yellow.
Solubility: Extremely soluble in acetone, even when old.
Cellulose Acetate—This is a close relative to cellulose nitrate and was used slightly later (1920 to 1980) and much less frequently. It is more brittle than cellulose nitrate but became popular because of its lower inflammability. It was recommended as a strengthening agent for fills (Lucas 1924). It oxidizes at room temperature, becomes brittle, and has poor water resistance.
UV fluorescence: Very pale white.
Solubility: Acetone, ethyl lactate, methylene chloride.
Polyester Resins—In use from the early to the late 20th century, these synthetic resins were recommended for fills on both ceramics and glass (Parsons and Curl 1963; Andr� 1976). They were sometimes strengthened or backed with fiberglass (fig. 22). Polyester resins shrink and are very exothermic during setting, tend to be very brittle, and are difficult to remove without loss of ceramic surface. Other forms of polyester resin include proprietary “car body fillers,” which were recommended under this category as suitable for filling porcelain (Williams 1983). Objections and drawbacks include the unknown compositions, accelerators for setting, considerable shrinkage, and color. Polyester resins are catalyzed by a peroxide initiator but also have added accelerators (for fast, controlled setting) which cause yellowing and anaerobic surface setting (Horie 1987; Skeist 1977).
Fig. 22.
Polyester resin, backed with fiberglass
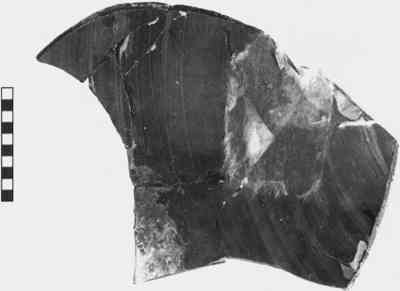 |
The excessive strength of the polyester resins makes them inappropriate for use on ceramics and they are also susceptible to yellowing, oxidation, and hydrolysis (Horie 1987).
UV fluorescence: Bright white; when deteriorated, yellow.
Solubility: Polyester resins swell in acetone, methylene chloride.
Poly (Vinyl Acetate) Putties—In the early to mid-20th century, vinyl acetate resin (grade unknown) mixed with clay was suggested as a plastic putty. This mixture “becomes extremely hard and strong after it sets” (Burns 1941, 161). White glues are proprietary emulsion adhesives based on polyvinyl acetate or acrylic resins and have also been bulked with whiting and pigments to form a paste for fills (Andr� 1976).
The dispersions in water have emulsifiers and plasticizers that cause yellowing and cross-linking (Horie 1987). They also have very low glass transition temperatures and tend to attract dirt and grime.
UV fluorescence: Pale white.
Solubility: Vinyl acetate resins are soluble in acetone, or alcohol, preferably with a small amount of water. White glue putties swell or gel in acetone and alcohol.
AJK/BJK Dough—In use as a fill material from 1960 to 1980, this consisted of a mixture of Alvar (polyvinyl acetal), jute, and kaolin in solvents, to be used as a putty (UNESCO 1968). It could also be rolled out and cut into small strips to be used dry. Since Alvar is thermoplastic, the dry strips could be warmed and shaped to fit the size and contours of a loss. After cooling, the shaped strips were stuck in place with an adhesive to form a support grid upon which more AJK Dough putty could be added to complete the fill. Because of the high proportion of solvents in the dough mixture, shrinkage was generally a serious problem, and it was necessary to apply thin layers one at a time. The filled area could then be worked to a final surface using solvents or mechanical means, often with an agreeable appearance, without any added coloring or inpainting (fig. 23).
Fig. 23.
Earthenware storage jar with losses filled using AJK dough. Fills are not pigmented or painted.
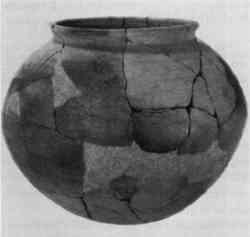 |
In 1980, Alvar ceased to be manufactured and was replaced by Butvar (polyvinyl butyral), made up to form BJK Dough. The properties and uses of the material remained the same. The idea of creating a stable and reversible backing or lattice-support that was thermoplastic remained popular. The BJK strips were stuck in place using an adhesive, and, instead of completing the fill with more BJK Dough, acrylic or other putties were generally used.
Although stocks of this dough still remain in numerous laboratories, its use has virtually ended and it has been replaced by other materials such as Hexcelite (Brown 1989).
UV fluorescence: AJK Dough fluoresces a very pale yellow-orange, mostly masked by the jute fibers. BJK Dough was not examined.
Solubility: AJK Dough is soluble in acetone, and acetone/alcohol. BJK Dough is soluble in alcohol.
|