AN ECONOMICAL DESIGN FOR A MICROCLIMATE VITRINE FOR PAINTINGS USING THE PICTURE FRAME AS THE PRIMARY HOUSING
LAURENT S. G. SOZZANI
ABSTRACT—This article describes an economically designed microclimate vitrine for panel paintings, which can be easily produced in-house with minimal aesthetic compromise to the paintings. The design uses the picture's frame as the primary housing in combination with museum glazing and a backplate to create a sealed microclimate vitrine. It is also adaptable to other framed artworks (canvas, paper, parchment) in need of microclimate protection. A sum-mary is given of tests carried out at the Central Research Laboratory in Amsterdam using this design and another more costly commonly used design. The latter consisted of a closed box made of inert materials containing the painting, which in turn is set into the picture's frame. Testing showed that the two designs perform with similar efficiency. Further, the use of silica gel in a closed system with minimized air space is reevaluated. A design plan and materials are included.
TITRE—Un Concept Economique de Vitrine Climatis�e pour Peintures pur Panneau, Utilisant le Cadre du Tableau comme Support. R�SUM�—Cet article pr�sente un concept �conomique de vitrine climatis�e, destin� aux peintures sur panneau; ce dispositif, satisfaisant du point de vue esth�tique, peut sans difficult� �tre mont� sur place. Le cadre de la peinture sert de support � un coffrage compos� d'un vitrage, du type habituellement utilis� pour les tableaux, et d'une plaque, dispos�e derri�re le panneau. L'auteur fait un r�sum� des tests effectu�s au Laboratoire central de recherches d'Amsterdam sur cette vitrine et sur u autre, couramment utilise mais plus on�reuse. Cette derni�re consiste en un bo�tier �tanche en mat�riaux inertes, qui renferme le tableau et s'ins�re dans le cadre. Les tests d�montrent que ces deux syst�mes pr�sentent une efficacit� comparable, et remettent en question la n�cessit� d'utiliser du gel de silice dans des vitrines de ce genre, qui ne contiennent qu'un volume d'air minime. L'article comprend enfin des sch�mas du coffrage et apporte des pr�cisions sur les mat�riaux utilis�s.
TITULO—Dise�o econ�mico de una vitrina con microclima para pinturas que utiliza el marco de la misma como montaje primario. RESUMEN—Este articulo describe un dise�o econ�mico de vitrina con microclima para pinturas sobre maderas, que puede ser f�cilmente fabricada en la instituci�n y que compromete la est�tica de las obras en forma m�nima. El dise�o utiliza el marco de la pintura en combinaci�n con vidrio apto para museo y una placa en la parte posterior para crear un microclima dentro de una vitrina sellada. Es apropiado tambi�n para otras obras de arte enmarcadas. Se presenta un resumen de las pruebas que fueron hechas en el Laboratorio Central de Investigaci�n de Amsterdam, utilizando este dise�o y otro mas costoso y com�nmente usado. Este ultimo consiste en una caja cerrada construida con materiales inertes que contiene la pintura, y que luego se monta en el marco original. Las pruebas demostraron que los dos dise�os funcionan con eficiencia similar. Ademas, como resultado de las pruebas se reconsidera el uso de gel de s�lice en un sistema cerrado con m�nimo espacio para aire. Se incluyen un plan del dise�o y los materiales de construcci�n.
1 INTRODUCTION
Fluctuations in ambient temperature and relative humidity and the subsequent deleterious effects on artworks is an accepted and well-studied subject that has generated numerous bibliographies (Thompson 1964; Padfield 1966; Hackney 1990; Michalski 1991; Skalka 1991). Maintaining the physical stability of artworks is essential to their preservation. The demand for traveling exhibitions escalates concern for the artworks' stability. For a painting on a wood support, these fluctuations can yield changes in the moisture content of the wood itself, causing shrinkage and expansion. These changes, in turn, can weaken the adhesion between the paint and/or ground layers and the wood support, resulting in paint loss. Controlling the moisture content of the wood panel and thereby minimizing this process has been the goal of many conservation practices.
The need to control moisture content has led to the development of systems for protecting panel paintings in sealed, climatically stable microenvironments used in transit and/or during exhibition in what may be climatically unstable external environments (Sack and Stolow 1978; Ramer 1984; Bosshard 1990; Hackney 1990; Richard 1994; Wadum forthcoming). Museums often use stationary, climate-controlled vitrines in-house, and borrowing institutions can provide them as part of a loan requirement. Even with proper packing and transport, however, such a requirement does not ensure protection during transfer of the artwork into or out of the vitrine, nor does it address the possible differences between the initial environment and the new preconditioned one. Further, though the design and construction of the in-house vitrine may be close to ideal and the internal environment carefully monitored, responsibility rests entirely on the borrowing institution.
2 MICROCLIMATE VITRINES FOR TRAVEL AND EXHIBITION
The use of preconditioned vitrines within which an artwork travels and remains during exhibition has been considered the safest system for keeping fragile, humidity-sensitive artworks stable. These vitrines, however, often prove to be aesthetically displeasing. Emil Bosshard (1990), following a design originally presented by B. Ramer (1984), solved this problem by designing a small vitrine that tightly encloses the panel painting. This package is subsequently set into the rabbet of the picture frame.1 The result, an aesthetic success, is no more disturbing than any glazing. The use of nonreflective safety glass further reduced glazing problems. Many institutions and private collectors have benefited greatly from this design. In the past, the Rijksmuseum in Amsterdam also used this type of vitrine, commercially made to order. The system was not without drawbacks, however. The cost for even the smallest vitrine began at approximately $600 (Dfl. 1,200) and could easily be $2,000 or more for a vitrine 70 � 80 cm in size. Orders often had to be placed far in advance, and the subsequent in-house installation of the painting into the vitrine was time consuming. Further, framing the whole could involve complex alterations to the original frame. Variations on the design developed at numerous institutions were often complex and time consuming to construct.
3 A NEW, ECONOMICAL DESIGN
In 1993 the following design for creating a microclimate vitrine for individual paintings was officially recognized by the Dutch Ministry of Culture2 as a viable and economical alternative to the more costly commercially fabricated vitrines following the Bosshard design. This design, like Hackney's (1990) enclosure, uses a picture's frame as the vitrine body. It differs primarily in that it is a completely sealed microclimate. It is meant to be produced in-house with a minimum number of components added to the frame, by personnel with basic conservation framing, glazing, and woodworking skills. Though intended primarily for wooden panel paintings, the design is also suitable for other framed artworks in need of a microclimate, such as paintings on canvas, parchment, and paper. This frame-vitrine design was first used by the paintings department of the Rijksmuseum in Amsterdam for three panel paintings by Rembrandt that traveled with the exhibition Rembrandt: The Master and His Workshop in 1991–92. With modifications it has subsequently been used for a number of other pictures, both traveling for loan and on permanent display.
Simply stated, the design consists of airtight glazing at the front and an airtight backplate attached to the reverse of the frame. The frame itself provides the airtight seal at the edges. In the case of an insect-damaged, very thin, or otherwise porous frame, the inside of the frame rabbet can be sealed with impermeable sheeting. Sealing and mounting variations are made to suit the needs of both painting and frame.
4 THE BASIC DESIGN
Figure 1 illustrates the overall simplicity of the design. Numerous options for sealing the glass and backplate can be explored and may depend on the availability of particular materials from local suppliers. Details of the design and materials are discussed in section 7.
Fig. 1.
Schematic of cross section of microclimate frame vitrine
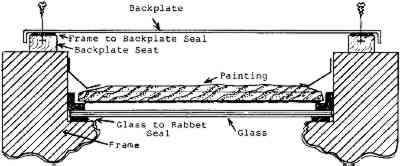 |
5 TESTING THE DESIGN
From 1992 to 1994 testing was carried out in Amsterdam at the Central Research Laboratory for Objects of Art and Science (CRL)3 in collaboration with the Rijksmuseum, Amsterdam, and the Mauritshuis, The Hague. The goal was to evaluate the mechanics and viability of microclimate vitrines as protection for panel paintings. The research was also designed to compare the effectiveness of the wooden picture-frame vitrine with the more commonly used Bosshard inert, insertable box design. A poster presented at the International Institute for Conservation 15th International Congress held in Ottawa, Canada, in 1994 gave details of the experimental setup and was published in the poster preprints (Wadum et al. 1994). A synopsis of the testing, results, and conclusions follows.
5.1 EXPERIMENT SETUP
Two microclimate vitrine designs were tested. The first was the wooden frame design, the type used in the Rijksmuseum and presented in this article. The second type, constructed following the Bosshard design, used an aluminum box as the housing for the painting. This vitrine design was in use at the time at the Mauritshuis (Wadum 1992).
An array of the two microclimate vitrine types was created, each assembled with different internal configurations that accounted for specific variables—empty or with a wooden panel and/or with silica gel.4Figure 2 depicts a partial view of the climate room at the CRL. Three of the six microclimate vitrines as assembled for testing are visible. The internal volume of each vitrine was approximately the same (� 5.4 L). The panels used were solid oak, equal in size and from the same source (� 75 years old). The amount of silica gel (Art-Sorb sheet) used was constant.
Fig. 2.
Partial view of the climate room at the Central Research Laboratory showing three of the six microclimate vitrines as assembled for testing. Photograph by Ton Jutte
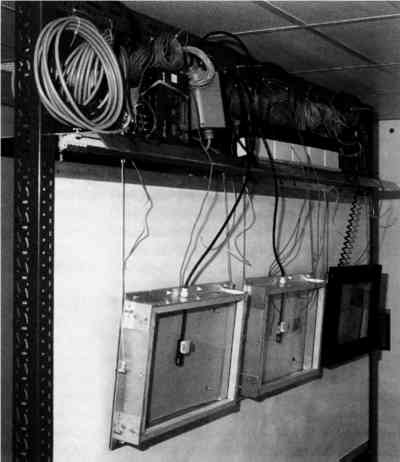 |
Six vitrines at a time were hung in a climate room (specially constructed at the Central Research Laboratory for this type of testing) and subjected to 18 week-long sessions of controlled cycles of varying temperature and/or relative humidity.5 RH and temperature sensors attached to data loggers were positioned at locations inside and around the vitrines.
5.2 SUMMARY OF RESULTS
With constant temperature and fluctuating relative humidity (30–70%) in the ambient environment, there was no effect on RH or temperature within the microclimate vitrines. Conversely, with cycles of fluctuating temperature (10–30�C) and constant RH, both the temperature and the RH fluctuated inside all boxes, regardless of the contents. (In vitrines containing silica gel, however, the RH fluctuation was minimal in the vicinity of the silica gel.) Temperature changes inside the boxes quickly followed outside temperature changes.
In the wooden frame vitrines that were empty or contained only a wooden panel, and in the aluminum vitrines that held only a wooden panel, RH values rose and fell in correspondence with increases and decreases in temperature. In an empty aluminum vitrine, however, the opposite occurred: as the outside temperature rose, the inside RH dropped and vice versa.
In both types of vitrines, when a panel and silica gel were inside, RH remained stable behind the panel where the silica gel was located, whereas fluctuations were recorded in front of the panel. This finding indicated little transport of humidity between the air space in front of the panel and that behind the panel, although 2 mm air gaps were maintained around the edges of each panel.
5.3 DISCUSSION
Normally, as recorded in the empty aluminum vitrine, a rise in temperature in a closed, inert environment leads to a lowering of RH. The rise and fall in RH with a corresponding rise and fall in temperature in the vitrines either made of wood or containing wooden panels (and no silica gel) indicates that the wood gives off some of its moisture with a rise in temperature (drying) and absorbs moisture when the temperature is lowered.
In the presence of silica gel, the moisture given off by the wood with a rise in temperature will be absorbed by the silica gel as the silica gel reacts to the change in RH thereby maintaining its preconditioned RH. Due to the response of silica gel, in a period of sustained, elevated temperature, the wood can continue to give off moisture that in turn, is absorbed by the silica gel. The consequence is a greater potential for dimensional change in the panel, precisely what one seeks to minimize by employing a vitrine.6
In contrast, under the same conditions of elevated temperature within a vitrine, in the absence of silica gel (or other RH-activated buffering material), the wood itself will quickly reach an equilibrium with the surrounding internal atmosphere after having exchanged only an inconsequential amount of moisture. The following data support this result:7
- internal volume of the microclimate boxes: 5400 cm3
- weight of wood panel: 400 g
- volume of wood panel: 900 cm3
- moisture content of panel: 36 g of contained water when stabilized at 20�C, 55% RH
- volume of air in a vitrine containing a panel: 5400 cm3–900 cm3 = 4500 cm3
- water content in 4500 cm3 air:
at 10�C, 55% RH = 0.027 g waterat 20�C, 55% RH = 0.049 g waterat 30�C, 55% RH = 0.090 g water
With a rise in temperature from 10�C to 30�C, the air will reach a moisture content equilibrium with the addition of 0.063 g of water (0.090–0.027 = 0.063). This change in moisture content results from moisture being released from the wood; it is recorded as a rise in RH in vitrines containing a panel. This additional moisture, if released entirely by the panel, is equal to only 0.18% of the 36 g of water contained in the wood panel at 20�C. More realistically, with a less dramatic rise in temperature, from 20�C to 30�C, the panel would release 0.041 g of water, a mere 0.11% of the 36 g of water in the panel at 20�C.
Further, with a fall in temperature from 20�C to 10�C, the air will lose 0.022 g of water (0.049–0.027 = 0.022). This amount is equal to only 0.07% of the 36 g of water in the wood panel at 20�C. These exchanges in moisture between the wood and the air may be recorded as large changes when measuring RH within the closed space of a vitrine, but the amounts of water involved are actually quite small and will result in little or no substantial dimensional change in the panel painting.
Minimizing the air space within the microclimate box will reduce the capacity for moisture exchange and hasten an equilibrium between wood and air.8 It is also probable that additional temperature-regulating hygroscopic material, such as the exposed wood at the inside of the frame or the addition of wood or other cellulosic materials (such as museum board placed behind the painting), will reduce the overall burden of moisture loss and uptake by the wood panel. This observation appears to be confirmed in current research at the Central Research Laboratory on the mechanics and materials of backing boards on canvas paintings.9 Preliminary testing of various backing board materials indicates that the more hygroscopic the backing board the greater the overall buffering effect.
5.4 SUMMARY OF CONCLUSIONS OF THE MICROCLIMATE RESEARCH PROGRAM
- Silica gel used as a buffering material sealed in a microclimate vitrine with minimum air volume can have an added negative effect on the fluctuations of moisture content into and out of wooden panels. Its use is especially detrimental at sustained high temperature and can result in greater moisture loss from a panel than when silica gel is absent. This finding implies a major change in commonly held beliefs regarding the necessity of silica gel and, in practice, implies an adapted design of microclimate vitrines.
- A wooden panel in a sealed microclimate vitrine with minimal air volume in the absence of added RH-activated buffering material (i.e., silica gel) will reach a moisture equilibrium with the surrounding air, stabilizing with inconsequential moisture transfer. Moisture exchange will remain inconsequential as RH within the vitrine changes in relation to temperature changes, if the volume of air within the vitrine is kept at a minimum and no leakage occurs.
- Outside fluctuations in RH have no effect on the RH inside a well-sealed vitrine.
- Most relevant to the evaluation of the economical design presented here is the absence of a significant difference in behavior between the two types of vitrines that were tested. The only difference was the additional buffering provided by the release and/or uptake of moisture by and from the exposed interior of a wooden frame.
6 IMPLICATIONS OF TESTING ON THE SIMPLIFIED ECONOMICAL DESIGN
The removal of silica gel as an RH buffer from the microclimate vitrines used by the Rijksmuseum, a consequence of the conclusions derived from the microclimate research program, is the single most significant change to the vitrine design since 1991. The omission of silica gel further simplifies the design and reduces the overall cost of fabrication. More important, it signals a shift from considering fluctuations in relative humidity and temperature as the only gauges for monitoring conditions within a sealed vitrine to including and emphasizing absolute moisture content (acknowledging the moisture exchange of the contents) as of primary importance. Despite the benefits of this design, it cannot be overemphasized that only in well-sealed microclimate vitrines with minimal internal air volume can the object come into a moisture equilibrium with the surrounding air with inconsequential moisture exchange between the air and object.
The fact that the economical frame-housing design performs at least as well as the previously popular box-insert design has positive financial implications for institutions and private owners. The implicit danger of allowing paintings to travel that otherwise would not have been available for travel should not be overlooked when considering any vitrine design. At the Rijksmuseum, however, as in many institutions that house a large number of panel paintings and have an active loan program as part of their cultural responsibility, an economical, safe, and effective traveling vitrine is a necessity.
7 DESIGN PLAN AND MATERIALS
The basic materials mentioned here are available in most countries. If a particular component is unavailable, another similar material can be substituted. Often, sealants, gasket material, and framing attachments can vary from vitrine to vitrine due to the structure of the particular frame or painting. Nevertheless, the basic design (fig. 3)—adding glass and a backplate to a frame, sealed to create an airtight package that encloses a painting within its frame—remains constant. The success of the design depends on properly sealing the system, eliminating the possibility of air exchange with the outside.10
Fig. 3.
Schematic of cross section of microclimate frame vitrine illustrating all additional parts and framing elements
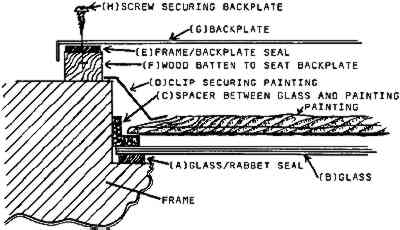 |
7.1 FRAME RABBET
The frame rabbet should be carefully examined and evaluated for possible leakage. A solid, flat, rabbet poses no problem for sealing the glass. Open corner joins, splits, and insect holes, however, should be filled and sealed with a good proprietary wood filler or silicon seal material. If a frame is badly insect-damaged or otherwise porous, the entire rabbet can be covered to seal it. This procedure can be done easily and quickly using a proprietary aluminum or polyester self-sticking tape. As an alternative, an aluminum or polyester film prepared with a heat-set adhesive can also be used. Marvelseal 360A, an aluminum polyethylene laminate prepared with BEVA 371 as the adhesive, is a good combination for this purpose.
7.2 SEAL BETWEEN GLASS AND FRAME (A)
Closed-cell neoprene, felt fabric lightly impregnated with microcrystalline wax, or any of a variety of proprietary self-sticking gasket materials that are relatively dense, impermeable, and neutral in color are suitable for use.
If the frame rabbet is uneven or out of plane, a thickened silicone-rubber mold material can be carefully applied to the rabbet and pressed flat by the glass during curing. The silicone-rubber will conform to the space between the glass and rabbet, forming a custom seal. After curing, any excess can be easily trimmed from the front along the edge of the sight opening and from the back along the edge of the glass.
7.3 GLASS (B)
The Rijksmuseum uses Schott Mirogard Protect Magic Glass, type 22.1, a nonreflective, glass-acrylic-glass laminate for both aesthetics and safety. (Noviflex: GE Coated Safety Glass, first quality, has also been used.)
7.4 SPACER BETWEEN GLASS AND PAINTING (C)
As in normal glazing practice; L-shaped wood or cork can function both as a spacer and to hold the painting in the proper sight position. Felt added to the spacer will protect the picture from abrasion.
7.5 CLIPS HOLDING THE PAINTING (D)
Spring clips, bent brass plates, or wood, cork, or foam blocks in different variations have been used.
(Note: With the exception of the air-tight sealing of the glass, after the clips are inserted, the painting is framed as with normal glazing.)
7.6 BACKPLATE SEAL (E) WITH OR WITHOUT WOODEN BATTENS (F)
This step both seals and seats the backplate to the frame. As with the glass-to-frame seal (section 7.2), it is important to create an airtight fit. A variety of options are available. As illustrated in figure 3, thin wooden battens are generally used to seat the turned-over lip of a metal backplate (G). The battens can be as thin as necessary to seat the backplate or adjusted in thickness to increase the depth of the frame rabbet to accommodate a thick or cradled panel. The battens must be sealed overall to the frame back and to each other at their corners. Silicone or acrylic seal materials are suitable for this purpose. Custom-shaping the undersurface of the wooden battens can level any slight unevenness of the frame back. As an alternative or for a very uneven or rough frame back, silicone rubber mold material can be used between the battens and frame to create a good seal, following a procedure similar to that in section 7.2. If available, a dense, impermeable gasket material of the proper thickness can be substituted for the wooden battens to both seat and seal the backplate.
7.7 BACKPLATE (G)
At the Rijksmuseum, 1-mm-thick sheet metal with the four edges bent over 3 mm to a 90� angle for added rigidity is being used most often. Stainless steel, galvanized steel, or aluminum are all suitable. These are made to order at a local sheet metal shop.
Other options for the metal plate include wood, acrylic sheet, polypropylene channel plate, and Fome-Cor covered on one side with Marvelseal 360. Backplate material should in any case be impermeable to long-term moisture. If the edge of the material is not sufficiently rigid, it is advisable to use L-shaped metal trim over the edges to increase the rigidity, thereby reducing the possibility of warping and subsequent air leaks. Figure 4 illustrates four of the many possible options for attaching different backplates. The backplates are attached to the wooden batten or frame back with wood screws (H). As a rule of thumb the screws are never more than 10 cm apart.
Fig. 4.
Fitting and sealing different backplates: (a) metal backplate with wooden battens; (b) metal backplate with a thick, dense gasket; (c) alternative backplate material with wooden battens and L-shaped metal added for rigidity at the edges; (d) alternative backplate material secured directly to the frame back using L-shaped wood or metal
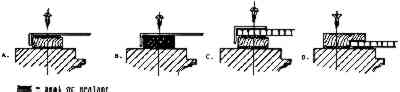 |
8 CONCLUSIONS
The viability of the microclimate frame-vitrine depends on successfully sealing the interior air space from the outside air. Minimizing the interior air volume in relation to the panel volume ensures minimal moisture transfer. The seals and backplate needed can be made from a variety of readily available, low-cost materials, thus ensuring the practicality of the design. The use of high-quality glass will be the greatest expense. The development of this vitrine design has resulted in cost savings of 60–70% per vitrine at the Rijksmuseum.
Fig. 5.
Rembrandt van Rijn, Jeremiah, 1630, oil on oak panel, Rijksmuseum, Amsterdam, SK-A 3279, in an antique frame that is now a microclimate vitrine, front view
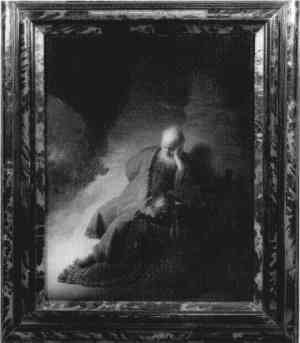 |
Fig. 6.
Reverse view of fig. 4 showing metal backplate. This early backplate has a cutout in the metal, sealed from the inside with an acrylic sheet, to allow the viewing of a paper hygrothermograph, a design aspect since discontinued
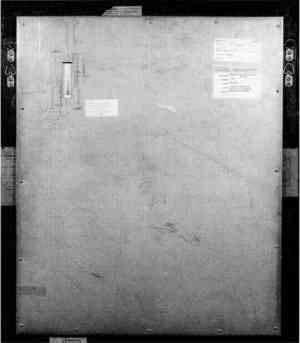 |
Fig. 7.
Detail of fig. 5, reverse frame corner, showing backplate mounted over wooden battens
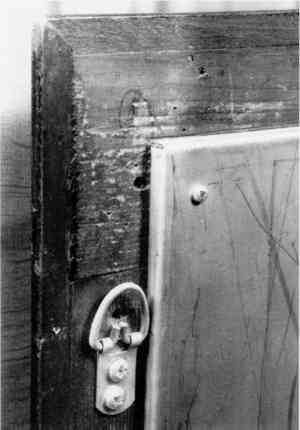 |
Fig. 8.
Rembrandt van Rijn, Old Woman Reading, c. 1631, oil on oak panel, Rijksmuseum, Amsterdam, SK-A-3066, in a new frame that is now a microclimate vitrine
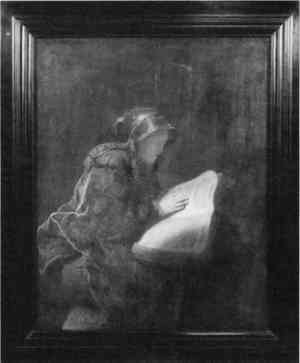 |
Fig. 9.
Reverse view of fig. 8, showing metal backplate
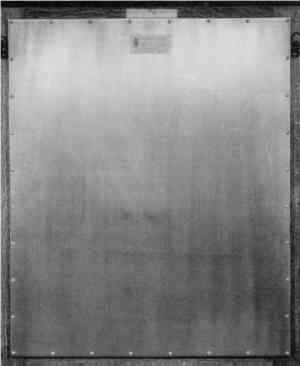 |
Fig. 10.
Detail of fig. 9, reverse frame corner, showing backplate mounted over wooden battens
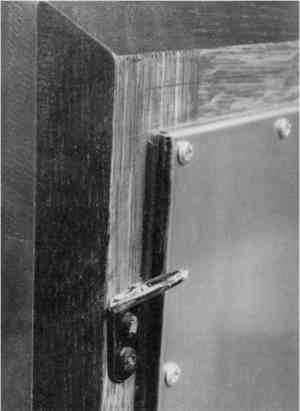 |
Fig. 11.
Frans van Mieris, The Letterwriter, 1680, oil on oak panel, Rijksmuseum, Amsterdam, SK-A-261, in a recently acquired antique frame that is now a microclimate vitrine. Photograph by the Rijksmuseum, Amsterdam
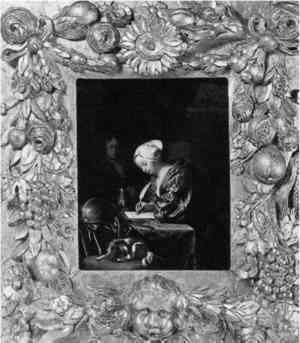 |
Fig. 12.
Reverse view of fig. 11, showing metal backplate. Photograph by the Rijksmuseum, Amsterdam
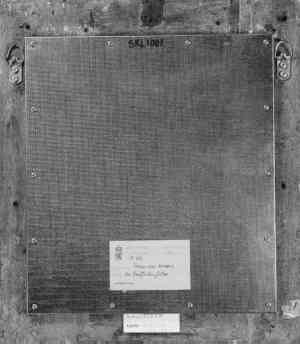 |
Fig. 13.
(above). Detail of fig. 11, edge of frame, showing metal backplate mounted to wooden batten. Photograph by the Rijksmuseum, Amsterdam
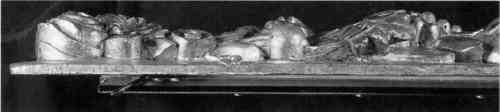 |
Fig. 14.
(left). Vitrine elements for fig. 11 (left to right): metal backplate; wooden betten with seal made from silicone mold material; frame, Photograph by Hubert Baya
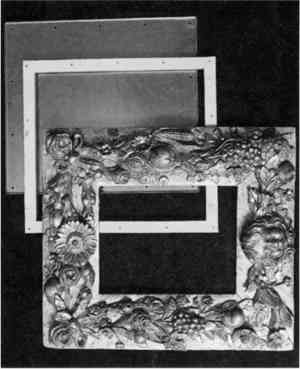 |
ACKNOWLEDGEMENTS
The author is greatly indebted to the Microclimates Research Group at the Central Research Laboratory, Amsterdam, for the comprehensive testing of the design model and to the Paintings Restoration Department of the Rijksmuseum, Amsterdam, for continual dialogue and support. Special appreciation is extended to Hubert Baya, Rijksmuseum frame restorer, for his ongoing involvement in the refinement and fabrication of the vitrines.
NOTES
1. This design concept is predated in an English patent of W. S. Simpson (1892). (Hackney [1990] refers to a J.M.W. Turner painting in the collection of the Victoria and Albert Museum that has never been removed from a Simpson box and appears to this day to be in good condition.) Sack and Stolow (1978) also established the overall viability of a similar design in their testing and application to a Fayum portrait.
NOTES
2. This design was recognized as follows: De Idee�ncommissie van het Ministerie van Welzijn, Volksgezondheid en Cultuur heeft een beloning toegekend aan de heer L.S.G. Sozzani voor een idee inzake klimaatdozen, in de lijst geplaatst. 10 maart 1993 (The Idea Commision of the Ministry of Welfare, Health, and Culture awards to Laurent Sozzani a prize for the idea of a climate box in the picture's frame. March 10, 1993).
NOTES
3. Centraal Laboratorium voor Onderzoek van Voorwerpen van Kunst en Wetenschap, Gabri�l Metsustraat 8, 1071 EA Amsterdam.
NOTES
4. The vitrines were assembled as follows: Aluminum frame design: (1) empty; (2) with oak panel only; (3) with silica gel only; (4) with oak panel and silica gel. Wooden frame design; (5) empty; (6) with oak panel and silica gel; (7) with oak panel only (after week 10).
NOTES
5. Weeks 11 to 17 included the addition of direct illumination of the vitrines and/or cooling of the wall behind the vitrines. Illumination to 450 lux using either tungsten or halogen lamps produced no more than a 3�C increase within any vitrine. Cooling the wall to 10�C lower than the room temperature had even less effect on internal temperatures.
NOTES
6. Richard (1994) refers to the temperature-induced expansion and contraction of wooden panels. In a personal communication (1996) he emphasized that at elevated temperature, expansion of a wood panel can counteract contraction due to moisture loss, and vice versa at lower temperatures, even if the changes are accentuated by the activity of silica gel. He does not recommend removing silica gel but prefers it as a safety factor in case of a leaking vitrine. He does concede that the overall effect of silica gel in a well-sealed vitrine with little air volume is so minimal that its presence or removal is of little consequence. Richard also warns that the improper conditioning of silica gel in a vitrine constitutes an additional drawback in its use.
NOTES
7. Simplified by Jorgen Wadum for the Research Program Microclimates Group using the approximate volumes and weights of the vitrines and panels used in the research program.
NOTES
8. Richard (1991) and Saunders et al. (1991) confirm and utilize this concept in their packing procedures.
NOTES
9. Collaborative research by G. Di Pietro, J. Wadum, IJ. Hummelen, W. Kragt, B.A.H.G. J�tte, L. Sozzani, and A. Brokerhof on microclimates, specifically backing boards, is in progress (1995–97) at the Central Research Laboratory, Amsterdam.
NOTES
10. Stolow (1967) warns of the extreme differences in air pressure and temperature encountered during air transport and the need for controlled cabin pressure and temperature when shipping sealed vitrines. These conditions are especially important with an airtight case to prevent the breaking of seals. Toishi and Gotoh (1994) further warn that at a sustained low temperature encountered on a flight, the drop in RH within a sealed package can cause moisture to migrate from a minor hygroscopic component in an artwork (i.e., gouache) to a major hygroscopic component (i.e., wood), resulting in desiccation of the minor component (irreversible in their example). These warnings emphasize the importance of providing thermal insulation to some packing cases.
REFERENCES
Bosshard, E.1990. Klimatvitrinen f�r Gem�lde. Restauro3: 176–80.
Hackney, S.1990. Framing for conservation at the Tate Gallery. Conservator14: 44–52.
Michalski, S.1991. Paintings: Their response to temperature, relative humidity, shock, and vibration. In Art in transit: Studies in the transport of paintings, ed.M. F.Mecklenburg..Washington D.C.: National Gallery of Art. 223–48.
Padfield, T.1966. The control of relative humidity and air pollution in show-cases and picture frames. Studies in Conservation11: 8–30.
Ramer, B.1984. The design and construction of two humidity-controlled display cases. ICOM Committee for Conservation preprints, 7th Triennial Meeting, Copenhagen. 4.17.46–47.
Richard, M. 1991. Control of temperature and relative humidity in packing cases. In Art in transit: Studies in the transport of paintings, ed.M.F.Mecklenburg. Washington D.C.: National Gallery of Art. 279–97.
Richard, M.1994. The transport of paintings in microclimate display cases. IIC Preprints, 15th International Congress, Ottawa.185–89.
Richard, M.1996. Personal communication. National Gallery of Art, Washington, D.C. 20565.
Sack, S. P., and N.Stolow. 1978. A micro-climate for a Fayum painting. Studies in Conservation23:47–56.
Saunders, D., C. L.Sitwell, and S.Staniforth.1991. Soft Pack–Soft Option? In Art in transit: Studies in the transport of paintings, ed.M. F.Mecklenburg. Washington D.C.: National Gallery of Art. 311–21.
Simpson, W. S.1892. An improved method or means of preserving oil paintings, water colour drawings, engravings, photographs, prints and printed matter from atmospherical deterioration and from decay. British Patent, # 6556.
Skalka, M.1991. Selected bibliography. In Art in transit: Studies in the transport of paintings, ed.M.F.Mecklenburg. Washington D.C.: National Gallery of Art. 259–72.
Sozzani, L.1992. Climate vitrine for paintings using the picture's frame as the primary housing. Unpublished paper, Rijksmuseum, Amsterdam, presented to the Netherlands Ministry of Welfare, Health and Culture, April.
Stolow, N.1967. The nonairtight case: Standards for the care of works of art in transit. Paper presented at International Institute for Conservation Conference on Museum Climatology, London.
Thompson, G.1964. Relative humidity: Variation with temperature in a case containing wood. Studies in Conservation9:153–68.
Toishi, K J., and T.Gotoh1994. A note on the movement of moisture between components in a sealed package. Studies in Conservation39:265–71.
Wadum, J.1992. De betere klimaatdoos (The better climate box). Het Mauritshuis Nieuwsbrief2:8–9.
Wadum, J.. Forthcoming. Microclimate boxes for panel paintings. Proceedings of the Symposium on the Structural Conservation of Panel Paintings, April 24–28, 1995. Los Angeles: Getty Conservation Institute.
Wadum, J., I.J.Hummelen, W.Kragt, B.A.H.G.J�tte, and L.Sozzani1994. Research program microclimates: Paintings on panel and canvas. Poster and IIC Preprints, 15th International Congress, Ottawa.
AUTHOR INFORMATION
LAURENT S. G. SOZZANI graduated from the Winterthur Museum/University of Delaware Program in Art Conservation in 1984. From 1984 to 1986 he worked with Perry Huston and Associates in Fort Worth, Texas, and from 1986 to 1989 he was a Fellow in the Paintings Restoration Department of the Metropolitan Museum of Art. He has been a paintings restorer at the Rijksmuseum since 1990. Address: Rijksmuseum, Postbus 74888, 1070 DN Amsterdam, The Netherlands.
Section Index |