CONSERVATION OF THE DARNAULT MIRROR: AN ACRYLIC EMULSION COMPENSATION SYSTEM
CYNTHIA MOYER, & GORDON HANLON
4 SECOND TREATMENT PHASE
When the treatment project resumed in January 1994, we were dealing with a partially cleaned, partially filled (in terms of gesso losses) series of carved molding sections. Degraded glue size, which had initially presented such cleaning difficulties, remained on the surface and discolored the gilding and the areas where there was no leaf. A fair amount of thick glue size, which had presumably pooled when used as a matting toner, was still on the surface of the moldings, proving to be too intractable. This dark coating was resistant to the emulsion systems recommended by Professor Wolbers.6 With further testing we found this glue size coating was not remotely susceptible to acetone gel but overly reactive to ethanol gel, which also softened the water gilding. Upon closer examination of the surfaces, it was determined that trying to continue the cleaning would reveal more original gilding. This determination would also help dictate a compensation approach that would satisfy the compromise we sought between the two test samples of gilding restoration campaigns on the central shell (M) and the two top moldings (T and CR). More of the bright original gilding would be revealed, and ingilding rather than overgilding would be warranted.
Before continued cleaning, we recorded the status of the 13 carved elements as to whether they had been: (1) simply cleaned with methylene chloride paint remover, which had been used to remove overpaint; (2) both (1) and consolidated with rabbit skin glue; (3) both (1) and had a barrier coat of Arkon P-90 applied; (4) all of the above and overgilded with a traditional water-gilding system including ochre and red bole; or (5) none of the above.
While the uppermost frame, which includes molding elements T (top), LT (left top), RT (right top), ML (mid-left), MR (mid-right), CL (center left), CR (center right), SR (side right), and M (middle central shell), retained almost 40% of its original gilding, it had been coated with rabbit skin glue and Arkon P-90. On the other hand, we found that elements L (left), R (right), B (base), and SL (side left), which constitute mostly the lower frame, had only been partially cleaned and not coated with either rabbit skin glue or Arkon P-90. These elements responded very well to cleaning with a xylene, water, and Triton X-100 emulsion system cleared with xylene. Though their gesso surfaces and gilding were the most severely degraded (L and R retaining only approximately 20% of their original water gilding, B and SL retaining 30%), the remaining surface, with its gilding and thin glue size coating intact, provided a standard to which we attempted to clean and compensate the other nine elements. We were able to easily reverse the overgilding on elements T and CL with cotton swabs soaked in warm water. The Arkon P-90 could easily be reversed with mineral spirits. What provided the greatest challenge was reversal of the two coats of rabbit skin glue consolidant and barrier coat, which did not penetrate the degraded gesso on some of the molding elements, particularly SL and SR, but sat on the surface, obliterating the delicate channels of recutting and forming a stubborn bond with the underlying original water gilding. Because in several instances the glue consolidant had cooled and gelled when it came into contact with the surface, it did not penetrate into the friable, powdery gesso as was the intention in the original treatment. Instead, it lay on the surface, locking in the degraded glue size coating and its incumbent grime and giving the gilt surface a gray cast. We could remove this glue only by soaking it to its gelled state and peeling it off mechanically. Though carried out on three moldings, ultimately this process proved too time-consuming, so we elected to bring the cleaning part of the treatment to a close and work on compensation methods for the gilding that remained.
Based on the extent of the pretreatment, by January 1994 we had to develop an expedient compensation system. This system would need to satisfy the minimum requirements of a simple gouache inpainting method to unify the surface as a whole but also serve as a mordant should the application of leaf be required. It would need to be reversible and distinguishable from the original gilding and be able to adhere to a barrier coat. We felt an inpainting mordant, a colored size, would be ideal, and we initially discussed a pigmented or dyed oil-type size. The issue of a matte appearance to the surface was of particular importance and was a major consideration in our decision-making process. We found that the Arkon P-90 barrier coat had been too glossy in appearance when used to isolate the matte water-gilded passages. Initially, Thornton's (1991) alternative gilding methods were helpful. We then considered an acrylic emulsion medium as a possibility and tested a number of products. We narrowed our testing down to the Instacoll system, the Rhoplex products, and the Liquitex products. The Liquitexes had the most desirable properties, particularly because they offered a premixed matte medium. This product alone, applied to a barrier coat of Soluvar matte medium diluted 1:1 with mineral spirits, gave us the nonglossy surface that all the other synthetic resins did not.
The acrylic resins are available through several manufacturers in a range of properties, including those that dry quickly and hard and those that dry more slowly and with a softer film. Products of the same manufacturer can be mixed together and adapted to achieve the desired effect and degree of tackiness. When the emulsion is rewetted by breathing on it or applying water, it becomes tacky for a short period of time; leaf or dry powders, either mica or gold, can then be applied to selected rewetted areas.
We conducted a number of tests with acrylic emulsion media and paints and finally settled on using Liquitex matte medium mixed with appropriate hues of ochre watercolor paint to simulate the losses in the matte water-gilded areas. This inpainting mordant could be made suitably transparent or opaque and served to join the islands of original gilding still exposed on the moldings. In turn, areas of loss to the burnished areas were inpainted with Liquitex gloss medium tinted to a reddish brown with watercolor pigment.
The inpainting alone integrated the surface as a whole, yet it remained nonreflective. After allowing the inpainting to dry overnight, any impasto brush strokes in the dark red areas were flattened by burnishing—gently rubbing the areas with an agate burnisher, very slightly oiled. These areas had French-manufactured, Versailles colored gold leaf applied to them, adhered by rewetting them with water and cutting and laying the leaf to fit just over the burnish losses, much like traditional water-gilding techniques. The edges were then feathered with an oil-free steel wool swab, and afterward the adhered leaf was burnished to impart a smooth surface. The proud edges and tips were distressed mechanically with a scalpel or a steel wool swab to reveal bole and gesso underneath.
The matte areas were treated differently. Gold leaf was felt to be too reflective for these matte passages, so instead gold-colored mica pigments were applied by selectively rewetting the acrylic inpainting and stippling mixtures of dry mica powders to areas of loss. Paler powders were used for areas of transition on the deep, redbrown emulsion inpainting mordant. Deeper colored mica powders were used for ochre areas to simulate the toned, matte water gilding. Too uniform an application of the powders had to be avoided, and, due to the powders' transparency, the ground color had to be carefully matched. No toner was applied over the gold or the powders except in the case of the upper frame, whose broad band of burnished molding had a layer of Liquitex gloss medium, tinted with watercolor, applied to areas of burnished gold leaf ingilding. With this system, the surface was unified for display (figs. 4, 5).
Fig. 4.
Darnault mirror, detail at upper left of frame where segments T and LT intersect. After treatment
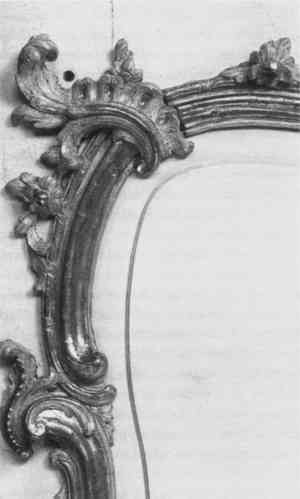 |
Fig. 5.
Darnault mirror, detail showing central shell in segment T. After treatment
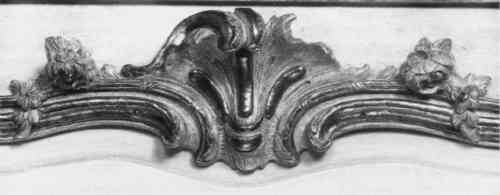 |
Carving losses were replaced with basswood, adhered with hot hide glue, coated with traditional gesso, recut, and ingilded with the acrylic emulsion system. Gesso losses remaining on exposed wood were filled traditionally over the barrier coat of Soluvar matte medium, with particular focus given to losses on the lower portion of the frame. We found that toning fresh gesso with watercolor prior to ingilding provided a ground color better resembling the off-white period gesso surface color.
The backboard surface was analyzed in cross section, revealing it had originally been painted white. We decided to simply clean the existing white paint coating, though it was not the original layer.7 Thick, fractured, unstable paint was consolidated with rabbit skin glue, and then a gelatine barrier coat was applied to areas of loss. Polyfilla pigmented with acrylic paint to match the underlying blue and green layers was used to bring the surface flush with the top paint film. The fills were smoothed, and Liquitex matte acrylic medium was mixed with white acrylic paint to simulate the transparency and the impasto of the white surface coating. When dry, the white was toned with a watercolor wash and sealed with Liquitex gloss acrylic medium to tie it visually to adjacent areas and to protect it when handled.
The paint surface of the wood upper panel insert, a 20th-century addition, was isolated with gelatine and overpainted with an off-white colored acrylic layer; a final watercolor wash was applied to simulate the earlier period white backboard paint color. Finally reassembled, the central portion of the Darnault mirror is currently installed in gallery 213 of the Getty Museum.
|