CONSERVATION OF THE DARNAULT MIRROR: AN ACRYLIC EMULSION COMPENSATION SYSTEM
CYNTHIA MOYER, & GORDON HANLON
ABSTRACT—A 1751 French boiserie mirror, which retained approximately 30% of its original gilding, was treated at the J. Paul Getty Museum. In the initial phase of the treatment, the mirror frame was thoroughly analyzed, its condition was documented, and testing of possible cleaning and compensation methods was begun. Ultimately, the conservators were not pleased with the results of that work, which was presented in a paper at the AIC Annual Meeting in 1994. Re-evaluation of the treatment led to the use of new materials for a barrier coat and for compensation of the losses in the gilding, including acrylic emulsion medium, mica pigments, and gold leaf. In creating the alternative system, the conservators and curators aimed to maintain the original goals of the project, including the proper interpretation and display of the mirror in the galleries as well as preservation of the physical integrity of the object. Methods for using nontraditional materials in a manner complementary to the original materials were devised with the hope that they could be applied to other objects needing the same treatment. This paper gives a brief overview of the previous work and presents the revised compensation treatment to the Darnault mirror frame.
TITRE—Restauration du miroir Darnault: Un syst�me de compensation avec �mulsion acrylique. R�SUM�—Un miroir en boiserie fran�aise de 1751, qui avait gard� environ 30% de sa dorure originale fut trait� au J. Paul Getty Museum. Lors de la phase initiale du traitement, le cadre du miroir fut compl�tement analys�, son �tat �tudi� et des tests sur de possibles m�thodes de nettoyage et de restauration entrepris. Finalement, les restaurateurs n'�taient pas satisfaits des r�sultats du travail qui furent pr�sent�s lors d'une communication � la r�union annuelle de l'AIC en 1994. Suite � une r��valuation du traitement, de nouveaux mat�riaux—comme par exemple un milieu d'�mulsion acrylique, des pigments de mica et la feuille d'or—furent utilis�s pour la couche protectrice et pour compenser les pertes de la dorure. En cr�ant le syst�me alternatif, les conservateurs et les restaurateurs voulaient garder les objectifs originaux du projet: l'interpr�tation correcte du miroir et son exposition dans le mus�e ainsi que la pr�servation de l'int�grit� de l'objet lui-m�me. Les restaurateurs mirent au point des m�thodes d'utilisation de mat�riaux non-traditionnels de mani�re � ce qu'ils compl�tent les mat�riaux originaux en esp�rant que ces nouvelles m�thodes puissent �tre appliqu�es � d'autres objets ayant besoin du m�me traitement. Cette communication r�sume le travail d�j� effectu� et pr�sente le nouveau traitement de restauration du cadre du miroir Darnault.
T�TULO—Conservaci�n del espejo Darnault: un sistema de compensaci�n con emulsi�n acr�lica. RESUMEN—Un espejo franc�s “boiserie” del a�o 1751, que conservaba aproximadamente un 30% de su dorado original, fue tratado en el Museo J. Paul Getty. En la fase inicial del tratamiento, el marco del espejo fue minuciosamente analizado, su condici�n fue documentada, y se iniciaron pruebas de posibles m�todos de limpieza y compensaci�n. En ultima instancia, los conservadores no quedaron satisfechos con los resultados de aquel trabajo, el cual fue presentado en una ponencia en la Reuni�n Anual del AIC en 1994. La reevaluaci�n del tratamiento condujo al uso de nuevos materiales para un recubrimiento protector y para la compensaci�n de las perdidas en el dorado, incluyendo un medio de emulsi�n acr�lica, pigmentos de mica y hojilla de oro. En la creaci�n de un sistema alternativo, los conservadores y curadores trataron de mantener los objetivos originales del proyecto, incluyendo la interpretaci�n y exhibici�n correctas del espejo en las galer�as, como as� tambi�n la necesidad de preservar la integridad f�sica del objeto en si mismo. Se concibieron m�todos para el uso de materiales no tradicionales en forma complementaria a los materiales tradicionales, con la esperanza de que estos pudieran ser aplicados a otros objetos que necesitaran el mismo tratamiento. Este trabajo da un breve panorama general del trabajo hecho previamente y presenta la revisi�n del tratamiento de compensaci�n al marco del espejo de Darnault.
1 INTRODUCTION
This paper is the result of an evolving treatment initiated by Nancie Ravenel and Gordon Hanlon at the J. Paul Getty Museum in 1992. The first part of their work focused on the technical and aesthetic considerations taken into account in determining a course of treatment, particularly cleaning systems and loss compensation systems, for a badly degraded, water-gilded, 1751 French rococo period mirror frame in the collection of the J. Paul Getty Museum (U.86.4). The mirror originally had been part of a boiserie, or paneled room (Ravenel 1994). This paper draws on that initial materials analysis, solubility and permeation testing, and compensation method sampling and elaborates on a re-evaluation of the results. The initial work provided a foundation for further cleaning tests and ultimately for a decision as to how to ingild and compensate the surface losses. This paper brings to light those conclusions.
As we set out on the second treatment phase, we grappled with the two initial main goals. The first goal, which is applicable to all conservation treatments, was to preserve the material integrity of the object, especially, in this case, what was left of the 20–40% of the delicately recut gesso and the water-gilding layer. By opening the search to materials not considered in the first phase, we were able to devise an alternative cleaning system and a surface loss compensation system that achieved the appropriate aesthetic, accomplished with what we have come to describe as an acrylic emulsion inpainting mordant system. The second goal was to satisfy the curatorial requirement that the mirror be integrated into the gallery display with other gilded objects that were in far better preserved and restored condition. An important requirement of the appearance of the mirror frame was to have it harmonize with the other gilt wood objects to be displayed in the rococo gallery installation at the new Getty Center in West Los Angeles, scheduled to open to the public in 1997. These objects include the Contant d'Ivry–designed, gilt wood, rococo period console table, ca. 1750, which will be displayed below the Darnault mirror panel ensemble, and the rococo period Tilliard bed, ca. 1750, which is water-gilded in both lemon and deep-colored leaf. The console table and the bed have dissimilar but nevertheless restored surfaces. Although the console table was restored in England, the bed was treated in Paris. There remains a strong emphasis within the European gilding community to restore degraded gilded surfaces with traditional materials, sometimes completely regessoing, recutting, and releafing the surface. Gilt wood pieces of French origin in the Getty collection have been treated in Parisian ateliers for restoration or regilding in the past. The craft tradition there remains strong, with many talented gilders in residence and with training and apprenticeships in traditional gilding techniques still available as they have been for centuries.
In this paper, we will first describe some of the provenance history concerning the mirror frame's attribution and provide a physical description of the mirror. The next section is a review of the first phase of the treatment, followed by an overview of the specifics of the second phase, which includes a description of the condition of the mirror between the two phases and the continued cleaning and compensation with the materials we tested and ultimately used. The paper ends with conclusions describing the attributes and potential drawbacks, as we see them, of this system.
2 ART HISTORICAL AND PHYSICAL DESCRIPTIONS
The mirror, as purchased, consists of three panel elements of a rococo period boiserie, two of which bear paper labels of the marchand–mercier Fran�ois Charles Darnault, whose shop was on the Rue Grenier St. Lazare in Paris in 1751. From the information on Darnault's label we know that he dealt in a variety of “fancy goods,” much like his father who operated a separate shop on the Rue de la Monnoie: carved, gilt wood, and ormolu objects including mirrors of all varieties; decorative items such as lusters and wall lights; and all types of furniture, such as console tables with marble tops, secretaries, gaming tables, writing desks, and screens, some with chinoiserie-type decorated surfaces, others with chased, gilded hardware; and even overdoor paintings. Research continues to be carried out at the Archives Nationales in Paris on the Darnault family and their dealings.1 Perhaps one day we will know in what building these boiserie elements would have been installed, but at this time we do not.
The boiserie mirror we treated, which is long and narrow (11 ft. tall and only 4 ft., 6� in. wide), is thought to have been originally designed for placement over a soubasement panel (rather than a mantel) within the context of an entire paneled room.2 The Darnault mirror's two narrow, flanking panels, referred to as parcloses, measure 12 in. wide and extend the full height of the central panel; they have not yet been treated at the time of this writing. The central panel, which is the focus of this paper, is composed of 13 separate water-gilded moldings, carved in basswood (or limewood), forming two continuous frames, one above the other. The moldings are fastened with brass screws and applied to a white-painted oak, panel, and frame backboard. One of the paper labels is located in a central floating panel on the backboard facing into the room under the glass plates. The flanking panels are also water-gilded, carved basswood moldings, though more delicate and glued to white-painted oak. The other paper label is on the reverse of one of these narrow panels. The central panel's uppermost frame would have originally surrounded a canvas painting, no longer part of the ensemble. It now surrounds a painted board. The lower frame surrounds the mirror plates (fig. 1). The carving above is characterized by a broad, burnished, scrolled band with a central shell at the crest and stylized rocaille at the corners and sides. Flowers, in the forms of marguerites and roses, punctuate the perimeter. Palmate carved moldings support this upper frame and the center shell from below, and floral garlands spiral down the sides to rest on symmetrical volutes, which flank a delicate, R�gence-style molding at the base, entwined in ribbon and ornamented with gadrooning and an inverted central shell. The 13 carved elements that constitute this double frame were originally water-gilded with an ochre size on the matte areas and a red-brown bole on the burnished areas.3 The palm frond motif used on the sides and lower crest moldings is of a design entirely different than that of the base molding. The top frame with its scrolling bands is different yet again. These three disparate carving themes represent a stylistic transition from the R�gence period in 1725 through the rococo. Different volumes of matte and burnished surface areas and dark- and light-colored areas between them draw the eye to the area of the frame above, no doubt to emphasize the painting that had originally been displayed in the upper frame.
Fig. 1.
Darnault mirror, central panel, French, 1751, gilded wood, 132 � 54 in. J. Paul Getty Museum U.86.4. After treatment
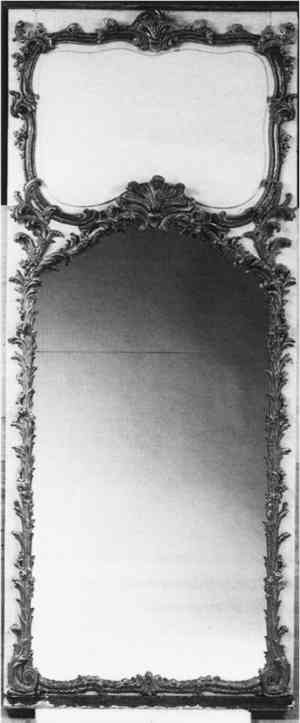 |
3 FIRST TREATMENT PHASE
Samples were taken from areas of carved wood, gilding, and paint. Sample tangential and radial wood fragments were analyzed microscopically resulting in the identification of the species Tilia spp., or basswood. Fluorescent microscopy was used to help determine the nature of the gesso and grounds: either glue wash or bole, gold leaf, and paint on the moldings and backboard. Fluorescent microscopy also helped to identify the nature of the residual overpaint on the gilt wood moldings from the backboard's repeated overpainting while the moldings remained in place as well as to determine the stratigraphy of the color campaigns on the oak backboard itself, numbering 10 in all. The analysis of the degraded gesso, the gilding, and the coatings with fluorescent microscopy included staining the samples with fluorochrome dyes in consultation with Richard Wolbers, associate professor, University of Delaware, during his stay as a guest conservator in 1992.4
The initial structural condition of the moldings and the gilding on both the main panel and the two parcloses was thoroughly documented with photography (figs. 2, 3) and diagrammatic descriptions in the form of Mylar overlays and hand-colored xeroxes. This documentation showed areas of repair and loss to the wood carvings as well as the patterns of the burnished and matte passages on the gilded surfaces.
Fig. 2.
Darnault mirror, detail from upper left corner of frame where segments T (top) and (left top) intersect. Before treatment
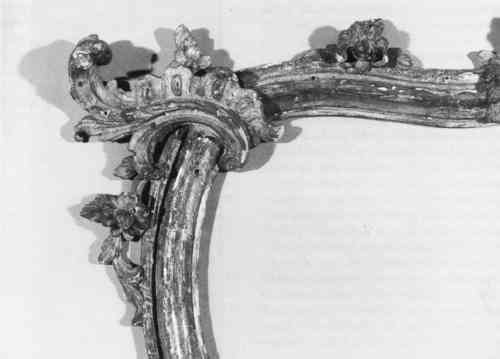 |
Fig. 3.
Darnault mirror, detail showing central shell in segment T. Before treatment
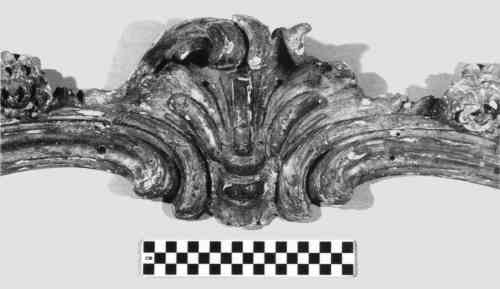 |
To determine the selection of a barrier coat, a test sample was fabricated to simulate aged gesso. The degree to which various percentage viscosities of a dyed synthetic resin, in this case Arkon P-90, would penetrate the surface of this simulated aged gesso layer coated with rabbit skin glue was tested.5 Three sample molding elements from the object were then treated for comparison in the following manner.
After initial cleaning of the overpaint and some of the degraded glue size embedded with surface dirt using methylene chloride paint remover, the middle central shell (M), which had minor losses to the gesso and gilt surface, was simply coated with Arkon on any exposed wood. Losses were then filled with a traditional gesso putty. A water-gilding system including traditional bole was used to compensate the burnished areas. Ochre-colored gouache inpainting was used for the matte water-gilded passages to tone out exposed gesso areas, leaving fragmented original gilding exposed. Two other carved sections from the upper frame, the top section (T) and the center right section (CR), which had 60% loss to the gilded surface, were treated differently. After cleaning, they were first completely coated with a 10% rabbit skin glue consolidant, then a 45% Arkon P-90 barrier coat. Finally, after filling only the gesso losses in badly damaged areas, they were completely coated with yellow ochre bole, selectively coated with deep red bole, overgilded, and selectively burnished. These two ranges of compensation carried out on elements M, T, and CR were examined carefully, but their appearance compared to the original gilding proved to be unsatisfactory.
The conservators felt that the initial approach to the final aesthetic of the Darnault mirror, as attempted by the compensation on element M, would have resulted in too many nonreflective matte areas due to the great number of surface losses compensated in gouache. On the other hand, when scrutinizing the surface compensation samples of molding elements T and CR, which were completely overgilded, the conservators found that the barrier coat of Arkon P-90, with its underlying double layer of rabbit skin glue consolidant, proved to be too inflexible to yield the appearance of a burnished gilt surface adjacent to a matte surface. In addition, the multiple coating layers on top of the original surface clogged the recutting in the gesso, obliterating its delicate sculptural quality. This result confirmed one of the original fears about this type of compensation, which includes many additional layers. In comparing the two systems, the conservators sought a compromise between the two sample compensation methods but had not yet come up with a solution by fall 1993.
4 SECOND TREATMENT PHASE
When the treatment project resumed in January 1994, we were dealing with a partially cleaned, partially filled (in terms of gesso losses) series of carved molding sections. Degraded glue size, which had initially presented such cleaning difficulties, remained on the surface and discolored the gilding and the areas where there was no leaf. A fair amount of thick glue size, which had presumably pooled when used as a matting toner, was still on the surface of the moldings, proving to be too intractable. This dark coating was resistant to the emulsion systems recommended by Professor Wolbers.6 With further testing we found this glue size coating was not remotely susceptible to acetone gel but overly reactive to ethanol gel, which also softened the water gilding. Upon closer examination of the surfaces, it was determined that trying to continue the cleaning would reveal more original gilding. This determination would also help dictate a compensation approach that would satisfy the compromise we sought between the two test samples of gilding restoration campaigns on the central shell (M) and the two top moldings (T and CR). More of the bright original gilding would be revealed, and ingilding rather than overgilding would be warranted.
Before continued cleaning, we recorded the status of the 13 carved elements as to whether they had been: (1) simply cleaned with methylene chloride paint remover, which had been used to remove overpaint; (2) both (1) and consolidated with rabbit skin glue; (3) both (1) and had a barrier coat of Arkon P-90 applied; (4) all of the above and overgilded with a traditional water-gilding system including ochre and red bole; or (5) none of the above.
While the uppermost frame, which includes molding elements T (top), LT (left top), RT (right top), ML (mid-left), MR (mid-right), CL (center left), CR (center right), SR (side right), and M (middle central shell), retained almost 40% of its original gilding, it had been coated with rabbit skin glue and Arkon P-90. On the other hand, we found that elements L (left), R (right), B (base), and SL (side left), which constitute mostly the lower frame, had only been partially cleaned and not coated with either rabbit skin glue or Arkon P-90. These elements responded very well to cleaning with a xylene, water, and Triton X-100 emulsion system cleared with xylene. Though their gesso surfaces and gilding were the most severely degraded (L and R retaining only approximately 20% of their original water gilding, B and SL retaining 30%), the remaining surface, with its gilding and thin glue size coating intact, provided a standard to which we attempted to clean and compensate the other nine elements. We were able to easily reverse the overgilding on elements T and CL with cotton swabs soaked in warm water. The Arkon P-90 could easily be reversed with mineral spirits. What provided the greatest challenge was reversal of the two coats of rabbit skin glue consolidant and barrier coat, which did not penetrate the degraded gesso on some of the molding elements, particularly SL and SR, but sat on the surface, obliterating the delicate channels of recutting and forming a stubborn bond with the underlying original water gilding. Because in several instances the glue consolidant had cooled and gelled when it came into contact with the surface, it did not penetrate into the friable, powdery gesso as was the intention in the original treatment. Instead, it lay on the surface, locking in the degraded glue size coating and its incumbent grime and giving the gilt surface a gray cast. We could remove this glue only by soaking it to its gelled state and peeling it off mechanically. Though carried out on three moldings, ultimately this process proved too time-consuming, so we elected to bring the cleaning part of the treatment to a close and work on compensation methods for the gilding that remained.
Based on the extent of the pretreatment, by January 1994 we had to develop an expedient compensation system. This system would need to satisfy the minimum requirements of a simple gouache inpainting method to unify the surface as a whole but also serve as a mordant should the application of leaf be required. It would need to be reversible and distinguishable from the original gilding and be able to adhere to a barrier coat. We felt an inpainting mordant, a colored size, would be ideal, and we initially discussed a pigmented or dyed oil-type size. The issue of a matte appearance to the surface was of particular importance and was a major consideration in our decision-making process. We found that the Arkon P-90 barrier coat had been too glossy in appearance when used to isolate the matte water-gilded passages. Initially, Thornton's (1991) alternative gilding methods were helpful. We then considered an acrylic emulsion medium as a possibility and tested a number of products. We narrowed our testing down to the Instacoll system, the Rhoplex products, and the Liquitex products. The Liquitexes had the most desirable properties, particularly because they offered a premixed matte medium. This product alone, applied to a barrier coat of Soluvar matte medium diluted 1:1 with mineral spirits, gave us the nonglossy surface that all the other synthetic resins did not.
The acrylic resins are available through several manufacturers in a range of properties, including those that dry quickly and hard and those that dry more slowly and with a softer film. Products of the same manufacturer can be mixed together and adapted to achieve the desired effect and degree of tackiness. When the emulsion is rewetted by breathing on it or applying water, it becomes tacky for a short period of time; leaf or dry powders, either mica or gold, can then be applied to selected rewetted areas.
We conducted a number of tests with acrylic emulsion media and paints and finally settled on using Liquitex matte medium mixed with appropriate hues of ochre watercolor paint to simulate the losses in the matte water-gilded areas. This inpainting mordant could be made suitably transparent or opaque and served to join the islands of original gilding still exposed on the moldings. In turn, areas of loss to the burnished areas were inpainted with Liquitex gloss medium tinted to a reddish brown with watercolor pigment.
The inpainting alone integrated the surface as a whole, yet it remained nonreflective. After allowing the inpainting to dry overnight, any impasto brush strokes in the dark red areas were flattened by burnishing—gently rubbing the areas with an agate burnisher, very slightly oiled. These areas had French-manufactured, Versailles colored gold leaf applied to them, adhered by rewetting them with water and cutting and laying the leaf to fit just over the burnish losses, much like traditional water-gilding techniques. The edges were then feathered with an oil-free steel wool swab, and afterward the adhered leaf was burnished to impart a smooth surface. The proud edges and tips were distressed mechanically with a scalpel or a steel wool swab to reveal bole and gesso underneath.
The matte areas were treated differently. Gold leaf was felt to be too reflective for these matte passages, so instead gold-colored mica pigments were applied by selectively rewetting the acrylic inpainting and stippling mixtures of dry mica powders to areas of loss. Paler powders were used for areas of transition on the deep, redbrown emulsion inpainting mordant. Deeper colored mica powders were used for ochre areas to simulate the toned, matte water gilding. Too uniform an application of the powders had to be avoided, and, due to the powders' transparency, the ground color had to be carefully matched. No toner was applied over the gold or the powders except in the case of the upper frame, whose broad band of burnished molding had a layer of Liquitex gloss medium, tinted with watercolor, applied to areas of burnished gold leaf ingilding. With this system, the surface was unified for display (figs. 4, 5).
Fig. 4.
Darnault mirror, detail at upper left of frame where segments T and LT intersect. After treatment
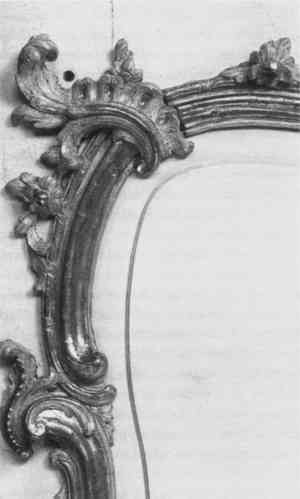 |
Fig. 5.
Darnault mirror, detail showing central shell in segment T. After treatment
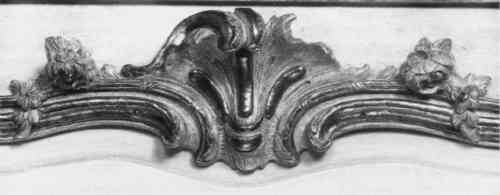 |
Carving losses were replaced with basswood, adhered with hot hide glue, coated with traditional gesso, recut, and ingilded with the acrylic emulsion system. Gesso losses remaining on exposed wood were filled traditionally over the barrier coat of Soluvar matte medium, with particular focus given to losses on the lower portion of the frame. We found that toning fresh gesso with watercolor prior to ingilding provided a ground color better resembling the off-white period gesso surface color.
The backboard surface was analyzed in cross section, revealing it had originally been painted white. We decided to simply clean the existing white paint coating, though it was not the original layer.7 Thick, fractured, unstable paint was consolidated with rabbit skin glue, and then a gelatine barrier coat was applied to areas of loss. Polyfilla pigmented with acrylic paint to match the underlying blue and green layers was used to bring the surface flush with the top paint film. The fills were smoothed, and Liquitex matte acrylic medium was mixed with white acrylic paint to simulate the transparency and the impasto of the white surface coating. When dry, the white was toned with a watercolor wash and sealed with Liquitex gloss acrylic medium to tie it visually to adjacent areas and to protect it when handled.
The paint surface of the wood upper panel insert, a 20th-century addition, was isolated with gelatine and overpainted with an off-white colored acrylic layer; a final watercolor wash was applied to simulate the earlier period white backboard paint color. Finally reassembled, the central portion of the Darnault mirror is currently installed in gallery 213 of the Getty Museum.
5 CONCLUSIONS
We feel that this system of compensation fulfills many of the requirements we initially sought. It is not only chemically distinguishable from the original water gilding but also physically distinguishable upon very close inspection. It is reversible should reinterpretation of the object be necessary in the future. It is a compensation method to which one can add varying degrees of gold leaf and/or mica or gold powders, depending on the requirements. A perfectly smooth gesso surface is not imperative for this system, as the inpainting and leaf application are selective. This procedure reduces preparation time and the introduction of additional gesso on original gesso surfaces. This system does not require a toner over the powders, just over the leaf. After the barrier coat application, only one layer in two colors is applied to areas of loss prior to the application of leaf or powders, establishing a very thin surface layer addition. As a result, original recutting details in the gesso are not lost.
Some difficulties and criticisms of the acrylic emulsion inpainting mordant arose in practice and may present themselves in the future. Color matching was a challenge because the acrylics dry darker than they do when mixed wet. They tend to be rubbery to work with, not flowing enough to provide the impeccably smooth surface sought in gilding grounds. Some of the mica pigments are more metallic, more “glittery” looking, and only the very finely ground powders are suitable in this application. The Li-quitex forms a poor bond with the Soluvar matte medium, a desirable quality in terms of reversibility but, in application, it may bead on the surface of this barrier coat when thinned with too much water. The question of the cross-linking potential of an acrylic in the future and its continued reversibility in the long run should be kept in mind (Horie 1987). Presently, the system can almost be peeled off the Soluvar, but otherwise, the acrylics are soluble in acetone, xylene, or toluene, and the Soluvar in mineral spirits. We question also whether the Triton X-100 component of the xylene, water, and Triton X-100 emulsion cleaning system is fully cleared from the porous gesso and to what degree the Soluvar matte is intractable from these areas. However, in spite of these concerns, the system fulfills our material and aesthetic requirements for displaying the mirror frame, both in context in the gallery and in its own right, on its own. Like any conservation treatment, it is a choice, based on many factors. We feel we have, however, indeed struck a balance.
ACKNOWLEDGEMENTS
We would very much like to thank John Childs, Brian Considine, Kathy Gillis, Joe Godla, Montserrat LeMense, Mark Leonard, Nancie Ravenel, and Gillian Wilson, all at the J. Paul Getty Museum at the time of this treatment, as well as Jonathan Thornton and Richard Wolbers for their contributions to this project.
NOTES
1. Further research on the Darnault family is found in Sargentson (1996).
2. For illustration, see figure 174 in Kimball ([1943] 1980), showing an elevation from the chambre de la Reine at Versailles dated 1730, with a mirror above soubasement paneling and a console table in front, much the way the Getty Darnault mirror would have been displayed. Another illustration, figure 232, also from Kimball shows another elevation from Versailles from the chambre de Louis XV. In addition, illustrations from Blondel ([1737] 1967) show a design for a mirror with a painting above, which is flanked by two narrow parcloses (73, pl. 67) and a mirror with a similar palm frond motif as the Getty Darnault mirror (72, pl. 64).
3. The palm frond mirror currently in the salon ovale du prince de Soubise from the Hotel Soubise in Paris, which is now used by the Archives Nationales, has recently been restored and looks as the Darnault mirror must have originally looked.
4. Test results showed the ground to include whiting and both protein and traces of oil. The overpaint on the carved moldings was found to be protein based. Recommendations for cleaning included trying an acetone gel and a xylene gel (Wolbers 1992).
5. The mock-up was made of a gesso consisting of overcooked glue soaked in water and heated in a microwave oven, which theoretically simulated the permeability of aged gesso. Arkon P-90 in 15%, 45%, and 90% strengths pigmented with yellow ochre was applied to this gesso to determine depth of penetration of the coating. The rabbit skin glue added as a consolidant prior to the Arkon prevented this low molecular weight resin from penetrating too much. A 45% solution of Arkon P-90 was chosen for its viscosity and low penetrability.
6. Equal parts of mineral spirits and water are shaken together with a few drops of Triton X-100, and the top half is decanted and used to clean the water gilding. It is mostly mineral spirits with very little water (Wolbers 1994).
7. Between the topmost white layer and the original were more than eight layers of paint campaigns, including light blues and greens, some bound in oil and/or protein with one layer being water-soluble.
REFERENCES
Blondel, J. F. [1737] 1967. De la distribution des maisons de plaisance, et de la decoration des edifices en general, vol. 1. London: Gregg Press.
Horie, C. V.1987. Materials for conservation: Organic consolidants, adhesives and coatings. London: Butterworths.
Kimball, F. [1943] 1980. The creation of the rococo decorative style. New York: Dover.
Ravenel, N.1994. Conservation of the Darnault mirror: Striking a balance. Loss compensation: Technical and philosophical issues, Objects Specialty Subgroup Postprints. American Institute for Conservation 22d Annual Meeting, Nashville. Washington, D.C.: AIC. 115–21.
Sargentson, C.1996. Merchants and luxury markets: The marchand merciers of Eighteenth-century Paris. London: Victoria and Albert Museum in association with the J. Paul Getty Museum.
Thornton, J.1991. The use of nontraditional gilding methods and materials in conservation. In Gilded wood: Conservation and history, ed.D.Bigelow et al. Madison, Conn.: Sound View Press. 217–28.
Wolbers, R.1992. Notes on fluorescent microscopy analysis. J. Paul Getty Museum. August 21.
Wolbers, R.1994. Personal communication. Associate Professor, University of Delaware, 303 Old College, Newark, Del. 19716.
FURTHER READING
Cession, C.1988. Les polychromies baroques et rococos du XVIIIe Siecle. Travail de fin d'etude, La Cambre, Brussels.
Derrick, M., L.Souza, T.Kieslich, H.Florsheim, and D.Stulik. 1994. Embedding paint cross section samples in polyester resins: Problems and solutions. Journal of the American Institute for Conservation33: 227–45.
Gettens, R. J., and G.L.Stout. 1996. Painting materials. New York: Dover.
Moyer, C.1991. Conservation treatments for border and freehand gilding and bronze-powder stencilling and freehand bronze. In Gilded wood: Conservation and history, ed.D.Bigelow et al. Madison, Conn.: Sound View Press. 331–41.
Pradere, A.1989. French furniture makers: The art of the �beniste from Louis XIV to the Revolution, trans. P.Wood. Malibu, Calif.: J. Paul Getty Museum.
Watin, J. F. [1772] 1787. L'art du peintre, doreur, vernisseur, 4th ed.Paris, n.p.
Wolbers, R. and G.Landrey. 1987. The use of direct reactive fluorescent dyes for the characterization of binding media in cross-sectional examinations. AIC preprints, American Institute for Conservation 15th Annual Meeting, Vancouver. Washington D.C.: AIC. 168–202.
SOURCES OF MATERIALSLiquitex acrylic mediumsBinney and Smith, 1100 Church Lane, P.O. Box 431, Easton, Pa. 18044–0431 Soluvar matte acrylic resinBinney and Smith, 1100 Church Lane, P.O. Box 431, Easton, Pa. 18044–0431 InstacollKolner-GlanzGold-Grund, Germany, Available from Sepp Leaf Products, 381 Park Ave. So., New York, N.Y. 10016 Rhoplex AC-33, Rhoplex N-580Rohm and Haas Co., Philadelphia, Pa., Distributed by Conservation Materials, Ltd., 240 Freeport Blvd., P. O. Box 2884, Sparks, Nev. 89432 Polyfilla, fine surfacePolycell Products, Ltd., Broadwater Rd., Welwyn Garden City, Herts AL7 3AZ, England
AUTHOR INFORMATION
CYNTHIA MOYER graduated with a B.A. in anthropology and sociology in 1975 from William Smith College. She served apprenticeships in the furniture restoration field in Philadelphia and New York. In 1977 she established a private restoration and conservation practice and for 16 years specialized in gilding and finishes. From 1979 through 1993 she worked primarily for Richard H. Jenrette, collector of American classical furniture and houses. She is a contributing author of the book Gilded wood: Conservation and history and has been an instructor in gilding for the Smithsonian Furniture Conservation Training Program at the Smithsonian Institution Conservation Analytical Laboratory. She has been under contract as an assistant conservator in the Department of Decorative Arts and Sculpture at the J. Paul Getty Museum since 1993, specializing in gilding conservation. Address: J. Paul Getty Museum, P.O. Box 2112, Santa Monica, Calif. 90407-2112.
GORDON HANLON received his B.A. in biology from the University of York, England, in 1979. From 1980 to 1984 he was assistant curator of road and transport and agricultural implements at the Museum of Science and Technology, London. In 1984 he started a four-year studentship at the Victoria and Albert Museum, London, specializing in the conservation of furniture and gilded objects. In 1988 he joined the J. Paul Getty Museum as an intern, and he is now associate conservator in the Department of Decorative Arts and Sculpture, specializing in the conservation of gilded furniture. Address: J. Paul Getty Museum, P.O. Box 2112, Santa Monica, Calif. 90407–2112.
Section Index |