WAX COATINGS ON ETHNOGRAPHIC METAL OBJECTS: JUSTIFICATIONS FOR ALLOWING A TRADITION TO WANE
DANAL L. MOFFETT
ABSTRACT—A case study of wax coating removal from a Benin copper alloy casting in the collection of the National Museum of African Art is presented. A brief review of possible reversal treatments used in the past is provided. Unexpected complications that occurred during the reversal treatment due to the different solubilities of the two components of the applied wax blend are described, along with the final successful treatment of the object. In conclusion, it is suggested that the routine coating of ethnographic metals be reevaluated.
1 INTRODUCTION
The literature on the conservation of metal objects focuses primarily on archaeological material and decorative arts collections. Consequently, ethnographic conservators must form treatment protocols by extrapolating information from this literature and from more general publications on conservation. Recommendations within these sources are rarely accompanied by warnings of the potential for interfering with the remnant casting material, indigenous coatings, or aesthetic aspects associated with ethnographic objects.
Since the era of Plenderleith, the use of protective wax coatings on metal objects has been advocated widely with several objectives in mind: to produce a barrier that excludes moisture and oxygen from the metal surface, to ensure against further introduction of contaminating elements by handling, and to provide a protective layer for undercoatings, such as Incralac formulated with benzotriazole, which may inhibit corrosion (Plenderleith and Werner 1971; Lafontaine 1981; CCI 1988; Pearson 1988; Barclay 1989; Grossbard 1992). In order to render a more homogeneous appearance on a metal surface, both clear and pigmented wax have been applied ostensibly to enhance objects aesthetically (Organ 1970). The majority of these authors recommend the use of wax blends (e.g., microcrystalline and polyethylene waxes) either made commercially or prepared in the conservation laboratory. Using a case study of a copper alloy Benin commemorative head, this paper will show that wax applications can create unforeseen problems when attempts at removal are made.
2 COLLECTION AND TREATMENT HISTORY
In 1897, the British military conducted a campaign against the kingdom of Benin (part of present-day Nigeria) in retaliation for the ambush and murder of the newly appointed colonial commissioner. Following the destruction of Benin City and the exile of the king, the military claimed as war prize a large number of cast copper alloy objects, now commonly known as the Benin “bronzes.” (Most Benin castings are technically brass.) Once in Europe, the castings were distributed among collectors, dealers, and museums.
The object under consideration, a hollow cast male head dating from the late 15th to early 16th century (NMAfA 82-05-002), had once belonged to the British general Augustus H. L. Pitt Rivers, who was a private collector and an early contributor to anthropological theory. The African art historian William Fagg has commented that most of the Benin heads from this period no longer retain a naturally patinated surface “due to the attentions of zealous housemaids” (Bassani 1991, 61). More specifically, Fagg has reported that the Benin objects in the general's care were given a protective coating of neat's-foot oil, a preservative more commonly used on cricket bats. On arrival at the National Museum of African Art (NMAfA) in 1982, the head exhibited an even olive-green coating that was wet in appearance in some areas (fig. 1). While the NMAfA curators found the object's surface aesthetically unacceptable, they were aware that the metal beneath probably had not retained its original patination. They were particularly concerned that the Western coating may have caused areas of uneven corrosion or that the surface had been stripped to bare metal before being coated. In addition, the inner surface of the head exhibited powdery, blue-green corrosion, probably a copper formate (Hopwood 1984).
Fig. 1.
Detail during 1984 treatment, male head, Edo peoples, Benin kingdom, Nigeria, late 15th–early 16th century, copper alloy and iron, height 8� in. The partially cleaned surface, left side, shows the olive-green coating. National Museum of African Art, purchased with funds provided by Smithsonian Collections Acquisition Program, 82–05–002. Photograph courtesy of NMAfA Conservation Archives
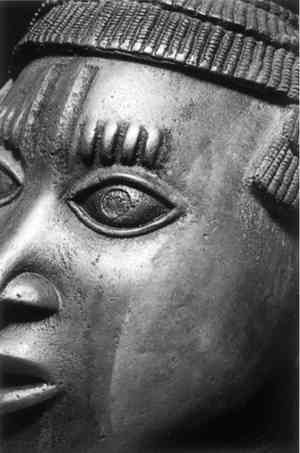 |
As a new member of the Smithsonian Institution, the NMAfA remained in a group of 19th-century townhouses on Capitol Hill while awaiting completion of its building on the National Mall; the museum was without a professional conservator of its own. Consequently, in 1984, a consulting conservator was asked to advise on the best treatment approach for the head. In trial tests, the conservator found that a solvent cocktail (toluene, ethanol, ethylene dichloride, Cellosolve, and Cellosolve acetate) applied with swabs easily removed the olive-green coating.1 Beneath, the metal surface appeared to be in good physical condition and aesthetically acceptable to the NMAfA curatorial staff (fig. 1). Cleaning of the entire piece proceeded to complete removal, at least visually. The copper formate corrosion products were removed mechanically. Following this treatment, as a precaution against further corrosion, the Benin head was given two coats of Incralac (methyl methacrylate copolymer with benzotriazole) followed by a final layer of Renaissance wax (microcrystalline-polyethylene wax blend) and returned to the old NMAfA building for exhibition.
In October 1991, the Benin head was lent to the National Gallery of Art, Washington, D.C., for exhibition in Circa 1492: Art in the Age of Exploration. For several years, the curators had noticed an accumulation of lint and dust on the piece and, in some areas, the 1984 wax coating had become clearly visible as a white haze on the metal surface; casting details seemed muted and flattened (fig. 2). On the object's return from the National Gallery, it was decided to take advantage of the interim period before reinstallation in the gallery, when the object would be in storage, to investigate a reversal of this last treatment.
Fig. 2.
Male head after 1984 treatment, showing lacquered and waxed surface. Photograph courtesy of NMAfA Conservation Archives
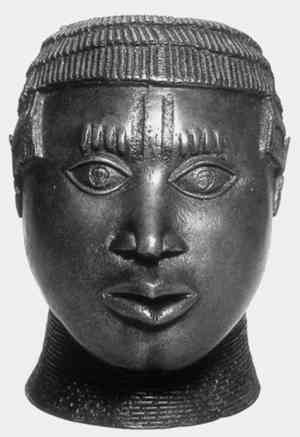 |
In addition to concerns about the aesthetic problems caused by the coating already noted, it was felt that any protective function the wax might have afforded was no longer required at the new museum building, where exhibition cases are constructed of high-quality materials and where the relative humidity is easily controlled on a general as well as a microenvironmental level. Moreover, Fenn and Foley (1975) reported that industrial research on several types of coatings, including wax, indicates that they do not provide an impervious barrier to water and oxygen, although they may offer protection from contamination during handling. Incomplete or damaged coatings may create electrochemical cells that encourage corrosion to proceed at the points of imperfection. Finally, the Benin head also had been coated with Incralac, which has been shown to age poorly under certain conditions (LaFontaine 1981; Erhardt et al. 1984). These factors, coupled with the aesthetic problems, intensified the desire to remove the lacquer as well as the wax and to leave the surface of this object coating-free, if possible.
3 PRESENT TREATMENT
Incralac is the trade name of a lacquer manufactured using Acryloid B-44 (methyl methacrylate copolymer), which can be solubilized readily in acetone, toluene, xylene, and dichloromethane, as well as in a number of solvents less commonly used in the conservation field (Horie 1987). Removal of the microcrystalline-polyethylene wax blend coating would not be as straightforward. Although the natural waxes were used early on in conservation treatments, the synthetic waxes are now more favored by the field; they are generally more neutral and stable and are unfettered with free fatty acids. Of the synthetic variety, microcrystalline and polyethylene waxes are most commonly employed. Semisynthetic by-products of petroleum, microcrystalline waxes are derived from the same source as paraffin but, as the name suggests, have a structure that allows for a considerable increase in plasticity; they are highly branched and irregular molecules. Moreover, these materials can hold other waxes in suspension, a characteristic that aids in the manufacture of smooth polishing pastes. Polyethylene waxes are made from the polymerization of ethylene gas derived from petroleum. Structurally, they vary little from paraffin and are usually white, translucent, hard, and tough.
In the last two decades, attempts have been made to reverse wax coatings with varying success. Treatments have focused on the application of solvents or heat or, in some cases, a combination of the two. Boiling water was suggested by Organ and Shorer (1962), but Johnson (1984) tested this approach and found it to be ineffective. The application of cold solvents is not always successful; hot solvents used in quantity pose health and safety risks, and consequently this approach may be unrealistic for large objects or for mass treatment of numerous artifacts. Johnson (1984) proposed the use of commercial solvent cleaning systems that employ a hot liquid wash, a hot vapor wash, or a combination of the two. These methods have yielded good results in industry but require commercial equipment that may be impractical for the treatment of individual objects.
Organ (1970) advocated the use of a Soxhlet extractor for wax removal on small pieces and a Fuller's Earth–toluene poultice for treatment of larger objects. The latter technique has been modified more recently by Dove (1989), who suggested poulticing a waxed surface with a polyvinyl acetate emulsion and diatomacious earth pack; heat is added by placing the poulticed object in an oven with the temperature set just above the melting point of the wax. The molten coating is successfully absorbed into the poultice after 24 hours.
In the case of the Benin head, the above treatments were discounted for various reasons. Poulticing techniques, reported to be the most successful, were rejected due to concern that the pack material would remain in the deep and intricate sculpting of the hair and face. Moreover, total poulticing of the metal surface under gently elevated temperatures posed the problem of control during cleaning; it would be impossible to keep an eye on the condition of the surface—important, as noted above, for aesthetic reasons—beneath the poultice. Heating large quantities of solvents without specialized equipment was felt to be unsafe, and industrial solvent cleaning systems were deemed financially impractical for one object.
Consequently, an attempt was made to try to reverse the coatings with cold solvents. As noted above, Renaissance wax is a mixture of microcrystalline and polyethylene waxes (Plenderleith and Werner 1971; Horie 1987), both of which are slightly soluble at room temperature in naphtha, xylene, and toluene (Warth 1956). It seemed possible and practical that one could remove both the lacquer and the wax with the same solvent, at one time, and toluene was tested in a small area using cotton ball applicators. Visual assessment, a slight discoloration of the cotton, and a change in the appearance of the surface suggested that at least some wax was removed with this method, and as a further test a portion of the head was immersed in a toluene bath for several hours. The unexpected result of this trial treatment, on evaporation of the solvent from the “cleaned” surface, was a brittle, translucent white residue tenaciously adhered to the treated area. This material was totally insoluble in toluene at room temperature (fig. 3).
Fig. 3.
Detail, male head during 1992 treatment showing white residue from solvent immersion. Photograph courtesy of NMAfA Conservation Archives
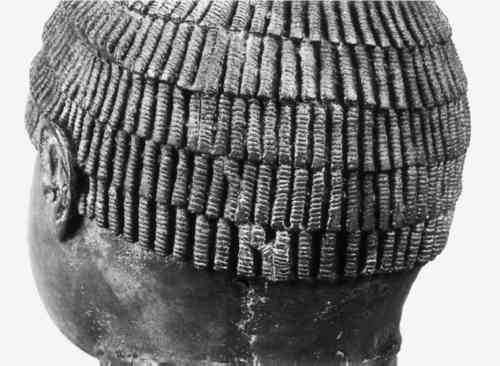 |
Regarding the exact nature of this residue, it seemed probable that the white waxy material would be one of the two components of the Renaissance wax. This assumption was substantiated by FTIR analysis; the spectrum closely matched that for polyethylene wax, and there were no signs of remaining Incralac or microcrystalline wax (Hopwood 1992).
The differing results obtained in the two trial cleanings may be explained by molecular weights—that of microcrystalline wax is lower than that of polyethylene wax. Although they are both reportedly soluble in toluene at room temperature, only the microcrystalline wax, because of its lower molecular weight, was completely reversible with extended immersion; the polyethylene wax was not. In the first trial, the added mechanical action of swabbing may have aided in the apparent removal of both waxes.
After conversations with various industrial chemists, a literature search, and trials with a number of solvents, it was found that hot (82�C) xylene (Warth 1956) would successfully remove the white flakes of polyethylene wax. As a safety precaution, only small quantities (150 ml) of xylene were heated within a fume hood to the desired temperature, and then the heated solvent was applied with cotton swabs to the affected surface. This procedure worked well to remove the white flakes. An unanticipated benefit of the treatment was the removal of a vivid yellow substance, which was identified as carboxylic acid by FTIR (Hopwood 1992); this organic acid is likely to be residual from the coating removed during the 1984 treatment.
After the polyethylene flakes were eliminated, the problem of removing the wax and lacquer from the rest of the object remained. For several reasons, the same hot solvent application was believed to be the best method for completing treatment of the object. First, heated xylene seemed to clean the surface more deeply than cold solvent, as evidenced by extraction of the residual carboxylic acid. Moreover, in a comparison of areas cleaned by the two methods, the surface treated with hot xylene appeared to be cleaner. With repeated applications of solvent, swabbing could proceed until no yellow discoloration was detected; this standard could serve as a gauge for completion of cleaning. Finally, the treatment to remove the polyethylene flakes demonstrated that, with due precaution, the solvent could be heated safely in small quantities. Thus, the treatment was carried through using hot xylene. With both the tenacious white flakes removed and the entire object cleaned, the surface of the Benin head was given more “life,” and the intricate details of the casting became sharper (fig. 4).
Fig. 4.
Male head after 1992 treatment with surface now coating-free. Photograph by Franko Khoury, National Museum of African Art
 |
4 DISCUSSION
Wax application has become an accepted treatment for ethnographic metals. Such coatings can leave surfaces and details muted as well as susceptible to accumulations of dust and lint. A particularly important note for ethnographic objects is that any type of coating may interfere with indigenously applied surfaces or investment material. The above case study illuminates the reversibility problems that may be experienced when objects have been coated with wax. Although the technical literature indicated that both waxes should be soluble in toluene at room temperature, the initial immersion test using this solvent produced unforeseen complications. Polyethylene wax coatings, though slightly soluble in several hydrocarbon solvents, are effectively and efficiently removed only with heated xylene.
In light of the present study, when attempting to remove wax from metal, one should be cognizant of the different components in blends of commercial preparations, and one should also consider that the apparent solubility of any one wax may vary according to the manner in which the solvent is applied. Pure microcrystalline waxes (e.g., Cosmolloid 80H) are available and may be preferable to the use of wax blends. Most important, ethnographic conservators should carefully weigh the necessity of applying wax coatings in museum environments where objects can be handled appropriately, as well as vitrined to provide protection; whenever possible, noninterventive alternatives to waxing should be sought.
ACKNOWLEDGEMENTS
The author thanks Walter Hopwood of the Conservation Analytical Laboratory, Smithsonian Institution, for FTIR analysis and interpretation of wax samples. Photographs and their color printing for this article were made possible by the National Museum of African Art.
NOTES
1. Interestingly, Fourier transform infrared spectroscopy (FTIR) analysis of the coating contradicts Fagg's report of the use of neat's-foot oil; the spectrum suggests a substance similar to gum tragacanth (Hopwood 1984).
REFERENCES
Barclay, B.1989. Basic care of coins and medals. Canadian Conservation Institute Notes9(4).
Bassani, E.1991. William, B. Fagg: One hundred notes from Christie's catalogues, 1974–1990: A selected anthology. Quaderni Poro7:59–61.
CCI. 1988. The cleaning, polishing, and protective waxing of brass and copper objects. CCI Notes9(3).
Dove, S.1989. A method for dewaxing ironwork. Conservation News40(11):11.
Erhardt, D., WHopwood, T.Padfield, and N.Veloz. 1984. The durability of Incralac: The examination of a ten-year old treatment. ICOM Committee for Conservation Preprints, 7th Triennial Meeting, Copenhagen. Paris: ICOM. 2:84.22.1–84.22.3.
Fenn, J., and K.Foley. 1975. Passivation of iron. In Conservation in archaeology and the applied arts: Preprints of the contributions to the Stockholm Congress, 2–6 June 1975. London: International Institute for Conservation of Historic and Artistic Works. 195–98.
Grossbard, E.1992. The care and conservation of metal artifacts. In Conservation concerns, ed.K. Bachmann. Washington, D.C.: Smithsonian Institution Press. 101–4.
Hopwood, W.1984. Conservation Analytical Laboratory Report 4444, April 13. Washington, D.C.: Smithsonian Institution.
Hopwood, W.1992. Conservation Analytical Laboratory Report 5369. March 13. Washington, D.C.: Smithsonian Institution.
Horie, V.1987. Materials for conservation. London: Butterworths.
Johnson, R.1984. The removal of microcrystalline wax from archaeological ironwork. In Adhesives and consolidants, ed.N. S.Brommelle et al. London: International Institute for Conservation of Historic and Artistic Works.107–9.
LaFontaine, R.1981. The use of a stabilizing wax to protect brass and bronze artifacts. Journal of the International Institute for Conservation—Canadian Group. 4(2):46–48.
Organ, R.1970. The conservation of bronze objects. In Art and technology, ed.S.Doeringer et al. Cambridge, Mass.: MIT Press. 73–84.
Organ, R., and P.Shorer. 1962. An improved method of consolidating fragile iron objects. Museums Journal62:109–13.
Pearson, C.1988. Conservation of ethnographic metal objects. In The museum conservation of ethnographic objects, ed.T.Morita and C.Pearson.Senri Ethnological Studies 23. Osaka, Japan: National Museum of Ethnology. 129–73.
Plenderleith, H., and A.Werner. 1971. The conservation of antiquities and works of art, 2d ed.London: Oxford University Press.
Warth, A.1956. The chemistry and technology of waxes. New York: Reinhold Publishing.
AUTHOR INFORMATION
DANA L. MOFFETT is conservator at the National Museum of African Art, Smithsonian Institution. In 1988, following internships at the British Museum and the Horniman Museum, she received a B.Sc. (Hons.) in archaeological conservation from the Institute of Archaeology, University College, University of London. She also holds an M.A. in anthropology (1989) with special emphasis on art and aesthetics from the University of Denver. Address: National Museum of African Art, Smithsonian Institution, Washington, D.C. 20560.
Section Index |