INTERPRETATION OF ANCIENT ARTISTRY: CONSERVATION OF A GOLD WREATH FROM THE FOURTH CENTURY B.C.
JEFFREY P. MAISH
3 INFORMATION OFFERED BY THE ARTIFACT
3.1 AUTHENTICITY
X-ray fluorescence analysis of several locations on the wreath (fig. 3) suggests a gold-copper alloy consistent with ancient gold production methods (Scott 1993). The construction methods were similar to those employed on other wreaths. The sophisticated craft techniques included a construction method in which melting points used by separate manufacturing steps may have been successfully lowered.
Fig. 3.
X-ray fluorescence spectra of four components of the wreath: the main tube, a leaf, a disc, and strip-twisted wire at the rear of the wreath
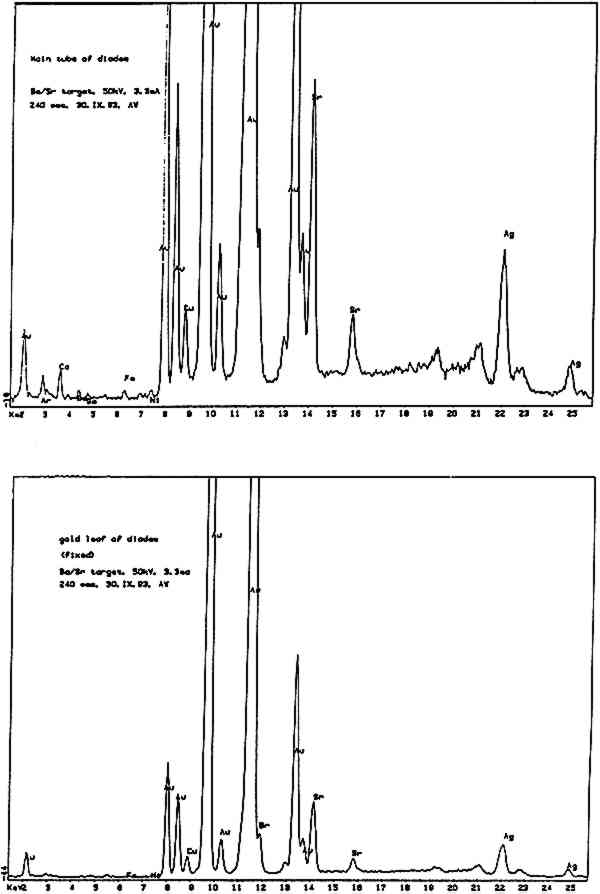 |
3.2 STATE OF PRESERVATION
Our decision-making process depends in a large part on the state of the object's preservation. In some situations, specific details from one area of an artifact may therefore be used to reconstruct another area. This artifact's structure, intricate yet also repetitive, enabled some technical information to be transferred. A technical survey of the wreath aided in establishing its degree of completeness. The survey of the main support tube showed that out of 46 possible spikes or points of attachment for branches, only 26 branches remained. What were initially thought to be tendrils of a vine actually proved to be locations of missing myrtle flower elements. A count of these wires showed that 124 pieces were missing. They may have been either all single flowers or a mix of flowers and rounded “buds” (illustrated in Polunin and Huxley 1978, Andronicos 1992). Of the preserved flowers, 80 remained attached to the wreath, and 55 were detached. The overall completion level was sufficient to give a reasonable idea of the design of the wreath.
3.3 TECHNICAL FEATURES
Initially, wire and foil were manufactured through methods that included hammering, stamping, twisting, and coiling. Segments of the manufacture such as foil and wire production could have been independent operations, although these components also may have been part of the wreath production method.
Lengths of twisted wire would have been produced by rolling thin strips of gold foil into small, tightly coiled tubes. More detailed components such as the flower petals and stamens could have been formed in large quantities at an early stage for later assembly into complete flowers.
The main support of the wreath was formed from two curved and tapered tubes. Spikes were then soldered on for the tubes of the branches (fig. 4). The two tube halves were joined at the rear with wire looping and at the front with a decorative Herakles knot (fig. 5). The branch stems were formed separately from smaller diameter tubes. Heavier gauge wires were inserted through punched holes in the tubes and then flattened and trimmed to form leaves. Flowers were assembled on wires that had been previously attached to the branch tubes. Each flower consists of three or possibly four components including a hemispherical support, a group of petals, and either a wire stamen or a single or double ring disc. In some instances a plasterlike core remained in the interior of the hemispherical portion of the flower. The plaster core may have supported the gold foil during forming but probably also gave the flower further structural support, or its added weight may have played an aesthetic role by allowing the flowers to sway. The petals may have been produced by stamping. The regularity of the shapes and sizes, suggests stamping, as do the matching outlines of two petal groups on one stem. A gradual bowing of the flowers' profiles also suggests stamping or punching.
Fig. 4.
Diagram showing the formation of (a) the two main tube sections; (b) individual branches; (c) flower components; and (d) final assembly.
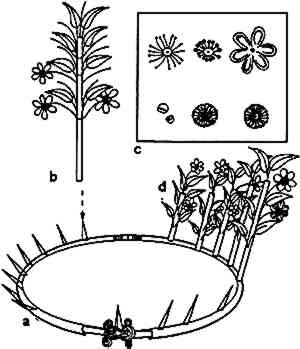 |
Fig. 5.
Detail showing the main wreath tube halves joined at the rear with two sets of coiled wire
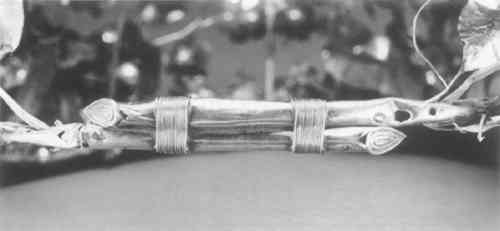 |
Soldering and heating most probably was carried out in a small oven capable of approximating the melting point of fine gold at 1063�C (Untracht 1975). The stamens (fig. 6) were produced using the following techniques in succession. After the preliminary mechanical working was completed, the artisan might have executed higher-temperature forming to shape the rounded tips of a stamen, followed by lower-temperature joining of individual parts of the wreath. Finally, a low-melting-point glass was added to some areas. Anthers of blue glass globules were fused to the tips of some wire stamens, and blue glass was added to color several flower petals. Bubbles or “seeds” in the glass are highly suggestive of lower-temperature work (Newton and Davison 1989). In addition to gas bubbles, environmental Scanning Electron Microscopy inspection of the glass surface (fig. 7) of one petal group shows the incomplete mixing of the glass components, another indication of fairly low-temperature glass working.
Fig. 6.
Diagram showing the successive methods (postulated) used in forming the wreath
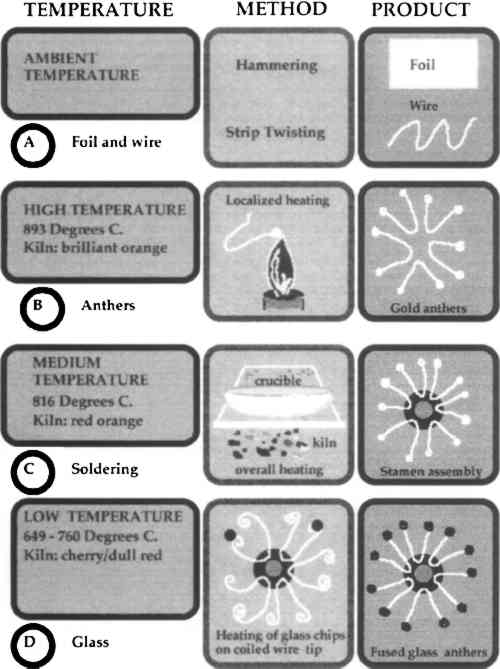 |
Fig. 7.
Environmental scanning electron micrograph image of the surface of the blue glass fill on a flower petal. Incomplete fusion has resulted in distinct glass phases. 280�
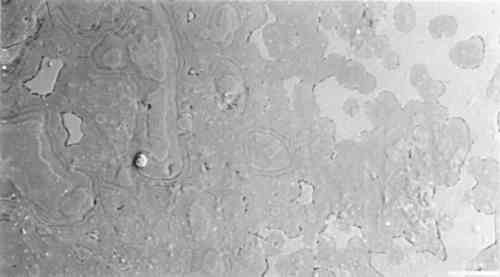 |
3.4 AESTHETIC
Some contemporaneous Lucanian wreaths from the fourth century B.C. include fanciful details in their design (Deppert-Lippitz 1985). Ornate elements such as star-shaped flowers and erotes, in one example, contrast with the more naturalistic aesthetic of the Getty wreath, which belongs to a group of wreaths possessing a significant degree of botanical accuracy.
When compared in photographs to a real myrtle branch, the accurate details of the Getty wreath can be seen to include the shape of the flowers and the leaves. The variable leaf size and tapering stem diameters also suggest natural growth patterns (Polunin 1969). This tradition of the naturalistic representation of plant life also seems to have included depictions of ivy, oak, and olive branches.
In a departure from absolute naturalism, the creator of the Getty wreath has inserted a mixed grouping of colored glass flowers at the front variously described as gentian or campanula, and even one example of a presumably imaginary flower with alternating blue and green petals (fig. 8).
Fig. 8a–e.
Details showing typical flower types found on the wreath: (a) 8-petal flower with low-temperature blue glass; (b) 12-petal flower with a strip-twisted wire bordering blue glass; (c) 6-petal flower with block-twisted petal borders; (d) 8-petal flower with block-twisted petal borders; and (e) 2 detached but assembled 6-petal foil flowers.
 |
Despite the seemingly random organization of the wreath, a careful examination revealed an underlying design. Spikes were soldered to the main branch tube in a roughly symmetrical pattern with some branches facing upward and forward, while others faced upward, forward, and slightly outward (fig. 9). It follows, therefore, that the branches, too, were arranged in a distinct pattern. Symmetrical placement is also found in the individual branches in which leaves were positioned opposite one another. The sum of the parts of the wreath was combined, however, to create a naturalistic and aesthetically gratifying design.
Fig. 9.
Diagram showing the attachment of the spikes onto the main wreath tube
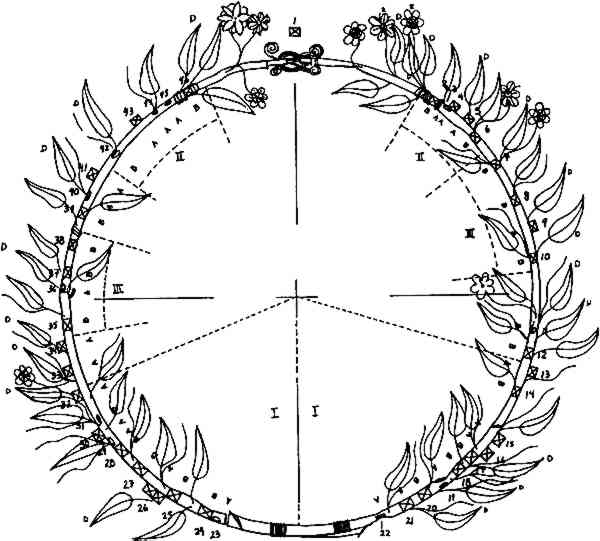 |
Each of the wreath's 26 individual branches was sketched, numbered, and mapped for technical features (fig. 10). The approximate sizes of the flowers were measured as well, and four distinct dimensions were noted as A, B, C, or D with sizes ranging from 15 to 20 mm. This range indicates that the artisan was interested not only in depicting a wreath but also in creating branches with variable vertical growth. Flower sizes were also noted by quadrant to show their horizontal distribution. One quadrant in particular was “depleted” of flowers. Although they were not surveyed, several leaf sizes could be noted on the wreath as well. Different design elements were also noted. Stamens, for example, were either of the less common wire type (with or without glass) noted above, or of the disc type (single or double ring). All these individual elements introduced a much higher degree of variability to the piece than was originally anticipated. Were the more complex elements meant to be placed at the front only, or to be scattered throughout the piece? Did the size of the flower petals determine their location of placement? Were wire stamens supposed to underlie the disc stamens or vice versa? In fact, the answers depended on one simple technique: the twist of a wire, which was the final step of each flower assembly. The ability to recognize an original twist, therefore, would allow us to better distinguish between the original elements and those altered by ancient repairers and modern restorers. Ultimately these sketches became maps that documented the additions during treatment.
Fig. 10.
Illustration of a single branch documenting condition, additions, and modifications during treatment
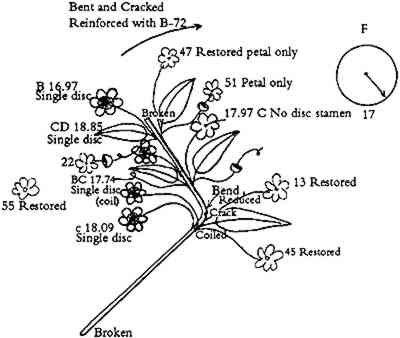 |
To all of this one may add the depredations of time, arising from the object's own chemical composition and its environment. In this case the surface alteration was generally minimal and confined to a light calcareous layer on some leaves. Several of the flowers, however, appear to have a high mirrorlike finish on one side (fig. 11). The question remains as to whether this effect is a result of an intentional finishing process, variable weathering during burial, or perhaps an uneven cleaning.
|