CHEMISTRY AND CONSERVATION OF PLATINUM AND PALLADIUM PHOTOGRAPHS
ADAM GOTTLIEB
ABSTRACT—The Stieglitz Colloquy in May 1993 drew attention to the deterioration of platinum and palladium photographs, even though the former is considered to be among the most “permanent” photographic techniques. The chemical composition of the two types of photographs is clarified to aid the conservator in distinguishing the prints and determining the types of deterioration they might be subjected to in the future. The prints are chemically characterized by three means: by searching the available literature for references to processes, beginning in the 1850s; by re-creating the processes according to the recipes; and by developing a method using energy dispersive x-ray spectroscopy to carry out elemental analysis of the metals used in the processes, thus allowing the chemical compounds that might have originally supplied the raw materials for the processes to be inferred.
1 INTRODUCTION
In May 1993, photograph curators adn conservators gathered at the National Gallery of Art in Washington, D.C., to discuss paper base discoloration in prints by Alfred Stieglitz. This Steiglitz Colloquy drew attention to the deterioration of platinum and palladium photographs, the former until recently considered “permanent.” As a first step toward developing a science of conservation specific to platinum and palladium photographs, this study aimed to identify their chemical composition. The goal of chemical characterization of prints is twofold: to enable conservators to care for or repair them and possibly others that are thought to have been made like them, and to illustrate the chemical changes that a print prepared in a certain way will undergo over time. Three interrelated approaches were used to achieve this goal. First, an extensive list of chemicals mentioned by periodicals between 1856 and 1940 for use in platinum and palladium printing and intensification was compiled. Second on the basis of this list, the palladium printing process was re-created in order to determine the effects of different chemicals and printing techniques on the appearance of photographs and so to provide a reference bank with which to identify, using visual information only, how a given print was made. Finally, a method to identify the chemicals used to make a given print was developed using elemental analysis provided by energy dispersive x-ray spectroscopy (EDX) and historical information to infer the compounds the elements could have come from.
2 PLATINUM AND PALLADIUM PHOTOGRAPHIC PROCESSES
2.1 HISTORY OF PLATINUM AND PALLADIUM PHOTOGRAPHY
Platinum is first mentioned for use in photography in 1856, palladium in 1859, both as intensifying agents for silver prints (Dancer 1856; Photographic Notes 1856; Gwenthlian 1859). Old sources often use the terms “toner” and “intensifier” interchangeably. Platinum and palladium treatment of iron, mercury, silver, and uranium prints is more properly viewed as intensification. William Willis is widely credited with having created the platinum printing process. However, the first mention in the literature of a sensitizer based on platinum cites the experiments of a Mr. Merget, in which paper is coated with platinic acid, ferric chloride, and tartaric acid, then exposed, and developed using mercury vapor (British Journal of Photography 1873; Abney and Clark 1898).
From this departure point, William Willis designed and patented the first successful platinum printing process using a ferric oxalate–potassium tetrachloroplatinite sensitizer. The oxidation-reduction chemistry of these two ingredients, whereby iron is reduced upon exposure to ultraviolet light, then oxidized by a developer with concomitant reduction of platinum, and finally cleared using hydrochloric acid, remains the basis of platinum and palladium printing. The terms “fixing” and “clearing” are used interchangeably in old and current sources alike. “Clearing” is used to distinguish platinum and palladium processes from silver printing. Whereas many firms, including Willis Platinotype Company, mass-produced platinum printing papers, the process survives today as it was created, with hand-coated papers.
Features of Willis's initial process that have since been changed include the use of the oxidizing agents lead nitrate and silver nitrate in the sensitizer to prevent ferric oxalate from being reduced prior to exposure and to produce a finer deposit of platinum; the need to heat the potassium oxalate developer (hence the name, hot-bath platinum printing”); and the use of a clearing agent consisting of ammonia, ammonium chloride, oxalic acid, sodium chloride, and sodium hyposulfite.
Willis himself was responsible for many of these changes, starting in 1878 with the elimination of silver nitrate from the sensitizer, addition of potassium tetrachloroplatinite to the developer, and replacement of the hyposulfite-based clearing agent with hydrochloric acid, and followed in 1880 by the replacement of lead nitrate in the sensitizer with ferric chlorate.
In 1882, Joseph Pizzighelli and Arthur von H�bl proposed two further modifications—replacement of ferric chlorate in the sensitizer with potassium chlorate and removal of potassium tetrachloroplatinite from the developer, which left the hot-bath process largely in its modern form. In contrast, the printing-out platinum process introduced by Pizzighelli in 1887 was short-lived, owing to its inconsistency. Potassium oxalate was incorporated into the ferric oxalate–potassium tetrachloroplatinite sensitizer; thus prints developed as they were being exposed, and processing required only clearing with hydrochloric acid.
Coincident with Pizzighelli's printing-out experiments, William Willis introduced a cold-bath platinum printing process, named after the tone of the image rather than the temperature of the developer, using potassium tetrachloroplatinite in the developer instead of in the sensitizer. The results of this process, too, were inconsistent, and in 1892 Willis replaced it by a true room-temperature–developer (cold-developer) platinum printing method. The chemistry of the sensitizer was never disclosed, but Abney and Clark (1898) indicate that a much speculated-upon secret ingredient was likely a dichromate salt.
Methods for toning (replacing the image-forming platinum deposit with gold, mercury, or uranium) and intensifying (proportionally adding silver, palladium, or platinum to the image-forming platinum deposit) finished platinum prints also proliferated in the mid-1880s. The main deterent to their continued practice is the cost and toxicity of the chemicals.
Palladium printing is first mentioned in 1874. The process was less popular than platinum printing, chiefly because palladium was more expensive at the time. The greater inertness and catalytic activity of platinum make it more useful in industry and prompted its price to rise sharply during the World War I. Both of these properties are relevant to printing and conservation: unlike platinum, palladium can be dissolved by acid, thus images can be bleached upon clearing and possibly upon storage in acidic environments; of concern to conservation, platinum's enhanced catalytic activity accelerates paper embrittlement and is responsible for image transfer (Reilly 1986).
Palladium was discovered after platinum and was initially more expensive. In part for these reasons, palladium was sometimes viewed with interest by photographers as the finer alternative. The warmer tones palladium produced were variously preferred and disfavored relative to those of platinum. A consideration in palladium printing's favor is that a hot developer is not required.
Palladium printing is rarely mentioned in the literature before 1895 and was not widespread until the late 1910s. As platinum is now 10 times more expensive than palladium, the latter is the decided preference of most amateur printers today. Nonetheless, most manuals continue to focus explicitly on platinum printing, treating palladium printing as a minor offshoot. Historically, both platinum and palladium prints have the reputation of being permanent, due to the stability of the metal that constitutes the final image. More recently, the stability of the paper supports for both platinum and palladium prints has come into question, as described by Reilly (1986) and addressed at the Stieglitz Colloquy. The internal and external sources for the discoloration are of interest, as well as the means of treating and avoiding the discoloration by proper handling, storage, and exhibition.
2.2 CHEMICALS USED IN PLATINUM AND PALLADIUM PHOTOGRAPHY: A REVIEW OF THE LITERATURE TO 1940
The periodical liteature of Great Britain, the United States, Germany, France, Austria, and Belgium between 1839 and 1940 was studied to ascertain the full range of chemicals that were experimented with for platinum and palladium printing and intensification in the 19th and early 20th centuries, and to expand both on the well-known manuals of Abney and Clark (1898), Horsley-Hinton (1898), and Pizzighelli and von H�bl (1886) and on latter-day manuals by Steinberg (1992), Sullivan (1992), Nadeau (1986), Shillea (1986), Hafey and Shillea (1979), and Rexroth (1977). Fifteen journals were chosen, mostly from the History of Photography microfilm series, and every article mentioning platinum or palladium printing or intensification was reviewed. In all, 391 articles in publications such as the British Journal of Photography, the Philadelphia Photographer, L'Amateur photographe, and the Jahrbuch f�r Photographie und Reproduktionstechnik were surveyed. The result was a list of chemicals mentioned for use in sizing, sensitizing, developing, clearing, toning, intensifying, reclearing, neutralizing, varnishing, and mounting platinum and palladium prints; in intensifying iron, mercury, silver, and uranium prints with platinum and palladium; and in preparing chemicals for platinum and palladium printing and intensification. This list is available from the author and at the library of the Department of Chemistry at Princeton University (Gottlieb 1993)
3 RE-CREATING THE PALLADIUM PRINTING PROCESS
3.1 METHODOLOGY
On the basis of this list of chemicals, the palladium printing process was re-created. To minimize contamination, materials free of metal parts were chosen for all contact with chemicals and prints; these include measuring spatulas, containers, print frames (except for hinges), trays, tongs, and clothespins.
Articles dating from the 19th century suggest that between 1.8 and 3.0 parts of iron (III) should be used per part of platinum(II) or palladium(II) (Pizzighelli and von H�bl 1886). Solutions of ferric oxalate and sodium tetrachloropalladite were prepared as follows, so that equal amounts would give 2.4 parts of iron(III) per part of palladium(II).
Ferric oxalate solution was prepared by disolving 24.8 g in distilled, deionized water to 100 ml final volume. Traditionally, about 1.7 g of oxalic acid are added to the ferric oxalate solution, and two solutions of ferric oxalate are prepared, to one of which 0.46 g of potassium chlorate are added. Oxalic acid was not used. In order to permit the maximum number of variables to be studied independently, potassium chlorate was prepared separately in 3% by weight solution rather than added to the ferric oxalate solution (see section 3.4.2). A coating of 22 drops ferric oxalate–potassium chlorate solution for use with low-contrast negatives, standard in modern platinum printing manuals, is replaced by 20 drops ferric oxalate solution plus 6 drops potassium chlorate solution. Sodium of tetrachloropalladite solution was prepared by dissolving 9.5 g palladious chloride dihydrate plus 8.3 g sodium chloride in distilled, deionized water to a final volume of 100 ml.
Crane's Kid Finish cotton rag paper was used. For the test discussed in section 3.4.1, the paper was sized prior to sensitization. The coating employed, except for the tests discussed in sections 3.4.2 and 3.4.3, consists of 20 drops ferric oxalate solution plus 4 drops potassium chlorate solution plus 20 drops sodium tetrachloropalladite solution. The drops are swirled together, poured along one edge of a sheet of paper, and spread across the paper by rolling with a glass rod. The paper was coated once, allowed to dry, and then coated again starting from the opposite end to make an even coat. If, upon inspection, the coating appeared to be uneven, another piece of paper was coated. For the test discussed in section 3.4.1, only one coating was possible. Only one final print was made for each level of each control variable; thus statistical validity of the results cannot be shown.
Coated paper was exposed by contact-printing with up to 12 identical 120- format negatives in a single contact print frame. Exposure was therefore identical for all prints within a test group, except for the tests discussed in sections 3.4.3 and 3.5.1. The exposure unit consisted of 12 20 W fluorescent ultraviolet-emitting bulbs, a total of exposure of 240W. After exposure, the paper was cut up into its individual images, which were then subjected to different treatments depending on the variable being tested.
Developers were prepared with distilled, deionized water; fixers, with tap water. Prints within a given test group were developed simultaneously or in quick succession, as soon after exposure as possible. They were developed for 3 minutes at 70�F, and cleared for 3 minutes in each of three baths of 1:199 hydrochloric acid. Cleared prints were rinsed together for 10 minutes in running tap water and then hung up together to air-dry on a line. Upon drying, all prints within a test group were sealed together in a plastic bag, which in turn was sealed in a light-tight plastic bag stored in a darkroom. Prints were stored in this way until they could be analyzed and again after analysis.
Prints were analyzed visually for tone, shadow density, grain size, and contrast. In many cases, differences were very subtle and difficult to interpret. In general, wherever prints do not have comparable shadow density, contrast is extremely difficult to assess for lack of a common reference point. Lower highlight density exaggerates the already warm or cold tone of a print.
Effects on contrast, grain size, and tone are extremely difficult to assess when bleaching occurs. Bleaching increases contrast and reduces shadow density. It also appears to make palladium prints grainier by making the palladium deposite less even, and warmer by removing density from the shadows. None of these variables is affected when bleaching does not occur. Thus, for tests in section 3.3, all apparent effects of the bleaching clearing agents citric acid, hydrochloric acid, and oxalic acid are discounted.
3.2 DEVELOPING
3.2.1 DIFFERENT DEVELOPERS
In contrast both to developers for silver prints and to sensitizers and toners for platinum prints, knowledge of the wide variety of developers for platinum and palladium prints has not survived in the modern literature. Present-day platinum printing manuals discuss only three kinds of developers: those based on potassium oxalate; those based on sodium acetate, and those based on citrates (Sullivan 1992; Steinberg 1992; Nadeau 1986; Shillea 1986; Hafey and Shillea 1979; Rexroth 1977). Many of the developers that have disappeared from the platinum printing literature remain inexpensive and available. As a group, they permit extensive control over print contrast and tone and required exposure time.
Nine of the most popular developers from the late 1800s were tested (table 1). Dilution formulas for single-compound developers other than potassium oxalate do not exist in the literature of the time. Thus, weight-equivalent solutions of the standard oxalate developer, 454 g to 1420 ml final volume in water, or 1.67M, were prepared.
TABLE 1 DEVELOPERS TESTED
Effects of different developers on contrast, tone, and shadow density are difficult to assess when hydrochloric acid is used as a clearing agent, as is discussed in section 2.1. Therefore, a second set of tests was performed with a nonbleaching clearing agent, tetrasodium ethylenediaminetetraacetate (EDTA tetrasodium). However, here tone cannot be compared in all cases because EDTA tetrasodium dramatically alters the color of prints processed in basic developers.
CONCLUSIONS: The developers tested (see table 1) can be grouped roughly into the following categories: warm-toned: 2, 3, 7; warm- to neutral-toned: 4, 5, 8; neutral- to cold-toned: 1, 6; weak: 2, 6, 7, 9; high-contrast: 1, 6, 8; low-contrast: 2, 7. Prints developed in potassium carbonate, sodium carbonate, monohydrate, or sodium phosphate dibasic heptahydrate become orange in tone when cleared with EDTA tetrasodium.
3.2.2 TEMPERATURE OF DEVELOPER
Room-temperature developers have long been standard in photography. Their advantages over hot developers include ease of use and lower volatility, so they are less toxic. Platinum printing was created as a hot-developer process. Many years later it became a cold-bath process like palladium printing (seesection 2.1). In modern platinum printing practice, a developer is heated only to increase its activity with a view to salvaging an underexposed print or to give prints a warmer tone. As the added density is not nearly proportional to the increase in temperature, the former is not a powerful remedy. Some sources indicate that sodium carbonate will work as a developer only when hot.
Ammonium citrate, potassium oxalate, and sodium carbonate were each tested at 40, 70, 110, and 180�F (fig. 1).
Fig. 1.
Prints showing the effects of varying developer temperature. Key: 1. ammonium citrate 40�F; 2. ammonium citrate 70�F; 3. ammonium citrate 110�F; 4. ammonium citrate 180�F; 5. potassium oxalate 40�F; 6. potassium oxalate 70�F; 7. potassium oxalate 110�F; 8. potassium oxalate 180�F; 9. sodium carbonate 40�F; 10. sodium carbonate 70�F; 11. sodium carbonate 110�F; 12. sodium carbonate 180�F
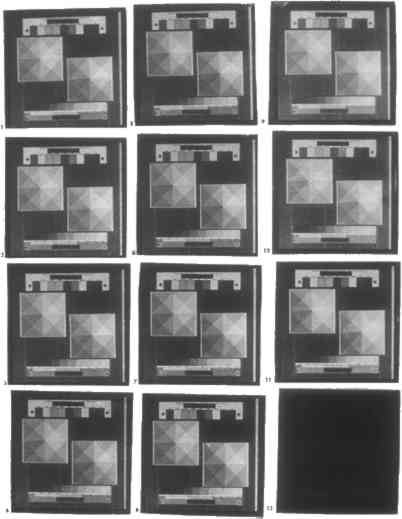 |
CONCLUSIONS: The most dramatic change that occurs as developer temperature is increased is warming of print tone. This change in behavior is best illustrated by ammonium citrate: it produces cold-toned prints at 40�F and warm-toned prints at 180�F. Potassium oxalate produces warm tones at all temperatures but especially at 180�F. In both cases, contrast decreases slightly with increasing temperature, while shadow density increases slightly. Sodium carbonate exhibits the same behavior as the other two developers up to between 70 and 110�F. Above this range prints begin to develop a yellow tone. Finally, at 180�F, sodium carbonate nearly blackens prints owing to the formation of insoluble ferrous carbonate.
3.2.3 DILUTION OF DEVELOPER
As indicated in section 3.2.1, dilution formulas for developers other than those based on potassium oxalate do not exist in the literature. At a concentration of 1.67M, the standard potassium oxalate developer is exceedingly strong by silver photography standards. Use of potassium oxalate at this concentration or other developers in weight-equivalent solution is not economical and may not be necessary.
Potassium oxalate, sodium acetate, and sodium carbonate were each tested at 0.05, 0.30, 0.83, and 1.67M concentration.
CONCLUSIONS: Potassium oxalate produces black shadows at as low a concentration as 0.30M. It becomes only slightly stronger as concentration is increased thereafter. Sodium acetate does not produce vigorous images below a concentration of 0.82M; its performance improves significantly with increased concentration. Both developers become colder in tone and higher in contrast as they are diluted.
3.2.4 ACIDITY OF DEVELOPER
Early sources recommend acidifying potassium oxalate developer with oxalic acid to prevent the formation of basic iron salts, which give prints a yellow tone (Pizzighelli 1883). It is now common practice to use oxalic acid in the sensitizer instead. However, with a citrate developer it would be more appropriate to use citric acid, whether in the sensitizer or in the developer. Excessive acidification of the developer may carry the danger of bleaching prints, by causing developer acidity to approach that of a clearing bath.
Ammonium citrate was tested with 0, 2, 12, 40, and 100 g/L citric acid added. Potassium oxalate was tested with 0, 1, 6, 20, and 50 g/L oxalic acid added.
CONCLUSIONS: Addition of any reasonable amount of oxalic or citric acid to potassium oxalate or ammonium citrate developer, respectively, will not affect prints in a visible way for developing times of 3 minutes or less. Since a clearing solution of 5% citric acid will begin to bleach prints visibly after between 9 and 24 minutes, some bleaching will occur if a print is immersed for that length of time in a citrate developer containing 50 g/L citric acid (see section 3.3.3). The same result occurs for developing times of 3 minutes or more in an oxalate developer containing 12.5 g/L oxalic acid.
3.2.5 DEVELOPING TIME
A characteristic of platinum printing cited in almost all of the literature is that it is impossible to overdevelop an exposed print. Beyond a certain point, a developer may bleach a print more than it continues to add density.
Ammonium citrate and potassium oxalate were each tested for 0.5, 2, 6, and 20 minutes developing time.
CONCLUSIONS: Exposed paper processed in either 1.67M potassium oxalate or 1.67M ammonium citrate will be completely developed after 30 seconds. No changes in contrast or shadow density will be observed with ammonium citrate for developing times up to 20 minutes. Potassium oxalate will very slightly decrease contrast and shadow density with increased developing time.
3.2.6 COMBINED EFFECTS: DEVELOPER DILUTION AND DEVELOPING TIME
This test was performed to determine the minimum developer dilution and time required to produce complete development when using potassium oxalate.
Dilution and developing time were cross-tested at 0.05, 0.30, 0.82, and 1.73M, and 1, 3, and 8 minutes, respectively.
CONCLUSIONS: Developing in potassium oxalate is complete for developing times greater than 30 seconds at a concentration of 0.30M or stronger. Potassium oxalate in 0.05M solution will not adequately develop prints for any developing time up to 8 minutes. Potassium oxalate will bleach prints at a concentration of 0.05M or higher.
3.3 CLEARING
There are two important considerations in the choice of clearing agent, clearing time, and clearing agent dilution. The first is permanence. The clearing agent must be strong enough and prints immersed long enough so that all iron salts are removed. Unexposed ferric oxalate will darken with further exposure to light and will in time both fog and stain a print; uncleared ferrous oxalate will also stain a print.
The second consideration is bleaching. Whereas platinum is not susceptible to bleaching, palladium is partially dissolved by acid (see section 2.1). Among traditional clearning agents, significant bleaching can occur with hydrochloric acid. Bleaching increases the required exposure time and, more important, gives prints a splotchy appearance. Whether a dilution is too strong or a clearing time too long is different for each clearing agent.
3.3.1 DIFFERENT CLEARING AGENTS
Three clearing agents have been used almost exclusively in the history of platinum and palladium printing: hydrochloric acid, oxalic acid, and citric acid. The first is by far the most common. Oxalic acid is rarely mentioned in current manuals. Many commercially available palladium printing kits now use EDTA tetrasodium, a nonbleaching clearing agent.
Different clearing agents cannot be compared on a simple basis, as developers can. The extent to which bleaching clearing agents will bleach prints depends on the dilution in which they are used and on the length of time for which a print is cleared. Conversely, the variables of time and dilution are almost absent in developing: overdeveloping is impossible, and most developers behave similarly with dilution. Therefore, a test like that performed in section 3.2.1, where different developers were compared, is inconclusive here. This section simply lists different clearing agents that have been used in platinum and palladium printing, together with the dilutions in which they are conventionally prepared (table 2).
TABLE 2 CLEARING AGENTS TESTED
3.3.2 DILUTION OF CLEARING AGENT
Prints were cleared for 3 minutes in each of three baths. Citric acid was tested in 1:19, 1:49, 1:99, and 1:249 dilution. EDTA tetrasodium was tested in 1:22, 1:44, 1:99, and 1:333 dilution. Hydrochloric acid was tested in 1:49, 1:149, 1:399, and 1:999 dilution. After rinsing and drying were complete, prints were exposed for 48 hours to ultraviolet light from a 240W exposure unit, to determine how well cleared they were. This procedure is primitive and does not indicate how the prints will behave over a long period. The result, given here and in section 3.3.4, that all prints appear to have been properly cleared, is not conclusive. Facilities for studying accelerated aging of photographs are required if a better assessment is to be made.
CONCLUSIONS: For 3 minutes of clearning in each of three baths, or 9 minutes total clearing time, only hydrochloric acid in solutions stronger than between 1:49 and 1:149 dilution will bleach prints. Neither citric acid nor EDTA tetrasodium will bleach prints when used in up to 2.5 and 3 times standard concentration, respectively, for this amount of time. All prints were properly cleared.
3.3.3 CLEARING TIME
Standard dilutions of each clearing agent were used. Citric acid, EDTA tetrasodium, hydrochloric acid, and oxalic acid were each tested for 1, 3, 8, and 20 minutes in each of three baths, or 3, 9, 24, and 60 minutes total. Prints were not tested for proper clearing.
CONCLUSIONS: Except for oxalic acid, which bleaches significantly when used for more than between 3 and 9 minutes, clearing agents used in standard dilution produce almost no bleaching. Among the three remaining clearing agents, hydrochloric acid bleaches slightly more than citric acid, and citric acid bleaches slightly more than EDTA tetrasodium, which does not bleach. Extensive bleaching occurred only upon 60 minutes of clearing in 1:149 hydrochloric acid.
3.3.4 COMBINED EFFECTS: CLEARING AGENT DILUTION AND CLEARING TIME
This test was undertaken in order to determine the optimal clearing agent dilution and clearing time for clearing prints thoroughly without bleaching when using a bleaching clearing agent. The test was performed with hydrochloric acid. After clearing, washing, and drying were complete, prints were exposed for 48 hours to ultraviolet light from a 240W exposure unit to determine how well cleared they were.
Dilution and clearing time were cross-tested at 1:49, 1:149, 1:399, and 1:999, and 1, 3, and 8 minutes per bath, or 3, 9, and 24 minutes total, respectively (fig. 2).
Fig. 2.
Prints showing the effects of varying clearing agent dilution and clearing time. (Test performed with hydrochloric acid.) Key: 1. 1:49 dilution, 3 minutes; 2. 1:49 dilution, 9 minutes; 3. 1:49 dilution, 24 minutes; 4. 1:149 dilution, 3 minutes; 5. 1:149 dilution; 9 minutes; 6. 1:149 dilution, 24 minutes; 7. 1:399 dilution, 3 minutes; 8. 1:399 dilution, 9 minutes; 9. 1:399 dilution, 24 minutes; 10. 1:999 dilution, 3 minutes; 11. 1:999 dilution, 9 minutes; 12. 1:999 dilution, 24 minutes
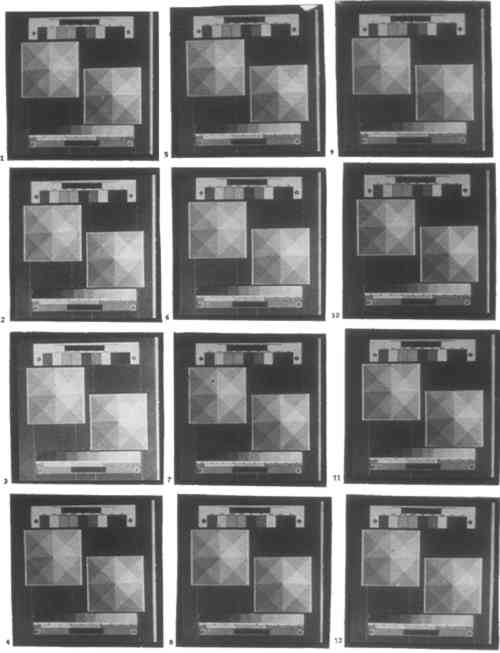 |
CONCLUSIONS: Hydrochloric acid will bleach prints noticeably when used in 1:49 dilution for 3 minutes total clearing time or longer. In 1:149 dilution, it will bleach prints very slightly when used for more than between 9 and 24 minutes. Bleaching action stops at weaker than between 1:149 and 1:399 dilution for total clearing times of 24 minutes or less. Remarkably, a developed print immersed in 1:999 hydrochloric acid for only 3 minutes will be properly cleared.
3.4 ADDITIVES
Additives—small amounts of chemicals that are not essential to the functioning of the platinum and palladium printing process—provide a direct and radical way to affect image contrast, image tone, and paper sensitivity.
Many additives that were popular while the chemistry of platinum printing was being developed, particularly the heavy metal salts lead nitrate, mercuric chloride, and uranyl nitrate, are highly toxic as well as now expensive or difficult to obtain.
The main drawback of most inorganic additives is that once they have been used, brushes, trays, and solutions become instantly if often imperceptibly contaminated. With the exception of aluminum potassium sulfate (alum), chromic potassium sulfate (chrome alum), and sodium carbonate, sizings that have been used with platinum paper are organic and will not interfere with the chemistry of the process.
3.4.1 SIZING
In the 19th and early 20th centuries paper to be used for platinum and palladium printing had to be sized. Sizing prevents the sensitizer from penetrating the paper fibers too deeply, thus yielding a weak image and wasting expensive palladium or platinum. As most papers today are sized by the manufacturer, sizing is now rarely necessary. Nonetheless, sizing affords surprisingly subtle control over image tone.
Three sizing agents have commonly been recommended for platinum and palladium printing: arrowroot, gelatin, and gum arabic. Each was tested. Sizing instructions usually call for the addition of a small amount of ethanol to speed drying. This method is optional and might affect image tone; it was not used. Gelatin solution is strained before using.
Sizing dilutions were arrived at through experimentation: solutions were prepared as concentrated as they could be without making an uneven coat. The concentrations used were arrowroot, 1.4% (w/v); gelatin, 0.66% (w/v); gum arabic, 15% (v/v). Paper was soaked in, rather than coated with, dilute solutions of sizing agent, and sized twice. Between coatings, paper was hung up and allowed to air-dry.
CONCLUSIONS: Among the sizing agents tested, gelatin and gum arabic will affect prints noticeably in the concentration used. Both increase highlight and shadow density equally and so lower contrast; gum arabic also gives prints a slightly warm tone. All effects appear to result from coloration of the paper by the sizing agent rather than from a change in the metal deposit.
3.4.2 ADDITIVES TO SENSITIZER
It is now standard practice to control contrast in platinum and palladium prints by means of additives to the sensitizer. Potassium chlorate is used almost exclusively for this purpose. Many years ago, potassium chlorate in the sensitizer was complemented by potassium dichromate in the developer. Modern platinum and palladium printing manuals consulted say that potassium dichromate cannot be use in palladium printing, as it will cause the image to be bleached upon clearing (Rexroth 1977; Shillea 1986). By contrast, potassium dichromate is mentioned for use specifically with palladium prints by the British Journal of Photography on three occasions (1918a, 1918b, 1921). Both potassium and sodium dichromate were tested as replacements for potassium chlorate in the sensitizer; the literature indicates that counterions other than dichromate will produce different tones. Powdered dichromates are extremely toxic.
Two related and milder oxidants, potassium chromate and potassium bromate, were also tested, as potassium nitrite, which can function as either an oxidizing or a reducing agent and is mentioned in the literature as a developer additive when processing stale paper.
These oxidants are analogous to restrainers in silver chemistry: they increase contrast, lengthen required exposure time, and affect print tone. In platinum and palladium printing, contrast control agents also serve to keep ferric oxalate from being reduced by platinous and palladious chlorides prior to exposure. In the 19th century, toning agents were often incorporated into the sensitizer. Mercuric chloride, for example, was used in commercial sepia platinum papers. These were not tested.
For the reason outlined in section 3.1, solutions were prepared weight-equivalent to 3% (0.24M) potassium chlorate, as follows: potassium bromate, 4.1%; potassium chromate, 4.8%; potassium dichromate, 7.2%; potassium nitrite, 2.1%; sodium dichromate dihydrate, 7.3%. Each additive was tested at 2 drops per coat. Potassium chlorate, potassium dichromate, and potassium nitrite were each further tested at 0, 1, 4, 7, and 12 drops per coat, 6 drops corresponding to the upper limit recommended by current manuals (see section 3.1). In the latter test, comparison among additives is not possible, as the exposure times that were required to enable comparison within each additive's series are different (fig. 3).
Fig. 3.
Prints showing the effects of varying sensitizer additives and the concentration of the additives. Key: 1. potassium bromate, 2 drops; 2. potassium chlorate, 0 drops; 3. potassium chlorate, 1 drop; 4. potassium chlorate, 2 drops; 5. potassium chlorate, 4 drops; 6. potassium chlorate, 7 drops; 7. potassium chlorate, 12 drops; 8. potassium chromate, 2 drops; 9. potassium dichromate, 0 drops; 10. potassium dichromate, 1 drop; 11. potassium dichromate, 2 drops; 12. potassium dichromate, 4 drops
 |
CONCLUSIONS: Of the six additives tested, only potassium chlorate, potassium dichromate, and sodium dichromate are useful for controlling contrast. These additives raise contrast while requiring longer exposure time. When the other three additives tested are used, black shadows cannot be obtained even by overexposure. There was no visible difference in the behaviors of potassium and sodium dichromate. Potassium bromate and potassium chromate are too weak to affect contrast appreciably. Potassium nitrite decreases both contrast and required exposure time and so functions as a reducing agent; it may also make prints cooler in tone. Potassium chlorate has a weaker effect on contrast and exposure time than do the dichromate salts. Remarkably, in contrast to the findings of Shillea (1986), neither potassium chlorate nor either of the dichromates will produce visible graininess when used to excess, up to 12 drops of 0.24M solution. When more than between 4 and 7 drops of either solution are used, even very long exposure times may fail to produce black shadows. Use of dichromate salts in the sensitizer will not cause palladium prints to be bleached upon clearing in hydrochloric acid.
3.4.3 ADDITIVES TO DEVELOPER
Only for the past 50 years has it been standard practice to use contrast-control additives exclusively in the sensitizer. The obvious benefit is that the contrast of an individual print can be controlled more finely while prints prepared and processed alongside it remain unaffected. In the long term, however, additives to the sensitizer will accumulate as an impurity in the developer. Conversely, by using contrast-control agents in the developer, paper that has already been coated can be contrast corrected. These additives can be used to prepare a series of developer having different contrast, much like having graded papers.
The same factors apply to toners and intensifiers in the developer. Given that these are more expensive than contrast control agents, and that it is more wasteful to use additives in the developer than in the sensitizer, their use is costly. Nonetheless, adding just enough toner or intensifier to the developer for one print should not be wasteful. Toners and intensifiers were not tested.
Additive solutions were prepared as in section 3.4.2. Potassium chlorate, potassium dichromate, and potassium nitrite were each tested at 0, 1, 8, and 50 drops per L of potassium oxalate developer.
CONCLUSIONS: The addition of as few as 8 drops of either 3% potassium chlorate or 7.2% potassium dichromate solution to 1 L of standard potassium oxalate developer may visibly raise contrast in a print. The effect remains so subtle that there is no substantial increase in required exposure time when up to 50 drops of additive are used. Potassium nitrite does not have any visible effect at the concentrations tested. The use of potassium dichromate in the developer does not cause bleaching.
3.4.4 TONER AND INTENSIFIER
The only way to change an individual print without at all affecting the chemicals used to process other prints is to tone or intensify it after clearing. While this procedure is not as economical as adding toning agents to the sensitizer, it affords more control because the toning process can be stopped at the desired moment.
A great many toners and intensifiers for platinum and palladium prints were used in the 19th century. As mentioned in section 3.4, most are extremely toxic. The relatively safe toners (gold chloride and ferric ammonium sulfate) and intensifiers (silver nitrate, potassium tetrachloroplatinite, and sodium tetrachloropalladite) require special solvents, developers, and clearing agents, many of which in turn are either mildly or highly toxic. Cupric chloride, a toner used in either the developer or clearing agent, is relatively safe. A toner test was not performed.
3.5 STORAGE
Due to stability problems associated with the paper base, platinum printing has turned out to yield far less permanent photographs than was thought or hoped. The state of old platinum and palladium prints is now of great concern. Investigation into why and how platinum prints deteriorate has been based exclusively on the study of existing prints, most of them several decades old (Rempel 1987; Reilly 1986; Flieder 1985; Norris 1985). The tests described below offer additional insights into the impermanence of platinum and palladium prints.
Unexposed and exposed but unprocessed platinum paper must be stored very carefully, especially the former. Over long periods of time finished platinum and palladium prints also deteriorate. In each case, the envisioned enemies of permanence are moisture, heat, and ultraviolet light. In the case of finished photographs, decay of the paper is also a factor. The decay chemistry peculiar to platinum prints may be related to the handling of the paper before exposure and before processing. Mishandling a platinum print in these stages may visible signs of decay much more rapidly than it will once the print is finished.
To test the often conflicting literature as to how platinum and palladium paper should be handled, the behavior of unexposed and exposed but unprocessed palladium paper was tested over a period of 12 days in a room-temperature, light- and air-tight, but not humidity-controlled, environment.
3.5.1 UNEXPOSED PAPER
Paper was coated, stored for a set period of time before it was exposed, and then processed immediately following exposure. Storage times tested were 0, 1, 6, 18, 48, 96, 168, and 288 hours, measured from the moment paper dried after coating.
CONCLUSIONS: Coated paper that is stored before exposure decreases gradually in contrast. Specifically, shadow density decreases slightly, while highlights darken. This effect begins to be noticeable after between 1 and 6 hours of storage.
3.5.2 EXPOSED BUT UNPROCESSED PAPER
Paper was coated, exposed immediately upon drying, and then stored for a set period of time before it was processed. Storage times tested were 0, 1, 6, 18, 48, 96, 168, and 288 hours, measured from the moment exposure was complete (fig. 4).
Fig. 4.
Prints showing the behavior over time of exposed but unprocessed paper. Key: 1. 0 hours storage; 2. 1 hour storage; 3. 6 hours storage; 4. 18 hours storage; 5. 48 hours storage; 6. 96 hours storage; 7. 168 hours storage; 8. 288 hours storage.
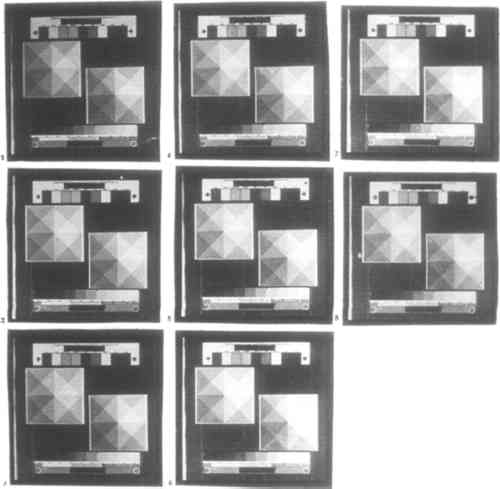 |
CONCLUSIONS: Paper that is stored between exposure and developing increases dramatically in contrast and grain size. Both effects begin to be visible after between 1 and 6 hours of storage. In terms of contrast, shadow density remains constant, while highlights lighten significantly.
This effect begins to reverse, however, after between 4 and 7 days of storage. While grain size does not change, contrast decreases significantly: highlights darken and shadows lighten. Paper that is stored unexposed exhibits the same behavior.
3.5.3 PROCESSED PAPER
Finished photographs have been far more extensively studied than either unexposed or exposed but unprocessed platinum and palladium papers, yet it is in the later group that long-term deterioration of prints can be observed. In most reports, the cause of deterioration of the photograph has been found to be decay of the paper, not of the image. Reilly (1986) cites the following factors: chemicals, notably iron salts and acid, already in the processed paper; the catalytic properties of platinum and to a lesser extent palladium; the absence of a binder layer; the quality of the paper; and exposure to light and chemicals during storage and exhibition. Similar information appears in Rempel (1987), Flieder (1985), and Norris (1985).
4 ANALYSIS OF PLATINUM AND PALLADIUM PHOTOGRAPHS BY ENERGY DISPERSIVE X-RAY SPECTROSCOPY
4.1 APPLICATION OF EDX TO PHOTOGRAPHIC CONSERVATION
Scanning electron microscopy (SEM) with energy-dispersive x-ray analysis (EDX) was used for elemental analysis of photographs. Data were obtained using a JEOL 840 spectro-photometer. Samples equal to or less than the size of the sample cell, 25.4 � 25.4 mm in the present study, can be analyzed by EDX. For this reason, and because it is a destructive technique, EDX can be applied only to small fragments in study collections; at the same time, it is essential to know which print or group of prints a fragment came from.
The scanning electron microscope used with EDX allows very small regions of a sample, for example a visible defect, to be analyzed in addition to the entire sample. Most samples can be analyzed without prior preparation: they are simply taped down onto a graphite disc, usually with both aluminum and copper tape, which serve to calibrate the instrument. Brittle or powdered samples are prepared for analysis by placing them on the graphite disc and overlaying them with an adhesive, such as polymethyl-methacrylate (PMMA), that will not interfere with the analysis.
Currently, the spectroscopic technique most in use in conservation is x-ray fluorescence spectroscopy (XRF). Several authors have compared the benefits of SEM-EDX and XRF (Russ 1971; Gilfrich et al. 1973; Bertin 1975; Jenkins 1976; Whiston 1987; Jenkins 1988). The two technique are comparable, although XRF is more often preferred, especially for its lower cost and nondestructive nature.
4.2 RESULTS OF ANALYSIS BY EDX OF FIVE PHOTOGRAPH FRAGMENTS
Broken fragments from five photographic prints, dating between at least 1870 and 1910, in the study-research collection of the Art Museum, Princeton University, were analyzed by EDX. Pretreatment was not required: the samples were simply taped to a graphite disc as described in section 4.1. Samples are described in table 3; historical information, in some cases inferred, was provided by the museum.
TABLE 3 DESCRIPTION OF PHOTOGRAPH FRAGMENTS
Table 4 shows the elements detected by EDX analysis. Table 5 classifies the elements in table 4 according to their relative abundance in water and the earth's crust. On this basis, the following elements can be said to constitute background noise to any material being analyzed: aluminum, calcium, chlorine, iron, magnesium, manganese, phosphorus, potassium, silicon, sodium, sulfur, zinc, and possibly chromium and nickel. Important nonphotographic sources that may add to this background are photographic paper, desiccants, storage materials, and air.
TABLE 4 EDX ANALYSIS OF IMAGE SURFACES OF FIVE PHOTOGRAPH FRAGMENTS
TABLE 5 BACKGROUND ELEMENTS IN EDX ANALYSIS
In principle, assignment can now be made as to the origin of the elements in each print, using historical and spectroscopic information. For each element shown by EDX to be present, all the chemicals, listed in Gottlieb (1993), that contain that element can be identified. In each case, only the most plausible sources of an element are discussed. Chemicals mentioned frequently in platinum processes are assumed to have also been used in palladium processes, even if never explicitly mentioned for use with palladium.
All samples contain or probably contain the following elements: aluminum or bromine; silicon; lead or sulfur; calcium, indium, or tellurium; iron; copper. These are discounted, as they provide no information particular to any specific sample. On the basis of table 5, peak 1 in table 4 should represent aluminum; peak 4, sulfur; and peak 9, calcium. Given peak 14, peak 16 should represent copper rather than zinc; peak 10, calcium. Elements that cannot be discounted are shown in bold and provide the basis for analysis of the print fragments.
Sample 1 is a palladium print. The presence of chromium (Cr) probably indicates either potassium dichromate, used in the sensitizer or developer as a contrast control agent (of 32 references to chromium in the literature, 23 are as potassium dichromate in the sensitizer or developer), or chromic potassium sulfate, a paper sizing and additive in platinum intensification of silver prints. Table 5 indicates that chromium may also be a background element (Gottlieb 1993). Silver may be present in the sample, which, if positively identified, could indicate either a silver-intensified palladium print or, less likely, a palladium-intensified silver print. Uranium and molybdenum are less probably present; there is a single mention of ammonium molybdate as an ingredient in platinum intensification of silver prints, whereas uranyl nitrate is mentioned frequently as a toner for platinum prints (38 of 56 mentions of uranium). Mercury may be also be present and would probably have come from mercuric chloride in the sensitizer or developer (69 of 100 mentions of mercury).
Sample 2 is a platinum print. The presence of molybdenum and gold is less likely. Palladium is also possibly present; it could indicate a sensitizer containing both platinum and palladium, palladium intensification of a platinum print, or platinum intensification of a palladium print. If the greater permanence of platinum were known at the time, palladium intensification should not have been common. Gold may also be present; gold chloride was a common toner for platinum prints (26 of 38 mentions of gold) as well as an occasional sensitizer ingredient. Chromium may also be present; its likely origins are the same as those discussed for sample 1. The absence of lead and silver possibly dates this print no earlier than 1883, when these metals disappeared from widespread use in the platinum printing process (Gottlieb 1993). Nickel may be a background element and is never mentioned in platinum photography; it is, however, an impurity in unrefined platinum.
Sample 3 is a silver print. Uranium and molybdenum are less probably present. Processes in which the binder is organically based cannot be distinguished from one another by EDX, which cannot verify whether this is an albumen print; visual information is required. The difficult detection of iron and silicon, both certainly present, possibly indicates advanced deterioration of the print. Chromium would not be expected in a silver print. If present, it probably indicates the paper sizing is chromic potassium sulfate, or it is a background element.
Sample 4 is a silver print. Once again, no in organic elements are present that could indicate which process was used to form the image. The discussion of sample 3 applies here as well.
Sample 5 contains both platinum and silver. It is either a platinum-intensified silver print (126 mentions), a silver-intensified platinum print (24 mentions), or a platinum print prepared with silver in the sensitizer (15 mentions). The possible presence of gold does not simplify the choice: as discussed for sample 2, gold could very plausibly have been used to tone or sensitize a platinum print. Combined gold and platinum toning baths for silver prints appear to have been popular in Germany and Great Britain between 1894 and 1902 (Gottlieb 1993). Matte collodion prints, which are silver printed-out images, were typically toned with gold and/or platinum. Mercury may also be present; its likely origins are discussed for sample 1. The possible presence of chlorine and potassium, both generally highly water soluble in ionic form and largely absent from the four other samples, may indicate that this print has been relatively well preserved, at least with respect to moisture.
The paper side of sample 1 was also analyzed by EDX (table 6). Qualitative comparison with, rather than subtraction of, the spectrum from analysis of the image side may provide information about differential absorption of chemicals from the storage environment by paper and by image and about migration of chemicals from the image layer through the paper, either within one print or between adjacent prints stored back-to-front. The two spectra are nearly identical. Questionable peaks for mercury, uranium, and copper in the image are absent in the paper, and the iron peak, certain in the image, is questionable in the paper. All the elements found on the paper surface were also present on the image surface, although possibly not vice versa. As iron is a background element, no meaningful conclusion can be drawn concerning peak 12. As discussed earlier, peaks 5 and 6 together suggest peak 8 in the image sample does not represent uranium. It is interesting to note that mercury, uranium, and copper are all toners for platinum and palladium prints, which, as image-forming substances, would not be expected to migrate.
TABLE 6 EDX ANALYSIS OF IMAGE AND PAPER SURFACES OF ONE PHOTOGRAPH FRAGMENT
5 FUTURE DIRECTIONS
A database of chemicals used in platinum and palladium printing and intensification has been created. Combined with EDX analysis, which elucidates the present elemental composition of a print and so gives clues as to its chemical status, the database can help conservators reconstruct the zero-point of a platinum or palladium print—that is, the chemistry and technique used to create it.
Further literature review could fill out the database. More important, only with further experimentation with EDX can it be known whether the methodology of reconstructing the zero-point is valid and how it can be refined. Likewise, the methodology can be tested in conjunction with either nondestructive (XRF) or more destructive (decomposition followed by ICP or AAS analysis) techniques.
The proposed national conservation resource, including results of literature review as well as data from spectroscopic and chemical analysis of prints, would greatly accelerate the ability to research these questions (Bunnell 1993).
ACKNOWLEDGEMENTS
The author would like to thank Toby Jurovics for his timely assistance.
REFERENCES
Abney, W. de W., and L.Clark. 1898. Platinotype: Its preparation and manipulation. New York: Scovill and Adams.
Bertin, E. P.1975. Principles and practice of x-ray spectrometric analysis. New York: Plenum.
British Journal of Photography. 1873. M. Merget's printing experiments. British Journal of Photography20(689):335.
British Journal of Photography. 1918a. New materials etc. British Journal of Photography65(3019):128.
British Journal of Photography. 1918b. Matt palladiotype. British Journal of Photography65(3023):169–70.
British Journal of Photography. 1921. Meetings of societies. British Journal of Photography68(3198):495.
Bunnell, P.1993. Personal communication. Art Museum, Princeton University, Princeton, N.J. 08544.
Camp, T. R., and R. L.Meserve. 1974. Water and its impurities. Stroudsburg, Pa.: Dowden, Hutchinson and Ross.65.
Dancer, J. B.1856. Chloride of platinum. Humphrey's Journal8(7):112.
Davenport, W. S.1900. The preparation of platinum paper. British Journal of Photography47(2076):376–78.
Flieder, F.1985. Conservation et restauration du patrimoine photographique. Paris: Paris Audiovisuel.
Gilfrich, J. V., et al. 1973. X-ray spectrometry for particulate air pollution. Analytical Chemistry45(12):2002–9.
Gottlieb, A.1993. Chemistry and conservation of platinum and palladium photographs. Senior thesis, Princeton University, Princeton, N.J. 6–42.
Gwenthlian. 1859. The palladium intensifying process. Photographic News2(48):262–63.
Hafey, J., and T.Shillea. 1979. The platinum print. Rochester, N.Y.: Graphic Arts Research Center.
Horsley-Hinton, A.1898. La platinotypie. Paris: Gauthier-Villars et fils.
Jahrbuch f�r Photographie und Reproduktionstechnik. 1903. Platinotypie. Jahrbuch f�r Photographie und Reproduktionstechnik17:545–47.
Jenkins, R.1976. An introduction to x-ray spectrometry. London: Heyden.
Jenkins, R.1988. X-ray fluorescence spectrometry. New York: John Wiley and Sons.
Merck and Co. 1989. The Merck index, 11th ed. Rahway, N.J.: Merck and Co.
Nadeau, L.1986. History and practice of platinum printing, 2d rev. ed.Fredericton, New Brunswick, Canada: published by the author.
Norris, D. H.1985. Platinum photographs: Deterioration and preservation. Photographic Conservation7(2):1.
Photographic Notes. 1856. On toning positives by chloride of platinum. Photographic Notes1(4):23.
Pizzighelli, J.1883. Des �preuves au platine. Bulletin de l'association belge de photographie10(3):119–27.
Pizzighelli, J., and A.Freihern von H�bl. 1886. Platinotype. London: Harrison and Sons.
Reilly, J. M.1986. Care and identification of 19th-century photographic prints. Rochester: Eastman Kodak.
Rempel, S.1987. The care of photographs. New York: Nick Lyons. 57, 66, 71, 83, 137.
Rexroth, N.1977. The platinotype. Yellow Springs, Ohio: Violet Press. 20.
Russ, J. C.1971. Energy dispersion x-ray analysis. Philadelphia: American Society for Testing and Materials.
Shillea, T.1986. Instruction manual for the platinum printing process. Rochester, N.Y.: Thomas John Shillea.
Steinberg, R. J.1992. Palladio instruction manual. Cambridge, Mass.: Palladio Company.
Sullivan, R.1992. Platinum and palladium printing instructions. Los Angeles: Bostick and Sullivan.
Whiston, C.1987. X-ray methods. Chichester: John Wiley and Sons. 300–2.
AUTHOR INFORMATION
ADAM GOTTLIEB is a B.Sc. chemist in environment and photography. This article was written as a senior thesis for the Department of Chemistry at Princeton University in 1993 and was subsequently reviewed by participants at the Stieglitz Colloquy in Washington, D.C. in May 1993. Address: 5035 Parc, Montreal, Quebec, H2V 4E9 Canada.
Section Index |