A PERSPECTIVE ON THE HISTORY OF THE CONSERVATION OF ARCHAEOLOGICAL COPPER ALLOYS IN THE UNITED STATES
TERRY DRAYMAN-WEISSER
2 A HISTORICAL REVIEW
Research for this review began with an examination of the archival materials in the files of the Walters Art Gallery's conservation laboratory, where pertinent correspondence was found dating to 1910. A look at a week's correspondence in December of that year between Henry Walters (fig. 1), two dealers, and the newly appointed director of the Metropolitan Museum of Art, Edward Robinson (an archaeologist by training), demonstrated Walters's concern for his bronzes. It also provided a glimpse at the understanding of and treatment for “bronze disease” at the beginning of this century.
Fig. 1.
Thomas C. Corner, Portrait of Henry Walters, 1938, oil on canvas. 45� � 38� in. Collection of the Walters Art Gallery, acc. no. 37.1682.
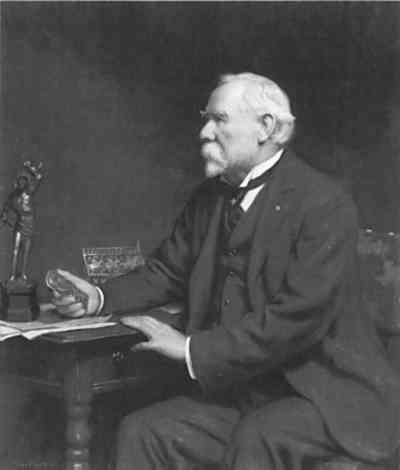 |
On December 6 (Walters correspondence), Walters wrote to Mr. Canessa, a New York dealer, saying:
I have two bronzes which came from Egypt and which have developed a corroding canker. Can you tell me what I should do to stop the eating away of these bronzes? One of these passed through the hands of Andr�1 in Paris, and I am very surprised that the canker should have broken out again.
On December 7 (Walters Correspondence), Canessa answered that he had found no “radical means of stopping a corroding canker which affects especially Egyptian bronzes.” He added that the most lasting method he had found was to rub wax with a small brush on the spot each time the spot reappeared.
On December 8 (Walters Correspondence), Walters wrote to Robinson passing on Canessa's advice and asking for information on Robinson's use of “lime” in display cases (Walters may be confused here since Robinson's reply describes the use of the highly hygroscopic potassium hydroxide, not lime). He also corresponded with another dealer, Mr. Kelekian, then in Paris, saying:
I am sorry to report that an ugly corroding canker has developed on the very fine little sitting figure of “The Athlete,” on the side of the face, and it has already made some inroads. Can you tell me any treatment I can give the bronze which will stop this? The same trouble I find on the bronze “Asp” which came from Mitrahene, and the Metropolitan Museum tell [sic] me …that much trouble of this nature has been found with the bronzes discovered at that place. They consider it due to some composition used in making the bronze.
On December 12 (Walters Correspondence), Robinson responded to Walters's letter of December 8. He warned:
As I told you ancient bronzes require constant watching, whatever treatment they receive to begin with. The main thing seems to be to keep the cases in which they are exhibited perfectly dry after their treatment, and for this purpose we use hydrate of potassium in sticks. These are placed in the bottom of the case in a small cup…. The moisture in the air gradually dissolves the sticks, and they should be renewed as fast as they are dissolved. With us they last from three to six months.
Robinson also enclosed a translation of Andr�'s description of the method by which he treated “diseased” bronzes, which they had been using with success at the Metropolitan for two years. According to the translation supplied by Robinson, Andr�'s method was: (1) to dry out the bronzes for a few days in an oven with “jewelers' sawdust”; (2) to remove the oxide with a needle; (3) to apply a drop of Palestine bitumen; and (4) to wipe off the excess after it had been given time to penetrate.
Correspondence in the files dated 10 years later indicates that Walters was still actively pursuing information on the treatment of bronzes. On May 4, 1923, he filed at the Walters Art Gallery a typewritten preliminary report titled, “Efficient Method for Restoration of Antique Bronzes Badly Corroded or Crusted Over,” written for Robinson by Colin G. Fink, professor of electrochemistry at Columbia University, assisted by Charles H. Eldridge (Fink and Eldridge 1923). The purpose of the study was to find a method for restoring badly corroded ancient bronzes, to determine the cause of “bronze disease,” and to find a simple means for combating it. However, the report, which covers the first four months of work, indicated that the restoration of surfaces was the primary thrust of the project. Fink and Eldridge's report included a discussion of the drawbacks of three treatments in use at the time: (1) the popular method of mechanical cleaning combined with dipping in an acid bath, which they thought too drastic; (2) Friedrich Rathgen's (1905) electrolysis in potassium cyanide solution, which, although an improvement, caused pitting; and (3) the formula of Alexander Scott (1921, 1923) of the British Museum for chemical cleaning, which led to pitting and loss of detail, although they felt it would be satisfactory for high silver alloys.
Fink and Eldridge discussed in detail their own electrolytic method whereby the metal compounds contained in the object's crust were reduced to metal, which was consolidated and hardened while other constituents such as carbonic acid, chlorine, and sulfur were removed. Their method involved an electrolytic bath with the object as cathode packed into fine clean silica sand contained in a porous cell. The cell was placed in a larger container and filled with a 1% solution of sodium hydrate (sodium hydroxide). A low density current was passed through the cell for two weeks or more. They claimed that details were revealed, there was no pitting, and completely corroded sections of the objects were reduced back to metal.
In 1925, Fink and Eldridge published their first report based on the above research. In the introduction, Edward Robinson made an interesting statement that reflects an often heard, but erroneous, belief (Robinson 1925). He stated that “one ‘diseased’ specimen in a show-case may and frequently does infect others.” Robinson also called for the establishment of a national laboratory to assure the highest-quality scientific treatment of artifacts for museums, private collectors, and dealers.
Fink and Eldridge began their book by noting that past treatments had been haphazard and usually secret and that therefore there are few references that give details on cleaning and restoring methods:
It has been unfortunate that men who undertook to clean, repair, and restore usually had no artistic or scientific knowledge or appreciation but were primarily interested in the sum to be realized upon completion of the “cleaning.”
They also stated that the “restorer” almost always tried to bring out details in design and yet not make the object appear to be of recent origin.
Fink and Eldridge set an ambitious treatment goal for themselves:
A really serviceable and generally applicable method of restoration must not be dependent upon differences in composition of the alloy or of the incrustation or patina, but must work well with all; and the resultant product must not leave any doubt in the mind of the restorer that perhaps some other method might have been more satisfactory.
The object of Fink and Eldridge's investigation was to remove the crust and at the same time restore or preserve intact any detail of shape, design, engraving, tool mark, or other signs of workmanship remaining on the specimen.
In support of the uniqueness of their treatment, Fink and Eldridge reviewed the literature and pointed out the differences between their electrolytic method and that of others (Finkener 1905; Frisch 1904; Rocchi 1920). They also mentioned two booklets written in 1921 and 1923 by Alexander Scott, who directed the laboratory at the British Museum after its founding in 1919, and stated that Scott used ordinary chemical methods, not electrolytic treatment, for removing the crust.
The main differences between the Fink and Eldridge electrolytic method proposed in the 1923 preliminary report and the method published in their 1925 book were (1) they no longer recommended packing the object in sand except if there was a danger of the object falling apart; (2) they increased the concentration of the electrolyte from 1% to 2%; and (3) they shortened the length of time required to complete the reduction from several weeks to three or four days.
They dealt with “bronze disease” in a separate section of the book. Although they did not know how “bronze disease” started at any particular spot, they stated that the cause was the presence of a trace of chloride and that the corrosion was primarily electrolytic. For stabilization treatment they recommended their electrolytic method, followed by coating with a mat cellulose acetate lacquer, renewing the coating at least every four years.
On patinating restored bronze surfaces, Fink and Eldridge stated:
The inevitably unlovely appearance of such bronzes after they have been through the treatment for the removal of the ugly crust is a matter of common experience no matter what the method for the removal of the crust has been. Dealers as well as museum authorities, recognizing the fact, have sought to overcome it by supplying an artificial patina, often deceptively successful. There is no doubt that a large percentage of the ancient bronzes in public and private collections have been artificially patinated.
They felt that it was allright to repatinate if it did not damage the bronze and if the patina could be readily removed if desired. One must wonder how they defined “damage” since they reported the best repatination results from a rather aggressive “simultaneous attack of ammonia and acetic acid gas.”
Fink and Eldridge concluded that they met their stated goal. They declared that their electrolytic method is of very general application and could be used with absolute safety in practically all cases of restoration. On April 15, 1925, the New York Times proclaimed in headlines, misquoting the name of the treatment, “Electric Acid Bath Restores Bronzes and Exposes Fakes.” In smaller print it added, “Exhibits in Metropolitan Museum Now are Undergoing the Treatment.” It is easy to see why everyone was so excited about the electrolytic treatment if one compares the before and after treatment photographs of an Egyptian bronze from the Walters collection (figs. 2a and b).
Fig. 2a.
Detail, Isis Nursing the Child Horus, Egyptian, Ptolemaic period (332–30 B.C.), bronze, 7� in. Collection of the Walters Art Gallery, acc. no. 54.792. Before electrolytic treatment.
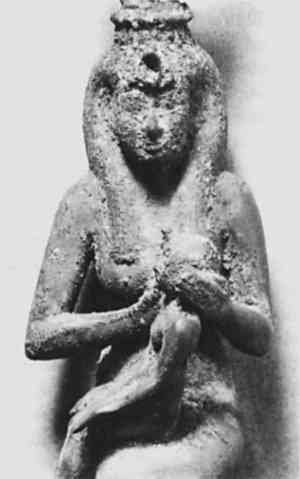 |
Fig. 2b.
Detail, Isis Nursing the Child Horus. After electrolytic treatment by Harold Ellsworth, 1936.
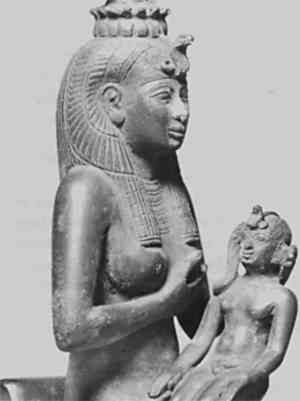 |
Soon after the publication of Fink and Eldridge's book, a conflicting view on appropriate treatment of ancient bronzes appeared. At the death of Major Herbert Garland, superintendent of laboratories at the Citadel in Cairo, his notes were compiled and published (Garland and Bannister 1927). Garland recommended mechanical cleaning with a chisel-ended hammer and avoiding immersion in acid or other liquid. He added that mechanically cleaned bronzes were less likely to corrode again, especially if not handled with “naked fingers” and if impregnated with wax immediately after removal of the crust. If the bronze was not solid, he recommended the use of chemical or electrochemical methods. Garland did mention that German museums were using electrolysis with potassium cyanide and that the leading German authority, Rathgen, painted on Zapon, a solution of nitrated cellulose, after treatment. Garland warned against the inflammability and decomposition of nitrocellulose to liberate free acid. He also implied, as Robinson had, that bronzes can contaminate each other. He wrote, “It is advisable to keep metal objects separate from one another in collections, in order to prevent decay being communicated,” and lamented, “This is not always done in our museums, some of which are very crowded.”
Fink and Eldridge continued to have a major impact on the treatment of bronzes in the United States, although Eldridge's name appears to have been dropped in many later publications and now will be dropped here. Henry W. Nichols (1930), associate curator of geology at Field Museum, Chicago, recommended the Fink electrolytic treatment and advised against even the most minor changes in the method. Nichols had begun to use Fink's method in 1925 to treat the Egyptian collection and between 1926 and 1929 had treated 360 bronzes from Egypt and Mesopotamia. In the foreword to Nichols's book, Berthold Laufer, curator in Field Museum's Department of Anthropology, pronounced that these objects had been returned to their original forms and that “In each and every case the objects … have obtained a new lease on their lives and are permanently preserved” (Laufer 1930). He added, “The advantages accruing to archaeology from this method cannot be overvalued and must be acknowledged with a deep sense of gratitude.” Nichols noted that the technique had two disadvantages: (1) special equipment is needed; and (2) it requires close supervision by “a man skilled in handling antique bronzes and by a skilled chemist.” He also emphasized the need to divide the labor between the chemist who does the electrolysis and the restorer who treats the surface afterward.
Nichols described in detail what he called “cement copper slime,” a form of dark, loosely adhering redeposited copper metal that forms on the surface of the bronze during the electrolytic treatment. He noted that this “cement copper” could be easily removed but is often left on the bronze intentionally to fill in the pits in the surface and to enhance the formation of a patina after the treatment. However, he warned of the possible development of a thin film of adherent bright metallic copper in the position formerly occupied by the original surface of the bronze. He was not certain why this film formed, and he acknowledged that it was difficult or impossible to remove.
Although Nichols strongly supported the use of Fink's electrolytic treatment, in the section of his book about “malignant patina” he described a chemical technique developed at Field Museum. The treatment, which was only for “bronze disease” confined to the surface, involved the application of a dilute solution of sulfate of silver to the affected areas. At the time of publication he could not yet state whether this treatment led to permanent stabilization.
The Fink electrolytic technique was also being employed in the 1930s at the Walters Art Gallery by the chemist, Harold Ellsworth. However, correspondence in the Walters files shows that a problem began to arise with some objects a few years after treatment. Elisabeth Packard, then a conservator at the Walters, wrote to George Stout at the Fogg Museum in January 1940 asking his advice about several ancient bronze statuettes that had been electrolyzed by the Fink method in 1936 (Walters Correspondence). These objects had developed a blue-green excrescence in areas that did not correspond to formerly active areas. Stout spoke with his colleague Rutherford John Gettens about the problem, and Gettens examined a few bronzes at the Fogg that he had treated electrolytically in 1933 or 1934 (Walters Correspondence). He discovered that they, too, had broken out with a blue-green, powdery deposit. He analyzed the material from one of the Walters bronzes and found it to be mainly copper carbonate.2 The blue-green deposit was removed from the Walters bronze, and the object was soaked in changes of distilled water to remove residual chemicals thought to be causing the problem. However, in 1980, the same Walters bronze broke out again with a blue-green product. Another bronze in the collection that had been electrolytically treated in 1936 also recently broke out (figs. 3a, 3b). The product has not yet been analyzed.
Fig. 3a.
Apis, Bull of Memphis, Egyptian, Late Dynastic or Late Period 663–332 B.C., bronze, 7 � 6⅝ in. Collection of the Walters Art Gallery, acc. no. 54.418. After electrolytic treatment by Harold Ellsworth, 1936.
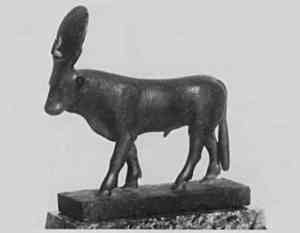 |
Fig. 3b.
Apis, Bull of Memphis. Disfigured by a recent effluorescence of a blue-green product, 1987.
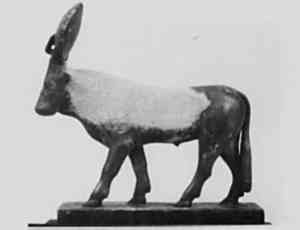 |
British publications on the treatment of antiquities became popular additions to the library at the Walters conservation laboratory and very likely would have been found on the bookshelves of other American conservators. These publications presented a variety of possible treatments for bronzes. Alfred Lucas (1932), chemist in the Department of Antiquities in Egypt, favored chemical treatments. For the treatment of “bronze disease” he recommended sodium sesquicarbonate. To treat heavy corrosion he stated that the whole patina must be removed, and he preferred sulfuric acid for this procedure. He mentioned “electrical” treatments—including Fink's, among others—but he did not appear to encourage their use over chemical methods. He stated that the “aim in cleaning antique objects should be to restore, as far as possible, the original appearance of the object.”
Harold Plenderleith (1934) made a passing reference to the use of the electrolytic method on iron, concluding that “it may on occasion prove useful,” but he did not recommend it in his section on treatment of bronzes. (He did, however, include it in his later publication [Plenderleith 1956].) He preferred electrochemical treatment with zinc and caustic soda, sulfuric acid, or citric acid, in combination with selective mechanical removal of incrustations. He implied that differences had developed between the treatment methods preferred by the Americans and the British when he stated that the electrolytic process “is favored by American workers.” Plenderleith also discussed the cause of “bronze disease,” attributing it to electrochemical reactions in the presence of chloride compounds and moisture, giving rise to light green powdery spots. “How to save a finely patinated bronze when chlorides which exist below the patina have become activated is one of the major problems in the preservation of metal antiquities,” he wrote.
According to Packard, Plenderleith's book quickly became the “Bible” for American conservators (Packard 1993). Also, around this time Joseph Ternbach, who arrived in New York as a refugee from Europe, was impressing dealers and collectors with aesthetically pleasing results from his mechanical cleaning treatments on bronzes (Ternbach 1981). Ternbach spoke about the advantages of mechanical treatment at the American Association of Museums meeting in Boston in 1948 and published an abstract of his paper (Ternbach 1949). (For an example of the detail that can be revealed by careful mechanical cleaning, see figs. 4a, 4b.) These events may help explain why the Fink method began to fall out of favor.
Fig. 4a.
Winged Isis, Egyptian, Late period (663–332 B.C.), bronze, 3� in. Collection of the Walters Art Gallery, acc no. 54.1020. Before mechanical cleaning, 1978.
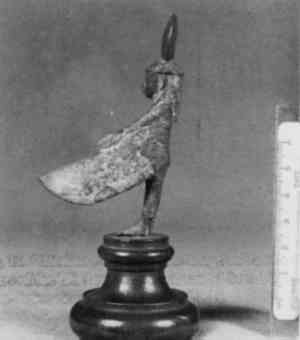 |
Fig. 4b.
Winged Isis. After mechanical cleaning by Helen Ganiaris, 1978.
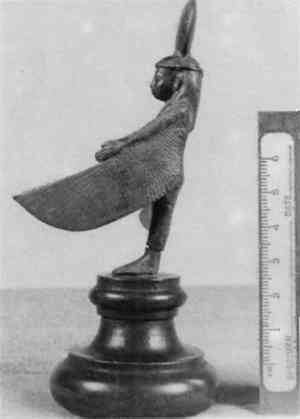 |
All of the above authors seem to agree about two things: that severely or actively corroding bronzes should be stabilized and that the aim of treatment should be to restore the object visually as much as possible to its original state. They showed no interest in preserving corrosion products for other than aesthetic reasons or for corrosion inhibition if the patina is thin and adherent. They did not appear to be concerned that the treatments they recommended change an object's composition by either removing metal ions or adding metals or their salts to the surface as a byproduct of treatment, e.g., redeposited copper with electrolysis and zinc products with electrochemical treatment.
However, some did begin to speak out about the disadvantages of altering the original metal composition and the advantages of preserving the burial patinas and accretions, expressing an attitude more in line with that of the professionally trained conservator today. In a 1935 letter, Earle R. Caley, assistant professor at Princeton University, explained to Robert Garrett, a collector in Baltimore, that he was not currently interested in the “so-called bronze disease” but in the chemical composition of bronzes (Walters Correspondence). He indicated that he had found a correlation between chemical composition and degree of corrosion and that “composition and time of manufacture are related in certain cases, which enable dating of objects to be done objectively from chemical analyses.” He felt that the study of bronze composition would have considerable value for detecting modern forgeries of antique bronzes.
Gettens also expressed his interest in what could be learned from the corrosion products on archaeological bronzes in a letter to Rodney Young of the University of Pennsylvania Museum on April 9, 1959, just before Young was setting off for Turkey (Walters Correspondence). Gettens sought to enlist Young's help in preventing the loss of unusual corrosion products on the bronze objects that were found in the tomb at Gordion:
I hope you can stay the hands of those who want to clean them off before they can be examined properly. The variety of copper corrosion products is most astonishing, and I think merits special study.
Several years later, Hanna Jedrzejewska of the Research Laboratory, Department of Antiquities, National Museum in Warsaw, supported a change in attitude (Jedrzejewska 1964). She made a case for sampling all elements of a bronze that would become changed or destroyed in further treatment and suggested that small areas should be left uncleaned. In another article, she concluded that “cleaning is irreversible.… A lot of harm has already been done … to the documentary evidence” and that uncleaned artifacts should be considered “documents of the past” (Jedrzejewska 1976).
Adding to the argument that bronzes and their patinas should be preserved unaltered were advances in analytical techniques and scientific instrumentation, which made it possible to learn more from a bronze and its accretions than ever before. This development encouraged conservators as well as archaeologists to consider more than just the aesthetic value of the patina and burial deposits. Evidence of other materials—for example, that of textile in contact with bronze during burial—could be studied through their residues preserved in the bronze corrosion layers, (figs. 5a, 5b).
Fig. 5a.
Bowl, Capuan, 6th–5th century B.C., bronze, D 13 ⅝ in. Collection of the Walters Art Gallery, acc. no. 54.144. As received, 1976.
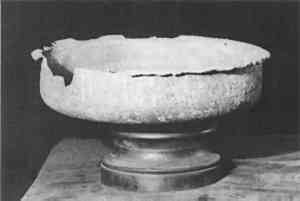 |
Fig. 5b.
Fragment of bowl, Capuan. Evidence of textiles preserved in the corrosion.
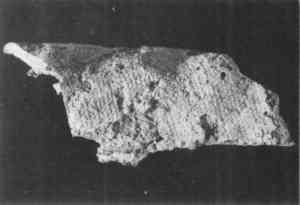 |
Although the ideal conservation method for arresting “bronze disease” while preserving the patina is through control of the environment—for example, creating low relative humidity to inhibit corrosion—realistically, such controls cannot be guaranteed for long-term preservation. A number of treatments have been developed and published in the conservation literature with the stated goal of stabilizing the bronze artifact while preserving its patina. Robert Organ, then at the Research Laboratory of the British Museum, introduced the use of silver oxide for treatment of individual spots of “bronze disease” (Organ 1961) and reintroduced the use of sodium sesquicarbonate for overall stabilization (Organ 1963). According to W. A. Oddy and M. J. Hughes of the British Museum Research Laboratory, bronzes could be stabilized by soaking for prolonged periods in sodium sesquicarbonate, dissolving the chlorides through the patina (Oddy and Hughes 1970). The method is simple, effective, and inexpensive; however, treatment can take over a year to complete, and it was demonstrated that although the sodium sesquicarbonate dissolved the chlorides, it also dissolved metallic copper (Weisser 1975).
H. B. Madsen of the Kalundborg Museum in Denmark introduced the use of benzotriazole for the treatment of “bronze disease” without removing the patina (Madsen 1967). Stabilization could be achieved by soaking a bronze in a dilute solution of benzotriazole for 24 hours. This technique quickly became the favored method due to its simplicity and immediate results. With time it became clear that there were bronzes that could not be stabilized directly with benzotriazole. Such difficult-to-stabilize bronzes can be treated by applying 5% sodium carbonate solution locally, rinsing thoroughly to remove all residues before drying, then treating again with benzotriazole (Weisser 1987). However, this treatment is not always successful or appropriate for all bronzes. Work still must be done to develop reliable methods to stabilize actively corroding bronzes without adversely affecting the core of remaining metal and without altering the patina and burial accretions.
|