EFFECTS OF AGING AND SOLVENT TREATMENTS ON SOME PROPERTIES OF CONTEMPORARY TRACING PAPERS
DIANNE VAN DER REYDEN, CHRISTA HOFMANN, & MARY BAKER
3 PROJECT 1: CHARACTERIZATION OF SELECTED CONTEMPORARY TRACING PAPERS
3.1 RESEARCH PROCEDURES
3.1.1 Method of Sample Papers Selection
Sample papers were selected to represent the various categories of tracing papers, generically referred to by manufacturers as natural, vegetable parchment, imitation parchment, vellum, and prepared tracing papers (table 1). Sealed packages of generic papers were supplied by several proprietors. To aid identification of the papers' furnish and formation, general observations, based on simple examination of the papers such as any conservator might do, have been supplemented by manufacturers' information as well as by analysis at CAL. The findings are noted in the summary of general characterization of selected contemporary tracing papers in table 2. Measurements of properties such as color, opacity, and gloss, were undertaken at CAL to enhance characterization and to provide a standard for comparison of changes in properties occurring as a result of the subsequent aging, solvent, and humidification and flattening projects, as recorded in tables 2–4.
3.1.2 Identification of Materials
GENERAL OBSERVATIONS: As indicated in table 2, general observations were made about fiber type, fiber and sheet processing, translucency, surface gloss, fluorescence, and dimensional stability. These observations were made by subjectively comparing the selected papers, as a conservator might, using relatively simple procedures. For instance, fiber type and processing were characterized using a polarized light microscope. Initial simple subjective comparison of translucency was made using transmitted light, of surface gloss using oblique light, and of fluorescence using long- and short-wave ultraviolet light. Subjective comparison of dimensional stability with regard to planar distortion was made using raking light to observe expansion and cockling of the samples in reaction to a drop of deionized water placed on the surface. For the subjective comparison, descriptors such as high, medium, and low were used. Numerical correlations for these descriptors for translucency and surface gloss may be deduced from the property measurements in the second part of table 2.
MANUFACTURER'S INFORMATION: Manufacturer's information came from supplier's correspondence and brochures about the formation procedures used to make the various papers and about furnish additives used as fillers and sizes, some of which were confirmed by subsequent analysis at CAL.
ANALYSIS: Analysis of formation and furnish of the papers was carried out, as indicated by table 2, using standard equipment and procedures, outlined below.
Scanning Electron Microscopy (SEM): SEM imaging and electron dispersive spectra (SEM/EDS) analysis were carried out on a Jeol JXA-840 a scanning electron microscope with Tracore Northern TN 5502 energy-dispersive x-ray analysis system. For imaging, the samples were mounted on aluminum stubs and gold coated. For elemental analysis, the samples were mounted on carbon stubs and carbon coated.
Fourier Transform Infrared Spectroscopy (FTIR): FTIR analysis was carried out on a Mattson Cygnus 100 Fourier Transform Infrared Spectro-photometer with a Spectratech IR-Plan Microscope. The surfaces of the bulk paper samples were analyzed by reflectance. For transmission spectra, fibers were pressed in a diamond anvil cell. To isolate coatings, samples of the papers were extracted with ethanol, acetone, and toluene; the solvents were evaporated and the residues analyzed by transmission in the diamond cell.
Gas Chromatograph Mass Spectroscopy (GC/MS): Selected samples were hydrolyzed in potassium hydroxide (10% in methanol) neutralized with 3M hydrochloric acid, extracted with diethyl ether, and then taken to dryness in a stream of nitrogen. Samples were redissolved in methylene chloride, and then an equal volume of dimethyl formamide-dimethyl acetal was added to form methyl esters. Each prepared sample was analyzed on a Carlo-Erba model 5360 gas chromatograph with a 30m � 0.32mm DB-1 column. One microliter of the sample plus a comparable volume of methylene chloride was injected. The injector temperature was 300�C. The initial column temperature of 50�C was immediately raised 10�C/min to 320�C. The effluent was detected with a flame ionization detector at 325�C. The chromatograms of the samples and that of standard solution K101 of methyl esters were compared.
3.1.3 Measurement of Properties:
Physical and chemical properties were measured, as noted in table 2, to provide a basis of comparison for the subsequent aging and treatment testing projects (recorded in tables 2–4), using the procedures outlined below.
COLORIMETRY, TRANSMISSION, AND OPACITY: Color (specular reflectance included), total transmission (diffuse plus regular transmission), and opacity were measured with the HunterLab Ultrascan Spectrocolorimeter (D65; 10� observer, diameter of area of view 1.2 in) using the CIE L∗a∗b∗ color notation, where L∗ represents the degree of brightness (100 white, 0 black), a∗ the degree of redness (positive numbers) or the degree of greenness (negative numbers), and b∗ the degree of yellowness (positive numbers) or the degree of blueness (negative numbers). For measurements in color reflectance, the samples were backed by a standard white tile. For transmission measurements of samples for the characterization, aging, and humidification-flattening treatment projects, the samples were suspended between the spherical illumination and the detector (flush with the sphere). For opacity measurements of samples for the characterization and solvent treatment projects, samples were read backed by a white tile and a black tile on the HunterLab Ultrascan Spectrocolorimeter to determine the ratio of reflection.
GLOSS: Gloss was measured with a Dr. Lange Labor-Reflektometer RL at each of the following angles: 20�, 60�, and 85�.
TENSILE STRENGTH: Tensile properties were measured using a Mecklenburg relaxation tensometer (Mecklenburg 1984) with a horizontal load applied in the machine direction to the paper strips. Narrow strips of uniform width (ca. 0.25 in) were cut with a Honeywell Nikor Safety Trimmer. After measurement of the paper thickness in five places with a micrometer, the paper strips were mounted horizontally in the tensometer exposed to laboratory atmosphere (ca. 21�C, 50% RH). After an initial equilibration period at a gauge length of 2.5 in, the strip was stretched 0.0025 in and 1 minute later the stress sustained by the paper strip was recorded. This process was repeated once per minute until the paper strip broke. Measurements were made on three strips of each paper. From these data, nominal stress (force applied per cross-sectional area of the strip) and strain (change in length divided by gauge length) were computed. Nominal stress was plotted as a function of strain for each paper strip. Some of the papers were too strong to be measured using this type of tensometer.
DIMENSIONAL CHANGES: Dimensions of the samples were measured once per sample per experimental procedure in mm (� mm) in both the cross and machine directions of each sample.
pH MEASUREMENTS: The pH was measured with a Corning Model 12 Research pH meter using an Orion model 81–35 flat surface combination electrode to compare differences in relative pH rather than absolute pH. The rinsed electrode, with a drop of deionized water, was held in contact for 5 minutes on a 1.5 � 1.5 cm square, cut from each sample and resting on a polyethylene bag padded with blotters. The electrode was calibrated with pH 7 and pH 4 buffer solutions before each measurement session.
3.2 FINDINGS AND DISCUSSION FOR PROJECT 1
General terms used to describe tracing paper in the conservation literature include transparent paper, translucent paper, oiled paper, onion skin paper, and waxed paper. The U.S. Federal Specifications for Tracing Papers (No. UU-P-561H 1972) recognizes four classifications or types of tracing paper. The four types consist of three classes of 100% rag fiber papers and one class of chemical wood pulp fibers. Each class is required to have its own degree of whiteness, translucency, strength, and permanence. The Federal Specifications also required that the color of the papers not appear changed upon subjective visual comparison following accelerated aging for 72 hours at 100�C, that initial opacity averages 28–70% depending on classification type, that opacity not increase following aging more than 3–7 percentage points for rag papers or 9 percentage points for chemical wood pulp, and finally that fold endurance not drop by more than 50% after aging.
In contrast to the classification system used by the Federal Specifications to group types of tracing papers, commercial manufacturers tend to classify their papers in other ways. Generally, manufacturers categorize such papers in generic groups referred to as natural tracing papers, vegetable parchment papers (genuine parchment paper or Pergamet), imitation parchment papers (Pergamyn or glassine), or prepared tracing or vellum papers (tables 1 and 2). Each of these papers is made by either (1) processing the fibers by overbeating the fiber rawstock pulp slurry, which breaks down fiber structure and reduces porosity, thereby eliminating light scattering air-fiber interfaces, or (2) processing the formed paper sheet to fill such interfaces with material having a refractive index similar to paper fibers. The latter process includes immersion of the paper sheet in acid, calendering of the sheet, or applying a transparentizer (coating or impregnating agents) to the sheet. Fiber processing is the primary procedure used to make natural tracing paper (highly overbeaten pulp), while sheet processing is primary to producing vegetable parchment paper (immersed in acid), imitation parchment paper (highly calendered), or prepared tracing paper or vellum paper (both impregnated with transparentizers). Papers representing each of these categories, selected for the current study, were examined by SEM imaging (van der Reyden et al. 1992a, 1992b), and their general characteristics are outlined in table 2.
The characterizations of the fundamental types of contemporary tracing papers used in our study are based on manufacturers' information (listed in table 2 under “Manufacturer's information”), analysis undertaken at CAL (listed in table 2 under “Analysis”), and a review of the literature (Bolam 1962, 1976; Casey 1980–83; Horie 1987; Kouris 1990; Mosher 1950; Robinson 1980; Roberts 1991; Roth and Weiner 1963; Rundle 1986; Vaurio 1960; Vincent 1932; Yates 1991–92). The papers can generally be described as natural tracings, parchment papers, or papers made with transparentizers (van der Reyden et al. 1992a, 1992b). The following section describes the characteristics generic to natural tracing papers, parchment papers (vegetable and imitation), and papers with transparentizers (vellum and prepared tracing papers), and to the samples used in our study.
Natural tracing paper is usually made from highly overbeaten chemical wood pulp. The natural tracing sample in our study is characteristic in that it is made from chemical wood pulp (bleached kraft) processed by overbeating fibers in a large volume of water (ca. 6% fiber content) at a high temperature (ca. 80�C) to soften the fibers and increase fibrillation and bonding (Bolam 1962, 1976; Robinson 1980). This fiber processing, compounded by machine calendering, results in the total collapse of interfiber pores and voids (fig. 1a) left, making the paper highly translucent, with a relatively matte surface. The natural tracing paper used in this study contains many additives intended to modify various functional properties pertinent to coating processes (such as dispersion, foam control, viscosity adjustment, leveling of wet film and water retention), to printing processes (dry pick, dry rub, wet pick, wet rub, and ink holdout or acceptance), and to special requirements (water and grease resistance, stiffness, folding endurance, gloss, opacity, and color) (Horie 1987; Kouris 1990; Roberts 1991). Additives in CAL's natural tracing sample listed by the manufacturer include sulphamic acid (to control sizing, flocculation, and algae growth during processing); artificial clay (containing magnesium silicate with 6% sodium fluoride); rust inhibitors (polyacrylate and phosphates); and defoaming agents (Yates 1991–92). Foam or bubbles, formed during processing, can be prevented by antifoamers or controlled by defoamers. Early anti- and defoamers included skimmed milk, pine oil, kerosene, animal fat, and vegetable oil. Defoamers, like the blend of hydrocarbon and nonionic emulsifiers used in this sample, are surface-active agents that weaken the walls of small bubbles, causing them to merge into larger ones, which then become buoyant enough to rise to the surface. Saponified oils may serve as antifoamers, defoamers, film levelers, and plasticizers. Talc, also found in this sample, controls pitch from the wood pulp, and along with calcium carbonate and sand, serves also as an extender to reduce the volume of polymer additives, in this case acrylonitrile. Acrylonitrile can increase stiffness and solvent resistance. Butylacrylate can improve aging, smoothness, and brightness. The final paper has a surface size of styrene maleic anhydride compound (that can increase resistance to water, oil, and grease and ensure gloss ink holdout) and modified starch. Starch is modified to improve handling properties by depolymerizing it by enzymes or by hydrolysis and oxidation using chemicals such as sodium hypochlorite and bisulfite, among others (Horie 1987; Roberts 1991).
Fig. 1a.
Scanning electron micrograph showing the top surface and cross-sectioned edge of natural tracing paper, untreated on left side of the photomicrograph and, on the right, treated with acetone applied by suction disk (showing slight expansion in cross-section).
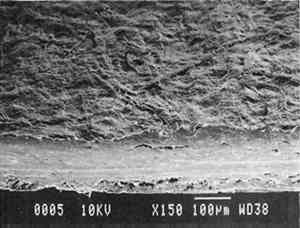 |
Parchment paper is a generic term that can refer to either genuine vegetable parchment paper or to imitation parchment paper. Each is made in distinctly different ways. Genuine vegetable parchment paper is usually made of slightly beaten chemical wood pulp (kraft or sulfate hardwood and softwood in the case of our sample). It is transparentized by momentary immersion in baths of diminishing strengths of acid (such as sulfuric acid for thin paper or zinc chloride for thicker paper), which swell and partially disperse wood fibers, leaching out short chain beta-cellulose and gamma cellulose, forming an amyloid gel. Translucency is achieved when washing and neutralization reconstitutes, solidifies, and reprecipitates the cellulose and gel (Robinson 1980). During drying, the dispersed short chain polysaccharides form membranes that are deposited on and around the remaining fiber structure, effectively dispelling air within the interfiber voids (fig. 1b). This process bonds the fibers into a grease- and solvent-resistant paper having high initial wet strength (Roth and Weiner 1963). The genuine vegetable parchment paper sample characterized in table 2 is coated with silica on one side (fig. 1c) and is recommended by its manufacturer for offset lithography and silk-screen printing.
Fig. 1b.
Scanning electron micrograph showing the top surface and cross-sectioned edge of genuine vegetable parchment paper, untreated
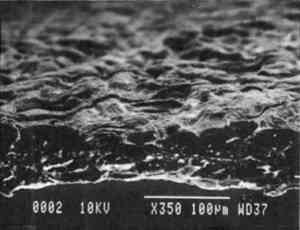 |
Fig. 1c.
SEM/EDS dot map of cross and surface sections of sample 1b showing location of silica (concentrated on back or wire side of sample)
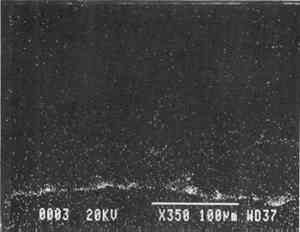 |
Imitation parchment paper, such as glassine (fig. 1d), is made of chemical wood pulp (sulfite) that undergoes prolonged beating (20–30% fiber content in water) to fibrillate and partially “gelatinize” the fibers. Translucency is enhanced when the sheet, dampened to 10–30% moisture content, is supercalendered under high pressure (ca. 2000–3000 lbs/linear in) and heat (surface roll temperature of 180–200�C), generating steam that dries the paper to a 5–7% moisture content and expels air, causing further collapse of the paper structure (Vincent 1932; Rundle 1986). Multi-nip off-machine supercalendering with 14–20 rolls increases the imitation parchment paper's density and gloss, as the paper is pressed and “molded” or “replicated” against smooth iron rolls and less smooth cotton-filled rolls. This process results in “two-sidedness” or different smoothness and optical properties on either side of the paper. The top side tends to be smooth owing to a higher concentration of fines or loading materials that otherwise pass through the wire or underside of the paper, increasing the ratio of fibrous furnish on the underside. Supercalendering imitation parchment paper causes the top side to become highly glazed as fines and filler are molded smooth, while fibers on the underside of the sheet become flattened (Bolam 1962, 1976).
Fig. 1d.
Scanning electron micrograph showing the top surface and cross-sectioned edge of imitation parchment paper, treated by water applied on a suction disk (showing change characteristic of fiber debonding in cross section)
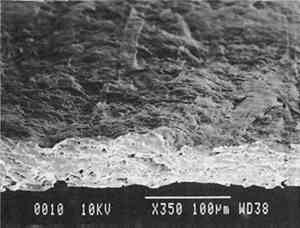 |
Transparentizers are used to make vellum papers, prepared tracing and recently developed “self-healing” tracing papers, all of which are usually made from slightly beaten cotton fibers. The low fibrillation potential of cotton fibers, combined with their twisted structure, prevents close conformation of the fibers, resulting in the scatter of light at the fiber-air interface around voids or pores. To achieve translucency, pores must be filled by impregnation or coating with transparentizers having a refractive index similar to cellulose (Vaurio 1960). Resins are added either to the fiber pulp slurry (wet-end additives) to improve wet and dry strength by preventing water from penetrating and breaking hydrogen bonds and to improve stiffness by increasing adhesion between fibers, or they are added to the surface of the formed paper sheet to improve water and scuff resistance.
Additives in our vellum sample (fig. 1e) include melamine and urea formaldehyde resins, which are formed by creating water-soluble oligomers of formaldehyde combined with melamine or urea, cross-linked by acid catalysts and heat to become hard and stiff. Melamine resins have the greatest chemical resistance to yellowing. Melamine formaldehyde is a wet-end additive that has a good affinity to all papermaking fibers. Urea formaldehyde can be modified with butanol to create organic soluble oligomers that are more flexible than the unmodified polymers, although they can be decomposed by concentrated acids and alkalis. The formaldehyde resins, which require an acid pH on the papermaking machine for reasonable cure rates, also improve dry pick, dry rub, and abrasion resistance.
Fig. 1e.
Scanning electron micrograph showing the top surface and cross-sectioned edge of vellum paper, untreated on left, and, on the right, treated by water applied by a poultice (showing breakup of the coating material)
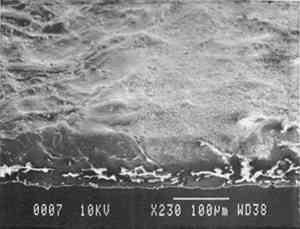 |
Our prepared tracing sample (figs. 2 and 6) has a coating that is pitted by minute air pockets or “pinholes” that may have resulted from foaming of the coating during processing, which can produce gas spheres of air 1–100μm diameter. As mentioned before, surfactant defoamers encourage the bubbles to merge and rise to the top. According to the manufacturer, this paper has been transparentized by an aromatic solvent-based synthetic resin and top coated by styrene and cellulose esters. Esters, formed from organic alcohols and acids, are weakly polar and hydrophilic and provide toughness, clarity, and antistatic properties to coatings. Coatings can be economically thickened with fillers such as precipitated silica and fumed silica, which can also increase strength and hardness and serve as flattening and matting agents. The thickening effect is greatest when the filler is well dispersed in nonpolar solvents for anionic polymers and polyacrylics, which have the best long-term stability. Alkali silicates, among the most common fillers in paper coatings, are made from various proportions of silica sand and soda ash, which are fused and then dissolved in water, forming “water glass.” Silicates are also used for water retention important for “print-on” coating systems. The prepared tracing sample used in this study also has an internal and external size of starch. Recently, continuing developments in paper manufacture have resulted in new categories of tracing papers, including “rag-free” vellum papers and “self-healing” tracing papers made of solvent-based “mobile” transparentizer resins, recommended by manufacturers for diazo copies (Kouris 1990; Roth and Weiner 1963; Yates 1991–92).
Fig. 2a.
Effects of aging on colorimetry measurements: b∗ of CIE L∗a∗b∗, indicating degree of yellowness
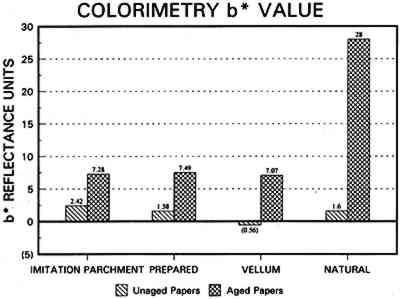 |
Fig. 2b.
Effects of aging on opacity measurements
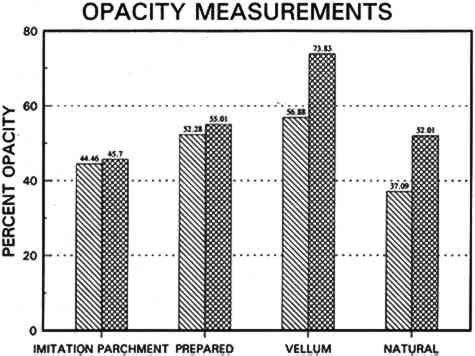 |
Fig. 2c.
Effects of aging on stress-strain measurements comparing natural tracing paper with Whatman paper
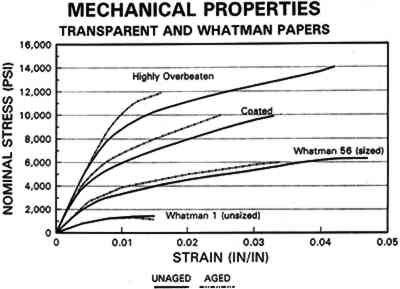 |
Fig. 2d.
Effects of aging on gloss measurements
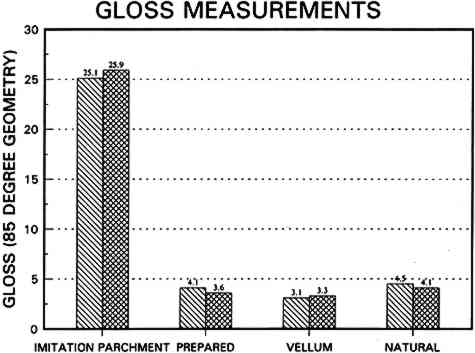 |
Fig. 6a.
Scanning electron micrograph of surface of prepared tracing paper sample, untreated
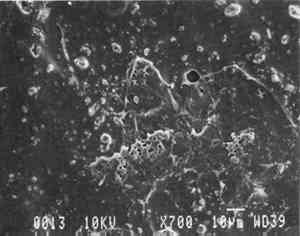 |
Fig. 6b.
Scanning electron micrograph of surface of prepared tracing paper sample, treated by humidification chamber, showing little change
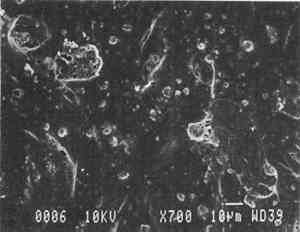 |
Fig. 6c.
Scanning electron micrograph of surface of prepared paper tracing sample, treated by immersion, showing cracking and loss of coating
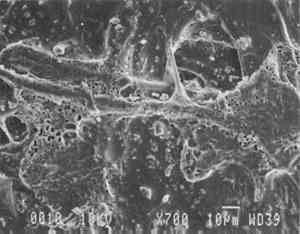 |
Fig. 6d.
Scanning electron micrograph of surface of prepared tracing paper sample, treated by humidification pack, showing loss of coating
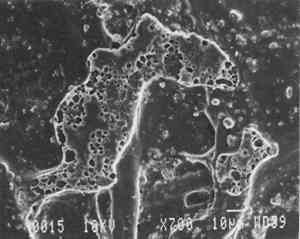 |
3.3 CONCLUSIONS FOR PROJECT 1
Based on manufacturers' information, the literature, and our own findings, there is much variation and overlap in the furnish and formation procedures for contemporary tracing papers (tables 1–2) that can make them difficult to distinguish. However, the furnish, formation, and properties of contemporary tracing papers follow certain trends that are sufficiently different so that conservators may be able to determine, with qualifications, whether a paper is characteristic of a natural tracing paper, a vegetable parchment paper, imitation parchment paper, or prepared or vellum paper. This determination may be done, with varying degrees of accuracy, using several techniques, summarized below, listed in order from simple procedures any conservator could perform to more complex techniques requiring instrumental analysis.
OBSERVATION: observing general appearance (high gloss for calendered imitation parchment paper, high translucency for natural tracing paper, high fluorescence for papers with transparentizers); dimensional stability (greater for coated prepared tracings); reactivity to water (greater for overbeaten natural or imitation parchment papers) or organic solvents (greater for heavily coated prepared tracings); and strength (weaker for overbeaten natural tracings after aging).
ANALYSIS: analyzing fiber content with polarizing light microscope (chemical wood pulp for natural and parchment tracing papers, cotton for prepared tracing papers) or sheet morphology by SEM; analyzing elemental composition using chemical reagents or SEM/EDS, FTIR, or GC/MS. In addition to the more frequently used GC/MS, microtome cross sectioning of samples combined with SEM, FTIR, and UV microscopy appears to have great potential for providing detailed information on composition and distribution of furnish and coating materials in samples.
|