EFFECTS OF AGING AND SOLVENT TREATMENTS ON SOME PROPERTIES OF CONTEMPORARY TRACING PAPERS
DIANNE VAN DER REYDEN, CHRISTA HOFMANN, & MARY BAKER
ABSTRACT�Contemporary tracing papers, also referred to as transparent or translucent papers, are produced by specially formulated furnish compositions and manufacturing formation processes that can make these papers reactive to solvents used in conservation treatments. An initial study to indicate areas of interest for further work was conducted. Four research projects were designed to determine (1) the various compositions and properties, (2) the degradative effects of aging, (3) some effects of solvents and techniques used for stain reduction and (4) humidification and flattening of contemporary tracing papers. Contemporary tracing papers can be characterized as transparentized either by fiber processing (overbeaten natural tracing papers) or by sheet processing, using either acid immersion (vegetable parchment papers); supercalendering (imitation parchment papers); or coating (vellum or prepared tracing papers). Although research is not yet complete, findings for this study indicated that aging resulted in the greatest change in color, opacity, and strength for a natural tracing paper sample, while solvent treatments resulted in the greatest increase in opacity in a prepared tracing paper, and humidification treatments resulted in the greatest gloss, transmission, and dimensional changes in an imitation parchment paper.
1 INTRODUCTION
Tracing papers have been used as the primary supports for a wide variety of materials found in museums, libraries, and archives, such as architectural drawings and fine arts paintings. As supports for architectural drawings and other technical designs, original tracings are frequently handled directly by workers and researchers, since they cannot always be effectively reproduced in photographs, facsimiles, or microfilm. Reproductions may not, for instance, capture faded or smudged media. In addition, reproductions may not clearly replicate subtle but important differences in media that may represent various elements or stages in design, or changes in media such as erasures, that may indicate the evolution of design concepts. Finally, notations in the margins or on the reverse of the drawings are often cropped in reproductions. Tracing papers are also used as supports for paintings by artists attracted by their translucency and relatively low cost. If exhibited, these papers may be damaged not only by handling but also by exhibition conditions. Unfortunately, the composition, size, age, past use, and fragility of tracing papers, compounded by handling and exhibition, makes them particularly susceptible to degradation and thus they frequently require conservation treatment.
Conservation treatment of tracing papers is complicated not only by diverse and sensitive media but also by the very nature of the paper supports. Contemporary tracing papers are produced by specially formulated compositions and manufacturing processes intended to achieve specific chemical and physical properties, such as translucency, whiteness, and smoothness. Special formulations and procedures may, however, render these papers exceptionally susceptible to surface marring, discoloration, and embrittlement. Tracing papers may absorb extraneous material such as adhesives, resulting in embedded stains that are difficult to remove. Often the papers are extremely hygroscopic, which makes them particularly susceptible to planar distortions and dimensional changes. Different manufacturing processes may also render the papers exceptionally sensitive to solvents used in conservation treatments (Baker et al. 1989). A review of the conservation literature indicates that the translucency of tracing papers may be affected by some solvents used for washing or deacidification (Flieder et al. 1988; Glaser 1988; Yates 1984); by consolidation or lining with aqueous, solvent-activated, or thermoplastic adhesives (Bachmann 1983, 1986; Bush 1986; Jirat-Wasiutynski 1980; Hoffenk de Graaff and Wolff 1982; Saucois 1981; Steinkellner 1979; Stone 1987); by stain-removal (Flieder et al. 1991); or by humidification and flattening (Flamm et al. 1990; Hofmann et al. 1992; McClintok 1986; van der Reyden et al. 1992a, 1992b).
To evaluate the effects on tracing papers caused by aging and by various types of solvents and solvent application techniques, several research projects were undertaken. This paper describes first the research design, followed by a separate description of each project with its experimental research procedures (methods and measurements), findings and discussion, and conclusions.1
1 The lack of previous work on this topic made sample choice difficult and made the number of necessary measurement replications for statistical validity unknown. The primary goal, then, was to identify promising areas for future, more in-depth, work, while maintaining a degree of usefulness in the data collected. Therefore, the number of replicates for each measurement varied. In some instances, one measurement of each sample was taken to provide a general overview; in others, multiple measurements were made to determine the significance of the differences seen. The tables of data included provide the number of replications and standard deviation, when calculable, to aid the reader in this determination.
2 RESEARCH DESIGN FOR CONTEMPORARY TRACING PAPER PROJECTS
While there is some conservation literature on the analysis and treatment of historic tracing papers (Flieder et al. 1988; Flamm et al. 1990; Mills 1986; Richardin et al. 1990), less information is available on contemporary tracing papers (Hoffenk de Graaf and Wolff 1982; Rundle 1986; Steinkellner 1979). Since 1987, the Conservation Analytical Laboratory (CAL) has been engaged in research characterizing several types of specialty papers, including coated and transparent or tracing papers, for a twofold purpose (Baker et al. 1989; Mosier et al. 1992; van der Reyden et al. 1992a, 1993a). The first purpose is to enable conservators to categorize, nondestructively if possible, the nature of various types of specialty papers, in order to anticipate potential changes to properties from aging and solvent treatment. The second purpose is to enable conservators to formulate better treatments by selecting solvents and application techniques appropriate to specific types of specialty papers. The ongoing work with respect to tracing papers is divided into four interrelated projects designed to characterize the paper samples (1) before aging, (2) after aging, (3) after solvent treatments, and (4) after humidification and flattening (tables 1�4).
Table 1. Research Design for Contemporary Tracing Papers Projects
 |
Table 2. Summary of Projects 1 and 2: Characterization of Selected Contemporary Tracing Papers and Their Properties Before and After Aging (Na=Not Analyzed)
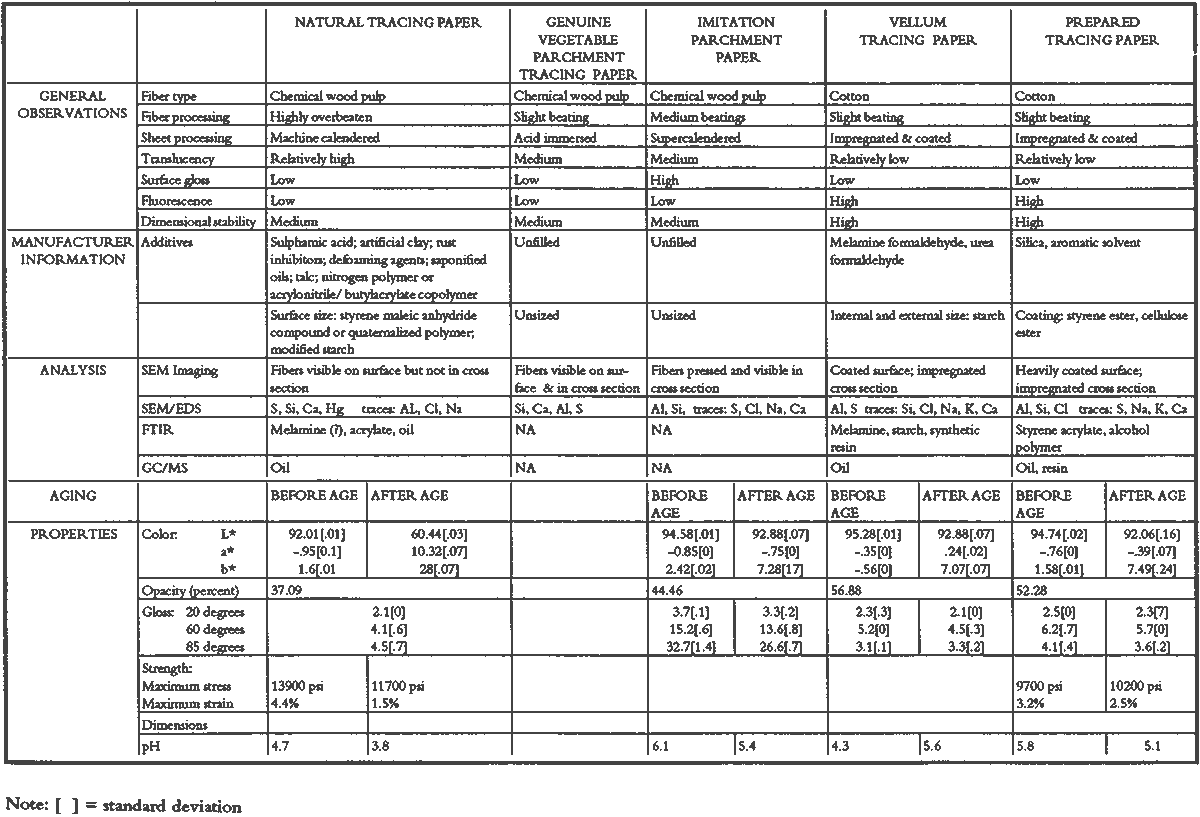 |
Table 3. Summary OF Data for Project 3: Effects of Solvents and Application Technique on Color, Opacity, and Gloss of Selected Contemporary Tracing Papers
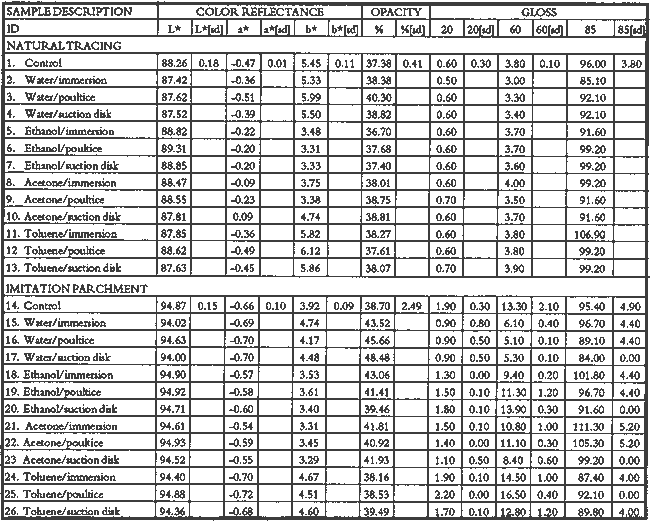 |
Table 3 (continued)
 |
3 PROJECT 1: CHARACTERIZATION OF SELECTED CONTEMPORARY TRACING PAPERS
3.1 RESEARCH PROCEDURES
3.1.1 Method of Sample Papers Selection
Sample papers were selected to represent the various categories of tracing papers, generically referred to by manufacturers as natural, vegetable parchment, imitation parchment, vellum, and prepared tracing papers (table 1). Sealed packages of generic papers were supplied by several proprietors. To aid identification of the papers' furnish and formation, general observations, based on simple examination of the papers such as any conservator might do, have been supplemented by manufacturers' information as well as by analysis at CAL. The findings are noted in the summary of general characterization of selected contemporary tracing papers in table 2. Measurements of properties such as color, opacity, and gloss, were undertaken at CAL to enhance characterization and to provide a standard for comparison of changes in properties occurring as a result of the subsequent aging, solvent, and humidification and flattening projects, as recorded in tables 2�4.
3.1.2 Identification of Materials
GENERAL OBSERVATIONS: As indicated in table 2, general observations were made about fiber type, fiber and sheet processing, translucency, surface gloss, fluorescence, and dimensional stability. These observations were made by subjectively comparing the selected papers, as a conservator might, using relatively simple procedures. For instance, fiber type and processing were characterized using a polarized light microscope. Initial simple subjective comparison of translucency was made using transmitted light, of surface gloss using oblique light, and of fluorescence using long- and short-wave ultraviolet light. Subjective comparison of dimensional stability with regard to planar distortion was made using raking light to observe expansion and cockling of the samples in reaction to a drop of deionized water placed on the surface. For the subjective comparison, descriptors such as high, medium, and low were used. Numerical correlations for these descriptors for translucency and surface gloss may be deduced from the property measurements in the second part of table 2.
MANUFACTURER'S INFORMATION: Manufacturer's information came from supplier's correspondence and brochures about the formation procedures used to make the various papers and about furnish additives used as fillers and sizes, some of which were confirmed by subsequent analysis at CAL.
ANALYSIS: Analysis of formation and furnish of the papers was carried out, as indicated by table 2, using standard equipment and procedures, outlined below.
Scanning Electron Microscopy (SEM): SEM imaging and electron dispersive spectra (SEM/EDS) analysis were carried out on a Jeol JXA-840 a scanning electron microscope with Tracore Northern TN 5502 energy-dispersive x-ray analysis system. For imaging, the samples were mounted on aluminum stubs and gold coated. For elemental analysis, the samples were mounted on carbon stubs and carbon coated.
Fourier Transform Infrared Spectroscopy (FTIR): FTIR analysis was carried out on a Mattson Cygnus 100 Fourier Transform Infrared Spectro-photometer with a Spectratech IR-Plan Microscope. The surfaces of the bulk paper samples were analyzed by reflectance. For transmission spectra, fibers were pressed in a diamond anvil cell. To isolate coatings, samples of the papers were extracted with ethanol, acetone, and toluene; the solvents were evaporated and the residues analyzed by transmission in the diamond cell.
Gas Chromatograph Mass Spectroscopy (GC/MS): Selected samples were hydrolyzed in potassium hydroxide (10% in methanol) neutralized with 3M hydrochloric acid, extracted with diethyl ether, and then taken to dryness in a stream of nitrogen. Samples were redissolved in methylene chloride, and then an equal volume of dimethyl formamide-dimethyl acetal was added to form methyl esters. Each prepared sample was analyzed on a Carlo-Erba model 5360 gas chromatograph with a 30m � 0.32mm DB-1 column. One microliter of the sample plus a comparable volume of methylene chloride was injected. The injector temperature was 300�C. The initial column temperature of 50�C was immediately raised 10�C/min to 320�C. The effluent was detected with a flame ionization detector at 325�C. The chromatograms of the samples and that of standard solution K101 of methyl esters were compared.
3.1.3 Measurement of Properties:
Physical and chemical properties were measured, as noted in table 2, to provide a basis of comparison for the subsequent aging and treatment testing projects (recorded in tables 2�4), using the procedures outlined below.
COLORIMETRY, TRANSMISSION, AND OPACITY: Color (specular reflectance included), total transmission (diffuse plus regular transmission), and opacity were measured with the HunterLab Ultrascan Spectrocolorimeter (D65; 10� observer, diameter of area of view 1.2 in) using the CIE L∗a∗b∗ color notation, where L∗ represents the degree of brightness (100 white, 0 black), a∗ the degree of redness (positive numbers) or the degree of greenness (negative numbers), and b∗ the degree of yellowness (positive numbers) or the degree of blueness (negative numbers). For measurements in color reflectance, the samples were backed by a standard white tile. For transmission measurements of samples for the characterization, aging, and humidification-flattening treatment projects, the samples were suspended between the spherical illumination and the detector (flush with the sphere). For opacity measurements of samples for the characterization and solvent treatment projects, samples were read backed by a white tile and a black tile on the HunterLab Ultrascan Spectrocolorimeter to determine the ratio of reflection.
GLOSS: Gloss was measured with a Dr. Lange Labor-Reflektometer RL at each of the following angles: 20�, 60�, and 85�.
TENSILE STRENGTH: Tensile properties were measured using a Mecklenburg relaxation tensometer (Mecklenburg 1984) with a horizontal load applied in the machine direction to the paper strips. Narrow strips of uniform width (ca. 0.25 in) were cut with a Honeywell Nikor Safety Trimmer. After measurement of the paper thickness in five places with a micrometer, the paper strips were mounted horizontally in the tensometer exposed to laboratory atmosphere (ca. 21�C, 50% RH). After an initial equilibration period at a gauge length of 2.5 in, the strip was stretched 0.0025 in and 1 minute later the stress sustained by the paper strip was recorded. This process was repeated once per minute until the paper strip broke. Measurements were made on three strips of each paper. From these data, nominal stress (force applied per cross-sectional area of the strip) and strain (change in length divided by gauge length) were computed. Nominal stress was plotted as a function of strain for each paper strip. Some of the papers were too strong to be measured using this type of tensometer.
DIMENSIONAL CHANGES: Dimensions of the samples were measured once per sample per experimental procedure in mm (� mm) in both the cross and machine directions of each sample.
pH MEASUREMENTS: The pH was measured with a Corning Model 12 Research pH meter using an Orion model 81�35 flat surface combination electrode to compare differences in relative pH rather than absolute pH. The rinsed electrode, with a drop of deionized water, was held in contact for 5 minutes on a 1.5 � 1.5 cm square, cut from each sample and resting on a polyethylene bag padded with blotters. The electrode was calibrated with pH 7 and pH 4 buffer solutions before each measurement session.
3.2 FINDINGS AND DISCUSSION FOR PROJECT 1
General terms used to describe tracing paper in the conservation literature include transparent paper, translucent paper, oiled paper, onion skin paper, and waxed paper. The U.S. Federal Specifications for Tracing Papers (No. UU-P-561H 1972) recognizes four classifications or types of tracing paper. The four types consist of three classes of 100% rag fiber papers and one class of chemical wood pulp fibers. Each class is required to have its own degree of whiteness, translucency, strength, and permanence. The Federal Specifications also required that the color of the papers not appear changed upon subjective visual comparison following accelerated aging for 72 hours at 100�C, that initial opacity averages 28�70% depending on classification type, that opacity not increase following aging more than 3�7 percentage points for rag papers or 9 percentage points for chemical wood pulp, and finally that fold endurance not drop by more than 50% after aging.
In contrast to the classification system used by the Federal Specifications to group types of tracing papers, commercial manufacturers tend to classify their papers in other ways. Generally, manufacturers categorize such papers in generic groups referred to as natural tracing papers, vegetable parchment papers (genuine parchment paper or Pergamet), imitation parchment papers (Pergamyn or glassine), or prepared tracing or vellum papers (tables 1 and 2). Each of these papers is made by either (1) processing the fibers by overbeating the fiber rawstock pulp slurry, which breaks down fiber structure and reduces porosity, thereby eliminating light scattering air-fiber interfaces, or (2) processing the formed paper sheet to fill such interfaces with material having a refractive index similar to paper fibers. The latter process includes immersion of the paper sheet in acid, calendering of the sheet, or applying a transparentizer (coating or impregnating agents) to the sheet. Fiber processing is the primary procedure used to make natural tracing paper (highly overbeaten pulp), while sheet processing is primary to producing vegetable parchment paper (immersed in acid), imitation parchment paper (highly calendered), or prepared tracing paper or vellum paper (both impregnated with transparentizers). Papers representing each of these categories, selected for the current study, were examined by SEM imaging (van der Reyden et al. 1992a, 1992b), and their general characteristics are outlined in table 2.
The characterizations of the fundamental types of contemporary tracing papers used in our study are based on manufacturers' information (listed in table 2 under �Manufacturer's information�), analysis undertaken at CAL (listed in table 2 under �Analysis�), and a review of the literature (Bolam 1962, 1976; Casey 1980�83; Horie 1987; Kouris 1990; Mosher 1950; Robinson 1980; Roberts 1991; Roth and Weiner 1963; Rundle 1986; Vaurio 1960; Vincent 1932; Yates 1991�92). The papers can generally be described as natural tracings, parchment papers, or papers made with transparentizers (van der Reyden et al. 1992a, 1992b). The following section describes the characteristics generic to natural tracing papers, parchment papers (vegetable and imitation), and papers with transparentizers (vellum and prepared tracing papers), and to the samples used in our study.
Natural tracing paper is usually made from highly overbeaten chemical wood pulp. The natural tracing sample in our study is characteristic in that it is made from chemical wood pulp (bleached kraft) processed by overbeating fibers in a large volume of water (ca. 6% fiber content) at a high temperature (ca. 80�C) to soften the fibers and increase fibrillation and bonding (Bolam 1962, 1976; Robinson 1980). This fiber processing, compounded by machine calendering, results in the total collapse of interfiber pores and voids (fig. 1a) left, making the paper highly translucent, with a relatively matte surface. The natural tracing paper used in this study contains many additives intended to modify various functional properties pertinent to coating processes (such as dispersion, foam control, viscosity adjustment, leveling of wet film and water retention), to printing processes (dry pick, dry rub, wet pick, wet rub, and ink holdout or acceptance), and to special requirements (water and grease resistance, stiffness, folding endurance, gloss, opacity, and color) (Horie 1987; Kouris 1990; Roberts 1991). Additives in CAL's natural tracing sample listed by the manufacturer include sulphamic acid (to control sizing, flocculation, and algae growth during processing); artificial clay (containing magnesium silicate with 6% sodium fluoride); rust inhibitors (polyacrylate and phosphates); and defoaming agents (Yates 1991�92). Foam or bubbles, formed during processing, can be prevented by antifoamers or controlled by defoamers. Early anti- and defoamers included skimmed milk, pine oil, kerosene, animal fat, and vegetable oil. Defoamers, like the blend of hydrocarbon and nonionic emulsifiers used in this sample, are surface-active agents that weaken the walls of small bubbles, causing them to merge into larger ones, which then become buoyant enough to rise to the surface. Saponified oils may serve as antifoamers, defoamers, film levelers, and plasticizers. Talc, also found in this sample, controls pitch from the wood pulp, and along with calcium carbonate and sand, serves also as an extender to reduce the volume of polymer additives, in this case acrylonitrile. Acrylonitrile can increase stiffness and solvent resistance. Butylacrylate can improve aging, smoothness, and brightness. The final paper has a surface size of styrene maleic anhydride compound (that can increase resistance to water, oil, and grease and ensure gloss ink holdout) and modified starch. Starch is modified to improve handling properties by depolymerizing it by enzymes or by hydrolysis and oxidation using chemicals such as sodium hypochlorite and bisulfite, among others (Horie 1987; Roberts 1991).
Fig. 1a.
Scanning electron micrograph showing the top surface and cross-sectioned edge of natural tracing paper, untreated on left side of the photomicrograph and, on the right, treated with acetone applied by suction disk (showing slight expansion in cross-section).
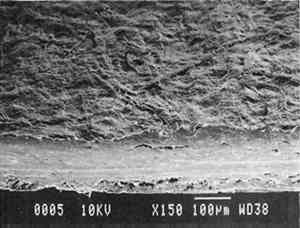 |
|
Fig. 1d.
Scanning electron micrograph showing the top surface and cross-sectioned edge of imitation parchment paper, treated by water applied on a suction disk (showing change characteristic of fiber debonding in cross section)
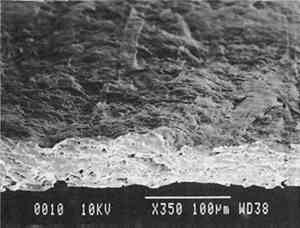 |
|
Fig. 1b.
Scanning electron micrograph showing the top surface and cross-sectioned edge of genuine vegetable parchment paper, untreated
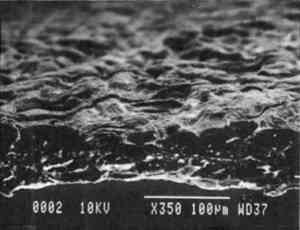 |
|
Fig. 1e.
Scanning electron micrograph showing the top surface and cross-sectioned edge of vellum paper, untreated on left, and, on the right, treated by water applied by a poultice (showing breakup of the coating material)
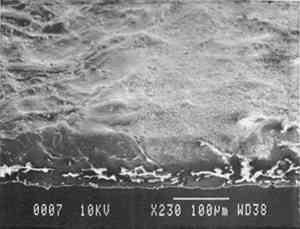 |
|
Fig. 1c.
SEM/EDS dot map of cross and surface sections of sample 1b showing location of silica (concentrated on back or wire side of sample)
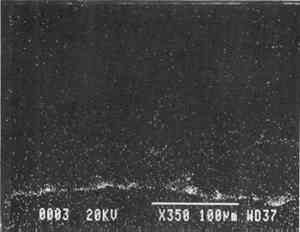 |
|
Fig. 1f.
SEM/EDS dot map of cross and surface sections of sample 1e showing location of silica (concentrated in treated area)
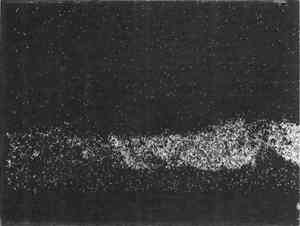 |
|
Parchment paper is a generic term that can refer to either genuine vegetable parchment paper or to imitation parchment paper. Each is made in distinctly different ways. Genuine vegetable parchment paper is usually made of slightly beaten chemical wood pulp (kraft or sulfate hardwood and softwood in the case of our sample). It is transparentized by momentary immersion in baths of diminishing strengths of acid (such as sulfuric acid for thin paper or zinc chloride for thicker paper), which swell and partially disperse wood fibers, leaching out short chain beta-cellulose and gamma cellulose, forming an amyloid gel. Translucency is achieved when washing and neutralization reconstitutes, solidifies, and reprecipitates the cellulose and gel (Robinson 1980). During drying, the dispersed short chain polysaccharides form membranes that are deposited on and around the remaining fiber structure, effectively dispelling air within the interfiber voids (fig. 1b). This process bonds the fibers into a grease- and solvent-resistant paper having high initial wet strength (Roth and Weiner 1963). The genuine vegetable parchment paper sample characterized in table 2 is coated with silica on one side (fig. 1c) and is recommended by its manufacturer for offset lithography and silk-screen printing.
Imitation parchment paper, such as glassine (fig. 1d), is made of chemical wood pulp (sulfite) that undergoes prolonged beating (20�30% fiber content in water) to fibrillate and partially �gelatinize� the fibers. Translucency is enhanced when the sheet, dampened to 10�30% moisture content, is supercalendered under high pressure (ca. 2000�3000 lbs/linear in) and heat (surface roll temperature of 180�200�C), generating steam that dries the paper to a 5�7% moisture content and expels air, causing further collapse of the paper structure (Vincent 1932; Rundle 1986). Multi-nip off-machine supercalendering with 14�20 rolls increases the imitation parchment paper's density and gloss, as the paper is pressed and �molded� or �replicated� against smooth iron rolls and less smooth cotton-filled rolls. This process results in �two-sidedness� or different smoothness and optical properties on either side of the paper. The top side tends to be smooth owing to a higher concentration of fines or loading materials that otherwise pass through the wire or underside of the paper, increasing the ratio of fibrous furnish on the underside. Supercalendering imitation parchment paper causes the top side to become highly glazed as fines and filler are molded smooth, while fibers on the underside of the sheet become flattened (Bolam 1962, 1976).
Transparentizers are used to make vellum papers, prepared tracing and recently developed �self-healing� tracing papers, all of which are usually made from slightly beaten cotton fibers. The low fibrillation potential of cotton fibers, combined with their twisted structure, prevents close conformation of the fibers, resulting in the scatter of light at the fiber-air interface around voids or pores. To achieve translucency, pores must be filled by impregnation or coating with transparentizers having a refractive index similar to cellulose (Vaurio 1960). Resins are added either to the fiber pulp slurry (wet-end additives) to improve wet and dry strength by preventing water from penetrating and breaking hydrogen bonds and to improve stiffness by increasing adhesion between fibers, or they are added to the surface of the formed paper sheet to improve water and scuff resistance.
Additives in our vellum sample (fig. 1e) include melamine and urea formaldehyde resins, which are formed by creating water-soluble oligomers of formaldehyde combined with melamine or urea, cross-linked by acid catalysts and heat to become hard and stiff. Melamine resins have the greatest chemical resistance to yellowing. Melamine formaldehyde is a wet-end additive that has a good affinity to all papermaking fibers. Urea formaldehyde can be modified with butanol to create organic soluble oligomers that are more flexible than the unmodified polymers, although they can be decomposed by concentrated acids and alkalis. The formaldehyde resins, which require an acid pH on the papermaking machine for reasonable cure rates, also improve dry pick, dry rub, and abrasion resistance.
Our prepared tracing sample (figs. 2 and 6) has a coating that is pitted by minute air pockets or �pinholes� that may have resulted from foaming of the coating during processing, which can produce gas spheres of air 1�100μm diameter. As mentioned before, surfactant defoamers encourage the bubbles to merge and rise to the top. According to the manufacturer, this paper has been transparentized by an aromatic solvent-based synthetic resin and top coated by styrene and cellulose esters. Esters, formed from organic alcohols and acids, are weakly polar and hydrophilic and provide toughness, clarity, and antistatic properties to coatings. Coatings can be economically thickened with fillers such as precipitated silica and fumed silica, which can also increase strength and hardness and serve as flattening and matting agents. The thickening effect is greatest when the filler is well dispersed in nonpolar solvents for anionic polymers and polyacrylics, which have the best long-term stability. Alkali silicates, among the most common fillers in paper coatings, are made from various proportions of silica sand and soda ash, which are fused and then dissolved in water, forming �water glass.� Silicates are also used for water retention important for �print-on� coating systems. The prepared tracing sample used in this study also has an internal and external size of starch. Recently, continuing developments in paper manufacture have resulted in new categories of tracing papers, including �rag-free� vellum papers and �self-healing� tracing papers made of solvent-based �mobile� transparentizer resins, recommended by manufacturers for diazo copies (Kouris 1990; Roth and Weiner 1963; Yates 1991�92).
Fig. 2a.
Effects of aging on colorimetry measurements: b∗ of CIE L∗a∗b∗, indicating degree of yellowness
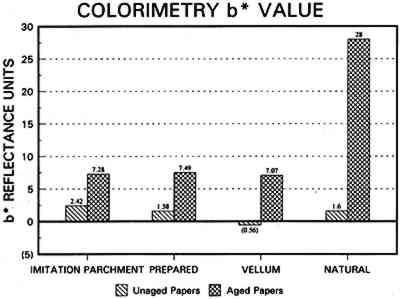 |
Fig. 2b.
Effects of aging on opacity measurements
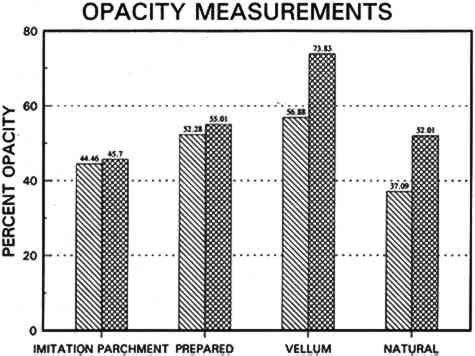 |
Fig. 2c.
Effects of aging on stress-strain measurements comparing natural tracing paper with Whatman paper
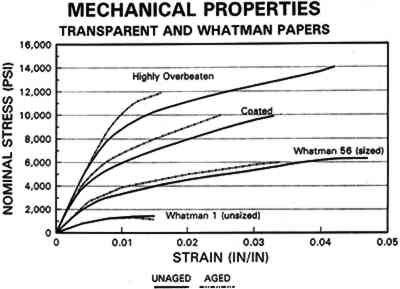 |
Fig. 2d.
Effects of aging on gloss measurements
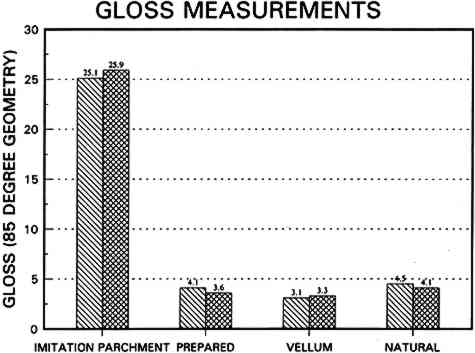 |
Fig. 6a.
Scanning electron micrograph of surface of prepared tracing paper sample, untreated
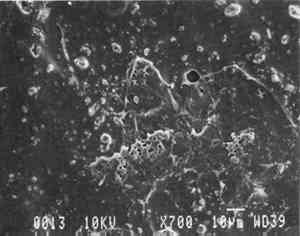 |
Fig. 6b.
Scanning electron micrograph of surface of prepared tracing paper sample, treated by humidification chamber, showing little change
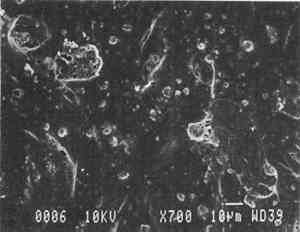 |
Fig. 6c.
Scanning electron micrograph of surface of prepared paper tracing sample, treated by immersion, showing cracking and loss of coating
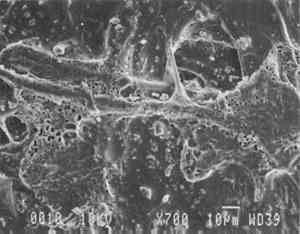 |
Fig. 6d.
Scanning electron micrograph of surface of prepared tracing paper sample, treated by humidification pack, showing loss of coating
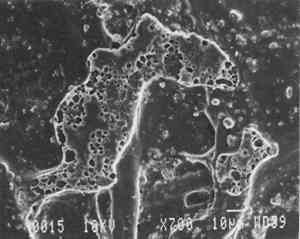 |
3.3 CONCLUSIONS FOR PROJECT 1
Based on manufacturers' information, the literature, and our own findings, there is much variation and overlap in the furnish and formation procedures for contemporary tracing papers (tables 1�2) that can make them difficult to distinguish. However, the furnish, formation, and properties of contemporary tracing papers follow certain trends that are sufficiently different so that conservators may be able to determine, with qualifications, whether a paper is characteristic of a natural tracing paper, a vegetable parchment paper, imitation parchment paper, or prepared or vellum paper. This determination may be done, with varying degrees of accuracy, using several techniques, summarized below, listed in order from simple procedures any conservator could perform to more complex techniques requiring instrumental analysis.
OBSERVATION: observing general appearance (high gloss for calendered imitation parchment paper, high translucency for natural tracing paper, high fluorescence for papers with transparentizers); dimensional stability (greater for coated prepared tracings); reactivity to water (greater for overbeaten natural or imitation parchment papers) or organic solvents (greater for heavily coated prepared tracings); and strength (weaker for overbeaten natural tracings after aging).
ANALYSIS: analyzing fiber content with polarizing light microscope (chemical wood pulp for natural and parchment tracing papers, cotton for prepared tracing papers) or sheet morphology by SEM; analyzing elemental composition using chemical reagents or SEM/EDS, FTIR, or GC/MS. In addition to the more frequently used GC/MS, microtome cross sectioning of samples combined with SEM, FTIR, and UV microscopy appears to have great potential for providing detailed information on composition and distribution of furnish and coating materials in samples.
4 PROJECT 2: EFFECTS OF ACCELERATED AGING ON SELECTED CONTEMPORARY TRACING PAPERS
4.1 RESEARCH PROCEDURES
4.1.1 Method of Aging
Samples of all the papers were subjected to accelerated aging for 4 weeks in the dark at 90�C and 50% RH in an Associated Environmental Systems HK-4116 Temperature/Humidity chamber. These conditions have been chosen as suitable for artificial aging studies (Erhardt 1988). Sets of transparent papers were sewn with cotton thread into Plexiglas frames so that all four corners were anchored and the samples did not touch one another, although the samples did vibrate in the oven draft.
4.1.2 Measurement of Properties
Evaluation of the effects of accelerated aging on the properties of the papers (except the vegetable parchment paper, which is still being tested) was undertaken by measuring changes after aging in color, opacity, gloss, mechanical strength, and pH, using the apparatus and systems outlined previously (table 2 and section 3.1.3).
4.2 FINDINGS AND DISCUSSION FOR PROJECT 2
As noted previously (section 3.2), U.S. Federal Specifications for Tracing Papers (No. UU-P-561H 1972) uses dry oven accelerated aging at 100�C for 72 hours. Our accelerated aging conditions of 90�C, 50% RH for 4 weeks employs higher humidity levels and longer exposure times that may engender more extensive hydrolysis and oxidation. This effect may account for the change, exceeding the Federal Specifications, that occurred in some properties of some of the samples tested under our more severe conditions (van der Reyden et al. 1992a, 1992b).
Following aging at 90�C, 50% RH for 4 weeks, all the papers underwent subjective and measurable change in color (fig. 2a). Opacity increase exceeded the Federal specification of 9 percentage points for the chemical pulp natural tracing paper and 3�7 percentage points for the rag pulp vellum sample (fig. 2b). Mechanical properties, as measured by tensile strain to break, decreased considerably for the natural tracing paper (fig. 2c). Accelerated aging appeared to have less effect on gloss (fig. 2d).
The natural tracing paper sample showed the greatest change in CIE L∗a∗b∗ values under our conditions, perhaps because of the sulphamic acid used during processing or the modified starch added to surface sizing. The natural tracing paper also underwent the greatest increase in opacity. With regard to strength, the tracing papers that could be measured had far greater strength than paper processed the standard way, possibly as a result of a combination of exceptionally strong sizes, coatings, and impregnants and overbeating. After accelerated aging, these papers underwent a reduction in elongation and tensile energy absorption (TEA) characteristic of embrittlement, perhaps from a breakdown in sizing and coating material. In addition, overbeating, as in the case of the natural tracing sample, which is responsible for substantial increases in strength before aging, may also result in a decrease in strength after aging, since the process produces shorter fibers and weakens fibrillar attachment (Yates 1991�92). The pH of all but one of the papers dropped after accelerated aging. The pH of the natural tracing sample paper, which was already acidic at 4.7, dropped to 3.8 after aging, as did the pH of the imitation parchment (from 6.1 to 5.4) and the prepared tracing (from 5.8 to 5.1). The vellum paper sample had a pH (4.3), which increased after aging (5.6).
4.3 CONCLUSIONS FOR PROJECT 2
Accelerated aging under the conditions used for this project caused dramatic differences in the properties of all the samples (table 2), sometimes in excess of the standards considered acceptable by the U.S. Federal Specifications for Tracing Papers (UU-P-561H 1972). There were significant differences in mechanical properties, before and after aging, depending on whether the samples were transparentized by overbeating or by transparentizing agents (fig. 2). In general, the heavily coated transparent paper samples seem to have better retention of optical and strength properties and dimensional stability after aging as compared with the overbeaten natural transparent and imitation parchment paper samples (van der Reyden et al. 1992a, 1992b).
5 PROJECT 3: EFFECTS OF SOLVENTS AND APPLICATION TECHNIQUES ON SELECTED CONTEMPORARY TRACING PAPERS
5.1 RESEARCH PROCEDURES
5.1.1 Solvent Treatment Methods
As shown in table 1, four solvents (water, ethanol, acetone, and toluene) were applied by three techniques (immersion, poultice, and suction disk) to each sample of paper using the following techniques.
IMMERSION TECHNIQUE: For the immersion technique, a 150 square mm section of each sample was dipped into a 3 ml solution of solvent and held there for 3 seconds. The sample was then allowed to air-dry.
POULTICE TECHNIQUE: The poultice technique consisted of placing diatomaceous earth saturated by solvent (0.3 gm diatomaceous earth to approximately 1�2 ml solvent, depending on solvent) on the front of each paper sample lying on a nonabsorbent support.2 The poultice covered an area approximately 5mm in diameter, and, contrary to normal practice, the wet poultice was not surrounded by dry poultice to diffuse the transition from wet to dry areas. The poultice was allowed to air-dry before being removed by an air bulb and brushing.
2 Diatomaceous earth (hydrated silica from diatom plant skeletons) was selected as a poultice for its working properties since, unlike gel poultices (methylcellulose, agarose, starch paste, or hydroxypropylethylcellulose) it can be mixed with aqueous or nonaqueous solvents to form a plaster or paste that absorbs solutes as it dries to a powder, which can then be brushed off. It is more cohesive than fused silica. It is whiter than Fuller's earth, which is formed from hydrated silicates of magnesium, calcium, aluminum, or other metals. It is more controllable than organic solid poultices such as powdered cellulose, paper, or cotton.
SUCTION DISK TECHNIQUE: The suction disk technique consisted of applying three drops of each solvent locally by dropper on a 15 cm fritted glass bead disk (masked off with polyester film), reaching an optimum pressure of ca. 25 in Hg.
5.1.2 Measurement of Properties
Evaluation of the effects of solvents and application techniques on tracing papers included measurement of properties (table 3), as outlined in section 3.1.3, as well as subjective observation of overall appearance (color, opacity, and gloss) in visible and ultraviolet light, and tracking dislocation of furnish materials by SEM and UV microscopy.
5.2 FINDINGS AND DISCUSSION FOR PROJECT 3
Aqueous and nonaqueous solvents are used in conservation treatments of tracing papers to aid in the removal of adhesives and stains, and in humidification prior to flattening. Solvents may also interact, however, with the special additives and morphologies characteristic of tracing papers. For example, water, ethanol, toluene, or acetone may affect the morphology of coatings and impregnants used to transparentize tracings by causing crazing or dissolution of the polymeric films. This effect in turn increases permeability, enabling the solvents to affect the morphology of the paper structure itself by debonding, swelling, and altering the porosity (and thereby the translucency) of the paper. The nature of the interaction of the solvent with the paper substrate is determined by several factors, and a review of a few of these might aid in interpreting the findings of this project. For example, the degree of interaction is affected by the solvent solubility parameters. On the other hand, the speed of interaction may be dictated by structure and evaporation rate of the solvents. Some solubility and evaporation rate parameters for the solvents used in this project are summarized in table 5.
Table 5. Some Properties of Selected Solvents
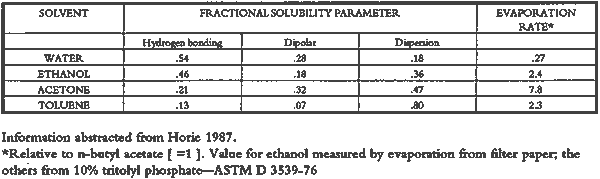 |
The effect of solvents on paper composition may also be influenced by how long a solvent is retained in a paper. Solvents retained in coating films may change the dimensional or chemical stability of a film. The retention time may be influenced not only by the evaporation rate but also by the solvent structure, concentration, temperature, ambient RH, and paper porosity. Depending on solvent molecular structure and shape, for example, water, ethanol, acetone, and toluene would have respectively increasing solvent retention times, since small solvent molecules that are linear, unbranched, and symmetrical (like water) can pass more easily between polymer molecules than solvents that are larger or branched. However, the speed of evaporation can reduce the normal retention time, so that, acetone for example may be removed from paper faster than water and ethanol, even though it is a larger molecule. Likewise, toluene is removed faster than water, due to its higher evaporation rate, even though it is several times larger.
On the other hand, the degree and speed of solvent-substrate interaction and retention time may be manipulated by conservators. Conservators can alter this interaction by selecting and controlling any of various solvent application techniques, using immersion, poultice, or suction systems. Such manipulations alter the conditions of solvent concentration; of the direction of penetration, evacuation, and evaporation of solvent; and of time and rate of solvent exposure. During conservation treatments, for example, as a solvent volatizes or evaporates, the resultant removal of heat may lower the temperature of the surrounding area to below the dew point, causing condensation of water from the atmosphere. Water, whether introduced as condensation or as a solvent, may be absorbed into a polymer film coating and become trapped there as chemically bound water. Such alteration in the hydration state of a film may change its refractive index, and an increase in light scatter causes the film to appear lighter and consequently more opaque, a phenomenon referred to as �bloom,� sometimes seen in coatings on furniture and paintings. For instance, acetone, a hydrophilic ketone that can dissolve cellulose derivatives as well as certain resins and waxes, has a high vapor pressure, and its high evaporation rate can cool coating surfaces, causing moisture condensation leading to bloom (Hess 1965; Horie 1987). Under normal circumstances, pure ethanol is anhydrous and not likely to cause bloom unless it absorbs moisture from the air. Toluene, with an aromatic benzene ring affecting resins and cellulose derivatives, is hydrophobic and a slower evaporator than acetone and so should be able to dry without bloom. However, if the evaporation rate of a solvent is speeded up at room temperature, for example as a result of application and evacuation of solvent by suction disk, the drop in temperature might reach dew point, causing condensation and bloom. Bloom may be confused with physical changes in appearance caused by crazing, leaching and precipitation or redeposition of coatings or additives, and fiber debonding and swelling. Crazing is a network of fine cracks or microfissures within a coating. Leaching can be defined as the dissolution, movement, and redeposition or precipitation of one or more components of a coating, leaving a less compact, often porous or uneven surface. Fiber debonding causes the formation or expansion of interfiber interstices, increasing refractive surfaces and, hence, light scatter. These variables may be responsible for some of the effects solvents and application techniques have on the properties of tracing papers (van der Reyden et al. 1992a, 1992b).
Under the conditions of this study, color was not significantly affected by the application of solvents. In addition, although solvents caused the opacity in most papers to increase to a degree that conservators might find visually unacceptable, the measurable percentage point change in opacity was generally less than the 3�7 percentage points for rag or the 9 percentage points for chemical wood pulp paper considered unacceptable (following aging) by the U.S. Federal Specifications for Tracing Papers (UU-P-561H 1972) (fig. 4). The major exception occurred with the prepared tracing paper, which underwent significant change in opacity (greater than 7 percentage points) following suction application of all solvents except ethanol (figs. 3b�d, 4). Water applied by suction disk caused a significant change in opacity for the chemical pulp imitation parchment. Water in fact generally caused the greatest net change in properties regardless of application technique or type of paper, resulting in appreciable planar distortions and a decrease in gloss. Ethanol decreased gloss in all but the natural tracing paper, regardless of application technique. Toluene generally appeared to have the least effect on the most properties of most of the papers tested in this study, other than its effect on the opacity of prepared tracing paper when applied by suction disk. Suction disk application generally caused the greatest changes in opacity, while poultice most frequently caused the greatest changes in gloss. The visual change induced by poultice may result in part from residual poultice material. Suction application appears to cause the greatest change to cross-section morphology, as seen in SEM images (van der Reyden et al. 1992a, 1992b).
Fig. 4.
Effects of solvent type and application technique on opacity
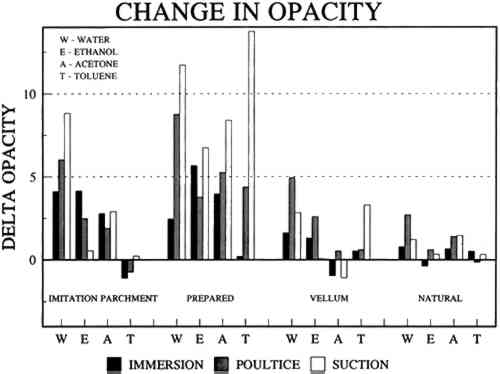 |
Fig. 3b.
SEM photomicrographs showing showing the top surface and cross-sectioned edge of prepared tracing paper after treatment with water (applied with suction disk), showing area characteristic of cracking or fissuring of coating
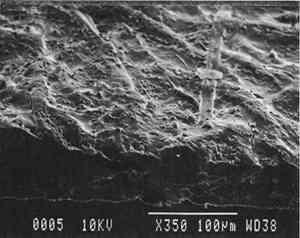 |
Fig. 3c.
SEM photomicrographs showing showing the top surface and cross-sectioned edge of prepared tracing paper after treatment with acetone (applied with suction disk) showing increased porosity, possibly from fiber debonding by acetone
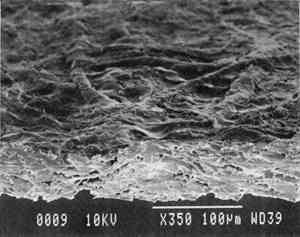 |
Fig. 3d.
SEM photomicrographs showing showing the top surface and cross-sectioned edge of prepared tracing paper after treatment with toluene (applied with suction disk) showing possible dissolution and loss of impregnating material
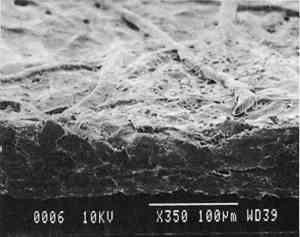 |
The increase in opacity measured in this study (fig. 4) could be caused by different reactions (i.e., chemically bound water, crazing, leaching of coating material or additives, or fiber debonding), depending on the solvent (water, ethanol, acetone, or toluene) and application technique (immersion, poultice, or suction). For example, treatment with ethanol applied by immersion or suction disk on the heavily coated prepared paper resulted in a concentration of material on the surface that was identified by SEM/EDS dot mapping as silica (van der Reyden et al. 1992b). A similar phenomenon occurred when the coated vellum paper was poulticed with water, as seen in cross-section SEM photomicrographs (figs. 1e�f). Increased concentration may be due to leaching of the medium, leaving the silica particles uncovered, rather than reprecipitation of material. When the heavily coated prepared tracing sample was treated with water, acetone, and toluene on the suction disk, the change in opacity increased substantially (fig. 4). However, in each case the increase in opacity may be the result of different mechanisms relating to the nature of the solvent-substrate interaction. Comparison of the opacity data (fig. 4) for the prepared tracing paper with the SEM details (fig. 3) of the same paper suggests that the change in opacity following water application on the suction disk may result from the scatter of light caused by crazing or microfissures in the coating (fig. 3b). The change in opacity following acetone application may be compounded by light scatter from fiber debonding (fig. 3c). Finally, the change in opacity following toluene application on the suction disk may be primarily attributable to light scatter from increased porosity following leaching of aromatic soluble resinous material (fig. 3d). The more pronounced change in appearance resulting from suction disk application may relate to the increase evaporation rate, a drop in temperature to dew point, and subsequent condensation of water on or within the polymer coating and paper substrate, causing crazing, bond breaking, swelling, and bloom.
Fig. 3a.
SEM photomicrographs showing the top surface and cross-sectioned edge of prepared tracing paper, untreated
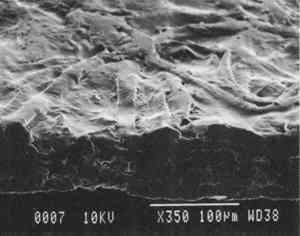 |
The paper most affected by all solvents was the heavily coated prepared tracing sample. Only immersion in toluene had no readily apparent effect, whereas when applied by suction disk, toluene caused an increase in opacity readily apparent in visible light. This finding suggests that the effect of toluene on this paper during a treatment, such as the removal of pressure sensitive tape or dry mount adhesive, might vary according to application technique. However, ultraviolet illumination revealed that areas treated by toluene applied by immersion and poulticing underwent increased absorption (reduced fluorescence), possibly indicative of some minor breakup of surface coating. As already noted, this paper may be prepared with a resin dispersed in toluene, as suggested by the manufacturer. The natural tracing sample (fig. 1a) was the least affected by all treatment conditions and had only a barely perceptible decrease in gloss and increase in planar distortion with water. The highly calendered imitation parchment sample (fig. 1d) and the lightly coated vellum paper sample (figs. 1e�f) were most affected by water.
5.3 CONCLUSIONS FOR PROJECT 3
The effects of solvents on the surface of tracing papers vary a great deal and seem to depend on the composition of the paper, the type of solvent, and the application technique. Of the papers studied here, the natural tracing paper was the least affected and the heavily coated prepared tracing paper was the most affected by the various solvents and application techniques. Water effected the greatest changes (increase in surface distortion and opacity and decrease in gloss) and toluene the least. The property most severely affected was opacity, which increased in most cases. Dimensional stability was most affected by water.
6 PROJECT 4: EFFECTS OF HUMIDIFICATION AND FLATTENING ON SELECTED CONTEMPORARY TRACING PAPERS
6.1 RESEARCH PROCEDURES
6.1.1 Humidification and Flattening Methods
As noted in table 1, this project investigated the effects of three humidification techniques (using immersion, ultrasonic humidification chamber, and a humidification pack system) and two flattening techniques (on a suction table and in a traditional blotter press with ca. 1 psi weight) (Flamm et al. 1990; Hofmann et al. 1992). Sample papers, both �new� (unaged) and �old� (aged as outlined in project 2), were treated by the following techniques.
HUMIDIFICATION TECHNIQUES: For humidification by immersion, the samples were first sprayed with deionized water, then immersed while supported on a polyester web and screen for 30 minutes in deionized water, followed by draining for several minutes until all standing water had evaporated. Humidification by a humidity chamber was undertaken by placing the samples on a screen between nonwoven polyester webs over a tray of hot water in a sealed chamber for 60 minutes. Humidification by a humidification pack consisted of placing the samples on a nonwoven polyester felt laminate (1/16> in thick), having a polytetrafluoroethylene membrane, on top of water-saturated, heavyweight blotters. The samples were covered with lightweight, nonwoven polyester webs and natural fiber felts for even contact, for 14 hours.
FLATTENING TECHNIQUES: One-third of all the humidified samples were allowed to air-dry. The second third were dried in a blotter press following evaporation of all standing water. The press consisted of polyester webs, blotters, felts, Plexiglas, and weight, creating a light but even pressure less than 1 psi. The blotters were replaced after 1 day, and the samples remained in the press for 2 weeks. The final third of the samples were given a preliminary flattening treatment on a domed Nascor suction table equipped with an ultrasonic humidifier. The samples, with the edges protected from drying by being covered with polyester film strips, were flattened by ca. 4 in Hg pressure for 10 minutes, followed by ca. 3 in Hg pressure for 20 minutes for the chamber and pack humidified samples or 50 minutes for the immersed samples. Following this step, the samples were dried in a blotter press as described above (Hofmann et al. 1992).
6.1.2 Measurement of Properties
Changes in opacity, gloss, strength, and dimensions (table 4) were measured as outlined in section 3.1.3.
Table 4. Summary of Data for Project 4: Effects of Humidification, Flattening, and Aging on Opacity, Gloss, Total Transmission, Tensile Strength, and Dimensions of Selected Contemporary Tracing Papers
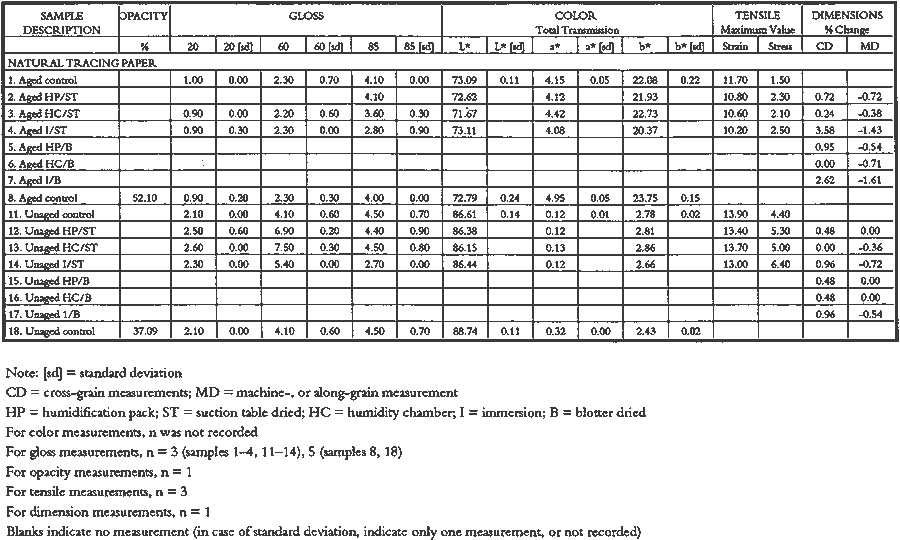 |
Table 4. (continued)
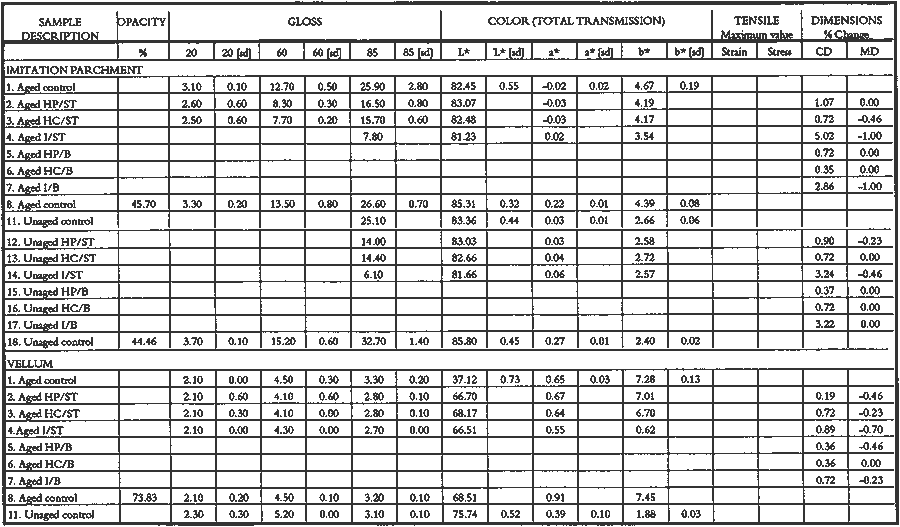 |
6.2 FINDINGS AND DISCUSSION FOR PROJECT 4
The most severe planar distortions occurred from immersion, especially for the overbeaten natural tracing paper (table 4). Humidification using the humidification pack and chamber caused less planar distortion, probably because these techniques effectively reduce water penetration into the paper fiber structure. Immersion also caused the greatest changes in dimensions and in mechanical properties, especially in comparison to humidification with a humidity chamber. This degree of change was particularly evident for the overbeaten natural tracing paper, for which immersion caused the greatest increase in strain to break, possibly because of rebonding after the release during immersion of dried-in strain produced during manufacture. Immersion caused a greater decrease in the stress and strain to break for prepared tracing paper sample, perhaps because water initiated the breakup of the coating material.
With respect to the two flattening techniques, compared to air-dried controls, suction table flattening and drying of immersed samples caused severe distortion, especially for the overbeaten natural tracing paper, as compared with flattening and drying in a traditional blotter press. Dimensional changes in the cross-grain direction were greatest for the overbeaten and calendered papers, following immersion and drying on the suction table. The coated papers were less affected dimensionally.
Imitation parchment paper underwent the greatest percentage change in gloss, particularly following immersion (fig. 5). The heavily coated prepared tracing sample incurred the greatest change in opacity, becoming mottled following immersion. This change may have resulted from a breakdown in coating, which appears to have occurred in this paper with each humidification technique, to some degree, causing some loss of surface, as evidenced by SEM photomicrographs of the sample after treatment using a humidification pack (figs. 6a�d).
Fig. 5.
Effects of humidification and drying on suction table, on gloss
 |
6.3 CONCLUSIONS FOR PROJECT 4
Different techniques for humidifying and flattening tracing paper affect properties in different ways. Based on our findings, conservators who must immerse a tracing paper in water might find dimensional changes less severe if the paper is dried in a blotter press rather than on a suction table. Tracing papers with heavy coatings that might soften on exposure to moisture should be humidified in a vapor chamber rather than by prolonged contact with a humidification pack system. This latter technique, however, might be better for uncoated or lightly coated natural tracing papers, since initial curling is prevented.
7 FINAL CONCLUSIONS
With respect to the color, opacity, and gloss properties of tracing papers subjected to the aging, solvents, and humidification and flattening conditions used in this study, the greatest change in color occurred with aging, the greatest change in opacity occurred with solvents, and the greatest change in gloss occurred following humidification and flattening. Water was the solvent that caused the greatest overall change in properties. The natural tracing paper was the paper most affected by aging; the prepared tracing paper was the paper most affected by solvents; and the imitation parchment was the paper most affected by humidification and flattening.
The preliminary findings of this research must be considered tentative for the following reasons: (1) vegetable parchment paper samples have not been completely analyzed and tested; (2) none of the papers have been aged after treatment to determine the long-term effects of treatment; (3) no solvent tests have been performed on aged papers; (4) techniques of microtomed cross sectioning and UV microscopy, both promising for characterization of papers before and after treatment, are still being developed, modified, and evaluated; (5) a database of FTIR reflectance spectra for thick coatings, transmission spectra on samples pressed on a diamond cell for medium coatings, and extraction spectroscopy for thin coatings is still being developed; (6) comparative studies of multiple papers, such as additional samples of vellum papers, have not been completed; (7) replication of the measurements of dimensional and planar changes has not been undertaken; and (8) there are many other solvents, application techniques, and humidification and flattening techniques (such as using a drying board or friction drying) that might be used successfully with tracing papers but were not tested in this project.
ACKNOWLEDGEMENTS
The authors would like to acknowledge the help of CAL staff and interns including Melanie Feathers, Mel Wachowiak, Ron Cunningham, and Jennifer Beers, and the many other consultants and conservation interns associated with various parts of this project over the years for their generous donation of materials, time, and expertise.
REFERENCES
Anderson, P.1990. Transparent paper: An examination of its uses through the centuries, with a close investigation of a collection of early 19th century tracings. Unpublished senior essay. New Haven: Yale College, History of Art Deptartment.
Andes, L. E.1907. The treatment of paper for special purposes. London: Scott and Greenwood.
Bachmann, K.1983. The treatment of transparent paper: A review. American Institute for Conservation Book and Paper Group Annual2:3�13.
Bachmann, K.1986. Transparent papers before 1850: History and conservation problems. In New directions in paper conservation: IPC 10th anniversary conference preprints. Oxford, Eng.: Institute of Paper Conservation.
Baker, M., D.van derReyden, and N.Ravenel. 1989. FTIR analysis of coated papers. American Institute for Conservation Book and Paper Group Annual8:1�12.
Bolam, F., ed.1962. The formation and structure of paper; Transactions of the symposium held at Oxford September 1961, vols. 1 and 2. London: Technical Section, British Paper and Board Makers' Association.
Bolam, F., ed.1976. The fundamental properties of paper related to its uses: Transactions of the symposium held at Cambridge, September 1973, vols. 1 and 2. London: Technical Section, British Paper and Board Makers' Association.
Booker, P. J.1979. A history of engineering drawing. London: Northgate Publishing.
Bush, A.1986. Conservation of 19th century tracing papers in the National Maritime Museum. In New directions in paper conservation: IPC 10th anniversary conference preprints. Oxford, Eng.: Institute of Paper Conservation. D61�D62.
Cable, C.1978. The architectural drawing: Its development and history 1300�1950. Monticello, Ill.: Vance Bibliographies.
Casey, J., ed.1980�83. Pulp and paper: Chemistry and chemical technology, 3d ed. New York: Wiley-Interscience.
Dawe, E. A.1914. Paper and its uses. London: Cosby, Lockwood and Son.
Erhardt, D.1988. Paper degradation: A comparison of industrial and archival concerns. In TAPPI proceedings: 1988 Paper Preservation Symposium, 19�21 October, ed.R.Smith and T.Norris. Washington, D.C: Technical Association of Pulp and Paper Industry. 83�90.
Flamm, V., C.Hofmann, S.Dobruskin, and G.Banik. 1990. Conservation of tracing papers. ICOM Committee for Conservation preprints, 9th Triennial Meeting, Dresden. 463�67.
Flieder, F., F.Leclerc, C.Laroque, P.Richardin, and B.Guineau. 1988. Analyse et restauration des papiers transparent anciens. In Les documents graphiques et photographiques, analyse et conservation 1986�1987. Paris: Archives Nationales. 93�139.
Flieder, F., M.Leroy, J. C.Andreoli, and F.Leclerc. 1991. Comparative study of four paper bleaching methods. In Proceedings for the International Federation of Library Associations-International Preservation and Conservation Research Seminar, ed.D.Clements. New York: IFLA.
Glaser, M. T.1988. Conservation of drawings by Frank Lloyd Wright at the New England Conservation Center. AIC preprints, 16th Annual Meeting, American Institute for Conservation, Washington, D.C.20�25.
Hess, M.1965. Paint film defects, their causes and cure. New York: Reinhold.
Hoffenk de Graaf, J., and C.E.M.Wolff. 1982. Eine Methode, um Transparentpapier zu Kaschieren. Maltechnik-Restauro3: 198�203.
Hofmann, C., D.van derReyden, and M.Baker. 1992. The effect of three humidification, flattening, and drying techniques on the optical and mechanical properties of new and aged contemporary transparent paper. In The Institute of Paper Conservation Conference Papers: Manchester. 247�56.
Horie, C.1987. Materials for conservation: Organic consolidants, adhesives, and coatings. London: Butterworths.
Jirat-Wasiutynski, T.1980. Sprayed poly (vinyl acetate) heat seal adhesive lining of pen and iron gall ink drawings on tracing paper. Journal of the American Institute for Conservation19:96�102.
Kouris, M.ed.1990. Pulp and paper manufacture Vol. 8: Coating, converting and specialty processes. Atlanta: TAPPI Press.
McClintok, T.1986. The drawings of Frank Lloyd Wright: Conservation of works on tracing paper. In New directions in paper conservation: IPC 10th anniversary conference preprints. Oxford, Eng.: Institute of Paper Conservation.
Mecklenburg, M.1984. The role of water on the strength of polymers and adhesives. Ph. D. diss., University of Maryland, College Park.
Mills, J. S.1986. Analysis of some 19th-century tracing paper impregnants and 19th-century globe varnishes. In New directions in paper conservation: IPC 10th anniversary conference preprints. Oxford, Eng.: Institute of Paper Conservation. D62�D63.
Mosher, R. H.ed.1950. Specialty papers, their properties and applications. Brooklyn, N.Y.: Remsen Press.
Mosier, E., D.van derReyden, and M.Baker. 1992. The technology and treatment of an embossed, chromolithographic �mechanical� Victorian valentine card. American Institute for Conservation Book and Paper Group Annual11:100�25.
Orme, E.1807. An essay on transparent prints and on transparencies in general. London.
Richardin, P., F.Flieder, S.Bonnaissies, and C.Pepe. 1990. Analyse par CG/SM des produits d'impregnation de papier calque anciens. ICOM Committee for Conservation preprints, 9th Triennial Meeting, Dreseden. 482�88.
Roberts, J. C.ed.1991. Paper chemistry. New York: Chapman and Hall.
Robinson, J. V.1980. Fiber bonding. In Pulp and paper chemistry and chemical technology, 3d ed., ed.J. P.Casey. New York: John Wiley and Sons.2:915�61.
Roth, L., and J.Weiner. 1963. Transparentising of paper. Bibliographic series 201. Appleton, Wis.: Institute of Paper Chemistry.
Rundle, C.1986. The composition and manufacture of contemporary tracing papers. In New directions in paper conservation: IPC 10th anniversary conference preprints. Oxford, Eng.: Institute of Paper Conservation. D64�65.
Saucois, C.1981. La restauration des papiers calques aux Archives Nationales. ICOM Committee for Conservation preprints, 6th Triennial Meeting, Ottawa. 81/14/16/1�7.
Sindall, R. W.1910. Paper technology: An elementary manual on the manufacture, physical qualities, and chemical constituents of paper and of paper-making fibres. London: Charles Griffin and Co.
Smart, H.1981. The methods of manufacture of translucent coated papers and their conservation problems. Unpublished 2d year project. Camberwell School of Art.
Steinkellner, C.1979. Transparentpapier. Maltechnik-Restauro1:9�13, 2:113�17.
Stone, J. L.1987. Treatment of 19th-century tracing papers from the Frederick Law Olmsted Collection. ICOM Committee for Conservation preprints, 8th Triennial Meeting, Sydney. 2:731�38.
van derReyden, D., C.Hofmann, and M.Baker. 1992a. Some effects of solvents on transparent papers. In Institute of Paper Conservation Conference Papers: Manchester, 234�46.
van derReyden, D., C.Hofmann, M.Baker, and M.Mecklenburg. 1992b. Contemporary transparent papers: Materials, degradation, and the effects of some conservation treatments. In Materials issues in art and archaeology III, Materials Research Society Symposium Proceedings. Vol. 267. eds.P. B.Vandiver, J. R.Druzik, G. S.Wheeler, I.C.Freestone. San Francisco: Materials Research Society. 267:379�95.
van derReyden, D., E.Mosier, and M.Baker. 1993a. Pigment-coated papers I: History and technology. ICOM Committee for Conservation preprints, 10th Triennial Meeting, Washington D.C. Forthcoming.
van derReyden, D., E.Mosier, and M.Baker. 1993b. Pigment-coated papers II: The effects of some solvent application techniques on selected examples. ICOM Committee for Conservation Preprints, 10th Triennial Meeting, Washington D.C.Forthcoming.
Vaurio, P.1960. Transparentizing of paper. TAPPI Journal43(1).
Vincent, H.1932. The materials used in the manufacture of tracing papers. Paper Trade Journal, TAPPI section. (December):304�5.
Watkins, S.1990. Chemical watermarking of paper. Journal of the American Institute for Conservation29:117�31.
Yates, M. I.1991�92. Personal communication.
Yates, S. A.1984. The conservation of nineteenth-century tracing paper. Paper Conservator8:20�39.
AUTHOR INFORMATION
DIANNE VAN DER REYDEN received certificates in conservation from Harvard University Art Museums (1981) and the Conservation Center, Institute of Fine Arts, New York University (1980), along with an M.A. in art history (1979), serving internships at the Fogg Art Museum, the Library of Congress, and the Museum of Modern Art. She is head of the Paper Conservation Laboratory at the Conservation Analytical Laboratory, Smithsonian Institution, engaged in research in the effects of treatments on specialty papers and in the training of interns and professionals. She is vice chair of the AIC Book and Paper Specialty Group, past secretary of AIC, and has been a Fellow for several years. Address: Conservation Analytical Laboratory, Museum Support Center, Smithsonian Institution, Washington, D.C. 20560.
CHRISTA HOFMANN received her master's degree in conservation from the Academy of Fine Arts, Vienna in 1989. She undertook internships at the Austrian National Library, the Graphic Collection Albertina, and the Conservation Analytical Laboratory.
MARY T. BAKER received her B.S. in chemistry in 1980 and her Ph.D. in 1986 in materials science with a specialty in polymer science from the Institute of Materials Science at the University of Connecticut. She has worked at the Conservation Analytical Laboratory, Smithsonian Institution, as a research chemist since 1987, collaborating with conservators on projects such as the effects of fumigation on materials; treatment and characterization of coated papers; light bleaching of paper; and methods development for analysis of microsamples of paints, varnishes, and other materials. Her current research is on the modern polymeric materials in air and space artifacts, their aging mechanisms, storage, treatment, and display. Address: Conservation Analytical Laboratory, Museum Support Center, Smithsonian Institution, Washington, D.C. 20560.
Section Index |