TREATMENT OF AN AMERICAN 19TH-CENTURY UPHOLSTERED CHAIR
CECELIA CHEWNING, & HAROLD F. MAILAND
ABSTRACT—A six-piece parlor suite made by Mitchell and Rammelsberg in the 19th century and bought by the Cincinnati Art Museum offered an opportunity to study original upholstery fabrics and see the combined examples of manufacturing technology and aesthetics of the United States in the mid-1870s. This paper reviews the history and condition of one chair from the suite and describes the cleaning and structural and visual compensation techniques used to treat it. Alternative cleaning and compensation techniques were used in order to preserve the original show cover and provide aesthetic integration.
1 HISTORY OF MITCHELL AND RAMMELSBERG
In 1986 the Cincinnati Art Museum purchased a sofa, armchair, and four side chairs from a Marion, Ohio, couple. This furniture was made by Mitchell and Rammelsberg, Cincinnati's premier 19th century furniture manufacturer (Peirce 1978). The company was founded in 1847 and grew rapidly to become the city's largest furniture maker. It was among the first in Cincinnati to adopt steam-powered machines. Its early success resulted in the opening of branch stores in St. Louis, Memphis, and New Orleans. By the 1870s the Cincinnati business included a vast factory complex and an impressive six-story retail building in the city's fashionable Fourth Street retail district. The company continued in business until the 1930s, though it was called the Robert Mitchell Furniture Co. after 1881.
In its 1879 catalog, Household Art: An Illustrated Business Brochure, Mitchell and Rammelsberg advertised a wide range of styles, including Renaissance, Louis XVI, Queen Anne, Japanese, Egyptian, Grecian and neo-Grec, Adams, and Eastlake (Mitchell and Rammelsberg 1879). The company sold furnishings for private residences, hotels, banks, stores, offices, churches, and schools. It stocked not only its own line of furniture, but furniture, fabrics, and decorative accessories made by other U.S. companies and imported from abroad. It is important to remember that the company sold many more items than it made. The 1879 catalog boasted that “every resource is taxed to meet the wants of all buyers, from the most fastidious and lavish to the most economical.” The bywords of the company appeared on the cover: art, durability, grace, economy, elegance. Since Mitchell and Rammelsberg was in business for more than 80 years, many of the company's wares must be extant throughout the Midwest and South as anonymous heirlooms.
2 MITCHELL AND RAMMELSBERG AND THE AESTHETIC MOVEMENT
Mitchell and Rammelsberg was praised as being in the vanguard for its rapid assimilation of the new modern gothic style when it displayed a sideboard and a hall stand at the 1876 Philadelphia Centennial Exhibition (Art Journal 1877). Modern gothic was promoted through the writings of Charles Locke Eastlake and through furniture designs and room settings by Bruce J. Talbert. Influential books by both Englishmen had been published in the United States by the early 1870s (Eastlake 1872; Talbert 1873). Mitchell and Rammelsberg's quick adoption of these British design reform ideas is highly significant, for many American furniture manufacturers did not incorporate Eastlake and modern gothic into their style repertories until the early 1880s.
Also praised for its Centennial display of modern gothic was the prestigious New York City firm of Kimbel and Cabus (1863–82). The Kimbel and Cabus offering was a drawing room setting, providing a complete, harmonious environment in which to show the company's furniture to its best advantage. A suite of ebonized cherry was described as “upholstered in maroon satin with gold cord and fringe,” a look similar to that of the Cincinnati Art Museum's Mitchell and Rammelsberg suite (Hanks 1982, 64).
Learning quickly from Eastlake, Talbert, and Kimbel and Cabus, around 1879 Mitchell and Rammelsberg “brought over from England an [unidentified] artist in household decoration” who designed three rooms in the store in the fashionable “aesthetic” taste (quoted in Peirce 1978, 229). According to a reviewer for The Week: Illustrated, “that innocent suite of rooms quietly revolutionized the interior decoration of the homes of wealth in the valley of Ohio” (quoted in Peirce 1978, 229). Engravings of two rooms in the company's 1879 brochure may be from that revolutionary suite. They closely resemble the illustrations in Talbert (1873).
Not only was Mitchell and Rammelsberg producing modern gothic furniture, it was also offering that furniture upholstered in the finest of aesthetic movement fabrics. The 1879 brochure noted, “The full resources of the upholstery department have been taxed to make the cushions and coverings worthy of the cabinet work” (Mitchell and Rammelsberg 1879, 15). Unfortunately, we have no records to indicate where the company purchased its upholstery fabric. We know that jobbers in Philadelphia and New York seem to have been the main suppliers of American-made and imported fabrics for furniture factories, and we know that Mitchell and Rammelsberg carried both (Moss 1992).
3 THE CINCINNATI ART MUSEUM'S SUITE
The six pieces of furniture purchased by the Cincinnati Art Museum have been dated ca. 1876–81. Probably described as a “suit” by the company, this group may have originally had a seventh piece, a lady's chair or the ubiquitous platform rocker (Grier 1988). Although the furniture had seen better days, what made it particularly appealing to the museum were these facts:
- The furniture was labeled. On the underside of each of the four side chairs was a faded paper Mitchell and Rammelsberg label.
- The furniture was in the modern gothic style that had brought the company national recognition at the 1876 Philadelphia Centennial.
- The structure of the furniture appeared to be quite sound. There was almost no damage to the wooden frames, which were ebonized and decorated with incised and gilded ornament according to Eastlake canons.
- The upholstery fabrics—an elaborate aesthetic movement jacquard pattern and a solid plush, as well as gimp and fringe—were worn and faded but intact as important documents of the suite's original appearance.
The jacquard fabric has a dull gold cotton warp. There are cotton wefts of dark olive drab and dull gold and silk wefts of crimson (cultivated) and gold (wild). The color combination would have been the height of fashion in the 1870s. In places where the fabric has not been exposed to light and wear, the colors are dramatic in their contrast. Most striking is the incredible sheen of the gold silk threads. The original impact of the suite must have been stunning, whether viewed in daylight or shimmering by gaslight.
The pattern of the jacquard fabric was undoubtedly inspired by the interest in the exotic patterns on the textiles, metalwork, and ceramics of Japan. Though Europeans had had a renewed fascination with things Japanese since mid-century, it was the Japanese pavilion at the Centennial that opened Americans' eyes to the art of that nation. Cincinnatians were most receptive to the Japanese influence: one need only look at the decoration of early Cincinnati art pottery by Rookwood.
We sent images of the jacquard fabric to several experts who agreed that it was imported. According to Linda Parry of the Victoria and Albert Museum, its sophistication points to England or France as the place of manufacture (Parry 1992). It would have been a top-of-the-line upholstery choice.
With this parlor suite, Mitchell and Rammelsberg clearly wedded art and industry to produce a classic document of American aesthetic movement furniture.
4 TREATMENT AND EXHIBITION CONCERNS
The Cincinnati Art Museum has been involved in a major renovation of its second-floor galleries since early 1991. When it was determined that the Mitchell and Rammelsberg parlor furniture would be exhibited in the renovated space, treatment decisions became necessary. We began to ask questions and consider alternatives, including the following:
- Were all pieces of the furniture to be exhibited?
- What was the value of having the original upholstery—to show it to the public in a gallery setting or to document it on the furniture, remove it, and retain it for study purposes?
- What did we want the final “look” to be in a gallery? Did we want to present the furniture as it looks today, or did we want to show it as it would have looked on the Mitchell and Rammelsberg showroom floor when a customer selected it?
- Would we consider exhibiting some pieces with original upholstery and some pieces reupholstered?
- Would the original pieces continue to deteriorate if they were displayed?
- If we decided to reupholster, could we find fabrics similar to the original? What would be the cost of an exact reproduction of our jacquard fabric?
We investigated replacements for the jacquard, the most critical fabric to the character of the suite, but we found nothing close to the original in today's market. In the process of looking, we became more convinced of the value of the distinctive design of the original fabric to the whole project, so we also investigated having the fabric reproduced. A major fabric house estimated the cost at $26,250: $4,000 to cut the jacquard cards and $445 per yard of fabric, with a minimum order of 50 yards.
In an effort to explore treatment possibilities, the museum asked Harold F. Mailand to examine the suite and propose basic procedures that would clean and stabilize the fabric surfaces. Following consultation and discussion with him, other treatment options were apparent. The Cincinnati Art Museum agreed to sponsor an experiment with upholstery infill on a chair, matching as closely as possible the current appearance of the jacquard fabric.
5 TREATMENT OF THE CHAIR
5.1 CONDITION
All pieces in the suite required work, but one side chair (CAM 1987.63.4) was chosen as a pilot project because it typified the condition problems (fig. 1). This chair showed considerable tears, loss, abrasion, and fading of the upholstery fabrics. There was also a heavy build-up of particulate matter on the horizontal surfaces. The seat showed the most damage; there was loss of both the cover fabric and the inner cotton batting, exposing the muslin cover. The major areas of damage along the front measured approximately 3� in � 24 in, and the damaged area in the middle measured 9� in � 11 in.
Fig. 1.
Side chair, Mitchell and Rammelsberg, Cincinnati, Ohio, 1879–81. Ebonized wood, cotton and silk jacquard woven brocade, silk velvet, silk gimp, and fringe. Cincinnati Art Museum, 1987.63.4 Overall view before treatment, showing upholstery loss, abrasion, facing, fraying, and surface accretion. All photographs by Harold F. Mailand.
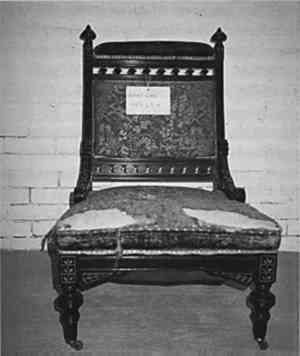 |
The gimp was detached, and there were areas of loss toward the back of the proper right-side skirt. The jute webbing was in an advanced state of deterioration. It was powdering and had little tensile strength. The jute was torn along the proper left side of the skirt, allowing the metal springs to rip the brown-dyed cotton scrim fabric underneath the chair (sometimes called a dustcover in the United States or bottoming in England).
5.2 STRUCTURAL STABILIZATION
We returned the profile of the seat by stabilizing the springs and jute in the following manner. The scrim fabric was removed by extracting the tacks or moving the fabric away from the tack heads. The original jute webbing and springs were realigned. Then, 2� in wide cotton webbing straps were secured to the bottom of the seat using new comparable nails and tacking between the old tack line. Heavy linen thread and a curved needle were used to secure springs to old and new straps. One end of each new strap was folded under and tacked. The other end was tacked, folded back, tacked again, and then clipped according to the original upholsterer's technique.
The scrim fabric, a common, inexpensive fabric used in the late 19th century to cover backs and bottoms of furniture, showed extensive tears and fraying. Due to its low priority, it could have been replaced with a modern fabric. However, it was the intention of this pilot project to preserve as much of the original construction and material as possible. Before determining its possible treatment, we realigned the scrim fabric with controlled heat, pressure, and steam using a conventional iron and commercial steamer. The paper label on the scrim was stable and hence not treated.
5.2.1 Rationale for Conservation of Scrim
Conventional textile conservation techniques of hand sewing the scrim fabric to a fabric support would have been prohibitive in time and cost, an especially important consideration when this low-priority fabric would not be viewable. Hand sewing also could have been extremely intrusive to the structure and may not have produced a stable structure capable of withstanding the tension when reattached.
While the use of adhesives and latex for the consolidation of tears and fraying has become widespread in other conservation media, it is not commonly used for textiles. Moreover, the crystalline nature of most adhesives and resins is antithetical to the flexibility of a textile structure. Beva 371, originally developed as an adhesive for use in relining paintings, seems to be the exception.1 Beva in naphtha can be applied as a spray coating to a backing fabric and heat set to a damaged area. This thermoplastic adhesive was chosen to stabilize the scrim. Textile Conservation Services has found it desirable for use in situations where hand sewing is impractical, impossible, or insufficient to stabilize a textile and has used it since 1983.
5.2.2 Stabilization of Scrim
A solution of equal parts of Beva 371 and VM&P naphtha was heated in a double boiler over a water bath until it became a clear and viscous liquid. Then it was flocked onto a brown organza fabric with a spray gun. The spray-coated fabric was cut into strips and placed on the back of the scrim fabric.
Initial placement was made with finger pressure. This technique was possible because Beva at room temperature has a “tooth” that allows partial adhesion. Then the two surfaces were bonded with a heat spatula. The scrim fabric was reattached with the same set of tacks using the same tack holes. The Beva spray–coated support fabric (underlayment) provided color compensation, structural stabilization, and reversibility with heat or even with a common dry-cleaning solvent such as perchlorethethylene. The original fabric was thus stabilized without a great expense of time.
5.3 CLEANING
The wood and fabric surfaces were initially cleaned with controlled low-power vacuuming. However, the fabric surface was still dull and dingy. The brocaded show cover and exposed inner cotton muslin lining were preconsolidated with basting stitches using white cotton sewing thread and an overlayment of white Maline,2 a nylon material, with a fine, diamond-mesh construction that allows it to be contoured to undulating shapes. It is available at fine fabric shops. Since Maline will not ravel, it can be cut to any shape. It has been used successfully as an overlayment to consolidate fabric surfaces and stabilize their edges. In this instance, the undyed Maline was laid on top of the upholstered surface and secured with backstitches. The nylon mesh stabilized the damaged fabric surface while allowing the fibers to be cleaned.
The velvet and brocade fabric surfaces were then cleaned in situ with Foamovator, a commercial foam solution.3 The foam solution, at a pH of 10, was spread gently over the fabric surface with a flat sheet of aluminum. The foam was then removed, and the fabric surface was neutralized with a defoaming agent consisting of water and acetic acid carried in a natural sponge and applied by hand in a forward and backward motion. The fabric surface was poulticed with cotton terry cloth toweling and the drying accelerated with fans.
Foam cleaning offers several advantages over wet cleaning. The process is easy to control because the solution is applied by hand. Because the fabric structure is not wetted completely through, the fabric can be cleaned in situ, and dries quickly. Thus, the mechanical stresses of immersion cleaning and reattachment are avoided.
5.4 COMPENSATION FOR LOSS
Reupholstering historic furniture has been commonplace in the home and in collecting institutions. Reproduction fabrics exist in many color ways and are relatively inexpensive. However, this approach can cause trauma to the original frame construction, and the process literally covers up or removes the object's original features, thus affecting its integrity and aesthetics. In this case, the fabric was a unique covering, and the weaving of a reproduction fabric in a limited quantity seemed costly. Moreover, removal of the show cover would have further weakened the fabric structure, destroyed the original upholstery craft, and placed too much stress on the fabric if treated off site and then reattached. Therefore, a means of in situ structural and visual compensation was sought.
The conventional treatment that conservators most often use to compensate for fabric loss is the application or insertion of neutral fabric overlayment or underlayment. A variety of stitches are used with this patching technique, including running, back, couching, and spannstich. Although these procedures are well intended and may do the job of stabilizing the textile, the aesthetics of the object often are not improved. Flat fabric patches can, in fact, be very distracting and compete visually with the object. The challenge of designing an appropriate fill for structural and visual loss depends on the degree of loss, the location of the loss, and the structure of the textile. Additional considerations are the projected use of the piece and the aesthetic expectations. The concern for aesthetic integration of the original and the new must be weighed against the need to use minimally interventive techniques that are potentially removable, if not reversible.
5.4.1 Silk Screen Infills
While an appropriately dyed fabric might have stabilized the structure, the repair would be improved visually if the design of the pattern could be reproduced. Commercial silk screen printing is a modified stencil process. The stencil is made by stretching a fine meshed fabric over a frame, and areas not to be printed are blocked out to make the pattern. Dye or pigment is pushed through the areas not blocked in the screen and onto the cloth below. A separate screen is used for each color of the pattern. Since 1988 we have applied this technology and have found that silk screening can be a viable means to satisfy our concern for aesthetic integration. From simple hand cut stencils to sophisticated photographic transfers, fabric patterns and color ways can be reproduced. The silk screened fabric can then be inserted behind the loss area and secured by conventional stitching. The infill can be reversed easily by clipping the stitches.
A fabric swatch provided by the museum (from the back of another chair in the parlor set) was used to study the pattern repeat. A professional photographer took an 8 x 10 in color transparency of the fabric swatch. Another firm stated that it could scan the transparency to distinguish the different color ways that make up the pattern and provide 1:1 positives for silk screening with opaque pigments. Instead, the scanner separated the transparency into the standard four color ways: magenta, yellow, cyan, and black. This type of color separation is designed for commercial transparent inks rather than opaque pigments, so the silk-screened samples made from the separations turned out to be muddy and inappropriate.
Since the separation method proved unsuccessful, a variation of another known method was used. From a 1:1 color copy of the fabric swatch, the perimeters of the pattern repeat were determined and a cut-out made. Next, a positive image of three separate color runs was hand drawn on Mylar using opaque ink and a technical pen. Photosensitive emulsion was applied to three screens, and the positive Mylar sheets were laid directly on the screens and exposed to sunlight, making a contact print of each color way. The excess photosensitive coating was then washed off.
To alter the base fabric color, a knit fabric was airbrushed with water-soluble pigments. Knit fabric was chosen for its stretchability, which allowed for matching the pattern, as the original fabric structure was under variable tension throughout. The knit fabric was silk screened with three color runs using water-soluble pigments (Createx Pure Pigments in a Super Print Base), and the colors were heat set to the knit fabric using steam, heat, and pressure. Using water-soluble pigments rather than dyes for silk screening and airbrushing allowed more freedom to custom-match the nuances of color found in the original fabric due to differential fading, abrasion, and soiling. The silk-screened fabric was inserted under the existing fabric. The original and new patterns were then aligned and the fabrics basted in place (fig. 2). Finally, the loss, tears, and detached warps and wefts were consolidated with a curved needle using dyed cotton thread and randomly couched to the original muslin cover (figs. 3, 4).
Fig. 2.
Detail of the side chair during treatment, side view showing silk-screened fabric underlay inserted in area of loss.
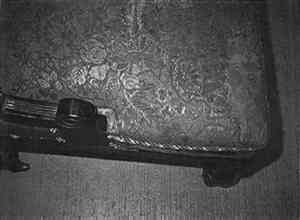 |
Fig. 3.
Detail of the side chair after treatment, front view showing cleaned surface, areas of loss compensated with silk-screened fabric underlay, and fraying consolidated with couching stitches to the original muslin cover.
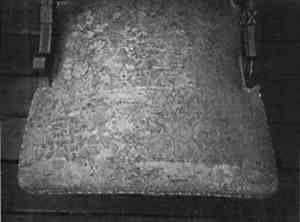 |
Fig. 4.
Overall view showing cleaned surface, areas of loss compensated with silk-screened fabric underlays, and fraying consolidated with couching stitches to the original muslin cover.
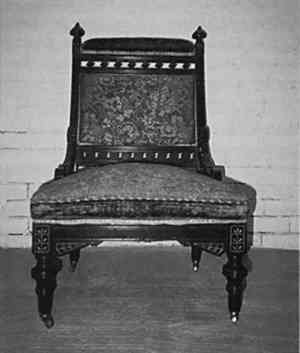 |
6 CONCLUSIONS
The final result was a printed fabric insert that successfully simulated the original fabric on the chair in both color and design. Although the surface of the printed knit underlayment does not have the same texture, nor does it reflect light in the same manner, the difference is not enough to detract noticeably from the finished piece. The inserts do not cause trauma to the original fabric. The stitches used to stabilize the loss areas and fraying are minimal and can be reversed easily. Furthermore, the condition and wear of the original upholstery fabric is visible upon close examination. This aspect is important to curators, historians, and conservators who want to keep the construction, use, and treatment discernible in an object. The chair is now structurally sound and aesthetically pleasing.
The above treatments provide the Cincinnati Art Museum with more options for exhibiting the Mitchell and Rammelsberg parlor suite. The remaining pieces could be treated in a similar manner. In addition, fabric yardage could be silk screened and used to slipcover the suite. This possibility would involve minimum intervention to the structure while protecting the original surfaces.
ACKNOWLEDGEMENTS
Ms. Chewning would like to thank the following people for comments on the museum's jacquard textile and for general assistance with the project: Regina Blaszczyk, Katherine C. Grier, Lynn Felsher (Fashion Institute of Technology), Gillian Moss (Cooper-Hewitt National Museum of Design), Linda Parry (Victoria and Albert Museum), and Odile Valansot (Center International D'Etude des Textiles Anciens, (CIETA)). Mr. Mailand would like to acknowledge the following staff members of Textile Conservation Services for their inspirational, technical, and editorial assistance, respectively: Maebel Danneman, Anne McKenzie Nickolson, and Mary Annette McLeroy. The authors also acknowledge the assistance of Michael J. Ruzga, assistant conservator, Cincinnati Art Museum, who performed the fiber analysis.
NOTES
1. The product used was purchased from Adam Chemical Co. prior to February 1987. Beva is a registered trademark owned by Gustav Berger since 1987. Only Conservator's Products Co. manufactures Beva products, which are tested regularly by Gustav Berger.
2. Introduced to the conservation profession by the Textile Conservation Workshop, South Salem, N.Y., ca. 1978.
3. The ingredients of Foamovator include water, sodium sesquicarbonate, tetrasodium, pyrophosphate, sodium sulfate, sodium laurel sulfate (Orvus WA paste), and isopropyl alcohol.
REFERENCES
Art Journal. 1877. The Centennial exhibition. XI. Art Journal3:115–16.
Eastlake, C. L.1872. Hints on household taste: In furniture, upholstery, and other details. 1868. Boston: J. Osgood and Co.
Grier, K. C.1988. Culture and comfort: People, parlors, and upholstery, 1850–1930. Rochester, N.Y.: Strong Museum. 201–35.
Hanks, D.1982. Kimbel and Cabus. In Nineteenth-century furniture: Innovation, revival and reform. New York: Art and Antiques for Billboard Publications. 60–69.
Mitchell and Rammelsberg. 1879. Household art: An illustrated business brochure. Sales Catalog. Washington, D.C.: National Museum of American History Archives.
Moss, G.1992. Private communication. Cooper-Hewitt National Museum of Design.
Parry, L.1992. Private communication. Victoria and Albert Museum.
Peirce, D. C.1978. Mitchell and Rammelsberg: Cincinnati furniture manufacturers, 1847–1881. Winterthur Portfolio13:209–29.
Talbert, B. J.1873. Gothic forms applied to furniture, metal work, and decoration for domestic purposes. 1867. Boston: J. Osgood and Co.
SOURCES OF MATERIALSBeva 371Conservator's Products Co., P.O. Box 411, Chatham, N.J. 07928 Createx Pure Pigments and Super Print BaseColor Craft, East Granby, Conn. 06026 Foamovator Rug SolutionDuraclean International, Deerfield, Ill., 60015
AUTHOR INFORMATION
CECELIA SCEARCE CHEWNING is associate curator of decorative arts at the Cincinnati Art Museum, where she has responsibility for the European decorative arts collection. She is currently cataloging the museum's British silver. She received an M.A. in art history from the University of Cincinnati, writing a thesis on the life, aesthetic philosophy, and teaching of the 19th-century Cincinnati woodcarver Benn Pitman. Before coming to the art museum in 1986, she worked in house museums operated by a local historical preservation organization. Address: Cincinnati Art Museum, Eden Park, Cincinnati, Ohio 45202.
HAROLD F. MAILAND holds a master's degree in education and textile design from Indiana University. His training in textile conservation includes internships at the Textile Museum, the Smithsonian Institution, the Museum of Fine Arts, Boston, and the Costume Institute of the Metropolitan Museum of Art with grants from the National Endowment for the Arts, the National Museum Act—Smithsonian Instiution, and others. Mailand was associate textile conservator at the Indianapolis Museum of Art, and in 1986 he founded Textile Conservation Services, Indianapolis. He is a Fellow of the American Institute for Conservation. Address: 928 N. Alabama St., Indianapolis, Ind. 46202–3350.
Section Index |