THE EFFECTS OF SOLUTION APPLICATION ON SOME MECHANICAL AND PHYSICAL PROPERTIES OF THERMOPLASTIC AMORPHOUS POLYMERS USED IN CONSERVATION: Poly(vinyl acetate)s
ERIC F. HANSEN, MICHELE R. DERRICK, MICHAEL R. SCHILLING, & RAPHAEL GARCIA
3 RESULTS AND DISCUSSION
3.1 SOLVENT RETENTION
FOR THE films averaging 0.08 mm thickness, significant amounts of solvent were retained after drying the films for 50 days; especially apparent are high concentrations of chloroform and toluene. A second set of thinner films was cast and allowed to dry for 180 days in order to obtain films with less solvent. This set was cast to confirm that the effects on the mechanical and physical properties were due to solution quality or polarity of the solution-cast films and not to retained solvent and also to compare the mechanical and physical properties of these films with a plasticized film cast from a toluene solution.
Films at this interval were also analyzed for water content. Films cast from chloroform and toluene did not show the presence of water. Films cast from an acetone or acetone/ethanol/water mixture showed traces of water (>0.1%).
Two methods of evaluating solvent retention by gas chromatography were explored. The “hot-jar” method consists of heating a known amount of polymer in a closed container and then analyzing volatile contents. Pyrolysis GC consists of flashing off the volatiles at a high temperature, but the analysis also causes polymer decomposition. Greater amounts of retained solvent were found with the pyrolysis method, evidently because heating in a closed container did not fully volatize all retained solvent. Therefore, the amounts reported in table 1 are those obtained by pyrolysis GC.
Concentrations of acetone and chloroform were below the detection limits for films cast from these solvents at a 180-day interval. However, films cast from toluene retained 4% by weight of solvent.
3.2 TENSILE PROPERTIES
The tensile properties of AYAT films cast from different solvents (tables 2, 3, and 4) are highly dependent upon both the solvent used for casting and the time interval after casting.
TABLE 2a Yield-Stress and Stress-at-Break of AYAT Films at 50 Days after Casting from Different Solvents
TABLE 2b Yield-Stress and Stress-at-Break of AYAT Films at 180 Days after Casting from Different Solvents
TABLE 3 Initial Elastic Modulus of AYAT Films at 50 and 180 Days after Casting from Different Solvents
TABLE 4 Percent Strain-to-Break of AYAT Films at 50 and 180 Days after Casting from Different Solvents
Representative stress-strain curves obtained from tensile fracture at a constant rate of elongation are shown in figures 2 and 3 for samples of films dried for 50 days and 180 days, respectively. The yield-stress differs from the stress-at-break for samples with a yield point, beyond which further elongation occurs with plastic flow. After drying for 50 days, only samples from films cast from the more polar acetone/ethanol mixture have a sharp break point, exhibiting no plastic flow at this elongation rate. After drying for 180 days, samples from films cast from both acetone and an acetone/ethanol mixture fracture with the peak applied stress at 3% elongation. Samples from films cast from both chloroform and toluene continue to flow to above a 200% strain-to-break after the yield point.
Fig. 2.
Representative tensile properties at 50 days of AYAT films cast from different solvents
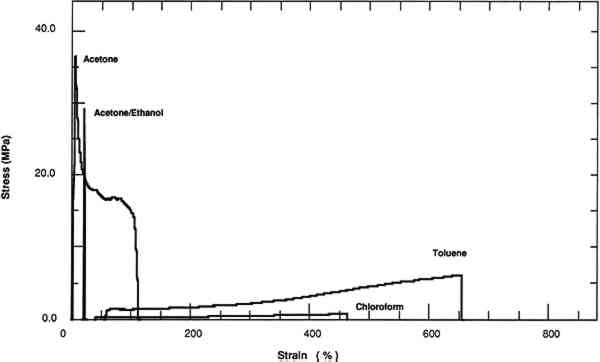 |
Fig. 3.
Representative tensile properties at 180 days of AYAT films cast from different solvents
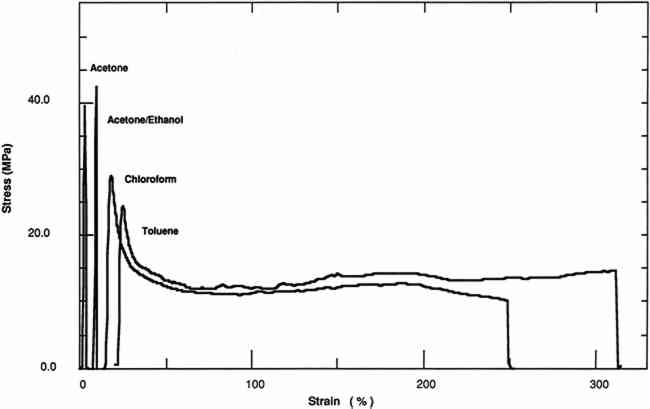 |
The initial elastic modulus increases with both drying time and solvent polarity. Again, two groups are apparent: one of higher modulus for films cast from acetone or acetone/ethanol solutions and a second of lower modulus for films cast from solutions of either chloroform or toluene.
The differences in tensile properties of the films can be related to the amount of retained solvent after 50 days of drying (see table 1). However, the data from the GC analysis for the 180-day interval confirms that the differences in the tensile properties of some films are related to solvent type and solvent retention (table 3). Only trace amounts of chloroform or acetone are still present in the films, but the tensile properties are distinctly different. When the better solvent, chloroform, is used in casting, the strain-to-break of the samples exceeds 200% compared to 3% for the acetone mixtures. With respect to films cast from toluene, the amount of retained solvent may still be important in plasticizing the films, with a resultant lower stress-to-break and greater strain-to-break compared to films cast from an acetone solution.
With time, changes in the properties of a cast resin are related not only to solvent release but also to the physical aging of the polymer. Amorphous polymeric materials move toward an increased state of brittleness with increasing time when maintained at a temperature below their Tg. In this case, performance with time should be evaluated with the understanding that increased brittleness will occur from physical aging (Struik 1978). This is a result of a thermodynamic drive toward a physical equilibrium state, in addition to the more well-known and addressed effect of chemical modifications (oxidation, hydrolysis, chain-breaking) that may also cause a more brittle state of a polymer.
Several problems exist when attempting to maximize a specific physical property of a cast resin by adjustments to the polymer/solvent mixture used for casting. Use of a different solvent may result in a different submicroporosity that affects the density and permeability of a cast film (Malkin 1983). Also, solvent mixtures are not explicitly additive in their effect on the polymer conformation due to polar interactions between the solvent and polymer.
Malkin (1983) has shown that the thermodynamic quality of the solution, as indicated by the intrinsic viscosity, cannot be used to predict a property of the resin cast from it. Instead, there are peaks in the curves for plots of intrinsic viscosity versus a mechanical property for acrylics and cellulose ethers. The tensile properties of ethyl cellulose do not correlate with solvent polarity but maximize at a 30% ethanol/toluene mixture (Tess 1985). For this polymer there is a simultaneous increase in elongation and strength, in contrast to poly(vinyl acetate) where the strength and elongation show inverse relations when changing solution quality and polarity. These results suggest that the exact effect of the solution quality and polarity on the mechanical properties of a polymer must be experimentally determined.
3.3 THERMAL ANALYSIS
The initial reason for using thermoanalytic techniques was to determine if the level of solvent was sufficient to cause plasticization of the films. Plasticizers are materials incorporated into other materials to increase flexibility, distension, or workability. Plasticizers, either intentionally incorporated or a result of retained solvent, may lower the melt viscosity, the second-order transition temperature, or the elastic modulus of a resin (Sears and Touchette 1982). The lower strength and greater elongation exhibited by resins plasticized due to retained solvent may be attributable to a lowering of the Tg. Therefore, if the difference in mechanical properties was due to retained solvent plasticizing the films and not necessarily an effect of the type of solution used for casting, these films would be expected to show a glass transition temperature below 22�C, the experimentally determined Tg of the bulk polymer. (This Tg is less than the Tg of PVAC, 28–31�C, listed in the Polymer Handbook[Lindeman 1975]).
The Tg values shown in table 1 were unexpected and demonstrate a further influence of prior processing on the physical properties of a polymer. At a 50-day drying interval, films cast from the more polar solutions of acetone and ethanol (which are also the poorer solvents), have a Tg 18�C to 29�C above the near-room temperature Tg of bulk PVAC. After a 180-day drying interval, the Tgs of the films, including a film with 4% toluene, are elevated above the Tg reported for the bulk polymer. At this interval the Tgs of the films cast from all solvents are above 40�C.
The Tg is generally considered a “basic” property of a polymer and not subject to the influence of processing, unless the thermal history of the polymer is varied. As the observed variation in the Tg is not related to specific solvents but is related instead to the amount of retained solvent in the polymer films, the elevated Tg of the polymer may therefore result from the solution deposition process alone. As the Tg is often a critical property in the selection of a resin for a particular use in conservation, this observation deserves much further consideration.
3.4 INFLUENCE OF MOLECULAR WEIGHT
Lower molecular weight grades of PVAC are more often used in conservation than AYAT (MW = 226,000). Because the effects of coiling and uncoiling of polymer chains might be less in polymers of lower molecular weights, the tensile properties and Tg of films of a lower molecular weight PVAC, AYAF (MW = 169,000), were determined and shown in table 5.
TABLE 5 Tensile Properties and Tg of 0.03 mm AYAF Films at a 180-Day Interval after Casting
The same effect is seen in films of the lower molecular weight grade PVAC in the same thickness, 0.03 mm, and at the same time interval after drying as for the higher molecular weight grade. For a nonpolar good solvent for PVAC, chloroform, there is pronounced elongation before breaking and lower tensile strength. For a more polar and poorer solvent for PVAC than chloroform, acetone, little elongation before breaking and higher tensile strength is evident. Also, the Tg is elevated for films cast from either solvent.
3.5 FOURIER TRANSFORM INFRARED SPECTRA
Further evidence of the change in conformation of the deposited film can be inferred from the measurements taken from the FTIR spectra of the PVAC molecular weight series (table 6). The PVAC resins were analyzed using chloroform and acetone as solvents. When the resins were prepared with chloroform there were noticeable spectral changes in the sizes of the methyl and methylene bands that correspond to the molecular weight progression of the polymer resins. Specifically, there is an increased absorption by the carbon-hydrogen bonds of methylene groups at 1373 cm−1 relative to that by terminal methyl groups at 1435 cm−1. Since a large polymer contains more methylene groups relative to the methyl groups at the end of the chain, it appears that each carbon-hydrogen bond has freedom of movement and thus that the absorptions are proportional to the species present.
TABLE 6 Ratio of Methylene to Methyl Infrared Absorption Bands of AYAT, AYAC and AYAA Deposited on KBr from Chloroform and Acetone
The PVAC samples prepared with acetone do not exhibit the same changes in spectral band intensity. In fact, the spectra of the samples with different molecular weights were all similar. One explanation for this apparent solvent dependence is that the chloroform disperses and separates the polymeric chains while the acetone solvation produces polymeric aggregates. Within such an aggregate the chain may be folded in such a conformation that some molecular vibrations are inhibited.
In comparing the two solvent systems, the highest molecular weight resin, AYAT, showed the most noticeable spectral differences. As an additional check, AYAT was prepared for analysis without using a solvent (i.e., grinding the bulk resin), which resulted in a spectrum more closely resembling the AYAT sample prepared with acetone. Thus, overall, the FTIR can discern morphological differences in the polymer that are specific to the solvent used in sample preparation.
|