THE EFFECTS OF SOLUTION APPLICATION ON SOME MECHANICAL AND PHYSICAL PROPERTIES OF THERMOPLASTIC AMORPHOUS POLYMERS USED IN CONSERVATION: Poly(vinyl acetate)s
ERIC F. HANSEN, MICHELE R. DERRICK, MICHAEL R. SCHILLING, & RAPHAEL GARCIA
ABSTRACT—The tensile properties of solution-cast poly(vinyl acetate) (PVAC) films are determined by the thermodynamic quality of the solvents. Higher strength and lower elongation are evident in polymer films of poly(vinyl acetate) AYAT (Union Carbide) cast from a solution of acetone or an acetone/ethanol/water mixture, while lower strength and greater elongation are evident in films cast from a solution of chloroform or toluene after drying for 180 days. Films of PVAC-AYAT cast from a toluene solution retained a significant amount (>4%) of solvent, while films cast from the other three solvents retained little solvent (>0.3%). For all polymer films, the glass transition temperature (Tg) was elevated greater than 18�C above the Tg of the bulk polymer. The differences in the tensile properties of the films with little retained solvent is explained on the basis of the thermodynamic quality of the solvents, i.e., the physical properties of the solution-cast polymer film in the dry state may be affected by the conformation of the polymer chain in the solvent. The polymer chain of poly(vinyl acetate) is relatively extended in the “good” solvent chloroform but is more contracted in the “poorer” and more polar solvent, acetone. The effect of solvent quality on the polymer morphology in the dried film was also demonstrated with Fourier transform infrared spectroscopy (FTIR). Changes in spectral band intensity in the FTIR spectra within a series of poly(vinyl acetate)s differing in molecular weights can be discerned when these are deposited on KBr from a chloroform solution but not when deposited from an acetone solution.
1 INTRODUCTION
WHEN SELECTING a thermoplastic polymer for a particular use as a coating, consolidant or adhesive, conservators consider the chemical stability and physical properties of the resin. Some polymers, such as poly(vinyl acetate)s (PVAC) and Acryloid B-72 (Rohm and Haas), have been shown by Feller (1978) to be relatively resistant to environmentally induced chemical modifications. These polymers have been widely used in conservation because they possess a range of physical properties suitable for the treatment of art objects. They have been designated class A materials, which by Feller's definition means that they are expected to remain in a museum environment in excess of 100 years with little comparative change in solubility.
In addition to sufficient “aging” properties, physical properties that accommodate the end use in the conservation of an object are also a concern. For example, if a hard coating is required, Acryloid B-72 is a more suitable choice than the softer poly(vinyl acetate) AYAA; but the latter resin is preferred when a more flexible adhesive joint is needed.1
However, another important consideration in selecting a polymer with suitable properties that has received little attention in conservation research, is the influence of the application procedure on the properties of the polymer. When thermoplastic polymers are applied from solution, the nature of the solvent affects the conformation of the polymer in solution, which may result in an effect upon the ultimate mechanical properties, physical properties, and aging characteristics of the dry polymer film.
This paper presents a short overview of the theoretical aspects that govern the ultimate physical properties of thermoplastic amorphous polymers applied from solution. The effect of solvent choice on the tensile properties, FTIR spectra, glass transition temperature (Tg) and the solvent retention of poly(vinyl acetate) cast as films is reported. Finally, suggestions are given for optimizing the solvent mixture for a given property of interest for a polymer.
1.1 THEORETICAL AND EXPERIMENTAL BACKGROUND
The conformation of a polymer chain in solution may depend upon the solvent. One of the reasons for conformational differences is the thermodynamic “quality.” When a polymer is in a solution where the solvent has a greater attraction for segments of the polymer than the polymer segments have for each other, the chain length is extended (fig. 1). Conversely, contraction will occur when a polymer is in a solvent in which the solvent-polymer attraction is less than the polymer-polymer attraction. Solvents for a particular polymer have been denoted “good” if the chain extension is promoted and “poor” if the chain extension is contracted. Good solvents dissolve a larger amount of polymer; if the solvent is too poor, the polymer will not dissolve (Daniels and Albertyh 1975). The basis for studying solution properties of polymers is that the effects from certain conformations of the polymer chain will persist in the film deposited from such solutions, with resulting variations in physical properties of the polymeric film. However, the solvent “type” describes only the thermodynamic quality of the solution and is not necessarily connected with “good” or “bad” properties of the resultant polymer film for a specific use in the conservation of an object.
Fig. 1.
The effects of solvent quality on the conformation of a polymer molecule in solution
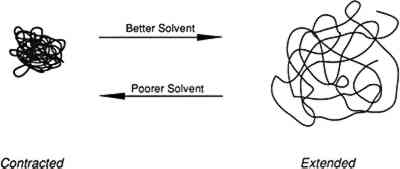 |
Some physical properties of many polymers have been shown to be dependent upon the solvent or solvent mixtures chosen for the solution application. This effect has been demonstrated with ethyl cellulose films on the tensile properties and the permeability to nitrogen and oxygen (Tess 1985) and on the birefringence, brittle-point temperature, and density (Haas et al. 1965). Similarly, for poly(methyl methacrylate) the surface properties of cast films (Schreiber and Croucher 1980), the hardness (Carre et al. 1980), and the shear strength (Briscoe and Smith 1983) have been shown to differ depending upon the solvent used. The time-dependent change (aging) of some mechanical and physical properties is also affected (Kurbanaliyiyev et al. 1982; and Materovsyan et al. 1985).
Olayemi and Adeyeye (1982) tested the tensile properties of PVAC films cast on clean mercury surfaces from solutions of methanol, acetone, and chloroform. They determined some mechanical properties of the films after exposure at 20�C and 65% RH and at 45�C and 65�C in dry ovens. The initial modulus, yield stress, tensile strength, and work-to-rupture were shown to be greater for films cast from a solution of acetone than for those cast from a solution of chloroform. The elongation-to-break showed the reverse trend. Methanol solutions yielded films too brittle for testing. The PVAC films cast from a chloroform solution exhibited the most constant mechanical properties over the longest time interval studied (360 hours). These properties were also dependent upon the temperature of the exposure, decreasing as the temperature increased.
These results were interpreted on the basis of solvent interaction with the polymer molecules both in solution and in the first stage of film formation. (In that stage, the drying rate is controlled by solvent volatility as opposed to solvent diffusion, which controls the second stage of film formation.) The results of the present study confirm those of Olayemi and Adeyeye (1982) and address further considerations: the dependence of the tensile properties of the films on the amount of retained solvent, and whether the physical properties tend toward an equilibrium value after a longer film drying time.
For many polymers used in conservation the choice of solvent deserves careful consideration. In fact, the variation in physical properties of one polymer applied from different solutions may exceed the variation in the physical properties between two different bulk polymers.
The results presented here provide some answers to the following questions:
- To what extent does solvent retention affect the physical properties of polymers used for conservation purposes? (Retained solvents may plasticize resins with the transitory effects on physical properties disappearing following full solvent release).
- Over what time period after application will persist the effects on a polymer's physical properties that result from application in a given solvent? If the properties of the polymer reach an equilibrium state relatively quickly after application, regardless of application process, the importance of solvent choice is minimized.
- Can a solvent be chosen or a solvent composition be manipulated in order to obtain one or more desired properties from a particular resin?
The answer to this last question depends in part upon other factors that affect the final properties of a film. These questions are addressed below in the discussion of film preparation history.
2 EXPERIMENTAL
2.1 MATERIALS
FOUR MOLECULAR weight PVAC resins were used: AYAT (MW = 226,000), AYAF (MW = 169,000), AYAA (MW = 110,000), and AYAC (MW = 14,500). (The molecular weights reported are the weight average molecular weights of PVAC grades as determined by gel permeation chromatography [GPC] [Druzik 1987]). AYAT and AYAF resins were used to cast films from different solvent systems. AYAA, AYAC, and AYAT resin samples were analyzed by FTIR spectroscopy.
Solvents for solution preparation included chloroform, toluene, acetone, and a solution of 10 parts by volume acetone, 10 parts by volume ethanol, and 1 part by volume water.
2.2 FILM PREPARATION
Four percent solutions (w[g]/v[ml]) of AYAT in each of the four solvent systems were cast upon a Teflon FEP (polyhexafluropropylene) surface in break-apart molds as previously described (Hansen and Taketomo 1989). Two series of films with an area of 0.0225 m2 were cast: one series 0.08 mm thick and dried for 50 days and one 0.03 mm thick and dried for 180 days. A constant temperature of 22�C and RH of 65% were maintained throughout the drying intervals.
Additionally, 4% solutions of AYAF in acetone and chloroform were cast in the same manner. Films 0.03 mm thick were dried under the same conditions for 180 days.
2.3 MECHANICAL TESTING
The stress-to-break, strain-to-break, yield-stress, and initial modulus for each drying interval were determined for films of AYAT and AYAF by tensile fracture at constant elongation according to the specifications in ASTM D-2370–82(87), “Standard Test Method of Tensile Properties of Organic Coatings” (ASTM 1989). Values were electronically recorded from an Instron 4201 Universal Testing Instrument and analyzed with the Instron software Series IX Automated Materials Testing System. The temperature and humidity were maintained at 20�C and 65% RH, respectively. Strips 12 mm in width were precision cut using a Thwing Albert JDC Precision Sample Cutter and were fractured at a cross-head speed of 50 mm/min from an initial gauge length of 76 mm. Film thickness over the gauge length varied less than �5%, determined with an eddy current–type coating thickness gauge which can measure the thickness of a dielectric film (Vector TX1). The tensile values reported for a cast film are the mean of four to nine samples, depending upon the range of the values obtained on the sample sets.
2.4 SOLVENT RETENTION
Films of AYAT were analyzed for residual amounts of solvent. Films at the 50-day drying interval were analyzed for weight percentage of residual solvent at an analytical service center (Baxter Analytical Labs, Irvine, Calif.) by direct insertion probe thermal desorption mass spectrometry using a HP 5987A Mass Spectrometer System. Solvent content was estimated from area ratios of the thermal desorption profile. Direct insertion probe conditions were a temperature ramp from 30�C to 350�C at 15�C/min with a hold at 350�C for 5 minutes.
After drying for 180 days films were analyzed on an HP 5890 Gas Chromatograph (GC) with a CDC 120 pyroprobe. The samples were pyrolyzed at 200�C with the ramp turned off and an interface temperature of 40�C. Optimal separation was obtained on a 25 m Carbowax 20M column with an initial temperature of 100�C ramped to 150�C at 5�C/min. Helium carrier gas was used at a flow rate of 30 ml/min. The FID detector was held at 220�C. Internal standards were used to identify and calibrate the solvent peaks. In addition, reference films were prepared for comparison in which the amount of solvent was determined by a gravimetric method of analysis of films during the drying process. Due to the limited solubility of PVAC AYAT in pure ethanol, this method was not used to determine residual amounts of ethanol.
2.5 THERMAL ANALYSIS
The Tg data of bulk AYAT and AYAF cast from the four solvent systems were obtained by differential scanning calorimetry (DSC). The method used to obtain the Tg has been previously described (Schilling 1989).
2.6 FOURIER TRANSFORM INFRARED SPECTROSCOPY (FTIR)
FTIR spectra were obtained at 4 cm−1 resolution on a DIGILAB 15-E FTIR spectrophotometer equipped with a Motorola 3200 computer and a dry nitrogen purge. A wide-range, cryogenically cooled MCT detector was used to examine the mid-IR region from 4000–500 cm−1. Each spectra was the accumulation of 200 scans.
Sample preparation for the infrared analysis of the bulk resin consisted of dissolving the resins (AYAA, AYAT, AYAC) in chloroform or acetone and depositing the solution on powdered KBr. The solvent was allowed to evaporate and then the mixture was pressed into a transparent pellet under vacuum. Additionally, for AYAT, a portion of bulk resin was powdered and mixed with KBr. The pellets were analyzed in transmissive mode using a 3 mm diameter beam.
2.7 FILM PREPARATION HISTORY
The physical properties of solution-cast films of thermoplastic polymers are influenced not only by the solvent type and solvent polarity, but also by:
- the concentration of the solution used for casting;
- the degree of plasticization of the polymer film by retained solvent;
- the thickness of the cast film;
- the substrate used in casting;
- the thermal history; and,
- for polymers that incorporate water, both the RH maintained during the drying process and the hygroscopicity of the solvent.
All of these factors were considered in the choice of the film history of the samples prepared for testing. The objective was to isolate as much as possible the results of the influence of one parameter—the solvent chosen for casting.
The solvents were chosen for their anticipated effect on the final physical properties of the cast films. All four solvents (chloroform, acetone, toluene, and ethanol) are good solvents for PVAC in that the molecular conformation is extended in comparison to the conformation in a theta solvent, where the polymer chain is neither extended nor contracted by interaction with the solvent. The best solvent in this series is chloroform because, as can be shown by both the Huggins coefficient and the intrinsic viscosity, the polymer chain is most extended (Olayemi and Adeyeye 1982). Acetone, in addition to being a relatively poorer solvent for PVAC than chloroform, has a greater degree of polarity. The addition of ethanol to acetone increases the polarity of the solution in comparison to pure acetone. Toluene was included as a solvent due to the well-known long-range solvent retention (Newman and Nunn 1975), which allowed the effects of plasticization by residual solvent to be assessed and compared with the effects of solvent type.
Relatively dilute (4% w[g]/v[ml]) solutions were used, because higher concentrations of polymer may promote interchain interactions, and thus the physical properties may show a dependence on the concentration. This effect has been shown for the refractive index of some polymers (Ashkok and Avadhani 1987). Therefore, a consistent concentration was maintained throughout the experiment.
Although thicker films are more convenient for the physical testing of the released film, the original thickness of the films (0.08 mm) tested at a 50-day interval contained higher concentrations of both chloroform and toluene than was desirable (table 1). Because solvent retention is dependent upon both the square root of the film thickness and the amount of time following casting (Newman et al. 1975), the amount of retained solvent was reduced by decreasing the thickness of the films and increasing the drying time to six months.
TABLE 1 Solvent Retention and Glass Transition Temperature of AYAT Films at 50 Days and 180 Days after Casting from Different Solvents
The casting substrate, Teflon, permits easy release of a film of PVAC at any interval following casting. The films can therefore be studied meaningfully in relation to coatings, since the system resembles a coated surface that allows solvent release from one surface only. In addition, the surface properties of films cast on Teflon should be isotropic at both the air and Teflon interfaces because Teflon is a low surface energy substrate. Anisotropic surface properties have been observed for poly(methyl methacrylate) films formed on metal substrates (Carre et al. 1980).
It was also decided to study the films without annealing the resin since most thermoplastic polymers are applied at room temperature to objects that can not be heated above the glass transition temperature in order to drive off residual solvent. In most laboratory studies of basic “properties” resins are first annealed because the thermal history of the polymer is known to affect certain properties, especially the Tg(Slade and Jenkins 1970).
A constant humidity level was also maintained during the drying intervals to minimize variation due to the water content of the films.
3 RESULTS AND DISCUSSION
3.1 SOLVENT RETENTION
FOR THE films averaging 0.08 mm thickness, significant amounts of solvent were retained after drying the films for 50 days; especially apparent are high concentrations of chloroform and toluene. A second set of thinner films was cast and allowed to dry for 180 days in order to obtain films with less solvent. This set was cast to confirm that the effects on the mechanical and physical properties were due to solution quality or polarity of the solution-cast films and not to retained solvent and also to compare the mechanical and physical properties of these films with a plasticized film cast from a toluene solution.
Films at this interval were also analyzed for water content. Films cast from chloroform and toluene did not show the presence of water. Films cast from an acetone or acetone/ethanol/water mixture showed traces of water (>0.1%).
Two methods of evaluating solvent retention by gas chromatography were explored. The “hot-jar” method consists of heating a known amount of polymer in a closed container and then analyzing volatile contents. Pyrolysis GC consists of flashing off the volatiles at a high temperature, but the analysis also causes polymer decomposition. Greater amounts of retained solvent were found with the pyrolysis method, evidently because heating in a closed container did not fully volatize all retained solvent. Therefore, the amounts reported in table 1 are those obtained by pyrolysis GC.
Concentrations of acetone and chloroform were below the detection limits for films cast from these solvents at a 180-day interval. However, films cast from toluene retained 4% by weight of solvent.
3.2 TENSILE PROPERTIES
The tensile properties of AYAT films cast from different solvents (tables 2, 3, and 4) are highly dependent upon both the solvent used for casting and the time interval after casting.
TABLE 2a Yield-Stress and Stress-at-Break of AYAT Films at 50 Days after Casting from Different Solvents
TABLE 2b Yield-Stress and Stress-at-Break of AYAT Films at 180 Days after Casting from Different Solvents
TABLE 3 Initial Elastic Modulus of AYAT Films at 50 and 180 Days after Casting from Different Solvents
TABLE 4 Percent Strain-to-Break of AYAT Films at 50 and 180 Days after Casting from Different Solvents
Representative stress-strain curves obtained from tensile fracture at a constant rate of elongation are shown in figures 2 and 3 for samples of films dried for 50 days and 180 days, respectively. The yield-stress differs from the stress-at-break for samples with a yield point, beyond which further elongation occurs with plastic flow. After drying for 50 days, only samples from films cast from the more polar acetone/ethanol mixture have a sharp break point, exhibiting no plastic flow at this elongation rate. After drying for 180 days, samples from films cast from both acetone and an acetone/ethanol mixture fracture with the peak applied stress at 3% elongation. Samples from films cast from both chloroform and toluene continue to flow to above a 200% strain-to-break after the yield point.
Fig. 2.
Representative tensile properties at 50 days of AYAT films cast from different solvents
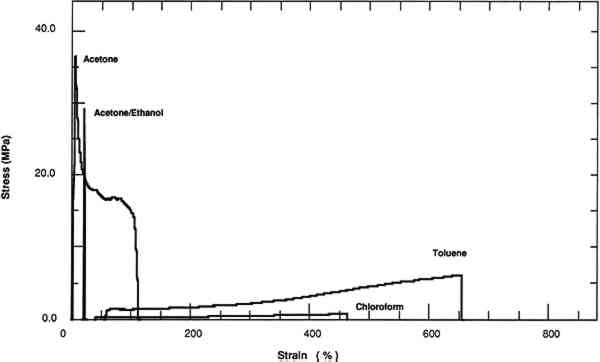 |
Fig. 3.
Representative tensile properties at 180 days of AYAT films cast from different solvents
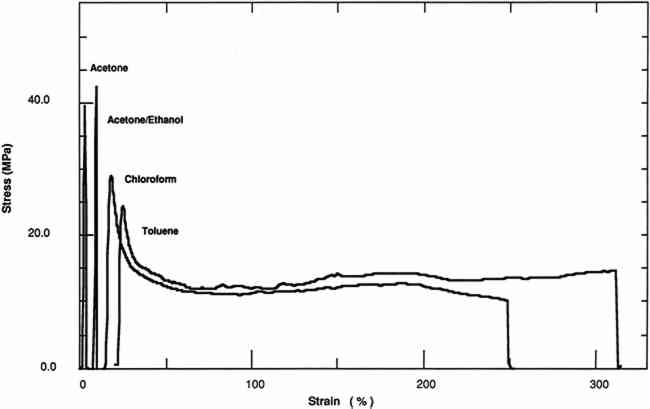 |
The initial elastic modulus increases with both drying time and solvent polarity. Again, two groups are apparent: one of higher modulus for films cast from acetone or acetone/ethanol solutions and a second of lower modulus for films cast from solutions of either chloroform or toluene.
The differences in tensile properties of the films can be related to the amount of retained solvent after 50 days of drying (see table 1). However, the data from the GC analysis for the 180-day interval confirms that the differences in the tensile properties of some films are related to solvent type and solvent retention (table 3). Only trace amounts of chloroform or acetone are still present in the films, but the tensile properties are distinctly different. When the better solvent, chloroform, is used in casting, the strain-to-break of the samples exceeds 200% compared to 3% for the acetone mixtures. With respect to films cast from toluene, the amount of retained solvent may still be important in plasticizing the films, with a resultant lower stress-to-break and greater strain-to-break compared to films cast from an acetone solution.
With time, changes in the properties of a cast resin are related not only to solvent release but also to the physical aging of the polymer. Amorphous polymeric materials move toward an increased state of brittleness with increasing time when maintained at a temperature below their Tg. In this case, performance with time should be evaluated with the understanding that increased brittleness will occur from physical aging (Struik 1978). This is a result of a thermodynamic drive toward a physical equilibrium state, in addition to the more well-known and addressed effect of chemical modifications (oxidation, hydrolysis, chain-breaking) that may also cause a more brittle state of a polymer.
Several problems exist when attempting to maximize a specific physical property of a cast resin by adjustments to the polymer/solvent mixture used for casting. Use of a different solvent may result in a different submicroporosity that affects the density and permeability of a cast film (Malkin 1983). Also, solvent mixtures are not explicitly additive in their effect on the polymer conformation due to polar interactions between the solvent and polymer.
Malkin (1983) has shown that the thermodynamic quality of the solution, as indicated by the intrinsic viscosity, cannot be used to predict a property of the resin cast from it. Instead, there are peaks in the curves for plots of intrinsic viscosity versus a mechanical property for acrylics and cellulose ethers. The tensile properties of ethyl cellulose do not correlate with solvent polarity but maximize at a 30% ethanol/toluene mixture (Tess 1985). For this polymer there is a simultaneous increase in elongation and strength, in contrast to poly(vinyl acetate) where the strength and elongation show inverse relations when changing solution quality and polarity. These results suggest that the exact effect of the solution quality and polarity on the mechanical properties of a polymer must be experimentally determined.
3.3 THERMAL ANALYSIS
The initial reason for using thermoanalytic techniques was to determine if the level of solvent was sufficient to cause plasticization of the films. Plasticizers are materials incorporated into other materials to increase flexibility, distension, or workability. Plasticizers, either intentionally incorporated or a result of retained solvent, may lower the melt viscosity, the second-order transition temperature, or the elastic modulus of a resin (Sears and Touchette 1982). The lower strength and greater elongation exhibited by resins plasticized due to retained solvent may be attributable to a lowering of the Tg. Therefore, if the difference in mechanical properties was due to retained solvent plasticizing the films and not necessarily an effect of the type of solution used for casting, these films would be expected to show a glass transition temperature below 22�C, the experimentally determined Tg of the bulk polymer. (This Tg is less than the Tg of PVAC, 28–31�C, listed in the Polymer Handbook[Lindeman 1975]).
The Tg values shown in table 1 were unexpected and demonstrate a further influence of prior processing on the physical properties of a polymer. At a 50-day drying interval, films cast from the more polar solutions of acetone and ethanol (which are also the poorer solvents), have a Tg 18�C to 29�C above the near-room temperature Tg of bulk PVAC. After a 180-day drying interval, the Tgs of the films, including a film with 4% toluene, are elevated above the Tg reported for the bulk polymer. At this interval the Tgs of the films cast from all solvents are above 40�C.
The Tg is generally considered a “basic” property of a polymer and not subject to the influence of processing, unless the thermal history of the polymer is varied. As the observed variation in the Tg is not related to specific solvents but is related instead to the amount of retained solvent in the polymer films, the elevated Tg of the polymer may therefore result from the solution deposition process alone. As the Tg is often a critical property in the selection of a resin for a particular use in conservation, this observation deserves much further consideration.
3.4 INFLUENCE OF MOLECULAR WEIGHT
Lower molecular weight grades of PVAC are more often used in conservation than AYAT (MW = 226,000). Because the effects of coiling and uncoiling of polymer chains might be less in polymers of lower molecular weights, the tensile properties and Tg of films of a lower molecular weight PVAC, AYAF (MW = 169,000), were determined and shown in table 5.
TABLE 5 Tensile Properties and Tg of 0.03 mm AYAF Films at a 180-Day Interval after Casting
The same effect is seen in films of the lower molecular weight grade PVAC in the same thickness, 0.03 mm, and at the same time interval after drying as for the higher molecular weight grade. For a nonpolar good solvent for PVAC, chloroform, there is pronounced elongation before breaking and lower tensile strength. For a more polar and poorer solvent for PVAC than chloroform, acetone, little elongation before breaking and higher tensile strength is evident. Also, the Tg is elevated for films cast from either solvent.
3.5 FOURIER TRANSFORM INFRARED SPECTRA
Further evidence of the change in conformation of the deposited film can be inferred from the measurements taken from the FTIR spectra of the PVAC molecular weight series (table 6). The PVAC resins were analyzed using chloroform and acetone as solvents. When the resins were prepared with chloroform there were noticeable spectral changes in the sizes of the methyl and methylene bands that correspond to the molecular weight progression of the polymer resins. Specifically, there is an increased absorption by the carbon-hydrogen bonds of methylene groups at 1373 cm−1 relative to that by terminal methyl groups at 1435 cm−1. Since a large polymer contains more methylene groups relative to the methyl groups at the end of the chain, it appears that each carbon-hydrogen bond has freedom of movement and thus that the absorptions are proportional to the species present.
TABLE 6 Ratio of Methylene to Methyl Infrared Absorption Bands of AYAT, AYAC and AYAA Deposited on KBr from Chloroform and Acetone
The PVAC samples prepared with acetone do not exhibit the same changes in spectral band intensity. In fact, the spectra of the samples with different molecular weights were all similar. One explanation for this apparent solvent dependence is that the chloroform disperses and separates the polymeric chains while the acetone solvation produces polymeric aggregates. Within such an aggregate the chain may be folded in such a conformation that some molecular vibrations are inhibited.
In comparing the two solvent systems, the highest molecular weight resin, AYAT, showed the most noticeable spectral differences. As an additional check, AYAT was prepared for analysis without using a solvent (i.e., grinding the bulk resin), which resulted in a spectrum more closely resembling the AYAT sample prepared with acetone. Thus, overall, the FTIR can discern morphological differences in the polymer that are specific to the solvent used in sample preparation.
4 CONCLUSIONS
A LARGE quantitative effect on the physical properties of thermoplastic polymers may result from the solvent chosen for application. The theoretical explanation is that the polymer conformation in solution affects the physical properties of the solid film and that the conformation differs in solvents of differing quality or polarity.
The change in physical properties persists with time, but is modified with time. This phenomenon may be specifically related to the desired performance of a coating, adhesive, or consolidant used for the conservation of an art object. Optimum performance should be gained from attention to solvent “type” and polarity and the experimentally determined effects on the polymer properties. Not only may polymer performance be optimized, but also the failures of polymers to perform as expected may be avoided. Furthermore, it can be seen that in this era of increased limitation of toxic substances replacing one solvent with a less toxic one could result in an unexpected performance of a resin for a specific purpose in the conservation of a work of art.
These effects are an important consideration for several materials that are widely used in conservation and applied from solutions of organic solvents: PVAC, acrylics, and cellulose ethers. Because the cellulose ethers soluble in organic solvents have been shown to have less potential use in conservation due to poorer performance in aging studies in comparison with the cellulose ethers that are water-soluble (Wilt and Feller, 1990), further exploration of these effects should concentrate on the acrylic polymers, such as Acryloid B72. In addition, research is currently being planned to find suitable solvents or solvent combinations to replace chloroform when it is desirable to have the most flexible PVAC of a certain molecular weight grade.
ACKNOWLEDGEMENTS
WE WOULD like to thank Robert Feller, director emeritus, Center for the Materials of the Artist and Conservator, Mellon Institute, for his encouragement in this project; Frank Preusser, associate director, Getty Conservation Institute, for his encouragement and support; Cecily Druzik, assistant scientist, Getty Conservation Institute, for the GPC analysis of PVAC molecular weights; and Steve Lee, student assistant, Getty Conservation Institute, for his assistance in preparing this manuscript. Portions of this paper were presented at the AIC annual meeting in Cincinnati, Ohio, June 1989.
NOTES
1. THE PVACs were obtained from Conservation Materials in Sparks, Nevada. The designations AYAC, AYAA, AYAF, and AYAT are copyrighted trade designations of Union Carbide.
REFERENCES
Ashkok. J., and S. S. S. S. V.Avadhani. 1987. Preparation and elipsometric study of polymer films. Indian Journal of Pure and Applied Physics25:239–41.
ASTM. 1989. 1989 Annual book of ASTM standards. Philadelphia: American Society for Testing Materials. 6.01:324–27.
Briscoe, B., and A. C.Smith. 1983. Rheology of solvent-cast polymer films. Journal of Applied Polymer Science28:3,827–48.
Carre, A., D.Gamet, J.Schultz, and H. P.Schreiber. 1986. Non-uniformity in thin polymer films. Journal of Macromolecular Science-ChemistryA23(1):1–18.
Daniels, F., and R.Albertyh. 1975. Physical chemistry, 4th ed.New York: John Wiley and Sons. 655.
Druzik, Cecily. 1987. GPC determination of PVAC molecular weights. Getty Conservation Institute internal report.
Feller, R. L.1978. Standards in the evaluation of thermoplastic resins. ICOM Committee for Conservation Preprints, 5th Triennial Meeting, Zagreb, 16(4):1.
Haas, H. C., L.Farney, and C.Valle, Jr.1965. Some properties of ethylcellulose films. Journal of Colloid Science7:584–99.
Hansen, E. F., and A. G.Taketomo. 1989. A technical note on the casting of unsupported polymeric films. Studies in Conservation34:147–51.
Kurbanaliyiyev, M. K., I. K.Dustov, and A. Ya.Malkin. 1982. Influence of the prehistory of formation of films from solutions on their longevity. Polymer Science U.S.S.R.24:2,626–34.
Lindeman, M. K.1975. Physical constants of poly(vinyl acetate). In Polymer handbook, ed.J.Brandup and E. H.Immergurt. New York: John Wiley and Sons. 5:51–54.
Malkin, A. Ya.1983. Strength and long-term fracture of polymers formed from different solvents. Polymer Process Engineering1(1):93–108.
Materovsyan, M. S., A. A.Askadski, G. L.Slonimskii, and Ya. V.Genin. 1985. Effect of processing history of amorphous polymeric films specimen on their relaxation properties. Polymer Science U.S.S.R.27:2,165–72.
Newman, D. J., C. J.Nunn, and J. K.Oliver, 1975. Release of individual solvents and binary solvent blends from thermoplastic coatings. Journal of Paint Technology47:70–78.
Olayemi, J. Y., and A. A.Adeyeye. 1982. Some properties of polyvinyl acetate films cast from methanol, acetone and chloroform as solvent. Polymer Testing3:25–35.
Schreiber, H. P., and M. D.Croucher. 1980. Surface characteristics of solvent-cast polymers. Journal of Applied Polymer Science25:1961–68.
Schilling, M. R.1989. The glass transition of materials used in conservation. Studies in Conservation34:110–16.
Sears, J. K., and N. W.Touchette. Plasticizers. Encyclopedia of chemical technology, 3d ed. New York: John Wiley and Sons. 18:111.
Slade, P. E., Jr., and L. T.Jenkins. 1970. Thermal characterization techniques. New York: Marcel Dekker, Inc.32–35.
Struik, L.C.E.1978. Physical aging in amorphous polymers and other materials. New York: Elsevier. 1.
Tess, R. W.1985. Solvents. In Applied polymer science, ed.R. W.Tess and G. W.Pohlein. Washington, D.C.: American Chemical Society. 668–69.
Wilt, M., and R. F.Feller. 1990. Evaluation of cellulose ethers for conservation. Los Angeles: Getty Conservation Institute. 93–99.
AUTHOR INFORMATION
ERIC F. HANSEN graduated from the University of California at Irvine in 1980 with an M.S. in organic chemistry and joined the Getty Conservation Institute in 1985. In his current position as an associate scientist he is pursuing his interests in the environmentally induced deterioration of synthetic and natural organic materials (including collagen, fibroin, and keratin), the conservation of ethnographic and archaeological objects, and the analysis of the effects of treatment parameters on the final physical and optical properties of treated objects. Address: Getty Conservation Institute, 4503 Glencoe Ave., Marina del Rey, Calif. 90292.
MICHELE R. DERRICK graduated from Oklahoma State University in 1979 with an M.S. in analytical chemistry. She joined the Getty Conservation Institute in 1983 and is currently an associate scientist. Her research involves the development of new methods for the characterization and identification of organic materials in cultural objects primarily using infrared spectroscopy and pyrolysis gas chromatography. Address: Getty Conservation Institute, 4503 Glencoe Ave., Marina del Rey, Calif. 90292.
MICHAEL R. SCHILLING graduated from California State Polytechnic University at Pomona in 1990 with an M.S. in chemistry. He joined the Getty Conservation Institute in 1983 and is currently an associate scientist. He specializes in thermal analysis research, the examination of painted surfaces, and instrumental analysis (gas chromatography-mass spectroscopy). Address: Getty Conservation Institute, 4503 Glencoe Ave., Marina del Rey, Caif. 90292.
RAFAEL GARCIA worked at the Getty Conservation Institute as a student assistant from 1987 to 1989 while pursuing undergraduate studies in chemistry at Loyola Marymount University. He received his B.S. in 1989 and is currently a graduate student in chemistry at California State University at Long Beach. Address: Getty Conservation Institute, 4503 Glencoe Ave., Marina del Rey, Calif. 90202.
Section Index |