A COMPARATIVE STUDY OF SILVER CLEANING ABRASIVES
GLENN WHARTON, SUSAN LANSING MAISH, & WILLIAM S. GINELL
3 EXPERIMENTAL METHODS AND MATERIALS
MOST OF the 13 abrasives used in this study have been used either historically or are in current use by conservators. Some of the abrasives that are not generally used by conservators were investigated for their potential as abrasive cleaning materials.
The two carrier fluids used in these tests are in common use by conservators. The first was a mixture consisting of 15 ml of reagent grade denatured ethyl alcohol with five drops of ammonium hydroxide (30%) (Plenderleith and Werner 1979). The second fluid was composed of 15 ml of deionized water and 5 drops of Triton X-100, a nonionic surfactant (approximately 0.02% by weight). Because the focus of this project was on abrasives, other carrier fluids were not studied. Nor were the efficacy of combining water and alcohol, the use of other alcohols, or the use of additives in the fluids considered. All experiments on silver samples were performed using Curity 100% cotton diapers as the abrasive support cloth. Systematic testing of cloths was not carried out at GCI.
Triplicate silver test samples were prepared from 18-gauge (1.05 mm) cold-rolled, sterling silver sheet. Discs, 19 mm diameter, were punched from the silver sheet and embedded in black phenolic resin using standard metallographic techniques. A hole was drilled and tapped into the back of the resin mount to allow the samples to be mounted in the polishing device. The silver samples were wet-ground with 600 grit silicon carbide paper on the polishing device to assure perpendicularity.
The silver surfaces were then hand-polished on a Buehler Ecomet V using: Fibermet, 3 micrometers (μm) silicon carbide discs; Metadi, 1.0μm diamond compound on Microcloth; and Miromet, 1.0μm cerium oxide on Mastertex cloth. Samples to be tested with cerium oxide as the abrasive were given a final polish with Metpolish (Cr2O3). After polishing, the samples were cleaned ultrasonically, rinsed with acetone, air-dried, and stored in a desiccator.
The relative loss of silver during polishing was determined by measurement of the mean change in dimensions of a set of six Knoop indentations impressed into the silver surface. The Knoop hardness measurement system employs a diamond ground to a shape that will produce an elongated, pyramidal depression in a metal. The long base axis of the depression is seven times the length of the short axis (fig. 1). The ratio of the long axis to the penetration depth (pyramid height) is 30.51, so that small changes in depth (abrasion loss of the silver surface) can be determined readily by measuring the change in length of the long, base axis. Production of the Knoop indentations (20 g load) and measurement of length changes were performed on a Leco Microhardness Tester equipped with a filar eyepiece micrometer.
Fig. 1.
Knoop indentations in diamond-polished sterling silver. 100x
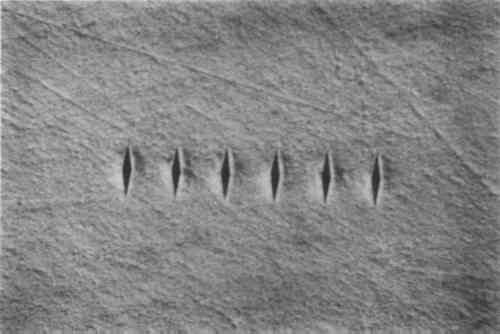 |
The silver samples were artificially tarnished in a stirred, 0.05% potassium sulfide solution for 10 minutes at room temperature. SEM measurement of a cross-section of the sulfided sample indicated that the sulfide layer varied in thickness between 0.5 and 1.0μm. Although this method of tarnish production does not replicate naturally formed tarnish, bench tests using cotton swabs, ethyl alcohol, and calcium carbonate indicated that the tarnish removal rate was similar to that of heavily tarnished art objects. Gas phase sulfidization tests resulted in poorly adherent, uneven tarnish films. Microscopic examination of a polished, sulfided sample revealed the presence of narrow, discontinuous copper-rich regions that were oriented in the rolling direction (fig. 2).
Fig. 2.
Copper-rich regions in polished, sulfided sterling silver. 100x
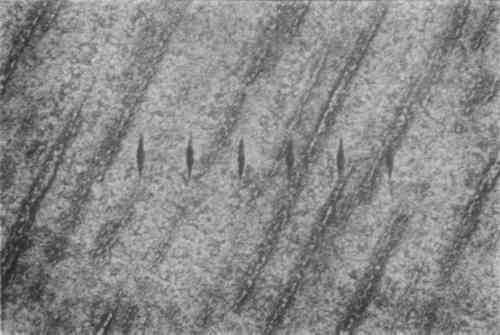 |
Polishing was performed on the polishing device shown in fig. 3. It consisted of an Eberbach shaker table modified by a motor-driven rotating spindle to which the silver specimen was mounted. The table surface was covered with 0.125-in, high-density polyethylene foam and two layers of 100% cotton diapers (Curity). The abrasive-carrier fluid slurry (5 g abrasive + 15 ml fluid) was stirred well and immediately distributed over the appropriate area of the cloth through a perforated aluminum grid (fig. 4).
Fig. 3.
Polishing device
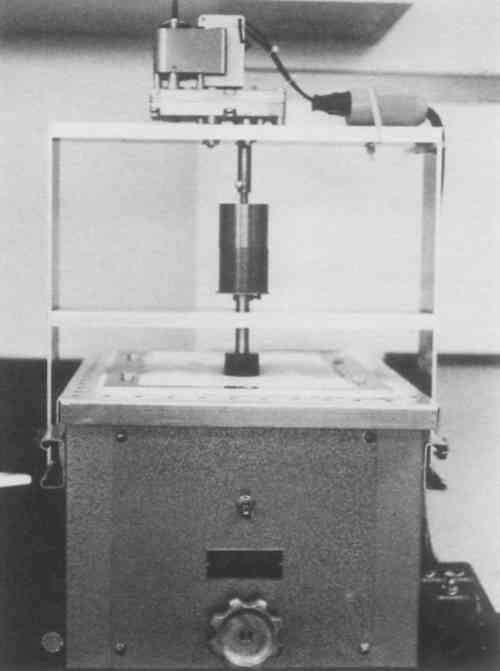 |
Fig. 4.
Application of abrasive suspension to polishing cloth
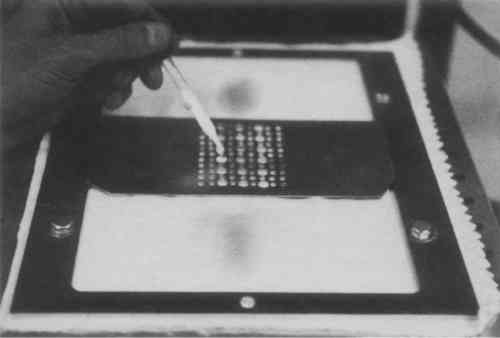 |
After the silver specimen was mounted, a constant 1-kg load was applied to the shaft. Specimens were polished for either 3 or 6 minutes at a rate of 120, 2.5 cm strokes/min and 6 circular rotations/min. A 1-kg load was selected for these tests on the basis of the measurement of the average force applied by a conservator during a manual silver polishing test.
Initially, silver samples were polished with each of the 13 abrasives for 3 minutes (E3) using alcohol as the carrier fluid. To determine the effect of polishing time, 7 abrasives were tested for 6 minutes using alcohol. To evaluate the effect of a carrier fluid change on abrasive performance, 4 abrasives in water suspension (W3) were used for 3 minutes.
During the planning phase for these experiments, consideration was also given to a procedure involving polishing for a series of short-time intervals, each followed by analyses for tarnish removal, silver loss, and scratch. Test-termination time would be determined by the achievement of a predetermined, satisfactorily tarnish-free, surface. However, this type of procedure would have been more time consuming than the one used if done in a reproducible, controlled manner and would have required the development of a quantitative method for tarnish measurement.
On the completion of the polishing operations, the long diagonal of the Knoop indentations on each of the samples was measured. Figures 5, 6, and 7 show photomicrographs of the indentations and surface condition of samples following polishing with calcium carbonate, gamma alumina, and rouge, respectively.
Fig. 5.
Silver sample polished with calcium carbonate. 250x
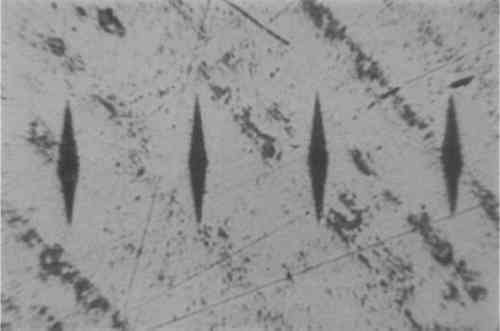 |
Fig. 6.
Silver sample polished with gamma alumina. 250x
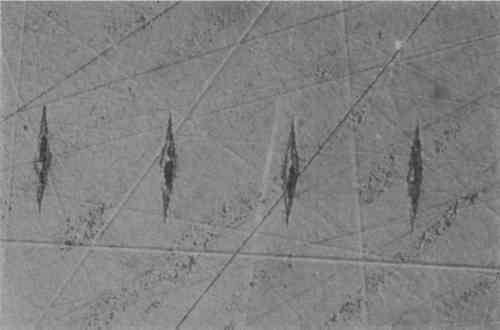 |
Fig. 7.
Silver sample polished with rouge. 250x
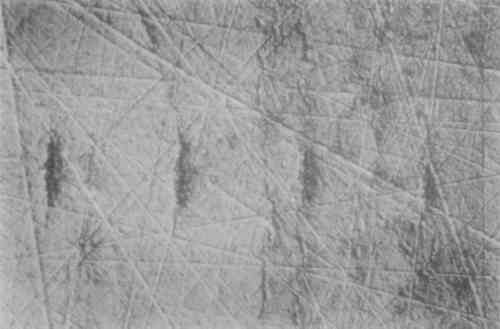 |
After calculating the mean value for each reading, the mean reduction in length, defined as Delta, was determined by subtracting the “after” reading from the “before” reading. The mean and standard deviation were then taken for all 18 indentations (6 on each of 3 samples). The numerical value of Delta was used as a measure of the relative amount of silver removed by the test abrasive.
When the polishing operations were completed, the appearance of the samples was evaluated subjectively in terms of Scratch and Tarnish. Integration of scratch depth and density was performed visually to yield a numerical rating that could be interpreted as the relative polish of the silver surface. Tarnish was judged visually on the basis of the final color of the surface after the abrasive polishing, and, again, the samples were rated numerically. The rating procedure was performed by two conservators working together under daylight fluorescent illumination in a color compensation booth (Macbeth Spectrolite).
All 78 samples to be evaluated were lined up, first in order of increasing Scratch and then in order of decreasing Tarnish. Because the first 13 samples had no visible scratches they were all rated equally and were assigned an average Scratch value of 7. The next sample in line with the least amount of visible scratches was assigned a value of 14. Similarly, the same samples were lined up in order of decreasing Tarnish. Twelve samples showed no evidence of tarnish removal, and all were assigned an average Tarnish value of 6. The next sample, with the smallest amount of visible tarnish removed, was assigned a value of 13. In this way, each sample was assigned numerical values for each of the three evaluation parameters.
|