CONTROLLING THE REFRACTIVE INDEX OF EPOXY ADHESIVES
John M. Messinger, & Peter T. Lansbury
ABSTRACT—A mixture of 1,2-epoxy-3-[2,4,6-tribromophenoxy] propane,2 and 1,2-epoxy-3-[2,4,6-triiodophenoxy]propane3 was used to increase the refractive indices of Ablebond� epoxy resin and HXTAL NYL-1� epoxy resin. The natural dark aging characteristics (for one year) of these mixtures is reported. The halogenated compounds do not seem to increase significantly the rate of yellowing of the Ablebond� mixtures.
1 INTRODUCTION
THE NEED FOR MATCHING THE REFRACTIVE INDEX of a mending adhesive to that of a broken glass object has been noted elsewhere.1,2 In an ideal world, this need could be met with a two-component adhesive system, one component of a very high refractive index and the other component of a very low refractive index. Mixing any ratio of the two components would yield an excellent glass adhesive, with the added bonus of creating an adhesive with a refractive index somewhere between the two components and dependent only on the relative amounts of each. Thus, the refractive index of the adhesive mixture could be tailored to that of the glass. Unfortunately, this adhesive system does not yet exist.
The purpose of this study was to find a compound with a very high refractive index that can be added to commercially available, two part epoxy adhesives with lower refractive indices, thereby raising the refractive index of the cured adhesive. Using this three component adhesive system (resin, hardener, and high refractive index additive), a mixture with a refractive index matching that of a cracked piece of glass might thus be obtained by varying the ratio of additive to epoxy resin.
2 DISCUSSION
IT HAS LONG BEEN REALIZED that liquids and glassy solids that contain elements with high atomic numbers will have higher refractive indices. For example, if the hydrogens in a typical hydrocarbon are replaced by halogens, a material with a higher refractive index will be obtained. High density materials also tend to have higher refractive indices. Thus, polymers that are highly cross-linked or have longer chain lengths, and therefore higher densities, are observed to have higher refractive indices than their counterparts that are not as highly cross-linked or have shorter chain lengths.3
Epoxy adhesives were chosen for this initial study because two of the most popular adhesives for glass are epoxide based, and epoxides containing several halogens can be prepared easily. It was assumed that incorporation of an epoxide group into the additive molecule would cause the additive to have minimal effects on the tensile strength of the final adhesive. Four compounds were initially investigated as potential additives. The first three are halogenated derivatives of 1,2-epoxy-3-phenoxypropane: 1,2-epoxy-3-pentabromophenoxypropane (compound 1), 1,2-epoxy-3-[2,4,6-tribromophenoxy]propane (compound 2), and 1,2-epoxy-3-[2,4,6-triiodophenoxy]-propane (compound 3). Compound 4 is the diglycidyl ether of tetrabromo bisphenol A. The hydrogen analogues of these compounds are present in many commercially available epoxy adhesives.4
Fig. .
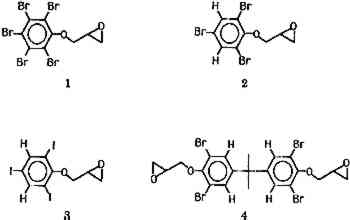 |
Precursors to these materials are particularly inexpensive due to their industrial use as fire retardants.5 All four were prepared from the corresponding phenol and epichlorohydrin in ca. 90% yield (scheme I), by an established procedure.6
Fig. .
scheme 1
 |
3 RESULTS
IT WAS ESTABLISHED rather early in this study that the pentabromo material (compound 1) and the bisphenol A derivative (compound 4) had low solubilities in the commercial resins utilized. As a consequence, they crystallized from the prepared adhesive mixtures to give cloudy, white, solid masses of polymerized resin. This phenomenon would occur even if the halogenated compounds were in low concentration and the halogen:resin mixtures were held at temperatures any lower than about 60�C.
This problem of crystallization persisted even with the trihalogenated compounds (2 and 3). However, when these compounds were mixed in a 1:2 ratio (2 to 3 by weight), much higher concentrations of halogenated compound to epoxy resin could be realized (as much as 2:1 by weight epoxy resin:halogenated compounds), and lower temperatures (30�C under a heat lamp) could be used. Hereafter, all references to “halogenated material” will describe this 1:2 (by weight) mixture of compounds 2 and 3.
Ablebond� resin and HXTAL NYL-1� resin were the commercially available resins chosen for this initial study, as they are two of the most popular resins that conservators use for glass restoration. Halogenated material was added to Ablebond� resin and HXTAL NYL-1� resin in varying proportions. Hardener also was added in varying proportions, disregarding the manufacturers' instructions for a specific proportion of hardener to be mixed with a specified quantity of resin. The samples were cast as small blocks. In this manner, 108 different samples were prepared of 45 different ratios of resin-to-halogenated material-to-hardener. The refractive index of each of the resulting samples was determined. These data were organized in two different ways. First, the refractive index of each sample with a particular proportion of hardener was graphed versus the ratio of commercial epoxy resin to halogenated material (by weight). This was done for Ablebond� resin (graphs 1–4) and HXTAL NYL-1� resin (graphs 5–8). The straight lines in these graphs were fit by the method of least squares. Next, the refractive index of each sample with a particular ratio of commercial epoxy resin to halogenated material (by weight) was graphed versus the proportion of hardener. This was done for Ablebond� resin (graphs 9–12) and HXTAL NYL-1� resin (graphs 13–15).
Fig. 1.
Graphs 1 and 2
 |
Fig. 2.
Graphs 3 and 4
 |
Fig. 3.
Graphs 5 and 6
 |
Fig. 4.
Graphs 7 and 8
 |
Fig. 5.
Graphs 9 and 10
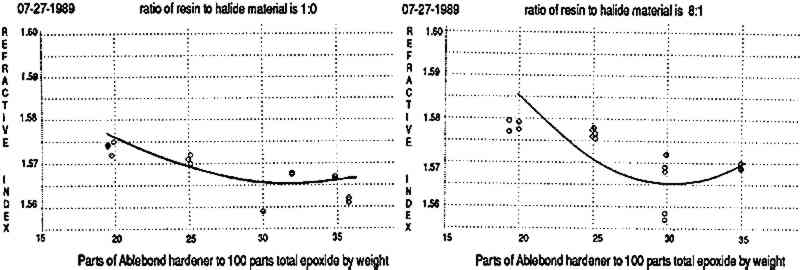 |
Fig. 6.
Graphs 11 and 12
 |
Fig. 7.
Graphs 13 and 14
 |
Fig. 8.
Graph15
 |
Graphs 1–8 show that the refractive index does indeed increase with increasing proportion of halogenated material in the mixture. These graphs also show that the refractive index of any particular ratio of components (even for pure resin and hardener) is not as reproducible as one might hope.
When the data are reexamined with refractive index graphed versus proportion of hardener present, one obtains the set of U shaped curves depicted in graphs 9–12 and to a certain extent in graphs 13–15. The curve minima are located approximately at the concentration of hardener to total resin (resin plus halogenated material) recommended by the manufacturers of the respective resins. Presumably, this may be interpreted in the following manner. With decreasing proportions of hardener, there is a corresponding increase in the proportion of halogen-containing material present in the total adhesive mixture, causing an increase in refractive index. As the proportion of hardener is increased, the relative amount of halogen containing material in the total adhesive mixture is decreased and the refractive index falls. Concurrently, however, as the proportion of hardener is increased, the proportion of cross-linking is also increased. This effect does not become particularly influential until the proportion of hardener in the mixture exceeds the manufacturer's recommendation, creating a material of particularly high density and thus higher refractive index. Note at this point that the refractive indices of both hardeners are significantly lower than those of the resins, the cured adhesives, and, of course, the halogenated material. Thus, if adhesives with very high refractive indices are to be obtained with this three-component system, a hardener containing many halogens is likely to be essential.
The natural dark aging characteristics of the epoxy blocks containing the halogen additive were investigated for one year of aging in a light-tight box at ambient temperature. The initial color of the HXTAL� resin-based mixtures is much more yellow than the Ablebond� resin-based mixtures, particularly at low hardener concentrations. After one year the average At∗ value for the Ablebond� samples was 0.01, with a sample standard deviation of 0.005, well below the universally acceptable limit of 0.1, as determined by Down.4 The average At values for the best HXTAL� samples after one year was 0.23 with a standard deviation of 0.08. In accordance with Down,4 an At value of 0.23 puts the best possible blocks of HXTAL� in the category of “questionable acceptability” when used with these halogenated additives. The yellowness of the HXTAL� samples is highly dependent on the proportions of hardener and halide used and on the curing temperature. In particular, when HXTAL� was used with less than the manufacturer's recommended amount of hardener and any of the halogenated material at all, significant yellowing of the cured adhesive resulted. HXTAL� samples containing halide and cured at a temperature in excess of 60�C were too highly absorbing in the 380 nm wavelength range for our instrument to measure, and thus their At values can be considered to be well into the unacceptable range.
∗
Fig. .
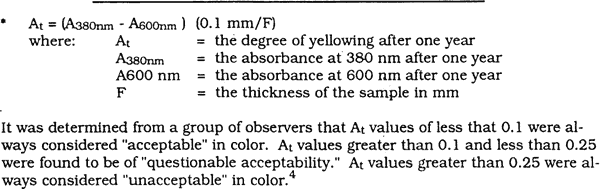 |
4 CONCLUSIONS
ONE CAN INDEED RAISE THE REFRACTIVE INDEX of two commercially available epoxy resins with additives 2 and 3, albeit to a limited degree. The refractive index of Ablebond� can be raised from about 1.565 to about 1.59. That of HXTAL� NYL-1 can be raised from about 1.515 to about 1.545. While the addition of these additives does cause yellowing in the cured HXTAL� resin, the amount of yellowing imparted to Ablebond� is well within acceptable limits. Decreasing the proportion of hardener present in an epoxy mixture does not seem to affect the tensile strength of Ablebond� until the proportion of hardener is below 22 parts hardener per 100 parts resin.∗ (32 to 100 is recommended for Ablebond�.) Decreasing the proportion of hardener present in an epoxy mixture does not affect the tensile strength of HXTAL� until the proportion of hardener is below 17 parts hardener per 100 parts resin. (25 to 100 is recommended for HXTAL�.) With low concentrations of hardener, both of these mixtures may be readily softened with methylene iodide and bromonaphthalene.
∗ Tensile strength was considered normal if manual flexing did not crack the epoxy blocks and/or a fingernail could not dent the blocks.
5 EXPERIMENTAL
A SARGENT-WELSH PYE UNICAM SP8-150 ultraviolet-visible wavelength spectrophotometer was used for absorbance measurements. A Bausch and Lomb 33-45-52 Abbe type refractometer was used for measuring the refractive index of cast epoxy blocks. Cargille immersion liquids were used in conjunction with the Becke line test for determining the refractive index of glass pieces. Halogenated compounds were prepared by standard methods of synthetic organic chemistry.
Physical Data of Compounds:
Typical preparation of epoxy samples: 12.00 g of Ablebond� resin, 0.67 g of 1,2-epoxy-3-[2,4,6-tribromophenoxy]propane (2), and 1.33 g of 1,2-epoxy-3-[2,4,6-triiodophenoxy]propane (3) were placed in a 10 ml beaker. The mixture was gently warmed over a microburner to dissolve the halogenated compounds in the resin. The mixture was kept warm either on a hotplate or in front of a heat lamp until ready for use and was used to prepare all 6:1 resin-to-halogenated compound samples. This mixture was divided into four portions. To the first was added enough hardener to prepare a 100:20 parts-by-weight mixture of resin:hardener. This material was cast into ca. 3 mm � 12 mm � 20 mm blocks in warmed molds made of silicon molding material. The mixed adhesive was cured at 50�C in an oven or at about 40�C in front of a heat lamp. Resin-to-hardener ratios of 100:25, 100:30, and 100:35 were prepared in like fashion. After curing for 24 to 48 hours the blocks were removed from the molds, and their six faces were ground and polished with 1 micron alumina.
6 HEALTH AND SAFETY NOTE
EPICHLOROHYDRIN IS A KNOWN CARCINOGEN, and chronic exposure can cause liver damage. Epoxides are a member of a class of compounds known as alkylating agents. Most alkylating agents have been found to be carcinogens. No MSDS is available for the halogenated additives, as they are new compounds.
ACKNOWLEDGEMENTS
FUNDING FOR THIS STUDY was provided by the State University of New York at Buffalo Graduate Research Initiative Visiting Professor Research Program. The authors wish to acknowledge F. Christopher Tahk and Dan Kushel for lively discussions and helpful suggestions.
REFERENCES
Ogden, Paul H.“A New Glass Adhesive.” Paper presented at IIC 6th International Congress, Stockholm (1975).
Tennent, N. H., and J. H.Townsend. “The Significance of the Refractive Index of Adhesives for Glass Repair”, in Adhesives and Consolidants (London: IIC, 1984): 205–212. Tennent, N. H., and J. H.Townsend. “Factors Affecting the Refractive Index of Epoxy Resins.”ICOM Committee for Conservation, 7th Triennial Meeting, Copenhagen, (1984), Vol. 2: 84.20.26–84.20.28.
Lange's Handbook of Chemistry, 7th ed., 1052. Sandusky, Ohio: Handbook Publishers, Inc., 1949.
Down, Jane L.“The Yellowing of Epoxy Resin Adhesives: Report on Natural Dark Aging.”Studies in Conservation29 (1984): 63–76.
Sherman, S., J.Gannon, G.Buchi, W.R.Howell“Epoxy Resins.” In Kirk-Othmer, Encyclopedia of Chemical Technology, 3d ed.9:267. New York: John Wiley & Sons, 1980. Larson, E. R.“Flame Retardants.” In Kirk-Othmer, Encyclopedia of Chemical Technology, 3d ed., 10:373. New York: John Wiley and Sons, 1980.
Kiersznicki, Tadeusz, ZbigniewNajzarek, and WieslawSzeja, (Politechnika Slaska). Pol. 86,612, 15 December 1976, Chemical Abstracts90:87234j.
Section Index |