AN EPOXY/MICROBALLOON MIXTURE FOR GAP FILLING IN WOODEN OBJECTS
R. Barclay, & C. Mathias
3 MECHANICAL TESTS
TESTS UNDER BOTH COMPRESSION AND TENSION were conducted on various mixtures of the microballoons and epoxy resin in order to establish a mixing ratio which gave a workable fill material with a strength below that of wood. Clearly, the strength of the wood is a factor which will vary depending upon the artifact in question. For this study the fill material was compared to fresh, kiln-dried western red cedar because this is a weak wood, with a low modulus of compression and low strength across the grain, and thus serves as a good model for deteriorated woods.
3.1 Compression Tests
Four ratios of epoxy resin to microballoons were chosen: 0.5 to 1, 1 to 1, 1.5 to 1 and 2 to 1 by weight. One centimeter cubes of these ratios were cast in a mold and allowed to cure for at least three days before testing (Figure 2). Ten cubes of each ratio were subjected to compression in an Instron compression and tensile testing instrument (Model TM, with 500kg load cell) with a cross head speed of 50mm/min. A set of similar blocks of western red cedar was subjected to the same test to afford a comparison. This test had been established previously in the absence of a comparable standard test for this purpose.8 Thus, the results are internally consistent only.
Fig. 2.
Test blocks of epoxy/microballoon filler and the mold in which they were cast.
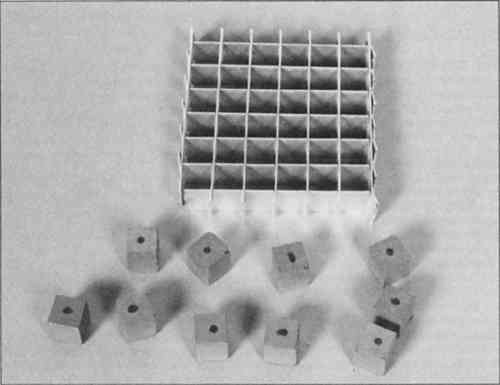 |
Figure 3 shows the point of failure of each of the ratios compared to that of cedar. Point of failure was determined as the point where irreversible compression or breakage took place. The stress/strain curve deviated from the linear at this point. For cedar, failure is sudden and dramatic, as shown in Figure 4a. The epoxy/microballoons mixture, on the other hand, exhibits the gradual change seen in Figure 4b, so that a true point of failure must be extrapolated from the portions of the curve before and after the change. From these data it can be seen that the 0.5 to 1 and the 1 to 1 mixtures have a compressive strength below that of the wood (16.2kg/cm2 and 29.9kg/cm2 respectively).
Fig. 3.
Point of failure of epoxy/microballoon test pieces and samples of western red cedar. Each plot represents 10 readings.
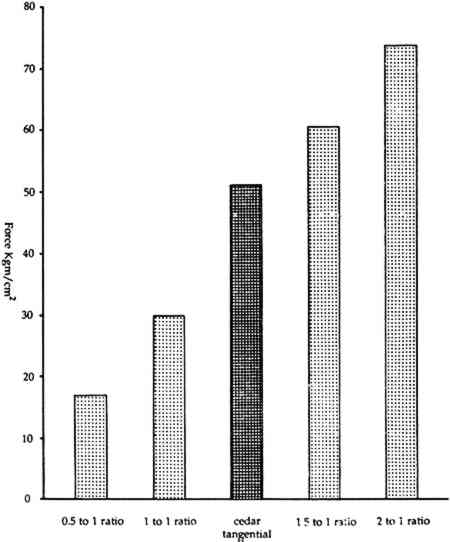 |
Fig. 4.
Characteristic stress/strain curves for a) western red cedar and b) epoxy/microballoon test sample.
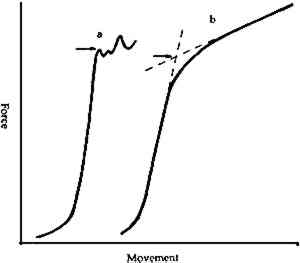 |
3.2 Tensile Tests
In cases where it is desirable to attach the fill firmly to the sides of the void it must be ensured that the fill is weaker under tension that the wood surrounding it. Shrinkage of the artifact will result in failure of the fill, not the wood. In this set of tests 1cm blocks of the same ratios of filler as the compression tests were cast between pieces of cedar so that the grain lay horizontal to the fill (Figure 5). In this orientation the test piece models the behaviour of an actual fill under tension. Before application of the filler the wood was first coated with the liquid epoxy resin to provide a sound bond between fill and wood. Although this procedure does not necessarily follow that actually used in filling a void in an artifact., it was obviously necessary in testing the filler under tension to ensure a good bond between it and the wood. When applying the filler to an artifact good adhesion may not be necessary. The test pieces were subjected to tensile stress in the Instron tester at a cross head speed of 50mm/min as above, and the site of failure noted. Site of failure was considered a more important indicator than the actual tensile strength required to break the sample, although the latter was recorded. Samples either failed within the wood, within the fill, or at the boundary of the two. The site of failure of the tests pieces is shown in Figure 6. These results indicate that failure of the weaker mixtures occurs in the majority of cases, either at the wood/fill interface or within the fill. Only in the 2 to 1 mixture was failure within the wood observed.
Fig. 5.
Tensile test samples showing the epoxy/microballoon mixture inserted between sticks of western red cedar.
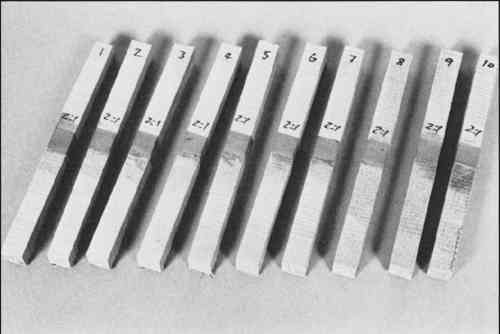 |
Fig. 6.
Site of failure under tension of epoxy/microballoon samples.
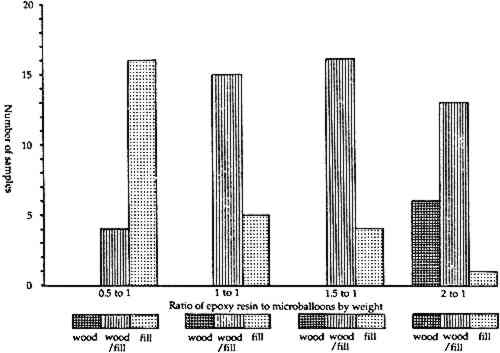 |
3.3 Mixing
Mixing a 1 to 1 ratio by weight of the filler poses problems as the volume of the microballoons is about fifty times greater than that of the resin. It is best to pre-weigh the microballoons into a sealable plastic bag and to add the mixed resin into a well in the centre. If the resin contacts the walls of the bag it tends to be less easy to mix it with the microballoons. The bag is then sealed and the mixture kneaded until thoroughly mixed. The putty has a usable life of between 15 and 30 minutes.
|