HOT MELTING CUTTING OF STABILTEX
Fonda G. Thomsen
3 WORKING TECHNIQUES AND RESULTS
3.1 Hot Melt Cutting
Using a metal straight edge, the fabric can be “hot melt” cut, on a glass surface, to give a clean straight edge that does not unravel (Fig. 1). The temperature of the blade should be adjusted to give a melt and not a “burn.” This can be verified by examination under the microscope. By placing a thin strip of glass on the historic object and cutting the Stabiltex free hand, a curved or wavy line can be followed to get an exact match.
Fig. 1.
Hot melted edge magnified 5x
 |
3.2 Encapsulation
A piece of fabric or ribbon can be encapsulated between two layers of Stablitex without sewing. The fabric is placed between the two layers of Stablitex. Using a half round metal ruler to keep a downward pressure on the Stabiltex, the two layers of Stabiltex are hot melt cut together (Fig. 2). This allows them to join, thereby encapsulating the fabric. The key to success is the curved metal ruler. There must be a downward pressure on the two Stabiltex layers at the melt site to get them to fuse. The same result can be accomplished by holding a thin metal straight edge perpendicular to the Stabiltex layers, but this was cumbersome for extensive use. To obtain the best results, the temperature of the tip and the speed at which you cut must be carefully adjusted. This is a skill which must be developed by trial and error.
Fig. 2.
Technique of melting two edges together
 |
3.3 Seaming
Two layers of Stabiltex can be joined to make a wider fabric. The two edges of the fabric are stacked. Using the curved ruler and downward pressure at the desired seam location, the two layers are hot melt cut together producing a fused seam. The edge should be given a few minutes to cool before the fabrics are opened and the seam stressed (Fig. 3).
Fig. 3.
Seamed Stabiltex magnified 5x
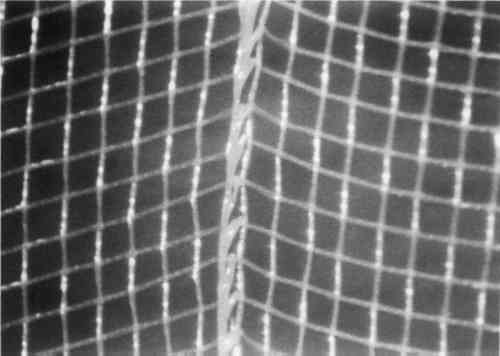 |
This technique can be used to cover three dimensional objects with Stabiltex. The Stabiltex is wrapped around the object. Where a seam is desired, the two selvage edges of the Stabiltex are held firmly together with a pair of long nosed fine tweezers. The hot knife is then run along the top edge of the tweezers, cutting away the excess fabric and producing a hot melt seam (Fig. 4).
Fig. 4.
Seaming on three dimensional objects
 |
3.4 Overlay
An applique, embroidery or beadwork may have a weak ground that you want to sandwich, but than should not cover the decorative work. By laying a thin piece of glass over the historic object, then the placing the Satbiltex on top, the areas of design can be hot melted out. This levaes the decrated areas open when the Stabiltex is placed over the textile for sandwiching (Fig. 5).
Fig. 5.
Voids created for overlay
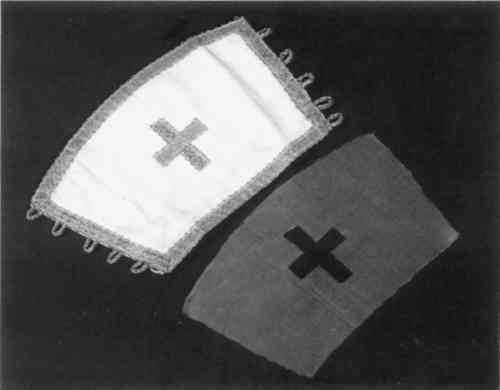 |
3.5 Butt Seams
A large United States national flag was covered with alternating layers of red and white Stabiltex. A different color of Stabiltex was needed over the heading. This would require butt seaming the Stabiltex in place. This would have been difficult to do without leaving the seam allowance on the surface. To avoid this, another technique was worked out. Cotton threads, the length of the heading, were soaked in a thermoplastic adhesive. The coated threads were placed along the desired seam line of each fabric. The seam allowance of each edge was rolled around the thread to the underside, then heat set with a tacking iron. The two edges were joined with a ladder stitch, making sure stitches went around the encased thread, giving a smooth strong seam. The seam allowances were now underneath and the seam was strong and smooth (Fig. 6).
Fig. 6.
Butt seaming—x section
 |
3.6 Silk Crepeline
Silk crepeline is still in widespread use in spite of its fragility because of its receptivity to dying. In some situations, the Stabiltex does not have a suitable color to produce the desired effect. Silk crepeline suffers from some of the same shortcomings as the Stabiltex. The edges fray and the plain weave distorts readily. Therefore, an attempt was made to apply some of the Stabiltex techniques to silk crepeline.
Silk does not have as wide a temperature range in the liquid state polyethylene. When heated, the silk would quickly char rather than melt and flow. By carefully controlling the temperature setting, a melted clean edge was finally obtained. The melted edge is more desirable than a cut edge because it doesn't fray as readily, but it is not as stable as the edge obtained on the Stabiltex. Overlay and butt seaming techniques were very successful with the silk. There was not, however, enough fiber melt to achieve seaming or encapsulation.
|