QUANTITATIVE STUDY: THE EFFECTS OF SIZED MATERIALS AND “DRYING TIME” IN THE USE OF LASCAUX 360 HV AS A LINING ADHESIVE
Danielle Allard, & Kenneth B. Katz
4 DISCUSSION
AS CAN BE SEEN in the tables and graphs, quantitative differences in peel and lap/shear strengths were noticed when the two tested lining parameters were varied.
It can be safely assessed that sizing the original canvas does increase bond strength. Table 1 shows that the values obtained with the samples of sized Belgian linen (s) were consistently higher than the values obtained when the Belgian linen was unsized (u). 1 Us (unsized polyester-sized linen) has an average peel strength of .21 Kg/cm compared to 1 Uu (unsized polyester-unsized linen) which has an average peel strength of .12 Kg/cm. Also 1 Ss (sized polyester-sized linen) has a value of .26 Kg/cm which is higher than the .10 Kg/cm value obtained with 1 Su (sized polyester-unsized linen). Test results from samples dried for 24 hours were also consistent in this trend.
Table 1 Summary of Data for Peel Tests
Table 2 Summary of Data for Lap/Shear Tests
However, sizing the lining canvas did not necessarily have the same effect. In fact, in the case of Su (sized polyester-unsized linen), the peel strength was slightly lower, .10 Kg/cm, than in the case Uu (unsized polyester-unsized linen) which recorded .12 Kg/cm. Since the separation in all cases occurred between the original canvas and the lining adhesive, it is to be expected that sizing of the lining canvas should not affect the bond strength significantly. It is difficult, though, to explain the lower readings obtained with Su (sized polyester-unsized canvas). An interesting phenomenon occurred when both the original and lining canvases were sized (Ss): the bond strength was significantly higher than all other samples. It seems in this case that sizing the lining canvas did have a measurable effect on the bonding properties.
The second parameter tested was drying time. Table 1 and Figure 1 show that the average peel strength values for 1 hour drying time were slightly higher than the values for 24 hours drying time in three cases (Uu, Us, Su) and lower in one case (Ss). When both the lining components were sized (Ss), the 24 hours drying time produced a stronger bond than the 1 hour drying time: .30 Kg/cm for 24 Ss compared to .26 Kg/cm for 1 Ss. This was confirmed by the lap/shear tests where the same phenomenon occurred.
Fig. 1.
Peel tests
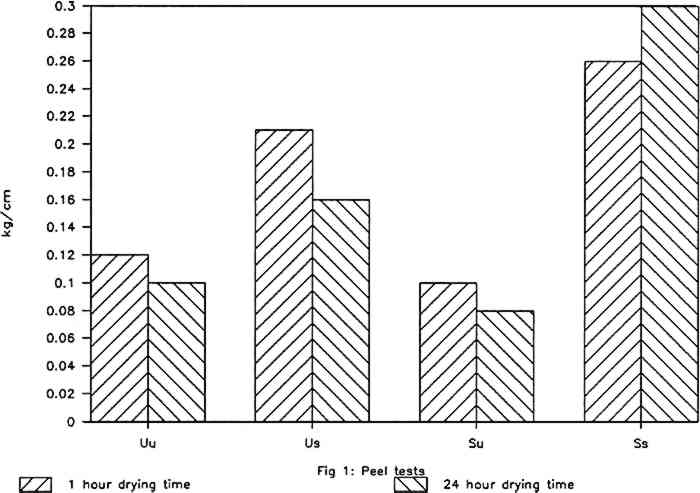 |
Fig. 2.
Lap/shear tests
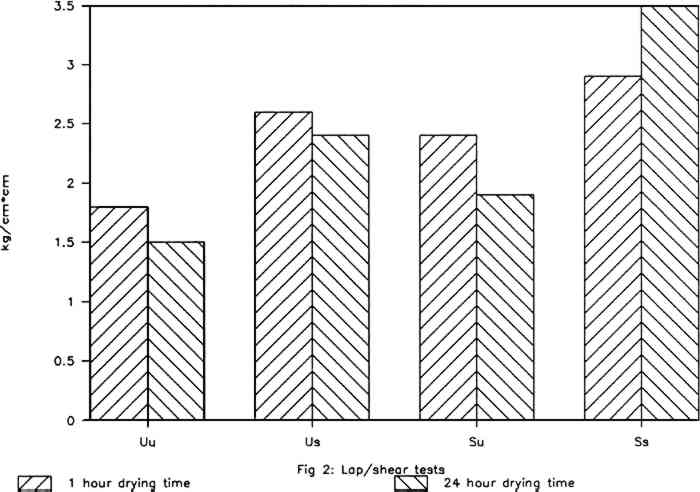 |
In general, the lap/shear tests proportionally correspond to the peel tests; that is, when the peel results were high, the lap/shear results were also high and vice versa. One exception is Su which had the lowest peel strength but the second lowest lap/shear strength.
|