CONSOLIDATION OF DETERIORATED WOOD WITH SOLUBLE RESINS
Y. Wang, & A.P. Schniewind
ABSTRACT—Consolidation of deteriorated wood by impregnation with soluble thermoplastic resins is considered the most promising method because of their physical and mechanical properties, and their reversibility compared with thermosetting synthetic resins. Type of soluble thermoplastic resin, type of solvent, resin concentration, and drying rate of solvent were examined in this study to find their effects on improvement in strength and stiffness. Butvar B98 appears to give somewhat better improvement in strength than Butvar B90. Acryloid B72 has limitations as a consolidant due to solvent retention, the latter acting as a plasticizer. The choice of solvent or of concentration cannot be made on absolute terms, and must be tailored to the particular requirements and conditions of the object to be treated. Very slow rates of solvent removal after treatment did not appear to be advantageous.
1 INTRODUCTION
THE OBJECTIVE of a consolidation treatment is to impart sufficient strength to an object while maintaining its integrity. There is much information on wood-polymer composits produced industrially by catalyst-heat or radiation process, but few articles concerned with consolidation treatments for degraded wood have been published. However, the principles relating to the formation of wood-polymer composites can be applied also to consolidation by resin impregnation. It has been found that wood-polymer composites can have significantly higher strength than untreated but intact, undamaged wood (Siau et al, 1968).
Before synthetic resins were developed, a number of materials such as animal glue, molten wax, drying oil, and natural resin were used as consolidants. However, each of these has its drawbacks (Plenderleith and Werner 1971).
2 SYNTHETIC RESINS AS CONSOLIDANTS
THERMOSETTING SYNTHETIC resins such as epoxy, polyester, and methyl acrylate are chemically or radiation curing synthetic polymers. This category of synthetic resins has been commercially applied in the manufacture of wood-plastic composites, and is known to impart strength as well as improve other physical properties of undegraded wood. Thermosetting synthetic resins such as epoxy and methyl methacrylate have also been used as consolidants for deteriorated wood (Schaffer, 1971, 1974; and Munnikendam, 1969). However, thermosetting resins are definitely not reversible. Also, epoxy treated wood may have an aesthetically unsatisfactory appearance (Schaffer, 1971), and the heat developed in curing may lead to out-of-control rapid cure and damage to an object (Munnikendam, 1978; Grattan, 1980).
Soluble thermoplastic resins are able to impart strength to deteriorated wood and to meet the requirement of reversibility. Grattan (1980) examined a number of commercially available thermoplastic resins, and found polyvinyl butyral and acrylics to be the most promising consolidants. Subsequently, Barclay (1981) used polyvinyl butyral to consolidate an eighteenth-century English fire engine.
In connection with the conservation of a canoe, Schniewind and Kronkright (1984) did a series of tests using different resins. Tests on bacterially degraded wood showed that polyvinyl butyral (Butvar) gave the most improvement in strength, followed by an acrylic (Acryloid B72) and then polyvinyl acetates (AYAT, AYAF, AYAA and AYAC). Moreover, they found that the relative improvement in strength was proportional to the degree of deterioration.
Many researchers (Munnikendam, 1978; Schaffer 1971; and Werner 1977) have criticized the use of this group of polymers, because large quantities of solvent are involved. Once conservators think about reversibility of treatment, however, impregnation with soluble thermoplastic polymers becomes the most promising method.
3 BASIC FACTORS IN THE TREATMENT OF WOOD
THE FLOW IN THE process of impregnation of consoldants into wood may be classified as unsteady-state flow, since the conditions for flow change as the void volume is being filled. By using the integrated form of Darcy's law for fluids, and assuming that permeability is constant with length, Siau (1984) derived Equ. 1 to calculate unsteady-state absorption.
Fig. .
 |
where:
FVL = fractional volumetric absorbtion of liquid for flow through both ends of a parallel-sided specimen L= length of specimen in flow direction K= specific permeability P= pressure differential t= time Va= porosity of specimen n= viscosity of liquid
Permeability is a basic characteristic of wood determining the flow of fluids during the impregnation process. There are many factors, such as pore size, pit aspiration, and other anatomical features; extractives; moisture content; and specimen flow length, which influence the permeability of wood (Nicholas and Siau, 1973). In general, permeability is higher in sapwood than in heartwood and it is also much higher in the longitudinal than in the transverse direction. Because flow of fluids through softwoods is essentially through the tracheids which are interconnected by bordered pit pairs, the fine pit structure controls the flow rate of fluids through softwood (Siau, 1984). In hardwoods the situation is more complex because of their more intricate structure. According to Siau (1970), permeability is the more significant factor affecting retention compared to pressure and viscosity.
According to Equ. 1, fractional volumetric retention is inversely proportional to the square root of viscosity of the treating solution. Relative void volume within the wood structure will largely determine the maximum retention of the treatment solution. Other properties of fluids, such as the polarity of the solvent, and dissolved gases also affect flow in wood. In general, wood is more permeable to non-polar than to polar solvents.
Equ. 1 indicates that an increased pressure gradient will improve the liquid absorbtion of woods. According to Equ. 1, the fractional volumetric retention is proportional to the square root of time. An initial vacuum applied prior to immersion or pressure can effectively remove the air from wood. Thus, the internal air cushion that might otherwise hinder penetration can be significantly reduced. Furthermore, the removal of air can create a driving force by subsequent release of atmospheric pressure.
4 OBJECTIVE
THE PURPOSE of this study was to determine the influence of type of soluble thermoplastic resin, type of solvent, resin concentration and drying rate of solvent on improvements in strengths and stiffness when resin solutions are impregnated into bacterically deteriorated wood.
5 EXPERIMENTAL MATERIALS AND METHODS
DOUGLAS-FIR FOUNDATION piles (long, heavy timbers, usually round, driven into soft soil to provide a secure foundation), which had been in service a short distance inland from the San Francisco waterfront for about 70 years, were chosen as the sample source. The first 25 mm from the pile surface had been found to be severely degraded by bacteria (Schniewind, et al., 1982). This material was chosen because it was a readily available source with a known cause and extent of deterioration. The piles had been water-logged while in service, but had been allowed to air-dry after extraction and removal. Since only the most severely deteriorated material was desired, specimens were cut from the outermost layer (first 4 to 5 mm) of a section of each of four piles.
Static bending tests of matchstick-size specimens were selected to evaluate improvements in strength and stiffness. Three by 3 by 50 mm bending specimens, as previously used by Schniewind and Kronkright (1984), were prepared. All specimens were conditioned to a nominal moisture content of 12% at 21�C and 65% relative humidity before treatment and prior to testing. These are standard conditions for wood testing. The authors believe that similar results would be obtained by testing at, say, 50% relative humidity.
Schniewind and Kronkright (1984) found that polyvinyl butyral (Butvar) gave the most improvement in strength, followed by acrylic (Acryloid B72). Accordingly, these commercially available thermoplastic polymers were further investigated in this study. Two different molecular weights of polyvinyl butyral, Butvar B90 and B98, were each dissolved in two solvents. For Acryloid acrylic resins, which are copolymers of acrylic and methacrylic acid and their esters, only one molecular weight of resin (Acryloid B72) was tested in two solvents. The solvents chosen for polyvinyl butyral were 95% ethanol and a mixture of 40% ethanol and 60% toluene on a weight basis. For Acryloid B72, acetone and toluene were used as solvents. For each resin and solvent combination, three resin concentration levels were chosen. These were 5.0%, 12.5%, and 20.0%. Three resins, two solvents, and three concentration levels provided eighteen different treatments. Another set of the same resin and solent combinations at 12.5% concentration was prepared for testing the effect of using a very slow rate of solvent removal. This added another six treatments. For each treatment, there were 20 replications, 5 specimens from each of 4 piles. This gave a total of 480 specimens. Another 100 specimens, 25 specimens from each of the 4 piles, made up a control (untreated) group. Thus, there were 580 specimens in this study.
After dissolving each polymer in its respective solvent, the specimens were submerged in the resin solution in a small dish which was covered with aluminum foil to prevent solvent evaporation. The specimens were allowed to soak in the respective resin solution for two hours before vacuum impregnation. The dish was then placed inside a desiccator, which served as vacuum chamber, followed by 19 minutes of vacuum using a tapwater aspirator. The aspirator was adjusted to produce a vacuum of about 68 to 69 cm Hg, as determined by a mercury manometer, in four minutes, and then the system was closed. This was done to minimize evaporation of solvent and resultant increases in resin concentration. In addition, another dish containing pure solvent was placed inside the desiccator to assist in saturating the space inside the desiccator with solvent vapor. The vacuum condition vs. time is shown in Fig. 1.
Fig. 1.
Typical plot of vacuum vs. time for the vacuum impregnation process.
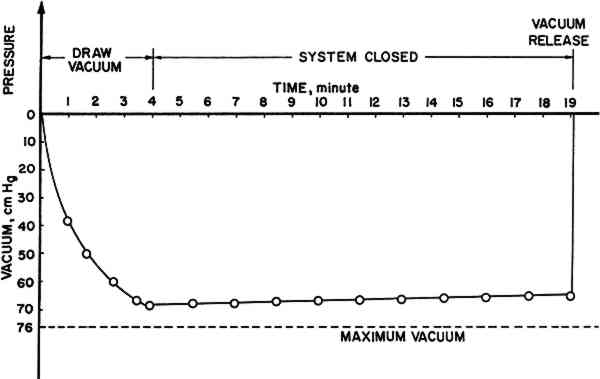 |
For Acryloid B72, the vacuum could only reach 66.5 cm Hg, instead of 68 cm Hg, since the solution started boiling at 67 cm Hg, the specimens acting like boiling chips in facilitating nucleation of bubbles. Boiling was considered undesirable because the rapid vaporation might hasten changes in concentration.
At the end of the vacuum period, air was introduced, and the specimens were allowed to soak in the solution for another 30 minutes. Then they were taken out of the solution and blotted with paper toweling. The majority of the specimens were set out to dry in a room held at 65% relative humidity and 21�C. The evaporation of solvent usually took place rapidly within the first day under the conditions stated above. For slow drying, specimens were dried in weighing bottles which were opened only briefly each day for 60 days. All specimens were left to equilibrate at 65% relative humidity and 21�C for about two weeks. All specimens were weighed before treatment and after being conditioned to determine resin retention.
According to Schniewind and Kronkright (1984), no significant increase in retention was found when the vacuum process (evacuation followed by release of pressure) was repeated. Therefore, the vacuum cycle was carried out only one time.
The static bending test was carried out on a table model Instron testing machine, over a span of 42 mm and with a loading speed of 0.01 inch per minute. Since the specimens are very small, bending strength might be influenced by whether latewood or earlywood bands happen to be at the top and bottom surfaces if load is applied to the tangential face. In order to avoid this, load was applied to the radial surface to obtain more reliable and uniform results. Values of modulus of rupture (blending strength) and modulus of elasticity (bending stiffness) were calculated for the treated and untreated specimens from the recorded load-deflection curves, followed by statistical analyses using a library computer routine called Statistical Analysis System (SAS package).
6 RESULTS AND DISCUSSION
THE TESTS OF SPECIMENS SUBJECTED to normal air drying will be discussed first, followed by a discussion of the effect of very slow drying. For the sake of convenience, every individual treatment is given a code as shown in Table 1. The first two numbers denote the resins, the first one or two characters following the resin code indicate the solvent, and the last character designates the concentration level. Slow drying (for 12.5% concentration only) is distinguished from normal air-drying by addition of the letter S to the code (not shown in Table 1).
Table I Coding of Treatments
6.1 Strength, Stiffness and Retention
Values of modulus of rupture (MOR) and modulus of elasticity (MOE) of treated and untreated bacterially degraded wood are shown in Table 2. There seems to be no clearly evident pattern among the strength values for treated and untreated specimens. However, the modulus of elasticity and modulus of rupture appeared to be strongly related to original wood density. Linear regression analysis (analysis of the relationship between two variables) showed them to be closely correlated, with coefficients of determination, r2, of 0.796 and 0.722 for strength and stiffness, respectively (r2 can vary from 0 to 1; an r2 of 0.8 means that 80% of the variation in one variable is explained by variation in the other variable). Therefore, the effect of density had to be eliminated in order to establish the true treatment effects (Snedecor and Cochran, 1980). Accordingly, an analysis of covariance was made taking original wood density as the covariate (an analysis of covariance examines the effect of known factors, such as treatments, on one variable—here strength or stiffness—while adjusting for the effects of another variable—here density). Adjusted values of MOR and MOE are listed in Table 3.
Table II MOR and MOE as tested, original wood density, weight retention and viscosity of resin solutions
Table III MOR and MOE Values Adjusted for Density
Table 3 shows that generally, within a resin and solvent combination, MOR and MOE increase in the order of increasing concentration, but there are exceptions where ethanol is the solvent. Among the treatments, 98ET.H, i.e., 20% Butvar B98 dissolved in ethanol/toluene, has the highest adjusted values of both MOE and MOR.
The weight retention of consolidant is proportional to concentration as shown in Table 2. Assuming the specimen has been completely saturated with resin solution, it is possible to calculate an estimated maximum resin retention from the original wood density (which determines void space) and the resin concentration. Estimated maximum retention values are shown in Table 4. Since the relationship between concentration and weight retention is similar for all treatment groups, only one polymer and solvent combination was examined. From Table 4, it is observed that the estimated maximum retention was less than the actual retention for each concentration. Volume increases were considered as a possible reason, but there was every reason to believe that the sample material was more like that of Barclay (1981) where expansion was too small to have a significant effect on retention, than the severely degraded material treated by Payton (1984) where linear expansion of the order of 5% had been observed. A more likely explanation is that concentration increased during treatment (which would also tend to increase actual retention), although every effort was made to keep this effect to a minimum.
Table IV Comparison Between Estimated Maximum Retention and Actual Retention
According to Siau (1971), volume retention of fluid in wood is related to pressure differential and the reciprocal of viscosity each to the power of 0.5 on a theoretical (cf. Equ. 1) or of 0.42 on an empirical basis for undegraded wood. However, in this study, viscosity did not appear to play a role in volume retention. Viscosity values of the resin solutions are listed in Table 2, and at the highest concentration, viscosity increased considerably. The 20% solution of Butvar B90 in ethanol, for example, was almost unworkable, but the specimens still appeared to reach complete saturation. This is probably due to the small size of the specimens, the fact that the wood is sapwood, the use of vacuum rather than external pressure, and possibly increased permeability of deteriorated wood. For instance, Ellwood and Ecklund (1959) observed that the sapwood of pine logs deteriorated by bacteria had greatly increased permeability in extreme cases because of destruction of the ray tissue. Also, solvents such as ethanol may be able to remove extractives from pit membranes and thus increase the permeability of specimens. Equ. 1 is therefore not applicable to the specimens of this study because it requires volumetric retention to be less than maximum.
6.2 Rule of Mixtures in Consolidation
Siau et al. (1968) proposed a geometrical model to predict improvements in strength and stiffness of wood-plastic composites by using the rule of mixtures. It is also possible to apply the rule of mixtures to wood-consolidant composites by assuming the consolidant is deposited in the cell lumens. Thus, the amount of structural material will increase without an increase in total volume.
The rule of mixtures for wood and consolidant can be expressed by the following equation which is a modified version of an equation given by Siau (Wang, 1984):
Fig. .
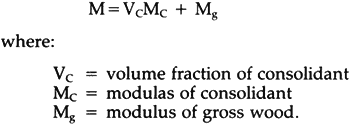 |
where:
Vc = volume fraction of consolidant Mc= modulas of consolidant Mg= modulus of gross wood.
Mechanical properties of Butvar B98 and Butvar B90 are listed in Table 5. The lower bounds of MOE of Butvar B98 and B90 were chosen to predict the stiffness of wood-consolidant composites. The average values of the lower and higher bounds of tensile strength of Butvar B98 and Butvar B90 were selected for the modulus of rupture; they are 6,100 psi and 6,200 psi, respectively. The predicted values of modulus of elasticity and modulus of rupture were then obtained from Equ. 2 and are listed in Table 6.
Table V Some Physical Properties of the Consolidants
Table VI Comparison Between Estimated and Adjusted MOR and MOE Values
Since no published information on the mechanical properties of Acryloid B72 was available, efforts were made to obtain the mechanical properties from cast film of Acryloid B72. The film as cast from solution was very soft and flexible, in contrast to the rigid pellets of Acryloid B72 as supplied. Films cast from either a toluene or an acetone solution lost about 3% in weight and became noticeably stiffer after heating in a vacuum oven at 45�C for twenty hours, and film heated at 100�C for two hours became hard and brittle. Thus, it may be concluded that solvent trapped in Acryloid B72 film acts as plasticizer. The same phenomenon is expected to take place in the wood-consolidant composite. This can be expected to limit the effectiveness of Acryloid B72 as a consolidant,∗ and no predicted values can therefore be shown for it in Table 6.
∗Additional experiments are planned to investigate the effect of longer drying times (1 year or more).
Table 6 indicates that all values of estimated MOR and MOE ascend with increasing concentration, without exception. However, it is noted that most ratios of estimated modulus to actual modulus are smaller than 1.00. This means that the predicted values tend to be too low, and that the rule of mixtures may not be sufficiently accurate for wood-plastic composites in bending. Plasticization of the resin by solvent retention cannot be a factor, as this would tend to have the opposite effect on reducing actual as compared to estimated values.
It is also noted that the few ratios of estimated to actual modulus greater than 1.00 are mostly for low concentration treatments. The ratios generally decrease with increasing concentration levels, as shown at the bottom of Table 6. There appears to be no ready explanation for this observation.
6.3 Interpretetation of Statistical Analyses
Analyses of covariance of all treatment data with normal air drying, taking original wood density as covariate, showed that treatment and pile∗ as main effects and their interaction are all significant at the 5% level for both MOE and MOR.
∗Since each pile originates from a different tree, and wood properties can be expected to vary from tree to tree, pile was included as a factor in the analysis.
The fact that pile was found to have a significant effect shows that there are factors other than density. Probably the difference is due to differing degrees of deterioration, since losses in strength are not always well correlated with weight loss and hence density.
Although treatment has a significant effect, this does not mean that each individual treatment is significantly different from the control group. Comparisons between individual treatments and the control group are listed in Table 7. There were more treatments that had a significant effect on MOR than on MOE. Although improvements in strength and stiffness depend on the mechanical properties of the consolidants used, strength would be more sensitive than stiffness to such improvements. This is because strength is controlled by local flaws or weak spots which are amenable to repair by the consolidant, while stiffness depends more on the quality of the entire specimen volume.
Table VII Probability Values for the Hypothesis: Control Mean = Treatment Mean, for Each Treatment Using Means Adjusted for Density
With respect to strength, all treatments with Butvar resulted in significant increases at medium and high concentrations, and in some cases even at low concentration. Acryloid B72, on the other hand, is significant for only one treatment (72A.H.). This is probably due to the plastization already discussed. The highest value of MOR is for treatment 98ET.H.
In order to examine the effect of concentration, drying rate, type of solvent, and molecular weight of Butvar, a set of four separate analyses of covariance was made. Two of these were 4-way analyses for Butvar, with molecular weight, solvent, pile, and either concentration or drying rate as the main effects, while the other two were 3-way analyses for Acryloid, with solvent, pile, and either concentration or drying rate as main effects.
Pile was a significant factor in each analysis conforming to the larger analysis of covariance already discussed. Concentration was a significant factor for both Butvar and Acryloid, as might be expected since there are substantial increases in retention when the concentration is increased (Table 2), with accompanying increases in bending strength in almost all cases (Table 3).
Detailed comparisons of the data in Table 3 show that both MOR and MOE are generally larger for B98 than B90-treated specimens. This difference was found to be statistically significant in the analysis where drying rate was one of the variables, but was not significant when concentration was the variable. Thus there is some evidence that B98 is more effective, probably owing to its lower molecular weight, allowing it to penetrate into smaller spaces, but the evidence is not very strong.
Examining the effect of type of solvent, the data in Table 3 show that generally the use of polar solvent (ethanol for Butvar and acetone for Acryloid) results in larger MOR and MOE values than the use of non-polar solvents (ethanol/toluene mixture for Butvar and toluene for Acryloid), although the highest strength values for a single treatment included a non-polar solvent. On the average, the polar solvent gave higher strength values in every case; but this difference was sometimes significant and sometimes not, so that here also the evidence is not very strong.
A comparison of MOR and MOE values for normal air drying and very slow drying is shown in Table 8. Since the data in this table are also adjusted data, but cover a different population of specimens, they cannot be compared with data for otherwise identical treatments in Table 3. With some exceptions, the values for slow drying are lower than those for normal air drying. In part this appears to be due to generally lower retention in the specimens dried slowly. The statistical analysis showed that the faster drying rate resulted in significantly higher values of both MOR and MOE for Butvar, while there were no statistically significant effects of drying rate in the case of Acryloid.
Table VIII Weight Retention, Retention, MOR and MOE for Two Drying Rates
Differences in drying rate might lead to two different phenomena. If there is a liquid flow, fast drying might lead to migration of solution to the surface resulting in enhanced retention of resin in the surface layers. Payton (1984) believed this to be an important factor. On the other hand, if there is no liquid flow, slow drying might lead to migration of resin into the specimen interior by diffusion. This would take place if partial evaporation from the surface layers leads to an increase in resin concentration, setting up a concentration gradient and subsequent diffusion of resin into the interior. All specimens were blotted after treatment, and in no case was there noticeable gloss on the surface after drying, which can taken as evidence that there was no significant migration of resin to the surface. On the other hand, the lower strength values associated with slow drying could be explained by an inward migration of resin, since it is less effective in the interior than at the surface in improving bending strength. In any case, the data indicate that in terms of improving strength properties, very slow drying has no advantages and may be detrimental.
6.4 Factors Affecting Retention
All specimens in this study seemed to have reached complete saturation during vacuum impregnation even at high concentration and its accompanying high solution viscosity. Thus, higher concentration solutions will deposit more resin and therefore impart more strength. However, for practical applications in which large objects or woods with low permeability are to be consolidated, full penetration is not easily obtained. In those cases, absorption could be increased by either increasing the pressure differential by application of positive pressure after the vacuum treatment (which would require more elaborate equipment), or by reducing the viscosity of the treating solution. The latter can be achieved either by reducing concentration, which is to some extent counterproductive since it reduces the retention in those parts that have been penetrated even though the total retention may be higher, or by choosing solvents which impart lower viscosity to the solution. Viscosity could also be lowered by heating, possibly at the expense of undesirable side effects. The choice of solvent or of concentration thus becomes one that cannot be made on absolute terms, but must be tailored to the particular requirements and conditions of the object to be treated.
7 CONCLUSIONS
BUTVAR GAVE MORE IMPROVEMENT IN strength and stiffness than Acryloid B72. This agrees with the results of Schniewind and Kronkright (1984). There is some evidence that Butvar B98 gives better improvement in strength than Butvar B90. Solvent retention in films of Acryloid B72 suggests that it has limited potential as a consolidant, but it has the advantage of producing solutions of lower viscosity than Butvar.
The data suggest that polar solvents may be better than non-polar ones. However, if penetration is a problem, non-polar solvents that produce lower viscosity (and may have other advantages since wood is more permeable to non-polar than to polar solvents) would be indicated.
Concentration should be as high as possible, consistent with achieving adequate penetration. Lowering the concentration in difficult cases would increase penetration, but of course the retention per unit of volume so treated would then be lower.
Using very slow drying led to lower strength values of specimens treated with Butvar but had no statistically significant effect on those treated with Acryloid.
BIBLIOGRAPHY
Barclay, R.1981. “Wood consolidation on an eighteenth century English fire engine.” Studies in Conservation26(4):133–139.
Ellwood, E.L., and Ecklund, B.A., 1959. “Bacterial attack of pine logs in pond storages.” Forest Products Journal9(9):283–292.
Grattan, D.W.1980. “Consolidants for degraded and damaged wood.” In Proceedings of the Furniture and Wooden Objects Symposium, pp.27–42. Ottawa: Canadian Conservation Institute.
Munnikendam, R.A.; and Wolschrijn, Th. J.1969. “Further remarks on impregnation of porous materials with monomers.” Studies in Conservation14(3):132–135.
Munnikendam, R.A.; and WolschrijnTh. J.1978. “Consolidation of fragile wood with low viscosity aliphatic epoxy resins.” In Conservation of Wood in Painting and the Decorative Arts, ed.Brommelle, N.S.; Moncrieff, A.; and SmithP., pp. 71–73, London: The International Institute for Conservation of Historic and Artistic Works.
Nicholas, D.D.1972. “Characteristics of preservative solutions which influence their penetration into wood.” Forest Products Journal22(5):31–36.
Nicholas, D.D., and Siau, J.F.1973. “Factors influencing the treatability of wood.” In Wood Deterioration and its Prevention by Preservatives Treatments, ed.Nicholas, D.D., Vol. II, pp.299–343. New York: Syracuse University Press.
Payton, R.1984. “The conservation of an eighth century B.C. table from Gordion.” In Adhesives and Consolidants, ed.Brommelle, N.S.; Pye, E.M.; Smith, P.; and Thomson, G., pp.133–137. London: The International Institute for Conservation of Historic and Artistic Works.
Plenderleith, H.J., and Werner, A.E.A.1971. The conservation of antiquities and works of art. 2d ed., London: Oxford University Press.
Schaffer, E.1971. “Consolidation of softwood artifacts.” Studies in Conservation. 15(3):110–113.
Schaffer, E.1974. “Consolidation of painted wooden artifacts.” Studies in Conservation19(4):212–221.
Schniewind, A.P.; Gammon, B.; and Bendsten, B.A.1982. “Strength of untreated Douglas-fir foundation piles after some 70 years' service.” Forest Products Journal32(11/12):39–46.
Schniewind, A.P.; Gammon, B.; and Bendsten, B.A., and Kronkright, D.P.1984. “Strength evaluation of deteriorated wood treated with consolidants.” In Adhesives and Consolidants, ed.Brommelle, N.S.; Pye, E.M.; Smith, P.; and Thomson, G., pp. 146–150. London: The International Institute for Conservation of Historic and Artistic Works.
Siau, J.F.; Davidson, R.W.; Meyer, J.A.; and Skaar, C.1968. “A geometrical model for wood-polymer composites.” Wood Science1(2):116–128.
Siau, J.F.; Davidson, R.W.; Meyer, J.A.; and Skaar, C.1970. “Pressure impregnation of refractory woods.” Wood Science3(1):1–7.
Siau, J.F.; Davidson, R.W.; Meyer, J.A.; and Skaar, C.1972. “The effects of specimen length and impregnation time upon the retention of oils in wood.” Wood Science4(3):163–170.
Siau, J.F.; Davidson, R.W.; Meyer, J.A.; and Skaar, C.1984. Transport Processes in Wood. Berlin: Springerverlag.
Snedecor, G.W., and Cochran, W.G.1980. Statistical Methods. 7th ed., Ames: The Iowa State University Press.
Wang, Y.1984. Consolidation of wood with soluble resins. M.S. Thesis, University of California, Berkeley.
Werner, A.E.A.1977. “Consolidation of deteriorated wooden artifacts.” In Conservation of Wood, International Symposium on the Conservation and Restoration of Cultural Property, pp. 17–21. Tokyo: Tokyo National Research Institute of Cultural Properties.
Section Index |