THE QUANTITATIVE TESTING AND COMPARISONS OF PEEL AND LAP/SHEAR FOR LASCAUX 360 H.V. AND BEVA 371
Kenneth B. Katz
2 EXPERIMENT
THE SUPPORT USED AS THE ORIGINAL canvas was a light-weight Belgian linen. The Belgian linen was stretched, wetted, and restretched again. After the second stretching, Liquitex gesso was applied to simulate a ground. A few days later, two coats of Rohm and Haas Paraloid B-72 (10% in xylene) were brushed into half the sample canvases. (The application made the linen noticeably stiffer.) The lining fabric in all cases was a woven plyester, P&S #39. The first experiment involved the application of Allois K. Diethelm AG Lascaux Acrylic adhesive 360 H. V. to the lining support. The adhesive was used undiluted from its container and applied through a fiberglas window screen material using a squeegee. After a 24-hour drying time, a second coat was applied in the same manner.
The samples were lined to produce a 1″ overlap for shear/lap testing and 3″ overlap for peel testing. Five samples were lined for each category and labeled. The labels were as follows:
To summarize the above table; each category had 5 test strips, 1″ wide, which would be tested. “P” stood for peel test, “H” stood for heat activation, “U” stood for the plain grounded Belgian linen. In another example: “L” stood for the samples intended for lap/shear testing, “X” for xylene activation and “S” for the grounded Belgian linen that had been sized with the B-72.
The linings were executed 15 days after application of the Lascaux 360 H. V. The heat activation of the Lascaux 360 H. V. took place on a Convectron vacuum hot table using (.001mm) Mylar as a membrane. The vacuum, as registered on the gauge, was never more than 2″ of Hg and the top of the table measured 58�C (138�F)∗ The temperature remained at 58�C for 5 minutes before the table was set on “cool.” The samples were rolled once using a nappy paint roller. The samples were on the table for a total of 45 minutes. Solvent activation of the Lascaux 360 H. V. took place using a paper suction table and xylene. The samples were placed on blotters which were placed on the suction table. Xylene was brushed over the adhesive and 30 seconds later, when the adhesive was tacky, the Belgian linen was placed on top. A Mylar membrane was used to cover the whole table surface and the suction table was run for 45 minutes.
∗All temperatures were recorded using a digital temperature meter. See footnote 3.
The next material tested was Adam Chemical Company's BEVA 371. The same original support and lining fabrics as used with the Lascaux 360 H. V. were used with the BEVA 371 samples. A one-quart spray container was � filled with un-diluted BEVA 371. The metal container was placed in a hot water bath and stirred until the adhesive became clear. Xylene was poured into the adhesive (⅓ by volume). Sprayer pressure was set at 50 lbs/sq. inch and the BEVA 371 was “flocked” by spraying onto the lining fabric to a thickness of about 3/32″ (Fig. 1)
Fig. 1.
Flocked BEVA 371 adhesive layer seen in raking light.
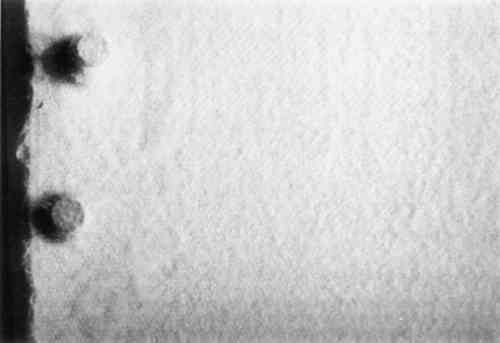 |
The heat-activated samples using Beva 371 as an adhesive were lined using a Versavac portable suction table and Dartek membrane. The vacuum was 30″ H20 (2.16Hg) and the temperature of the adhesive was 60�C. The solvent activation was also performed on the Versavac. Xylene was brushed onto the flocked BEVA 371 until it was translucent and tacky. As with the Lascaux 360, the original canvas samples were then placed on the lining fabrics. The samples were then covered with a Dartek membrane and put under 60″ of H20 pressure. After 1� hours, the membrane was removed locally, keeping the airflow on, to allow the BEVA to dry. A strong solvent smell was still noticeable and no adhesion was noted. The samples remained on the table with just airflow, without a membrane for another � hour and were then allowed to air-dry over night. No weights were used. The overnight evaporation of the solvent produced markedly stronger bonds. The samples were cut into the 1″ wide strips and labeled as follows:
All samples were sent to the Nordson Corporation testing facility in Westlake, Ohio where lap/shear and peel tests were performed on an Instron 1115 tester. The conditions were as follows for the test:
- Peel test: 50 Kg load cell1–5 Kg minimum loadxxx speed 2mm/min.chart speed 2mm/min.
- Lap shear test: 500 Kg load cell50–100 maximum loadxxxx speed 1cm/min.chart speed 1 cm/min.
Results: (see Tables/Fig. 2, 3) all samples were climatized to 72� F and 55% RH
Table 2 Comparisons of Average Peel Test Strengths Between Lascaux 360 and Beva 371
Table 3 Summary and Comparisons of Lap/Shear Tests Between Lascaux 360 and Beva 371
Fig. 2.
Peel tests.
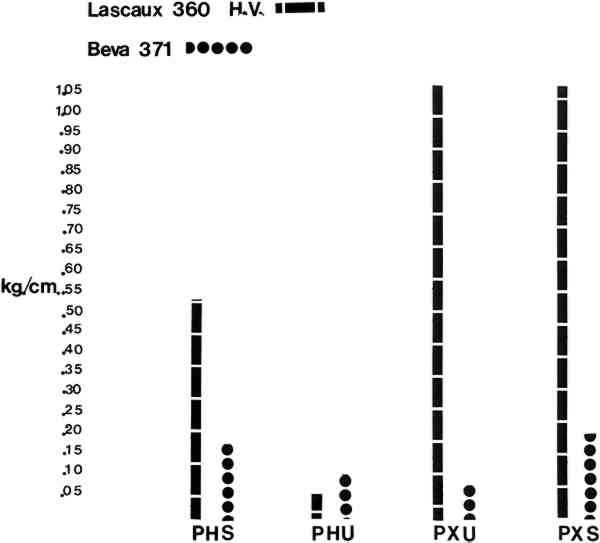 |
Fig. 3.
Lap/shear tests.
 |
|